- Graco
- 3A5216H, Doseur ProMix PD2K pour applications par pulvérisation automatique
- Manuel du propriétaire
Graco 3A5216H, Doseur ProMix PD2K pour applications par pulvérisation automatique Manuel du propriétaire
Ajouter à Mes manuels60 Des pages
▼
Scroll to page 2
of
60
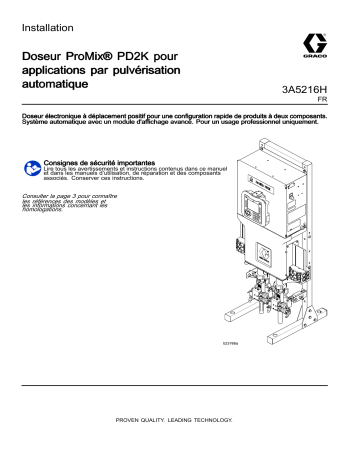
Installation Doseur ProMix® PD2K pour applications par pulvérisation automatique 3A5216H FR Doseur électronique à déplacement positif pour une configuration rapide de produits à deux composants. Système automatique avec un module d'affichage avancé. Pour un usage professionnel uniquement. Consignes de sécurité importantes Lire tous les avertissements et instructions contenus dans ce manuel et dans les manuels d’utilisation, de réparation et des composants associés. Conserver ces instructions. Consulter la page 3 pour connaître les références des modèles et les informations concernant les homologations. PROVEN QUALITY. LEADING TECHNOLOGY. Contents Manuels afférents ............................................... 2 Modèles ............................................................. 3 Mises en garde................................................... 6 Informations importantes concernant les isocyanates (ISO).................................. 9 Informations importantes concernant les catalyseurs acides................................. 11 Schéma des commandes du système 16P577................................................. 13 Configurez votre système.................................... 15 1. Sélection d’un modèle de base ................. 15 2. Sélection de tuyaux.................................. 19 3. Sélection du collecteur mélangeur à distance ......................................... 21 4. Sélection d'un pistolet pulvérisateur ........... 21 5. Sélection de kits de module de commande de changement de couleur et de catalyseur .................. 23 6. Sélection de kits de collecteur de changement de couleur et de catalyseur ...................................... 24 7. Sélection des kits d'extension de pompe ........................................... 26 8. Sélection des options de communication ............................... 26 9. Kit d’outils accessoires ............................. 26 10. Kit de mise à niveau ............................... 26 Informations générales........................................ 27 Emplacement ..................................................... 27 Installer le module d'affichage.............................. 28 Mise à niveau du logiciel pour le système ProMix PD3K+................................ 29 Alimentation en air .............................................. 30 Alimentation en produit ....................................... 31 Exigences de matière de fluide ..................... 31 Branchements à couleur unique.................... 32 Raccordements liés au changement de couleur........................................... 32 Raccords de solvant..................................... 32 Raccords de solvant sur système avec deux panneaux............................... 33 Raccords de solvant du PD3K+ .................... 33 Kit de coupelle de TSL ........................................ 34 Alternative pour le liquide d'étanchéité pour presse-étoupe (TSL) dans la tuyauterie pour les pompes PD2K à catalyseur d’ISO sensibles à l’humidité/très réactives................... 36 Accessoire de débitmètre de solvant.................... 38 Accessoire de la colonne témoin.......................... 38 Alimentation électrique........................................ 39 Configuration électrique requise.................... 39 Raccordements électriques .......................... 39 Mise à la terre .................................................... 41 Schémas électriques........................................... 43 Modèles standard (AC1000, AC2000, AC3000, AC4000) .......................... 43 Modèles à deux panneaux (AC1002, AC2002, AC3002, AC4002)............. 49 Modules et câbles en option ................................ 55 Dimensions ........................................................ 57 Données techniques ........................................... 58 Manuels afférents Les manuels sont disponibles sur www.graco.com. Réf. du manuel Description 332709 Manuel de réparation–Pièces du doseur PD2K, systèmes automatiques 332564 Manuel d'utilisation du doseur PD2K, systèmes automatiques 3A4486 Manuel du doseur PD2K à deux panneaux, systèmes manuels 3A6287 Manuel d'utilisation du doseur PD3K+, systèmes automatiques 332339 Manuel de réparation/pièces de rechange de la pompe 332454 Vannes de distribution de couleur/catalyseur, Instructions — Pièces 2 Réf. du manuel Description 332455 Manuel d'instructions/pièces de rechange des kits de changement de couleur 333282 Manuel d'instructions/pièces de rechange des kits de changement de couleur 332456 Manuel d'instructions/pièces de rechange des kits des pompes n° 3 et 4 334494 Kits d'installation du CGM du ProMix PD2K, Manuel Instructions — Pièces 3A5216H Modèles Modèles Consulter les Fig. 1-7 pour les étiquettes d'identification de composant, y compris les informations d'homologation et la certification. Référence Série Pression d’air de service maximale Pression de service maximale du produit AC0500 AC0502 A 0,7 MPa (7,0 bars, 100 psi) Avec des pompes basse pression : 2,068 MPa (20,68 bars, 300 psi) Emplacement des étiquettes de l'unité PD2K et du boîtier de commandes électriques (ECB) Avec des pompes haute pression : 10,34 MPa (103,4 bars, 1500 psi) AC1000 AC1002 A 0,7 MPa (7,0 bars, 100 psi) 2,068 MPa (20,68 bars, 300 psi) A 0,7 MPa (7,0 bars, 100 psi) 10,34 MPa (103,4 bars, 1500 psi) Matériau à base d'acide AC3000 AC3002 AC2000 AC2002 Matériau à base d'acide AC4000 AC4002 0359 II 2 G Figure 1 Étiquette d'identification des modèles AC1000, AC1002, AC3000 et AC3002 (basse pression) 3A5216H Suite page suivante. 3 Modèles Figure 2 Étiquette d'identification du boîtier de commandes 24M672 et 26A188 Figure 3 Étiquette d'identification des modèles AC2000, AC2002, AC4000 et AC4002 (haute pression) Figure 4 Étiquette d'identification des modèles AC0500 et AC0502 Figure 5 Étiquette d'identification de contrôle de changement de couleur sans sécurité intrinsèque (accessoire) 4 3A5216H Modèles Figure 6 Étiquette d'identification de contrôle de changement de couleur à sécurité intrinsèque (accessoire) Figure 7 Étiquette d'identification de kit d'extension de pompe (accessoire) PART NO. DATE / SERIES RECOGNIZED COMPONENT SERIAL NO. 4003764 Conforms to UL STD 508 Certified to CAN/CSA STD C22.2 No. 14 Artwork No. Pending 293656 Rev. D 12-30 VDC 4 AMP MAX Type 1 ENCL U.S. Patent Figure 8 Étiquette d'identification module de passerelle de communication (CGM) 3A5216H 5 Mises en garde Mises en garde Les mises en garde suivantes portent sur la configuration, l'utilisation, la mise à la terre, l’entretien et la réparation de ce matériel. Le point d’exclamation représente une mise en garde générale et le symbole de danger fait référence aux risques particuliers des procédures. Lorsque ces symboles apparaissent dans le texte du présent manuel, veuillez vous référer à ces mises en garde. Les symboles de danger et les mises en garde spécifiques au produit qui ne sont pas référencés dans cette section pourront, le cas échéant, apparaître dans le texte du présent manuel. AVERTISSEMENT RISQUE D'INCENDIE ET D'EXPLOSION Les vapeurs inflammables, telles que les vapeurs de solvant et de peinture, dans la zone de travail peuvent s’enflammer ou exploser. La circulation de la peinture ou du solvant dans l’appareil peut produire de l’électricité statique et des étincelles. Afin d'éviter les risques d'incendie ou d'explosion : • Utiliser l’équipement uniquement dans des locaux bien aérés. • Supprimer toutes les sources potentielles d’incendie, telles que les flammes pilotes, cigarettes, torches électriques portables et bâches en plastique (risque de décharge d’électricité statique). • Mettre à la terre tous les équipements présents dans la zone de travail Voir les instructions de terre. mise à la terre • Ne jamais pulvériser ou rincer du solvant sous haute pression. • Veiller à ce que la zone de travail soit toujours propre, exempte de déchets, solvants, chiffons et essence. • En présence de vapeurs inflammables, ne pas raccorder/débrancher des cordons d’alimentation électrique, ne pas allumer/éteindre des interrupteurs électriques ou des lampes. • Utiliser uniquement des tuyaux mis à la terre. • Lors de la pulvérisation dans un seau, bien tenir le pistolet contre la paroi du seau. N’utiliser en aucun cas de revêtements pour seaux, sauf s’ils sont antistatiques ou conducteurs. • Arrêtez immédiatement le système en cas d’étincelle d’électricité statique ou en cas de décharge électrique. Laissez l'équipement à l'arrêt tant que vous n'avez pas identifié la cause du problème et y avez remédié. • Un extincteur opérationnel doit être disponible dans la zone de travail. RISQUE DE DÉCHARGE ÉLECTRIQUE Cet équipement doit être mis à la terre. Une mauvaise mise à la terre, une mauvaise configuration ou une mauvaise utilisation du système peut provoquer une décharge électrique. • Couper le courant au niveau de l’interrupteur principal avant de débrancher un câble ou de faire un entretien ou une installation sur l’équipement. • Raccorder uniquement à une source d’alimentation électrique reliée à la terre. • Tout le câblage électrique doit être effectué par un électricien qualifié et doit répondre à l’ensemble des réglementations locales en vigueur. 6 3A5216H Mises en garde AVERTISSEMENT SÉCURITÉ INTRINSÈQUE Un équipement à sécurité intrinsèque qui serait mal installé ou relié à d’autres équipements qui ne seraient pas à sécurité intrinsèque peut s’avérer dangereux et provoquer un incendie, une explosion ou une décharge électrique. Respecter les réglementations locales et les consignes de sécurité suivantes. • Veiller à ce que l'installation soit conforme aux réglementations nationales, régionales et locales en vigueur concernant l'installation d'appareils électriques sur un site à risque de Classe I, Groupe D, Division 1 (Amérique du Nord) ou Classe I, Zones 1 et 2 (Europe), y compris l'ensemble des réglementations locales en matière d'incendies (par exemple, NFPA 33, NEC 500 et 516, OSHA 1910.107, etc.). • Afin d’éviter les risques d’incendie ou d’explosion : • N’installer aucun équipement homologué uniquement pour des zones non dangereuses dans une zone dangereuse. Se reporter à l'étiquette d'identification présente sur l'équipement pour connaître son classement de sécurité intrinsèque. • Ne jamais substituer des composants de l’appareil, car cela pourrait affecter sa sécurité intrinsèque. • Les équipements en contact avec des bornes intrinsèquement sûres doivent être répertoriés dans la catégorie de sécurité intrinsèque. Cela comprend les voltmètres, les ohmmètres, les câbles et branchements. Sortir l’équipement de la zone dangereuse lors d’un dépannage. SOUS--CUTANÉE RISQUE D’INJECTION SOUS Le liquide sous haute pression s’échappant du pistolet, par une fuite dans un tuyau ou par des pièces brisées peut transpercer la peau. Une telle blessure par injection peut ressembler à une simple coupure, mais il s’agit en fait d’une blessure grave qui peut même nécessiter une amputation. Consulter immédiatement un médecin pour une intervention chirurgicale. • • • • • • Ne pas pulvériser sans avoir d’abord mis en place le protège-buse et le protège-gâchette. Verrouiller la détente à chaque arrêt de la pulvérisation. Ne jamais diriger le pistolet sur une personne ou sur une partie du corps. Ne jamais placer votre main devant la buse de pulvérisation. Ne pas arrêter ou dévier les fuites avec la main, le corps, un gant ou un chiffon. Appliquer la Procédure de décompression à la fin du cycle de pulvérisation/distribution et avant toute procédure de nettoyage, de vérification ou d’entretien de l’équipement. • Serrer tous les branchements de produit avant de faire fonctionner l'équipement. • Vérifier les tuyaux et raccords tous les jours. Immédiatement remplacer les pièces usées ou endommagées. RISQUES LIÉS AUX PIÈCES EN MOUVEMENT Les pièces en mouvement risquent de pincer, couper ou sectionner des doigts ou d’autres parties du corps. • Se tenir à l’écart des pièces en mouvement. • Ne pas faire fonctionner l’équipement si des écrans de protection ou des couvercles ont été enlevés. • Un équipement sous pression peut se mettre en marche sans prévenir. Avant de faire une vérification de l’appareil, avant de le déplacer et avant de faire un entretien sur l’appareil, exécuter la Procédure de décompression et débrancher toutes les sources d’alimentation électrique. 3A5216H 7 Mises en garde AVERTISSEMENT PRODUITS OU VAPEURS TOXIQUES Les produits ou vapeurs toxiques risquent causer des blessures graves, voire fatales, en cas de projection dans les yeux ou sur la peau, ou en cas d’inhalation ou d’ingestion. • Lire la fiche technique santé-sécurité (FTSS) pour les instructions de maniement et pour connaître les risques propres aux produits utilisés, y compris les conséquences d’une exposition de longue durée. • Lors des opérations de pulvérisation, d'entretien de l'équipement et des interventions dans la zone de travail, veillez toujours à bien aérer la zone de travail et à porter des équipements de protection individuelle appropriés. Voir les avertissements dans le chapitre Équipements de protection individuelle dans ce manuel. • Entreposer les produits dangereux dans des récipients homologués et les jeter en observant les recommandations en la matière. ÉQUIPEMENT DE PROTECTION INDIVIDUELLE Toujours porter des équipements de protection individuelle appropriés et couvrir toutes les parties du corps (dont la peau) lorsque l’on pulvérise ou effectue un service de maintenance sur l’équipement ou lorsque l’on travaille dans la zone de travail. Les équipements de protection individuelle permettent de réduire les risques de blessures graves, notamment l'exposition à long terme aux produits, l'inhalation de fumées, embruns ou vapeurs toxiques, les réactions allergiques, les brûlures, les lésions oculaires et les pertes d'audition. Ces équipements de protection individuelle comprennent notamment : • Un masque respiratoire bien adapté (au besoin à adduction d’air), des gants imperméables aux produits chimiques, des vêtements de protection et des protections qui couvrent les pieds, et ce, en fonction des recommandations du fabricant du produit et des règlements locaux. • Des lunettes de protection et une protection auditive. RISQUES ASSOCIÉS À UNE MAUVAISE UTILISATION DE L’ÉQUIPEMENT Toute mauvaise utilisation peut provoquer des blessures graves, voire mortelles. • Ne pas utiliser l’appareil lorsque l’on est fatigué ou sous l’influence de médicaments, de drogue ou d’alcool. • Ne pas dépasser la pression de service maximale ni les valeurs limites de température spécifiées pour le composant le plus faible de l’équipement. Voir le chapitre Données techniques présent dans tous les manuels des équipements. • Utiliser des produits et solvants compatibles avec les pièces en contact avec le produit. Voir le chapitre Données techniques présent dans tous les manuels des équipements. Lire les avertissements du fabricant de produits et solvants. Pour plus d’informations sur le matériel, demander la fiche signalétique (SDS) au distributeur ou au revendeur. • Ne pas quitter la zone de travail tant que l'équipement est sous tension ou sous pression. • Éteindre tous les équipements et exécuter la procédure de décompression lorsque ces équipements ne sont pas utilisés. • Vérifier quotidiennement l’équipement. Réparer ou remplacer immédiatement toute pièce usée ou endommagée, et ce, uniquement par des pièces d’origine du fabricant. • Ne pas altérer ou modifier l’équipement. Toute altération ou modification peut annuler les homologations et entraîner des risques liés à la sécurité. • Veiller à ce que tout l'équipement soit adapté et homologué pour l’environnement dans lequel il est utilisé. • Utiliser l’équipement uniquement aux fins auxquelles il est prévu. Pour plus d’informations, contacter son distributeur. • Éloigner les tuyaux et câbles électriques des zones de circulation, des bords coupants, des pièces en mouvement et des surfaces chaudes. • Ne pas tordre ou trop plier les tuyaux, ne pas utiliser les tuyaux pour soulever ou tirer l’équipement. • Tenir les enfants et animaux à distance de la zone de travail. • Observer toutes les consignes de sécurité en vigueur. 8 3A5216H Informations importantes concernant les isocyanates (ISO) Informations importantes concernant les isocyanates (ISO) Les isocyanates (ISO) sont des catalyseurs utilisés dans les matériaux à deux composants. Inflammation spontanée des produits de pulvérisation Conditions concernant l’isocyanate Les produits de pulvérisation et de distribution contenant des isocyanates engendrent des embruns, des vapeurs et des particules atomisées potentiellement nocives. • Lire et comprendre les avertissements et la fiche technique santé-sécurité (FTSS) du fabricant du produit pour connaître les risques spécifiques et les précautions à prendre avec les isocyanates. • L’utilisation des isocyanates implique des procédures potentiellement dangereuses. Ne pas pulvériser avec cet équipement à moins d'y être formé, qualifié, et d'avoir lu et compris les informations contenues dans ce manuel et dans les instructions d'utilisation et la fiche de sécurité du fabricant du produit. • L’utilisation d’un équipement mal entretenu ou mal réglé peut entraîner un durcissement inapproprié du produit. L'équipement doit être soigneusement entretenu et réglé conformément aux instructions du manuel. • Afin de prévenir l'inhalation des embruns, vapeurs et particules atomisées d'isocyanates, le port d'une protection respiratoire appropriée est obligatoire pour toute personne se trouvant dans la zone de travail. Toujours porter un masque respiratoire bien adapté, au besoin à adduction d’air. Aérer la zone de travail conformément aux instructions de la FTSS du fabricant de produits de pulvérisation. Certains produits peuvent s’enflammer spontanément s’ils sont appliqués en couche trop épaisse. Lire les avertissements et la fiche technique santé-sécurité (FTSS) du fabricant de produits. Tenir séparés les composants A et B La contamination croisée peut entraîner le durcissement du produit dans les conduites de produit, ce qui peut provoquer des blessures graves ou endommager l’équipement. Pour éviter une contamination croisée : • Ne jamais interchanger les pièces en contact avec le composant A avec celles en contact avec le composant B. • Ne jamais utiliser de solvant d’un côté s’il a été contaminé par l’autre côté. • Éviter tout contact cutané avec les isocyanates. Toute personne se trouvant dans la zone de travail doit porter des gants imperméables aux produits chimiques, des vêtements de protection et des protections qui couvrent les pieds, et ce, conformément aux recommandations du fabricant de produits de pulvérisation, ainsi qu’aux règlements locaux. Observer toutes les recommandations du fabricant du produit, y compris celles concernant la manipulation des vêtements contaminés. Après la pulvérisation, se laver les mains et le visage avant de manger ou de boire quelque chose. 3A5216H 9 Informations importantes concernant les isocyanates (ISO) Sensibilité des isocyanates à l’humidité Les isocyanates qui sont exposés à l’humidité ne durciront que partiellement et formeront de petits cristaux durs et abrasifs qui resteront en suspension dans le produit. Une pellicule finit par se former sur la surface et les ISO commencent à se gélifier, augmentant ainsi leur viscosité. ATTENTION Les isocyanates partiellement durcis réduiront le rendement et la durée de vie de toutes les pièces en contact avec le produit. • Toujours utiliser un bidon hermétiquement fermé avec un dessicateur dans l’évent ou une atmosphère d’azote. Ne jamais conserver des isocyanates dans un récipient ouvert. • Maintenir la coupelle ou le réservoir (s’il est installé) de la pompe à isocyanates remplis avec du lubrifiant adapté. Le lubrifiant crée une barrière entre l’isocyanate et l’atmosphère. • N’utiliser que des tuyaux imperméables compatibles avec les isocyanates. • Ne jamais utiliser de solvants de récupération, ils pourraient contenir de l’humidité. Toujours garder les bidons de solvant fermés lorsqu’ils ne sont pas utilisés. REMARQUE : L’importance de la formation d’une peau et le degré de cristallisation varient en fonction de la combinaison isocyanates, humidité et température. Changement de produits ATTENTION Changer le type de produit utilisé dans l’équipement nécessite une attention particulière pour éviter d’endommager l’équipement et réduire le temps d’indisponibilité. • Lors d’un changement de produit, rincer plusieurs fois l’équipement pour s’assurer qu’il est bien propre. • Toujours nettoyer les crépines d’admission du produit après le rinçage. • Vérifier la compatibilité chimique avec le fabricant de produits. • Lorsque l’on passe d’époxydes à des uréthanes ou des polyrésines, démonter et nettoyer tous les composants au contact du produit et remplacer les tuyaux. Les époxydes contiennent souvent des amines du côté B (durcisseur). Les polyrésines ont souvent des amines du côté A (résine). • Lors du remontage, toujours lubrifier les pièces filetées avec un lubrifiant adapté. 10 3A5216H Informations importantes concernant les catalyseurs acides Informations importantes concernant les catalyseurs acides Seulement les modèles de doseur PD2K pour catalyseurs acides sont conçus pour les catalyseurs acides (« acide ») actuellement utilisés dans les produits de finition bicomposant pour bois. Les acides actuellement utilisés (avec des niveaux de pH jusqu’à 1) sont plus corrosifs que les anciens acides. Les produits de construction au contact des acides doivent être plus résistants à la corrosion et ils doivent être utilisés sans remplacement pour résister aux caractéristiques corrosives des acides. Conditions pour les catalyseurs acides Les acides sont inflammables et la pulvérisation ou la distribution de liquides qui contiennent des acides créent des vapeurs, des embruns et des particules atomisées potentiellement nocifs. Pour prévenir les incendies, explosions ou décharges électrique : • Lire et comprendre les avertissements du fabricant et la fiche de sécurité (SDS) pour prendre connaissance des risques spécifiques aux acides. • Utiliser uniquement des pièces originales, recommandées par le fabricant comme étant compatibles avec l’acide dans le système à catalyseur (tuyaux, raccords, etc.). Des réactions sont possibles entre toute pièce de remplacement et l’acide. • Afin de prévenir l’inhalation des embruns, vapeurs et particules atomisées d’acide, le port d’une protection respiratoire appropriée est obligatoire pour toute personne se trouvant dans la zone de travail. Toujours porter un masque respiratoire bien adapté, au besoin à adduction d’air. Aérer la zone de travail conformément aux instructions sur la FTSS du fabricant de l’acide. • Éviter tout contact de la peau avec l’acide. Toute personne se trouvant dans la zone de travail doit porter des gants imperméables aux produits chimiques, des vêtements de protection et des protections qui couvrent les pieds, des tabliers et des écrans de protection du visage, conformément aux recommandations du fabricant du produit et des règlements locaux. Respecter toutes les recommandations du fabricant du produit, dont celles portant sur le traitement des vêtements contaminés. Se laver les mains et le visage avant de manger ou de boire quelque chose. • Inspecter régulièrement l’équipement pour vérifier s’il fuit et éliminer immédiatement les pertes pour éviter un contact direct ou l’inhalation de l’acide et de ses vapeurs. • Conserver l’acide à l’abri de la chaleur, des étincelles et des flammes nues. Ne jamais fumer dans la zone de travail. Éliminer toute source d’inflammation. • Stocker l’acide dans le conteneur d’origine dans une zone fraîche, sèche et bien aérée, loin de la lumière directe du soleil et d’autres produits chimiques conformément aux recommandations du fabricant du produit. Pour prévenir la corrosion des conteneurs, ne pas stocker l’acide dans des conteneurs de remplacement. Refermer de façon étanche le conteneur d’origine pour ne pas contaminer le local de stockage et les environs. 3A5216H 11 Informations importantes concernant les catalyseurs acides Sensibilité à l’humidité des catalyseurs acides Les catalyseurs acides peuvent être sensibles à l’humidité atmosphérique et à d’autres contaminants. Il est recommandé d’enduire les joints de la pompe et de la vanne à catalyseur exposés à l’atmosphère avec de l’huile aux isocyanates, du lubrifiant de garniture (TSL) ou autre produit compatible pour prévenir l’accumulation d’acides et des dommages prématurés aux joints. ATTENTION L’accumulation d’acide endommage les joints de vanne et réduit les prestations et la durée de vie de la pompe à catalyseur. Pour empêcher d’exposer les acides à l’humidité : • Toujours utiliser un bidon hermétiquement fermé avec un dessicateur dans l’évent ou une atmosphère d’azote. Ne jamais stocker les isocyanates dans un réservoir ouvert. • Les joints de la pompe et de la vanne à catalyseur doivent être enduits d’un lubrifiant approprié. Le lubrifiant crée une barrière entre les acides et l’atmosphère. • Utiliser uniquement des tuyaux résistant à l’humidité et compatibles avec les acides. • Lors du remontage, toujours lubrifier les pièces filetées avec un lubrifiant adapté. 12 3A5216H Schéma des commandes du système 16P577 Schéma des commandes du système 16P577 Ne jamais remplacer les composants du système ou y apporter des modifications, au risque d’en altérer la sécurité intrinsèque. Consulter les manuels d’instructions afin d'obtenir toutes les instructions en matière d’installation, de maintenance et de fonctionnement du système. Ne jamais installer dans une zone dangereuse des équipements spécifiquement homologués pour des zones d'installation non dangereuses. Consulter l’étiquette d’identification pour plus d'informations concernant les homologations en matière de sécurité intrinsèque du modèle utilisé. REMARQUES SUR LE SCHÉMA DES COMMANDES DU SYSTÈME 16P577 (CERTIFICATION DE L'ENSEMBLE DU SYSTÈME FM13ATEX0026) Autres câbles CAN M12, pour sites à risque Réf. Câble Longueur ft (m) 16V423 2.0 (0.6) 16V424 3.0 (1.0) 16V425 6.0 (2.0) 16V426 10.0 (3.0) 16V427 15.0 (5.0) 16V428 25.0 (8.0) 16V429 50.0 (16.0) 16V430 100.0 (32.0) 2. Les bornes sans sécurité intrinsèque (rail électrique) ne doivent pas être raccordées aux dispositifs utilisant ou générant une puissance Um = 250 Vrms ou CC, sauf s’il a été établi que la tension a fait l’objet d’une isolation adéquate. 3. La vis de terre de protection électrique doit être raccordée à une véritable prise de terre à l'aide de la tresse de masse fournie (223547) ou par un conducteur isolé équivalent de 10 AWG ou plus. La résistance de la prise de terre de la protection électrique à la véritable prise de terre ne doit pas dépasser 1 Ohm. 4. Une mise à la terre multiple des composants est autorisée. L'appareil à sécurité intrinsèque fournit une isolation de 500 VRMS à partir de la terre. Ne pas faire fonctionner le système si le couvercle de la barrière d'alimentation électrique a été retiré. 6. L'installation doit être conforme à la norme ANSI/ISA RP12.06.01 « Installation des systèmes à sécurité intrinsèque pour les endroits (classés) dangereux » et au Code national d'électricité® (ANSI/NFPA 70). 7. L'installation au Canada doit être conforme à la réglementation électrique canadienne, CSA C22.1, partie I, annexe F. 8. Pour la zone ATEX, l'installation doit être conforme à la norme EN 60079-14 et aux réglementations locales et nationales en vigueur. 9. Pour la zone IECEx, l'installation doit être conforme à la norme IEC 60079-14 et aux réglementations locales et nationales en vigueur. 3A5216H 13 Schéma des commandes du système 16P577 SITE SANS RISQUE SEULEMENT SITE (CLASSÉ) À RISQUE Classe 1, Div. 1, Groupe D, T3 (États-Unis et Canada) Classe 1, Zone 1, Groupe IIA, T3 (ATEX et IECEx) Ta = 2° C à 50° C HAZARDOUS (CLASSIFED) LOCATION NON-HAZARDOUS LOCATION ONLY CLASS 1, DIV 1, GROUP D, T3 (USAAND CANADA) CLASS 1, ZONE 1, GROUP IIA, T3 (ATEXAND IECEx) Ta = 2 C TO 50 C POWER IN 250 VAC MAXIMUM SUPPL Y VOLTAGE BOOTH CONTROL (24M731) FM13ATEX0026 IECEx FMG 13.0011 INTRINSIC SAFE APPARATUS 5 COMMUNICA TION BARRIE R (24M485) J4 OR CABLE (16V 429) CABLE (16V 429) J3 CABLE (16V426) FM13ATEX0026 IECEx FMG 13.0011 ASSOCIATED APPARATUS CABLE (16V426) POWER BARRIE R (248192) SPLITTER 17L058 PROMIX PD2K ELECTRICAL ENCLOSURE (24M672) COLOR CHANGE MODULE (24R219, 24R220, 24R221, 24R222) (24V406, 24V407, 24V408) (24V409, 24V410, 24V411) FM13ATEX0026 IECEx FMG 13.0011 INTRINSIC SAFE APPARATUS COLOR CHANGE MODULE (24R219, 24R220, 24R221, 24R222) (24V406, 24V407, 24V408) (24V409, 24V410, 24V411) FM13ATEX0026 IECEx FMG 13.0011 INTRINSIC SAFE APPARATUS BOOTH CONTROL (24M731) FM13ATEX0026 IECEx FMG 13.0011 INTRINSIC SAFE APPARATUS Figure 9 Schéma des commandes du système 16P577 14 3A5216H Configurez votre système Configurez votre système 1. Sélection d’un modèle de base Sélectionner un modèle de base PD2K qui répond aux besoins de l’application. Voir Modèles, page 3 . Les modèles de base comprennent les composants A à F indiqués sur le schéma de l’installation type sur la page suivante. Les composants de l’appareil de base sont décrits dans le tableau suivant. Composant Description Pompes à produit de pulvérisation (A, B) Les modèles de base contiennent deux pompes à produit de pulvérisation, une pour la résine, l’autre pour le catalyseur. Installer dans la zone non dangereuse. Commutateur de débit de solvant (C) Règle le débit de solvant vers le pistolet pendant la purge. Les modèles de base contiennent deux commutateurs de débit de solvant, un pour la résine et l’autre pour le catalyseur. Boîtier des commandes électriques (D) Le boîtier des commandes électriques contient une carte barrière, une carte d’isolation à sécurité intrinsèque, des alimentations électriques de 24 V c. c. et 48 V c. c., un module amélioré de commande de produit de pulvérisation et des modules de commande de pompe. Le module de communication de passerelle (gateway) est installé dans le boîtier des commandes électriques. Il peut être alimenté avec une tension de 90–250 V c.a. et convertit cette tension en signaux basse tension acceptables utilisés par d’autres composants du système. Installer le boîtier de commandes électriques dans la zone non dangereuse. Module d’affichage avancé (E) Le module d’affichage avancé (ADM) permet à l’utilisateur d’installer, surveiller et commander le système. Installer le module d’affichage avancé (ADM) dans la zone non dangereuse. Câble CAN (F) Le câble CAN raccorde le module de communication de passerelle (gateway) au module de commande à distance à sécurité intrinsèque du mélange. 3A5216H 15 Configurez votre système ENDROIT (CLASSIFIÉ COMME) DANGEREUX ENDROIT SANS DANGER UNIQUEMENT Figure 10 Installation type Composant Description ★ Les composants A à F sont compris avec l’appareil de base. A★ Pompe du produit A (couleur) B★ Pompe du produit B (catalyseur) C★ Commutateur de débit de solvant D★ Boîtier de commandes électriques E★ Module d’affichage avancé (ADM) F★ Câble de communication CAN Les composants G à K sont compris dans les kits optionnels de changement de couleur. G Vannes de changement de couleur (accessoire, zone non dangereuse) H Module de changement de couleur (accessoire, zone non dangereuse) J Vannes de changement de catalyseur (accessoire, zone non dangereuse) K Module de changement de catalyseur (accessoire, zone non dangereuse) Les composants L à S sont des accessoires et doivent être commandés séparément. L Faisceau de tuyaux de produit/d’air (accessoire) M Collecteur de changement de couleur distant (accessoire, zone dangereuse) N Collecteur mélangeur distant (accessoire, zone dangereuse) P Pistolet pulvérisateur automatique (accessoire) R Module de commande de mélangeur distant à sécurité intrinsèque (accessoire, zone dangereuse) S Tuyau de produit pour pistolet (accessoire) T Vannes de vidange des conduites d’alimentation (accessoires, nécessaires, pas montrées) 16 3A5216H Configurez votre système ENDROIT (CLASSIFIÉ COMME) DANGEREUX ENDROIT SANS DANGER UNIQUEMENT Figure 11 Installation type avec panneau double (uniquement pour AC1002 et AC2002) Composant Description ★ Les composants A à F sont compris avec l’appareil de base. A★ Pompe du produit A (couleur) B★ Pompe du produit B (catalyseur) C★ Commutateurs de débit de solvant E★ Boîtier de commandes électriques F★ Module d’affichage avancé (ADM) Les composants G à K sont compris dans les kits optionnels de changement de couleur. G Vannes de changement de couleur (accessoire) H Module de changement de couleur (accessoire) J Vannes de changement de catalyseur (accessoire) K Module de changement de catalyseur (accessoire) Les composants L à T sont des accessoires et doivent être commandés séparément. L Module de commande de mélangeur distant à sécurité intrinsèque (accessoire, zone dangereuse) M Collecteur mélangeur distant (accessoire, zone dangereuse) N Pistolet pulvérisateur automatique (accessoire) P Collecteur de changement de couleur distant (accessoire, zone dangereuse) R Câble de communication CAN (accessoire) S Tuyau de produit pour pistolet (accessoire) T Vannes de vidange des conduites d’alimentation (accessoires, nécessaires, pas montrées) U Faisceau de tuyaux de produit/d’air (accessoire) 3A5216H 17 Configurez votre système ENDROIT (CLASSIFIÉ COMME) DANGEREUX ENDROIT SANS DANGER UNIQUEMENT Figure 12 Installation type du PD3K+ (AC1000, AC2000, AC3000, AC4000) Composant Description ★ Les composants A à F sont compris avec l’appareil de base. A★ Pompe à produit A B★ Pompe à produit B C★ Pompe à produit C D★ Vanne de solvant E★ Commande dans la cabine F★ Boîtier de commandes électriques G★ Module d’affichage avancé (ADM) Les composants G à K sont compris dans les kits optionnels de changement de couleur. H Vannes de changement de couleur (accessoire) J Module de changement de couleur (accessoire) K Vannes de changement de catalyseur (accessoire) L Collecteur mélangeur externe Les composants L à S sont des accessoires et doivent être commandés séparément. M Faisceau de tuyaux de tuyaux de produit/d’air (accessoire) – Voir le manuel d’installation (332458) du système PD2K pour plus d’informations sur les faisceaux de tuyaux de produit/d’air N Collecteur mélangeur (accessoire) – Voir le manuel (3A2801) d’instructions/pièces du collecteur mélangeur pour plus d’informations sur les collecteurs mélangeurs qui résistent aux acides P Pistolet pulvérisateur pneumatique (accessoire) R Tuyau d’air pour pistolet (accessoire) S Câbles CAN à sécurité intrinsèque (pour raccorder la commande dans la cabine au boîtier de commandes électriques) T Tuyau de produit pour pistolet (accessoire) U Vannes de changement de couleur à distance V Vannes de changement de catalyseur à distance 18 3A5216H Configurez votre système 2. Sélection de tuyaux Outil de sélection de tuyaux REMARQUE : Lorsqu’on utilise le tableau suivant pour sélectionner des lignes avec un collecteur 3K, utiliser une sélection en deux étapes : d’abord les lignes A:B, puis les lignes A:C. Lorsqu’on obtient des résultats de taille différents, sélectionner les tuyaux A recommandés plus grands et les tuyaux des côtés B et C plus petits. Utiliser ce tableau pour déterminer le faisceau de tuyaux de la bonne taille pour la viscosité et le rapport de mélange, puis sélectionner un faisceau de tuyaux pour votre application à partir des tableaux sur la page suivante. REMARQUE : Toujours utiliser des tuyaux Graco. REMARQUE : Les zones grises peuvent utiliser des tailles de tuyau d’une des deux zones voisines. SYSTÈME À BASSE PRESSION, 0–2,1 MPa (0–21 bars, 0–300 psi) Tailles de tuyau recommandées (diamètre intérieur) pour A et B 20 - 50 18 3/8 ʺ A 1/8 ʺ B 16 14 3/8 ʺ A 1/4 ʺ B 12 10 Rapport de mélange (X/1) 8 1/4 ʺ A 1/4 ʺ B 6 4 2 0 10:1 Résine épaisse (A) 1/4 ʺ A 3/8 ʺ B 7.5:1 5:1 2.5:1 1:1 1:2.5 Viscosités égales 1:5 1:7.5 1:10 Résine fine (A) Catalyseur épais (B) Catalyseur fin (B) Rapport de viscosité (résine [A] : Catalyseur [B] 3A5216H 19 Configurez votre système Considérations supplémentaires pour les systèmes PD3K+ être exécutées en phases, collecteurs 2K avec mélange au mur.) Étape 1 : Détermination des exigences en matière de matériel – Les produits de pulvérisation A et B sont d’abord combinés, puis C est ajouté (produits en phase aqueuse). • Nombre de pompes (maximum 3–4) – Pompe A (1 ou 2) – Pompe B (1 ou 2) – Pompe C (1 ou 2) • Taille de pompe (35 cc ou 70 cc) – Les produits de pulvérisation A et C sont d’abord combinés, puis B est ajouté (réduction de solvant pour de la résine pour régler la viscosité). – Les emplacements des collecteurs mélangeurs dépendent de la structure chimique des produits de pulvérisation, de la durée de conservation en pot, des viscosités des composants et des aspects en matière de rinçage/lavage des différents produits de pulvérisation. – Le troisième rapport de produit de pulvérisation d’un composant détermine la taille de pompe. Les rapports plus petits que 1 utilisent une pompe de 35 cc et les rapports plus grands que 1 utilisent une pompe de 70 cc. Étape 3 : Détermination de l’endroit de l’équipement PD3K autour de la cabine de pulvérisation • Les produits de pulvérisation pour chaque pompe (résine, catalyseur, diluant ou couleur) • Comprend le doseur, les blocs de changement de couleur et les collecteurs mélangeurs. – Pompe 1 (produit de pulvérisation A, B ou C) — Typiquement pour le produit de pulvérisation à résine et le volume de rapport le plus élevé. • Prendre le tracé des conduites en considération, puis déterminer les longueurs de tuyau nécessaires pour achever chaque partie de l’installation des conduites. – Pompe 2 (produit de pulvérisation A, B ou C) — Typiquement pour le produit de pulvérisation à catalyseur et un volume de rapport plus petit. Étape 4 : Calcul des tailles des conduites – Pompe 3 (produit de pulvérisation A, B ou C) — Typiquement pour un diluant (solvant, eau, activateur ou accélérateur) et une grande variété de volume de rapport. • Déterminer les débits de chaque composant individuellement en prenant le débit des différents pistolets pulvérisateurs et les rapports de mélange des produits. • Nombre de couleurs/produits de pulvérisation à chaque pompe • Calculer la perte de pression au niveau du premier collecteur pour chacun des composants. Sélectionner les tailles de conduite de sorte que les pertes de pression au niveau de chaque composant soient aussi proches que possible entre eux – Nombre de vannes de produit/couleur de la pompe A – Perte de pression = (Constante x Viscosité x Débit x Distance)/Diamètre intérieur^4 – Nombre de vannes de produit/couleur de la pompe B – Constante = 0,000273 – Nombre de vannes de produit/couleur de pompe C – Débit = g/min – Pompe 4 — Typiquement pour une couleur particulière ou un quatrième composant. – Nombre de couleurs pour la pompe 4, si utilisée Étape 2 : Détermination des configurations de collecteur mélangeur • Collecteurs 3K avec mélange au mur (système manuel ou automatique) – Les trois produits de pulvérisation peuvent être combinés au niveau du même collecteur 3K avec mélange au mur. • Collecteurs 2K : d’abord combinaison de A et B (ou A et C), puis de A+B à C (ou A+C à B) avant de pulvériser avec le pistolet. Certains produits de pulvérisation peuvent être combinés sans une durée de conservation en pot, de sorte que le produit de pulvérisation provenant du second collecteur doive probablement être rincé. (Les applications manuelles peuvent aussi bien utiliser le mélangeur à la ceinture que le mélangeur au mur. Les applications automatiques peuvent 20 – Viscosité = CPS – Distance = pieds – Diamètre intérieur4 = le diamètre intérieur du tuyau à la quatrième puissance • Estimer la viscosité du produit au niveau de la première étape en prenant en compte les différentes viscosités de chacun des différents produits et les rapports de composant. • Calculer la perte de pression dans les conduites de produit vers le collecteur de la seconde étape. Inclure la perte de pression sur le premier tuyau, plus la perte de pression sur le mélangeur et le tuyau entre le premier et le second collecteur. • Calculer la perte finale de pression sur la conduite de produit mélangé entre le second collecteur et le pistolet pulvérisateur. En prenant des tailles de conduite optimales, l’on réduit les pressions de pulvérisation et minimise les impacts de transition importants sur les changements de débit. 3A5216H Configurez votre système Tuyaux avec un diam. int. de 6 mm (1/4 po.) Application Produit Blocage de l’humidité Catalyseur Pression Solvant Air d’atomisation 15,2 m (50 pi.) 947078 24T134 24T135 13,8 MPa (138 bars, 2000 psi) Faible 1,6 MPa (16 bars, 225 psi) 17C967 24T266 24T267 Élevé 28,3 MPa (283 bars, 4100 psi) 238825 239107 239111 Faible 1,6 MPa (16 bars, 225 psi) 17C967 24T266 24T267 Élevé 28,3 MPa (283 bars, 4100 psi) 238825 239107 239111 Faible 1,6 MPa (16 bars, 225 psi) 17C967 24T266 24T267 Élevé 28,3 MPa (283 bars, 4100 psi) 238825 239107 239111 Faible 1,6 MPa (16 bars, 225 psi) 17C967 24T194 24T195 Nylon Nylon Nylon 7,6 m (25 pi.) Élevé et faible Nylon Résine Pression de service maximale Longueur du produit 4,6 m (15 pi.) 3. Sélection du collecteur mélangeur à distance Les kits suivants de collecteur mélangeur à distance sont disponibles. Les collecteurs mélangeurs peuvent être attachés au mur, dans la zone dangereuse, ce qui permet de mélanger à proximité de l’endroit où l’on pulvérise. Pour plus d’informations, voir le manuel des kits de changement de couleur et du collecteur mélangeur à distance dans Manuels afférents, page 2 Le système PD3K+ permet d’utiliser plus qu’un collecteur et/ou un collecteur mural à trois orifices. Description Pression de service maximale du produit 25D543 Collecteur mélangeur à distance à basse pression 2,1 MPa (21 bars, 300 psi) 25D605 Collecteur mélangeur à distance à haute pression 10,5 MPa (105 bars, 1500 psi) 26C288 Collecteur mélangeur à distance à basse pression à trois orifices 2,1 MPa (21 bars, 300 psi) Collecteur mélangeur REMARQUE : Le collecteur 26C288 n’est utilisé qu’avec le système ProMix PD3K+. Des kits (24T787) supplémentaires de commutateurs de débit peuvent être nécessaires lorsqu’on doit installer des composants supplémentaires. 4. Sélection d'un pistolet pulvérisateur Pistolets pulvérisateurs Sélectionner un pistolet pulvérisateur automatique dans le tableau suivant. Application Modèle de pistolet Référence manuel du pistolet Pression de service maximale du produit Pulvérisation pneumatique classique AirPro 313516 0,7 MPa (7 bars, 100 psi) Pulvérisateur d’air électrostatique Pro Xs 309297 0,7 MPa (7 bars, 100 psi) 3A5216H 21 Configurez votre système Application Modèle de pistolet Référence manuel du pistolet Pression de service maximale du produit Pulvérisation à assistance pneumatique classique G40 311052 28 MPa (280 bars, 4000 psi) Pistolet à assistance pneumatique électrostatique Pro Xs AA 309298 21 MPa (210 bars, 3000 psi) 22 3A5216H Configurez votre système 5. Sélection de kits de module de commande de changement de couleur et de catalyseur Utiliser les tableaux suivants pour choisir les kits de module de commande de changement de couleur/catalyseur selon les besoins de l’application que l’on utilise. Les kits contiennent un module de commande avec des électrovannes. Pour plus d'informations, voir les manuels des kits de changement de couleur et des kits de changement de couleur et de collecteur mélangeur à distance dans Manuels afférents, page 2 REMARQUE : Tous les kit de module de commande de couleur/catalyseur ne peuvent être placés qu’en dehors de l’endroit dangereux. Si l’application que l’on utilise demande que le changement de couleur à distance et les modules de commande soient placés dans l’endroit dangereux. Pour les kits autorisés qui comprennent des modules de commande agréés à sécurité intrinsèque, voir le manuel des kits de changement de couleur et du collecteur mélangeur à distance dans Manuels afférents, page 2 Table 1 Kits avec commande de changement de couleur/catalyseur (2,068 MPa [20,06 bars, 300 psi]) Référence du kit Description du kit 25D474 Module de commande avec 6 électrovannes 25D475 Module de commande avec 7 électrovannes 25D476 Module de commande avec 8 électrovannes 25D477 Module de commande avec 9 électrovannes 25D478 Module de commande avec 10 électrovannes 25D479 Module de commande avec 11 électrovannes 25D480 Module de commande avec 12 électrovannes 25D481 Module de commande avec 13 électrovannes 25D482 Module de commande avec 14 électrovannes 25D483 Module de commande avec 15 électrovannes 25D484 Module de commande avec 16 électrovannes Référence du kit Description du kit 25D328 Module de commande avec 4 électrovannes 25D485 Module de commande avec 17 électrovannes 25D329 Module de commande avec 5 électrovannes 25D486 Module de commande avec 18 électrovannes 3A5216H 23 Configurez votre système 6. Sélection de kits de collecteur de changement de couleur et de catalyseur Utiliser les tableaux suivants pour choisir les kits de collecteur de commande de changement de couleur/catalyseur selon les besoins de l’application que l’on utilise. Les kits comprennent un collecteur avec des vannes. Pour plus d'informations, voir les manuels des kits de changement de couleur et des kits de changement de couleur et de collecteur mélangeur à distance dans Manuels afférents, page 2 Table 2 Collecteur de changement de couleur/catalyseur à basse pression Référence du kit Description du kit Kits sans circulation de pompes à basse pression 24Y936 Collecteur à 2 vannes 24Y938 Collecteur à 3 vannes 24Y940 Collecteur à 4 vannes 24Y942 Collecteur à 5 vannes 24Y944 Collecteur à 6 vannes 24Y946 Collecteur à 7 vannes 24Y948 Collecteur à 8 vannes 24Y950 Collecteur à 9 vannes 24Y952 Collecteur à 10 vannes 26A272 Collecteur à 11 vannes 26A274 Collecteur à 12 vannes 26A286 Collecteur à 13 vannes 24 Référence du kit Description du kit 26A276 Collecteur à 14 vannes 26A278 Collecteur à 15 vannes 26A280 Collecteur à 16 vannes 26A282 Collecteur à 17 vannes 26A284 Collecteur à 18 vannes Kits à circulation basse pression 24Y937 Collecteur à 2 vannes 24Y939 Collecteur à 3 vannes 24Y941 Collecteur à 4 vannes 24Y943 Collecteur à 5 vannes 24Y945 Collecteur à 6 vannes 24Y947 Collecteur à 7 vannes 24Y949 Collecteur à 8 vannes 24Y951 Collecteur à 9 vannes 24Y953 Collecteur à 10 vannes 26A273 Collecteur à 11 vannes 26A275 Collecteur à 12 vannes 25A605 Collecteur à 13 vannes 26A277 Collecteur à 14 vannes 26A279 Collecteur à 15 vannes 26A281 Collecteur à 16 vannes 26A283 Collecteur à 17 vannes 26A285 Collecteur à 18 vannes 3A5216H Configurez votre système Table 3 Collecteur de changement de couleur/catalyseur à haute pression Référence du kit Description du kit Kits sans circulation de pompes à haute pression Référence du kit Description du kit 24X360 Collecteur à 2 vannes 24U182 Collecteur à 3 vannes 24U183 Collecteur à 4 vannes 24T647 Collecteur à 2 vannes 24T648 Collecteur à 3 vannes 24T677 Collecteur à 2 vannes 24T649 Collecteur à 4 vannes 24T678 Collecteur à 3 vannes 24T650 Collecteur à 5 vannes 24T679 Collecteur à 4 vannes 24T651 Collecteur à 6 vannes 24T680 Collecteur à 5 vannes 24T652 Collecteur à 7 vannes 24T681 Collecteur à 6 vannes 24T653 Collecteur à 8 vannes 24T682 Collecteur à 7 vannes 24T654 Collecteur à 9 vannes 24T683 Collecteur à 8 vannes 24T655 Collecteur à 10 vannes 24T684 Collecteur à 9 vannes 24T656 Collecteur à 11 vannes 24T685 Collecteur à 10 vannes 24T657 Collecteur à 12 vannes 24T686 Collecteur à 11 vannes 24T658 Collecteur à 13 vannes 24T687 Collecteur à 12 vannes 24T659 Collecteur à 14 vannes 24T688 Collecteur à 13 vannes 24T660 Collecteur à 15 vannes 24T689 Collecteur à 14 vannes 24T661 Collecteur à 16 vannes 24T690 Collecteur à 15 vannes 24T662 Collecteur à 17 vannes 24T691 Collecteur à 16 vannes 24T663 Collecteur à 18 vannes 24T692 Collecteur à 17 vannes Kits sans circulation haute pression compatibles avec de l'acide 24T693 Collecteur à 18 vannes 3A5216H Kits à circulation haute pression 25 Configurez votre système 7. Sélection des kits d'extension de pompe 8. Sélection des options de communication REMARQUE : Ils ne sont pas nécessaires pour les systèmes pour produits acides, qui n’utilisent qu’un seul catalyseur ou pour les systèmes avec deux panneaux, étant donné qu’ils sont déjà munis de quatre pompes. 1. Si vote application a besoin de l’intégration avec un automate programmable (PLC) : Le tableau suivant répertorie les kits disponibles pour ajouter une troisième ou quatrième pompe à votre système. Chaque kit comprend une pompe, un module de commande de pompe, une électrovanne, un cadre, un support de montage et le câblage. Pour plus d’informations, voir le manuel 332456 du kit d’extension de pompe. Référence du kit a. 24W829, kit de CGM pour PD2K 26A303, kit de CGM pour PD2K à deux panneaux 25D997, kit de CGM pour PD2K à deux panneaux avec ProfiNet 26C284, kit de CGM pour PD3K+ b. CGMEP0, Ethernet IP CGMDN0, Device Net CGMPN0, ProfiNet* 24W462, Modbus TCP Description du kit * Deux modules de CGM compris avec 25D997, kit de CGM pour PD2K à deux panneaux avec ProfitNet. Pompes basse pression (2,068 MPa [20,68 bars, 300 psi]) 24R968 Pompe 70 CC résine basse pression 24R970 Pompe 35 CC de catalyseur basse pression Pompes haute pression (10,34 MPa [103,4 bars ; 1 500 psi]) 24R969 Pompe 70 CC résine haute pression 24R971 Pompe 35 CC de catalyseur haute pression 2. Si votre application doit avoir une interface web avancée (AWI) : a. 24W829, Kit CGM pour PD2K b. 24W462, Modbus TCP** c. 15V337, Module AWI REMARQUE : Le module d’interface web avancée (AWI) n’est pour l’instant pas disponible pour les systèmes avec deux panneaux. ** Le module d’interface web avancée (AWI) doit avoir son propre module Modbus TCP. Si l’automate programmable (PLC) communique aussi avec le Modbus TCP, il faut alors deux modules 24W462. 9. Kit d’outils accessoires Les kits suivants comprennent un jeu d’outils pour l’entretien et la réparation du système PD2K. Référence du kit Description du kit 25D980 Kit d’outils d’entretien pour PD2K 10. Kit de mise à niveau Le kit suivant contient le logiciel et les pièces nécessaires pour transformer (mise à niveau) un ProMix PD2K en un PD3K+. 26 Référence du kit Description du kit 26C416 Kit de mise à niveau PD3K+ 3A5216H Informations générales Informations générales Emplacement • Les numéros de référence et les lettres entre parenthèses dans le texte renvoient aux nombres et lettres des figures. • Veiller à ce que à ce que les dimensions et les pressions de service nominales de tous les accessoires soient adaptées aux caractéristiques requises du système. • Pour protéger les écrans des peintures et des solvants, des écrans de protection en plastique transparents (10 par boîte) sont disponibles. Indiquer la réf. no. 197902 pour commander le module d'affichage avancé (ADM). Si nécessaire, nettoyer les écrans à l'aide d'un chiffon sec. Pour éviter le basculement, ce qui peut entraîner des blessures graves et des dégâts matériels, le support de montage doit être solidement ancré au sol ou sur une base appropriée. Le support n'est pas destiné à l'utilisation autoportante ou au montage mural. Montage de l'unité de base du PD2K : • Monter l'unité PD2K dans un emplacement non-dangereux. • S’assurer que la surface de montage et le matériel de montage soient suffisamment solides pour supporter le poids de l’équipement, du produit, des tuyaux, et résister aux contraintes lors du fonctionnement. • Ne pas monter sur un mur. • Fixer le support sur le sol avec des boulons de 13 mm (1/2 in) qui rentrent d'au moins 152 mm (6 in) dans le sol pour prévenir le basculement de l'unité. Voir Dimensions, page 57. • Le dégagement doit être suffisant tout autour de l'équipement pour permettre l'installation, l'accès de l'opérateur, la maintenance et la ventilation. Les ventilateurs situés à l'arrière de l'unité doivent disposer d'un espace minimum de 152 mm (6 in) de la surface la plus proche pour assurer une circulation correcte de l'air. 3A5216H 27 Installer le module d'affichage Installer le module d'affichage 1. Utiliser les vis (11) pour monter le support (10) du module d'affichage avancé (12) à l'avant du boîtier de commandes ou sur le mur. Repère Description J Couvercle sur la pile 2. Cliquer le module d'affichage avancé dans le support. K Numéro de modèle L Interface USB M Raccordement de câble CAN N Voyant d'état du module d'affichage avancé P Raccordement de câble d'accessoires R Couvercle d’accès au jeton Figure 13 Installer le module d'affichage 3. Raccorder une extrémité du câble CAN de 1,5 m (5 ft) (fourni) au module d'affichage avancé (M). L'autre extrémité du câble est déjà reliée au module de commande de produit amélioré (EFCM). REMARQUE : Pour une liste de câbles de longueurs différentes, consulter Schémas électriques, page 43. La longueur totale de tout câble utilisé dans le système ne doit pas dépasser 45 m (150 ft). Figure 14 Ports de branchement du module d'affichage avancé 28 3A5216H Installer le module d'affichage Mise à niveau du logiciel pour le système ProMix PD3K+ Si l’on met son système ProMix PD à niveau vers un PD3K+, le logiciel doit aussi être mis à niveau lors du démarrage du système. Le logiciel du PD3K+ est fourni sur un jeton noir avec le kit de mise à niveau 26C416 (voir 10. Kit de mise à niveau, page 26). 3. Introduire le jeton (T) dans la fente et bien pousser dessus. REMARQUE : Le jeton peut être inséré dans les deux sens. Installation du jeton de mise à niveau du PD3K+ 1. Mettre l’interrupteur d’alimentation du PD2K sur OFF (Arrêt). 2. Enlever le panneau d’accès au jeton. Figure 16 Introduction du jeton 4. Remettre l’interrupteur d’alimentation sur ON (Marche). Le témoin lumineux rouge (L) clignote jusqu’à ce que le nouveau micrologiciel soit complètement téléchargé. 5. Sortir le jeton (T). 6. Remettre le panneau d’accès au jeton. Figure 15 Retrait du panneau d’accès au jeton 3A5216H 29 Alimentation en air Alimentation en air Exigences de l'alimentation en air Raccords de l’air • Pression d'alimentation en air comprimé : 0,6-0,7 MPa (6-7 bars ; 85-100 psi). 1. Serrez tous les raccords des conduites d'air et de fluide du système au cas où ils se seraient desserrés pendant le transport. • Tuyaux d’air : utiliser des tuyaux mis à la terre, dimensionnés en fonction de l’appareil. • Régulateur de débit d’air et vanne d’arrêt à purgeur : monté sur chaque tuyau d’air raccordé à l’équipement d’alimentation en produit. Installer une vanne d'arrêt supplémentaire en amont de tous les accessoires des conduites d'air afin de les isoler pendant l'entretien. 2. Raccordez la conduite d'alimentation d'air principale au régulateur du débit d’air/filtre à air 17M842, puis à l'entrée d'air principale (136). Cette conduite d'air alimente les électrovannes, les vannes et les pompes. N'utilisez pas cette conduite pour alimenter le pistolet en air d'atomisation. 3. Raccorder une conduite d’alimentation en air propre séparée et dédié à l’entrée d’air du pistolet qui atomise de l’air. L'air emprisonné peut provoquer un démarrage intempestif de la pompe ou de la vanne de distribution, ce qui peut entraîner des blessures graves par projection ou en raison des pièces en mouvement. Utiliser des vannes d'arrêt à purgeur. Pour réduire les risques d'incendie et d'explosion en cas d'utilisation d'un pistolet électrostatique Graco, vous devez installer une vanne d'arrêt sur la conduite d'air du pistolet afin d'arrêter l'air d'atomisation et de turbine du pistolet. Prenez contact avec votre distributeur Graco pour de plus amples informations sur les vannes d’arrêt d'air à usage électrostatique . • Filtre de conduite d’air pour l’air de commande du système : Utiliser le régulateur du débit d’air/filtre à air 17M842 fourni pour alimenter de l’air sec et propre aux électrovannes de commande du système. • Filtre de conduite d’air pour l’air d’atomisation : Fourni par d’autres pour filtrer l’huile et l’eau de l’alimentation en air et contribuer à empêcher que la peinture devienne sale. Pour connaître les exigences en matière de filtration de l’air, voir Données techniques, page 58. 30 Figure 17 Raccords de l’air d’atomisation et du collecteur d’air Légende Raccord Description A Entrée d’air C Sortie (bouchée) de coupure de l’air M Silencieux d'échappement S Sortie (bouchée) de coupure du solvant 3A5216H Alimentation en produit Alimentation en produit Exigences de matière de fluide • Pour réduire le risque d'une pression excessive et d'une rupture de l'équipement, ce qui peut provoquer des blessures, notamment une injection dans la peau, ne dépassez pas la pression spécifiée du composant le plus sensible du système. Consultez l'étiquette d'identification pour connaître la pression maximum de service de cet équipement. • Afin de réduire les risques de blessures, tels que l'injection de fluide, il est recommandé d'installer une vanne d'arrêt entre chaque conduite de fluide et le collecteur mélangeur. Utilisez les vannes pour couper l'arrivée des produits pendant la maintenance et l'entretien. Il existe des modèles pour actionner des systèmes de pulvérisation pneumatique (300 psi) ou à assistance pneumatique (1 500 psi) avec une capacité allant jusqu'à 800 CC/minute (selon la viscosité du matériau). • Les réservoirs de pression d'alimentation en fluide, les pompes d'alimentation, ou les systèmes de circulation peuvent être utilisés pour alimenter le système en fluide. • Installez un filtre de fluide de 100 mesh (minimum) sur la conduite d'alimentation en fluide, avec une vanne de vidange. • La taille de la conduite d'alimentation doit être de sorte que la perte de pression ne soit pas plus que quelques millibars entre la tête de circulation et l’orifice de l’entrée de produit du doseur. REMARQUE : L'alimentation en produit doit se faire sans pointes de pression habituellement causées par le basculement du mouvement de pompage pendant la course de la pompe. Lire la pression d'alimentation sur le manomètre (P, voir la figure sur la page suivante). Chaque pompe doit pouvoir pomper au moins 2 fois le débit de service maximal. La pression d'alimentation doit être aussi près que possible du point de consigne de la pression : • Pour les systèmes à basse pression, 0,7 MPa (7 bars ; ± 100 psi) de point de consigne. REMARQUE : Pour les systèmes à basse pression, il est recommandé de maintenir la pression d'alimentation entre 1/2 et 2/3 de la pression de pulvérisation de service du système. • Pour les systèmes à haute pression, ± 2,1 MPa (21 bar, 300 psi) de point de consigne. Au besoin, installez les régulateurs de pression ou un réservoir tampon sur les conduites d'entrée de fluide de pompe afin de réduire la pulsation. Contactez votre distributeur Graco pour toute information supplémentaire. • Le transfert des produits peut se faire à partir de leurs réservoirs d'origine ou d'une conduite de recirculation de peinture centralisée. 3A5216H 31 Alimentation en produit Branchements à couleur unique REMARQUE : Les clapets anti-retour (J, L) sont fournis sur les collecteurs d'entrée (K) et de sortie (H) de chaque pompe. 1. Branchez la conduite d'alimentation de couleur au raccord d'entrée de fluide de pompe (S). 2. Branchez la conduite de sortie de couleur au raccord de sortie de fluide de pompe (R). 3. Effectuez les mêmes branchements sur le côté du catalyseur. REMARQUE : Pour les matériaux du catalyseur en isocyanates, le flexible résistant à l'humidité est nécessaire pour fournir le fluide au système et aussi pour faire office de conduite de fluide entre la pompe et le collecteur mélangeur. Raccordements liés au changement de couleur Si vous installez le kit d'accessoires de changement de couleur, effectuez les raccords de fluide comme décrit dans le manuel 333282. Raccords de solvant 1. Raccorder la conduite d’alimentation en solvant pour la résine au raccord d’entrée (17) pour l’interrupteur de débit de solvant 1 (FS1) 2. Raccorder la conduite d’alimentation en solvant pour le catalyseur au raccord d’entrée (17) pour l’interrupteur de débit de solvant 2 (FS2) 3. Raccorder la conduite de sortie de solvant pour la résine au raccord de sortie (74) de l’interrupteur de débit de solvant 1 (FS1), puis à la bonne vanne de changement de couleur à distance. 4. Raccorder la conduite de sortie de solvant pour le catalyseur au raccord de sortie (74) de l’interrupteur de débit de solvant 2 (FS2), puis à la bonne vanne de changement de couleur à distance. Figure 18 Branchements d'entrée et de sortie de pompe 32 Figure 19 Raccords de solvant 3A5216H Alimentation en produit Raccords de solvant sur système avec deux panneaux 2. Raccorder la conduite d’alimentation en solvant pour le composant B au raccord d’entrée (17) pour le commutateur de débit de solvant 2 (FS2). 1. Raccorder la conduite d’alimentation en solvant pour la résine pour le mélangeur #1 au raccord d’entrée (17) pour l’interrupteur de débit de solvant 1 (FS1) 3. Raccorder la conduite d’alimentation en solvant pour le composant C au raccord d’entrée (17) pour le commutateur de débit de solvant 3 (FS3). 2. Raccorder la conduite d’alimentation en solvant pour le catalyseur pour le mélangeur #1 au raccord d’entrée (17) pour l’interrupteur de débit de solvant 2 (FS2) 3. Raccorder la conduite de sortie de solvant pour le mélangeur de résine #1 au raccord de sortie (74) de l’interrupteur de débit de solvant 1 (FS1), puis à la bonne vanne de changement de couleur à distance. 4. Raccorder la conduite de sortie de solvant pour le mélangeur de catalyseur #2 au raccord de sortie (74) de l’interrupteur de débit de solvant 2 (FS2), puis à la bonne vanne de changement de couleur à distance. 5. Répéter les étapes 1–4 pour le mélangeur #2 en utilisant l’interrupteur de débit de solvant 3 (FS3) et l’interrupteur de débit de solvant 4 (FS4), et ce, pour la conduite d’alimentation en résine d’une part et pour la conduite d’alimentation en catalyseur d’autre part. 4. Raccorder la conduite d’alimentation en solvant pour le composant D au raccord d’entrée (17) pour le commutateur de débit de solvant 4 (FS4) 5. Raccorder la conduite de sortie de solvant pour le composant A au raccord de sortie (74) du commutateur de débit de solvant 1 (FS1), puis à la bonne vanne de changement de couleur à distance. 6. Raccorder la conduite de sortie de solvant pour le composant B au raccord de sortie (74) du commutateur de débit de solvant 2 (FS2), puis à la bonne vanne de changement de couleur à distance. 7. Raccorder la conduite de sortie de solvant pour le composant C au raccord de sortie (74) du commutateur de débit de solvant 3 (FS3), puis à la bonne vanne de changement de couleur à distance. 8. Raccorder la conduite de sortie de solvant pour le composant D au raccord de sortie (74) du commutateur de débit de solvant 4 (FS4), puis à la bonne vanne de changement de couleur à distance. 9. Raccorder les fils de commutateur de débit sur les bornes comme montré dans le tableau ci-dessous. Commutateur de débit de solvant 1 : Solvant à distance du composant A Broches 11-12 du connecteur EFCM J6 Commutateur de débit de solvant 2 : Solvant à distance du composant B Broches 9-10 du connecteur EFCM J7 Commutateur de débit de solvant 3 : Solvant à distance du composant C Broches 7-8 du connecteur EFCM J6 Commutateur de débit de solvant 4 : Solvant à distance du composant D Broches 9-10 du connecteur EFCM J6 Figure 20 Raccords de solvant sur système avec deux panneaux Raccords de solvant du PD3K+ 1. Raccorder la conduite d’alimentation en solvant pour le composant A au raccord d’entrée (17) pour le commutateur de débit de solvant 1 (FS1). 3A5216H 33 Kit de coupelle de TSL Kit de coupelle de TSL La coupelle est réservée au liquide d'étanchéité pour presse-étoupe (TSL) ou à l'huile ISO. Ces liquides empêchent que l'air ou l'humidité soit exposé à la résine ou au catalyseur au niveau des joints de presse-étoupe et des vannes de dosage de la pompe. Le doseur PD2K est équipé de deux kits de coupelle TSL, un pour chaque pompe. Les coupelles fournissent du TSL aux cartouches de presse-étoupe supérieures de la pompe à couleur (70 CC), aux cartouches de presse-étoupe supérieures et inférieures de la pompe à catalyseur (35 CC) et aux quatre vannes de dosage de pompe. En cas d'utilisation de catalyseurs d'isocyanates, la coupelle fixée sur le côté du catalyseur du doseur PD2K permet de fournir de l'huile ISO aux cartouches de presse-étoupe supérieures et inférieures de la pompe à catalyseur (35 CC) et aux vannes de dosage de catalyseur. 2. Placez la coupelle à TSL (73) dans le support (73a). REMARQUE : le TSL et l'huile ISO doivent être commandés séparément. Pour le TSL, référence de commande n° 206995, 0,95 litre (1 quart). Pour l'huile ISO, référence de commande n° 217374, 0,48 litre (1 pinte). 1. Faites glisser le support de montage du kit sur un côté de l'écrou hexagonal de la pompe. Figure 21 Installation du kit de coupelle de TSL REMARQUE : La cartouche de presse-étoupe supérieure de la pompe est munie de trois orifices (deux sont utilisés). Déplacez un bouchon (73d) si nécessaire pour que le raccord cannelé (73b) puisse être placé dans l'orifice le plus proche de la coupelle de TSL. REMARQUE : avant d'installer la coupelle, tracez une ligne horizontale avec un marqueur indélébile noir sur l'avant de la coupelle environ à mi-chemin entre la partie supérieure et inférieure de la coupelle. Tracez une deuxième ligne horizontale environ 3 mm (1/4 po.) au-dessus de la première ligne. Émettre une lumière intense vers ces lignes permettra d'avoir une ombre visible de l'intérieur de la coupelle de TSL. 34 3. Vérifiez que le joint torique est en place sur le raccord cannelé (73b). Enduisez de colle à filetage de force minimum et installez le raccord dans l'orifice de la cartouche de presse-étoupe supérieure. Assurez-vous que les deux orifices sont utilisés (73d). 3A5216H Kit de coupelle de TSL 4. Répétez l'opération pour la cartouche de presse-étoupe inférieure. 6. Coupez le tuyau (73c) à la longueur nécessaire. Branchez les raccords de coupelle de TSL aux raccords sur la pompe et les vannes. Le TSL est alimenté par gravité de la coupelle à la pompe et aux vannes ; mettez les raccords et tuyaux en place pour éviter les nœuds et permettre au TSL de s'écouler librement vers la vanne et à l'air d'entrer et de sortir de la vanne. 5. Si vous lubrifiez les vannes de dosage, retirez le bouchon (73d) et le joint d'étanchéité de l'orifice de la vanne (V) le plus proche de la coupelle de TSL. REMARQUE : choisissez l'orifice de vanne dirigé vers le haut. Cela permettra l'écoulement du liquide dans la vanne tout en laissant l'air en sortir. Vérifiez que le joint torique est en place sur le raccord cannelé (73b). Enduisez d'adhésif à filetage de force minimum et installez le raccord dans l'orifice de vanne (V). REMARQUE : ne confondez pas l'orifice de vanne (V) avec l'orifice d'air (W). 7. Remplissez la coupelle jusqu'à la ligne horizontale inférieure noire avec du TSL ou de l'huile ISO, convenant aux résines et aux catalyseurs utilisés. REMARQUE : si le TSL fuit au niveau de la protection de la barre de la pompe à couleur (70 CC), assurez-vous que le joint de coupelle en U inférieur est installé dans la cartouche de presse-étoupe inférieure. REMARQUE : Si vous ne lubrifiez pas les vannes de dosage, retirez les raccords cannelés (73b) non utilisés du bas de la coupelle de TSL (73). Enduisez de colle à filetage de force minimum et installez les bouchons et les joints d'étanchéité fournis avec le kit. 3A5216H REMARQUE : les niveaux de fluides dans les coupelles de TSL doivent être contrôlés tous les jours. Les niveaux de fluides doivent rester statiques pendant une longue période. L'augmentation ou la diminution des niveaux de fluides dans une coupelle de TSL peut indiquer qu'un état nécessite une attention immédiate. Pour plus de conseils, reportez-vous aux étapes de dépannage figurant dans le manuel de réparation. 35 Kit de coupelle de TSL Procédure de remplissage de l'huile ISO Il est recommandé de mettre de l'huile ISO sur la coupelle de TSL de la pompe à catalyseur plutôt que du TSL en cas d'utilisation de revêtements en polyuréthane avec des catalyseurs d'isocyanates dans des environnements très humides. L'huile ISO constituera un obstacle empêchant le catalyseur de se durcir au contact de l'humidité. Lorsque vous remplissez pour la première fois une coupelle avec de l'huile ISO, il faudra purger l'air hors de la conduite d'alimentation. REMARQUE : s'ils n'y sont pas déjà sur la coupelle de TSL, tracez les deux lignes horizontales au niveau, et légèrement au-dessus, du centre vertical de l'avant de la coupelle avant de la remplir. Pour purger l'air : 1. Remplissez la coupelle de TSL de la pompe à catalyseur jusqu'à la ligne horizontale inférieure. 2. Retirez un bouchon (73d) de la cartouche de presse-étoupe supérieure et laissez l'air de cette zone circuler tant que de l'air est expulsé. Remplacez le bouchon. 3. Répétez l'étape 2 pour la cartouche de presse-étoupe inférieure. 4. Utilisez des chiffons absorbants pour nettoyer l'excès d'huile ISO qui s'est échappée des orifices du bouchon. 5. Remplissez la coupelle de TSL d'huile ISO jusqu'à la ligne horizontale inférieure. 36 Alternative pour le liquide d'étanchéité presse--étoupe (TSL) dans la pour presse tuyauterie pour les pompes PD2K à catalyseur d’ISO sensibles à l’humidité/très réactives REMARQUE : Graco recommande cet autre liquide d'étanchéité pour presse-étoupe (TSL) dans la tuyauterie de l’installation uniquement sur les pompes à catalyseur, parce que la protection ouverte des tiges des pompes à résine empêche la circulation de ce liquide (TSL). Cet autre liquide d'étanchéité pour presse-étoupe (TSL) de la pompe à catalyseur permet à ce liquide de circuler dans le joint du haut et la cartouche de roulements (à billes) en utilisant mouvement de la protection de tige et de la tige du bas. Cette circulation purge le liquide TSL sali par l’isocyanate et l’humidité hors du joint du presse-étoupe et empêche ainsi la réaction de cristallisation de l’isocyanate et de l’humidité, empêchant tout dépôt et endommagement des joints de la pompe, de la tige de piston et des roulements (à billes). 1. Remplacer un bouchon (73d) par un raccord cannelé (73b) sur un second orifice de la cartouche de presse-étoupe supérieure de la pompe (ne boucher qu’un seul orifice). Vérifiez que le joint torique est en place sur le raccord cannelé (73b). Enduisez de colle à filetage peu forte et installez le raccord dans l'orifice de la cartouche de presse-étoupe supérieure. Veiller à ce qu’il y ait un bouchon sur le troisième orifice (73d). 3A5216H Kit de coupelle de TSL 2. Brancher sur le tuyau (73c1) venant du raccord cannelé (73b) sur la cartouche de presse-étoupe inférieure sur un des raccords cannelés (73b) sur la cartouche de presse-étoupe supérieure.** Brancher le tuyau (73c2) venant de l’autre raccord cannelé (73b) sur la cartouche de presse-étoupe supérieure sur un raccord de coupelle de liquide d'étanchéité pour presse-étoupe (TSL). presse-étoupe (TSL) dépend de plusieurs facteurs : La réactivité du catalyseur, la température et l’humidité autour de la pompe et l’état d’usure des joints. Le liquide d'étanchéité pour presse-étoupe (TSL) doit être remplacé toutes les semaines lorsque les conditions ambiantes sont difficiles. Une autre procédure d’entretien qui agrandit la durée de vie de la pompe consiste à purger le nouveau liquide d'étanchéité pour presse-étoupe (TSL) dans la protection de la tige pendant le remplacement du liquide d'étanchéité pour presse-étoupe (TSL). En purgeant ainsi le liquide d'étanchéité pour presse-étoupe (TSL), tout l’air est purgé de la protection et de la cartouche du roulement (à billes), évitant de sorte à salir l’air humide durant le remplacement de ce liquide d'étanchéité pour presse-étoupe (TSL). 1. Déposer et bien nettoyer la protection de la tige de pompage. 2. Remplir la protection de la tige avec du nouveau liquide d'étanchéité pour presse-étoupe (TSL). 3. Mettre la protection de la tige sur la tige. 4. Remplir le réservoir et laisser la force de gravité remplir les conduites du liquide d'étanchéité pour presse-étoupe (TSL). 5. Lorsque le liquide d'étanchéité pour presse-étoupe (TSL) commence à déborder de la protection, visser le dos de cette protection sur la pompe. ATTENTION * Aucun autre raccord ou tuyau n’est nécessaire pour cet autre liquide d'étanchéité pour presse-étoupe (TSL) pour tuyauterie si le raccord cannelé (73b) venant de la coupelle de liquide d'étanchéité pour presse-étoupe (TSL) (73) et le second bouchon (73d) venant de la cartouche de presse-étoupe sont utilisés pour les permuter l’un l’autre. Entretien et précautions supplémentaires Le liquide d'étanchéité pour presse-étoupe (TSL) dans le réservoir de TSL doit être remplacé plus fréquemment lorsque l’on utilise l’autre liquide d'étanchéité pour presse-étoupe (TSL) pour tuyauteries. Cette recommandation permet de ne pas salir le liquide d'étanchéité pour presse-étoupe (TSL) à cause du dépôt dans le réservoir qui salira la conduite de produit et, à cause d’une viscosité plus réduite (liquide plus épais), augmentera la pression dans les conduites de TSL. La fréquence de remplacement du liquide d'étanchéité pour 3A5216H Le volume de liquide d’étanchéité qui circule dans la protection de la tige par le roulement (à billes) et les raccords cannelés de la cartouche supérieure durant les régimes élevés de la pompe ou par le remplissage et le processus de remplacement de couleur peut mettre le liquide sous pression dans la conduite de liquide d’étanchéité pour presse-étoupe (TSL) entre la cartouche supérieure et la cartouche inférieure de la pompe. Guider et fixer les conduites de liquide d'étanchéité pour presse-étoupe (TSL) de telle façon que l’équipement ne soit pas endommagé en cas de fuite dans des conduites ou lorsqu’un raccord cannelé devait se défaire. ATTENTION Les conduites de liquide d'étanchéité pour presse-étoupe (TSL) sont souples, transparentes et adaptées au liquide d'étanchéité pour presse-étoupe (TSL). Ces caractéristiques font que l’installation se déroule plus facilement et permettent de voir dans quel état se trouve le liquide d'étanchéité pour presse-étoupe (TSL). Les conduites de liquide d'étanchéité pour presse-étoupe (TSL) doivent être remplacées pour éviter que l’équipement soit endommagé à cause d’une exposition trop longue de ces conduites à un produit catalyseur. 37 Accessoire de débitmètre de solvant Accessoire de débitmètre de solvant Accessoire de la colonne témoin Pour installer le kit de débitmètre de solvant 280555, consultez le manuel 308778. Pour installer le kit de colonne témoin 24K337, consulter le manuel 3A1906. REMARQUE : Installez le débitmètre de solvant en aval du commutateur d'arrêt de solvant près de l'unité de base. 38 3A5216H Alimentation électrique Alimentation électrique Raccordements électriques Voir Schémas électriques, page 43. Un mauvais câblage peut provoquer une décharge électrique ou des blessures graves si le travail n’est pas effectué correctement. Tout le câblage électrique doit être effectué par un électricien qualifié et être conforme à la réglementation locale. Configuration électrique requise Loger tous les câbles posés dans la cabine de pulvérisation et dans des zones à forte circulation dans des gaines pour éviter tout risque de détérioration par la peinture, les solvants et la circulation. L'unité fonctionne avec une puissance d'entrée de de 90-250 VCA, 50/60 Hz, et une intensité maximale de 7 A. Le circuit d'alimentation électrique doit être protégé par un disjoncteur de 15 A maximum. • Le cordon d'alimentation électrique compatible avec votre configuration électrique locale n'est pas compris. Le calibre de câble doit être compris entre 2,08 et 5,26 mm² (entre 8 et 14 AWG). 1. Vérifier que l’alimentation électrique soit coupée sur le panneau principal. Ouvrez le capot du boîtier de commandes. 2. Faites passer les câbles électriques à travers le réducteur de tension (S). 3. Branchez les fils (L, N, G) correctement sur la borne correspondante du bloc de bornes (T), comme indiqué ci-dessous. 4. Serrez bien l'écrou de détente. 5. Fermer le boîtier de commande. Rétablir l'alimentation électrique. 6. Suivre les instructions du chapitre Mise à la terre, page 41. Légende des câbles Câble Description L Conduite d'alimentation N Neutre G Terre • Le diamètre du port d'accès d'entrée du courant est de 22,4 mm (0,88 in). Un détendeur est fourni, il accepte un diamètre de cordon de 4 à 9 mm (0,157 à 0,354 po.). Si une autre taille de cordon est utilisée, un détendeur de taille appropriée fourni par l'utilisateur doit être installé. Figure 22 Raccords électriques du boîtier de commande 3A5216H 39 Alimentation électrique Raccords du bus de terrain Si utilisé, raccorder le câble Ethernet au CGM. Raccorder l'autre extrémité du câble au dispositif de bus de terrain (FieldBus). REMARQUE : Raccorder le CGM au bus de terrain (FieldBus) en respectant les normes FieldBus. L’interface du Modbus TCP fonctionne à 100 Mbit, duplex intégral. L'interface a une capacité de détection de polarité et de liaison automatique. 1. Le raccord (F) se trouve sur le boîtier de commandes électriques. 2. Dévisser l’écrou sur le raccord (F). 3. Sortir le raccord suffisamment loin pour le démonter et ouvrir l’œillet. 4. Guider le câble (EC) du FieldBus dans la goulotte gauche jusqu’à l’œillet. Faire attention que le câble Ethernet soit introduit avec une longueur suffisante pour qu’il puisse suffisamment être guidé dans le boîtier et raccordé au CGM. 5. Introduire le câble du FieldBus dans le trou de l’œillet, puis introduire l’œillet dans le raccord. 6. Introduire le raccord dans la paroi du boîtier de commandes électriques, puis visser l’écrou dessus. Serrer l’écrou avec les doigts. 7. Attacher un bloc en ferrite (3) proche de l’extrémité du câble du FieldBus. 8. Attacher le câble du FieldBus sur le module de passerelle de communication (CGM). 40 3A5216H Mise à la terre Mise à la terre Consultez l'illustration de la page suivante. dangereuse doivent être raccordés à une véritable prise de terre dans la zone dangereuse. Pompes d'alimentation ou pots sous pression Cet équipement doit être mis à la terre afin de réduire le risque d’étincelles d’électricité statique ou de décharge électrique. Les étincelles électriques et d’électricité statique peuvent mettre le feu aux vapeurs ou les faire exploser. Une mauvaise mise à la terre peut provoquer une décharge électrique. La mise à la terre offre un câble échappatoire au courant électrique. Raccorder un fil et un collier de terre entre une véritable prise de terre et les pompes ou les pots. Consulter le manuel de la pompe ou du pot sous pression. Tuyaux d’air et de produit Boîtier de commandes électriques N'utiliser que des tuyaux mis à la terre. Le boîtier de commandes électriques est équipé de deux points de mise à la terre. Les deux branchements doivent être effectués. Objet à peindre • Branchez le fil de terre (Y) à la vis de terre sur le boîtier de commandes électriques. Reliez l'extrémité du collier à une véritable prise de terre. • L'alimentation électrique doit être reliée à la terre conformément à la réglementation locale. Branchez le fil de terre d'alimentation électrique à la borne de terre dans le boîtier de commandes électriques. Voir Raccordements électriques, page 39. Observer les réglementations locales. Réservoir de solvant ou poste de purge Respecter la réglementation locale Utiliser uniquement un réservoir de solvant ou un poste de purge conducteur posé sur une surface mise à la terre. Ne jamais poser le réservoir de solvant ou le poste de purge sur une surface non conductrice, telle que du papier ou du carton, ce qui coupera la continuité de la mise à la terre. Contrôle de la résistance Figure 23 Vis de terre et interrupteur électrique Pour que la mise à la terre soit bonne et pour réduire le risque d’incendie ou d’explosion, la résistance entre les composants et une vraie terre doit être plus petite que 1 Ohm. Réservoir d’alimentation en produit de pulvérisation Pistolet pulvérisateur Observer les réglementations locales. Respecter les instructions de mise à la terre figurant dans le manuel des pistolets. Module de changement de couleur Raccordez un fil de terre entre le module de changement de couleur et une véritable prise de terre. Les modules de changement de couleur intrinsèquement sûrs se trouvant dans la zone 3A5216H • Non-électrostatique : Raccorder le pistolet pulvérisateur à la terre en le branchant sur un tuyau d'alimentation de produit mis à la terre homologué par Graco. • Électrostatique : Mettre à la terre le pistolet pulvérisateur en le reliant à un tuyau d'air mis à la terre et approuvé par Graco. Raccorder le fil de terre du tuyau d'air à une vraie terre. 41 Mise à la terre EMPLACEMENT DANGEREUX NON--DANGEREUX EMPLACEMENT NON Figure 24 Mise à la terre du système Légende 1 Vis de terre du boîtier de commandes électriques 2 Fil de terre du boîtier de commandes électriques 3 Fils de terre du module de changement de couleur (CC) 4 Câble à sécurité intrinsèque (IS) 42 5 Véritable prise de terre ; consultez la réglementation locale pour connaître les prescriptions 6 Câble à sécurité non intrinsèque 7 Fil de terre du module de commande du mélangeur à distance 3A5216H Schémas électriques Schémas électriques Modèles standard (AC1000, AC2000, AC3000, AC4000) REMARQUE : Le schéma électrique montre toutes les extensions de câblage possibles dans un appareil ProMix PD2K : modèles AC1000 et AC2000. Certains composants montrés ne sont pas présents dans tous les systèmes. REMARQUE : Pour une liste avec les options de câble, voir Modules et câbles en option, page 55. CABLE 16H078 AWI GATEWAY (24R910) 2 CABLE (15V206) CABLE (15V206) 2 CATALYST CHANGE MODULE 6 6 (24N935) CATALYST CHANGE MODULE 5 6 (24N935) COLOR CHANGE MODULE 4 6 (24N935) COLOR CHANGE MODULE 3 6 (24N935) 2 CABLE (15V206) MAC SERIES 46 SOLENOID (16P812) PUMP V/P FOR FLUID REG. UP DOWN FLOW SENSOR (120278) OR G3000 METER (239716, 258718 16M510, 16M519) PUMP INLET TRANSDUCER (16P289, 16P290) PUMP OUTLET TRANSDUCER (16P289, 16P290) PUMP V/P FOR FLUID REG. MAC SERIES 46 SOLENOID (16P812) PUMP OUTLET TRANSDUCER (16P289, 16P290) BREAKOUT MODULE PUMP 3 (24N527) PUMP INLET TRANSDUCER (16P289, 16P290) ENCODERAND MOT OR (16P036, 16P037) WIRE HARNESS (24P684, 24P685) UP DOWN FLOW SENSOR (120278) OR G3000 METER (239716, 258718 16M510, 16M519) SWITCH (120278) SOLVENT METER (258718) CABLE (16V429) COLOR CH ANGE MODULE 7 (24R219) 7 1 CABLE (16V426) 1 LIGHT TOWER (15X472) 1 CABLE (16T280) CABLE (16T659) CABLE (16T659) CABLE (16T659) CABLE (16T659) SOLVENT FLOW INPUTS SAFETYINTERLOCK SWITC H 3 ADVANCED CABLE DISPLAY MODULE (121003) (24E451) 4 FAN (24P658) BARRIER BOARD (248192) GFB INTERF ACES SOLVENTCUTOFF (121324) SWITCH (120278) FLOW RATE ANALOG IN FLOW SENSOR (120278) OR G3000 METER (239716, 258718 16M510, 16M519) FAN (24P658) ENCODER AND MOT OR (16P036, 16P037) WIRE HARNESS (24P684, 24P685) UP DOWN SPLITTER (16P243) PRESSURE SW (121323) GCA MODULE EFCM (24N913) FLOW RATE ANALOG IN FLOW SENSOR (120278) OR G3000 METER (239716, 258718 16M510, 16M519) PUMP V/P FOR FLUID REG. BREAKOUT MODULE PUMP 2 (24N527) UP DOWN PUMP OUTLET TRANSDUCER (16P289, 16P290) COLOR CH ANGE MODULE 8 (24R219) 7 BOOTH CO NTROL(24M731) BREAKOUT MODULE PUMP 4 (24N527) MAC SERIES 46 SOLENOID (16P812) PUMP V/P FOR FLUID REG. PUMP INLET TRANSDUCER (16P289, 16P290) MAC SERIES 46 SOLENOID (16P812) PUMP OUTLET TRANSDUCER (16P289, 16P290) BREAKOUT MODULE PUMP 1 (24N527) PUMP INLET TRANSDUCER (16P289, 16P290) FAN (24P658) ENCODERAND MOT OR (16P036, 16P037) WIRE HARNESS (24P684, 24P685) SOLENOID (121324) FLOW RATE ANALOG IN FAN (24P658) 119159 119159 119159 119159 16T072 CAN IS BOARD (24M485) ENCODER AND MOT OR (16P036, 16P037) WIRE HARNESS (24P684, 24P685) GUNTRIGGER INPUTS CABLE (16V426) 16W159 16W159 POWER IN 16W159 16W159 TERMINAL BLOCKS WITH FUSES FLOW RATE ANALOG IN TERMINAL BLOCK (114095) 3 CABLE (121227) 2 5 COLOR CHANGE MODULE 2 6 (24N935) 48V-10APOWER SUPPLY (16U820) 3 CABLE (121001) 3 CABLE (121227) LINEFILTER (16V446) 5 24V POWER SUPPLY (16T660) CABLE (15V206) CABLE 16T658 INTEGRA TION GATEWAY COLOR CHANGE MODULE 1 6 (24N935) POWER MODULE (24R257) 2 CABLE (15V206) 2 CABLE (15V206) 065161, 065159 RELAY 2 POSITION SWITCH (16U725) HAZARDOUS LOCATION NON-HAZARDOUS LOCATION Figure 25 Schéma électrique, feuille 1 3A5216H 43 Schémas électriques CONTINUED ON P AGE 3 CONTINUED ON P AGE 3 UNUSED UNUSED 5 4 3 2 1 10 1 2 3 4 5 8 1 2 3 4 5 6 7 8 9 10 11 12 5 AWI GATEWAY (24R910) 12345 CAN IS BOARD (NONIS) (IS) 4 CABLE 1 2 3 4 5 1 2 3 4 5 (121227) P3 P4 5 12345 1 2 3 UNUSED 54 3 2 1 SOLVENT CUTOFF (121324) PWR (RED) SIG (WHITE) COM(BLACK) SHIELD/GRN SOLVENT UNUSED BARRIER BOARD (248192) +24VDC COM UNUSED UNUSED +24VDC COM +24VDC COM UNUSED 1 RED WIRE (06 5161) 2 1 2 3 4 5 6 7 8 9 10 11 12 13 14 15 16 17 18 19 20 21 22 23 24 25 METER (258718) GROUND BAR 1 2 3 4 5 6 7 8 9 10 11 12 13 14 15 16 17 18 19 20 21 22 23 24 25 4 25 PIN D-SUB CABLE (16T659) UNUSED UNUSED CABLE (16T280) GFB INTERFACE (121324) 123 UNUSED UNUSED GCAMODULE EFCM (24N913) 3 3 (24M485) 12345 SPLITTER (16P243) (121001) INTEGR ATION GATEWAY 3 5 1 CABLE 1 2 3 4 5 4 25 PIN D-SUB CABLE (16T659) BLAC K WIRE (065159) 24V POWER SUPPLY (16T660) 1 2 3 4 5 6 7 8 9 10 11 12 13 14 15 16 17 18 19 20 21 22 23 24 25 1 2 3 4 5 6 7 8 9 10 11 12 13 14 15 16 17 18 19 20 21 22 23 24 25 1 1 3 2 12345 1234 4 BREAK OUT MODULE PUMP 2 (24N527) 7 6 5 12345 12345 1234 13 A1(+) A2(-) 8 12 34 12 34 5678 7 6 5 12345 1234 12 3 4 8 12 34 5678 +24VDC COM +24VDC COM PUMP 2 UP PUMP 2 DOWN MANIFOLD MAC SERIES 46 (16P812 QTY 2) +-+-+-+- LINE FILTER (16V446) V/P FOR FLUID REG. PUMP 2 OUTLET TRANSDUCER PUMP 2 (16P289 OR 16P290) SEE DET AILAOR B INLET TRANSDUCER PUMP 2 (16P289 OR 16P290) FAN PUMP 1 (24P658) PWR (RED) SIG (WHITE) COM(BLACK) SHIELD/GRN +24VDC COM +24VDC COM PUMP 1 UP ENCODER/MO TOR AND WIRE HARN ESS PUMP2 MANIF OLD MAC SERIES 46 (16P812 QTY 2) F2 F1 F4 N F3 +-+-+-+- POWER MODULE (24R257) N04 4 12345 PUMP 1 DOWN SEE DET AILAOR B V/P FOR FLUID REG. PUMP 1 + - CABLE (16T658) L ENCODER/MOT OR AND WIRE HARN ESS PUMP1 N03 2 POSITION SWITCH (16U725) N04 INLET TRANSDUCER PUMP 1 (16P289 OR 16P290) N (BLUE) L (BROWN) N03 GRND 48V-10A POWER SUPPLY (16U820) OUTLET TRANSDUCER PUMP 1 (16P289 OR 16P290) 14 N L 3 1234 +48V COM +48V COM RELAY 2 12345 +48V COM +48V COM BREAK OUT MODULE PUMP 1 (24N527) GRND (GRN/YEL) PWR (RED) SIG (WHITE) COM(BLACK) SHIELD/GRN 2 P4 P3 16T072 12345 1 1 2 3 4 5 FAN PUMP 2 (24P658) CABLE (121227) CABLE (15V206) CABLE (16V429) 2 UNUSED 3 G3000 METER PUMP 1 (EITHER, 239716, 258718,16M510, OR 16M519) GRND SCREW TWIST ED PAIR CABLE (16W159) G3000 METER PUMP 2 (EITHER, 239716, 258718,16M510, OR 16M519) GRND SCREW TWIST ED PAIR CABLE (16W159) L GRND N MOTOR MOUNTING SCREW 1 2 3 4 5 6 78 9 1011 12 WIRE HARN ESS (24P685) 1 2 3 4 5 6 78 9 PUMP ENCODER AND MOTOR (16P037) 12 10 1 2 3 4 5 67 8 9 MOTOR MOUNTING SCREW 1011 12 UNUSED UNUSED UNUSED DRAIN/FOIL UNUSED DRAIN/FOIL UNUSED UNUSED DRAIN/FOIL UNUSED UNUSED UNUSED UNUSED DRAIN/FOIL DRAIN/FOIL MOTOR GROUND SCREW UNUSED UNUSED UNUSED UNUSED WIRE HARN ESS (24P684) L N GRND 3 1234 1 2 3 4 5 67 8 9 UNUSED UNUSED 12345 1234 UNUSED UNUSED 12345 BREAKOUT MODULE (24N527) 2 3 UNUSED UNUSED UNUSED 2 UNUSED UNUSED UNUSED UNUSED UNUSED BREAKOUT MODULE (24N527) TERMINAL BLOCK (114095) UNUSED L N GRND POWER IN DETAIL B, HIGH PRESSURE PUMPS (24M707, 24M71 5, 24T800) DETAILA, LOW PRESSURE PUMPS (24M706, 24M714, 24T799) UNUSED CABLE (16H078) 10 PUMP ENCODER AND MOTOR (16P036) Figure 26 Schéma électrique, feuille 2, partie 1 SUITE EN PAGE SUIVANTE 44 3A5216H Schémas électriques Figure 27 Schéma électrique, feuille 2, partie 2 SUITE EN PAGE SUIVANTE 3A5216H 45 Schémas électriques FROMCAN IS BOARD (24M485) 2 CABLE(15V206) 12 34 5 COLOR CHANGE MODULE 1 (COLORS 1 THRU 8) MANIFOLD FLUSH COLOR1 COLOR2 COLOR3 COLOR4 COLOR5 COLOR6 COLOR7 COLOR8 +24VDC COM +24VDC COM +24VDC COM 1 2 3 4 5 6 +24VDC COM +24VDC COM +24VDC COM 1 2 3 4 5 6 +24VDC COM +24VDC COM +24VDC COM 1 2 3 4 5 6 J8 MANIFOLD J9 6 5 4 3 2 1 COM +24VDC COM +24VDC COM +24VDC J16 6 5 4 3 2 1 COM +24VDC COM +24VDC COM +24VDC J10 6 5 4 3 2 1 COM +24VDC COM +24VDC COM +24VDC 6 J15 J14 DUMP COLOR1 COLOR2 COLOR3 COLOR4 COLOR5 COLOR6 COLOR7 COLOR8 MANIFOLD *FLUSH COLOR9 COLOR10 COLOR11 COLOR12 COLOR13 COLOR14 COLOR15 COLOR16 12 34 5 COLOR CHANGE MODULE 2 (COLORS 9 THRU 16) +24VDC COM +24VDC COM +24VDC COM 1 2 3 4 5 6 +24VDC COM +24VDC COM +24VDC COM 1 2 3 J15 4 5 6 +24VDC COM +24VDC COM +24VDC COM 1 2 3 4 5 6 J9 J8 6 J16 J14 MANIFOLD MANIFOLD J10 6 5 4 3 2 1 COM +24VDC COM +24VDC COM +24VDC 6 5 4 3 2 1 COM +24VDC COM +24VDC COM +24VDC 6 5 4 3 2 1 COM +24VDC COM +24VDC COM +24VDC DUMP* FLUSH COLOR9 CATALYST 1 COLOR10 CATALYST 2 COLOR11 CATALYST 3 COLOR12 CATALYST 4 COLOR13 COLOR14 COLOR15 COLOR16 CATALYST CHANGE MODULE 5 (CATALYST 1 THRU 4) +24VDC COM +24VDC COM +24VDC COM 1 2 3 4 5 6 +24VDC COM +24VDC COM UNUSED UNUSED 1 2 3 4 5 6 J15 UNUSED UNUSED UNUSED UNUSED UNUSED UNUSED 1 2 3 4 5 6 J14 J8 COLOR17 COLOR18 COLOR19 COLOR20 COLOR21 COLOR22 COLOR23 COLOR24 12 34 5 COLOR CHANGE MODULE 3 (COLORS 17 THRU 24) +24VDC COM +24VDC COM +24VDC COM 1 2 3 4 5 6 J8 +24VDC COM +24VDC COM +24VDC COM 1 2 3 4 5 6 J15 +24VDC COM +24VDC COM +24VDC COM 1 2 3 4 5 6 J14 J9 6 J16 6 5 4 3 2 1 COM +24VDC COM +24VDC UNUSED UNUSED J10 6 5 4 3 2 1 UNUSED UNUSED UNUSED UNUSED UNUSED UNUSED DUMP CATALYST 1 CATALYST 2 CATALYST 3 CATALYST 4 12 34 5 2 CABLE (15V206) 2 CABLE MANIFOLD J9 COM +24VDC COM +24VDC COM +24VDC 6 12 34 5 *FLUSH MANIFOLD 6 5 4 3 2 1 MANIFOLD MANIFOLD 6 5 4 3 2 1 COM +24VDC COM +24VDC COM +24VDC 6 5 COM +24VDC COM +24VDC COM +24VDC J16 43 2 1 6 5 4 J10 3 2 1 COM +24VDC COM +24VDC COM +24VDC *FLUSH DUMP* COLOR17 COLOR25 COLOR18 COLOR26 COLOR19 COLOR27 COLOR20 COLOR28 COLOR21 COLOR29 COLOR22 COLOR30 COLOR23 COLOR24 54 3 2 1 (15V206) 2 CABLE (15V206) 12 34 5 12 34 5 COLOR CHANGE MODULE 4 (COLORS 25 THRU 32) +24VDC COM +24VDC COM +12VDC COM 1 2 3 4 5 6 J8 +24VDC COM +24VDC COM +24VDC COM 1 2 3 4 5 6 J15 +24VDC COM UNUSED UNUSED UNUSED UNUSED 1 2 3 4 5 6 J14 J9 6 J16 J10 MANIFOLD 6 5 4 3 2 1 COM +24VDC COM +24VDC COM +24VDC 6 5 4 3 2 1 COM +24VDC COM +24VDC COM +24VDC 6 5 4 3 2 1 COM +24VDC UNUSED UNUSED UNUSED UNUSED DUMP* COLOR25 COLOR26 COLOR27 COLOR28 COLOR29 COLOR30 12 34 5 2 CABLE(15V206) Figure 28 Schéma électrique, feuille 3 * Peut ne pas être utilisé avec certaines configurations. SUITE EN PAGE SUIVANTE 46 3A5216H Schémas électriques CATALYST CHANGE MODULE 6 (CATALYST 3 THRU 4) MANIFOLD FLUSH CATALYST 3 CATALYST 4 +24VDC COM +24VDC COM +24VDC COM 1 2 3 4 5 6 J8 UNUSED UNUSED UNUSED UNUSED UNUSED UNUSED 1 2 3 4 5 6 J15 UNUSED UNUSED UNUSED UNUSED UNUSED UNUSED 1 2 3 4 5 6 MANIFOLD 6 5 4 3 2 1 COM +24VDC COM +24VDC COM +24VDC J16 6 5 4 3 2 1 UNUSED UNUSED UNUSED UNUSED UNUSED UNUSED J10 6 5 4 3 2 1 UNUSED UNUSED UNUSED UNUSED UNUSED UNUSED 6 5 4 3 2 1 COM +24VDC COM +24VDC COM +24VDC J16 6 5 4 3 2 1 UNUSED UNUSED UNUSED UNUSED UNUSED UNUSED J10 6 5 4 3 2 1 UNUSED UNUSED UNUSED UNUSED UNUSED UNUSED J9 6 J14 DUMP CATALYST 3 CATALYST 4 2 CABLE (15V206) 12 34 5 MANIFOLD FLUSH CATALYST 1 CATALYST 2 54 3 2 1 CATALYST CHANGE MODULE 5 (CATALYST 1 THRU 2) +24VDC COM +24VDC COM +24VDC COM 1 2 3 4 5 6 J8 UNUSED UNUSED UNUSED UNUSED UNUSED UNUSED 1 2 3 4 5 6 J15 UNUSED UNUSED UNUSED UNUSED UNUSED UNUSED 1 2 3 4 5 6 MANIFOLD J9 6 J14 DUMP CATALYST 1 CATALYST 2 (15V206) 2 CABLE 12 34 5 12 34 5 COLOR CHANGE MODULE 4 (COLORS 25 THRU 32 ) ALTERNATE CONFIGURATION FOR CATALYST CHANGE CONTROL Figure 29 Schéma électrique, feuille 3, configuration alternée pour le contrôle du changement de catalyseur SUITE EN PAGE SUIVANTE 3A5216H 47 Schémas électriques FROMCAN IS BOARD (24M485) NON-HAZARDOUS LOCATION HAZARDOUS LOCATION MANIFOLD COLOR FLUSH COLOR 1 COLOR 2 COLOR 3 COLOR 4 COLOR 5 COLOR 6 COLOR 7 COLOR 8 +12VDC COM +12VDC COM +12VDC COM 1 2 3 4 5 6 +12VDC COM +12VDC COM +12VDC COM 1 2 3 4 5 6 +12VDC COM +12VDC COM +12VDC COM 1 2 3 4 5 6 12 34 5 COLOR CHANG E MODULE 7 (COLORS 33 THRU 40) J8 MANIFOLD J9 6 5 4 3 2 1 COM +12VDC COM +12VDC COM +12VDC J16 6 5 4 3 2 1 COM +12VDC COM +12VDC COM +12VDC 6 5 4 3 2 1 COM +12VDC COM +12VDC COM +12VDC 7 J15 J14 J10 CATALYST FLUSH CATALYST 1 CATALYST 2 CATALYST 3 CATALYST 4 COLOR 9 COLOR 10 COLOR 11 COLOR 12 1 CABLE (16V426) 12 34 5 MANIFOLD COLOR 13 COLOR 14 COLOR 15 COLOR 16 COLOR 17 COLOR 18 COLOR 19 COLOR 20 COLOR 21 12 34 5 COLOR CHANG E MODULE 8 (COLORS 41 THRU 48) +12VDC COM +12VDC COM +12VDC COM 1 2 3 4 5 6 J8 +12VDC COM +12VDC COM +12VDC COM 1 2 3 4 5 6 J15 +12VDC COM +12VDC COM +12VDC COM 1 2 3 4 5 6 MANIFOLD 6 5 4 3 2 1 COM +12VDC COM +12VDC COM +12VDC J16 6 5 4 3 2 1 COM +12VDC COM +12VDC COM +12VDC J10 6 5 4 3 2 1 COM +12VDC COM +12VDC COM +12VDC J9 7 J14 COLOR 22 COLOR 23 COLOR 24 COLOR 25 COLOR 26 COLOR 27 COLOR 28 COLOR 29 COLOR 30 1 CABLE (16V426) 54 3 2 1 5 4 3 2 1 BOOTH CONTROL (24M731) Figure 30 Schéma électrique, feuille 3, zone dangereuse 48 3A5216H Schémas électriques Modèles à deux panneaux (AC1002, AC2002, AC3002, AC4002) REMARQUE :Le schéma électrique illustre toutes les extensions de câblage possibles dans un appareil ProMix PD2K : modèles AC1002 et AC2002. Certains composants montrés ne sont pas présents dans tous les systèmes. REMARQUE : Pour une liste avec les options de câble, voir Modules et câbles en option, page 55. CABLE 16H078 RELAY 2 PUMP OUTLET TRANSDUCER (16P289, 16P290) MAC SERIES 46 SOLENOID (16P812) PUMPV/PFOR FLUID REG. UP DOWN FLOW SENSOR (120278) OR G3000 ME TER (239716, 258718 16M510, 16M519) ENCODERAND MOT OR (16P036, 16P037) WIRE HARNESS (24P684, 24P685) PUMP INLET TRANSDUCER (16P289, 16P290) PUMP OUTLET TRANSDUCER (16P289, 16P290) PUMPV/PFOR FLUID REG. MAC SERIES 46 SOLENOID (16P812) PUMP INLET TRANSDUCER (16P289, 16P290) CABLE (16T280) BARRIER BOARD (248192) UP DOWN FLOW SENSOR (120278) OR G3000 ME TER (239716, 258718 16M510, 16M519) CATALYST CHANGE MODULE 6 6 (24N935) CATALYST CHANGE MODULE 5 6 (24N935) COLOR CHANGE MODULE 4 6 (24N935) GFBPRESS. SW. 1 (121323) GFBPRESS. SW. 2 (121323) AIR CONTROL MODULE (26A231) SOLVENT CUTOFF VALVE (121324) SOLVENT CUTOFF VALVE (121324) SWITCH (120278) SOLVENT FLOW INPUTS SWITCH (120278) SWITCH (120278) SWITCH (120278) SAFETY INTERLOCK SWITCH CABLE (121003) 3 ADV ANCED DISPLA Y MODULE (24E451) COLOR CHANGE MODULE 7 (24R219) 7 COLOR CHANGE MODULE 8 (24R219) 7 4 CABLE (16T659) FAN (24P658) BREAKOUT MODULE PUMP 3 (24N527) ENCODERAND MOT OR (16P036, 16P037) WIRE HARNESS (24P684, 24P685) SPLITTER (16P243) GCA MODUL E EFCM (24N913) 17L058 SOLVENT METER 2 (258718) FAN (24P658) CABLE (15V206) GFBVALVE 1 (121324) GFBVALVE 2 (121324) PLC DISCRETE 1 (4-20mA) SOLVENT METER 1 (258718) UP DOWN 2 AIR FLOW SW. 2 (119159) PLC DISCRETE 2 (4-20mA) UP DOWN CABLE 126232 OR 17N315 BREAKOUT MODULE PUMP 4 (24N527) MAC SERIES 46 SOLENOID (16P812) CABLE 126232 OR 17N315 PUMP OUTLET TRANSDUCER (16P289, 16P290) BREAKOUT MODULE PUMP 2 (24N527) PUMP OUTLET TRANSDUCER (16P289, 16P290) PUMP INLET TRANSDUCER (16P289, 16P290) MAC SERIES 46 SOLENOID (16P812) PUMP INLET TRANSDUCER (16P289, 16P290) ENCODERAND MOT OR (16P036, 16P037) WIRE HARNESS (24P684, 24P685) CABLE (15V206) CABLE 15V819 16T072 FAN (24P658) BREAKOUT MODULE PUMP 1 (24N527) ENCODERAND MOT OR (16P036, 16P037) WIRE HARNESS (24P684, 24P685) 2 AIR FLOW SW. 1 (119159) CAN IS BOARD (24M485) FAN (24P658) CABLE (15V206) 3 CABLE (121227) 16W159 16W159 16W159 16W159 TERMINAL BLOCK WITH FUSES POWER IN 2 5 2 RELAY 1 TERMINAL BLOCK (114095) AWI GATEWAY (24R910) COLOR CHANGE MODULE 3 6 (24N935) LINE FIL TER (16V446) 3 CABLE (121001) CABLE (15V206) 48V-10APOWER SUPPLY (16U820) 3 CABLE (121227) 5 24V POWER SUPPLY (16T660) COLOR CHANGE MODULE 2 6 (24N935) COLOR CHANGE MODULE 1 6 (24N935) INTEGRA TION GATEWAY 2 POSITION SWITCH (16U725) CABLE 16T658 2 CABLE (15V206) 2 CABLE (15V206) POWERMODULE (26A189) 1 CABLE (16V429) LIGHT TOWER (15X472) 1 BOOTHCONTROL (24M731) CABLE (16V426) WITH SHUNT (17M540) 1 CABLE (16V426) BOOTH CONTROL (24M731) HAZARDOUS LOCA TION NON-HAZARDOUS LOCA TION Figure 31 Schéma électrique, feuille 1 3A5216H 49 Schémas électriques UNUSED UNUSED 2 UNUSED CABLE (15V206) 3 CABLE (121227) 1 2 3 4 5 CANIS BOARD 2 (NON IS) (IS) 4 SPLITTER (17L058) SPLITTER (16P243) UNUSED (121227) 3 P3 1 2 3 4 5 P4 (121001) INTEGRA TION GATEWAY 5 1 2 3 4 5 8 3 1 2 3 +24VDC COM +24VDC SOLVENTCUTOFF VALVE 2 (121324) COM GREEN/BLACK +24VDC ORANGE/BLACK COM GFBOUTPUT VALVE 1 BLUE/BLACK +24VDC RED/WHITE COM GFBOUTPUT VALVE 2 UNUSED SIG SAFETYINTERLOCK SWITCH COM UNUSED J5 J4 1 2 3 4 5 6 7 8 9 10 11 12 6 1 2 3 4 5 6 7 8 9 10 11 12 7 1 2 3 4 5 6 7 8 9 10 11 12 9 1 2 3 4 5 GCAMODULE EFCM (24N913) 5 SOLVENTCUTOFF VALVE 1 (121324) 123 5 1 4 3 2 BARRI ER BOARD (248192) UNUSED 54 3 2 1 UNUSED UNUSED 1 2 3 4 5 10 12345 CABLE (16T280) 1 1 2 3 4 5 1 2 3 4 5 CABLE 3 (24M485) 12345 1 2 3 4 5 AWI GATEWAY (24R910) 1 UNUSED UNUSED 2X CABLE (16V429) 16T072 12345 12345 P4 P3 CABLE 5 4 3 2 1 25 PIN D-SUB CABLE(16T659) 4 GROUND BAR 24V POWER SUPPLY (16T660) 1 BREAKOUT MODULEUMP P 1 (24N527) 3 2 12345 1234 4 7 6 5 1 2 3 45 12345 1234 1 BREAKOUT MODULE PUMP 2 (24N527) 12 34 8 12 34 5678 3 2 12345 1234 4 12345 7 6 5 12345 1234 12 34 8 12 34 5678 BLACK RED RED +48V COM +48V COM RED BLACK RED BLACK FAN PUMP 2 (24P658) RED PWR WHITE SIG BLACK COM GRN SHIELD PUMP2 MANIFOLD SOLVENT METER1 (258718) GND SCREW BLACK RED BLACK N LINE FILTER (16V446) +24VDC COM +24VDC COM UP PUMP1 MANIF OLD DOWN OUTLET TRANSDUCER PUMP 2 (16P289 OR 16P290) INLET TRANSDUCER PUMP 2 (16P289 OR 16P290) RED BLACK RED BLACK FAN PUMP 1 (24P658) +24VDC COM +24VDC COM SEE DET AILAOR B CABLE (126232 OR 17N315) RED L CABLE (126232 OR 17N315) + - + - +- + 4 3 2 1 BLACK CABLE (16T658) WHITE BLACK N04 N04 BROWN (UNUSED) DRAIN (UNUSED) BLUE BLACK ENCODER/MOT OR AND WIRE HARNESS PUMP2 MAC SERIES 46 (16P812 QTY 2) 2 POSITION SWITCH (16U725) 15 RELA Y A1 1 18 A2 RED PWR WHITE SIG BLACK COM GRN SHIELD POWER MODULE (26A189) N (BLUE) L (BROWN) N03 N03 15 RELA Y A1 2 18 A2 BROWN (UNUSED) DRAIN (UNUSED) BLUE BLACK UP SEE DET AILAOR B --++ DOWN ENCODER/MOT OR AND WIRE HARNESS PUMP1 MAC SERIES 46 (16P812 QTY 2) GRND 48V-10A POWER SUPPLY (16U280) OUTLET TRANSDUCER PUMP 1 (16P289 OR 16P290) N L INLET TRANSDUCER PUMP 1 (16P289 OR 16P290) +48V COM +48V COM GRND (GRN/YEL) SOLVENT METER2 (258718) GND SCREW TWISTED PAIR CABLE (16W159) TWISTEDPAIR CABLE (16W159) MOTOR GROUND SCREW MOTOR MOUNTING SCREW 123456789 PUMP ENCODER AND MOTOR (16P037) 12 10 MOTOR MOUNTING SCREW 1 2 3 4 5 67 8 9 1011 12 UNUSED UNUSED UNUSED DRAIN/FOIL UNUSED UNUSED DRAIN/FOIL 1011 12 UNUSED UNUSED 1 2 34 5 6 7 8 9 DRAIN/FOIL UNUSED UNUSED UNUSED UNUSED DRAIN/FOIL DRAIN/FOIL L N GND 3 1234 WIRE HARNESS (24P685) 123456789 UNUSED UNUSED 12345 1234 WIRE HARNESS (24P684) UNUSED UNUSED 1 2 34 5 BREAKOUT MODULE (24N527) 2 3 UNUSED UNUSED UNUSED 2 UNUSED UNUSED UNUSED UNUSED UNUSED BREAKOUT MODULE (24N527) TERMI NAL BLOCK (114095) UNUSED L N GND POWER IN DETAIL B, HIGH PRESSURE PUMPS (24M707, 24M715, 24T800) DETAILA, LOW PRESSURE PUMPS (24M706, 24M714, 24T799) UNUSED UNUSED UNUSED UNUSED CABLE (16H078) WHITE GRN BLACK L GND N 10 PUMP ENCODER AND MOTOR (16P036) Figure 32 Schéma électrique, feuille 2, partie 1 SUITE EN PAGE SUIVANTE 50 3A5216H Schémas électriques 8 GCAMODULE EFCM (24N913) 7 SIG COM SIG COM SIG COM SIG COM SIG COM SIG COM 1 2 3 4 5 6 7 8 9 10 11 12 PLC DISCRETE 4-20mAINPUT 1 PLC DISCRETE 4-20mACOMMON 1 PLC DISCRETE 4-20mAINPUT 2 PLC DISCRETE 4-20mACOMMON 2 UNUSED UNUSED UNUSED UNUSED SIG ORANGE COM BLUE SIG WHITE/BLACK COM RED/BLACK 5 9 1 2 3 4 AIR FLOW SWITCH 1 1 2 3 4 5 6 7 8 9 10 11 12 1 2 3 4 5 BLACK WHITE RED GREEN AIR FLOW SWITCH 2 SOLVENT FLOW SW. 1 (120278) LEFT BRKT SOLVENT FLOW SW. 2 (120278) LEFT BRKT SOLVENT FLOW SW. 3 (120278) RIGHT BRKT TERMINAL BLOCKS GFB INPUT PRESSURE SWITCH 1 1 2 3 4 5 1 2 3 4 5 ADVANCED DISPLAY MODULE (24E451) 1 2 3 4 5 6 7 8 9 10 11 12 BLAC K WHITE RED GREEN ORANGE BLUE WHITE/BLACK RED/BLACK GREEN/BLACK ORANGE/BLACK BLUE/BLACK RED/WHITE CABLE 15V819 GFB INPUT PRESSURE SWITCH 2 CABLE (121003) AIR CONTROL MODULE (26A231) SOLVENT FLOW SW. 4 (120278) RIGHT BRKT LIGHT TOWER (15X472) + SIG - COM + SIG - COM + SIG - COM + SIG - COM + 24VDC - COM + 24VDC - COM AIR FLOW SWITCH 1 119159 AIR FLOW SWITCH 2 119159 GFB INPUT PRESSURE SWITCH 1 121323 GFB INPUT PRESSURE SWITCH 2 121323 RED BLAC K RED BLAC K GFB OUTPUT VALVE 1 121324 GFB OUTPUT VALVE 2 121324 3 25 PIN D-SUB CABLE (16T659) 1 2 1234 1 BREAKOUT MODULE PUMP 3 (24N527) 4 12345 12345 7 6 5 1234 12 34 8 12 34 5678 2 3 12345 1234 BREAKOUT MODULE PUMP 4 (24N527) 4 12345 5 12345 7 6 1234 12 34 8 12 34 5678 RED PWR WHITE SIG BLACK COM GRN SHIELD DOWN V/P FOR FLUID REG. PUMP 4 UP PUMP 4 MANIFOLD PUMP 3 MANIFOLD G3000 METER PUMP 3 MAC SERIES 46 (16P812 QTY 2) MAC SERIES 46 (16P812 QTY 2) +24VDC COM +24VDC COM OUTLET TRANSDUCER PUMP 4 (16P289 OR 16P290) INLET TRANSDUCER PUMP 4 (16P289 OR 16P290) RED BLACK RED BLACK ENCODER/M OTOR AND WIRE HARNESS PUMP 4 SEE DET AILAOR B FAN PUMP 3 (24P658) RED PWR WHITE SIG BLACK COM GRN SHIELD DOWN V/P FOR FLUID REG. PUMP 3 +24VDC COM +24VDC COM UP OUTLET TRANSDUCER PUMP 3 (16P289 OR 16P290) ENCODER/M OTOR AND WIRE HARNESS PUMP 3 SEE DET AILAOR B INLET TRANSDUCER PUMP 3 (16P289 OR 16P290) +48V COM +48V COM 12345 3 4 +48V COM +48V COM 6 RED BLACK RED BLACK 1 2 3 4 5 6 7 8 9 10 11 12 10 FAN PUMP 4 (24P658) 5 4 3 2 1 1 2 3 4 5 (EITHER, 239716, 258718,16M510, OR 16M519) GND SCREW G3000 METER PUMP 4 (EITHER, 239716, 258718,16M510, OR 16M519) GND SCREW TWISTED PAIR CABLE (16W159) TWISTED PAIR CABLE (16W159) Figure 33 Schéma électrique, feuille 2, partie 2 SUITE EN PAGE SUIVANTE 3A5216H 51 Schémas électriques FROMCAN IS BOARD (24M485) 2 CABLE(15V206) 12 34 5 COLOR CHANGE MODULE 1 (COLORS 1 THRU 8) MAN IFOLD FLUSH COLOR 1 COLOR 2 COLOR 3 COLOR 4 COLOR 5 COLOR 6 COLOR 7 COLOR 8 +24VDC COM +24VDC COM +24VDC COM 1 2 3 4 5 6 +24VDC COM +24VDC COM +24VDC COM 1 2 3 4 5 6 +24VDC COM +24VDC COM +24VDC COM 1 2 3 4 5 6 J8 MAN IFOLD J9 6 5 4 3 2 1 COM +24VDC COM +24VDC COM +24VDC J16 6 5 4 3 2 1 COM +24VDC COM +24VDC COM +24VDC J10 6 5 4 3 2 1 COM +24VDC COM +24VDC COM +24VDC 6 J15 J14 DUMP COLOR 1 COLOR 2 COLOR 3 COLOR 4 COLOR 5 COLOR 6 COLOR 7 COLOR 8 MAN IFOLD *FLUSH COLOR 9 COLOR 10 COLOR 11 COLOR 12 COLOR 13 COLOR 14 COLOR 15 COLOR 16 12 34 5 COLOR CHANGE MODULE 2 (COLORS 9 THRU 16) +24VDC COM +24VDC COM +24VDC COM 1 2 3 4 5 6 +24VDC COM +24VDC COM +24VDC COM 1 2 3 J15 4 5 6 J16 +24VDC COM +24VDC COM +24VDC COM 1 2 3 4 5 6 J10 J9 J8 6 J14 MAN IFOLD MAN IFOLD 6 5 4 3 2 1 COM +24VDC COM +24VDC COM +24VDC 6 5 4 3 2 1 COM +24VDC COM +24VDC COM +24VDC 6 5 4 3 2 1 COM +24VDC COM +24VDC COM +24VDC DUMP* FLUSH COLOR 9 CATALYST 1 COLOR 10 CATALYST 2 COLOR 11 CATALYST 3 COLOR 12 CATALYST 4 COLOR 13 COLOR 14 COLOR 15 COLOR 16 CATALYST CHANGE MODULE 5 (CATALYST 1 THRU 4) +24VDC COM +24VDC COM +24VDC COM 1 2 3 4 5 6 +24VDC COM +24VDC COM UNUSED UNUSED 1 2 3 4 5 6 J15 UNUSED UNUSED UNUSED UNUSED UNUSED UNUSED 1 2 3 4 5 6 J14 J8 COLOR 17 COLOR 18 COLOR 19 COLOR 20 COLOR 21 COLOR 22 COLOR 23 COLOR 24 12 34 5 COLOR CHANGE MODULE 3 (COLORS 17 THRU 24) +24VDC COM +24VDC COM +24VDC COM 1 2 3 4 5 6 J8 +24VDC COM +24VDC COM +24VDC COM 1 2 3 4 5 6 J15 +24VDC COM +24VDC COM +24VDC COM 1 2 3 4 5 6 J14 J9 6 J16 6 5 4 3 2 1 COM +24VDC COM +24VDC UNUSED UNUSED J10 6 5 4 3 2 1 UNUSED UNUSED UNUSED UNUSED UNUSED UNUSED DUMP CATALYST 1 CATALYST 2 CATALYST 3 CATALYST 4 12 34 5 2 CABLE (15V206) 2 CABLE MAN IFOLD J9 COM +24VDC COM +24VDC COM +12VDC 6 12 34 5 *FLUSH MAN IFOLD 6 5 4 3 2 1 MAN IFOLD MAN IFOLD 6 5 4 3 2 1 COM +24VDC COM +24VDC COM +24VDC 6 5 COM +24VDC COM +24VDC COM +24VDC J16 43 2 1 6 5 4 J10 3 2 1 COM +24VDC COM +24VDC COM +24VDC *FLUSH DUMP* COLOR 17 COLOR 25 COLOR 18 COLOR 26 COLOR 19 COLOR 27 COLOR 20 COLOR 28 COLOR 21 COLOR 29 COLOR 22 COLOR 30 COLOR 23 COLOR 24 54 3 2 1 (15V206) 2 CABLE (15V206) 12 34 5 12 34 5 COLOR CHANGE MODULE 4 (COLORS 25 THRU 32) +24VDC COM +24VDC COM +24VDC COM 1 2 3 4 5 6 J8 +24VDC COM +24VDC COM +24VDC COM 1 2 3 4 5 6 J15 +24VDC COM UNUSED UNUSED UNUSED UNUSED 1 2 3 4 5 6 J14 J9 6 J16 J10 MAN IFOLD 6 5 4 3 2 1 COM +24VDC COM +24VDC COM +24VDC 6 5 4 3 2 1 COM +24VDC COM +24VDC COM +24VDC 6 5 4 3 2 1 COM +24VDC UNUSED UNUSED UNUSED UNUSED DUMP* COLOR 25 COLOR 26 COLOR 27 COLOR 28 COLOR 29 COLOR 30 12 34 5 2 CABLE(15V206) Figure 34 Schéma électrique, feuille 3, partie 1 * Peut ne pas être utilisé avec certaines configurations. SUITE EN PAGE SUIVANTE 52 3A5216H Schémas électriques FROMCAN IS BOARD (24M485) 1 CABLE (16V429) NON-HAZARDOUS LOCATION HAZARDOUS LOCATION MANIFOLD COLOR FLUSH COLOR 1 COLOR 2 COLOR 3 COLOR 4 COLOR 5 COLOR 6 COLOR 7 COLOR 8 RED +12VDC BLACK COM RED +12VDC BLACK COM RED +12VDC BLACK COM 1 2 3 4 5 6 RED +12VDC BLACK COM RED +12VDC BLACK COM RED +12VDC BLACK COM 1 2 3 4 5 6 RED +12VDC BLACK COM RED +12VDC BLACK COM RED +12VDC BLACK COM 1 2 3 4 5 6 12 34 5 COLOR CHANGE MODULE 7 (COLORS 6 33 THRU 40) 5 4 J9 3 J8 2 1 7 J15 J16 J14 J10 MANIFOLD COM BLACK +12VDC RED COM BLACK +12VDC RED COM BLACK +12VDC RED CATALYST FLUSH 6 5 4 3 2 1 COM BLACK +12VDC RED COM BLACK +12VDC RED COM BLACK +12VDC RED CATALYST 3 6 5 4 3 2 1 COM BLACK +12VDC RED COM BLACK +12VDC RED COM BLACK +12VDC RED CATALYST 1 CATALYST 2 CATALYST 4 COLOR 9 COLOR 10 COLOR 11 COLOR 12 1 CABLE (16V426) 54 32 1 54 32 1 BOOTH CONTROL (24M731) WITH SHUNT (17M540) MANIFOLD COLOR 13 COLOR 14 17M540 COLOR 15 COLOR 16 COLOR 17 12 34 5 J1 COLOR 18 COLOR 19 COLOR 20 COLOR 21 RED +12VDC BLACK COM RED +12VDC BLACK COM RED +12VDC BLACK COM 1 2 3 4 5 6 RED +12VDC BLACK COM RED +12VDC BLACK COM RED +12VDC BLACK COM 1 2 3 4 5 6 RED +12VDC BLACK COM RED +12VDC BLACK COM RED +12VDC BLACK COM 1 2 3 4 5 6 12 34 5 COLOR CHANGE MODULE 8 (COLORS 41 THRU 48) J8 MANIFOLD 6 5 4 3 2 1 COM BLACK +12VDC RED COM BLACK +12VDC RED COM BLACK +12VDC RED COLOR 22 J9 COM BLACK +12VDC RED COM BLACK +12VDC RED COM BLACK +12VDC RED COLOR 25 J16 6 5 4 3 2 1 J10 6 5 4 3 2 1 COM BLACK +12VDC RED COM BLACK +12VDC RED COM BLACK +12VDC RED 7 J15 J14 COLOR 23 COLOR 24 COLOR 26 COLOR 27 COLOR 28 COLOR 29 COLOR 30 1 CABLE (16V426) 54 3 2 1 5 4 3 2 1 BOOTH CONTROL (24M731) Figure 35 Schéma électrique, feuille 3, partie 2 SUITE EN PAGE SUIVANTE 3A5216H 53 Schémas électriques +24VDC COM +24VDC COM +24VDC COM CATALYST CHANGE MODUL E6 (CA TALYST 1 2 3 THRU 4) 3 J9 4 J8 5 6 6 5 4 3 2 1 COM +24VDC COM +24VDC COM +24VDC UNUSED UNUSED UNUSED UNUSED UNUSED UNUSED 1 2 3 4 5 6 J16 6 5 4 3 2 1 UNUSED UNUSED UNUSED UNUSED UNUSED UNUSED UNUSED UNUSED UNUSED UNUSED UNUSED UNUSED 1 2 3 4 5 6 J10 6 5 4 3 2 1 UNUSED UNUSED UNUSED UNUSED UNUSED UNUSED 6 5 4 3 2 1 COM +24VDC COM +24VDC COM +24VDC J16 6 5 4 3 2 1 UNUSED UNUSED UNUSED UNUSED UNUSED UNUSED J10 6 5 4 3 2 1 UNUSED UNUSED UNUSED UNUSED UNUSED UNUSED MANIFOLD FLUSH CATALYST 3 CATALYST 4 MANIFOLD 6 J15 J14 DUMP CATALYST 3 CATALYST 4 2 CABLE (15V206) 12 34 5 +24VDC COM +24VDC COM +24VDC COM 54 3 2 1 CATALYST CHANGE MODUL E5 1 (CATALYST 1 THRU 2) 2 3 J9 4 J8 5 6 UNUSED UNUSED UNUSED UNUSED UNUSED UNUSED 1 2 3 4 5 6 UNUSED UNUSED UNUSED UNUSED UNUSED UNUSED 1 2 3 4 5 6 MANIFOLD FLUSH CATALYST 1 CATALYST 2 6 J15 J14 MANIFOLD DUMP CATALYST 1 CATALYST 2 (15V206) 2 CABLE 12 34 5 12 34 5 COLOR CHANGE MODUL E4 (COLORS 25 THRU 32) ALTERNATE CONFIGURATION FOR CATALYST CHANGE CONTROL INNON-HA ZARDOUS LOCATION Figure 36 Schéma électrique, feuille 4, configuration alternée pour le contrôle du changement de catalyseur 54 3A5216H Modules et câbles en option Modules et câbles en option REMARQUE : La longueur totale de tous les câbles utilisés dans le système ne peut pas dépasser les 45 m (150 pi.). Voir le Schémas électriques, page 43. Câbles CAN M12, pour endroits dangereux REMARQUE : La longueur totale d'un câble utilisé dans la zone dangereuse ne doit pas dépasser 36 m (120 pi.). Réf. Câble Longueur ft (m) 16V423 2.0 (0.6) 16V424 3.0 (1.0) 16V425 6.0 (2.0) 16V426 10.0 (3.0) 16V427 15.0 (5.0) 16V428 25.0 (8.0) 16V429 50.0 (16.0) 16V430 100.0 (32.0) 15U531 15U532 15V205 15V206 15V207 15V208 15U533 15V213 Câbles CAN M12, uniquement pour endroits sans danger 2.0 (0.6) 3.0 (1.0) 6.0 (2.0) 10.0 (3.0) 15.0 (5.0) 25.0 (8.0) 50.0 (16.0) 100.0 (32.0) Câbles CAN, uniquement pour endroits sans danger Réf. Câble Longueur ft (m) 125306 1.0 (0.3) 123422 1.3 (0.4) 121000 1.6 (0.5) 121227 2.0 (0.6) 121001 3.0 (1.0) 121002 5.0 (1.5) 121003 10.0 (3.0) 120952 13.0 (4.0) 121201 20.0 (6.0) 121004 25.0 (8.0) 121228 50.0 (15.0) 3A5216H Câbles D-SUB à 25 broches, uniquement pour endroits sans danger 16T659 2.5 (0.8) 16V659 6.0 (1.8) Voir 8. Sélection des options de communication, page 26. Alternatifs pour les modules de changement de couleur selon la référence (configuration par défaut), uniquement pour endroits sans danger Description Réf. Module 24T557 2 couleurs/2 catalyseurs 24T558 4 couleurs/4 catalyseurs 24T559 6 couleurs/6 catalyseurs 24T560 8 couleurs/8 catalyseurs Alternatifs pour les modules de changement de couleur selon la référence (configuration par défaut), uniquement pour endroits dangereux 24T571 2 couleurs/2 catalyseurs 24T572 4 couleurs/2 catalyseurs 24T573 6 couleurs/2 catalyseurs 24T574 8 couleurs/2 catalyseurs, 13-24 couleurs 24T774 12 couleurs/2 catalyseurs 24T775 4 couleurs/4 catalyseurs 24T776 6 couleurs/4 catalyseurs 24T777 8 couleurs/4 catalyseurs 24T778 12 couleurs/4 catalyseurs, 13-30 couleurs 24T779 13-18 couleurs 55 Remarques Remarques 56 3A5216H Dimensions Dimensions Figure 38 Figure 37 Figure 39 A 1659 mm (65,3 po) 3A5216H B avec l'ADM sans l'ADM 368 mm (14,5 po) 282 mm (11,12 po) C D E F G H J 572 mm (22,5 po) 489 mm (19,26 po) 57 mm (2,25 po) 457 mm (18,0 po) 438 mm (17,26 po) 13 mm (0,52 po) Minimum 152 mm (6 po.) pour la surface de montage et fixation 57 Données techniques Données techniques Doseur à déplacement positif Impérial Métrique Systèmes de pulvérisation pneumatique AC1000 et AC1002 300 psi 2,1 MPa ; 21 bars Systèmes de pulvérisation à commande pneumatique AC2000 et AC2002 1500 psi 10,5 MPa ; 105 bars Pression de service maximale d'air : 100 psi 0,7 MPa ; 7,0 bars Alimentation en air : 85–100 psi Pression de service maximale du produit : 0,6–0,7 MPa ; 6,0–7,0 bar) Taille de l’entrée du filtre à air pour une logique d’air : 1/4 npt(f) Taille de l’entrée du filtre à air pour l’air d’atomisation : 3/8 npt(f) Filtration d'air pour logique d'air : Filtration de 5 microns (minimum) requise, air sec et propre Filtration d'air pour air d'atomisation (fournie par l'utilisateur) : Filtration de 30 microns (minimum) requise, air sec et propre Plage des rapports de mélange : Produits utilisés : 0,1:1 — 50:1, ±1 % Un ou deux composants : • Peintures au solvant et à l'eau • polyuréthanes • Peintures époxy • Vernis à catalyse acide • Isocyanates sensibles à l'humidité Plage de viscosité du produit : 20 à 5000 centipoises Filtration du produit (fournie par l'utilisateur) : 100 mesh minimum Débit de produit maximal : 800 cc/minute (en fonction de la viscosité du produit) Taille de sortie de produit : 1/4 npt(m) Exigences en alimentation électrique externe : 90 - 250 Vca, 50/60 Hz, 7 A maximum Disjoncteur de 15 A maximum obligatoire Calibre de câble d'alimentation électrique de 8 à 14 AWG Plage de température de fonctionnement : 36 à 122°F 2 à 50°C Plage de température de stockage : -4 à 158°F -20 à 70°C 195 lb 88 kg Poids (approx.) du modèle de base : Caractéristiques sonores : Inférieure à 75 dB(A) Pièces en contact avec le produit : 58 3A5216H Données techniques Doseur à déplacement positif Impérial Métrique AC1000, AC1002, AC3000 et AC3002 Inox 303, 304, 17–4PH, carbure de tungstène (avec anneau en nickel), perfluoroélastomère, PTFE, PPS, UHMWPE AC2000, AC2002, AC4000 et AC4002 Acier inoxydable 17–4PH et 316, PEEK, perfluoroélastomère, PTFE, PPS, UHMWPE 3A5216H 59 Garantie standard de Graco Graco garantit que tout l’équipement mentionné dans le présent document, fabriqué par Graco et portant son nom, est exempt de défaut de matériel et de fabrication à la date de la vente à l’acheteur et utilisateur initial. Sauf garantie spéciale, élargie ou limitée, publiée par Graco, Graco réparera ou remplacera, pendant une période de douze mois à compter de la date de la vente, toute pièce de l’équipement jugée défectueuse par Graco. Cette garantie s'applique uniquement si le matériel est installé, utilisé et entretenu conformément aux recommandations écrites de Graco. Cette garantie ne couvre pas et Graco ne sera pas tenu pour responsable de l’usure et de la détérioration générales ou de tout autre dysfonctionnement, des dégâts ou de l’usure causés par une mauvaise installation, une mauvaise application ou utilisation, une abrasion, de la corrosion, un entretien inapproprié ou incorrect, une négligence, un accident, une modification ou une substitution par des pièces ou composants qui ne portent pas la marque Graco. Graco ne sera également pas tenu pour responsable en cas de mauvais fonctionnement, dommage ou usure dû à l’incompatibilité de l’équipement Graco avec des structures, accessoires, équipements ou matériaux non fournis par Graco ou dû à une mauvaise conception, fabrication, installation, utilisation ou un mauvais entretien desdits structures, accessoires, équipements ou matériels non fournis par Graco. Cette garantie sera appliquée à condition que l’équipement objet de la réclamation soit retourné en port payé à un distributeur agrée de Graco pour une vérification du défaut signalé. Si le défaut est reconnu, Graco réparera ou remplacera gratuitement toutes les pièces défectueuses. L’équipement sera renvoyé à l’acheteur original en port payé. Si l’examen de l’équipement n’indique aucun défaut matériel ou de fabrication, les réparations seront effectuées à un coût raisonnable pouvant inclure le coût des pièces, de la main-d’œuvre et du transport. CETTE GARANTIE EST UNE GARANTIE EXCLUSIVE ET REMPLACE TOUTE AUTRE GARANTIE, EXPRESSE OU IMPLICITE, COMPRENANT, MAIS SANS S'Y LIMITER, UNE GARANTIE MARCHANDE OU UNE GARANTIE DE FINALITÉ PARTICULIÈRE. La seule obligation de Graco et le seul recours de l’acheteur pour toute violation de la garantie seront tels que décrits ci-dessus. L’acheteur convient qu’aucun autre recours (pour, mais sans s’y limiter, des dommages indirects ou consécutifs de manque à gagner, perte de marché, dommages corporels ou matériels ou tout autre dommage indirect ou consécutif) ne sera possible. Toute action pour violation de la garantie doit être intentée dans les deux (2) ans à compter de la date de vente. GRACO NE GARANTIT PAS ET REFUSE TOUTE GARANTIE RELATIVE À LA QUALITÉ MARCHANDE ET À UNE FINALITÉ PARTICULIÈRE EN RAPPORT AVEC LES ACCESSOIRES, ÉQUIPEMENTS, MATÉRIAUX OU COMPOSANTS VENDUS MAIS NON FABRIQUÉS PAR GRACO. Les articles vendus, mais non fabriqués par Graco (tels que les moteurs électriques, interrupteurs, tuyaux, etc.) sont couverts par la garantie, s’il en existe une, de leur fabricant. Graco fournira à l’acheteur une assistance raisonnable pour toute réclamation faisant appel à ces garanties. En aucun cas, Graco ne sera tenu pour responsable de dommages indirects, particuliers ou consécutifs résultant de la fourniture par Graco de l’équipement ci-dessous ou de garniture, de la performance, ou utilisation de produits ou d’autres biens vendus au titre des présentes, que ce soit en raison d’une violation contractuelle, violation de la garantie, négligence de Graco, ou autre. FOR GRACO CANADA CUSTOMERS The Parties acknowledge that they have required that the present document, as well as all documents, notices and legal proceedings entered into, given or instituted pursuant hereto or relating directly or indirectly hereto, be drawn up in English. Les parties reconnaissent avoir convenu que la rédaction du présent document sera en anglais, ainsi que tous documents, avis et procédures judiciaires exécutés, donnés ou intentés, à la suite de ou en rapport, directement ou indirectement, avec les procédures concernées. Informations concernant Graco Pour les informations les plus récentes sur les produits de Graco, consulter le site Internet www.graco.com. Pour toutes les informations concernant les brevets, consultez la page www.graco.com/patents. commande, contacter le distributeur Graco local ou téléphoner pour connaître le Pour passer une commande distributeur le plus proche. Téléphone : 612-623-6921 ou appel gratuit : 1-800-328-0211 Fax : 612-378-3505 Toutes les données écrites et visuelles contenues dans ce document sont le reflet des dernières informations sur le produit disponibles au moment de la publication. Graco se réserve le droit de procéder à des modifications à n'importe quel moment et sans préavis. Traduction des instructions originales. This manual contains French. MM 332458 Siège social de Graco : Minneapolis Bureaux à l’étranger : Belgique, Chine, Japon, Corée GRACO INC. ET FILIALES • P.O. BOX 1441 • MINNEAPOLIS MN 55440-1441 • USA 2014,, Graco Inc. Tous les sites de fabrication de Graco sont certifiés ISO 9001. Copyright 2014 www.graco.com Révision H, février 2019