Krone BigPack 12130 XC Mode d'emploi
PDF
Download
Document
Instructions de service 150 000 051 02 FR Presse à grosses balles Big Pack 12130 Big Pack 12130 / XC (à partir du n° machine 770 932) Déclaration de conformité CE selon la directive européenne 98/37/CE Nous Maschinenfabrik Bernard Krone GmbH domiciliée Heinrich-Krone-Str. 10 à D-48480 Spelle déclarons, en toute responsabilité, que le produit Types : Presse à grosses balles Krone Big Pack 12130 ; Big Pack 12130XC auquel se rapporte cette déclaration est conforme aux exigences fondamentales concernant la sécurité et la santé spécifiées dans la directive CE sur les machines 98/37/CE. Spelle, le 28.06.05 (Dr.-Ing. Josef Horstmann, directeur) (pp. Dr.-Ing. Klaus Martensen, responsable construction et développement) Cher client, Chère cliente, Vous avez entre les mains les instructions de service du produit KRONE que vous venez d’acheter. Ces instructions de service contiennent des informations importantes pour l’utilisation conforme et la commande en toute sécurité de la machine. Si, pour une raison quelconque, une partie ou la totalité de ces instructions de service n’était plus utilisable, vous pouvez obtenir un nouvel exemplaire des ces instructions de service en indiquant le numéro figurant au verso. Table des matières Table des matières 1 Généralités......................................................................................... I -1 1.1 1.2 1.3 1.4 1.4.1 1.4.2 1.5 1.6 1.7 1.7.1 1.7.2 1.7.3 1.7.4 But d’utilisation ........................................................................................................ Conformité d’utilisation ............................................................................................ Indications concernant les demandes de renseignements et les commandes ........ Caractéristiques techniques .................................................................................... Big Pack 12130 / XC ............................................................................................... Lubrifiants ................................................................................................................ Conditions de l’attelage sur le tracteur .................................................................... Description technique générale............................................................................... Vues d’ensemble ..................................................................................................... Face gauche de la presse à grosses balles Big Pack avec essieu tandem ............. Face droite de la presse à grosses balles Big Pack avec essieu tandem ................ Fonctionnement du système de transport VFS ........................................................ Description fonctionnelle de la presse à grosses balles .......................................... 2 Sécurité .............................................................................................. II -1 2.1 2.2 2.2.1 2.2.2 2.2.3 2.2.4 2.2.5 2.2.6 2.2.7 2.2.8 2.2.9 2.2.10 2.2.11 2.3 2.3.1 2.3.2 2.4.3 2.4 2.4.1 2.4.2 Caractéristique des consignes de sécurité figurant dans ces instructions ............... II -1 Consignes de sécurité et règlements de prévoyance contre les accidents ............. II -1 Qualification et formation du personnel ................................................................... II -1 Dangers liés au non-respect des consignes de sécurité ......................................... II -1 Maîtrise des risques ................................................................................................ II -1 Prescriptions de sécurité et de prévoyance des accidents ...................................... II -2 Appareils tractés ...................................................................................................... II -3 Utilisation de l’arbre de prise de force ..................................................................... II -3 Installation hydraulique ........................................................................................... II -3 Pneumatiques ......................................................................................................... II -4 Maintenance ............................................................................................................ II -4 Transformations réalisées par l’exploitant et fabrication de pièces de rechange ..... II -4 Modes d’exploitation non autorisés ......................................................................... II -4 Introduction .............................................................................................................. II -6 Emplacement des autocollants de sécurité sur la machine ..................................... II -6 Position des panneaux d’avertissement généraux sur la machine .......................... II -9 Extincteur .............................................................................................................. II -10 Consignes de sécurité spéciales........................................................................... II -10 Echelle de montée ................................................................................................ II -10 Garde-fou de sécurité ............................................................................................ II -10 I -1 I -1 I -1 I -2 I -2 I -3 I -4 I -5 I -6 I -6 I -7 I -8 I -9 3. Mise en service et transport ........................................................... III -1 3.1 3.2 3.2.1 3.2.2 3.2.3 3.2.4 3.2.5 3.3 3.4 Consignes de sécurité ............................................................................................ III -1 Commande générale .............................................................................................. III -1 Béquille de support ................................................................................................ III -1 Béquille de support hydraulique (en option)........................................................... III -2 Frein parking .......................................................................................................... III -2 Frein de blocage du volant ..................................................................................... III -3 Ajustage de la hauteur du timon ............................................................................. III -3 Attelage au tracteur ................................................................................................ III -4 Arbre à cardan principal ......................................................................................... III -4 1 Table des matières 3.4.1 3.4.2 3.5 3.5.1 3.5.2 3.5.3 3.5.4 3.5.5 3.5.6 3.6 3.6.1 3.6.2 3.6.3 3.6.4 3.7 3.7.1 3.7.2 3.7.3 3.7.3.1 3.8 Ajustage de l’arbre à cardan principal .................................................................... III -4 Montage côté tracteur ............................................................................................. III -5 Raccordement hydraulique, d’air comprimé et électrique ....................................... III -6 Frein hydraulique (en fonction des spécifications nationales) ................................ III -6 Raccordement hydraulique pour le blocage de l’essieu mené (option) .................. III -6 Raccordement Load-Sensing (option) .................................................................... III -7 Frein à air comprimé ............................................................................................... III -8 Fixations des flexibles hydrauliques ...................................................................... III -8 Câbles de liaison électriques ................................................................................. III -9 Remise en service après un arrêt prolongé .......................................................... III -10 Consignes de sécurité .......................................................................................... III -10 Généralités ........................................................................................................... III -10 Accouplement de surcharge au niveau du volant ................................................. III -10 Stockage pendant l’hiver ...................................................................................... III -11 Transport .............................................................................................................. III -12 Préparatifs pour le déplacement sur route ............................................................ III -12 Manœuvre ............................................................................................................ III -13 Essieu directeur mené (option) ............................................................................. III -14 Manœuvre de la machine sans raccord hydraulique ............................................ III -14 Immobiliser la presse à grosses balles................................................................. III -15 4 Unité de commande confort Machine medium / confort ............................................................. IV -1 4.1 4.2 4.3 4.4 4.5 4.5.1 4.5.2 4.6 4.7 4.8 4.8.1 4.8.2 4.9 4.9.1 4.9.2 4.9.3 4.9.4 4.9.5 4.9.6 4.9.7 4.9.8 4.9.9 4.9.10 4.9.11 4.9.12 4.9.13 4.9.14 Description générale ............................................................................................. IV -1 Montage ................................................................................................................ IV -2 Unité de commande .............................................................................................. IV -4 Ordre de marche .................................................................................................... IV -5 Mode manuel......................................................................................................... IV -6 Ecran initial Mode manuel 1/2 ............................................................................... IV -6 Ecran initial Mode manuel 2/2 ............................................................................... IV -8 Mode automatique ............................................................................................... IV -13 Boutons-poussoirs sur la machine ...................................................................... IV -14 Description de la compression des balles ........................................................... IV -15 Canal de pressage vide ...................................................................................... IV -15 Canal de pressage plein ..................................................................................... IV -15 Niveau de menu .................................................................................................. IV -16 Appeler le niveau de menu.................................................................................. IV -16 Menu principal 1 « Réglages » ............................................................................ IV -17 Menu 1-1 « Valeur de correction de longueur des balles » .................................. IV -18 Menu 1-2 « Signal de noueur » ........................................................................... IV -19 Menu 1-3 « Sensibilité indicateur de direction » .................................................. IV -20 Menu 1-4 « Contraste » ....................................................................................... IV -21 Menu 1-5 «Graissage centralisé» ........................................................................ IV -22 Menu principal 2 « Compteurs » .......................................................................... IV -24 Menu 2-1 « Compteur client » ............................................................................. IV -24 Menu 2-2 « Compteur total » ............................................................................... IV -26 Menu principal 4 « Service » ............................................................................... IV -27 Menu 4-2 «Test manuel des capteurs» ................................................................ IV -27 Menu 4-4 «Test manuel des actionneurs» ........................................................... IV -31 Menu 4-5 « Alarmes actuelles » .......................................................................... IV -34 2 Table des matières 4.9.15 4.9.16 4.9.17 4.10 4.11 4.12 4.12.1 4.12.2 4.12.3 Menu principal 5 « Information » ......................................................................... IV -35 Fenêtre d’information .......................................................................................... IV -35 Menu principal 6 « Installateur » .......................................................................... IV -36 Message d’alarme ............................................................................................... IV -37 Messages d’alarme ............................................................................................. IV -38 Commande ISO ................................................................................................... IV -44 Principe de fonctionnement ................................................................................. IV -44 Montage .............................................................................................................. IV -44 Fonctions différentes par rapport à la commande confort KRONE ...................... IV -45 5 Ce chapitre est resté délibérément vierge ! .............................. VIII -1 6 Ce chapitre est resté délibérément vierge ! .............................. VIII -1 7 Travail avec la presse à grosses balles ...................................... VII -1 7.1 7.2 7.3 7.4 7.5 7.6 7.7 7.7.1 7.7.2 7.8 7.8.1 7.8.2 7.8.3 7.9 Consignes de sécurité .......................................................................................... VII -1 Ramasseur ........................................................................................................... VII -1 Mécanisme de coupe XC ..................................................................................... VII -3 Régulation de la force de compression ................................................................ VII -6 Vider le canal de pressage ................................................................................... VII -7 Rampe d’éjection à rouleaux à commande hydraulique (option) ......................... VII -7 Réglage de la longueur des balles ....................................................................... VII -8 Réglage de longueur manuel ............................................................................... VII -8 Réglage électrique de longueur (option) .............................................................. VII -8 Ficelle de liage ..................................................................................................... VII -9 Indication électrique signalant un problème au niveau de la ficelle ..................... VII -9 Affichage du parcours de la ficelle de dessus (noueur double) ............................ VII -9 Déclencher manuellement le processus de nouage .......................................... VII -10 Entraînements .................................................................................................... VII -11 8. Réglages ........................................................................................ VIII -1 8.1 8.2 8.2.1 8.2.2 8.2.3 8.2.3.1 8.2.4 8.3 8.3.1 8.3.2 8.3.3 8.3.4 8.4 8.5 8.5.1 8.5.2 8.6 8.6.1 8.6.2 Consignes de sécurité ......................................................................................... VIII -1 Dispositif de liage ................................................................................................ VIII -1 Ficelle de liage .................................................................................................... VIII -1 Réglage des aiguilles .......................................................................................... VIII -4 Barre à ficelle ...................................................................................................... VIII -9 Réglage de la barre à ficelle (noueur double) ..................................................... VIII -9 Frein de ficelle ................................................................................................... VIII -11 Noueur .............................................................................................................. VIII -13 Noueur double ................................................................................................... VIII -13 Retenue de la ficelle .......................................................................................... VIII -14 Réglage de la force de retenue du reteneur de ficelle (6) .................................. VIII -15 Levier du couteau .............................................................................................. VIII -15 Réglage du piston de presse ............................................................................. VIII -16 Réglage de l’empaqueteur par rapport au piston de presse .............................. VIII -18 Contrôle de l’enclenchement de l’accouplement de l’empaqueteur .................. VIII -18 Réglage de l’empaqueteur ................................................................................ VIII -18 Système de remplissage variable VFS .............................................................. VIII -20 Montage du râteau de retenue ........................................................................... VIII -20 Réglage de l’accouplement Réglage de l’accouplement (en position neutre) .. VIII -20 3 Table des matières 8.6.2.1 8.6.3 8.6.4 8.6.5 8.7 8.8 8.9 Réglage de la position neutre : .......................................................................... Réglage de la sensibilité de déclenchement ..................................................... Dispositif amortisseur ........................................................................................ Réglage de ressort de position zéro .................................................................. Réglage de base du frein à bande du volant ..................................................... Régler la rampe d’éjection des balles ............................................................... Réglage du ressort du tendeur de chaîne sur le ramasseur (modèle sans mécanisme de coupe) ................................................................. VIII -20 VIII -21 VIII -22 VIII -22 VIII -23 VIII -23 VIII -24 9 Entretien, maintenance et graissage ........................................... IX -1 9.1 9.2 9.2.1 9.2.2 9.2.3 9.3 9.3.1 9.3.2 9.3.3 9.3.4 9.4 9.4.1 9.4.2 9.4.3 9.4.4 9.4.5 9.4.6 Consignes de sécurité ........................................................................................... IX -1 Généralités ............................................................................................................ IX -1 Couples de serrage ............................................................................................... IX -1 Nettoyage .............................................................................................................. IX -2 Pneumatiques ....................................................................................................... IX -2 Système hydraulique ............................................................................................. IX -3 Consignes de sécurité spéciales........................................................................... IX -3 Système hydraulique de bord ................................................................................ IX -3 Hydraulique de travail (confort) ............................................................................. IX -5 Actionnement manuel d’urgence ........................................................................... IX -6 Vidange et contrôle du niveau d’huile au niveau des transmissions ..................... IX -7 Généralités ............................................................................................................ IX -7 Boîte de transmission principale ........................................................................... IX -7 Engrenage de l’empaqueteur ................................................................................ IX -7 Boîte de distribution ............................................................................................... IX -8 Transmission supérieure et inférieure du ramasseur ............................................. IX -8 Transmission de l’entraînement du mécanisme de coupe modèle Big Pack XC en haut et en bas ........................................................................................................ IX -9 Système de freinage ............................................................................................ IX -10 Consignes de sécurité spéciales......................................................................... IX -10 Réservoir à air comprimé .................................................................................... IX -10 Régler le dispositif de transmission ..................................................................... IX -11 Vérins de freinage ............................................................................................... IX -11 Compresseur ....................................................................................................... IX -12 Lubrification ......................................................................................................... IX -13 Consignes de sécurité spéciales......................................................................... IX -13 Généralités .......................................................................................................... IX -13 Graissage ............................................................................................................ IX -13 Arbre à cardan principal ...................................................................................... IX -13 Arbres à cardan ................................................................................................... IX -14 Lubrifier les galets de roulement des leviers des couteaux ................................. IX -15 Points de lubrification .......................................................................................... IX -16 Graissage centralisé (option) ............................................................................... IX -21 Emplacement des capteurs ................................................................................. IX -22 Réglage des capteurs ......................................................................................... IX -24 9.5 9.5.1 9.5.2 9.5.3 9.5.4 9.6 9.7 9.7.1 9.7.2 9.7.3 9.7.3.1 9.7.3.1 9.7.3.2 9.7.4 9.7.5 9.8 9.9 4 Table des matières 10 Défauts, causes, remèdes .............................................................. X -1 10.1 10.2 10.3 10.4 Consignes de sécurité ............................................................................................ X -1 Défauts généraux ................................................................................................... X -2 Défauts du noueur .................................................................................................. X -4 Recherche des erreurs dans la lubrification centrale............................................ X -15 A1 Schémas de câblage du système hydraulique ........................... A -1 A1.1 A1.2 A1.3 A1.4 A1.5 Hydraulique de travail partie I pour l’électronique des versions de médium et confort ................................................................................................... A -1 Hydraulique de travail partie II pour l’électronique de la version confort ................ A -2 Hydraulique de travail partie II pour l’électronique des versions de médium.......... A -3 Système hydraulique de bord pour l’électronique de la version médium .............. A -4 Système hydraulique de bord pour l’électronique de la version confort ................. A -4 A2 Schémas de circuits électriques ................................................... A -5 A2.1 A2.2 Unité de commande médium .................................................................................. A -5 Unité de commande confort ................................................................................. A -11 5 Table des matières 6 Généralités 1 Généralités Ces instructions de service contiennent des informations fondamentales devant être respectées lors du montage, du fonctionnement et de la maintenance. C’est pourquoi le personnel doit impérativement avoir lu ces instructions de service avant toute utilisation et mise en service. D’autre part, le personnel doit toujours pouvoir avoir accès à ces instructions. Le respect des conditions de fonctionnement, de maintenance et de remise en état prescrites par le fabricant fait également partie d’une utilisation conforme de la machine. Matières à presser autorisées : Récoltes agricoles telles que le foin et la paille Le ramassage et le pressage d’autres matériaux ne sont autorisés qu’après accord du fabricant. L’andainage de la récolte à presser ainsi que l’insertion automatique lors du passage du ramasseur sont cependant deux conditions préalables. Vous devrez tenir compte non seulement des consignes de sécurité générales énoncées au chapitre 2, Sécurité, mais aussi des consignes de sécurité spéciales énoncées dans les autres chapitres. Fabricant : Maschinenfabrik Bernard Krone GmbH Heinrich-Krone-Strasse 10 D-48480 Spelle (Germany) Téléphone : 0 59 77/935-0 Téléfax : 0 59 77/935-339 E-Mail : info.ldm@krone.de Toutes les informations, figures et données techniques figurant dans ces instructions correspondent à la version la plus récente au moment de la publication. Nous nous réservons le droit d’apporter, à tout moment et sans en indiquer les motifs, des modifications conceptuelles. Déclaration de conformité CE selon la directive européenne se trouve au verso de la page de garde. 1.3 Indications concernant les demandes de renseignements et les commandes Les pièces de rechange d’origine et les accessoires autorisés par le fabricant assurent votre sécurité. L’utilisation d’autres pièces peut avoir pour effet de dégager notre responsabilité quant aux conséquences qu’elles pourraient entraîner. 1.1 But d’utilisation Les presses à grosses balles Big Pack 12130 / XC ; sont des ramasseuses-presse avec le « système de remplissage variable ». Dans toutes les conditions d’intervention, elles pressent des grosses balles fortement compactées et de géométrie stable d’une longueur de 1,0 à 3,2 m. Les présentes instructions sont valables pour les presses à grosses balles : Big Pack 12130 / XC Les données machine figurent sur une plaque signalétique (1). Elle est apposée sur la face droite de la machine. Le type de la machine, le numéro d’identification du véhicule ainsi que l’année de construction de la machine doivent toujours être indiqués lors de toute demande de renseignements concernant la machine ou de commande de pièces de rechange. 1.2 Conformité d’utilisation Maschinenfabrik Bernard Krone GmbH Heinrich-Krone-Str. 10 D-48480 Spelle Made in Germany Les presses à grosses balles Big Pack 12130 / XC sont exclusivement conçues pour être utilisées dans les travaux agricoles (utilisation conforme). Toute utilisation sortant de ce cadre est considérée comme non conforme. Le fabricant décline toute responsabilité des dommages qui pourraient en résulter ; le risque va uniquement à la charge de l’utilisateur. BPXC0100 Type N° d’ident. du véhicule Année de construction L’intégralité de l’identification a valeur officielle et ne doit être ni modifiée ni camouflée ! I-1 Généralités 1.4 Caractéristiques techniques 1.4.1 Big Pack 12130 / XC Big Pack 12130 Big Pack 12130 XC Essieu simple Tandem Tandem Vitesse max. autorisée : [km/h] 40 50 50 Longueur de position de travail [mm] 10850 Longueur de position 9060 de transport [mm] Hauteur [mm] 3600 Poids [kg] 11150 12340 Pneumatiques 500/55-20 500/55-20 800/40 R26,5TL 620/50 R22,5 620/50 R22,5 Largeur [mm] 3410 2995 2995 Ecartement des roues [mm] 2500 2400 2400 Canal de pressage Hauteur [mm] 1300 Largeur [mm] 1200 Longueur [mm] 3200 Longueur des balles [mm] de 1000 à 3200 (réglable en continu) Largeur de préhension [mm] 2380 Nombre de noueurs 6 Puissance consommée 130 kW (177 CV) 145 kW (197 CV) Mécanisme de coupe 26 (nombre de couteaux) Embrayage à friction entraînement 3000 Nm Accouplement de Accouplement de coupure à clavette 8000 Nm Accouplement de surcharge Cliquet en étoile 800 Nm Cliquet en étoile 1000 Nm Accouplement de coupure à cames 7000 Nm du mécanisme de coupe Accouplement de surcharge Accouplement de coupure à cames 16500 Nm de l’empaqueteur Tige de traction des aiguilles Vis de cisaillement M10 x55 DIN 931-10.9z I-2 Généralités 1.4.2 Lubrifiants Volumes de remplissage et lubrifiants du mécanisme Volume en litres Désignation/marque Boîte de transmission principale 35 Engrenage de l’empaqueteur 4,0 Boîte de transfert du noueur/empaqueteur 1,0 Esso-Spartan EP 150 Transmission du ramasseur supérieur 0,5 Shell Omala Öl 150 0,5 Fuchs - EP 85 W90 Transmission du ramasseur inférieur SAE 90 GL 4 Lubrifiants bio ou sur demande Castrol EPX 90 Transmission de l’entraînement du mécanisme de coupe pour XC haut 2,8 Transmission de l’entraînement du mécanisme de coupe pour XC bas 2,7 Volume de remplissage et huile du système Volume en litres Réservoir d’huile de la presse 15 Désignation/marque Fuchs Renolin MR 46 MC BP Energol SHF 46 Shell Tellus 46 Esso Univis N 46 Aral Vitan VS 46 Lubrifiants bio sur demande Volume de remplissage et désignation de l’huile du compresseur Volume en litres jusqu’à la marque supérieure de la jauge Désignation/marque Huile moteur normale SAE 20 ou 20 W 40 Lubrifiants bio sur demande 0,2 Dans le cas des huiles biologiques, il est nécessaire de respecter les intervalles de vidange en raison du vieillissement des huiles. I-3 Généralités 1.5 Conditions de l’attelage sur le tracteur Raccordement des freins : Pour les presses à grosses balles avec : freins à air comprimé freins hydrauliques (6) Raccordements électriques : Eclairage de la presse à grosses balles Alimentation de la commande électronique Machines avec homologation 65 km/h Système de freinage à deux conduites nécessaire Raccordement de freins hydrauliques nécessaire (pression de fonctionnement max. 120 bar) Prise de courant à 7 pôles DIN ISO 1124 Prise 2 pôles (raqccordement direct de la batterie nécessaire en courant permanent) Prise ABS • Les raccords hydrauliques sont identifiés par des clips de couleur pour flexibles. • Veuiller, lors de l’accouplage des conduites hydrauliques, tenir compte de l’autocollant pour le système hydraulique du tracteur (voir chapitre Sécurité « Position des autocollants de remarques générales au niveau de la machine »). Raccordements hydrauliques : Les raccordements suivants sont possibles en fonction de la version de presse à grosses balles qui a été livrée : en fonction du modèle : Levage du ramasseur (1) soupape de commande à simple effet (rouge 2) Blocage de l’essieu orientable (5) soupape de commande à simple effet (rouge 7) Pied d’appui (hydraulique) (sans figure) soupape de commande à double effet • Pied d’appui vers le haut (rouge 6) • Pied d’appui vers le bas (bleu 6) Electronique version de base/Electronique version médium: Rabat de la barre de coupe soupape de commande ŕ double effet • Abaisser la barre de coupe (2) • Remonter la barre de coupe (4) Sortir les barres de coupe soupape de commande ŕ double effet • Pression (7) • Recul (8) Electronique version confort: Boîtier à soupapes pression (9) Boîtier à soupapes recul (3) Circuit de commande de charge * (4) (bleu 5) (rouge 5) (rouge 4) (bleu 4) soupape de commande à simple effet (NW 15) Rücklauf Tank (NW 18) LS-Anschluß (NW 12) (rouge 1) (bleu 1) (rouge 3) * uniquement pour tracteurs avec hydraulique Load-Sensing 6 5 1 7 8 3 I-4 2 4 9 BPXC0232 Généralités 1.6 Description technique générale Vitesse de rotation de la prise de force 1000 tr/min Arbre à cardan côté tracteur : côté machine : Attelage Œillet d'attelage à rotule - charge d'appui autorisée : 2 000 kg maxi, attelage bas à rotule - charge d'appui autorisée : 2 500 kg maxi (timon réglable en hauteur) Attention ! Lors du réglage, les vis à tête hexagonale doivent être serrées au couple de serrage selon le tableau « Couples de serrage » au chapitre 8.2. Appui Pied d’appui, à réglage manuel en hauteur. Option : Pied d’appui hydraulique Rouleau de ramasseur non commandé EasyFlow Levage hydraulique grand angle accouplement à roue libre Réglage de la hauteur à l’aide d’une barre à trous sur la roue de support. Barre porte-dents : 5 pièces Nombre de dents : 16 (20) pointes réversibles/barre porte-dents Chargement latéral vis d’alimentation droite et gauche Amenée des matières à presser variable (VFS) Entrée forcée par le cylindre d’empaquetage Cylindre d’empaquetage avec : 5 empaqueteurs de transport et 1 empaqueteur d’alimentation embrayable Sur le modèle XC, un entraînement de mécanisme de coupe est installé en amont. Piston de presse Longueur de course 750 mm - cadence de piston 50 coups par minute (Big Pack 890) - cadence de piston 38,5 coups par minutre (Big Pack 1270 et 1290) Le piston de presse se déplace sur 4 galets de roulement 5/7 couteaux au niveau du piston Réglage de la densité de pressage Réglage de la force hydro-électronique (à partir du tracteur pour chaque version) Boîtes à ficelle des deux côtés, pour un total de 32 bobines de ficelle Ficelle de liage Ficelle synthétique (110 à 130 m/kg) En fin de rouleau de ficelle et ficelle sectionnée Contrôle électrique de la ficelle avec signal acoustique et optique. Déchets des balles restantes/dépose des balles être Rampe d’éjection des balles d’une seule pièce (devant relevéelors du transport). Commande en fonction de la version ( médium, confort) sur la machine ou le tracteur Frein de blocage Actionnement par manivelle à gauche à l’arrière de la presse I-5 Généralités 1.7 Vues d’ensemble 8 11 15 BP1213030 1.7.1 Face gauche de la presse à grosses balles Big Pack avec essieu tandem 1. 2. 3. 4. 5. 6. 7. 8. Frein de blocage du volant Ordinateur de bord Détection de longueur des packs Manivelle du frein parking Dispositif de tension et de contrôle de la ficelle Ramasseur avec roue de jauge Dispositif de placage à rouleaux Coffre d’outils I-6 9. Timon réglable en hauteur 10. Arbre à cardan grand angle avec limiteur de charge et roue libre 11. Boîtes à ficelle 12. Déclenchement manuel noueur et blocage de l’arbre du noueur 13. Extincteur 14. Languette intermédiaire 15. Soupape de commande électronique Généralités 8 7 9 1 5 3 6 2 4 BP1213031 1.7.2 Face droite de la presse à grosses balles Big Pack avec essieu tandem 1. 2. 3. 4. Zone de liage Réservoir d’huile hydraulique Béquille de support Fixation pour raccords rapides et fiches 5. 6. 7. 8. 9. Entraînement mécanisme de coupe XC Robinet d’arrêt système hydraulique du ramasseur Reteneur de ficelle dans la boîte à ficelle Rampe d’éjection des balles Remplissage système variable I-7 Généralités 1.7.3 Fonctionnement du système de transport VFS 16 1 2 3 14 15 4 5 6 7 8 9 10 11 12 14 15 13 16 16 1 2 3 4 5 6 7 8 9 10 11 12 13 I-8 16 BPXC0200 Généralités 1.7.4 Description fonctionnelle de la presse à grosses balles La presse à grosses balles BIG PACK doit être entraînée par un tracteur d’une puissance min. de 115 kW. La presse à grosses balles BIG PACK est couplée au dispositif d’attelage ou à la barre d’attelage. Le timon peut être réglé en hauteur afin que la presse à grosses balles puisse fonctionner en position horizontale. La force du piston de presse est réglée électroniquement par cylindre hydraulique (9) au niveau des volets du canal de pressage. Lorsque la longueur de balle réglée est atteinte, le disque soleil dépassant dans le canal de pressage déclenche le mécanisme de nouage. La Big Pack 12130 possèdent, quant à elles, 6 noueurs (7). Les grosses balles sont déposées par une rampe d’éjection des balles (10). La presse BIG PACKest entraînée via un arbre à cardan transmettant le couple provenant du tracteur à un engrenage cylindrique conique (12) par l’intermédiaire d’une masse tournante (11). Le vitesse d’entrée max. de 1000 tr/min ne doit pas être dépassée car cela pourrait endommager la machine. L’arbre à cardan est équipé d’une articulation grand angle côté tracteur. Les instructions de service prévues pour l’arbre à cardan se trouvent au niveau de l’arbre à cardan. Il est également nécessaire de lire les instructions des service de l’arbre à cardan avant de faire fonctionner la presse à grosses balles. Ces instructions décrivent principalement le raccourcissement de l’arbre à cardan ainsi que les éventuels travaux de réparation et d’entretien. Le ramasseur (2) de 2 m (2,4 m) de largeur ramasse proprement les matières à presser. Un dispositif de placage à rouleaux réglable en hauteur (1) permet un ramassage sans anomalies et contribue à éviter les engorgements. La récolte est transportée vers le cylindre d’empaquetage (13), le rotor de coupe (14) et les couteaux (15) par deux vis d’alimentation (3) se trouvant sur le côté droit et le côté gauche du ramasseur. Le ramasseur peut être élevé et abaissé grâce au système hydraulique du tracteur. Les roues de jauge du ramasseur peuvent être réglées en hauteur afin d’obtenir une hauteur de travail optimale pour le ramasseur. Les empaqueteurs de transport (4) remplissent le couloir d’alimentation. Les empaqueteurs permettent le rassemblement de la récolte dans le couloir d’empaquetage. Le niveau de remplissage du couloir d’alimentation est détecté par des palpeurs (16). Lorsqu’un certain niveau de remplissage est atteint, le palpeur se rabat et l’empaqueteur d’alimentation transporte la récolte dans le canal de pressage. Les matières à presser sont pressées en grosses balles fortement comprimées dans le canal de pressage par le piston de presse (6). La longueur et la densité des grosses balles peuvent être réglées en continu. Il est ainsi possible de produire des balles adaptées à différentes exigences. I-9 Généralités I - 10 Sécurité 2 Sécurité 2.1 Caractéristique des consignes de sécurité figurant dans ces instructions Les consignes de sécurité contenues dans ces instructions qui, en cas de non-respect, impliquent la mise en danger des personnes, sont caractérisées par le symbole de danger usuel : Symbole de sécurité selon DIN 4844 - W9 Les remarques générales relatives aux fonctions sont accompagnées du symbole suivant : 2.2 Consignes de sécurité et règlements de prévoyance contre les accidents 2.2.1 Qualification et formation du personnel L’utilisation, l’entretien et la maintenance de la presse à grosses balles sont réservés aux personnes formées et connaissant les dangers qui y sont liés. L’exploitant devra délimiter clairement les domaines de responsabilité, les compétences et les tâches de surveillance incombant à chaque membre du personnel. Si le personnel ne détient pas les connaissances nécessaires, il faudra lui dispenser une formation et lui fournir des instructions. L’exploitant est tenu de s’assurer que le personnel a bien compris le contenu des instructions. Les travaux de remise en état non décrits dans la présente notice d’utilisation sont exclusivement réservés à des ateliers agréés. 2.2.2 Dangers liés au non-respect des consignes de sécurité Tenir compte des consignes apposées directement sur la machine qui doivent, d’autre part, être lisibles en permanence. Le non-respect des consignes de sécurité peut mettre en danger des personnes, mais peut également impliquer un risque pour l’environnement et la machine. Le nonrespect des consignes de sécurité peut entraîner la perte du droit aux dommages et intérêts. Dans le détail, le non-respect des consignes de sécurité peut par exemple engendrer les risques suivants : – Mise en danger des personnes en raison de zones de travail non protégées. – Défaillance des fonctions importantes de la machine. – Echec des méthodes prescrites de maintenance et d’entretien. – Mise en danger des personnes en raison des influences mécaniques et chimiques. – Risques pour l’environnement en raison de la fuite d’huile hydraulique. 2.2.3 Maîtrise des risques Respecter les consignes de sécurité décrites dans ces instructions de service, les prescriptions de prévoyance des accidents ainsi que les éventuelles prescriptions de travail, d’exploitation et de sécurité de l’exploitant. Les prescriptions visant la sécurité au travail et celles préventives des accidents, publiées par les mutuelles d’assurances professionnelles, sont contractuelles. Vous devrez respecter les consignes de sécurité du fabricant du véhicule. II - 1 Sécurité Lorsque vous empruntez une voie de circulation publique, vous devrez respecter les prescriptions légales applicables (la réglementation sur la réception et l’homologation des véhicules, le code de la route). 2.2.4 Prescriptions de sécurité et de prévoyance des accidents 1. En plus des consignes figurant dans ces instructions de service, respecter les prescriptions générales de sécurité et de prévoyance des accidents ! 2. Les plaquettes et panneaux d’avertissement et à mentions apposés fournissent des renseignements importants, permettant un fonctionnement sans risque ; en les respectant, vous préservez votre sécurité ! 3. Lorsque vous empruntez la voie publique, respectez les dispositions applicables dans chaque cas ! 4. Avant d’entamer les travaux, familiarisez-vous avec tous les équipements, les organes de commande ainsi qu’avec leurs fonctions. Au moment de réaliser le travail, ce n’est plus le moment de le faire ! 5. Utilisateur, portez des vêtements moulants. Evitez les vêtements amples. tels que l’éclairage, les appareils d’avertissement et éventuellement les équipements de protection ! 15. Les organes de commande (câbles, chaînes, tringles, etc.) des équipements commandés à distance doivent être placés de sorte à ne pas déclencher de déplacements non voulus dans toutes les positions de transport et de travail. 16. Lors de la conduite sur route, veiller à ce que les appareils soient dans l’état prescrit et les verrouiller selon les directives du constructeur. 17. Pendant la conduite, interdiction de quitter le poste de conduite ! 18. La vitesse de déplacement doit toujours être adaptée aux conditions environnantes ! Lorsque vous conduisez en montée, en descente ou transversalement à une pente, évitez de virer brutalement ! 19. Le comportement en marche, la capacité de freinage et le maniement de la direction sont modifiés par les appareils couplés ou suspendus, ainsi que par les poids de lestage. Pour cette raison, veillez à conserver une maniabilité et une puissance de freinage suffisantes ! 6. Pour éviter tout risque d’incendie, maintenez la machine propre ! 20. Lorsque vous franchissez des virages, souvenezvous du déport et/ou de la masse cinétique engendrés par l’appareil ! 7. Avant de commencer à rouler et avant de faire entrer la machine en servir, contrôlez le périmètre de la machine ! (Pensez aux enfants !) Veiller à ce que la vue soit suffisante ! 21. Ne mettre les appareils en service que lorsque tous les dispositifs de protection sont installés et en position de protection ! 8. Ne pas se tenir sur l’équipement de travail pendant le travail et le déplacement. 9. Accouplez les appareils réglementairement, ne les fixez et sécurisez que contre les dispositifs prescrits. 10. Lorsque vous rapportez et déposez des appareils, amenez les équipements de soutènement dans la position respective voulue. 11. Lors du couplage et du découplage d’appareils au niveau du tracteur, il est nécessaire de procéder avec une prudence particulière ! 12. Fixez toujours les poids de ballast réglementairement, aux points de fixation prévus. 13. Respectez les charges admissibles aux essieux, ne dépassez pas le poids total ni les dimensions maximales de transport. 14. Contrôlez et montez les équipements de transport II - 2 22. Il est interdit de séjourner sur l’aire de travail ! 23. Ne séjournez jamais dans la zone de rotation et de pivotement de l’appareil ! 24. N’actionnez les cadres rabattables hydrauliques qu’après avoir vérifié que personne ne se trouve dans la zone de pivotement ! 25. Les pièces servocommandées (hydrauliquement par ex.) comportent des zones d’écrasement et de cisaillement ! 26. Avant de quitter le tracteur, couper le moteur et retirer la clé de contact ! 27. Ne jamais se tenir entre le tracteur et l’appareil, tant que tout déplacement du véhicule n’est pas empêché grâce au frein de blocage et/ou à des cales d’arrêt ! Sécurité 2.2.5 Appareils tractés 1. Bloquer les appareils afin d’empêcher tout déplacement involontaire. 2. Respecter la charge d’appui de l’étrier de guidage, de la barre d’attelage ou de l’attelage « hitch » ! 3. Dans le cas d’un attelage par timon, veiller à ce que la mobilité soit suffisante au niveau du point d’attelage ! 2.2.6 Utilisation de l’arbre de prise de force 1. N’utilisez que les arbres à cardan prescrits par le fabricant. 2. Le tube et l’entonnoir protégeant l’arbre à cardan, ainsi que le dispositif protégeant l’arbre de prise de force, devront avoir été fixés - y compris du côté de l’appareil - et se trouver dans un état correct. 3. En ce qui concerne les arbres articulés, respectez le recouvrement prescrit pour le tube dans les positions de travail et de transport. 4. Ne montez et déposez les arbres à cardan qu’après avoir désactivé l’arbre de prise de force, éteint le moteur et retiré la clé de contact ! 5. Si vous utilisez des arbres à cardan à accouplement débrayant en cas de surcharge ou à accouplement à roue libre non capotés par l’équipement de protection situé sur le tracteur, il faudra monter ces accouplements du côté de l’appareil. 6. Veillez toujours à monter et sécuriser correctement l’arbre à cardan. 7. Accrochez les chaînes pour empêcher que la protection de l’arbre à cardan tourne avec celui-ci. 8. Avant de connecter la prise de force, s’assurer que la vitesse de la prise de force du tracteur choisie correspond à la vitesse autorisée de l’appareil ! 9. Avant de connecter la prise de force, vérifier que personne ne se trouve dans la zone de danger de l’appareil ! 10. N’enclenchez jamais l’arbre de prise de force tandis que le moteur est à l’arrêt ! 11. Lors de travaux avec l’arbre de prise de force, interdiction à toute personne de séjourner dans la zone de l’arbre de prise de force ou de l’arbre à cardan en rotation. 13. Attention ! Après avoir désactivé l’arbre de prise de force, pensez au risque que pose la masse cinétique en déplacement inertiel ! Pendant cette période, ne vous approchez pas de l’appareil. Ne continuer les travaux sur la machine que lorsque celle-ci est totalement à l’arrêt et que la masse tournante est verrouillée avec le frein de blocage. 14. Nettoyage, lubrification ou réglage des appareils entraînés par l’arbre de prise de force ou l’arbre à cardan uniquement après avoir déconnecté la prise de force, coupé le moteur et retiré la clé de contact ! Serrer le frein de blocage au niveau de la masse tournante. 15. Déposez sur la fixation prévue l’arbre à cardan découplé. 16. Après avoir déposé l’arbre à cardan, emmanchez la gaine protectrice sur l’embout de l’arbre de prise de force. 17. En présence de dégâts, supprimez-les immédiatement, avant de travailler avec l’appareil. 18. Desserrer le volant avant d’activer l’arbre de prise de force. 2.2.7 Installation hydraulique 1. L’installation hydraulique se trouve sous pression ! 2. Lors du raccordement des cylindres et des moteurs hydrauliques, veiller à ce que le branchement des flexibles hydrauliques soit conforme aux directives ! 3. Lors du branchement des flexibles hydrauliques sur le système hydraulique du tracteur, veiller à ce que le système hydraulique du tracteur et de l’appareil ne soit pas sous pression ! 4. Au niveau des liaisons de fonction hydrauliques entre le tracteur et la machine, marquer différemment les manchons d’accouplement et les fiches de réseau, afin d’exclure toute erreur de manœuvre ! Lorsque les raccords ont été intervertis, les fonctions sont inversées (abaisser/soulever par exemple) - Risque d’accident ! 5. Contrôlez régulièrement les flexibles hydrauliques et changez-les s’ils sont endommagés ou présentent des signes de vieillissement. Les conduites souples de remplacement doivent répondre aux exigences techniques du fabricant de l’appareil ! 6. Lors de la recherche des fuites, utilisez des accessoires appropriés, ceci en raison du risque de blessures. 12. Désactivez toujours l’arbre de prise de force en présence de coudes excessifs et lorsqu’il ne sert pas. II - 3 Sécurité 7. Les liquides (l’huile hydraulique) sortant sous haute pression peuvent perforer la peau et provoquer des blessures graves ! Si des blessures ont été occasionnés, rendez-vous immédiatement chez un médecin ! Risque d’infection ! 8. Avant d’effectuer des travaux sur l’installation hydraulique, mettez cette dernière hors pression et arrêtez le moteur ! 2.2.8 Pneumatiques 7. Si les équipements de protection sont exposés à une usure, vous devrez les contrôler régulièrement et les remplacer à temps. 8. Lors des travaux de soudure électrique sur le tracteur et les appareils, débrancher les câbles au niveau du générateur et de la batterie. 9. Les pièces de rechange doivent se conformer au minimum aux spécifications techniques définies par le fabricant de l’appareil. Les pièces de rechange KRONE d’origine garantissent cette conformité. 1. Lors des travaux sur les pneus, il est important de veiller à ce que l’appareil soit bien stabilisé et que tout déplacement involontaire de celui-ci soit impossible (cales d’arrêt). 10. Lors du stockage de gaz, utiliser uniquement de l’azote pour le remplissage - risque d’explosion 2. Seules les personnes disposant des connaissances suffisantes et des outils nécessaires sont habilitées à monter les roues et les pneus ! 2.2.10 Transformations réalisées par l’exploitant et fabrication de pièces de rechange 3. Les travaux de réparation au niveau des roues et des pneus ne doivent être exécutés que par des spécialistes disposant des outils adaptés. 4. Contrôler régulièrement la pression d’air ! Respecter la pression d’air prescrite. 2.2.9 Maintenance 1. Les travaux de remise en état, de maintenance et de nettoyage, la suppression des dysfonctionnements n’auront fondamentalement lieu qu’après avoir désactivé le mécanisme d’entraînement et immobilisé le moteur. - Retirez la clé de contact. Serrer le frein de blocage de la masse tournante. 2. Contrôlez régulièrement que les écrous et vis sont bien fixés, resserrez-les le cas échéant. 3. Lors de travaux de maintenance sur l’appareil soulevé, sécurisez-le toujours en position au moyen d’éléments de soutènement appropriés. 4. Lorsque vous changez les outils de travail comportant des tranchants, utilisez un outillage approprié ainsi que des gants. 5. Mettez les huiles, graisse et filtres au rebut en respectant la réglementation. 6. Avant de travailler sur les circuits électriques, débranchez toujours l’alimentation électrique. II - 4 Les transformations ou modifications au niveau de la machine ne sont possibles qu’après concertation avec le fabricant. Les pièces de rechange d’origine et les accessoires autorisés par le fabricant assurent votre sécurité. L’utilisation d’autres pièces peut avoir pour effet de dégager notre responsabilité quant aux conséquences qu’elles pourraient entraîner. 2.2.11 Modes d’exploitation non autorisés La sécurité de fonctionnement de la machine livrée n’est garantie que dans le cas d’une utilisation conforme selon le chapitre intitulé Informations générales de ces instructions de service. Ne dépassez en aucun cas les valeurs limites indiquées dans les fiches de données. Sécurité II - 5 Sécurité 2.3 Introduction La presse à grosses balles KRONE est équipée de tous les équipements de sécurité (équipements de protection). Il est impossible à la fois de sécuriser intégralement toutes les zones dangereuses de cette machine, et de conserver toutes ses fonctionnalités. Des indications concernant les risques résiduels figurent sur la machine. Ces indications sont présentes sous la forme de pictogrammes d’avertissement. Des remarques importantes concernant l’emplacement de ces plaques indicatrices ainsi que leur signification ainsi et explications complémentaires figurent ci-après dans ces instructions de service. L’utilisateur est tenu de prendre connaissance des explications figurant à côté de chaque pictogramme d’avertissement. Le texte explicatif et l’emplacement choisi au niveau de la machine donnent des indications sur les endroits dangereux spécifiques de la machine. 2.3.1Emplacement des autocollants de sécurité sur la machine 9 6 6 RE/LI à droite/à gauche 7 à RE/LI droite/à gauche 8 7 3 2 4 6 6 6 5 àLIgauche 3 7 6 àRE/LI droite/à gauche RE/LI 7 7 àRE/LI droite/à gauche RE/LI BP1213029 II - 6 Sécurité 1 2 939 101-4 1000/min MAX. 200 bar MAX. Avant la mise en service, lire les instructions et les consignes de sécurité et les respecter. La vitesse de rotation de la prise de force ne doit pas être supérieure à 1000 tr/min ! La pression de fonctionnement de l’installation hydraulique ne doit pas être supérieure à 200 bars ! N° de commande : 939 471-1 (1x) N° de commande : 939 101-4 (1x) 3 Danger dû à la rotation de la vis. 4 Ne jamais intervenir dans la zone de travail du ramasseur tant que la machine fonctionne. Un autocollant se trouve sur le côté droit et gauche de la machine. N° de commande : 939 520-1 (2x) 5 N° de commande : 939 407-1 (2x) 6 Ne pas monter sur la machine lorsque la prise de force est raccordée et que le moteur tourne. Un autocollant figure de part et d’autre du dispositif de montée vers la plateforme de travail. Fermer l’équipement de protection avant la mise en service ! N° de commande : 939 408-2 (1x) N° de commande : 942 002-4 (14x) 7 Ne jamais intervenir dans la zone de danger d’écrasement, tant que des pièces peuvent s’y déplacer. (uniquement pour rampe d’éjection à rouleaux et mécanisme de coupe XC) N° de commande : 942 196-1 (4 exemplaires) 8 Tenez-vous suffisamment éloigné des surfaces chaudes. (option) N° de commande : 942 210-0 (1x) II - 7 Sécurité 9 6 6 RE/LI à droite/à gauche 7 RE/LI gauche à droite/à 8 7 3 2 4 6 6 6 5 àLIgauche 3 7 6 àRE/LI droite/à gauche RE/LI 7 7 àRE/LI droite/à gauche RE/LI BP1213029 9 Ne stationnez pas dans la zone de pivotement de la rampe d’éjection. Maintenez la distance. N° de réf. 939 469-1 (2 x) II - 8 Sécurité 2.3.2 Position des panneaux d’avertissement généraux sur la machine 1 BP1213091 27 002 746 0 X P T 1 1 LS 3 2 4 4 5 5 6 6 7 1 27 002 746 0 (1x) II - 9 Sécurité 2.4 Consignes de sécurité spéciales 2.4.1Echelle de montée • • Ne monter à l’échelle que lorsque la prise de force est déconnectée, le moteur coupé et la clé de contact retirée ! Il est interdit de prendre place sur la presse à grosses balles et sur l’échelle d’accès pendant la marche. Sur le côté arrière gauche de la machine au niveau du canal de pressage se trouve une échelle de montée (1) permettant notamment d’exécuter les travaux de maintenance au niveau du mécanisme de nouage. 1 BPXC0107 2.4.2 Garde-fou de sécurité Le garde-fou de sécurité (1) doit être relevé chaque fois qu’un opérateur prend place sur la plate-forme. 1 Pour ce faire : • Relevez le garde-fou de sécurité (1) et poussez-le vers l’avant jusqu’à ce que le verrouillage (2) s’engage. Abaissez le garde-fou de sécurité (1) en quittant la plate-forme. Pour ce faire : Desserrez le verrouillage (2), poussez le garde-fou de sécurité vers l’arrière et abaissez-le. 2 BP1213038 Le garde-fou de sécurité (1) doit être en position basse et replié pour circuler sur la voie publique. 2.4.3 Extincteur L’extincteur (1) se trouve à l’avant, sur le timon, à gauche dans le sens de la marche. Cet extincteur doit être enregistré, et ce afin de garantir que les inspections exigées sont bien effectuées. 1 BPXC0108 II - 10 Mise en service et transport 3. Mise en service et transport 3.1 Consignes de sécurité • • • • • • • • • Une prudence toute particulière s’impose lors de l’attelage et du dételage de la presse à grosses balles au tracteur. Aucune personne ne doit se trouver entre le tracteur et la presse à grosses balles. La presse ayant été attelée, couper le moteur et retirer la clé de contact. Serrer le frein du volant. Lors des travaux de maintenance, d’entretien, de réglage et de révision effectués sur la presse à grosses balles, toujours déconnecter la prise de force, couper le moteur et retirer la clé de contact. Ne mettre la presse à grosses balles en service que lorsque tous les dispositifs de protection sont installés et se trouvent en position de protection. La presse à grosses balles peut fonctionner avec une vitesse de prise de force maximale de 1000 tr/min. Seul l’arbre à cardan prescrit par l’utilisateur peut être utilisé avec l’accouplement de surcharge et la roue libre correspondants. L’arbre à cardan peut être monté et démonté uniquement lorsque la prise de force est déconnectée, le moteur coupé et la clé de contact retirée ! Poser les flexibles et les câbles de liaison de telle sorte qu’ils ne se tendent pas et n’entrent pas en contact avec les roues du tracteur dans les virages. Contrôler régulièrement les conduites souples hydrauliques et les remplacer lorsqu’elles sont endommagées ou usées ! Lors du raccordement et du démontage des flexibles hydrauliques au niveau du système hydraulique du tracteur, veiller à ce que le système hydraulique ne soit pas sous pression, aussi bien côté tracteur que côté machine. 3.2 Commande générale 3.2.1 Béquille de support Tant que la presse à grosses balles n’est pas attelée au tracteur, le timon repose sur la béquille de support 1 Relever la béquille de support : • • • Dès que la presse à grosses balles est attelée au tracteur, tourner la manivelle (1) dans le sens des aiguilles d’une montre de plusieurs tours jusqu’à ce que la béquille de support (3) soit soulagée. Retirer le boulon d’arrêt (5) dans la partie inférieure de la béquille de support (2), insérer la béquille de support et la bloquer dans la bonne position (4) à l’aide du boulon. Ensuite monter la béquille de support au maximum. Descendre la béquille support (appui du timon) : • • Pour découpler la presse à grosses balles du tracteur, descendre d’abord la béquille support (2) avec la manivelle (1) de plusieurs tours. Retirer le boulon (5) et sortir la partie inférieure de la béquille de support. Bloquer à l’aide du boulon (5). Lorsque la dureté du support est insuffisante, augmenter la base d’empattement (3) en calant un madrier. 2 5 3 4 BPXC0109 III - 1 Mise en service et transport Mécanisme à manivelle sur la béquille de support : La manivelle (2) peut être placée sur deux positions, (a) et (b) au niveau de la tête de la béquille de support. Position a) Rapport de transmission directe 1:1 pour le montage et l’abaissement rapides de la béquille de support Position b) Rapport de démultiplication pour le montage et l’abaissement, quand la presse à grosses balles s’appuie sur la béquille. 2 1 a b BP380-7-016 3.2.2 Béquille de support hydraulique (en option) La presse à grosses balles peut être équipée en option d’une béquille de support hydraulique. La béquille de support hydraulique est activée (monte et baisse) sur la soupape appropriée du tracteur. 1 Descendre la béquille de support : • • Descendre la béquille de support de la cabine du tracteur jusqu’à ce qu’elle ait une bonne assise au sol. Ensuite, il est absolument nécessaire de fermer le robinet à bille (1) sur la tête de la béquille de support. Lorsque la dureté du support est insuffisante, augmenter la base d’empattement (3) en calant un madrier. BPXC0180 Monter la béquille de support : • • Ouvrir d’abord le robinet à bille (1) sur la tête de la béquille de support. Ensuite, lever la béquille de support de la cabine du tracteur. 3.2.3 Frein parking Le frein de parking est destiné à sécuriser la presse à grosses balles contre le déplacement inopiné, en particulier quand elle est dételée. La manivelle (1) du frein parking se trouve sur le côté gauche de la presse à grosses balles sous le canal de pressage. Serrer le frein de parking : • Tourner la manivelle dans le sens des aiguilles d’une montre jusqu’à ce que la résistance soit perceptible. Desserrer le frein de parking : • Tourner la manivelle dans le sens inverse des aiguilles d’une montre jusqu’à ce que le câble de frein donne un peu de mou. III - 2 1 BP1213000 Mise en service et transport 3.2.4 Frein de blocage du volant Le frein de volant (frein à bande) se trouve sur le côté gauche de la machine au niveau du timon. • Pour immobiliser le volant, faire passer le levier de frein (1) du volant de la position (a) à la position (b). Le volant est alors freiné. a Un signal sonore retentit si l’électronique de la presse à grosses balles est activée. 1 b Attention ! Desserrer toujours le frein de blocage avant de connecter la prise de force. BPXC0201 3.2.5 Ajustage de la hauteur du timon • • • Empêcher tout déplacement involontaire de la presse à grosses balles en la bloquant à l’aide de cales d’arrêt et en serrant le frein parking. Utiliser les blocs d’arrêt adaptés pour soutenir la presse à grosses balles. Risque d’écrasement des pieds lors de l’abaissement de la béquille de support. Le timon peut être réglé pour un attelage haut ou bas. La hauteur du timon peut être adaptée à la hauteur d’attelage du tracteur (étrier de guidage ou barre d’attelage), aussi bien en position « attelage haut » qu’en position « attelage bas ». 4 2 Pour un fonctionnement optimal, la presse à grosses balles doit être attelée à l’horizontale. L'arête de référence est le support d'essieu sur lequel est vissé l'essieu. 3 1 BPXC0111 Avant de procéder au réglage, appuyer la presse à grosses balles sur la béquille de support et dételer le tracteur. Réglage de la hauteur d’attelage : • • • Piur régler la hauteur de timon, ajuster en hauteur l’œillet d’attelage (2) en desserrant les boulons (1). Si cela ne suffit pas, régler en hauteur les pièces latérales (4) en desserrant les boulons (3). Pour obtenir un attelage bas, tourner les deux pièces latérales (4). 4 2 3 Couple de serrage, voir la section 9.2.1. 1 BPXC0110 III - 3 Mise en service et transport 3.3 Attelage au tracteur • • • • La presse à grosses balles ne peut être attelée qu’aux tracteurs possédant un dispositif d’attelage approprié. Lors du recul du tracteur devant la presse à grosses balles, veiller à ce que personne ne se trouve entre la presse et le tracteur. Respecter la charge de traction et d’appui maximale du dispositif d’attelage du tracteur. Atteler et verrouiller la presse à grosses balles au dispositif d’attelage du tracteur conformément aux directives. Le modèle série de la presse à grosses balles est équipé d’un œillet d’attelage prêt à servir Ø 40 mm (DIN 11 026). En fonction des conditions spécifiques des interventions, les attelages suivants sont disponibles : - tête d’attelage à boule (K 80), - œillet d’attelage rotatif, - crochet de traction (exportation uniquement) BPXC0112 3.4 Arbre à cardan principal 3.4.1 Ajustage de l’arbre à cardan principal • • • Avant de fixer l’arbre à cardan sur la prise de force du tracteur, déconnecter la prise de force, couper le moteur et retirer la clé de contact. Serrer le frein du volant. Immobiliser le tracteur et la presse à grosses balles pour empêcher tout déplacement involontaire. Lors des virages nécessaires pour le réglage de la longueur de l’arbre à cardan, veiller à ce que personne ne se trouve entre la presse et le tracteur. Pour procéder au réglage de la longueur de l’arbre à cardan, atteler la presse à grosses balles au tracteur. La position la plus courte de l’arbre à cardan correspond à la position dans les virages serrés. • Pour procéder à la mesure, démonter l’arbre à cardan et installer la partie (1) au niveau de la presse et la partie (2) au niveau du tracteur. Pour connaître la procédure exacte d’ajustage de la longueur, consulter les instructions de service du fabricant de l’arbre à cardan. 2 1 BP800002 III - 4 Mise en service et transport 3.4.2 Montage côté tracteur 2 Avant de monter l’arbre à cardan sur la prise de force du tracteur, bloquer impérativement le volant à l’aide du frein de blocage. Côté tracteur • Libérer l’arbre à cardan de la chaîne de maintien (1). • Le moteur étant à l’arrêt et la clé de contact retirée, placer l’arbre à cardan sur la prise de force du tracteur et le bloquer. • Empêcher toute rotation de la protection de l’arbre à cardan en fixant la chaîne de sécurité (2). • • • S’assurer que le blocage de l’arbre à cardan est enclenché après le montage. N’utiliser que l’arbre à cardan fourni. Desserrer toujours le frein de blocage avant de connecter la prise de force. 1 BPXC0114 ZX400040 a) b) Veillez à passer la chaîne correctement : • La chasse de la chaîne doit être si possible à angle droit par rapport à l’arbre à cardan. (Voir la figure (a)) • La chasse de la chaîne ne doit jamais être en diagonale par rapport à l’entonnoir de protection. (Voir la figure (b)) Veillez à ce qu’il y ait un espace de manœuvre suffisant pour tous les états de fonctionnement dans la zone de pivotement de l’arbre à cardan. Le contact avec les composants du tracteur ou de l’appareil peut provoquer des dommages. III - 5 Mise en service et transport 3.5 Raccordement hydraulique, d’air comprimé et électrique Pour la presse à grosses balles, selon le modèle, le nombre de soupapes hydrauliques de commande nécessaires au niveau du tracteur varie. Les raccords hydrauliques (1) sont différenciés par des colliers de flexible en couleur (voir également chapitre 1 « conditions du raccord tracteur ») 2 1 Pour raccorder les flexibles hydrauliques, veiller à ce que la pression soit coupée soit sur le tracteur et sur la machine. • • • Déposer les flexibles hydrauliques (1) de la fixation sur le timon (2). Retirer les capuchons de protection sur les raccords de flexibles. Nettoyer intensément les accouplement emboîtables avant de les raccorder. BPXC0115 3.5.1 Frein hydraulique (en fonction des spécifications nationales) Un frein hydraulique est prévu pour certaines versions de presses à grosses balles (destinées à l’exportation). Dans ce cas, une soupape de freinage hydraulique est nécessaire sur le tracteur. Le flexible hydraulique affecté est raccordé à la soupape de commande du tracteur. Le frein est activé par la soupape de commande. 3.5.2 Raccordement hydraulique pour le blocage de l’essieu mené (option) Raccorder le flexible hydraulique du cylindre d’arrêt de l’essieu directeur (rouge 7) à un raccordement à simple effet de l’hydraulique de transport. Respecter les consignes d’utilisation du fabricant du tracteur sur le fonctionnement parallèle des appareils de commande du tracteur ! Le raccordement du cylindre d’arrêt de l’essieu directeur doit être approvisionné par priorité ou au même niveau par l’hydraulique de la presse à grosses balles ! III - 6 1 BPXC0113 Mise en service et transport 3.5.3 Raccordement Load-Sensing (option) La presse à grosses balles avec électronique confort et hydraulique confort peut être dotée de l’équipement Load-Sensing. L’utilisation sur un tracteur approprié présente l’avantage de réduire la puissance consommée grâce à un échauffement plus faible de l’huile. Lors de l’utilisation du système Load-Sensing, l’alimentation en huile est réalisée par le Power-Beyond du système hydraulique du tracteur. Le circuit de commande doit être raccordé entre le raccord de signalisation (LS) du bloc de commande et le raccord de signalisation du tracteur. Le circuit de commande(rouge 3) (1) au niveau de la presse Big Pack avec hydraulique de confort se trouve directement sous le raccordement du ramasseur à l’avant près du timon. 1 Adaptation du système hydraulique L’ hydraulique confort est conçue pour une circulation continue et doit être adaptée à l’hydraulique du tracteur. Cette adaptation est réalisée grâce au réglage de la vis du système hydraulique sur le bloc des soupapes de commande de la presse à grosses balles. Le bloc des soupapes de commande se trouve à l’avant, à gauche, sous le capot latéral. BPXC0308 Le système hydraulique doit être réglé alors que la pression est coupée ! La vis du système hydraulique (1) du bloc de soupapes de commande doit être desserrée lorsque le circuit de commande est raccordé. Le boulon du système hudraulique (1) est arrêté par un contre-écrou (2). Pour desserrer le boulon du système, desserrer d’abord le contre-écrou. Le contre-écrou doit ensuite être resserré manuellement en le tournant vers le boîtier (à la main). Version I: Visser la vis du système (1) jusqu’à la butée dans les cas suivants : – Tracteurs avec système hydraulique normal (pompe constante). – Tracteurs avec pompe LS et circuit de commande non raccordé. Ce dernier réglage est spécifié par l’usine. Version II: Desserrer le boulon du système (1) jusqu’à la butée dans les cas suivants : – Tracteurs avec système hydraulique fermé (par exemple John Deere). – Tracteurs avec pompe LS et circuit de commande raccordé simultanément. 2 Version I 1 Version II LS BPXC0117 III - 7 Mise en service et transport 3.5.4 Frein à air comprimé Insérer les têtes d’accouplement de différentes couleurs des tuyaux à air comprimé (1) dans les accouplements aux couleurs correspondantes sur le tracteur. 1 Commencer par la tête d’accouplement jaune, puis la tête d’accouplement rouge. Le démontage se fait dans l’ordre inverse. BP380-7-018 3.5.5 Fixations des flexibles hydrauliques Coupler les tuyaux flexibles à air comprimé (1) dans les fixations correspondantes (2) sur la face supérieure du timon. 2 1 BPXC0303 III - 8 Mise en service et transport 3.5.6 Câbles de liaison électriques Une source de tension est nécessaire pour l’alimentation de l’ordinateur de bord et de l’éclairage de la presse à grosses balles. Une prise de courant est fournie pour le montage sur le tracteur. • • • 3 1 2 La prise fournie doit être raccordée directement à la batterie 12 V du tracteur Insérer et verrouiller les câbles de liaison dans les prises de courant correspondantes de la presse. Si nécessaire, retirer le capuchon de protection avant le branchement. Prise 1 : Câble de liaison entre l’ordinateur de bord et le pupitre de commande sur le tracteur. Prise 2 : Alimentation en tension de l’ordinateur de bord. Reliez le raccordement côté fiche à la prise montée. Prise 3 : BPXC0118 4 Prise standard à 7 pôles pour l’éclairage (phares de travail (4), option). Dès que la fiche de l’alimentation en courant permanent est insérée et l’appareil de commande et d’affichage connecté, le signal sonore du contrôle de la ficelle retentit s’il n’y a pas de ficelle à lier dans les aiguilles. 5 BP1213024 Les feux de stationnement du tracteur alimentent les phares de travail (option) (4). • Pour allumer ou éteindre les phares de travail, il suffit d’actionner l’interrupteur rotatif (5). Les phares de travail (4) ne fonctionnent que quand les feux de stationnement sont activés. III - 9 Mise en service et transport 3.6 Remise en service après un arrêt prolongé 3.6.1 Consignes de sécurité • • • • • • Pour tous les travaux de maintenance, de montage, de réparation et de réglage, les mesures suivantes doivent toujours être prises Amener la machine à l’arrêt. Couper le moteur. Retirer la clé de contact. Serrer le frein de volant. Immobiliser le tracteur et la presse à grosses balles pour empêcher tout déplacement. Eviter tout contact entre la peau et les huiles, les graisses, les solvants et les détergents. En cas de blessure ou de brûlure par acide provoquées par des huiles, des détergents ou des solvants, consulter immédiatement un médecin. Lorsque les travaux de maintenance et d’entretien sont terminés, remonter correctement tous les revêtements et dispositifs de protection. Respecter également toutes les autres consignes de sécurité. 3.6.2 Généralités • • • • • • • • • • • • Avant la remise en service, déclencher manuellement le processus de nouage et tourner manuellement la presse à grosses balles. Lors de cette opération, contrôler les fonctions du noueur et des aiguilles. Nettoyer le noueur de toutes traces d’agents de conservation (huiles à base végétale). Dégraisser et nettoyer le disque d’entraînement du reteneur de ficelle. Graisser tous les points de lubrification et huiler les chaînes. Essuyer la graisse en excédent au niveau des points de lubrification. Changer l’huile dans toutes les transmissions. Vérifier l’étanchéité des flexibles et des conduites souples hydrauliques et les remplacer si nécessaire. Contrôler la pression d’air dans les pneus et les gonfler si nécessaire. Vérifier le serrage de toutes les vis et les resserrer si nécessaire. Contrôler tous les câbles de liaison ainsi que l’éclairage. Le cas échéant, réparer ou remplacer. Contrôler l’ensemble des réglages de la presse à grosses balles, ajuster si nécessaire. Vérifier le fonctionnement de la commande. Contrôler le fonctionnement du frein de l’arbre du noueur (à droite de l’arbre du noueur). 3.6.3 Accouplement de surcharge au niveau du volant Après une période d’immobilisation prolongée, les garnitures de l’accouplement de surcharge (1) peuvent adhérer aux surfaces frottantes. Avant l’utilisation, débloquer l’accouplement de surcharge. 3 • • • • L’accouplement de surcharge se trouve au niveau du volant (3). Pour le déblocage, serrer en croix les écrous (2) au niveau de l’accouplement de surcharge (1). Tourner manuellement l’arbre à cardan. Desserrer les écrous en croix. 1 2 BPXC0300 III - 10 Mise en service et transport 3.6.4 Stockage pendant l’hiver • • • • • • Les travaux de révision, d’entretien, de maintenance et de nettoyage doivent uniquement être effectués sur la machine à l’arrêt. Couper le moteur et retirer la clé de contact. Serrer le frein du volant. Immobiliser le tracteur et la presse à grosses balles pour empêcher tout déplacement. Lorsque les travaux de maintenance et d’entretien sont terminés, remonter correctement tous les revêtements et dispositifs de protection. Eviter tout contact entre la peau et les huiles, les graisses, les solvants et les détergents. En cas de blessure ou de brûlure par acide provoquées par des huiles, des détergents ou des solvants, consulter immédiatement un médecin. Afin d’éviter toute blessure ou accident, respecter également toutes les autres consignes de sécurité. Avant de stocker la presse à grosses balles pour la période hivernale, la nettoyer soigneusement, aussi bien à l’intérieur qu’à l’extérieur. En cas d’utilisation d’un nettoyeur à haute pression, ne pas diriger le jet d’eau directement sur les paliers. Après le nettoyage, lubrifier tous les points de lubrification. Ne pas essuyer la graisse sortant des paliers. La couronne de graisse constitue une protection supplémentaire contre l’humidité. Retirer les chaînes d’entraînement ainsi que les chaînes des attelages à chaînes (contrôler ensuite le réglage de l’empaqueteur) et les laver dans du pétrole (ne pas utiliser d’autre solvant). Vérifier l’usure des chaînes et des roues à chaîne. Lubrifier les chaînes nettoyées, les monter et les tendre. Contrôler le fonctionnement de tous les éléments mobiles tels que les galets de renvoi, les joints d’accouplement, les galets tendeurs, etc. En cas de besoin, démonter, nettoyer, lubrifier puis remonter les éléments. Le cas échéant, remplacer les pièces défectueuses par des pièces neuves. N’utiliser que des pièces de rechange KRONE d’origine. Démonter les arbres à cardan. Graisser les tubes internes ainsi que les tubes protecteurs. Graisser le graisseur au niveau du joint à cardan ainsi qu’au niveau des bagues de roulement des tubes protecteurs. Placer la presse à grosses balles dans un lieu sec, dans un local ne contenant pas d’engrais chimique et n’abritant pas d’animaux. Remédier aux dommages au niveau de la peinture. Enduire abondamment d’huile à base végétale les endroits non recouverts de peinture comme les œillets à ficelle, les noueurs (bec du noueur et disque reteneur de la ficelle) et le canal de pressage. Ne soulever la presse à grosses balles sur sa béquille qu’à l’aide d’un cric adapté. Veiller à ce que la machine soit en position stable sur la béquille. Mettre la presse à grosses balles en appui sur sa béquille pour décharger les pneus (les pneus peuvent être endommagés en cas de maintien prolongé de la presse à grosses balles sur la même position). Protéger les pneus contre les influences extérieures telles que l’huile, la graisse, le rayonnement solaire, etc. Serrer le frein parking et le frein du volant. Laisser s’écouler les condensats des réservoirs d’air comprimé. Procéder aux travaux de révision nécessaires directement après la saison des récoltes. Etablir une liste de toutes les pièces de rechange nécessaires. Ceci facilite le traitement des commandes par les commerçants KRONE. Grâce à toutes ces mesures, la presse à grosses balles sera en état de marche dès le début de la prochaine saison de récolte. III - 11 Mise en service et transport 3.7 Transport 3.7.1Préparatifs pour le déplacement sur route • • • • • • • La conduite sur les voies de communication publiques n’est autorisée que lorsque le canal de pressage est vide et la rampe d’éjection des balles repliée. Respecter la vitesse maximale de déplacement (voir le chapitre 1, Caractéristiques techniques). Le transport de personnes sur la presse à grosses balles n’est pas autorisé. Respecter la charge de traction et d’appui maximale du dispositif d’attelage du tracteur. Contrôler et garantir les mesures de sécurité de transport de la presse à grosses balles, particulièrement l’éclairage, le verrouillage des revêtements de protection ainsi que des volets des boîtes à ficelle, le verrouillage du ramasseur en position haute. Avant le démarrage, veiller à ce que rien ne vienne gêner les conditions de visibilité au niveau du tracteur et entre le tracteur et la presse à grosses balles. Dans le cas des machines avec autorisation d’exploitation, respecter les conditions figurant dans l’autorisation d’exploitation ! Exécuter les travaux suivants avec le déplacement sur route, sur la presse à grosses balles et le tracteur : Levage du ramasseur • Lever le ramasseur et le verrouiller au niveau du robinet d’arrêt (1) pour l’empêcher de retomber. b Le levier se trouve sur le côté gauche à l’avant de la machine au niveau du timon. • 1 Pour lever le ramasseur, le levier doit être poussé de la position (a) vers la position (b). a BPXC0120 Rampe d’éjection à rouleaux à commande hydraulique (option) : • 2 Amener la rampe d’éjection à rouleaux en position pliée par commande hydraulique. Au terme de la manœuvre, veiller à ce que le verrouillage mécanique encastre correctement. 1 Desserrer le frein de parking (voir aussi la section 3.2.3) • Tourner la manivelle dans le sens inverse des aiguilles d’une montre jusqu’à ce que le câble de frein donne un peu de mou. III - 12 BP1213002 Mise en service et transport Vérifier l’installation d’éclairage : • • 1 Contrôler le fonctionnement des feux arrières (2) et des catadioptres (1) et les nettoyer. Procéder de même avec les réflecteurs jaunes situés sur les côtés de la presse à grosses balles ainsi qu’avec les feux de gabarit blancs à l’avant. 2 1 BP1213020 3.7.2 Manœuvre La presse à grosses balles peut être déplacée pour exécuter la manœuvre avec le frein à air comprimé raccordé. Il est interdit d’exécuter la manœuvre de la presse à grosses balles sur la voie publique sans frein à air comprimé raccordé ! 1 Avant d’actionner la soupape de desserrage et/ou d’évacuer la pression du réservoir, immobiliser la machine pour empêcher tout déplacement inopiné. La valve de desserrage se trouve à l’avant, à droite, sous le capot latéral. Dans le cas où une pression minimale de 4 bar est établie dans le réservoir (2) du système de freinage de la presse à grosses balles, le frein peut être desserré en plaçant le bouton-poussoir (1) de la valve de desserrage sur la position (a). Aussitôt que les tuyaux flexibles sont à nouveau raccordés au système de freinage à air comprimé, le bouton-poussoir retourne en position initiale (b). Si la pression d’air dans le réservoir (2) est inférieure à 4 bars, la pression résiduelle doit également être évacuée au niveau de la valve de purge (3). Ce n’est qu’alors que la presse à grosses balles peut être déplacée. 1 a b 3 2 BPXC0212 III - 13 Mise en service et transport 3.7.3 Essieu directeur mené (option) II Veillez à ce que le robinet d’arrêt (1) soit sur la position (I) (ouvert) lors de l’utilisation de la machine. Avant d’exécuter la marche arrière , amener d’abord les roues menées de l’essieu arrière en position rectiligne et appliquer la pression sur le cylindre d’arrêt. Il se peut qu’il soit nécessaire d’exécuter un bref déplacement en ligne droite. Pendant la marche arrière , maintenir la pression sur le raccord hydraulique. En marche avant , amener la soupape du tracteur pour l’essieu directeur en position «Abaisser» afin que les roues puissent s’adapter librement au braquage. Il peut être utile de bloquer l’essieu directeur quand le guide latéral de l’essieu avant non directeur ne suffit pas, par exemple - sur les déclivités, - sur un sol non stabilisé, - pour un déplacement de transport rapide sur une voie non stabilisée. Pour ce faire, appliquer la pression sur le cylindre d’arrêt jusqu’à ce que les roues menées se trouvent en position rectiligne. Maintenir la pression hydraulique pendant la marche avant avec essieu directeur bloqué. 3.7.3.1 Manœuvre de la machine sans raccord hydraulique Pour que la machine puisse être manœuvrée également sans raccorder la conduite hydraulique, il est nécessaire d’appliquer la pression sur les vérins d’arrêt, le robinet d’arrêt étant fermé. III - 14 I 1 BPXC0274 Mise en service et transport 3.8 Immobiliser la presse à grosses balles • • • • • Ne déposer la presse à grosses balles que sur un support plan et stable. Lorsque la presse à grosses balles est déposée sur un support instable, augmenter la surface d’appui de la béquille de support. Empêcher tout déplacement involontaire de la presse à grosses balles en serrant le frein de blocage et en posant des cales d’arrêt. Procéder avec prudence lors de l’abaissement de la béquille de support. Risque d’écrasement des pieds ! Avant de déconnecter les tuyaux hydrauliques, évacuer la pression dans l’installation hydraulique côté tracteur et côté machine. Ne retirer l’arbre à cardan que lorsque la prise de force est déconnectée, le moteur à l’arrêt et la clé de contact retirée. Serrer le frein du volant. Frein parking : • A l’aide de la manivelle (1), serrer le frein parking de la presse à grosses balles. 1 BP1213000 Cales d’arrêt : Les cales d’arrêt (1) se trouvent à l’arrière à gauche et à droite à côté du canal de pressage. • 1 Déposer les cales d’arrêt devant et derrière les pneus. Ceci permet d’empêcher tout déplacement de la machine. BP1213022 Empêcher tout déplacement involontaire de la machine avec essieu tandem à direction traînée (en option) en plaçant des cales. 1 1 BPXC0211 III - 15 Mise en service et transport III - 16 Unité de commande confort 4 Unité de commande confort Machine medium / confort 1 4.1 Description générale L’équipement électronique de la presse à grosses balles est constitué pour l’essentiel de l’ordinateur de tâches, de l’unité de commande et des organes de commande et fonctionnels. BPK40470 L’ordinateur de tâches (1) se trouve à l’avant, à gauche sur la machine, sous le capot latéral. Ses fonctions sont : – Réglage de la densité de compression – Compteur de balles – Commande des actionneurs installés sur la machine – Transmission des messages d’alarme – Diagnostic des capteurs/des actionneurs L’unité de commande (2) donne au conducteur des informations et permet d’exécuter les réglages de la presse à grosses balles, qui sont enregistrés et traités par l’ordinateur de tâches. 2 BPK40481 L’unité de commande (2) doit être protégée de l’eau. Pendant les périodes d’immobilisation prolongée de la presse à grosses balles (par exemple en hiver), l’unité de commande (2) sera entreposée dans un local sec. Avant d’exécuter les travaux de montage et de réparation, en particulier les travaux de soudure sur la presse à grosses balles, sectionner l’alimentation électrique de l’unité de commande (2). L’électronique de l’unité de commande peut être endommagée par surtension. IV - 1 Unité de commande confort 4.2 Montage nstaller l’unité de commande avec la fixation (1) dans le champ visuel du conducteur. 2 Fixation directe • • Mettre en place la fixation (1) en utilisant les alésages existants (2). L’unité de commande (3) est adaptée à la fixation (1) par les plaques magnétiques (4). 1 ZX000027 4 3 1 ZX000029 IV - 2 Unité de commande confort Alimentation en tension Pendant le montage, veiller à ne pas tendre le câble de liaison électrique et à ce qu’il n’entre pas en contact avec les roues du tracteur. • • Raccordez le câble de tension (12 V) à la prise de courant à 3 pôles (DIN 9680) côté tracteur et au connecteur Delphi (5) côté machine. Le connecteur Delphi (5) est situé dans le sens de déplacement, côté gauche de la machine, sur le capotage et à proximité du volant. 2 3 BPK40480 Unité de commande • Raccordez le câble fourni à la douille (4) située, dans le sens de déplacement, à gauche sur le capotage et à proximité du volant, et à la douille (3) de l’unité de commande. 4 5 BPK40659 IV - 3 Unité de commande confort 4.3 Unité de commande Vue d’ensemble 1 2 3 7 1 Touche marche/arrêt 2 Afficheur 3 Touches (1 à 8) 4 Potentiomètre rotatif 5 Touche Esc (F) 6 Touche de menu (E) 7 Touches A à D IV - 4 6 5 4 BPK41010 Unité de commande confort Description des touches Touches 1 à 8 Les touches 1 à 8 servent pour activer les touches sensitives de la colonne de droite. L’affectation est donnée par l’illustration. S’il n’y a pas de touche sensitive à côté de la touche, la touche n’a pas de fonction. Potentiomètre rotatif Le potentiomètre rotatif a deux fonctions : 1. Par rotation du potentiomètre, modifier les réglages et sélectionner le menu souhaité au niveau du menu. 2. Les réglages sont sauvegardés en appuyant sur le potentiomètre rotatif. Si l’afficheur donne plusieurs possibilités de réglage, le symbole BPK40013 bascule automatiquement sur la possibilité de réglage suivante. Pendant le fonctionnement, le symbole devrait être en position de parking afin de prévenir la modification inopinée des réglages. retourne en position de parking après environ 15 secondes d’inactivité. BPK40014 Touches A à D Les touches A à D servent pour activer les touches sensitives de la ligne supérieure. L’affectation est donnée par l’illustration. S’il n’y a pas de touche sensitive au-dessus de la touche, la touche n’a pas de fonction. Touche E La touche sert pour appeler le niveau de menu. Touche F La touche sert pour accéder à l’écran précédent ou au niveau de menu précédent. Retour à l’écran initial en appuyant un certain temps sur la touche. 4.4 Ordre de marche Mise sous tension • Appuyer sur la touche . La liaison avec l’ordinateur de tâchesest établie après la mise sous tension. Le message ci-contre est affiché si la connexion n’est pas possible. Vérifiez les connexions CAN et l’ordinateur des tâches. Après établissement de la connexion, l’écran «Mode manuel» (voir le chapitre 4.5.1) est affiché. BPK41011 IV - 5 Unité de commande confort 4.5 Mode manuel 4.5.1 Ecran initial Mode manuel 1/2 BPK41017_4 IV - 6 Unité de commande confort Ligne d’état Les états actuels de la machine sont affichés sur la ligne supérieure de l’écran (en fonction des équipements) : • Message d’alarme en attente • Volets de pressage ouverts, si l’arbre de • rendement max. pour inversion totale. clignote en rendement faible si l’inversion n’est pas activée en pressage => vérifier le capteur d’alimentation de l’empaqueteur. prise de force tourne, le symbole • volets de pressage fermés clignote • Rampe d’éjection des balles en haut Touches sensitives : Les touches sensitives suivantes se trouvent sur la ligne inférieure : Rampe d’éjection des balles en bas • Rendement de la machine Barre de coupe en haut ou les couteaux sont activés : coupe en cours • Dépose de balles en cours Commutation Mode manuel/automatique Le fonctionnement actif est affiché. Commutation sur Mode automatique Barre de coupe en bas ou les couteaux sont Appuyer sur la touche inactivés : pas de coupe • sensitive Extraction de l’éjecteur de balles Rentrée de l’éjecteur de balles pour la touche • Ajuster le compteur client Appuyer sur la touche sensitive pour la touché . Le menu 2-1 «Compteur client» est affiché. (Réglages: voir le chapitre 4.9.9) • Information sur le pressage Appuyer sur la touche pour la touche sensitive (pour une description, voir le chapitre 4.9.16) • Commutation menu de base page 1/2 sur page 2/2 La page active est affichée . Commutation sur page 2/2 Appuyer sur la touche pour touche sensitive IV - 7 Unité de commande confort 4.5.2 Ecran initial Mode manuel 2/2 BPK41012_3 Touches sensitives : Les touches sensitives suivantes se trouvent dans la colonne de droite de la page 1/2 : • Les touches sensitives suivantes se trouvent dans la colonne de droite de la page 2/2 : • Appuyer sur la touche Abaisser la rampe d’éjection des balles pour touche • Libérer les volets de pressage pour la touche Appuyer sur la touche sensitive • pour touche sensitive Abaisser la rampe d’éjection des balles Appuyer sur la touche Activer le noueur Lever/Abaisser la barre de coupe Le fonctionnement actif est affiché. Lever la barre de coupe Appuyer sur la touché • Ejecteur de balles automatique Ejecteur de balles pour la touche sensitive Abaisser la barre de coupe Appuyer sur la touche sensitive Appuyer sur la touche pour la touche sensitive pour la touché Les volets de pressage sont libérés. Appuyer une nouvelle fois sur la touche sensitive pour la touche sensitive , le symbole est affiché en couleurs inver ses. 10 éjections de balles sont exécutées. IV - 8 Unité de commande confort Affichages de la fenêtre principale (en fonction de l’équipement de la machine) • Force de compression actuelle en % (100% = max.) • Total actuel de balles du compteur client • • Indicateur de densité de pressage actuelle en mm ou en pouce. (uniquement pour réglage électrique de longueur de balle) Nombre de couches par balle • Vitesse actuelle de l’arbre de prise de BPK40442_3 force (tr/min) • Affiché un instant après nouage,s’il est • activé (voir le chapitre 4.9.4) signal sonore (avertisseur ~ 1 sec) Indicateur de direction de déplacement Flèches (1) à gauche/droite de l’affichage. Les flèches (1) ont trois dimensions différentes, numérotées de 1 à 3. Elles indiquent au conducteur sur quel côté et avec quelle intensité il doit corriger la direction pour franchir l’andain pour assurer une alimentation régulière de la chambre de compression. Si les avertissements de conduite sont trop forts ou trop faibles, ils peuvent être adaptés (voir le chapitre 4.9.5) 1 BPK40500 IV - 9 Unité de commande confort • Pression des volets de pressage (en bar) La valeur sous la barre indicatrice et la hauteur de barre (1) donnent la pression actuelle sur les volets de pressage. La valeur au-dessus de l’indicateur de barre et la flèche sur la barre indicatrice (2) donnent la valeur de pression de consigne qui a été réglée en bar. • 2 Balles multiples (en option) La première valeur (1) donne le nombre de balles multiples pressées actuellement. La deuxième valeur et la petite flèche (2) donnent le nombre de consignes des balles multiples par grosse balle. Chaque balle multiple est signalée par un signal sonore bref et la fin des balles est indiquée par un signal sonore long. • 1 BPK40510 1 2 Indicateur de longueur de balles (uniquement pour réglage électrique de longueur de balle) La première valeur sous la barre indicatrice et la longueur de la barre (3) donnent l’état réel de longueur de balles. La deuxième valeur et la grande flèche (4) donnent la valeur de consigne de longueur de balle. 4 3 BPK40550 IV - 10 Unité de commande confort Réglage de la pression de consigne des volets presseurs En Mode manuel, la pression est ajustée par l’utilisateur. Lorsque la prise de force fonctionne et que la machine est à l’arrêt, la pression est immédiatement établie ; les variations de pression affichées sur l’écran sont très faibles. Si la pression réglée est excessive, la machine peut être soumise à une surcharge mécanique pendant la compression, ce qui risque de provoquer la destruction. Pour prévenir ce risque, abaisser la pression sur les volets de pressage à une valeur inférieure, immédiatement avant la surcharge. Après quelques secondes, la pression réglée par l’utilisateur est rétablie. En cas de surcharge, réduire la pression de consigne des volets de pressage. Régler la pression de consigne sur les volets de pressage • Tourner le potentiomètre rotatif jusqu’à ce que le symbole se trouve devant la valeur de consigne A de pression sur les volets de pressage (A). • • Ajuster la pression de consigne sur les volets de pressage en tournant le potentiomètre rotatif. Appuyer sur le potentiomètre rotatif jusqu’à ce que le symbole B BPK40441_3 soit en position de parking (B). Réglage de longueur de balles (uniquement pour réglage électrique de longueur de balle) (BP 890 ; 1270 ; 1290) Les balles peuvent être réglées sur une longueur de 100 à 270 cm (39 à 106 pouces). (BP1290 HDP; BP 12130) Les balles peuvent être réglées sur une longueur de 100 à 320 cm (39 à 126 pouces). Pour éviter qu’une longueur divergente apparaisse en cours de fonctionnement, la longueur de balles devrait être réglée au début de la mise en balles. • Tourner le potentiomètre rotatif jusqu’à ce que le symbole • • se trouve devant la valeur de consigne de longueur de balles (A). Ajuster la longueur de balle souhaitée en tournant le potentiomètre rotatif. Appuyer sur le potentiomètre rotatif jusqu’à ce que le symbole soit en position de parking (B). A B BPK40461_3 IV - 11 Unité de commande confort Réglage du nombre de balles multiples (uniquement MultiBale) Régler d’abord la longueur de balles. Longueur minimale de balle multiple : 45 cm (17,7 inch). A Pour éviter le mélange de balles totales et de balles multiples, la modification du nombre de balles multiples ne sera exécutée qu’au début de la mise en balles. • Tourner le potentiomètre rotatif jusqu’à ce que le symbole • • se trouve devant le symbole (A). Ajuster le nombre de balles multiples souhaité en tournant le potentiomètre rotatif. Appuyer sur le potentiomètre rotatif jusqu’à ce que le symbole IV - 12 soit en position de parking (B). B BPK40451_3 Unité de commande confort 4.6 Mode automatique BPK41015_3 Description générale, voir le chapitre 4.5 Mode manuel Réglage de la consigne de la force de compression Différences par rapport au Mode manuel En mode automatique la pression est réglée automatiquement grâce à la force du piston mesurée. Touches sensitives : • Commutation Mode manuel/automatique Le fonctionnement actif est affiché. Commutation sur Mode manuel Appuyer sur la touché L’indicateur de pression sur l’afficheur peut fluctuer considérablement. Le réglage ne fonctionne que quand l’empaqueteur alimente le piston en fourrage. pour la touche sensitive Indicateurs de la fenêtre principale : • • Pression actuelle du volet de pressage en 2 bar Force de compression (en %) La valeur sous la barre indicatrice et la hauteur de barre (1) donnent la pression actuelle en %. La valeur au-dessus de la barre indicatrice et la flèche sur la barre indicatrice (2) donnent la valeur de la force de compression consigne qui a été réglée en %. 1 BPK40560 IV - 13 Unité de commande confort 4.7 Boutons-poussoirs sur la machine La variante confort de la machine possède plusieurs boutons-poussoirs externes permettant d’exécuter des fonctions au niveau de la machine. 1. A l’avant du côté gauche de la machine sur la face avant de la boîte à ficelle se trouvent deux boutonspoussoirs. Ces deux boutons ont les fonctions suivantes : 1 2 (1) Monter la barre de coupe BPK40640 (2) Descendre la barre de coupe 2. A l’arrière du côté gauche de la machine se trouvent 4 boutons-poussoirs. Ces boutons ont les fonctions suivantes : (1) Déplacer l’éjecteur de balles vers l’avant (2) Déplacer l’éjecteur de balles vers l’arrière Appuyer sur la touche , les volets de pressage sont libérés. Appuyez brièvement sur la touche 2 3 4 BPK40630 , 10 éjections de balles sont exécutées ou appuyez plus longtemps sur la touche , l’éjecteur de balles se déplace vers l’arrière (3) Lever la rampe d’éjection des balles (4) Descendre la rampe d’éjection des balles IV - 14 1 Unité de commande confort 4.8 Description de la compression des balles 4.8.1 Canal de pressage vide 4.8.2 Canal de pressage plein A l’activation de l’unité de commande, l’indicateur est toujours sur Mode manuel. Comme le chapitre 4.8.1, avec cette différence : Pour ce réglage et afin de prévenir la torsion des volets de pression, travaillez d’abord avec une pression du canal de pression de 50 bar env. (pour la paille) et 25 bar (pour l’ensilage). Quand le canal de pressage est plein, augmenter la pression pour que les balles aient la consistance souhaitée. Pour obtenir des balles de densité régulière malgré les caractéristiques variables du matériau (par exemple différence d’humidité du matériau sur le même champ), commuter ensuite sur le Mode automatique. La force de compression établie précédemment en Mode manuel est transférée. La force de pression des volets de pressage dans le canal de pressage est réglée automatiquement par l’ordinateur de tâchesde manière à ce que la force de compression réglée soit établie. La compression des balles devient plus difficile pour une humidité plus forte et, pour cette raison, la pression sur les volets de pressage sera légèrement diminuée. Pour le matériau sec, augmenter la pression sur les volets de pressage. L’indicateur de pression sur l’afficheur peut fluctuer fortement. La qualité et la densité des balles restent constantes. 1. Pour presser en Mode automatique, activer le Mode automatique immédiatement après le démarrage de la machine. La dernière pression de consigne opérationnelle est affectée, c’est-à-dire qu’il est possible de travailler avec les mêmes réglages après déconnexion et activation de la machine. L’indication de la pression ne doit pas avoir été modifiée après la mise sous tension de la commande en Mode manuel, car, dans ce cas, la commande ne conserverait pas les derniers réglages. 2. Lorsque la compression doit être effectuée en Mode manuel, la pression peut être réglée sur la valeur souhaitée directement après le démarrage de la commande. Information : La force de compression est mesurée par deux capteurs sur la partie intérieure de la partie avant du châssis, amplifiée et transmise à l’ordinateur de tâches. L’ordinateur de tâchesanalyse les signaux et ajuste la pression sur le cylindre hydraulique de volet de pressage. Les signaux sont aussi utilisés par l’unité de commande pour l’indication de la direction de déplacement. Les avertissements de l’indicateur de direction de déplacement sont amplifiés à mesure que la différence s’accentue pour la pression mesurée par le capteur de gauche et le capteur de droite. Si les avertissements de conduite sont trop forts ou trop faibles, ils peuvent être adaptés (voir le chapitre 4.9.5) IV - 15 Unité de commande confort 4.9 Niveau de menu Vue d’ensemble Valeur de correction longuer des balles 1-1 1-2 Signal de noueur 1 Réglages 1-3 2-1 Sensibilité Indicateur de direction Compteur client 2 Compteurs 1-4 2-2 Compteur global 4 Service Contraste 1-5 4-2 5 Information 4-4 6 Installateur Graissage centralisé Test manuel des capteurs Test manuel des actionneurs 4-5 Alarmes actuelles BPK40420 6-1 Réglages 4.9.1 Appeler le niveau de menu • Appuyer sur la touche (1). Le niveau de menu est affiché. Quitter le niveau de menu en appuyant sur la touche (2). 1 IV - 16 2 BPK40011 Unité de commande confort Le niveau de menu est divisé en cinq menus principaux : • = Menu principal 1 « Réglages » • = Menu principal 2 « Compteurs » • = Menu principal 4 « Service » • = Menu principal 5 « Information » • = Menu principal 6 « Installateur » • Sélectionner les menus principaux avec le potentiomètre rotatif ; le symbole sélectionné est affiché en couleurs inverses : • Appeler le niveau de menu du menu principal qui a été sélectionné en appuyant sur le potentiomètre rotatif. • Abandonner le menu qui a été appelé en appuyant sur la touche BPK40020 . 4.9.2 Menu principal 1 « Réglages » Appeler le menu principal • Appeler le niveau de menu en appuyant sur la touche • . Sélectionner le menu principal 1 sur le potentiomètre rotatif, le symbole est affiché en couleurs inverses. • Appuyer sur le potentiomètre rotatif. L’écran affiche le niveau de menu 1 « Réglages ». En fonction de l’équipement de la machine, le niveau de menu 1 « Réglages » est divisé en cinq menus : • = Menu 1-1 « Valeur de correction de longueur des balles » • = Menu 1-2 « Signal de noueur » • = Menu 1-3 « Sensibilité indicateur de BPK40020 direction » • = Menu 1-4 « Contraste » • = Menu 1-5 « Graissage centralisé » • = Menu 1-6 « Soufflante du noueur » • = Menu 1-7 « Unité de mesure » BPK40031 IV - 17 Unité de commande confort 4.9.3 Menu 1-1 « Valeur de correction de longueur des balles » (Sur les machines avec réglage électrique de longueur de balles) Les variations de caractéristiques du matériau (par exemple paille, ensilage) peuvent modifier la longueur de balle réelle par rapport à la valeur de consigne. L’écart est corrigé avec la valeur de correction. Réglages ex usine : 100% Appeler le menu Le menu principal 1 « Réglages » a été appelé • Sélectionner le menu 1-1 BPK40031 sur le potentiomètre rotatif, le symbole est affiché en couleurs inverses. • Appuyer sur le potentiomètre rotatif. L’écran affiche le menu 1- 1 « Valeur de correction de longueur de balles ». La barre indicatrice et la valeur en pour-cents donnent la valeur de correction qui a été réglée. sur la ligne supérieure indique que la Le symbole valeur a été sauvegardée. BPK40081 Régler et sauvegarder la valeur de correction Réduire la valeur de correction si les balles sont trop longues ; augmenter si les balles sont trop courtes. • Régler la valeur de correction sur le potentiomètre de la ligne supérieure s’éteint. rotatif, le symbole • Appuyer sur le potentiomètre rotatif, la valeur réglée est sauvegardée, le symbole est affiché sur la ligne supérieure. • Abandonner le menu qui a été appelé en appuyant sur la touche . L’écran affiche le niveau de menu 1 « Réglages ». • Appeler l’écran initial en appuyant deux fois sur la touche IV - 18 . Unité de commande confort 4.9.4 Menu 1-2 « Signal de noueur » Activation/désactivation d’un signal sonore lors de la réalisation d’un nœud. Appeler le menu Le menu principal 1 « Réglages » a été appelé • Sélectionner le menu 1-2 sur le potentiomètre rotatif, le symbole est affiché en couleurs inverses. • Appuyer sur le potentiomètre rotatif. BPK40051 L’écran affiche le menu 1-2 « Signal de noueur ». L’état actuel est affiché sous forme de symbole : • = Signal de noueur activé • = Signal de noueur désactivé Le symbole sur la ligne supérieure indique que l’état affiché a été sauvegardé. Modifier et sauvegarder l’état BPK40041 • Régler l’état sur le potentiomètre rotatif, le symbole de la ligne supérieure s’éteint. • Appuyer sur le potentiomètre rotatif, l’état réglé est sauvegardé, le symbole est affiché sur la ligne supérieure. • Abandonner le menu qui a été appelé en appuyant sur la touche . L’écran affiche le niveau de menu 1 « Réglages ». • Appeler l’écran initial en appuyant deux fois sur la touche . IV - 19 Unité de commande confort 4.9.5 Menu 1-3 « Sensibilité indicateur de direction » Régler la sensibilité de l’indicateur de la direction. Appeler le menu Le menu principal 1 « Réglages » a été appelé • Sélectionner le menu 1-3 sur le potentiomètre rotatif, le symbole est affiché en couleurs inverses. • Appuyer sur le potentiomètre rotatif. BPK40071 L’écran affiche le menu 1-3 « Sensibilité indicateur de direction ». La barre indicatrice donne la sensibilité qui a été réglée. La sensibilité de direction est d’autant plus grande que la barre est élevée. Le symbole sur la ligne supérieure indique que la valeur affichée a été sauvegardée. Régler et sauvegarder l’indicateur de direction de sensibilité Les avertissements de conduite matérialisés par la forme de la flèche (1) sont d’autant plus intenses que la sensibilité de l’indicateur de direction est élevée. • Régler la sensibilité sur le potentiomètre rotatif, le symbole • BPK40061 de la ligne supérieure s’éteint. 1 Appuyer sur le potentiomètre rotatif, la sensibilité réglée est sauvegardée, le symbole est affiché sur la ligne supérieure. • Abandonner le menu qui a été appelé en appuyant sur la touche . BPK40500 L’écran affiche le niveau de menu 1 « Réglages ». • Appeler l’écran initial en appuyant deux fois sur la touche IV - 20 . Unité de commande confort 4.9.6 Menu 1-4 « Contraste » Réglage du contraste d’écran. Appeler le menu Le menu principal 1 « Réglages » a été appelé • sur le Sélectionner le menu 1-4 potentiomètre rotatif, le symbole est affiché en couleurs inverses. • Appuyer sur le potentiomètre rotatif. BPK40091 L’écran affiche le menu 1-4 « Contraste ». La barre indicatrice donne la valeur de contraste qui a été réglée. Le symbole sur la ligne supérieure indique que la valeur a été sauvegardée. Régler et sauvegarder le contraste Le contraste de l’afficheur est d’autant plus fort que la barre est élevée. • Régler le contraste sur le potentiomètre rotatif, le de la ligne supérieure s’éteint. symbole • BPK40101 Appuyer sur le potentiomètre rotatif, le contraste réglé est sauvegardé, le symbole est affiché sur la ligne supérieure. • Abandonner le menu qui a été appelé en appuyant sur la touche . L’écran affiche le niveau de menu 1 « Réglages ». • Appeler l’écran initial en appuyant deux fois sur la . touche ZX000021 Affichage jour et nuit Les couleurs de l’écran sont inversées en basculant de jour sur nuit. • Appuyer sur la touche • sur la touche . pour la touche sensiti• ve Abandonner le menu qui a été appelé en appuyant . Appeler l’écran de base en appuyant assez longtemps sur la touche . Les couleurs de l’afficheur sont inversées. Réinitialiser l’afficheur : • Appuyer sur la touche ve pour la touche sensiti- . L’afficheur est réinitialisé : IV - 21 Unité de commande confort 4.9.7 Menu 1-5 «Graissage centralisé» (Sur les machines avec graissage centralisé) Réglage de la périodicité et de la durée du graissage. Appeler le menu Le menu principal 1 « Réglages » a été appelé sur le • Sélectionner le menu 1-5 • potentiomètre rotatif, le symbole est affiché en couleurs inverses. Appuyer sur le potentiomètre rotatif. L’écran affiche le menu 1-5 « Graissage centralisé ». La valeur supérieure (A) indique la durée de graissage, la valeur inférieure (B) la durée de pause de graissage. BPK40111 sur la ligne supérieure indique que la Le symbole valeur affichée a été sauvegardée. La durée de graissage peut être augmentée de quelques minutes. La lubrification centralisée est réglée ex usine pour un fonctionnement optimal. A Presses jusqu’au numéro de machine 770 299: Réglage en usine : Sans graissage d’empaqueteur Avec graissage d’empaqueteur Durée de graissage 16 min (A) 22 min (A) Pause de graissage 30 min (B) 30 min (B) Le réservoir de l'installation de lubrification centralisée des presses à partir du numéro de machine 770 299 a un volume de 2,5 kg Presses à partir du numéro de machine 770 300 : Durée de graissage : 20 min (A) Pause de graissage: 5 min (B) Le réservoir de l'installation de lubrification centralisée des presses à partir du numéro de machine 770 300 a un volume de 4,5 kg IV - 22 B BPK40121 Unité de commande confort • Appuyer sur la touche pour la touche sensitive DEF : les valeurs du réglage ex usine sont transférées, il se peut que le symbole de la ligne supérieure s’éteigne. • Régler la sensibilité sur le potentiomètre rotatif, le de la ligne supérieure s’éteint. symbole • Appuyer sur le potentiomètre rotatif, la valeur chronométrique est sauvegardée, le symbole est affiché sur la ligne supérieure. Déclenchement manuel du graissage • Appuyer sur la touche pour la touche sensitive Le graissage est lancé pour la durée qui a été réglée. • Abandonner le menu qui a été appelé en appuyant sur la touche . L’écran affiche le niveau de menu 1 « Réglages ». • Appeler l’écran initial en appuyant deux fois sur la touche . IV - 23 Unité de commande confort 4.9.8 Menu principal 2 « Compteurs » Appeler le menu principal • Appeler le niveau de menu en appuyant sur la touche • . Sélectionner le menu principal 2 sur le potentiomètre rotatif, le symbole est affiché en couleurs inverses. • Appuyer sur le potentiomètre rotatif. BPK40130 L’écran affiche le niveau de menu 2 « Compteurs ». Le niveau de menu 2 « Compteurs » est divisé en 2 menus : • = Menu 2-1 « Compteur client » • = Menu 2-2 « Compteur global » 4.9.9 Menu 2-1 « Compteur client » Appeler le menu BPK40140 Le menu principal 2 « Compteurs » a été appelé • Sélectionner le menu 2-1 sur le potentiomètre rotatif, le symbole est affiché en couleurs inverses. • Appuyer sur le potentiomètre rotatif. L’écran affiche le menu 2-1 « Compteur client ». Signification des symboles : • = nombre total de balles • = nombre de balles non coupées • = nombre de balles coupées BPK40140 (Uniquement pour les machines avec X-Cut) • = compteur de durée de service • (n’est actif que quand l’arbre de prise de force tourne) = compteur client (1 - 20) • • 2 m ft = Compteur de longueur de balles IV - 24 n A (unité de mesure métrique en mètres) 50 = Compteur de longueur de balles 20 (unité de mesure US en pieds) = Compteur de nœuds (y compris nœuds « balles multiples w») Le compteur client activé (A) est affiché en couleurs inverses. • 2-1 30 2 h m 1.5 100.0 50 BPK40150 Unité de commande confort Activer le compteur client • Sélectionner le compteur du client (A) souhaité en tournant le potentiomètre rotatif et activer en appuyant sur celui-ci. 2 50 ). Activation du compteur de balles (balles coupées et non coupées) Le compteur activé est affiché en couleur inverse „ „ (ici, le compteur de balles non coupées) et représenté en tant que touche sensitive • n A Le compteur client souhaité (dans notre cas le compteur client 2) est affiché en couleurs inverses ( 2-1 Appuyer sur la touche 20 30 2 h m 1.5 100.0 50 BPK40150 . pour touche sensitive afin d’activer le compteur „balles coupées“. Modifier le nombre de balles • • • Sélectionner le compteur du client (A) souhaité en tournant le potentiomètre rotatif et activer en appuyant sur celui-ci. sélectionner le compteur à changer (balles coupées, balles non coupées) Appuyer sur la touche ve • pour la touche sensiti- et incrémenter le nombre des balles. Appuyer sur la touche pour la touche sensitive et décrémenter le nombre des balles. Simultanément, le compteur saisonnier et le compteur journalier du menu 2-2 « Compteur totalisateur de balles » (voir chapitre 4.9.10) ainsi que les compteurs de longueurs et de nœuds sont modifiés. Remise à zéro du compteur client • Avec le potentiomètre rotatif, amener le compteur client devant être effacé entre les deux barres transversales (A). • Appuyer sur la touche sensitive pour la touche . Le compteur client qui a été sélectionné est remis à zéro. • Abandonner le menu qui a été appelé en appuyant sur la touche . L’écran affiche le niveau de menu 2 « Compteurs ». • Appeler l’écran initial en appuyant deux fois sur la touche . IV - 25 Unité de commande confort 4.9.10 Menu 2-2 « Compteur total » Appeler le menu Le menu principal 2 « Compteurs » a été appelé • Sélectionner le menu 2-2 sur le potentiomètre rotatif, le symbole est affiché en couleurs inverses. • Appuyer sur le potentiomètre rotatif. L’écran affiche le menu 2-2 « Compteur total». Le total des balles est la somme de toutes les balles qui ont été pressées. Aucun compteur client n’y est affecté. BPK40160 Signification des symboles : • = nombre total de balles • = nombre de balles non coupées • = nombre de balles coupées (uniquement pour les machines avec X-Cut) • = compteur de durée de fonctionnement • = compteur de balles (indélébile) • = compteur saisonnier 1 (peut être effacé) • = compteur journalier 2 (peut être effacé) Effacer le compteur saisonnier 1, le compteur journalier 2 • Appuyer sur la touche sensitive pour la touche . Le compteur saisonnier 1 est remis à zéro. • Appuyer sur la touche sensitive pour la touche . Le compteur journalier 2 est remis à zéro. • Abandonner le menu qui a été appelé en appuyant sur la touche . L’écran affiche le niveau de menu 2 «Compteurs». • Appeler l’écran initial en appuyant deux fois sur la touche IV - 26 . BPK40170 Unité de commande confort 4.9.11 Menu principal 4 « Service » Appeler le menu principal • Appeler le niveau de menu en appuyant sur la touche • . Sélectionner le menu principal 4 sur le potentiomètre rotatif, le symbole est affiché en couleurs inverses. • Appuyer sur le potentiomètre rotatif. L’écran affiche le niveau de menu 4 « Service ». BPK40180 Le niveau de menu 4 « Service » est divisé en 2 menus : • = Menu 4-2 « Test manuel des capteurs » • = Menu 4-4 « Test manuel des actionneurs » • = Menu 4-5 « Alarmes actuelles » 4.9.12 Menu 4-2 «Test manuel des capteurs» BPK40190 Le test manuel des capteurs contrôle l’absence de défaut des capteurs installés sur la machine de plus, le test manuel des capteurs peut aussi servir pour ajuster correctement les capteurs. La garantie de bon fonctionnement de la machine n’est donnée que quand les capteurs sont réglés correctement. La prise de force ne doit pas tourner lors du test des capteurs. Appeler le menu Le menu principal 4 « Service » est affiché. BPK40190 • Sélectionner le menu 4-2 sur le potentiomètre rotatif, le symbole est affiché en couleurs inverses. • 4-2 Appuyer sur le potentiomètre rotatif. state: 8,3V L’écran affiche le menu 4-2 « Test manuel de capteur ». 1 7,3V Sélectionner le capteur • Sélectionner le capteur avec le potentiomètre rotatif. Le capteur sélectionné est affiché en couleurs inverses et soumis à un test. B10 5,2V B4 2,4V 7,8V BPK40200 IV - 27 Unité de commande confort Diagnostic des capteurs de type Namur 4-2 Etat (state) : • state: métallisé sous vide (fer) • non métallisé sous vide (pas de fer) • rupture de câble • court-circuit 8,3V 1 7,3V B10 5,2V B4 2,4V 7,8V Valeurs de réglage : La partie supérieure de la barre indicatrice donne la valeur de réglage minimale et maximale du capteur métallisé (métal sur capteur). La valeur de réglage actuelle (valeur instantanée) est affichée sous la barre indicatrice. BPK40200 L’écart entre le capteur et le métal doit être réglé de telle manière que l’état métallisé des barres se trouve sur la marque supérieure. Vérifier ensuite si la barre à l’état non métallisé se trouve dans le domaine de la marque inférieure. Capteurs possibles (en fonction de l’équipement de la machine) Description N° B1 Frein du volant B12 Dépose de balles B2 Barre de coupe supérieure B14 Ejecteur de balles B3 Lubrification centralisée B20 Ramasseur B4 Mesurer B5 Etalonner B6 Contrôle de l’empaqueteur B7 Alimentation de l’empaqueteur B8 Contrôle de ficelle B9 Tige de traction d’aiguille B10 Contrôle de noueur N° B11 IV - 28 Symbole de capteur Rampe d’éjection des balles Symbole de capteur Description * Décompte des capteurs en commençant dans le sens de déplacement de gauche à droite Unité de commande confort Diagnostic de bouton-poussoir Etat (state) : • rupture de câble • court-circuit • actionné • non actionné Valeurs de réglage : Quand le bouton-poussoir est appuyé, la barre doit se trouver dans la partie marquée inférieure de la barre indicatrice et se situer dans la partie supérieure quand l’action cesse sur le bouton-poussoir. BPK40210 Boutons-poussoirs possibles (en fonction de l’équipement de la machine) Description N° S1 Bouton-poussoir barre de coupe monte S4 Bouton-poussoir de sortie de l’éjecteur de balles S2 Bouton-poussoir barre de coupe baisse S5 Bouton-poussoir rampe d’éjection de balles monte S3 Bouton-poussoir de rentrée de l’éjecteur de balles S6 Bouton-poussoir rampe d’éjection de balles baisse N° Symbole Symbole Description Diagnostic des capteurs analogiques Etat (state): 4-2 • Rupture de câble ou court-circuit • Défaut du capteur ou de l’ordinateur de tâches La barre doit se trouver dans la partie marquée de la barre indicatrice. Capteurs analogiques possibles (en fonction de l’équipement de la machine) B15 B17 B21 Symbole 5,1 V B17 Valeurs de réglage : N° state S2 Description B15 0,9V 3,0V BPK40521 Disque soleil (tourner le disque soleil : pour une rotation complète, la barre doit se trouver dans la zone marquée) Pression du volet de pressage (pour une pression de 0 bar, la barre doit se trouver dans la partie inférieure de la zone marquée) Balles multiples (contrôle du bon fonctionnement du capteur, le réglage doit être effectué lors de la mise au point par le monteur) IV - 29 Unité de commande confort Diagnostic des capteurs de force Les messages d’état ne sont valables que pour autant que les capteurs de force ont été réglées correctement au préalable. Etat (state): • Rupture de câble ou court-circuit • Défaut du capteur/de l’amplificateur de mesure de force ou de l’ordinateur de tâches Valeurs de réglage : Si un capteur a été changé ou si la barre se trouve à l’extérieur de la marque extérieure, l’amplificateur de force des barres doit être réglé sur le potentiomètre de manière qu’il se trouve sur la marque intérieure. BPK40531 Marque intérieure La barre doit se trouver entre les marques ,8 V et 2,0 V 1,8 V et 2,0 V : La barre doit se trouver entre 1,1 V et 4,0 V Capteurs de force N° Symbole Description B18 Effort de piston gauche B19 Effort de piston droite Diagnostic des tensions d’alimentation Tensions de consigne : • • • • • • • 12V total : 12V term : SS_5V : 8V ana : 8V num : 12V Pow2 : 12V Pow3 : 12 - 14,5 V 12 - 14,5 V 4,5 - 5,5 V 8,5 - 9,1 V 8,5 - 9,1 V 12 - 14,5 V 12 - 14,5 V BPK40220 N° Symbole Description U1 • Tension d’alimentation Abandonner le menu qui a été appelé en appuyant sur la touche . L’écran affiche le niveau de menu 4 « Service ». • Appeler l’écran initial en appuyant deux fois sur la touche IV - 30 . Unité de commande confort 4.9.13 Menu 4-4 «Test manuel des actionneurs» Le test des actionneurs permet de tester les actionneurs de la machine. Les actionneurs ne peuvent être testés que s’ils sont sous tension. En conséquence, le test des actionneurs consiste à piloter à la main les actionneurs sur une course réduite afin de détecter les défauts éventuels. Pendant le test des actionneurs, la prise de force ne doit pas tourner. Les actionneurs sont pilotés pendant le test. Ceci peut conduire à des réactions imprévisibles de la machine. C’est pourquoi ce test doit être réalisé dans une position sûre en dehors de la zone d’action des pièces de la machine mises en mouvement par les actionneurs. Appeler le menu Le menu principal 4 « Service » est affiché. • Sélectionner le menu 4-4 sur le potentiomètre rotatif, le symbole est affiché en couleurs inverses. • Appuyer sur le potentiomètre rotatif. BPK40230 L’écran affiche le menu 4-4 « Test manuel des actionneurs ». Sélectionner l’actionneur • Sélectionner l’actionneur avec le potentiomètre rotatif. L’actionneur sélectionné est affiché en couleurs inverses. BPK40240 IV - 31 Unité de commande confort Diagnostic des actionneurs numériques Les défauts ne sont signalés que quand l’actionneur est activé et qu’un test est possible pour l’actionneur (voir le tableau « Actionneurs numériques possibles »). Si nécessaire, le contrôle peut être exécuté directement sur la DEL du connecteur. • Appuyer sur la touche pour la touche sensitive Etat (state): BPK40240 • acteur activé • acteur désactivé • erreur générale au niveau d’un acteur • pas de tension d’alimentation, vraisemblablement défaut de fusible Actionneurs numériques possibles (en fonction de l’équipement de la machine) N° Y01 Symbole Description N° Soupape principale Y14 Symbole Description BigBale (Identification du défaut impossible) Y02 Soupape principale Y15 Balles multiples (Identification du défaut impossible) Y03 Rampe d’éjection des balles Y30 Nettoyage de noueur (Identification du défaut impossible) Y04 Rampe d’éjection des balles Y31 Lubrification centrale Y05 Ejecteur de balles M1 Déclenchement de noueur Y06 Ejecteur de balles Y07 Barre de coupe Y08 Barre de coupe Y09 Soupape de libération des volets de pressage IV - 32 (Identification du défaut impossible) Unité de commande confort Diagnostic des actionneurs analogiques (par exemple soupape régulatrice de pression) Une intensité (en mA) peut être réglée par modulation d’impulsions en largeur (en pour mille). Pour une modulation d’impulsion en largeur = 500, l’intensité du courant devrait être entre 1 000 mA et 3 000 mA (en fonction de la soupape utilisée et de la température de fonctionnement) • Appuyer sur la touche pour la touche sensitive , la modulation d’impulsions de largeur est incrémentée. • BPK40250 Appuyer sur la touche pour la touche sensitive , la modulation d’impulsions de largeur est décrémentée. Etat (state): • acteur activé • acteur désactivé • pas de tension d’alimentation, vraisemblablement défaut de fusible Actionneurs analogiques possibles N° Symbole Description Y11 • Soupape de régulation Abandonner le menu qui a été appelé en appuyant sur la touche . L’écran affiche le niveau de menu 4 « Service ». • Appeler l’écran initial en appuyant deux fois sur la touche . IV - 33 Unité de commande confort 4.9.14 Menu 4-5 « Alarmes actuelles » Les défauts en attente actuellement sont affichés sous la rubrique « Alarmes actuelles ». Appeler le menu Le menu principal 4 « Service » est affiché. • Sélectionner le menu 4-5 sur le potentiomètre rotatif, le symbole est affiché en couleurs inverses. • BPK40235 Appuyer sur le potentiomètre rotatif. L’écran affiche le menu 4-5 « Alarmes actuelles ». La partie inférieure (1) indique les alarmes actuelles avec le numéro d’alarme qui leur est affecté (2) 1 • Vous basculez sur une autre fenêtre en utilisant le potentiomètre rotatif. (Possible uniquement si plus de trois défauts sont en attente simultanément) 2 BPK40237 IV - 34 Unité de commande confort 4.9.15 Menu principal 5 « Information » Appeler le menu principal • Appeler le niveau de menu en appuyant sur la touche . • Sélectionner le menu principal 5 sur le • potentiomètre rotatif, le symbole est affiché en couleurs inverses. Appuyer sur le potentiomètre rotatif. L’écran affiche le menu 5 « Information ». Seite 5-1: Version de logiciel complet de la machine • Appuyez sur la touche BPK40260 pour charger la • • page 5-2 1290HDP = type de machine Medium = variante machine • SW = Version de logiciel complet de la machine = version de l’ordinateur de tâches • • ISO • Abandonner le menu qui a été appelé en appuyant 5 = Version de logiciel ISO sur la touche BPK40270_4 . L’écran affiche le menu principal 5 « Information ». • Appeler l’écran initial en appuyant sur la touche . 4.9.16 Fenêtre d’information Le menu 5-9 « Nombre de couches par balle » est affiché. • Quitter le menu activé et revenir à l’image de base en appuyant sur la touche ou . IV - 35 Unité de commande confort 4.9.17 Menu principal 6 « Installateur » Appeler le menu principal • Appeler le niveau de menu en appuyant sur la touche • . Sélectionner le menu principal 6 sur le potentiomètre rotatif, le symbole est affiché en couleurs inverses. • Appuyer sur le potentiomètre rotatif. Le menu principal 6 «Installateur» est protégé par mot de passe. BPK40280 L’interrogation du mot de passe est affichée à l’écran. BPK40300 IV - 36 Unité de commande confort 4.10 Message d’alarme Si un défaut apparaît sur la machine, un message d’alarme est affiché et un signal sonore retentit (avertisseur à fréquence rapide). La description des causes possibles et du dépannage se trouve au chapitre 4.11. Toutes les fonctions du menu recouvert restent actives. Les touches sensitives recouvertes par le message d’alarme sont inactives. Stopper le signal sonore : • Appuyer sur la touche sensitive BPK40430 pour la touche . Acquitter l’alarme : • Appuyer sur la touche pour la touche sensitive , l’alarme est acquittée et le signal sonore cesse. Le message est affiché une nouvelle fois si le défaut réapparaît. Effacer l’alarme : L’effacement de l’alarme ne sera activé qu’en cas d’urgence. • Appuyer sur la touche pour la touche sensitive ,pendant 5, l’alarme est effacée. Si le défaut réapparaît, il n’y a plus de message d’alarme. C’est seulement après que l’unité de commande a été désactivée et réactivée que le message d’alarme réapparaît en présence du défaut. IV - 37 Unité de commande confort 4.11 Messages d’alarme N° Description Cause possible Dépannage A01 Défaut fusible 2 Court-circuit sur les sorties Remplacer le fusible, vérifier ensuite qu’il n’y a aucun courtcircuit sur actionneur en testant tous les actionneurs. A02 Défaut fusible 3 Court-circuit de l’alimentation des (correction automatique) capteurs. A03 Interruption de la Défaut de câblage CAN connexion CAN entre le terminal et l’ordinateur de tâches A04 Défaut EEPROM A05 Interruption de la Câblage CAN défectueux connexion CAN entre Ordinateur E/S Krone désactivé l'ordinateur de tâches et l'ordinateur E/S Krone A 11 Affichage erroné L'affichage médium est raccordé à Raccorder l'affichage confort. la machine confort. Sous-tension • Défaut de la batterie du tracteur Raccorder le câble Krone • Dynamo du tracteur trop faible directement à la batterie • Câble d’alimentation 12 V sur le tracteur de section trop faible ou pas connecté directement à la batterie Surtension Défaut du dynamo du tracteur A14 A15 IV - 38 Défaut de l’ordinateur de tâches Contrôler le câblage du potentiomètre de balles multiples, le disque soleil, le capteur de pression et l’amplificateur de mesure de force. Vérifier le câblage CAN Remplacer l’ordinateur de Contrôler le câblage CAN Contrôler le câblage Remplacer l'ordinateur E/S Krone Vérifier l’alternateur Unité de commande confort N° 0 1 2 3 4 Description Cause possible Dépannage Contrôle de ficelle - Ficelle arrachée - Fin de la ficelle - Contrôler la ficelle et le tendeur de ficelle - Engorgement dans la zone d’alimentation de l’empaqueteur - Stopper immédiatement la traction 2 roues - Réduire la vitesse de l’arbre de prise de force jusqu’à ce que l’engorgement soit éliminé Contrôle de l’empaqueteur Dépassement par excès de la force de compression Quand, sous l’effet d’une pression élevée, la machine est exposée à une surcharge mécanique, la pression sur les volets de pressage est abaissée à une valeur sûre peu de temps avant le franchissement du seuil critique. Dépassement de la L’intensité de cette réduction est fonction force de compression du matériau comprimé. La réduction est sur le capteur de droite moins forte pour la paille que pour l’ensilage. Dépassement de la force de compression sur le capteur de gauche Contrôle de noueur Dysfonctionnement du noueur - Défaut de réglage de capteur Prendre les dispositions suivantes: 1. En Mode manuel : - Réduire la pression 2. En Mode automatique : - Si l’alarme apparaît souvent, réduire légèrement la consigne de force de compression - Vérifier le noueur et le déclenchement de noueur - Régler correctement le capteur de contrôle de noueur Contrôle de mesure Défaut de capteur de mesure ou erreur de réglage - Régler le capteur correctement Contrôle de l’étalonnage Défaut de capteur d’étalonnage ou erreur de réglage - Régler le capteur correctement - Desserrer le frein Frein du volant Frein de volant serré Vis de cisaillement sectionnée - Changer la vis de cisaillement 8 Tige de traction d’aiguille La rampe d’éjection des balles est en position supérieure et l’arbre de prise de force tourne - Vérifier les aiguilles - Vérifier la zone de pivotement des aiguilles - Vérifier le guidage de ficelle 9 Rampe d’éjection des balles Défaut de la soupape de limitation de - Abaisser la rampe d’éjection des balles pression 5 6 7 10 Pression de compression dépassée par excès 11 L’arbre de prise de force tourne 12 Barre de coupe inférieure - Stopper l’arbre de prise de force Eventuellement défaut de capteur de - Vérifier que la soupape de pression limitation de pression n’est pas encrassée - Stopper immédiatement l’arbre L’arbre de prise de force tourne au de prise de force Exécuter le début du diagnostic de capteur et diagnostic avec l’arbre de prise d’actionneur ou pendant le diagnostic de force en place - La basse de coupe est en position inférieure pendant la compression - Lever la barre de coupe IV - 39 Unité de commande confort N° Description Cause possible Dépannage 16 Ramasseur Le ramasseur ou le mécanisme de coupe ne tournent pas Engorgement - Vérifier les organes mécaniques - Nettoyer 17 Moteur de noueur Le moteur de noueur n’a pas déclenché de nœud ou le capteur de noueur n’est pas réglé correctement - Vérifier l’appareillage électrique du moteur de noueur - Vérifier les organes mécaniques à la hauteur du déclencheur de noueur - Régler correctement le capteur de noueur 18 Balles multiples Les 2 positions balles multiples et grosses balles ne peuvent pas être ajustées - Pas d’air comprimé - Régler le capteur de balles multiples correctement - Vérifier les organes mécaniques à la hauteur du déclencheur de noueur - Défaut de la soupape de balles multiples (la soupape colle, défaut de la bobine, etc.) - Vérifier l’électronique au niveau du verrouillage de balles multiples 19 Alimentation d’empaquetage Défaut de réglage du capteur de l’empaqueteur - Régler le capteur correctement 20 Défaut d’activation de l’éjecteur de balles L’éjecteur de balles a été activé, bien que la rampe d’éjection des balles soit en haut - Descendre la rampe d’éjection des balles et activer l’éjecteur de balles 21 Mesurer/Etalonner Il est possible que les capteurs de mesure et d’étalonnage soient intervertis - Remplacer les connecteurs des capteurs de mesure et d’étalonnage IV - 40 Unité de commande confort N° Description Cause possible Dépannage 28 Contrôle de la lubrification centralisée Pas de graisse Engorgement La pompe ne fonctionne pas. - Faire l’appoint de graisse - Nettoyer la lubrification centrale (centralisée) - Vérifier l’appareillage (système) électrique et la pompe 101 Capteur de contrôle de noueur Défaut du capteur ou du conducteur d’amenée - Exécuter le test des capteurs - Vérifier que le capteur et le conducteur d’amenée ne sont pas endommagés 102 Capteur de contrôle d’empaqueteur Défaut du capteur ou du conducteur d’amenée - Exécuter le test des capteurs - Vérifier que le capteur et le conducteur d’amenée ne sont pas endommagés 103 Capteur d’alimentation d’empaqueteur Défaut du capteur ou du conducteur d’amenée - Exécuter le test des capteurs - Vérifier que le capteur et le conducteur d’amenée ne sont pas endommagés 104 Capteur de barre de coupe supérieure Défaut du capteur ou du conducteur d’amenée - Exécuter le test des capteurs - Vérifier que le capteur et le conducteur d’amenée ne sont pas endommagés IV - 41 Unité de commande confort N° Description Cause possible Dépannage Capteur de couteau activé Défaut du capteur ou du conducteur d’amenée - Exécuter le test des capteurs - Vérifier que le capteur et le conducteur d’amenée ne sont pas endommagés 106 Capteur de contrôle de noueur Défaut du capteur ou du conducteur d’amenée - Exécuter le test des capteurs - Vérifier que le capteur et le conducteur d’amenée ne sont pas endommagés 107 Capteur de mesure de force Défaut du capteur ou du conducteur d’amenée - Exécuter le test des capteurs - Vérifier que le capteur et le conducteur d’amenée ne sont pas endommagés 108 Capteur d’étalonnage de force Défaut du capteur ou du conducteur d’amenée - Exécuter le test des capteurs - Vérifier que le capteur et le conducteur d’amenée ne sont pas endommagés 109 Capteur de frein de volant Défaut du capteur ou du conducteur d’amenée - Exécuter le test des capteurs - Vérifier que le capteur et le conducteur d’amenée ne sont pas endommagés 110 Capteur de tige de traction d’aiguilles Défaut du capteur ou du conducteur d’amenée - Exécuter le test des capteurs - Vérifier que le capteur et le conducteur d’amenée ne sont pas endommagés 111 Capteur de rampe d’éjection des balles Défaut du capteur ou du conducteur d’amenée - Exécuter le test des capteurs - Vérifier que le capteur et le conducteur d’amenée ne sont pas endommagés 112 Capteur de force à droite Défaut du capteur, de l’amplificateur de mesure ou du conducteur d’amenée - Vérifier que le capteur et le conducteur d’amenée ne sont pas endommagés 113 Capteur de force à gauche Défaut du capteur, de l’amplificateur de mesure ou du conducteur d’amenée - Vérifier que le capteur et le conducteur d’amenée ne sont pas endommagés 114 Capteur de pression hydraulique Défaut du capteur ou du conducteur d’amenée - Exécuter le test des capteurs - Vérifier que le capteur et le conducteur d’amenée ne sont pas endommagés 115 Capteur de dépose de balles Défaut du capteur ou du conducteur d’amenée - Exécuter le test des capteurs - Vérifier que le capteur et le conducteur d’amenée ne sont pas endommagés 116 Capteur d’éjecteur de balles Défaut du capteur ou du conducteur d’amenée - Exécuter le test des capteurs - Vérifier que le capteur et le conducteur d’amenée ne sont pas endommagés 105 IV - 42 Unité de commande confort Description Cause possible Dépannage Capteur de disque soleil Défaut du capteur (potentiomètre rotatif) ou du conducteur d’amenée - Exécuter le test des capteurs - Vérifier que le capteur et le conducteur d’amenée ne sont pas endommagés Capteur de ramasseur Défaut du capteur ou du conducteur d’amenée - Exécuter le test des capteurs - Vérifier que le capteur et le conducteur d’amenée ne sont pas endommagés 119 Bouton-poussoir rampe d’éjection de balles monte Défaut du bouton-poussoir ou du conducteur d’amenée - Exécuter le test des capteurs - Vérifier que le bouton-poussoir et le conducteur d’amenée ne sont pas endommagés 120 Bouton-poussoir rampe d’éjection de balles baisse Défaut du bouton-poussoir ou du conducteur d’amenée - Exécuter le test des capteurs - Vérifier que le bouton-poussoir et le conducteur d’amenée ne sont pas endommagés 121 Bouton-poussoir de sortie de l’éjecteur de balles Défaut du bouton-poussoir ou du conducteur d’amenée - Exécuter le test des capteurs - Vérifier que le bouton-poussoir et le conducteur d’amenée ne sont pas endommagés 122 Bouton-poussoir de rentrée de l’éjecteur de balles Défaut du bouton-poussoir ou du conducteur d’amenée - Exécuter le test des capteurs - Vérifier que le bouton-poussoir et le conducteur d’amenée ne sont pas endommagés 123 Bouton-poussoir barre de coupe monte Défaut du bouton-poussoir ou du conducteur d’amenée - Exécuter le test des capteurs - Vérifier que le bouton-poussoir et le conducteur d’amenée ne sont pas endommagés 124 Bouton-poussoir barre de coupe baisse Défaut du bouton-poussoir ou du conducteur d’amenée - Exécuter le test des capteurs - Vérifier que le bouton-poussoir et le conducteur d’amenée ne sont pas endommagés 125 Capteur de balles multiples Défaut du capteur (potentiomètre rotatif) ou du conducteur d’amenée - Exécuter le test des capteurs - Vérifier que le capteur et le conducteur d’amenée ne sont pas endommagés 132 Capteur - Lubrification centralisée Défaut du capteur ou du conducteur d’amenée - Exécuter le test des capteurs - Vérifier que le capteur et le conducteur d’amenée ne sont pas endommagés N° 117 118 IV - 43 Commande ISO 4.12 Commande ISO 4.12.1 Principe de fonctionnement La commande ISO est utilisée uniquement pour les machines et systèmes correspondant au niveau d’utilisation 1 de l’organisation internationale de normalisation (ISO) 11783. L’objectif de ISO 11783 est de mettre à disposition un système cohérent et ouvert pour les systèmes électroniques dans le véhicule. Grâce à un système homogène et facilement compréhensible, ISO 11783 doit permettre la communication entre les unités de commande électroniques. Les unités de commande simples, adaptables et séparées de l’affichage proprement dit permettent d’utiliser l’écran comme moniteur de puissance pour le tracteur et comme moniteur pour un appareil annexe ISO 11783. 4.12.2 Montage 4 Pendant le montage, veiller à ne pas tendre le câble de liaison électrique et à ce qu’il n’entre pas en contact avec les roues du tracteur. 5 2 Installer le faisceau de câbles fourni. Pour ce faire : • Raccordez le câble de tension (12 V) à la prise de courant à 3 pôles (DIN 9680) côté tracteur et au connecteur Delphi (5) côté machine. • Le connecteur Delphi (5) est situé dans le sens de déplacement, côté gauche de la machine, sur le capotage et à proximité du volant. • Raccordez le câble fourni à la douille (4) située, dans le sens de déplacement, à gauche sur le capotage et à proximité du volant, et à la douille de l’unité de commande. • accoupler le connecteur ISO 9 (2) pôles à la prise bus ISO (1) du tracteur. BPXC0306 1 LBS_0002 IV - 4 Commande ISO 4.12.3 Fonctions différentes par rapport à la commande confort KRONE L’unité de commande ISO met à disposition des informations et des fonctions de commande sur l’écran du terminal ISO via l’appareil annexe. La commande avec le terminal ISO est analogue à celle de la commande confort KRONE. Avant la mise en service, il convient de prendre connaissance du principe de fonctionnement de la commande confort KRONE dans la notice d’instructions. Une différence importante par rapport à la commande confort KRONE réside dans la disposition des touches sensitives définie par le terminal ISO sélectionné. Seules les fonctions différentes de celles de la commande confort sont décrites ci-après. Le remplacement des fonctions du potentiomètre rotatif (rotation à gauche, rotation à droite ainsi que l’appui sur le potentiomètre rotatif) par les touches sensitives suivantes représente une différence importante par rapport à la commande confort KRONE Commande confort KRONE correspond à la touche sensitive pour le terminal ISO Potentiomètre rotatif « rotation à droite », « rotation à gauche » pour aller en avant ou revenir en arrière. aller en avant ou revenir en arrière Potentiomètre rotatif « rotation à droite », « rotation à gauche » pour augmenter ou diminuer la valeur. augmenter la valeur diminuer la valeur Appuyer sur le potentiomètre rotatif pour enregistrer la valeur OK La touche $$$ permet d’accéder à l’écran précédent ou au niveau de menu précédent. ESC ferme le menu appelé La touche $$$ permet d’appeler le niveau de menu. Les valeurs pour la « pression / force des volets de pressage », la « longueur de balle » et le « nombre de balles multiples » réglées avec le potentiomètre rotatif dans l’écran de base de la commande confort KRONE, le sont avec le terminal ISO à l’aide de la touche de sélection prescrite par le terminal ISO (voir notice d’instructions du fabricant du terminal ISO). IV - enregistrer la valeur Appeler le niveau de menu Commande ISO Le point de menu 1-4 « Contraste » de la commande confort KRONE n’est pas appelé avec le terminal ISO. Le réglage est effectué directement par le terminal ISO ( si disponible) (voir notice d’instructions du fabricant du terminal ISO). Le point de menu 1-7 « Unité de mesure » de la commande confort KRONE n’est pas appelé avec le terminal ISO. Le réglage est effectué directement par le terminal ISO. (si disponible) (voir notice d’utilisation du fabricant du terminal ISO) Des signaux sonores doivent être éventuellement débloqués par le terminal (voir notice d’instructions du fabricant du terminal ISO). IV - 5 Ce chapitre est resté délibérément vierge ! V-1 V-2 6 Ce chapitre est resté délibérément vierge ! VI - 1 VI - 2 Travail avec la presse à grosses balles 7 Travail avec la presse à grosses balles 7.1 Consignes de sécurité • • • • • • Pour tous les travaux de maintenance, de montage, de réparation et de réglage, les mesures suivantes doivent toujours être prises Déconnecter la prise de force. Couper le moteur et retirer la clé de contact. Serrer le frein du volant. Pendant le fonctionnement, maintenir une distance de sécurité suffisante avec toutes les parties mobiles de la presse à grosses balles. Ceci est particulièrement important pour les dispositifs de ramassage de la récolte. Ne mettre la presse à grosses balles en service que lorsque tous les dispositifs de protection sont installés et sont en bon état. Eliminer les engorgements uniquement lorsque la machine est à l’arrêt. Couper le moteur et retirer la clé de contact. Serrer le frein du volant. En cas de situation dangereuse, déconnecter immédiatement la prise de force et stopper la presse à grosses balles. Ne jamais laisser la presse à grosses balles fonctionner en l’absence de personnel de service sur le tracteur. 7.2 Ramasseur Pour tout déplacement vers l’avant ou vers l’arrière, élever le ramasseur ! Réglage de la hauteur de travail Pour régler la hauteur du ramasseur, lever ce dernier et empêcher tout abaissement involontaire en actionnant le robinet d'arrêt sur le côté gauche de la machine. Le réglage de la hauteur de travail se fait au niveau des roues de jauge (3) des deux côtés du ramasseur. Pour procéder au réglage, relever et bloquer le ramasseur. Retirer la fiche de ressort (2) et placer les roues de jauge dans la position souhaitée au niveau de la barre à trous (1). Bloquer à nouveau les roues de jauge avec la fiche de ressort. Veiller à ce que les roues de jauge sur les deux côtés du ramasseur se trouvent sur la même position au niveau de la barre à trous. 2 1 3 BPXC0125 VII - 1 Travail avec la presse à grosses balles Fixation de la hauteur de travail du ramasseur La hauteur de travail du ramasseur est ajustée manuellement en déplaçant les butées (1) sur les deux côtés de la machine. De cette manière, il est possible de piloter la machine sans roue de palpage avec ramasseur en position fixe. 1 Pour le réglage, desserrer les boulons (2) et amener le limiteur de profondeur sur la position souhaitée dans l’orifice. Resserrer ensuite les boulons. 2 Veiller à ce que les limiteurs de profondeur sur les deux côtés du ramasseur se trouvent sur la même position. BPXC0126 Réglage du dispositif de placage à rouleaux Le dispositif de placage à rouleaux sert de protection contre les accidents et ne doit pas être retiré pendant le fonctionnement. • 2 X 1 5 4 Contraindre le ressort (3) en serrant l'écrou (4) au niveau de la vis à œillet (5) jusqu'à ce que la longueur X soit de 55 mm. 3 Lors du réglage de la tôle du dispositif de placage (2), choisir l'angle de sorte que le canal d'alimentation soit légèrement agrandi vers l'arrière sur le ramasseur. BPXC0290 La tôle du dispositif de placage (2) ne doit pas rétrécir le canal d’alimentation vers le mécanisme de coupe ou l’empaqueteur. Le réglage de la hauteur du dispositif de placage à rouleau (3) se fait au niveau des chaînes de maintien (2), accrochées dans les fixations (1) des deux côtés de la machine. Veiller à ce que les chaînes aient la même longueur dans les supports. Régler la hauteur du rouleau du dispositif de placage (1) de manière à ce qu’il roule en permanence sur l’andain. 2 1 3 BPXC0127 VII - 2 Travail avec la presse à grosses balles 7.3 Mécanisme de coupe XC Consignes de sécurité • • • • • • Pour tous les travaux de maintenance, de montage, de réparation et de réglage sur le mécanisme de coupe, les mesures suivantes doivent toujours être prises : Stopper la presse à grosses balles. Couper le moteur et retirer la clé de contact. Immobiliser le tracteur et la presse à grosses balles pour empêcher tout déplacement. Empêcher tout abaissement involontaire du ramasseur. Risque de blessure lors du montage et du démontage des couteaux. Ne saisir les couteaux qu’avec des gants appropriés. Serrer le frein du volant. Généralités La presse Big Pack XC possède un mécanisme de coupe avec cylindre de coupe et couteaux fixes. La coupe permet un meilleur traitement ultérieur des grosses balles et augmente la densité de pressage. En cas d’engorgement, il est possible, par commande hydraulique à partir du tracteur, d’extraire les couteaux du couloir d’alimentation. Chaque couteau est protégé individuellement contre toute surcharge. La machine peut également être utilisée sans couteaux. Dans ce cas, utiliser des obturateurs remplaçant les couteaux. Le cylindre de coupe se charge alors du transport entre le ramasseur et le canal de pré-compression. Longueur de coupe Le mécanisme de coupe de la presse Big Pack 890 XC peut être équipé de 26 couteaux max.La longueur de coupe théorique est de 44 mm. La longueur de coupe est déterminée par le nombre de couteaux utilisés. 0 Pour activer le mécanisme de coupe, le montage des couteaux (position 1) doit être enclenché et le mécanisme de coupe amené en position haute par commande hydraulique. Longueur de coupe mm Nombre de couteaux Casier à couteaux utilisé 1 BPXC0128 Réglage BP12130 - 0 quelconque 0 44 26 chacun 1 88 13 un sur 2 1 132 6 1 sur 3 1 VII - 3 Travail avec la presse à grosses balles Remplacement des couteaux Le remplacement des couteaux se fait sur les côtes gauche et droit de la machine. Nous expliquons ci-dessous les travaux sur le côté gauche de la machine. Procéder de même sur le côté droit. Abaisser le mécanisme de coupe Avant l’abaissement, la commande des couteaux doit se trouver en position (1) afin que les couteaux soient extraits du canal. • • Abaisser le mécanisme de coupe avec le système hydraulique du tracteur (Electronique de confort : Activer l’hydraulique du tracteur et, sur l’afficheur de l’unité de commande ou les boutons-poussoirs de la machine, maintenir l’action sur «Abaisser la barre de coupe» jusqu’à ce que la barre de coupe soit entièrement abaissée.) Retirer la clé de contact et déconnecter l’appareillage électrique de l’unité de commande Le mécanisme de coupe ne peut être remonté que lorsque les deux parties du mécanisme de coupe sont entrées latéralement et verrouillées A l’aide d’une clé (ouverture de clé 30), amener le montage des couteaux de la position (1) à la position (0). 0 1 Lors de cette modification, veiller à ce que la pression du ressort agisse sur la clé (risque de blessure !) BPXC0129 Déverrouiller le mécanisme de coupe en actionnant le levier (1) et sortir le mécanisme de coupe latéralement jusqu’à la butée. 1 0 1 BPXC0130 VII - 4 Travail avec la presse à grosses balles Déverrouiller l’arbre des couteaux • • • • • 2 Déverrouiller le levier de verrouillage (1) (pos. II) Les couteaux (2) peuvent maintenant être extraits verticalement par le haut. Placer des couteaux neufs. Placer les obturateurs là où il n’y a pas de couteaux. Bloquer l’arbre des couteaux à l’aide du levier de verrouillage (1) (pos. I) II I Position I = arbre des couteaux verrouillé Position II = arbre des couteaux déverrouillé 1 BPXC0131 • • • Insérer les deux parties du mécanisme de coupe (4) jusqu’à ce que le levier de verrouillage (3) s’enclenche de lui-même. A l’aide d’une clé (ouverture de clé 30), amener la commande des couteaux de la position (II) à la position (I). Soulever hydrauliquement le mécanisme de coupe Le mécanisme de coupe ne peut être remonté que lorsque les deux parties du mécanisme de coupe sont entrées latéralement et verrouillées II I 3 4 BPXC0132 Déconnecter hydrauliquement les couteaux : Le mécanisme de coupe peut être baissé à l’aide d’un cylindre hydraulique. Le montage zéro hydraulique des couteaux permet d’éliminer un éventuel engorgement. Pour exécuter les travaux sans couteaux, placez les obturateurs. La garde au sol étant réduite, le mécanisme de coupe doit être immédiatement remonté après élimination de l’engorgement, sans quoi le mécanisme de coupe sera endommagé. Si le mécanisme de coupe est fortement encrassé, nettoyez avant de le relever. VII - 5 Travail avec la presse à grosses balles 7.4 Régulation de la force de compression 1 La force de compression dans le canal de pressage est régulée par un système électro-hydraulique. Le réglage de la force de compression s’effectue au niveau de la commande du tracteur. La pression est lue directement sur l’unité de commande (voir les chapitres 4 et 5). Un autre manomètre (1) se trouve sur le côté gauche de la machine sous le capot latéral, sur la soupape de limitation de pression. BP1213001 Maintien de la pression de compression lorsque le système électronique est désactivé (médium/confort) Pour maintenir la pression de compression dans le canal de pressage, le système électronique ne doit pas être désactivé avant que la machine, respectivement le volant, ne soit immobilisé. Robinet de fermeture pour libérer le canal de pressage a Modèles de médium : Le robinet d’arrêt (1) permet de débloquer le canal de pressage. En position (a), la machine est en position de travail. Le canal de pressage est débloqué den position (b) (retour vers le réservoir) Lorsque le robinet d’arrêt se trouve sur la position (b), aucune pression ne peut s’établir. Modèle confort : Sur le modèle confort, cette fonction est activée sur l’unité de commande ou sur les touches de la machine (voir le chapitre 4). VII - 6 1 b BPXC0138 Travail avec la presse à grosses balles 7.5 Vider le canal de pressage Avant de procéder au vidage du canal de pressage, la balle se trouvant dans le canal doit être liée. Pour ceci, déclencher manuellement le processus de liage (voir chapitre « Déclenchement manuel du processus de liage »). Ouvrir ensuite le canal de pressage (robinet de blocage du canal de pressage, voir le chapitre 7.4). 1 1 Attendre que les volets de serrage soient entièrement ouverts pour éjecter la balle. Dans les modèles de médium, l’actionnement de l’éjecteur de balles restantes se fait par le levier de commande supérieur à l’arrière sur le côté gauche de la machine. • • BP380-7-052 Ouvrez le robinet d’arrêt (4) (position I) Soulever la douille de sécurité (2) et amener le levier de commande (3) sur la position (a) ou (b). Position (a) :L’éjecteur des balles restantes est déplacé vers l’avant Position (b) : L’éjecteur des balles restantes est déplacé vers l’arrière Après l’éjection d’une balle, ramener impérativement l’éjecteur de balles en position avant. Pour ce faire, amener le levier de commande (3) en position (a) comme l’indique la description cidessus.Ensuite, fermez le robinet d’arrêt (4) (position (II)) 7.6 Rampe d’éjection à rouleaux à commande hydraulique (option) b a 2 I 3 4 II BP800063 Immobiliser le tracteur et la machine pour empêcher tout déplacement involontaire. Lors du pliage et du dépliage de la rampe d’éjection à rouleaux, avertir les personnes se trouvant dans la zone de danger. La conduite sur les voies publiques n’est autorisée que lorsque la rampe d’éjection à rouleaux est repliée. La commande de la rampe d’éjection dépend du modèle. Sur les modèles d’unité de commande de médium, activer l’appareil de commande sur le tracteur. L’appareil de commande (1) de la rampe d’éjection rabattable à commande hydraulique et de l’éjecteur des balles restantes se trouve à l’arrière à gauche près du frein parking. Position a = robinet de blocage ouvert Posirtion b = robinet de blocage fermé • • Désactiver le verrouillage mécanique de la rampe d’éjection à rouleaux. Ouvrir le robinet d’arrêt (1) 1 b 2 a BPXC0134 VII - 7 Travail avec la presse à grosses balles • • Pour déplier la rampe d’éjection des balles (2), soulever la douille de sécurité (3) et placer le levier de commande inférieur (4) sur la position (b). Pour plier la rampe d’éjection des balles (2), soulever la douille de sécurité (3) et placer le levier de commande (4) sur la position (a). 2 Position a = soulever la rampe d’éjection des balles Position b = rabattre la rampe d’éjection des balles Pour circuler sur la voie publique, la rampe d’éjection à rouleaux doit toujours être repliée et verrouillée par encastrement. 3 a La commande de la variante confort est décrite au chapitre 4 ! b 4 BPXC0135 7.7 Réglage de la longueur des balles 1 7.7.1 Réglage de longueur manuel 3 La longueur des balles est réglée manuellement sur la presse à grosses balles sur le côté gauche de la machine à partir de l’échelle. 2 La longueur des balles peut être sélectionnée en tournant la manivelle (1). L’aiguille (2) sur l’échelle graduée (3) facilite le réglage. BPXC0139 7.7.2 Réglage électrique de longueur (option) Avec le réglage électrique de longueur de balles, la longueur de balles est sélectionnée sur l’unité de commande du tracteur (voir les chapitres 4 et 5). VII - 8 Travail avec la presse à grosses balles 7.8 Ficelle de liage 7.8.1 Indication électrique signalant un problème au niveau de la ficelle Lorsque l’extrémité de la ficelle est atteinte ou lorsque la ficelle est arrachée, les tendeurs de ficelle à ressort (1) se placent sur l’angle de rotation (2). Un signal sonore est délivré par l’unité de commande. Un message d’erreur apparaît sur l’affichage. Pour déconnecter le signal d’avertissement sonore pendant l’enfilage du fil, voir chapitre « Messages d’alarme » dans la description de la commande confort. 1 BP1213003 7.8.2 Affichage du parcours de la ficelle de dessus (noueur double) Le parcours supérieur de la ficelle est contrôlé par des réflecteurs (indicateurs du parcours de la ficelle) installés au dessus de la machine. Au cours de la formation des balles, les indicateurs de parcours de la ficelle doivent effectuer des mouvements de va-et-vient pulsés. En général, tous les indicateurs s’élèvent et se rabaissent simultanément, sauf en cas de défaut. En cas de défaut au niveau de l’un des indicateurs du parcours de la ficelle, ce dernier ne se trouve pas dans la même position que les autres indicateurs. Les défauts suivants peuvent être affichés : Les indicateurs du parcours de la ficelle restent en position haute : - La ficelle s’est enroulée autour du crochet du noueur. - L’aiguille n’a pas saisi l’écheveau supérieur (la ficelle n’est pas coupée). - Le nœud est resté au niveau du crochet du noueur (après le liage, un indicateur du parcours de la ficelle reste plus longtemps que les autres en position basse). Les indicateurs du parcours de la ficelle restent en position basse : - La tension de la ficelle est trop basse. - L’écheveau supérieur est arraché. - Le crochet du noueur n’a pas fait de nœud. BP1213004 VII - 9 Travail avec la presse à grosses balles 7.8.3 Déclencher manuellement le processus de nouage Afin que la ficelle de liage arrive dans le canal de pressage et puisse être saisie par le noueur, le processus de liage doit être déclenché manuellement. Pour ceci: • Amenez le levier de sécurité (2) en position basse. Pour déclenchement mécanique : • Pousser le levier (1) vers le haut, ce qui déclenche l’opération de liage. Pour déclenchement électrique (en option) : • Pousser le levier (3) vers l’arrière, ce qui déclenche l’opération de liage. Ensuite, en procédant manuellement au niveau du volant (dans le sens de travail) ou en connectant la prise de force, déplacer les aiguilles vers le haut en direction des noueurs, puis les rabaisser. La ficelle de liage se trouve alors dans le canal de pressage. Sur le noueur simple, veiller à ce que les ficelles soient tirées vers l’arrière après le dernier nouage, sinon la ficelle risque de s’enchevêtrer dans la machine au nouage suivant. 1 2 BP380-7-051 3 2 BPXC0230 VII - 10 Travail avec la presse à grosses balles 7.9 Entraînements Entraînement principal Un engrenage cylindrique conique tient lieu d’entraînement principal. Le couple nécessaire est transmis par l’intermédiaire de l’arbre à cardan et d’une masse tournante largement dimensionnée. La vitesse d’entraînement maximale ne doit pas être supérieure à 1000 tr/min. Côté machine, l’arbre à cardan doit être protégé par un accouplement patinant (1). Un accouplement à friction à cames (3) est installé entre l’embrayage à friction (1) et le volant (2). Dès que l’accouplement réagit, stopper la machine, stopper le tracteur, déconnecter immédiatement la prise de force et freiner le volant. Dès que le défaut est éliminé, l’accouplement de coupure à cames se reconnecte automatiquement. 2 3 1 BP1213092 VII - 11 Travail avec la presse à grosses balles Entraînement du cylindre d’empaquetage L’entraînement du cylindre d’empaquetage se trouve sur le côté gauche de la machine. La transmission est bloquée par un embrayage à cliquets à ressort et/ou une vis de cisaillement. Dès que l’embrayage à cliquets à cames se déclenche, stopper le tracteur et réduire la vitesse de rotation jusqu’à ce que la machine se soit dégagée d’ellemême. Dès que le défaut est éliminé, l’accouplement à cliquets se remet automatiquement à fonctionner. BP1213006 Un message de défaut est affiché à l’écran de l’unité de commande. Entraînement de l’arbre du noueur Un engrenage angulaire assure l’entraînement de l’arbre du noueur. Un arbre à cardan transmet le couple à l’arbre du noueur par l’intermédiaire de la transmission du noueur. BP1213007 Entraînement du mécanisme de coupe XC Un engrenage angulaire assure l’entraînement du rotor de coupe. Un arbre intermédiaire transmet le couple via un accouplement de coupure à cames vers un engrenage angulaire. Dès que l’accouplement de coupure à cames se déclenche, stopper le tracteur et diminuer la vitesse de rotation jusqu’à ce que la machine se soit dégagée d’ellemême. L’accouplement de coupure à cames redémarre automatiquement. Un message de défaut est affiché à l’écran de l’unité de commande. VII - 12 1 BP1213008 Travail avec la presse à grosses balles Entraînement du ramasseur avec mécanisme de coupe XC A partir de la sortie de l’engrenage angulaire du mécanisme de coupe, le couple de rotation est transmis à la chaîne d’entraînement du ramasseur par un cliquet en étoile. Dès que l’accouplement de coupure à cames se déclenche, stopper le tracteur et diminuer la vitesse de rotation jusqu’à ce que la machine se soit dégagée d’ellemême. L’accouplement de coupure à cames redémarre automatiquement. Un message de défaut est affiché à l’écran de l’unité de commande. BPXC0147 Entraînement du ramasseur via la transmission (sans mécanisme de coupe XC) Le couple de rotation est transmis par un engrenage angulaire à partir du haut via un arbre à cardan avec limiteur de charge (cliquet en étoile) vers le bas sur engrenage angulaire. Dès que l’accouplement de coupure à cames se déclenche, stopper le tracteur et diminuer la vitesse de rotation jusqu’à ce que la machine se soit dégagée d’ellemême. L’accouplement de coupure à cames redémarre automatiquement. Un message de défaut est affiché à l’écran de l’unité de commande. BPXC0028 VII - 13 Travail avec la presse à grosses balles VII - 14 Réglages 8. Réglages 8.1 Consignes de sécurité • • • • • Pour tous les travaux de maintenance, de montage, de réparation et de réglage, les mesures suivantes doivent toujours être prises Déconnecter la prise de force. Couper le moteur et retirer la clé de contact. Serrer le frein du volant. Ne mettre la presse à grosses balles en service que lorsque tous les dispositifs de protection sont installés et en bon état. En cas de situation dangereuse, déconnecter immédiatement la prise de force et stopper la presse à grosses balles. Ne jamais laisser la presse à grosses balles fonctionner en l’absence de personnel de service sur le tracteur. Lors des travaux sur les aiguilles se trouvant sous la machine et dans le canal de pressage, bloquer impérativement le porte-aiguilles pour l’empêcher de tomber. Risque de blessure ! 8.2 Dispositif de liage 8.2.1 Ficelle de liage La presse à grosses balles est équipée des deux côtés de la machine de boîtes à ficelle pouvant contenir 16 rouleaux de ficelle chacune. Pour garantir une sécurité de liage suffisante, veiller à n’utiliser que de la ficelle synthétique d’une longueur de 110 - 130 m/kg. Lier les rouleaux de ficelle avec les nœuds plats adjacents. Raccourcir les extrémités des nœuds sur x = 15 - 20 mm. X Avant chaque insertion d’une nouvelle ficelle de liage, procéder aux mesures suivantes : - déconnecter la prise de force du tracteur, couper le moteur du tracteur, bloquer mécaniquement le volant, immobiliser l’arbre du noueur en actionnant le levier de sécurité X BP 380-7-043 VIII - 1 Réglages Mise en place de la ficelle de liage 1 Avant de mettre en place une nouvelle ficelle de liage, l’arbre du noueur doit être bloqué afin d’empêcher tout déplacement du cadre de suspension des aiguilles. Pour ceci, faire passer le levier de sécurité (1) de la position (a) à la position (b) et le déposer sur le bouton (2). b 2 a b 2 a 1 BP380-7-044 Lors de la mise en place de la ficelle de liage dans la boîte à ficelle, veiller à ce que les inscriptions du rouleau soient lisibles. Tenir compte de l’inscription « Haut ». Type de machine Nombre Nombre de rouleaux Nombre de rouleaux Réserve Ficelle/Noueur Noueur Ficelle/Noueur (Ficelle en bas) (Ficelle en bas) Big Pack 12130 6 6 2 8 Pendant le circuit de liage des balles, deux écheveaux sont amenés vers chacun des 6 noueurs, le premier étant amené depuis le bas par les aiguilles (2), et le deuxième depuis le haut directement vers les balles (1). Les rouleaux de ficelle se trouvant à l’avant dans le sens de déplacement sont les ficelles de dessus et conduisent aux noueurs (1). Les rouleaux de ficelle se trouvant à l’arrière dans le sens de déplacement sont les ficelles de dessous et conduisent aux aiguilles (2). Serrez les freins des boîtes à ficelle de sorte que la ficelle soit tout juste tendue (ne prenne pas de mou) ! VIII - 2 1 I I I I I I R R II II II II II II R R 2 BPXC0252 Réglages Enfiler la ficelle Enfiler dans les freins la ficelle de liage provenant des œillets de ficelle inférieurs de la boîte à ficelle par le guidage de ficelle externe. Enfiler ensuite la ficelle dans les aiguilles de liage par les ressorts tendeurs de ficelle, et la nouer au niveau des œillets correspondants sur le cadre. c b a c a b b a c Big Pack 12130 côté droit b a c BPXC0016 c b a Big Pack 12130 côté gauche c b a c b a b c a BPXC0018 VIII - 3 Réglages Ècheveau supérieur : La ficelle (1) passe par les œillets (2) de la boîte à ficelle, via le guidage de ficelle (3) par les œillets (9) dans le frein (4). Elle est ensuite acheminée jusqu’à la face supérieure de la balle via l’œillet du bras de serrage (5) par les rouleaux d’aiguille supérieure (6). 9 Lorsque la presse à balles est vide, les écheveaux supérieur et inférieur peuvent être noués l’un à l’autre au centre de la chambre des balles. BPXC0152 L’écheveau supérieur est conduit sous la traverse arrière (7) de la table du noueur et fixé à l’endroit prévu sur le cadre, Cet endroit peut être le boulon de charnière (8) du volet de serrage supérieur par exemple. La ficelle doit être fixée de sorte à ce que le bras de serrage (5) soit sous tension. Après le prochain processus de liage, la ficelle doit être coupée du boulon de charnière. Quand le canal de pressage est plein, il est également possible de presser l’extrémité de la ficelle supérieure libre dans la balle. Pour ceci, la ficelle doit passer par les rouleaux d’aiguille supérieure (6) et un bout de ficelle d’une longueur de 50 cm environ doit dépasser dans le canal de pressage. Lors des pressages suivants, la ficelle se coince dans la récolte et tire alors le bras de serrage vers le bas. Il est important que le bras de serrage soit tendu peu avant le déclenchement du processus de liage. 8.2.2 5 4 1 6 BPXC0221 Réglage des aiguilles Réglage latéral des aiguilles Insérer les aiguilles (1) au centre dans les trous oblongs du cadre de suspension des aiguilles, les aligner avec les fentes des aiguilles et les bloquer à l’aide des vis (2). Pour pouvoir procéder au réglage, il est nécessaire de déclencher manuellement le processus de liage et de tourner manuellement vers le haut le cadre de suspension des aiguilles au niveau de la masse tournante dans le sens de travail. Lorsqu’elles montent, les aiguilles doivent toucher légèrement les supports du noueur sur le côté droit dans le sens de déplacement. Pour corriger l’écart latéral, desserrer les vis (2) et aligner latéralement les aiguilles. Alors que les aiguilles sont dans cette position, déplacer le piston latéralement avec un levier de montage pour identifier le contact latéral éventuel des aiguilles. (Voir chapitre 8.4). Le réglage étant terminé, vérifier impérativement que toutes les vis sont bien serrées. Les aiguilles doivent avoir toute liberté de manœuvre. Elles ne doivent pas effleurer d’autres pièces (cadre, piston, etc.) ! VIII - 4 1 2 BPXC0022 Réglages Procéder aux réglages uniquement lorsque la ficelle est enfilée ! Hauteur des aiguilles sur le noueur Pour régler la hauteur des aiguilles (4) lors de leur entrée dans le noueur, tourner le cadre de suspension des aiguilles en tournant à la main la masse tournante dans le sens de la marche après avoir déclenché un processus de liage jusqu’à ce que le rouleau inférieur se trouve dans la pointe de l’aiguille au-dessus des nettoyeurs (6) de l’entraîneur (2) (I). En présence de ficelle, l’écart « a » entre le bord inférieur du galet et le bord supérieur du disque de nettoyage doit être compris entre a = 1 à 3 mm. Si cette cote ne peut pas être obtenue, il faut affiner le réglage en agissant sur les vis (7). A leur entrée dans le noueur, les aiguilles doivent toucher légèrement le noueur sur le côté droit. Point mort haut des aiguilles Afin de pouvoir vérifier le point mort supérieur des aiguilles, il faut tourner le cadre de suspension des aiguilles dans sa position la plus haute (point mort) (II). Afin de pouvoir vérifier le point mort supérieur des aiguilles, il faut tourner le berceau d’aiguille dans sa position la plus haute (point mort). Les aiguilles (4) sortent maintenant du noueur. La cote « b » entre le bord supérieur du disque d’entraînement (2) et le centre du galet inférieur doit être égale à b = x mm. Si le réglage n’est pas correct, jouer sur la longueur du tirant (3) jusqu’à obtenir la cote requise. Dans leur position la plus haute, les aiguilles ne doivent pas toucher le nettoyeur (6) de l’entraîneur (2). a b 6 1 2 3 4 5 7 BPXC0155 Noueur double : b = 105 - 115 mm Lors de leur mouvement de montée et descente, ni les aiguilles ni le berceau d’aiguille ne doivent entrer en collision avec le châssis, le piston ou d’autres éléments de la machine. VIII - 5 Réglages Réglage du frein de balancier d'aiguilles Pour régler le frein du balancier d'aiguilles, le balancier d'aiguilles doit se trouver en position finale, ce qui est reconnaissable au fait que le galet du déclencheur (1) se trouve dans l'évidement de l'engrenage du noueur. • 1 Monter le frein à inertie avec les garnitures de friction (4) de sorte que le tube (2) du balancier d'aiguilles se trouve dans la position arrière, directement derrière l'arrête du frein à inertie (3). Les surfaces de freinage peuvent être réglées à l'aide des trous oblong (plan et angle). • Régler l'inclinaison de la garniture de friction (4) par rapport au profilé en U (5) dans le réglage du base sur une cote Z = 45 mm. • Contraindre le ressort du frein à aiguilles en serrant l'écrou (7) jusqu'à une longueur de ressort X = 85 mm (longueur du ressort uniquement, sans rondelle). • Régler ensuite les contre-écrous (6) de la vis de serrage sur une cote Y = 7 mm par rapport au profilé en U (5). Bloquer les contre-écrous (6) à l'aide du deuxième écrou. Si le balancier d'aiguilles a toujours tendance à vibrer après la fixation, il est possible d'accroître la pente de la surface de freinage 7 2 3 Resserrer toutes les vis au terme du réglage pour empêcher toute modification ultérieure du réglage du frein à inertie. BP1213009 6 4 5 BP1213090 VIII - 6 Réglages Aiguilles par rapport au piston de presse Pour régler les aiguilles par rapport au piston de presse, démonter, dans un premier temps, l’arbre à cardan de l’entraînement de l’arbre du noueur. Tourner ensuite manuellement le piston de presse au niveau de la masse tournante dans le sens de travail jusqu’à ce que le bras de manivelle (3) et la tige de piston (4) se trouvent en position haute (c’est-à-dire lorsque le piston de presse se trouve sur le point mort avant). 3 4 BP1213010 La transmission du noueur est ensuite tournée jusqu’à ce que la marque de couleur (1) sur la couronne de l’arbre du noueur soit alignée avec l’arête arrière supérieure du carter de transmission du noueur (2). Lorsque ce réglage est terminé, remonter et bloquer l’arbre à cardan de l’entraînement du noueur. Contrôler le réglage comme cela est décrit dans le chapitre suivant. 2 1 BPXC0190 Contrôle du réglage des aiguilles par rapport au piston de presse Pour contrôler le réglage d’aiguille sur le piston, desserrer entièrement le frein de balancier d’aiguilles Pour pouvoir contrôler le réglage des aiguilles par rapport au piston de presse, le processus de liage est déclenché. Le piston de presse (2) est tourné, au niveau de la masse tournante, à la main, dans la direction de travail jusqu’à ce que les pointes des aiguilles de liage (1) se trouvent à la hauteur du couteau du piston. Dans cette position, la pointe d’aiguille doit être recouverte par la bordure avant du piston de presse de a = 60 à 90 mm. Si ce n’est pas le cas, le réglage doit être corrigé en changeant l’arbre à cardan de l’entraînement du noueur. 2 a 1 BPXC0156 VIII - 7 Réglages Réglage de l’aiguille supérieure Régler l’aiguille supérieure de manière que les différents bras de l’aiguille supérieure (1) soient en position médiane dans les fentes du canal (2). Ce réglage est exécuté par compensation avec des rondelles sur les extrémités de l’arbre d’aiguille supérieur. 1 1 4 4 2 2 BPXC0224 Contrôle du réglage Tirer le fil vers l’arrière et commander le liage. Tourner le volant à la main jusqu’à ce que les bras de l’aiguille supérieure (1) montent. Juste avant que l’aiguille de noueur saisisse la ficelle supérieure (3), tirer le frein de volant. A ce moment, la ficelle de dessus devrait se trouver en position médiane devant le rouleau supérieur (4) de l’aiguille de noueur. Si ce n’est pas le cas, rectifier l’ajustage des différents bras de l’aiguille supérieure (1). 3 1 3 4 VIII - 8 4 BPXC0225 Réglages 8.2.3 Barre à ficelle La barre à ficelle (1) écarte la ficelle de liage de l’aiguille et la presse contre le crochet du noueur. Si la ficelle n’est pas saisie par la barre à ficelle, le crochet du noueur ne peut pas recevoir la ficelle. 5 1 6 7 8.2.3.1 Réglage de la barre à ficelle (noueur double) Dans le cas d’un noueur double, le réglage de la barre à ficelle est effectué lors du deuxième nœud, le liage se poursuit grâce à la rotation du volant. Après la réalisation du premier nœud (nœud à boucles), l’aiguille se déplace à nouveau vers le bas et les bras d’insertion se trouvent sur leur point le plus bas dans la fente du canal. Les barres à ficelle basculent alors pour la deuxième fois au dessus des ouvertures. Lorsque les barres à ficelle saisissent la ficelle, elles doivent présenter une portée de saisie minimale de b = 5 à 10 mm (la ficelle doit être saisie à une distance minimale de 5 à 10 mm de la pointe de la barre à ficelle). Le réglage s’effectue grâce au desserrage des vis (4) et (3) de la barre à ficelle (1). Le réglage de l’écart latéral « a » s’effectue au niveau des tringles de commande (5) de la barre à ficelle (1). Pour régler, desserrez les contre-écrous (6) et le boulon (7) du palier articulé (8). Tourner les tringles de commande jusqu’à ce que la distance « a » soit comprise entre 5 et 12 mm. Lorsque la barre à ficelle est pressée en direction de la fente du canal, la distance « a » doit encore être respectée. Resserrer ensuite les contre-écrous. Les barres à ficelle doivent avoir toute liberté de déplacement dans cette position. Pendant le montage, veiller à ce que le coude (5) de la tringle de commande soit orienté vers le haut, à gauche. 3 4 2 BPXC0242 b a 1 BPXC0243 8 12 Pendant le montage, veiller à ce que le coude (5) de la tringle de commande soit orienté vers le haut, à gauche. Contrôle de réglage de la barre à ficelle • • • • • Commander le nouage (voir le chapitre « Déclencher manuellement le processus de nouage ») Tourner le volant en position de travail jusqu’à ce que les bras de l’aiguille supérieure (8) décollent légèrement. Dévisser la vis (9) du noueur et lever le noueur. Desserrer l’écrou assemblé (10) de manière à soulager le ressort (11). Déplacer les barres à ficelle (12) manuellement par mouvement de va-et-vient. La pointe de la barre à ficelle (12) ne doit pas heurter les bras de l’aiguille supérieure (8). Si nécessaire, reculer la barre à ficelle (12) après avoir dévissé les vis (3) et (4) de manière que la barre à ficelle (12) ne vienne pas heurter les bras de l’aiguille supérieure (8). Après correction de réglage de la barre à ficelle (1), vérifier la cote « a ». BPXC0226 11 10 9 BPXC0227 VIII - 9 Réglages Précontrainte de l’arbre de barre à ficelle 1 a Contraindre le ressort (1) de l’arbre de barre à ficelle jusqu’à ce que la cote a= 220 mm entre les œillets du ressort (1). BPXC0228 Réglage du frein de l’arbre de noueur 1 a Contraindre les ressorts (1) du frein de l’arbre de noueur, jusqu’à ce que la cote a = env. 22 mm. 1 a BPXC0228 BPXC0229 VIII - 10 Réglages 8.2.4 Frein de ficelle Les freins des boîtes à ficelle (1) servent uniquement à tendre la ficelle. Lorsque la précontrainte de l’écheveau est réglée sur une valeur trop importante, des dysfonctionnements peuvent intervenir au niveau du noueur, et les composants concernés seraient alors soumis à une charge trop importante. 1 1 Réglage X= 30-35 mm BPXC0158 Différents types de ficelle de liage peuvent avoir des propriétés de frottement différentes. La contrainte de traction de l’écheveau doit être contrôlée lors du changement du type de ficelle de liage.La cote « X » dépend de la ficelle de liage choisie et doit être déterminée au cas par cas grâce au contrôle de l’écheveau. 3 x BP-VFS-016 VIII - 11 Réglages Tension de la ficelle sur l’écheveau supérieur Les écheveaux supérieurs (1) doivent être retenus par les freins (2) jusqu’à une force de traction comprise entre 100 et 120 N. Avant que les tendeurs de ficelle ne laissent glisser la ficelle, le bras de serrage de la ficelle (3) doit se déplacer vers le bas contre le retour élastique jusqu’à ce que la ficelle (1) soit conduite dans les œillets du bras du tendeur (4) pratiquement sans coude. Contrôle de la tension de la ficelle : Lier la ficelle (1) à une balance à ressort. La balance à ressort peut afficher une valeur comprise entre 100 et 120 N peu avant le glissement de la ficelle. BP-VFS-041 Pour augmenter la force de serrage, serrer l’écrou à ailettes (5). Desserrer l’écrou à ailettes pour diminuer la tension. La cote « X » dépend de la ficelle de liage choisie et doit être déterminée au cas par cas grâce au contrôle de l’écheveau. Lorsque la précontrainte de l’écheveau est réglée sur une valeur trop importante, des dysfonctionnements peuvent intervenir au niveau du noueur, et les éléments concernés seraient alors soumis à une charge trop importante. x Réglage X= 65 mm BPXC0204 Tension de la ficelle sur l’écheveau inférieur Les reteneurs de ficelle (1) de l’écheveau inférieur se trouvent ici derrière l’empaqueteur sous le canal de pressage. Pour augmenter la force de serrage, serrer l’écrou à ailettes (2). Desserrer l’écrou à ailettes pour diminuer la tension. 1 Réglage X= 70 mm Contrôle de la contrainte de traction : VIII - 12 BP1213012 1 X 1. Enfiler la ficelle conformément aux directives. 2. Déclencher manuellement le processus de nouage. 3. Tourner le volant à la main dans le sens de travail jusqu’à ce que les aiguilles de liage atteignent leur point mort haut. 4. Extraire la ficelle de liage des aiguilles sur une longueur de 200 mm environ, et la couper. 5. Tirer lentement et régulièrement l’écheveau jusqu’à ce que les ressorts tendeurs de la ficelle sous le canal atteignent leur position la plus haute. 6. Lors du maintien de la ficelle, les ressorts tendeurs doivent rester dans cette position sans que la ficelle puisse être retendue par le frein. 7. En cas de légère augmentation de la force de traction, le frein doit laisser glisser la ficelle. 2 BPXC0234 Réglages 8.3 Noueur Consignes de sécurité • • • Tous les travaux de maintenance, de réglage et de réparation sur les noueurs doivent exclusivement être effectués alors que la machine est à l’arrêt. Couper le moteur et retirer la clé de contact. Serrer le frein du volant. Rabattre la barre d’arrêt pour empêcher tout déclenchement involontaire du noueur. Mise en service Le noueur a été réglé et contrôlé par le fabricant. Il doit pouvoir fonctionner correctement sans qu’aucun réglage supplémentaire ne soit nécessaire. Si des problèmes surviennent avec le liage lors de la première mise en service, il n’est pas nécessaire de procéder tout de suite à une modification du réglage des dispositifs, car, dans ce cas, il s’agit la plupart du temps d’un problème dû à la peinture, à la rouille ou à des endroits rugueux. Il est recommandé, avant la première mise en service, d’éliminer la graisse antirouille du reteneur de ficelle et du noueur. 8.3.1 Noueur double Le ressort à lames (3) du contacteur (1) permet de tendre la lame (5) du crochet du noueur (2). • Si l’action de serrage est trop importante au niveau de la lame du noueur (5), le nœud reste accroché à la lame du noueur. L’écheveau casse. • Si l’action de serrage est trop faible, aucun nœud ou un nœud lâche est formé. Ces défauts peuvent être évités en corrigeant la tension du ressort à lames (3). Pour ceci : • Desserrer ou serrer l’écrou (4) du ressort à lames (3) de 60° env. 5 2 1 3 4 BPXC0046 La lame du noueur (5) requiert une tension minimale. Donc ne jamais complètement la desserrer. VIII - 13 Réglages 8.3.2 Retenue de la ficelle Réglage de l’entraîneur de ficelle Le fonctionnement de l’entraîneur de ficelle (5) dépend de la position de l’entaille par rapport à celle du nettoyeur (7) du disque porte-ficelle. L’entraîneur de ficelle (5) est préréglé en usine avec a= 0-2 mm • • Si l’entaille de l’entraîneur de ficelle (5) se trouve dans une position trop avancée (dans le sens des aiguilles d’une montre), la ficelle amenée par l’aiguille ne peut pas être saisie par l’entraîneur. Si l’entaille de l’entraîneur de ficelle (5) est par contre positionnée trop à l’arrière (dans le sens inverse des aiguilles d’une montre), les ficelles risquent de s’enrouler autour du bec noueur ou de ne pas être saisies par le bec du noueur. Réglage de l’entraîneur de ficelle (5) Pour ce faire, l’entaille de l’entraîneur de ficelle (5) doit se trouver dans la position indiquée. Puis : • • • • Desserrer l’écrou (4) jusqu’à ce qu’il affleure l’extrémité du filetage de la vis sans fin. Desserrer la vis sans fin en tapant légèrement contre l’écrou (4). Régler la cote a=0-2 mm en tournant la vis sans fin. Serrer l’écrou (4). Pour le contrôle de la position de l’entaille il faut que deux processus de liage aient été effectués au minimum. VIII - 14 1 6 2 7 3 5 a 4 BPXC0169 Réglages 8.3.3 Réglage de la force de retenue du reteneur de ficelle (6) La force de retenue est préréglée en usine. La nature et le degré d’humidité de la récolte, la densité de pressage, de même que le choix de la ficelle de liage, conditionnent les différents réglages qui, en cas de besoin, peuvent être adaptés dans les conditions de fonctionnement. 3RXUFHFL • • • Desserrer le contre-écrou (3) Serrer ou desserrer un peu les ressorts de retenue de la ficelle (2) au-dessus de la vis (1) (un demi-tour env.). Serrer le contre-écrou (3). Le reteneur de ficelle doit serrer la ficelle avec une force telle que la ficelle ne puisse pas être extraite de la retenue de la ficelle lors du processus de liage. Un effet de serrage trop intensif effiloche la ficelle. 1 6 2 7 3 5 a 4 BPXC0169 8.3.4 Levier du couteau Le levier du couteau (1) doit être aligné de sorte que le crochet du noueur (2) puisse tourner librement sans toucher le levier du couteau. Le peigne (3) du levier du couteau doit légèrement mais régulièrement toucher l’arrière du crochet du noueur (2). En position du point mort du levier du couteau, l’écart entre le peigne du levier du couteau et la pointe du crochet du noueur doit être égal à a = 15 à 18 mm. 3 1 a 2 Le levier du couteau a atteint la position du point mort lorsque le rouleau du levier du couteau se trouve sur le point le plus haut de la came (4) dans le disque du noueur (5). BPXC0048 5 4 BPXC0049 VIII - 15 Réglages Les zones conduisant les écheveaux du levier du couteau (zone marquée) doivent être lissées et arrondies pour éviter d’arracher la ficelle. Le levier du couteau doit être remplacé dès l’apparition de marques d’usure au niveau de la zone marquée (formation de stries). BP 380-7-096 Il est impératif de veiller à ce que l’arête de coupe du couteau de ficelle soit réaffûtée dès que les extrémités de la ficelle sont coupées à des longueurs différentes ou sont effilochées. En cas de cassure ou d’usure importante du couteau, ce dernier doit être remplacé. BP 380-7-097 8.4 Réglage du piston de presse • • Les galets du piston de presse doivent porter uniformément. Le fente entre les couteaux du piston de presse et les couteaux dans le canal de pressage doit être constante sur toute la largeur du piston. Le canal de pressage est équipé de deux couteaux (6). • Le piston de presse (3) du modèle Big Pack 1270/ 1290 possède sept couteaux. • Le piston de presse (3) du modèle Big Pack 890 ne possède que cinq couteaux (5) en raison de la faible largeur du canal de pressage. 2 Réglage des couteaux du piston de presse 1 Un réglage précis des couteaux du piston de presse est nécessaire pour obtenir des grosses balles au dessous lisse. Pour obtenir un écart « a » compris entre 2 et 4 mm, le piston de presse peut être réglé en hauteur grâce à des galets à excentrique (2). Lorsque les logements de serrage (1) sont desserrés, tourner les galets à excentrique pour lever et abaisser le piston de presse. Après le réglage, le logement de serrage doit être à nouveau serré. Veiller à ce que les rails de guidage (4) et les galets ne s’encrassent pas. Un encrassement des rails de guidage et des galets conduirait à une usure accrue et un réglage en hauteur imprécis du piston de presse. VIII - 16 a 1 2 3 4 5 6 BPXC0159 Réglages Nettoyage des glissières Des barres de nettoyage (2) sont montées au niveau des quatre galets (3) du piston de presse. Ces barres libèrent les glissières du piston de presse de tout dépôt. Pour procéder au réglage, desserrer les vis (1) et régler les barres de guidage sur la cote a = 1 - 2 mm. Resserrer les vis. 3 2 2 1 1 a Les barres de nettoyage (2) doivent pouvoir basculer légèrement sur l’axe des galets ! BP380-7-063 Réglage latéral du piston Le piston de compression doit être ajusté au centre du canal de pressage. Veiller à ce que le piston ait toute liberté de manœuvre et ne vienne pas frotter contre les racloirs sur le fond de canal ni sous la table du noueur. Pour régler latéralement le piston (2), l’amener en position la plus avancée en tournant le volant. BP1213013 3 Le réglage latéral du piston (2) est réalisé sur les plaques de compensation (1) (283-676-0), qui sont installées entre le piston (2) et le disque de glissement (3). 1 La lumière du piston sur le point le plus étroit du canal de pressage devrait être de a = 1 - 2 mm . 2 BPXC0192 VIII - 17 Réglages 8.5 Réglage de l’empaqueteur par rapport au piston de presse Le réglage de l’empaqueteur n’est nécessaire que si l’engrenage de ce dernier ou les chaînes de liaison des attelages à chaînes doivent être remplacés. 8.5.1 • 1 Contrôle de l’enclenchement de l’accouplement de l’empaqueteur 2 L’accouplement de l’empaqueteur est correctement engagé lorsque les deux marques extérieures (1) sur cet accouplement correspondent à la marque (2) sur la bague intérieure de ce même accouplement. BPXC0272 S’assurer que le système VFS se trouve en position neutre (voir le chapitre Réglage de la position neutre) 8.5.2 2 1 Réglage de l’empaqueteur Tournez l’empaqueteur en position de travail en tournant le volant à la main jusqu’à ce que • l a baguette d’arrivée (1) apparaisse dans la fenêtre d’inspection (2) sur le côté gauche de la machine (reconnaissable au fait qu’aucun rouleau n’apparaît dans la fenêtre d’inspection (2).) et • que le grand rouleau (3) de la barre d’empaqueteur (4) apparaisse dans la fenêtre d’inspection (5). Puis • tournez encore l’empaqueteur jusqu’à ce que le grand rouleau (3) de la barre d’empaqueteur (4) disparaisse d’environ la moitié dans la partie supérieure de la fenêtre d’inspection (5) 4 2 1 5 3 VIII - 18 5 3 4 BP1213014 Réglages • • • Stabiliser l’empaqueteur sur cette position avec un levier de montage. Retirer la chaîne articulée (5) de l’arbre levier de d’entraînement de l’engrenage de l’empaqueteur (7). Amener les tiges de piston en position étendue (point mort arrière) jusqu’à ce que les repères du (8) sur l’engrenage principal coïncident. 8 L’empaqueteur stabilisé par le levier de montage et le piston sont ainsi en position de réglage. • • • Placer et bloquer la chaîne articulée (5) de l’attelage à chaînes. Monter le revêtement de protection et retirer le levier de montage. Exécuter à la main un tour complet du volant dans le sens de travail. Vérifier ensuite une nouvelle fois le réglage. BPXC0206 5 7 BPXC0024 VIII - 19 Réglages 8.6 Système de remplissage variable VFS 8.6.1 Montage du râteau de retenue Le râteau de retenue (1) doit être monté dans la position supérieure (a). En cas de problèmes de débit avec les matériaux humides ou courts, il est possible de monter la coulisse de palpation (1) dans l'alésage inférieur (B). La forme des balles peut se détériorer après l'abaissement de la coulisse de palpation. 1 A B BP1213015_1 8.6.2 Réglage de l’accouplement Réglage de l’accouplement (en position neutre) 3 4 9 8.6.2.1 Réglage de la position neutre : Tourner manuellement le volant dans le sens de travail pour faire subir une rotation à l’empaqueteur, jusqu’à ce que le rouleau (8) s’enclenche dans le dispositif de positionnement neutre (9). Puis : 5 7 1. Ajuster la vis de réglage (3) de manière que le centre de rouleau (4) soit à B = 10 - 12 mm sur la languette de déclenchement (5) alors que l’accouplement est déconnecté et que l’enclume (6) est appliquée. 8 B 1 2. Pour cette position de l’enclume (4), la tige filetée (2) doit être ajustée de manière que le râteau de retenue (1) soit à C = 5 - 10 mm de la bordure de l’auge du râteau. 6 BPXC0160_1 C 2 BP1213028_1 VIII - 20 Réglages 3. Tirer alors le râteau de retenue (1) en position arrière. Les pointes des dents du râteau de retenue peuvent alors pénétrer de D = 0 - 5 mm dans l’auge de râteau. Marquer cette position avec la vis de réglage (7). D S’il est impossible d’obtenir les valeurs (C et D), il est possible que le dispositif amortisseur s’oppose au déplacement de pivotement du râteau de retenue. Si c’est le cas, corriger l’ajustage de la fourche de frein du dispositif amortisseur. (voir 8.6.4) 8.6.3 1 BPXC0236 4 Réglage de la sensibilité de déclenchement Le ressort (8) sert, par l’intermédiaire de l’enclume (4) et de la tige filetée (2), à contraindre le râteau de retenue et à le ramener dans sa position relevée après le ramassage de la récolte. Pour ceci, l’enclume (4) doit venir au niveau de la vis de réglage (7) de l’installation. La cote indicative de contrainte de ressort est de C = 215 mm. 8 7 2 C BP1213018_1 La tension du ressort doit être augmentée lorsque le remplissage en hauteur du canal de pressage n’est pas suffisant. -> Les vides sur les coins de balles sont dus la plupart du tempsà un andain mal formé ou à une conduite unilatérale. Réduire la tension de ressort si l’accouplement de surcharge de l’empaqueteur est activée trop souvent ! Une tension du ressort trop élevée peut bloquer l’empaqueteur et donc entraîner une diminution du débit. VIII - 21 Réglages 8.6.4 Dispositif amortisseur 2 1 Le dispositif amortisseur sert pour empêcher que le râteau de retenue provoque l’activation de l’accouplement VFS par un mouvement de recul. La longueur de course de freinage sur les deux positions finales est réglée sur la fourche de frein (2). Régler la fourche de frein (2) de manière que l’écart entre la plaque de frein (3) pour la position finale du râteau de retenue par rapport aux deux bords extérieurs de l’enclume (4) soit égal. Si ce n’est pas le cas, la fourche de frein (2) peut limiter la course de pivotement du râteau de retenue. 4 b BPXC0167_1 Le ressort (1) de frein sera contraint à la cote B = 60 mm (longueur utile de ressort). Contrôle du réglage Amener l’enclume (4) en position arrière en se servant du râteau de retenue. Mesurer la cote A entre le bord de l’enclume et le disque de frein (3). Amener l’enclume (4) en position avant en se servant du râteau de retenue. La cote A sur l’autre face de l’enclume doit être la même que précédemment. Si ce n’est pas le cas, corriger le réglage en déplaçant la fourche de frein (2). 3 A A 4 4 3 BPXC0237 8.6.5 Réglage de ressort de position zéro Le réglage du ressort s’effectue en position neutre (cf. chapitre Réglage de la position neutre) • En position d’encastrement zéro, le ressort doit être tendu à la cote « A » = 185 mm. A 1 BPXC0207 VIII - 22 Réglages 8.7 Réglage de base du frein à bande du volant a Le frein à bande se trouve sur le côté gauche du volant. Lorsque l’effet de freinage lors de l’actionnement du frein à bande n’est plus suffisant, ce dernier peut être ajusté grâce à l’allongement de la broche (1). Position de base : Cote a = 182 mm 1 BPXC0168 8.8 Régler la rampe d’éjection des balles La rampe d’éjection des balles représente une prolongation du canal de pressage lorsqu’elle est dépliée. Afin que les grosses balles soient déposées correctement sur le sol, la hauteur de la bordure arrière de la rampe d’éjection par rapport au sol ne doit pas être trop forte, sinon les balles risquent d’être endommagées pendant la dépose. 2 BP1213039 • • L’inclinaison de la rampe d’éjection des balles par rapport au sol est réglée sur la chaîne de fixation (2) de la rampe d’éjection des balles. Pour ce faire, ajuster les écrous (1) sur les deux côtés du canal de pressage. 2 1 BPXC0208 VIII - 23 Réglages 8.9 Réglage du ressort du tendeur de chaîne sur le ramasseur (modèle sans mécanisme de coupe) • Contraindre le ressort (1) en serrant l'écrou (2) pour obtenir une longueur de ressort X=62 mm. X BPXC0302 VIII - 24 Entretien et maintenance 9 Entretien, maintenance et graissage 9.1 Consignes de sécurité • • • • • • 9.2 Les travaux de révision, d’entretien, de maintenance et de nettoyage doivent toujours être effectués sur la machine à l’arrêt. Couper le moteur et retirer la clé de contact. Serrer le frein du volant. Immobiliser le tracteur et la presse à grosses balles pour empêcher tout déplacement. Lorsque les travaux de maintenance et d’entretien sont terminés, remonter correctement tous les revêtements et dispositifs de protection. Eviter tout contact entre la peau et les huiles ou les graisses. Les fluides hydrauliques s’écoulant sous haute pression peuvent causer de graves blessures. En cas de blessure, consulter immédiatement un médecin ! Risque d’infection. Afin d’éviter toute blessure ou accident, respecter également toutes les autres consignes de sécurité. Généralités Des intervalles d’entretien et de maintenance précis doivent être respectés pour garantir un fonctionnement parfait de la presse à grosses balles et pour réduire l’usure. Ceci concerne notamment le nettoyage, le graissage, la lubrification et l’enduction d’huile des éléments et composants. 9.2.1 Couples de serrage Couple de serrage MA (sauf en cas d’indication contraire). 5,6 Ø 29 42 8,8 10,9 MA (Nm) 2,2 3 4,4 4,5 5,9 8,7 7,6 10 15 18 25 36 37 49 72 64 85 125 100 135 200 145 215 160 210 310 225 330 425 610 730 1050 12,9 5,1 10 18 43 84 145 235 255 365 390 710 1220 800 1100 1150 1450 1350 1800 1950 2450 A 8.8 0. 1 M4 M5 M6 M8 M 10 M12 M14 M14x1,5 M 16 M16x1,5 M 20 M 24 M 24x1,5 M 24x2 M 27 M 27x2 M30 6,8 9 A A = Taille du filetage (Classe de résistance indiquée sur la tête de vis) BP380-7-073 350 1150 1550 1650 2100 Vérifier régulièrement le serrage des écrous et des vis (environ toutes les 50 heures) et les resserrer si nécessaire. IX - 1 Entretien et maintenance 9.2.2 Nettoyage Chaque fois qu’elle a été en contact avec de la poussière ou de la glume, la presse à grosses balles (et particulièrement les noueurs) doit être nettoyée. Lorsque les conditions de travail sont très sèches, le nettoyage doit être répété plusieurs fois par jour. Débarrasser également tous les jours la commande de l’empaqueteur et le volant de toute trace de poussière et de glume. 9.2.3 Pneumatiques • • • • • Les travaux de réparation au niveau des roues et des pneumatiques ne doivent être exécutés que par des spécialistes disposant des outils adaptés. Ne déposer la presse à grosses balles que sur un support plan et stable. Stabiliser en plaçant des cales et en serrant le frein de parking. Vérifier régulièrement le serrage des écrous de roue et les resserrer si nécessaire. Ne pas se tenir devant les pneus lors du gonflage à l’air comprimé. Les pneumatiques peuvent éclater par pression intérieure excessive. Risque de blessure ! Contrôler régulièrement la pression d’air. Lors du desserrage et du serrage des écrous de roue, respecter l’ordre indiqué sur la figure ci-contre. Lorsque la machine a fonctionné pendant 10 heures après le montage, contrôler le serrage des écrous de roue et les resserrer si nécessaire. Contrôler ensuite le serrage toutes les 50 heures de fonctionnement. Filetage M20 x 1,5 IX - 2 Ouverture Couples de serrage: MA (Nm) de clé boulons de boulons de moyeu moyeu non graissés graissés 27 360 380 1 8 3 6 5 4 7 2 BP 380-7-074 Entretien et maintenance Pression des pneumatiques Contrôler régulièrement la pression des pneus, la corriger si nécessaire.La pression des pneus dépend de la taille des pneus. Les valeurs figurent dans le tableau suivant. BP 12130 (XC) Désignation despneumatique Roues de jauge : 15x6.00 - 6 10 PR Essieux individuel : 800/45 R 26,5 174 D Essieu tandem : 500/55-20 150 A8 550/45-22,5 20 PR 620/50 R 22,5 154 D *) Type de machine Pression minimale Pression maximale (bar) (bar) Vmax <= 10 km/h tous les Big Pack Pression des pneus* recommandée (bars) Vmax <= 40 km/h pour essieux simples, Vmax <= 50 km/h pour essieux tandem 3,7 1,5 BP 12130 1,2 4,0 2,4 BP 12130 (XC) BP 12130 (XC) BP 12130 (XC) 1,6 1,2 1,2 3.0 4,0 3,2 3,0 3,5 2,4 La recommandation s'applique en particulier au type d'intervention mixte (champ/route) à la vitesse maximale autorisée de la machine. Si nécessaire, il est possible de réduire la pression des pneumatiques jusqu'à la valeur minimale. Il convient alors de respecter la vitesse maximale correspondante autorisée IX - 3 Entretien et maintenance 9.3 Système hydraulique 9.3.1 Consignes de sécurité spéciales • • • • • • • • Avant d’exécuter les travaux sur la presse à grosses balles, couper la pression sur les cylindres hydrauliques des volets de canal de pressage. Contrôler régulièrement les flexibles et les circuits hydrauliques et les remplacer lorsqu’ils sont endommagés. Les pièces de rechange utilisées doivent répondre aux exigences techniques du fabricant de la machine. Pour cette raison, n’utiliser que des pièces de rechange KRONE d’origine. Les travaux de réparation sur l’installation hydraulique ne peuvent être effectués que par des spécialistes habilités. Lors des travaux sur le système hydraulique, veiller à une propreté absolue. Contrôler le niveau d’huile hydraulique avant chaque mise en service. Respecter les intervalles de vidange de l’huile hydraulique et de remplacement du filtre à huile hydraulique. Eliminez l’huile usagée conformément à la réglementation. 9.3.2 Système hydraulique de bord Lors de la vidange de l’huile hydraulique, les cylindres hydrauliques des clapets de canal de pressage doivent être rentrés. Le système hydraulique de bord de la presse à grosses balles est alimenté en pression par une pompe hydraulique. Cette pompe est bridée à la boîte de transmission principale et ne demande aucun entretien. 3 2 L’huile hydraulique doit être vidangée et le filtre à huile hydraulique remplacé une fois par an au début de la saison des récoltes. Pour vidanger l’huile, tenir un récipient adapté prêt pour recueillir l’huile usée. Desserrer et sortir la vis de purge (1) sur le réservoir (2). Lorsque toute l’huile s’est écoulée, serrer à nouveau la vis de purge. Dévisser la vis de jauge (3) et verser la quantité correspondante d’huile hydraulique. Contrôler le niveau d’huile à l’aide de la tige de jaugeage (3). Les spécifications de l’huile hydraulique figurent dans les « Caractéristiques techniques ». Le filtre hydraulique (4) se trouve sur le côté gauche de la machine devant la boîte à ficelle. Intervalle de remplacement du filtre • Au début de chaque saison (au moins 1x par an) • Evacuer la pression du système hydraulique de la machine • Dévisser le logement de filtre • Remplacer l’élément filtrant • Visser le logement de filtre • Vérifier l’absence de fuites IX - 4 1 BP1213019 4 BPXC0175 Entretien et maintenance 9.3.3 Hydraulique de travail (confort) Remplacement du filtre : Le filtre hydraulique (1) se trouve dans la partie avant du timon et doit être remplacé une fois par an. Remplacement du filtre : voir chapitre « Système hydraulique de bord ». 5 Actionnement manuel d’urgence : Si le système électronique devait tomber en panne, les soupapes sont équipées d’un « Actionnement manuel d’urgence ». Exemple : BPXC0209 Rampe d’éjection à rouleaux 1. Visser la vis moletée au niveau de la soupape à siège A1 et B1. 2. A l’aide d’un objet pointu, enfoncer le coulisseau magnétique de la soupape à canaux (A). La rampe d’éjection à rouleaux est levée. 3. Maintenir le coulisseau magnétique enfoncé et sortir à nouveau les deux vis moletées jusqu’à la butée. Après l’actionnement manuel d’urgence, toutes les vis moletées des soupapes à siège doivent à nouveau être desserrées. A B3 A3 B2 A2 B1 A1 B P T LS IX - 5 Entretien et maintenance 9.3.4 Actionnement manuel d’urgence 9.3.4.1 Réglage de la force de compression • • Le réglage de pression des volets de canal de pressage est exécuté en mode de secours, alors que la machine fonctionne. Lors du réglage, procéder avec une grande prudence. Risque de blessure ! S’assurer que la machine puisse être immédiatement stoppée en cas de danger. • En cas de panne de l’électronique, il est possible de poursuivre le travail avec la presse à grosses balles en régime de secours pendant une durée limitée. • La force de compression maximale peut être dépassée en l’absence de régulation électronique. Ceci peut causer des dommages importants. Ne jamais travailler pendant une durée prolongée sans commande électronique. Le réglage de la force de compression des volets du canal de pressage s’effectue au niveau du bloc de commande hydraulique (1) sur le côté gauche de la machine sous le capot avant. 4 2 Réglage : • • Visser lentement la vis moletée (2) pour régler la pression souhaitée Lire la pression sur le manomètre (4). Après l’actionnement manuel d’urgence, la vis moletée (2) doit à nouveau être desserrée. 1 2 BPXC0188 9.3.4.2 Libérer le canal de pressage (confort) La soupape à siège « Desserrer les volets de pressage » se trouve à droite à côté du bloc de commande hydraulique pour la régulation de la force de compression au niveau du côté gauche de la machine sous le capot latéral. 3 Réglage : • Visser lentement la vis moletée (3) jusqu’à la butée pour desserrer les volets de pressage. Après l’actionnement manuel d’urgence, la vis moletée (3) doit à nouveau être desserrée. IX - 6 3 BPXC0189 Entretien et maintenance 9.4 Vidange et contrôle du niveau d’huile au niveau des transmissions 9.4.1 Généralités • • • Lors du contrôle du niveau d’huile des transmissions, veiller à ce que la presse à grosses balles se trouve bien en position horizontale. Utiliser les arêtes inférieures des boîtes à ficelle comme arête de référence. Les huiles à utiliser pour les différentes transmissions ainsi que les volumes de remplissage sont indiqués au chapitre « Caractéristiques techniques ». Pendant la saison des récoltes, contrôler quotidiennement tous les niveaux d’huile d’engrenage avant chaque utilisation et faire l’appoint lorsque cela est nécessaire. 9.4.2 Boîte de transmission principale Le verre-regard du niveau d’huile (3) et les vis de purge (2) se trouvent sur le côté gauche de la boîte de transmission principale (1). 1 Contrôle du niveau d’huile Avant chaque utilisation de la machine, contrôler le niveau d’huile dans la boîte de transmission principale. L’huile doit être visible sur le verre-regard (3). 2 3 Vidange Vidanger l’huile à chaque fin de saison. Pour ceci, dévisser la vis de contrôle (3) et la vis de purge (2). Recueillir l’huile s’écoulant dans un récipient adapté. Revisser la vis de purge et verser de l’huile neuve jusqu’au sondage de contrôle. Revisser la vis de contrôle. BP1213025 9.4.3 Engrenage de l’empaqueteur L’engrenage de l’empaqueteur (3) se trouve sur le côté gauche de la machine. Contrôle du niveau d’huile 3 Avant chaque utilisation de la machine, contrôler le niveau d’huile dans l’engrenage de l’empaqueteur (3). Pour ceci, desserrer la vis de contrôle (1). Le niveau d’huile doit atteindre le sondage de contrôle. Si nécessaire, faire l’appoint d’huile. Après le contrôle du niveau, revisser la vis de contrôle. Changement d’huile Vidanger l’huile à chaque fin de saison. Pour ceci, dévisser la vis de contrôle (1) et la vis de purge (2). Recueillir l’huile s’écoulant dans un récipient adapté. Revisser la vis de purge et verser de l’huile neuve jusqu’au sondage de contrôle. Revisser la vis de contrôle. 1 2 BP1213093 IX - 7 Entretien et maintenance 9.4.4 Boîte de distribution La boîte de transfert (2) se trouve sur le côté gauche de la machine. 2 Contrôle du niveau d’huile Avant chaque utilisation de la machine, contrôler le niveau d’huile dans la boîte de transfert (2). Pour ceci, desserrer la vis de contrôle (1). Le niveau d’huile doit atteindre le sondage de contrôle. Si nécessaire, faire l’appoint d’huile. Après le contrôle du niveau, revisser la vis de contrôle. 1 Changement d’huile 3 Vidanger l’huile à chaque fin de saison. Pour ceci, dévisser la vis de contrôle (1) et la vis de purge (3). Recueillir l’huile s’écoulant dans un récipient adapté. Revisser la vis de purge et verser de l’huile neuve jusqu’au sondage de contrôle. Revisser la vis de contrôle. BP380-7-080 4 1 3 9.4.5 Transmission supérieure et inférieure du ramasseur Les transmissions supérieure et inférieure du ramasseur (3) se trouvent sur le côté droit de la machine. 2 Contrôle du niveau d’huile Avant chaque utilisation de la machine, contrôler le niveau d’huile dans la transmission supérieure du ramasseur (3). Pour ceci, desserrer la vis de contrôle (1). Le niveau d’huile doit atteindre le sondage de contrôle (1). Si nécessaire, faire l’appoint d’huile. Après le contrôle du niveau, revisser la vis de contrôle. 4 Vidange Vidanger l’huile à chaque fin de saison. Pour ceci, desserrer la vis de contrôle (1) de la transmission supérieure ainsi que la vis de sortie d’air (4) et la vis de purge (2) de la transmission. Recueillir l’huile s’écoulant dans un récipient adapté. Revisser la vis de purge. Resserrer la vis de contrôle et la vis de sortie d’air. 3 1 2 BP000036 IX - 8 Entretien et maintenance 9.4.6 Transmission de l’entraînement du mécanisme de coupe modèle Big Pack XC en haut et en bas Sur le côté droit de la machine se trouvent en haut un engrenage angulaire, et en bas, une boîte de transfert ramasseur/mécanisme de coupe. Contrôle du niveau d’huile Avant chaque utilisation de la machine, contrôler le niveau d’huile dans l’engrenage angulaire supérieur (3). Pour ceci, desserrer la vis de contrôle (1). Le niveau d’huile doit atteindre l’arête inférieure du sondage de contrôle, faire l’appoint si nécessaire. 3 1 Changement d’huile Vidanger l’huile à la fin de chaque saison de récolte. Pour ceci, desserrer la vis de purge (2) et la vis de contrôle (1). Recueillir l’huile dans un récipient adapté et l’éliminer dans le respect de l’environnement. Serrer la vis de purge (2) et verser de l’huile jusqu’au sondage de contrôle. Serrer la vis de contrôle (2). 2 4 5 6 Contrôle du niveau d’huile 1 BPXC0179 Avant chaque utilisation de la machine, contrôler le niveau d’huile de la boîte de transfert (5) ramasseur/mécanisme de coupe en bas. Pour ceci, desserrer la vis de contrôle (1). Le niveau d’huile doit atteindre l’arête inférieure du sondage de contrôle, si nécessaire, verser de l’huile par l’alésage de purge d’air (4). Changement d’huile Vidanger l’huile à la fin de chaque saison de récolte. Pour ceci, desserrer la vis de sortie d’air (4), la vis de purge (6) et la vis de contrôle (1). Recueillir l’huile dans un récipient adapté et l’éliminer dans le respect de l’environnement. Serrer la vis de purge (6) et verser de l’huile jusqu’au sondage de contrôle. Resserrer la vis de contrôle (1) et la vis de sortie d’air (4). IX - 9 Entretien et maintenance 9.5 Système de freinage 9.5.1 Consignes de sécurité spéciales • • • • • Les travaux sur le système de freinage ne doivent être exécutés en atelier spécialisé ou par les spécialistes ayant reçu une formation adéquate. Les Ets KRONE n’endossent aucune garantie pour l’usure naturelle, les dysfonctionnements par surcharge et les modification du système de freinage. Il est interdit de modifier le système de freinage sans autorisation des Ets KRONE. Remédier immédiatement aux dysfonctionnements et défauts du système de freinage. La presse à grosses balles ne doit être utilisée en intervention ou sur la route que si le système de freinage est en parfait état. 9.5.2 Réservoir à air comprimé Avant de laisser s’écouler les condensats des réservoirs d’air comprimé, s’assurer que la machine est correctement immobilisée et ne risque pas de se déplacer. Serrer le frein parking et bloquer les roues à l’aide de cales. Les presses à grosses balles équipées d’un frein à air comprimé possèdent deux réservoirs à air comprimé, ainsi que des vérins de freinage pneumatiques. L’eau de condensation s’accumule dans les réservoirs à air comprimé. L’eau de condensation peut être à l’origine de dysfonctionnements. C’est pourquoi elle doit être évacuée une fois par semaine. L’eau de condensation peut s’écouler au niveau de la valve de purge (3). Les modèles avec freins à commande hydraulique ne disposent que d’un seul réservoir à air comprimé pour le nettoyage du noueur. Dans les presses à grosses balles avec freins à air comprimé, le réservoir à air comprimé (2) du système de freinage se trouve sur le côté droit de la machine. Il est relié au réservoir à air comprimé (4) pour le nettoyage du noueur par une conduite de haute pression (1). Le réservoir pour le nettoyage du noueur se trouve sur le côté droit de la machine, en haut à droite sur la boîte à ficelle. Dans ce réservoir également, les condensats doivent être évacués par la valve de purge. IX - 10 1 4 2 3 BP1213026 Entretien et maintenance 9.5.3 Régler le dispositif de transmission Réglage des freins Vérifier régulièrement l’usure et le fonctionnement des freins en fonction de la sollicitation et procéder si nécessaire aux corrections. Après les premiers kilomètres de déplacement, les dispositifs de transmission et les garnitures de freins sur le tambour de frein se sont adaptés. Le jeu qui apparaît alors doit être compensé. a 2 Réglage sur la tringlerie 1 - tous les 200 heures de fonctionnement - b 3 Actionner manuellement la tringlerie dans le sens de la pression. Pour une course à vide (a) de max. 35 mm le réglage de la tringlerie doit être ajusté. BPXC0178 Le réglage se fait au niveau de la vis de réglage (b) de la tringlerie. Régler la course à vide «a» à 10 - 12 % de la longueur de hauteur de relevage de frein «B», par exemple hauteur de levage 125 mm = course à vide de 12 à 15 mm. 9.5.4 Vérins de freinage 1 Risque de blessure ! Avant de démonter le cylindre à membrane, purger la surpression sur le système d’air comprimé. Les vérins de freinage (1) ne nécessitent aucun entretien spécifique. Tous les deux ans au minimum, les vérins de freinage à membrane doivent être démontés, nettoyés, munis de nouvelles pièces d’usure puis remontés. BP380-7-085 IX - 11 Entretien et maintenance 9.6 Compresseur Sur la presse à grosses balles à freins hydrauliques, l’alimentation en air comprimé pour le nettoyage de noueur est réalisée par un compresseur (1) installé entre les poutres de timon. Il est actionné par une poulie de courroie trapézoïdale (3) et une courroie trapézoïdale (2) installées sur le volant. La tension de la courroie trapézoïdale est ajustée par déplacement du compresseur sur les orifices (5). Le niveau d’huile dans le compresseur doit être contrôlé tous les jours avant la mise en service à l’aide de la jauge d’huile (4). Faire le plein d’huile si nécessaire (huile moteur SAE 20). Les spécifications de l’huile hydraulique figurent dans les « Caractéristiques techniques ». Nettoyez le filtre à air (6) au moins une fois par jour, en cas de forte exposition à la poussière plusieurs fois par jour. Si l’encrassement du filtre est trop fort, le manchon d’aspiration (7) peut être fixé sur le toit de la cabine du tracteur avec le jeu de pièces à rapporter (n° de référence 287 363). Nettoyage de filtre • • • • • • Basculer l’étrier de support (2) du filtre à air (1) vers le haut/bas. Démonter le couvercle (4). Démonter la cartouche filtrante (3), secouer et la souffler à l’air comprimé de l’intérieur vers l’extérieur. Démonter le couvercle (4) et secouer Monter la cartouche filtrante Placer le couvercle sur le filtre et fixer avec les étriers Veillez à ce que le pot du filtre et le filtre à air soient absolument hermétiques. IX - 12 1 5 2 7 6 3 4 1 BPXC0249 2 2 3 4 BP800100 Entretien et maintenance 9.7 Lubrification 9.7.1 Consignes de sécurité spéciales • • • • • Les travaux de révision, d’entretien, de maintenance et de nettoyage doivent uniquement être effectués sur la machine à l’arrêt. Couper le moteur et retirer la clé de contact. Serrer le frein du volant. Immobiliser le tracteur et la presse à grosses balles pour empêcher tout déplacement. Lorsque les travaux de maintenance et d’entretien sont terminés, remonter correctement tous les revêtements et dispositifs de protection. Eviter tout contact entre la peau et les huiles ou les graisses. En cas de blessure due à l’huile, consulter immédiatement un médecin. 9.7.2 Généralités Selon les modèles, la presse à grosses balles est équipée de différents systèmes de lubrification. Utiliser, comme graisse lubrifiante, des graisses à base de savon de lithium de classe NLGI 2 avec des additifs extrême-pression selon la norme DIN 51825. L’utilisation de graisses lubrifiantes à base d’autres produits est déconseillée. Ne pas utiliser de graisses contenant du graphite ! Eviter de mélanger différentes graisses ! Fabricant ARAL à base d’huiles minérales Graisse longue tenue H BP Energrease LS-EP2 DEA Glissando EP2 FINA Marson EPL 2A Shell Alvania Ep2 ESSO EGL 3144 lubrifiants biologiques sur demande 9.7.3 Graissage Les points de lubrification de la presse à grosses balles doivent être graissés régulièrement. Les plans de graissage de la notice d’utilisation donnent la localisation des points de graissage et la périodicité de graissage. Après le graissage, éliminer la graisse excédentaire au niveau des paliers. 50 10 939 212-1 Intervalles de graissage : 10 h correspond à une fois par jour environ 50 h correspond à une fois par semaine environ 200 h correspond à une fois par semaine environ 939 450-1 BP 380-7-088 9.7.3.1 Arbre à cardan principal Les intervalles de graissage de l’arbre à cardan principal figurent sur la figure ci-contre. Pour plus de renseignements, consulter les instructions d’utilisation du fabricant de l’arbre à cardan. IX - 13 Entretien et maintenance 9.7.3.1 Arbres à cardan Les arbres articulés doivent être lubrifiés toutes les 50 heures au niveau des points marqués. Le nombre d'actionnement de pompe par point de graissage est indiqué sur les figures BPXC0283 et BPXC0284. Pour plus de renseignements, consulter les instructions d’utilisation du fabricant de l’arbre à cardan. BP 1290 HDP BP 12130 5x Arbre à cardan, entraînement principal 40x 8x 5x 5x 1x BPXC0283 BP 1290 HDP BP 12130 Arbre à cardan, volant 5x 5x 1x BPXC0284 IX - 14 Entretien et maintenance 9.7.3.2 Lubrifier les galets de roulement des leviers des couteaux • Abaisser le mécanisme de coupe et sortir latéralement le tiroir (voir chap. " Mécanisme de coupe XC "). • Verrouiller l'arbre de commande (1) avec le levier de commande du couteau (2). 2 1 BP050910 • Déposer le levier de l'outil de lubrification (1 a) sur le logement des deux leviers (2) sur le mécanisme de coupe. 2 • Serrer le levier de l'outil de graissage (1 a). • Enclencher le support de l'outil de graissage (1 b) sur le cadre du mécanisme de coupe. 1a 1b BP050920 • Lubrifier le nipple de graissage (1) à côté des deux leviers reculés. 1 BP050292 IX - 15 Entretien et maintenance 9.7.4 Points de lubrification Le tableau suivant répertorie les points de lubrification de la presse à grosses balles ainsi que le nombre de graisseurs. Points de lubrification Big Pack 12130 (XC) gauche droite Intervalle (lubrification centralisée automatique) Lubrification centralisée Maneton de manivelle de l'entraînement de piston 1 1 autom. graissage centralisé Axe du piston de l'entraînement du piston de presse 1 1 autom. graissage centralisé Galets de roulement du piston 2 2 autom. graissage centralisé Empaqueteur : Peigne : Levier convoyeur 10 Mécanisme de coupe XC : Ramasseur : 2 Arbre d'entraînement vertical (option) Limiteur débrayable Protection individuelle des couteaux Guidage à cames Lubrification chaîne droite et gauche Lubrification chaîne d'entraînement Roue libre Roues de jauge pendulaires : 13 huiler 1 1 5 13 50 h 50 h 200 h non non non 1 huiler huiler 1 10 h 10 h 50 h autom. graissage centralisé autom. graissage centralisé autom. graissage centralisé non autom. graissage centralisé 1 Frein parking 1 Essieu simple : Palier de levage de frein (en option) 1 Essieu tandem : Palier d'axe pendulaire Palier auto-suiveur, auto-suiveur (en option) Palier de came de frein Palier de levage de frein 1 2 4 2 Arbre à cardan Entraînement principal Ramasseur entraînement (en option) Entraînement noueur 11 2 3 Noueur double : Cadre de suspension des aiguilles Palier de noueur sur moyeu Palier du levier du couteau Palier du bec du noueur Palier du reteneur de ficelle Palier arbre d'entrainement du reteneur de ficelle Palier central arbre de noueur 1 IX - 16 autom. graissage centralisé 200 h non 1 50 h non 1 2 4 2 50 h 50 h 50 h autom. graissage centralisé non non non 50 h 200 h 200 h non non non 1 1 autom. graissage centralisé autom. graissage centralisé autom. graissage centralisé autom. graissage centralisé autom. graissage centralisé autom. graissage centralisé autom. graissage centralisé Entretien et maintenance Points de lubrification de la presse à grosses balles (côté gauche de la machine) Modèle avec mécanisme de coupe XC 10h 50h 50h 10h 200h BP1213036 * 10h 10h 5x 8/13 x 200h 200h * 10h 50h * 10h 50h * lubrification centralisée automatique complète Autres informations, voir chapitre Graissage. IX - 17 * Entretien et maintenance Points de lubrification de la presse à grosses balles (côté droit de la machine) BP1213037 10h IX - 18 10h 10h BP 12130 = 8 x 10h 10h 50h 50h 50h 10h 200h 8/13 x 4x 10h 50h 50h 200h 50h 10h Modèle avec mécanisme de coupe XC Entretien et maintenance Points de lubrification de la presse à grosses balles avec mécanisme de coupe XC (côté gauche de la machine) BP1213032 50h 50h 10h 50h 250h 10h 10h 5x 10h 200h 50h 50h 50 100 bar 150 10h 50h Modèle sans mécanisme de coupe XC IX - 19 Entretien et maintenance Points de lubrification de la presse à grosses balles avec mécanisme de coupe XC (côté droite de la machine) IX - 20 BP1213033 10h BP 12130 = 8 x 10h 10h 50h 50h 50h 10h 50h 10h 50h 10h 200h 50h 10h Modèle sans mécanisme de coupe XC Entretien et maintenance 9.7.5 Graissage centralisé (option) Description fonctionnelle du graissage centralisé BEKA-MAX Le graissage centralisé BEKA-MAX est une installation progressive. Progressive signifié que tous les points de graissage connectés à l’installation sont graissés les uns après les autres. Grâce à ce graissage progressif, l’installation peut être surveillée facilement par une soupape de surpression. Quand un point de graissage ne reçoit pas de graisse du distributeur, le distributeur progressif est bloqué et la pression sur le graissage centralisé s’établit à 280 bar.La sortie de graisse sur la vanne de surpression de l’élément de pompe permet de reconnaître un blocage. Tout excès de graisse au niveau de la vanne de surpression de la pompe peut entraîner un blocage. Un message d’erreur apparaît sur l’affichage. Structure du graissage centralisé BEKA-MAX Une pompe à piston à commande électrique EP-1 transporte le graisse dans le distributeur progressif principal. Celui-ci dose la quantité de graisse correcte en direction des sous-distributeurs. Les sousdistributeurs alimentent les différents points de graissage. 2 3 4 5 6 7 8 9 Réservoir transparent Bouchon de remplissage Soupape de surpression Distributeur progressif principal Sous-distributeur progressif Circuit principal Circuits de graisse Points de graissage 4 2 3 7 5 9 6 8 Description de la commande Les temps de graissage et de pause sont réglés sur l’unité de commande dans la cabine du tracteur (voir les chapitres 4 et 5). IX - 21 Entretien et maintenance 9.8 Emplacement des capteurs 4 5 BP1213034-2 Côté droit de la machine 1 2 3 4 Contrôle de noueur Capteur de force droit Capteur de force gauche Etalonner IX - 22 5 6 7 8 Mesurer Ejecteur de balles Alimentation de l’empaqueteur Contrôle de l’empaqueteur Entretien et maintenance BP1213035 Côté gauche de la machine 1 2 3 4 5 6 7 8 Couteaux activés Barre de coupe supérieure Pression sur les volets de pressage Contrôle de ficelle Tige de traction d’aiguille Dépose de balles Frein du volant Pickup 9 Bouton-poussoir barre de coupe monte Bouton-poussoir barre de coupe baisse 10 Balles multiples 11 Bouton-poussoir de rentrée de l’éjecteur de balles Bouton-poussoir de sortie de l’éjecteur de balles Bouton-poussoir rampe d’éjection de balles monte Bouton-poussoir rampe d’éjection de balles baisse 12 Rampe d’éjection des balles IX - 23 Entretien et maintenance 9.9 Réglage des capteurs Capteur type Namur d = 12 mm La distance entre le transmetteur (2) et le capteur (1) doit être égale à « a » = 2 mm. 3 Réglage • Desserrer les écrous des deux côtés du capteur. • Tourner les écrous jusqu’à ce que la distance « a » = 2 mm soit atteinte. • Resserrer les écrous. 1 a 2 BP-VFS-088-1 Capteur type Namur d = 30 mm La distance entre le transmetteur (2) et le capteur (1) doit être égale à « a » = 6 mm. 3 Réglage • Desserrer les écrous des deux côtés du capteur. • Tourner les écrous jusqu’à ce que la distance « a » = 5 mm soit atteinte. • Resserrer les écrous. 1 a 2 BPXC0172 IX - 24 Défauts - causes - remèdes 10 Défauts, causes, remèdes 10.1 Consignes de sécurité • • • • • • • • Pour tous les travaux de maintenance, de montage, de réparation et de réglage, les mesures suivantes doivent toujours être prises Stopper la machine. Couper le moteur. Retirer la clé de contact. Serrer le frein de volant. Immobiliser le tracteur et la presse à grosses balles pour empêcher tout déplacement. Verrouiller le noueur pour empêcher tout actionnement involontaire. Activer le frein de volant et bloquer le volant. Eviter tout contact entre la peau et les huiles, les graisses, les solvants et les détergents. En cas de blessures ou de brûlures par acide provoquée par des huiles, des détergents ou des solvants, consulter immédiatement un médecin. Lorsque les travaux de maintenance et d’entretien sont terminés, remonter correctement tous les revêtements et dispositifs de protection. Respecter également toutes les autres consignes de sécurité. X-1 Défauts - causes - remèdes 10.2 Défauts généraux Cause et/ou remède Défaut Le piston de presse/dispositif de liage reste immobile. 1. Immobiliser immédiatement le tracteur. 2. L’accouplement de coupure à cames dans le volant s’enclenche à nouveau lorsque la vitesse de rotation est réduite. 3. Diminuer la force de pression. 4. Contrôler la vitesse de l’arbre à cardan du tracteur. 5. Sortir les aiguilles du canal de pressage, si nécessaire remplacer la vis de cisaillement dans l’entraînement du noueur et des aiguilles. Les aiguilles retombent. 1. Serrer le frein de l’arbre du noueur. Balles trop lâches. 1. Augmenter la force de pression. Balles trop compactes. 1. Diminuer la force de pression. 1. Le coupleur de surcharge s'engrène – réduire la vitesse du moteur. 2. Immobiliser le tracteur et la machine et éliminer l’engorgement. 3. Diminuer la vitesse de déplacement. L’empaqueteur reste immobile. 1. Le coupleur de surcharge s'engrène – déconnecter l’entraînement de la prise de force et éliminer l’engorgement. 2. Diminuer la vitesse de déplacement. 3. Se placer au milieu au dessus des andains. Le ramasseur reste immobile. Le rotor de coupe et le ramasseur restent immobiles. Le cadre de suspension des aiguilles reste immobile. 1 2 BP380-7-133 X-2 1. Engorgement dans la zone du rotor, l’accouplement de coupure à cames dans la barre d’entraînement du rotor engrène. 2. Réduire la vitesse du moteur. L’accouplement s’enclenche à nouveau lorsque la vitesse diminue. 3. Basculement vers l’extérieur de la lame 4. Si le rotor ne se libère pas tout seul, stopper le tracteur et la machine et éliminer l’engorgement. 5. Diminuer la vitesse de déplacement. 1. La tige de traction (1) du cadre de suspension des aiguilles est bloquée par une vis de cisaillement (2). 2. Vérifier si la vis de cisaillement est rompue. 3. Si nécessaire, la remplacer par une vis M10 x 55, DIN 931-10.9. Défauts - causes - remèdes X-3 Défauts - causes - remèdes 10.3 Défauts du noueur La pratique a montré que la plupart des problèmes de liage proviennent d’une tension de ficelle insuffisante. Contrôler le parcours et la tension de la ficelle avant de commencer le travail. Le tableau ci-dessous répertorie les défauts les plus fréquents ainsi que leur cause et une indication concernant leur élimination. Le chapitre dans lequel le thème traité est expliqué en détail est également cité. X-4 Supprimer les emplacements rugueux, remplacer les pièces défectueuses. Contrôler puis corriger, le cas échéant, le parcours inférieur de la ficelle. 2.1 Emplacements usés ou rugueux sur le crochet du noueur, respectivement crochet ou lame du noueur masquée. 2.2 Tension de la ficelle trop faible sur l’écheveau inférieur. Le nœud reste accroché au crochet du noueur. 2 2.3 Force de retenue du reteneur de ficelle trop faible. Voir n°2 1.1 Le deuxième nœud reste accroché à la lame du noueur. Lame du noueur pliée ou cassure fréquente de la lame du noueur 1 Dégraisser le reteneur de ficelle Ajuster le reteneur de ficelle en : • desserrant le contre-écrou (2) • serrant un peu plus les ressorts de retenue de la ficelle (3) au-dessus de la vis (1) (env. un demi-tour) • serrant le contre-écrou (2). • retirant l’accumulation de saleté dans tous les œillets de la ficelle (4), du reteneur de ficelle (1) et sur l’angle de pendule (7). • remplaçant les ressorts cassés (2), les ressorts tendeurs de la ficelle (5) ou les œillets usés de la ficelle (4). • remplaçant les roues de freinage cassées ou usées (6). Serrer le reteneur de ficelle (1) en : • serrant le ressort (2) en tournant 1-2 fois les écrous à oreilles (3). Dépannage Cause possible Défaut N° 2 1 4 3 1 3 5 6 2 4 BPXC0255 BPXC0254 7 Défauts - causes - remèdes X-5 X-6 2.5 Tension de la ficelle trop faible sur l’écheveau supérieur. Desserrer la lame du noueur (3) en : • déterminant d’abord la force de serrage à l’aide d’un tournevis (insérer le tournevis (4) sous la lame du noueur (3) puis déterminer la force en le tournant). • desserrant l’écrou (2) du ressort à lames (1) de 60° env. • insérant le tournevis (4) sous la lame du noueur (3) puis en contrôlant la force réglée en tournant le tournevis 2.4 Tension excessive au niveau de la lame du noueur. Le nœud reste accroché au crochet du noueur. 2 • retirant l’accumulation de saleté dans tous les œillets de la ficelle (4) et du reteneur de ficelle (1). • remplaçant les ressorts cassés (2) ou les œillets usés de la ficelle (4). • remplaçant les roues de freinage cassées ou usées (6) • contrôlant la liberté de manœuvre du bras de serrage (5) (cf. défaut n° 6.3 illustration BPXC0263) Serrer le reteneur de ficelle (1) en : • serrant le ressort (2) en tournant 1-2 fois les écrous à oreilles (3). La lame du noueur (3) requiert une tension minimale. Donc ne jamais complètement la desserrer. Dépannage Cause possible Défaut N° 6 1 2 1 2 4 3 3 4 BPXC0256 BPXC0259 Défauts - causes - remèdes Défaut Le nœud reste accroché au crochet du noueur. N° 2 Dépannage Serrer l’écrou (1) de l’axe du levier du couteau (2) ou remplacer le levier du couteau (3), respectivement le coussinet du levier du couteau. 2.10Disque entraîneur de la ficelle trop en avant. Vérifier le réglage, ajuster si nécessaire. (voir le chapitre Réglages noueur double « reteneur de ficelle ») 2.9 Couteau du dévêtisseur du Régler, affûter ou remplacer la lame de coupe (4). levier émoussé. 2.8 Peigne du levier du couteau Ajuster le levier du couteau : (cf. défaut n° 2.5 n’est pas centré au-dessus illustration BPXC0260) du bec du noueur. • Remplacer le levier du couteau 2.7 Jeu axial du levier du couteau. Lors du pivotement vers le haut du noueur, il faut sentir une légère résistance lorsque le levier du couteau passe sur le bec du noueur 2.6 Levier du couteau trop loin Ajuster le levier du couteau : du crochet du noueur. • pivoter le chevalet de noueur vers le haut jusqu’à ce que le levier du couteau (1) pivote au-delà du crochet du noueur (2). • Ajuster prudemment le levier du couteau (1) au moyen d’un marteau jusqu’à ce que le peigne (3) du levier du couteau affleure de manière homogène l’arrière du crochet du noueur (2). Cause possible 1 2 3 2 1 2 BPXC0269 3 ! 4 BPXC0257 1 BPXC0260 Défauts - causes - remèdes X-7 X-8 Premier nœud : (nœud à 4.1 L’aiguille inférieure n’arrive boucles) pas à saisir la ficelles de la ficelle s’enroule dessus du côté gauche. autour du crochet du noueur. 4 4.2 Disque entraîneur de la ficelle réagit trop tard. Premier nœud : (nœud à 3.1 La barre à ficelle n’a pas boucles) existant saisi l’écheveau inférieur. exclusivement au niveau de l’écheveau supérieur. Cause possible 3 N° Défaut Veiller à ce que l’aiguille du noueur touche le noueur en position haute. (voir le chapitre Réglages « Point mort supérieur des aiguilles » (noueur double)) • déclenchant le noueur et en tournant le volant jusqu’à ce que l’aiguille supérieure se soulève. • ajustant l’aiguille supérieure (1) de 1-2 mm vers la gauche à l’aide d’un levier de montage (2). Tourner le disque entraîneur de la ficelle dans le sens des aiguilles d’une montre pour l’avancer. (voir le chapitre Réglages noueur double « reteneur de ficelle ») Légèrement décaler l’aiguille supérieure vers la gauche en : Contrôler le réglage d’aiguille. (voir le chapitre Réglages « Réglage d’aiguille ») Ajuster la barre à ficelle. (voir le chapitre Réglages « Réglage de la barre à ficelle (noueur double) ») Dépannage 1 BPXC0261 2 Défauts - causes - remèdes Remplacer ou fixer à nouveau le ressort (1). Contrôler de haut en bas que le bras de 6.3 Le bras de serrage ne fonctionne pas correctement. serrage (2) dispose de suffisamment d’espace libre. Le cas échéant, l’ajuster ou décaler la conduite de la lubrification centralisée (3). 6.2 Ressort du bras de serrage supérieur cassé ou décroché. Deuxième nœud : 6.1 La barre à ficelle est réglée (nœud de départ) trop loin de l’aiguille nœud existant supérieure et ne peut pas exclusivement au niveau saisir l’écheveau supérieur. de l’écheveau inférieur (pas de nœud au niveau de l’écheveau supérieur). 6 Régler la barre à ficelle en direction de l’aiguille supérieure. ATTENTION : lors du réglage de la barre à ficelle, s’assurer qu’elle ne heurte pas l’aiguille supérieure et l’aiguille du noueur (voir le chapitre Réglages « Réglage de la barre à ficelle (noueur double) ») L’aiguille inférieure n’arrive pas Légèrement décaler l’aiguille supérieure vers la droite en : à saisir la ficelle de dessus à droite • déclenchant le noueur et en tournant le volant jusqu’à ce que l’aiguille supérieure se soulève. • ajustant l’aiguille supérieure (1) de 1-2 mm vers la droite à l’aide d’un levier de montage (2). Premier nœud : (nœud à boucles) La ficelle de dessus glisse d’une balle à l’autre. Nœud sur l’écheveau inférieur 5 Dépannage Cause possible Défaut N° 3 2 1 BPXC0263 2 1 BPXC0262 Défauts - causes - remèdes X-9 X - 10 8 7 • serrant le ressort (2) en tournant 1-2 fois les écrous à oreilles (3). Veiller à ce que les ressorts tendeurs inférieurs de la ficelle (5) disposent de l’espace nécessaire. Serrer le reteneur de ficelle (1) en : Ajuster le reteneur de ficelle (cf. défaut n° 2.2) Desserrer le frein de ficelle (1) en : • serrant le ressort (2) en tournant 1-2 fois les écrous à oreilles (3) (cf. défaut n° 2.4) Contrôler le parcours de la ficelle supérieure entre le noueur et la bobine dans la boîte à ficelle Remplacer le galet (1) ou veiller à ce que l’aiguille supérieure puisse se déplacer facilement. Contrôler le ressort (2). Dépannage 8.1 Les bras de serrage Deuxième nœud : supérieurs ne fonctionnent (nœud de départ) pas correctement. la ficelle s’enroule autour • La trajectoire de serrage est du crochet du noueur. bloquée • La tension est insuffisante. S’assurer que les bras de serrage se déplacent facilement. • Libérer la trajectoire de serrage (cf. défaut n° 6 illustration BPXC0263) • Augmenter la tension (cf. défaut n° 2 illustration BPXC0256) 7.3 La barre à ficelle n’est pas Contrôler le réglage par rapport à la barre à assez précise ou est mal réglée. ficelle (voir le chapitre Réglages « Réglage de la barre à ficelle (noueur double) ») 7.2 Dépassement insuffisant de Contrôler le réglage des aiguilles. l’aiguille au niveau du point (voir le chapitre Réglages « Réglage mort supérieur. d’aiguille ») 6.7 Force de retenue du reteneur Deuxième nœud : de ficelle trop faible. (nœud de départ) nœud existant exclusivement au niveau 7.1 Les ressorts tendeurs inférieurs de la ficelle ne de l’écheveau supérieur fonctionnent pas (pas de nœud au niveau correctement. de l’écheveau inférieur). 6.6 Tension de la ficelle trop élevée au niveau de l’écheveau supérieur du reteneur de ficelle. 6.4 Défaut de la commande de Deuxième nœud : l’aiguille supérieure. Le galet (nœud de départ) ne suit pas le disque-came. nœud existant L’aiguille supérieure ne exclusivement au niveau descend pas assez de l’écheveau inférieur profondément. (pas de nœud au niveau de l’écheveau supérieur). 6.5 Obstruction du parcours de la ficelle supérieure. 6 Cause possible Défaut N° 2 1 3 2 5 1 BPXC0265 BPXC0264 Défauts - causes - remèdes 9 Aucun nœud existe, ni dans l’écheveau supérieur ni dans l’écheveau inférieur. Les écheveaux sont coupés dans le reteneur de ficelle. ou 9.4 Ressorts de retenue de la ficelle trop tendus. Eliminer les dépôts de poussière et de glume sous les ressorts de retenue de la ficelle (5). Desserrer le réglage du ressort de retenue de la ficelle. Pour ceci : • Desserrer le contre-écrou (4) • desserrer légèrement les ressorts de retenue de la ficelle (5) au-dessus de la vis (6) (un demi-tour env.) 9.3 Tension insuffisante au Augmenter la tension au niveau de la lame du niveau de la lame du noueur. noueur (1). Pour ceci : • serrer l’écrou (2) du ressort à lames (3) de 60° env. (cf. défaut n° 2.3) 9.2 Lame du noueur endommagée. Remplacer la lame du noueur (1). Contrôler le mécanisme d’arrêt de la ficelle et son réglage. (voir le chapitre Réglages « Réglage de la barre à ficelle (noueur double) ») Contrôler le réglage d’aiguille (voir le chapitre Réglages « Point mort supérieur des aiguilles » (noueur double)) 8.5 Dépassement trop important de l’aiguille au niveau du point mort supérieur 9.1 La barre à ficelle n’est pas actionnée. Tourner le disque entraîneur de la ficelle dans le sens des aiguilles d’une montre pour l’avancer. (voir le chapitre Réglages noueur double « reteneur de ficelle ») • Augmenter la tension (cf. défaut n° 2.1 illustration BPXC0254) Remplacer ou remonter le ressort. (cf. défaut n° 2.1 illustration BPXC0254) Dépannage 8.4 Disque entraîneur de la ficelle réagit trop tard. Deuxième nœud : 8.2 Ressort tendeur inférieur de (nœud de départ) ficelle cassé ou détaché. la ficelle s’enroule autour du crochet du noueur. 8.3 Tension de la ficelle insuffisante au niveau de l’écheveau inférieur. 8 Cause possible Défaut N° 1 5 3 5 4 2 BPXC0267 Défauts - causes - remèdes X - 11 X - 12 Contrôler le parcours de la ficelle. Pour obtenir des extrémités du nœud plus longues, augmenter dans un premier temps la tension de la ficelle inférieure (cf. défaut n° 2 illustration BPXC0254) Lorsque cela ne suffit pas, augmenter la tension de la ficelle supérieure 10.2 Tension de la ficelle incorrecte. La ficelle n’est plus enfilée sur l’aiguille du noueur mais liée à la dernière balle. 11 Centrer le ressort de la ficelle (1) par rapport au reteneur de ficelle (2) et à l’aiguille du noueur (3). Augmenter la tension au niveau de la lame du noueur (1). (cf. défaut n° 9 illustration BPXC0267) 10.1 Tension insuffisante au niveau de la lame du noueur. Extrémités du nœud trop courtes. Le nœud s’ouvre de temps en temps (le deuxième nœud généralement). 10 Le ressort tendeur de ficelle s’est tordu Remplacer la pointe (1) de la roue motrice du crochet du noueur (2). Aucun nœud existe, ni 9.5 Le crochet du noueur ne dans l’écheveau tourne pas. supérieur ni dans l’écheveau inférieur Dépannage 9 Cause possible Défaut N° 2 3 BPXC0270 1 2 1 BPXC0268 Défauts - causes - remèdes Forte usure des anneaux de Rupture fréquente de la guidage de la ficelle. vis de cisaillement sur la tige de traction des aiguilles Ceci entraîne l ’arrêt du cadre de suspension des aiguilles. 12 Cause possible Défaut N° Remplacez les anneaux de guidage de la ficelle (1) et la vis de cisaillement (2) sur la tige de traction des aiguilles. Dépannage 1 2 1 BPXC0276 BPXC0275 Défauts - causes - remèdes X - 13 Cause possible La commande ou le raccord vers la commande sont défectueux. Défaut La presse à grandes balles ne peut pas être commandée via le terminal. N° 13 TDévisser le câble du terminal de la douille (1) se trouvant à gauche dans le sens de déplacement au niveau de l'habillage en tôle à proximité du volant. Brancher le connecteur pour le mode d'urgence (2) dans le connecteur (1). Le mode d'urgence est activé après 10 secondes avec les réglages suivants : • ancienne longueur de consigne • mode automatique • dernière force de consigne réglée Dépannage X - 14 2 BPXC0304 BPXC0305 1 Défauts - causes - remèdes Défauts - causes - remèdes 10.4 Recherche des erreurs dans la lubrification centrale Défaut Elimination des défauts Blocage dans l’installation ou dans un palier raccordé. Trouver et éliminer la cause du blocage. Installations actionnées manuellement. Le levier ne peut pas être bougé, ou alors difficilement. PROCEDURE Dans un premier temps, vérifier que la pompe refoulante fonctionne et fournit du lubrifiant au répartiteur principal. Pour ceci, desserrer la sortie de la pompe et actionner la pompe. Si la pompe fonctionne correctement, raccorder à nouveau la sortie de la pompe. (Conclusion : la pompe est en bon état.) Laisser fonctionner la pompe jusqu’au prochain blocage et/ ou jusqu’à la prochaine augmentation de pression non autorisée. Laisser reposer la pression. Desserrer, les uns après les autres, les raccords à vis d’entrée au niveau des répartiteurs principaux ou secondaires dans les installations à étage unique. Le répartiteur au niveau duquel du lubrifiant s’échappe suite au desserrage sous pression du raccord à vis d’entrée permet d’identifier l’origine du défaut.. Resserrer les raccords à vis d’entrée. Desserrer les uns après les autres les raccords à vis de palier correspondants. Le palier bloqué est le palier au niveau duqel du lubrifiant s’échappe suite au desserrage sous pression des raccords à vis d’entrée. Eliminer le blocage au niveau du palier. Blocage dans le répartiteur Lorsque toutes les sorties du répartiteur principal et/ou des répartiteurs secondaires ont été desserrées, il n’y a plus d’écoulement de lubrifiant au niveau des sorties ; le répartiteur est bloqué. Remplacer le répartiteur bloqué. Si nécessaire, le répartiteur peut être nettoyé dans les conditions suivantes : Poste de travail propre. Eliminer tous les raccords à vis de branchement de tube. Retirer les vis de fermeture du piston avec un tournevis solide, si nécessaire, taper légèrement avec un marteau sur la vis pour la desserrer. Extraire les pistons à l’aide d’un poinçon souple (Ø inférieur à 6 mm, si possible en plastique). Très important : Les pistons ne devant pas être intervertis, il est nécessaire de noter, pour chaque piston, l’alésage correspondant. Laver soigneusement plusieurs fois le corps du répartiteur dans un produit nettoyant dissolvant les graisses et purger avec de l’air comprimé. Au niveau des extrémités des filetages des alésages de fermeture des pistons se trouvent des canaux obliques d’un diamètre de 1,5 mm devant être percé à l’aide d’un fil métallique ou d’une pointe. Laver encore plusieurs fois le répartiteur et le purger avec de l’air comprimé. De la graisse durcie peut se trouver dans les vis de fermeture du piston. Cette graisse doit être éliminée. Réassembler le répartiteur en remplaçant tous les disques de cuivre. Avant de visser les raccords à vis de sortie de tube, pomper plusieurs fois, à l’aide d’une pompe manuelle ou d’une installation similaire, de l’huile dans le répartiteur. La contre-pression dans le répartiteur ne doit pas être supérieure à 25 bars lors de cette opération. Une contre-pression supérieure à cette valeur signifie que le répartiteur n’est pas propre ou que l’alésage du piston est endommagé Si, malgré toutes les mesures prises, la pression de fonctionnement du répartiteur ne baisse pas en dessous de 25 bars, remplacer le répartiteur. X - 15 Défauts - causes - remèdes X - 16 Annexe A1 Schémas de câblage du système hydraulique A1.1 Hydraulique de travail partie I pour l’électronique des versions de médium et confort Raccord à l'hydraulique de tracteur : 1x EW ramasseur 2x DW béquille de support 1x EW essieu directeur ramasseur Raccord de tracteur 331 742 1x EW L12 919-603 Capuchon de protection : 920-901 921-153 276-337 2x 344-466 béquille de support Raccord de tracteur L12 921-211 2x DW Capuchon de protection : 918-501 essieu directeur Raccord de tracteur L12 Cylindre de blocage sur essieu directeur 1x EW Capuchon de protection : A- 1 Annexe A1.2 Hydraulique de travail partie II pour l’électronique de la version confort Raccord à l'hydraulique de tracteur : 1x EW / (DW) Avance / Pression 1x T / (DW) Recul / Réservoir 1x LS Circuit de commande de charge pour bloc électronique confort : barre de coupe, éjecteur de balles, rampe d'éjection à rouleaux S04 286-203 L12 B3 A3 2x 334-997 Z3 Y08 Y07 Barre de coupe L12 B2 A2 Z2 Y06 Y05 B1 S02 334-997 Rampe d'éjection à rouleaux S03 Y04 Y03 Z1 S01 Y01 Y02 P LS T 920-932 921-169 P T Autocollant de direction Power Beyond Tractor Sensing uniquement pour électronique de tracteur Load-Sensing raccord sur Power-Beyond A-2 Ejecteur de balles L12 A1 LS 282-203 P (A) (B) T Raccord sur A et B uniquement pour tracteur a) sans Load-Sensing b) sans recul libre T Annexe A1.3 Hydraulique de travail partie II pour l’électronique des versions de médium Raccord à l'hydraulique de tracteur : 2x DW Barre de coupe 2x DW Ejecteur de balles / Rampe d'éjection à rouleaux Rampe d'éjection à rouleaux et éjecteur de balles S01 (modèle 1) (Medium uniquement) 334-997 282-203 919-603 919-714 B B A A Autocollant pour la direction Raccord de tracteur P 1 1 0 0 T A B 2x DW 2 Capuchon de protection : 2 1 0 2 105 Rampe d'éjection à rouleaux 1 0 2 (modèle 2) (sans éjecteur de balles) S01 (Medium uniquement) 334-997 919-603 919-714 B B A A Autocollant pour la direction Raccord de tracteur P 1 1 0 0 T A B 2x DW Capuchon de protection : 2 2 1 0 2 105 Ejecteur de balles 1 0 2 (modèle 2) (sans rampe d'éjection à rouleaux) Raccord de tracteur 282-203 L12 A B 2x DW Capuchon de protection : Barre de coupe S04 (Medium uniquement) Raccord de tracteur L12 A B 2x DW Capuchon de protection : 920-890 2x 334-997 A- 3 Annexe A1.4 Système hydraulique de bord pour l’électronique de la version médium L12 302-647 P U 919-163 921-122 (in front of yoke) 2x 918-435 Plu.-Zyl. 80-250 (1270/90/130) 1x 918-435 Plu.-Zyl. 80-250 (890) 2x 918-492 Plu.-Zyl. 120-220 (1290HDP) 920-914 (neben DBV) 921-148 920-933 2x 918-436 Plu.-Zyl. 90-150 (890) 2x 918-481 Plu.-Zyl. 80-150 (1270) 2x 918-524 Plu.-Zyl. 100-150 (1290) 4x 918-524 Plu.-Zyl. 100-150 (12130) L12 919-129 (right rotation, 1270/1290/HDP/12130) 919-130 (left rotation, 890) 4x 918-510 Plu.-Zyl. 100-140 (1290HDP) n= 1000 U/min V= 2,2 ccm/U L12 L12 919-131 Tank contents 15 l (without filter) A1.5 Système hydraulique de bord pour l’électronique de la version confort L12 302-647 P 919-163 U 919-067 (near DBV) 2x 918-435 Plu.-Zyl. 80-250 (1270/90/130) 1x 918-435 Plu.-Zyl. 80-250 (890) 2x 918-492 Plu.-Zyl. 120-220 (1290HDP) 920-914 (near DBV) 921-148 2x 918-436 Plu.-Zyl. 90-150 (890) 2x 918-481 Plu.-Zyl. 80-150 (1270) 2x 918-524 Plu.-Zyl. 100-150 (1290) 920-933 4x 918-524 Plu.-Zyl. 100-150 (12130) 4x 918-510 Plu.-Zyl. 100-140 (1290HDP) L12 919-129 (right rotation, 1270/1290/HDP/12130) 919-130 (left rotation , 890) n= 1000 U/min V= 2,2 ccm/U L12 L12 919-131 Tank contents 15 l (without filter) A-4 0 Modification 1 25.06.2007 C 14.10.2004 B Steckerpin Bezeichnung geändert Control battery ground - ok revision Date Stecker 8-polig A esc Display + A Tastenanordnung, Aderfarben Control battery +12V -A3 display 25A last modification Albers 2 3 4 2 Buchse 5 8 25.09.2003 created Rickermann 3 Origin white brown green yellow A grey pink blue Stift 7 6 1 4 5 8 3 2 3 1: frei 2: frei 3: SS_5V 4: +12VFU TERMI 5: CAN 1-L 6: GND TERMI 7: CAN 1-H 8: frei 1 7 6 12.11.2007 -1F2 Tractor 2 15/30 -1X6Bb 4 4 15/30 Repl. for 31 1 -1X6Ba 31 6 5 6 7 Standard power supply 150100082 000 05 Repl. by 8 8 SS_5V (X1_9) 9 Plant Sh. of No. Sheet No. Location 9 1/6 1 GND (X1_29) +12V_EIN (X1_28) CAN 1-H (X1_5) GND TERMI (X1_15) CAN 1-L (X1_6) +12VFU TERMI (X1_14) Control Big Pack Medium 890/1270/1290... 7 Doc-No.: D24 white brown green yellow grey pink blue Drawbar 5 -1X5a 2 7 1 6 5 4 3 B A -1X5b 2 7 1 6 5 4 3 -1X6a -1X6b B A 0 /2.0 /2.0 /2.3 /2.1 /2.3 /2.0 /2.0 Annexe A2 Schémas de circuits électriques A2.1 Unité de commande médium A- 5 C B 0 Modification 30 16 31 17 1 32 34 25.06.2007 33 19 6 Date 35 21 Versorgung über FU6 (30A) +12V_EIN Schaltspannungseingang SS_5V X1_9 X1_28 X1_29 X1_26 Masse 12V Versorgung GND_L X1_8 Masse 12V Versorgung GND_L X1_15 Masse 12V Versorgung GND_L Digitalsensor 7 Digitalsensor 10 DIG_GND_10 Digitalsensor 6 DIG_GND_6 Digitalsensor 3 DIG_GND_3 Digitalsensor 2 DIG_GND_2 Digitalsensor 1 DIG_GND_1 DIG_GND_7 X1_11 X1_23 X1_25 X1_13 X1_21 X1_17 X1_19 2 37 Albers 22 23 38 10 last modification Digitalsensor 11 DIG_GND_11 SS_5V (X1_9) +12V_EIN (X1_28) GND (X1_29) +12VFU TERMI (X1_14) GND TERMI (X1_15) GND_L (X1_27) GND_L (X1_37) DIG_GND_1 (X1_11) DIG_GND_2 (X1_23) DIG_GND_3 (X1_25) DIG_GND_6 (X1_13) DIG_GND_7 (X1_21) DIG_GND_11 (X1_19) /1.9 /1.9 /1.9 /1.9 /1.9 /5.1 /5.3 /3.1 /3.7 /3.8 /3.3 /3.5 /3.4 Versorgung Analogsensoren 9 12.11.2007 36 8 X1 7 revision 20 /3.5 X1_14 X1_27 Masse 12V Versorgung GND_L Versorgung Digitalsensoren 18 /3.1 /3.3 5 Measuring B4 Calibration B5 Packer monitoring B6 Versorgung Masse 12V Versorgung GND +12VFU_TERMI +12V Versorgung TERMI X1_37 Masse 12V Versorgung GND_L 4 A Pin- Belegung MULTI_1/ANAHFRQ_3 geändert. 10.11.2003 KMC1 -A1 29 15 3 40 created 39 GND Analogsensoren GND_ANA GNDAnalogsensoren GND_ANA Analogspannung +8VANA Analogspannung +8VANA X1_31 X1_34 X1_32 X1_35 25 CAN 1 26 3 Origin 41 X1_6 CAN_1-L X1_5 CAN_1-H 27 /5.1 42 HBPWMSTR_1 X1_1 28 /6.6 /4.8 Repl. for X1_4 TERMI_2 X1_39 CAN_2-L X1_3 CAN_2-L X1_38 CAN_2-H X1_2 CAN_2-H 4 KMC2 -A2 X2_28 16 31 3 5 17 32 4 18 33 5 19 34 6 20 35 21 6 36 8 X2 7 22 37 9 23 38 10 24 X2_7 Digitalsensor 16 DIG_GND_16 X2_27 Digitalsensor 14 DIG_GND_14 X2_20 Digitalsensor 12 DIG_GND_12 X2_3 Digitalsensor 9 DIG_GND_9 Digitalsensor 8 DIG_GND_8 Digitalsensor 5 DIG_GND_5 Digitalsensor 4 DIG_GND_4 39 11 25 40 12 26 7 41 13 27 Analogspannung 0,1A +8VANA Analogspannung 0,1A +8VANA X2_36 X2_38 X2_34 X2_11 X2_13 +12V2FU_L (X2_28) GND (X2_14) GND (X2_15) GND_L (X2_29) GND_L (X2_17) DIG_GND_4 (X2_36) DIG_GND_5 (X2_38) DIG_GND_8 (X2_34) DIG_GND_14 (X2_27) DIG_GND_18 (X2_11) /1.9 /1.9 /5.7 /6.2 /6.1 /5.6 /5.8 /4.2 /4.1 /4.5 /4.4 /4.7 X2_31 X2_23 X2_40 X2_24 X2_41 +8V ANA (X2_40) GND_ANA(X2_41) 41 GNDAnalogsensoren GND_ANA 40 /5.5 /5.5 42 CAN 1 14 28 /5.8 X2_6 CAN_1-L X2_5 CAN_1-H -1X2.0 A job computer Repl. by 30 2 X2_9 Digitalsensor 17 DIG_GND_17 11 150100082 000 05 Versorgung über FU2 (25A) +12V2FU_L X2_15 Masse 12V Versorgung GND Digitalsensor 18 DIG_GND_18 27 Big Pack Medium 890/1270/1290... 15 X2_25 Versorgung 3A (Poly) X2_21 Masse 12V Versorgung GND_L X2_32 Masse 12V Versorgung GND_L Digitalsensor 19 DIG_GND_19 Versorgung Analogsensoren GND Analogsensoren GND_ANA 7 Doc-No.: D24 29 1 X2_14 Masse 12V Versorgung GND +12V3FU_L X2_29 Masse 12V Versorgung GND_L X2_17 Masse 12V Versorgung GND_L Versorgung Digitalsensoren Digitalsensor 21 DIG_GND_21 36 38 34 /4.5 17 /4.2 /4.1 Cutterbar up B2 /4.4 29 Bale chute B11 Needle connecting rod B9 Twine monitoring B8 +KB_1X2-1X2b 28 25 14 15 DIGFRQ_14 X2_26 /4.7 /6.1 /5.4 Knotter release M1 6 DIG_16 X2_4 HBPWMSTR_3 5 DIGHFRQ_4 X2_35 DIG_17 X2_8 Central lubrication B3 DIG_21 X2_30 HBPWMSTR_4 X2_42 4 DIGHFRQ_5 DIGFRQ_9 X2_2 DIG_18 X2_10 Squeeze-flap pressure B17 MULTI_1 X2_39 PWMLA_4 X2_18 X2_1 CAN 1-H (X1_5) CAN 1-L (X1_6) CAN 2 14 HBPWMSTR_2 Central lubrication Y31 X1_42 13 Force sensors simulation PWMLA_1 X1_40 6 pressure control valve Y11 PWMLA_8 X1_7 /5.3 Versorgung EINGÄNGE DIGFRQ_8 X2_33 X2_37 DIGFRQ_12 X2_19 DIG_19 X2_12 Star wheel B15 ANAHFRQ_3 X2_22 AUSGÄNGE PWMLA_10 X2_16 3 Knotter cleaning Y30 LA_1 X1_36 5 AUSGÄNGE 12 25.09.2003 24 11 Rickermann DIGHFRQ_1 X1_10 2 DIGHFRQ_6 X1_12 1 DIGFRQ_7 /3.4 /3.7 /3.8 19 DIGFRQ_10 X1_16 X1_20 Packer feed B7 Knotter monitoring B10 Flywheel brake B1 11 23 25 13 21 DIGFRQ_11 X1_18 27 37 DIG_2 X1_22 /6.5 +KB_1X1-1X1b 9 28 29 14 15 DIG_3 X1_24 Plunger force left B18 /6.3 2 ANAHFRQ_1 X1_30 Plunger force right B19 /4.8 1 ANAHFRQ_2 X1_33 GND pressure control valve Y11 0 EINGÄNGE G_STROM_1 X1_41 A-6 8 8 Sh. of No. Sheet No. Plant Location +12V3FU_L (X2_25) Klemme1 +12V3FU_L (X2_25) Klemme2 +12V3FU_L (X2_25) Klemme3 9 9 2/6 2 /6.2 /6.1 /5.5 Annexe /2.2 C 1 25.06.2007 Measuring B4 Date Modification I/O 2 DIGHFRQ_6 X1_12 created Rickermann 25.09.2003 Calibration B5 KMC1 last modification Albers 25.06.2007 Modul DIGHFRQ_1 KMC1 Anschl. X1_10 revision Modul I/O Anschl. -A1 +KB_1X1-1X1b 12 +KB_1X1-1X1b 10 -A1 2 +KB_1X1-XB5a 2 2 +KB_1X1-XB4a 2 +KB_1X1-B5 Calibration 1 +KB_1X1-B4 Measuring +KB_1X1-XB5a 1 1 2 +KB_1X1-XB4a 1 B 0 1 /2.2 DIG_GND_6 (X1_13) 3 Origin /2.2 3 4 /2.2 2 Modul I/O Anschl. -A1 Repl. for 4 Packer feed B7 KMC1 DIGFRQ_11 X1_18 +KB_1X1-1X1b 18 +KB_1X1-XB7a 2 +KB_1X1-B7 Packer feed 1 +KB_1X1-XB7a 1 DIG_GND_11 (X1_19) I/O DIG_2 KMC1 Knotter monitoring B10 Modul X1_22 /2.2 Repl. by 5 6 7 2 1 8 Modul I/O Anschl. -A1 Sh. of No. Sheet No. Location Plant Flywheel brake B1 KMC1 DIG_3 X1_24 +KB_1X1-1X1b 24 +KB_1X1-XB1a 2 +KB_1X1-B1 Flywheel brake Big Pack Medium 890/1270/1290... /2.2 Anschl. -A1 +KB_1X1-1X1b 22 8 +KB_1X1-XB1a 1 Input sensors Packer monitoring B6 KMC1 DIGFRQ_7 X1_20 2 +KB_1X1-XB10a 2 +KB_1X1-B10 Knotter monitoring 1 +KB_1X1-XB10a 1 7 150100082 000 05 Modul I/O Anschl. -A1 +KB_1X1-1X1b 20 6 Doc-No.: D24 /2.2 2 +KB_1X1-XB6a 2 +KB_1X1-B6 Packer monitoring 1 +KB_1X1-XB6a 1 5 /2.2 DIG_GND_7 (X1_21) /2.1 DIG_GND_2 (X1_23) /2.1 DIG_GND_3 (X1_25) /2.1 DIG_GND_1 (X1_11) A 0 /2.2 9 9 3/6 3 Annexe A- 7 /2.6 1 C Modification 1 Date revision 25.06.2007 B 2 last modification Albers /2.6 created Rickermann 25.09.2003 Bale chute B11 KMC2 DIGHFRQ_4 12.11.2007 Modul A Needle connecting rod B9 KMC2 I/O I/O Modul Anschl. X2_37 DIGHFRQ_5 Anschl. X2_35 +KB_1X2-1X2b 35 +KB_1X2-1X2b 37 -A2 +KB_1X2-XB11a 2 +KB_1X2-XB9a 2 -A2 2 2 +KB_1X2-B11 Bale chute +KB_1X2-XB11a 1 2 1 1 +KB_1X2-XB9a 1 +KB_1X2-B9 Needle connecting rod 0 /2.5 DIG_GND_5 (X2_38) /2.5 DIG_GND_4 (X2_36) 3 Origin Modul I/O Anschl. -A2 4 Repl. for 4 Twine monitoring B8 KMC2 DIGFRQ_14 X2_26 +KB_1X2-1X2b 26 +KB_1X2-XB8a 2 2 1 +KB_1X2-XB8a 1 +KB_1X2-B8 Twine monitoring 3 /2.6 DIG_GND_14 (X2_27) /2.6 2 X2_33 X2_10 Central lubrication B3 KMC2 DIG_18 /2.6 Repl. by 5 6 7 PWMLA_8 X1_7 KMC1 2 1 X1_41 G_STROM_1 KMC1 /2.2 /2.2 8 Sh. of No. Sheet No. Location Plant GND pressure control valve Y11 Modul I/O Anschl. -A1 +KB_1X1-1X1b 41 0-100% +KB_1X1-XY11b 2 +KB_1X1-Y11 pressure control valve +KB_1X1-XY11b 1 +KB_1X1-1X1b 7 Input sensors Modul I/O Anschl. -A2 +KB_1X2-1X2b 10 I/O Anschl. -A1 8 pressure control valve Y11 Modul 150100082 000 05 /2.6 -XB3b 2 +KB_1X2-XB3a 2 7 Big Pack Medium 890/1270/1290... Cutterbar up B2 KMC2 DIGFRQ_8 1 +KB_1X2-XB3a 1 +KB_1X2-B3 central lubrication 4 +KB_1X2-XB3a 4 -XB3b 1 +KB_1X2-XB3a 1 6 /2.6 Doc-No.: D24 Modul I/O Anschl. -A2 +KB_1X2-1X2b 33 +KB_1X2-XB2a 2 +KB_1X2-B2 Cutterbar up 1 +KB_1X2-XB2a 1 5 /2.6 DIG_GND_8 (X2_34) A-8 DIG_GND_18 (X2_11) 0 9 9 4/6 4 Annexe KMC1 HBPWMSTR_2 X1_42 -A1 -XY31a 2 -XY31b 2 +KB_1X1-XY31b 2 2 C Zusätzliches Ventil Knoter 0 12.11.2007 B Sternrad B15 hinzugefügt. Modification 10.11.2003 25.06.2007 A Motor Knoterauslösung hinzugefügt. revision Date 2 /2.2 3 created Rickermann 25.09.2003 3 Origin -XY30b 2 2 1 -XY30b 1 -Y30.2 Knotter cleaning last modification Albers 12.11.2007 +KB_1X1-XY30b 2 2 1 +KB_1X1-Y30.1 Knotter cleaning LA_1 X1_36 KMC1 Knotter cleaning Y30 +KB_1X1-1X1b 36 1 +KB_1X1-Y31 central lubrication I/O Modul Anschl. +KB_1X1-XY30b 1 1 /2.2 +KB_1X1-XY31b 1 -XY31b 1 -XY31a 1 +KB_1X1-1X1b 42 -A1 I/O Modul Anschl. 2 /2.7 /2.7 -1X2.3a 1 3 2 Repl. for 4 Modul I/O Anschl. 3 -XM1 -XM1a 2 -XM1b 2 -XM1 -M1 Motor Knotter release M +KB_1X2-XB15b 6 85 86 -XM1a 3 Repl. by 5 6 7 Big Pack Medium 890/1270/1290... 8 86 85 -XM1b 3 30 30 87 87 outputs A +KB_1X2-XKM7 -KM7 Relay Knotter release 87a -XM1a 4 -XM1b 4 -XS1 12 Sh. of No. Sheet No. Location Plant 12 11 -XS1 11 /2.6 -S1 limit switch PWMLA_4 X2_18 KMC2 +KB_1X2-1X2b 18 -A2 8 Knotter release M1 150100082 000 05 /2.6 I/O Modul Anschl. +KB_1X2-XKM7b -XM1a 1 -XM1b 1 7 Doc-No.: D24 B Star wheel B15 KMC2 ANAHFRQ_3 X2_22 +KB_1X2-1X2b 22 -1X2.3b 2 -1X2.3a 2 +KB_1X2-XB15b 2 1 5 Option elektr. Knotter release -1X2.3b 1 3 4 +KB_1X2-B15 Star wheel -A2 /2.9 +8V ANA (X2_40) GND_ANA(X2_41) +12V3FU_L (X2_25) Klemme1 +KB_1X2-XB15b 1 3 4 /2.5 GND_L (X2_29) /2.4 +12V2FU_L (X2_28) 1 87a Central lubrication Y31 GND_L (X1_27) /2.1 GND_L (X1_37) /2.1 GND_L (X2_17) /2.5 0 9 23 9 5/6 5 24 Annexe A- 9 /2.5 /2.9 +12V3FU_L (X2_25) Klemme2 GND (X2_15) P 3 U 2 B B /2.6 C 0 B Aderfarben ergänzt Modification 1 25.06.2007 A Pin- Belegung MULTI_1/ANAHFRQ_3 geändert 10.11.2003 A Squeeze-flap pressure B17 KMC2 I/O Modul X2_39 MULTI_1 Anschl. -A2 +KB_1X2-1X2b 39 blue +KB_1X2-XB17b 3 +KB_1X2-B17 Bale channel flap pressure 1 +KB_1X2-XB17b 1 2 brownwhite Date revision -1X2.1b 2 -1X2.1a 2 2 2 last modification Albers 12.11.2007 1 1 25.09.2003 created Rickermann 3 Origin X1_33 KMC1 ANAHFRQ_2 4 4 /2.2 Repl. for Plunger force right B19 Modul I/O Anschl. -A1 +KB_1X1-1X1b 33 3 Modul I/O X1_30 KMC1 ANAHFRQ_1 X1_40 PWMLA_1 KMC1 B 3 4 4 3 brown white blue black -B18 Left force sensor R 1 2 F 3 4 1 2 rechts Repl. by 5 6 7 force measurement F brown white blue black grey -B19 Right force sensor /2.2 2 Poti Poti 150100082 000 05 Force sensors simulation Modul I/O Anschl. 1 F T315mA -XN1b 1 2 3 4 5 Amplifier -N1 7 Big Pack Medium 890/1270/1290... /2.2 -A1 +KB_1X1-1X1b 40 6 0V +12V Sign re Doc-No.: D24 Plunger force left B18 Anschl. -A1 +KB_1X1-1X1b 30 5 Sign li 1 GND (X2_14) +Sign 0V +12V -Sign Schalter 8 R 8 DIP /2.5 4 3 2 1 ON +12V3FU_L (X2_25) Klemme3 /2.9 links 2 3 Sh. of No. 4 +Sign Sheet No. Location Plant brown white blue black 1 0V +12V -Sign DIP 1 2 3 4 ON A - 10 1 2 3 4 0 9 9 6/6 6 Annexe 0 Modification 1 25.06.2007 C 14.10.2004 B 5 Date D E 7 6 1 revision C Stift 8 B Steckerpin Beschreibung geändert 1x6B 2 3 4 A Aderfarben ergänzt Control battery ground A Control 0 battery +12V -A4 display 25A 8 7 Albers 12.11.2007 -F1 F 6 4 2 5 3 1 2 last modification esc Tractor 3 4 2 Buchse 5 8 Stecker 8-polig created Rickermann 14.08.2003 3 Origin 1: frei 2: frei 3: SS_5V 4: +12VFU TERMI 5: CAN 1-L 6: GND TERMI 7: CAN 1-H 8: frei 1 7 6 3 15/30 Repl. for 15/30 white brown green yellow A grey pink blue -1X6Bb 2 31 1 -1X6Ba 31 4 4 white brown green yellow grey pink blue 5 150100081 000 05 Doc-No.: D24 Repl. by 6 Drawbar 5 -1X5a 2 7 1 6 5 4 3 B A -1X5b 2 7 1 6 5 4 3 7 6 Standard power supply 7 8 8 SS_5V (X1_9) 9 Plant Sh. of No. Sheet No. Location 9 1/10 1 GND (X1_29) +12V_EIN (X1_28) CAN 1-H (X1_5) GND TERMI (X1_15) CAN 1-L (X1_6) +12VFU TERMI (X1_14) Control Big Pack Comfort 890/1270/1290... -1X6a -1X6b B A 0 /2.0 /2.0 /2.3 /2.1 /2.3 /2.0 /2.0 Annexe A2.2 Unité de commande confort A- 11 C B 0 30 16 Modification 15 2 31 3 17 X1_28 Versorgung über FU6 (30A) +12V_EIN X1_9 Schaltspannungseingang SS_5V X1_29 32 1 X1_26 Masse 12V Versorgung GND_L X1_8 Masse 12V Versorgung GND_L X1_15 Masse 12V Versorgung GND_L 18 33 19 /4.0 X1_14 X1_27 Masse 12V Versorgung GND_L SS_5V (X1_9) +12V_EIN (X1_28) GND (X1_29) +12VFU TERMI (X1_14) GND TERMI (X1_15) GND_L (X1_26) GND_L (X1_27) GND_L (X1_37) /1.9 /1.9 /1.9 /1.9 /1.9 /7.2 /7.3 /7.5 Versorgung Digitalsensoren 5 Measuring B4 34 6 /4.2 Versorgung Masse 12V Versorgung GND +12VFU_TERMI +12V Versorgung TERMI X1_37 Masse 12V Versorgung GND_L 4 A Pin- Belegung MULTI_1/ANAHFRQ_3 geändert. 10.11.2003 KMC1 -A1 29 1 Date 35 21 revision 20 Digitalsensor 6 DIG_GND_6 Digitalsensor 3 DIG_GND_3 Digitalsensor 2 DIG_GND_2 Digitalsensor 1 DIG_GND_1 DIG_GND_7 X1_11 X1_23 X1_25 X1_13 X1_21 X1_17 X1_19 2 37 Albers 22 23 38 10 last modification Digitalsensor 7 Digitalsensor 10 DIG_GND_10 DIG_GND_1 (X1_11) DIG_GND_2 (X1_23) DIG_GND_3 (X1_25) DIG_GND_6 (X1_13) DIG_GND_7 (X1_21) DIG_GND_10 (X1_17) DIG_GND_11 (X1_19) /4.0 /4.7 /4.9 /4.2 /4.6 /4.3 /4.5 Versorgung Analogsensoren 9 12.11.2007 36 8 X1 7 DIGHFRQ_1 X1_10 Calibration B5 /4.6 Digitalsensor 11 DIG_GND_11 11 23 25 13 21 17 19 DIGHFRQ_6 X1_12 Packer monitoring B6 /4.3 /4.9 26 27 37 DIGFRQ_7 X1_20 Pick-up B20 /4.5 /4.7 Flywheel brake B1 /10.5 created 40 14.08.2003 39 GND Analogsensoren GND_ANA GNDAnalogsensoren GND_ANA Analogspannung +8VANA Analogspannung +8VANA X1_31 X1_34 X1_32 X1_35 25 CAN 1 26 3 Origin 41 42 /7.2 HBPWMSTR_1 Machine lighting H1 X1_1 X1_6 CAN_1-L X1_5 CAN_1-H 27 /7.3 HBPWMSTR_2 Central lubrication Y31 X1_42 28 /10.6 /7.1 /7.5 Repl. for X1_39 CAN_2-L X1_3 CAN_2-L X1_38 CAN_2-H X1_2 CAN_2-H 4 KMC2 -A2 X2_28 16 31 3 5 17 X2_15 Masse 12V Versorgung GND 4 32 X2_21 Masse 12V Versorgung GND_L 18 33 5 19 34 6 20 35 21 6 36 8 X2 7 22 9 37 X2_3 Digitalsensor 9 DIG_GND_9 Digitalsensor 8 DIG_GND_8 Digitalsensor 5 DIG_GND_5 Digitalsensor 4 DIG_GND_4 X2_36 X2_38 X2_34 23 38 10 24 11 13 31 39 11 25 40 12 26 7 41 13 27 Analogspannung 0,1A +8VANA Analogspannung 0,1A +8VANA X2_23 X2_40 X2_24 X2_41 +12V2FU_L (X2_28) GND (X2_14) GND (X2_15) GND (X2_29) GND (X2_32) GND (X2_17) DIG_GND_4 (X2_36) DIG_GND_5 (X2_38) DIG_GND_8 (X2_34) DIG_GND_9 (X2_3) DIG_GND_12 (X2_20) DIG_GND_14 (X2_27) DIG_GND_16 (X2_7) DIG_GND_17 (X2_9) DIG_GND_18 (X2_11) DIG_GND_19 (X2_13) DIG_GND_21 (X2_31) +8V_ANA (X2_40) GND_ANA (X2_41) 41 GNDAnalogsensoren GND_ANA 40 /1.9 /1.9 /8.7 /10.2 /10.1 /8.7 /8.1 /8.8 /5.3 /5.2 /5.7 /5.6 /6.4 /5.5 /6.1 /6.2 /5.1 /5.9 /6.5 /8.5 /8.5 42 CAN 1 14 28 /8.8 X2_6 CAN_1-L X2_5 CAN_1-H -1X2.0 A job computer 30 2 Repl. by Versorgung über FU2 (25A) +12V2FU_L X2_29 Masse 12V Versorgung GND_L X2_20 Digitalsensor 12 DIG_GND_12 X2_11 9 150100081 000 05 X2_25 Versorgung 3A (Poly) X2_32 Masse 12V Versorgung GND_L X2_27 Digitalsensor 14 DIG_GND_14 Digitalsensor 18 DIG_GND_18 X2_13 X2_31 20 27 7 Big Pack Comfort 890/1270/1290... 15 X2_14 Masse 12V Versorgung GND +12V3FU_L X2_17 Masse 12V Versorgung GND_L Versorgung Digitalsensoren X2_7 Digitalsensor 16 DIG_GND_16 Digitalsensor 19 DIG_GND_19 Versorgung Analogsensoren GND Analogsensoren GND_ANA 7 Doc-No.: D24 29 1 /5.3 X2_9 Digitalsensor 17 DIG_GND_17 Digitalsensor 21 DIG_GND_21 36 38 34 3 Bale chute B11 /5.2 /6.5 29 32 17 DIGHFRQ_4 X2_35 Needle connecting rod B9 /5.7 /5.6 /6.4 /5.5 /6.1 /6.2 /5.9 Push button Bale chute down S6 /8.5 +KB_1X2-1X2b 28 25 14 15 DIGHFRQ_5 X2_37 Cutterbar up B2 Bale set-down B12 Push button Bale chute up S5 Twine monitoring B8 Push button bale-ejector in S3 Push button bale-ejector out S4 /5.1 Bale ejector B14 /10.1 6 DIGFRQ_8 X2_33 DIG_16 X2_4 HBPWMSTR_3 X2_42 Knotter release M1 5 DIGFRQ_9 X2_2 DIG_17 X2_8 Central lubrication B3 DIG_21 X2_30 HBPWMSTR_4 4 DIGFRQ_12 X2_19 DIG_18 X2_10 Squeeze-flap pressure B17 MULTI_1 X2_39 PWMLA_4 X2_18 X2_1 CAN 1-H (X1_5) CAN 1-L (X1_6) CAN 2 14 Force sensors simulation PWMLA_1 X1_40 13 X1_7 6 pressure control valve Y11 PWMLA_8 X1_4 TERMI_2 Versorgung EINGÄNGE DIGFRQ_14 X2_26 DIG_19 X2_12 Star wheel B15 ANAHFRQ_3 X2_22 AUSGÄNGE PWMLA_10 X2_16 3 Knotter cleaning Y30 LA_1 X1_36 5 AUSGÄNGE 12 Rickermann 24 11 /7.1 +KB_1X1-1X1b 9 28 29 14 15 DIGFRQ_10 X1_16 Packer feed B7 Knotter monitoring B10 Plunger force left B18 /10.3 2 DIGFRQ_11 ANAHFRQ_1 X1_30 Plunger force right B19 GND pressure control valve Y11 1 DIG_2 X1_18 ANAHFRQ_2 X1_33 0 EINGÄNGE DIG_3 X1_24 X1_22 G_STROM_1 X1_41 A - 12 8 8 Sh. of No. Sheet No. Plant Location +12V3FU_L (X2_25) Klemme1 +12V3FU_L (X2_25) Klemme2 +12V3FU_L (X2_25) Klemme3 +12V3FU_L (X2_25) Klemme4 9 9 2/10 2 /8.5 /10.2 /10.1 /8.0 Annexe A- 13 0 B C Date revision A 0 Modification KMC3 -A3 29 1 15 30 2 16 1 31 17 32 4 18 33 19 34 /6.6 20 Versorgung X3_18 Masse 12V Versorgung X3_5 Masse 12V Versorgung GND_L X3_13 Masse 12V Versorgung GND_L X3_11 Masse 12V Versorgung GND_L X3_9 Masse 12V Versorgung GND_L X3_29 Masse 12V Versorgung X3_15 Masse 12V Versorgung X3_1 Masse 12V Versorgung GND GND GND X3_28 Versorgung über FU2 (25A) +12V2FU_L X3_42 Versorgung über FU1(25A) +12V1FU_L Versorgung +12V1FU_L GND_L Masse 12V Versorgung GND_L 2 8 36 Albers 21 Masse 12V Versorgung GND_L Masse 12V Versorgung GND_L Masse 12V Versorgung created 14.08.2003 /8.2 39 Digitalsensor 20 DIG_GND_20 Digitalsensor 13 DIG_GND_13 X3_14 X3_22 X3_7 X3_35 X3_41 X3_20 GND_L (X3_9) GND_L (X3_11) GND_L (X3_13) GND_L (X3_5) GND_L (X3_18) GND_L (X3_22) GND_L (X3_7) GND_L (X3_35) GND_L (X3_37) DIG_GND_13 (X3_41) DIG_GND_20 (X3_20) /7.8 /7.9 /7.6 /9.1 /9.7 /9.8 /9.2 /9.4 /9.5 /6.6 /6.8 Versorgung Analogsensoren +8VANA 25 Analogspannung +8VANA Analogspannung 3 GND_ANA 26 GNDAnalogsensoren 41 GND_ANA 13 Origin 40 12 GND Analogsensoren X3_24 X3_27 X3_16 X3_25 CAN 2 27 42 14 CAN_2-H 28 Multibale release 1 Y14 PWMLA_2 X3_2 /9.1 /7.8 /7.9 /8.3 11 Cutterbar Y07 PWMLA_3 X3_4 24 master control valve Y01 PWMLA_5 X3_8 /7.6 10 X3_10 38 Rickermann 23 master control valve Y02 PWMLA_6 9 37 Multibale release 2 Y15 PWMLA_7 X3_21 41 20 Squeeze-flap release valve Y09 PWMLA_9 X3_12 /9.7 /9.2 3 Bale chute Y03 PWMLA_11 X3_30 /9.8 X3_37 Versorgung Digitalsensoren 22 12.11.2007 35 7 last modification /8.0 /8.3 X3 Push button cutterbar up S1 DIGFRQ_13 X3_40 /6.8 6 Push button cutterbar down S2 DIG_20 X3_19 5 Multibale B21 MULTI_2 X3_23 /8.2 GND_L 3 MULTI_3 X3_26 Bale chute Y04 PWMLA_12 +KB_1X3-1X3b 9 11 13 5 18 22 7 35 37 GND Multibale release 1 Y14 STROM_2 X3_3 X3_6 X3_32 Repl. for Bale ejector Y06 2 GND Multibale release 2 Y15 STROM_3 X3_31 Cutterbar Y08 LA_2 X3_34 1 EINGÄNGE STROM_4 X3_33 AUSGÄNGE Bale ejector Y05 LA_3 LA_4 X3_36 X3_38 X3_39 CAN_2-L TERMI_2 /9.4 X3_17 /9.5 4 4 Repl. by 5 150100081 000 05 Doc-No.: D24 5 6 7 7 Big Pack Comfort 890/1270/1290... job computer 6 8 8 Sh. of No. Plant Location Sheet No. 9 9 3/10 3 Annexe /2.1 C 0 Modification 1 Date revision /2.2 2 last modification Schrameyer 15.10.2004 Calibration B5 KMC1 B Modul 2 DIGHFRQ_6 A Measuring B4 KMC1 I/O I/O Modul Anschl. X1_10 DIGHFRQ_1 Anschl. X1_12 +KB_1X1-1X1b 12 +KB_1X1-1X1b 10 -A1 +KB_1X1-XB5a 2 +KB_1X1-XB4a 2 -A1 2 2 +KB_1X1-B5 Calibration 1 +KB_1X1-B4 Measuring +KB_1X1-XB5a 1 1 /2.2 1 +KB_1X1-XB4a 1 DIG_GND_1 (X1_11) /2.2 DIG_GND_6 (X1_13) 2 created Rickermann 15.08.2003 Modul I/O Anschl. -A1 3 Origin Pick-up B20 KMC1 DIGFRQ_10 X1_16 +KB_1X1-1X1b 16 +KB_1X1-XB20a 2 +KB_1X1-B20 Pick-up 1 +KB_1X1-XB20a 1 3 /2.2 DIG_GND_10 (X1_17) /2.2 2 Repl. for 4 Modul I/O Anschl. -A1 KMC1 DIG_2 X1_22 Knotter monitoring B10 Modul I/O Anschl. -A1 +KB_1X1-1X1b 22 /2.2 Repl. by 5 6 7 /2.1 8 Modul I/O Anschl. -A1 Sh. of No. Sheet No. Location Plant Flywheel brake B1 KMC1 DIG_3 X1_24 +KB_1X1-1X1b 24 +KB_1X1-XB1a 2 2 1 +KB_1X1-XB1a 1 8 +KB_1X1-B1 Flywheel brake Input sensors /2.2 2 +KB_1X1-XB10a 2 +KB_1X1-B10 Knotter monitoring 1 +KB_1X1-XB10a 1 7 150100081 000 05 Packer monitoring B6 KMC1 DIGFRQ_7 X1_20 6 Big Pack Comfort 890/1270/1290... Modul I/O Anschl. -A1 +KB_1X1-1X1b 20 +KB_1X1-XB6a 2 2 1 +KB_1X1-XB6a 1 +KB_1X1-B6 Packer monitoring /2.2 5 Doc-No.: D24 Packer feed B7 KMC1 DIGFRQ_11 X1_18 +KB_1X1-1X1b 18 +KB_1X1-XB7a 2 +KB_1X1-B7 Packer feed 1 +KB_1X1-XB7a 1 4 /2.2 DIG_GND_11 (X1_19) /2.2 DIG_GND_7 (X1_21) /2.1 DIG_GND_2 (X1_23) A - 14 DIG_GND_3 (X1_25) 0 9 9 4/10 4 /2.2 Annexe /2.6 C 0 1 Date 2 last modification Albers 12.11.2007 Needle connecting rod B9 revision Modification DIGHFRQ_5 X2_37 KMC2 B Central lubrication B3 Modul I/O /2.6 DIG_18 KMC2 Anschl. X2_10 -A2 A Modul I/O Anschl. -A2 +KB_1X2-1X2b 10 +KB_1X2-XB3a 2 2 +KB_1X2-1X2b 37 +KB_1X2-XB9a 2 +KB_1X2-XB3a 1 -XB3b 2 2 1 +KB_1X2-B9 Needle connecting rod 1 +KB_1X2-B3 central lubrication +KB_1X2-XB9a 1 4 1 +KB_1X2-XB3a 4 -XB3b 1 +KB_1X2-XB3a 1 DIG_GND_18 (X2_11) /2.5 DIG_GND_5 (X2_38) 15.08.2003 created DIGHFRQ_4 3 X2_35 Bale chute B11 KMC2 Origin Modul I/O Anschl. -A2 +KB_1X2-1X2b 35 Rickermann /2.6 2 +KB_1X2-XB11a 2 +KB_1X2-B11 Bale chute 1 +KB_1X2-XB11a 1 3 /2.5 DIG_GND_4 (X2_36) Repl. for /2.6 4 Modul I/O Anschl. -A2 5 /2.6 Repl. by 5 6 Bale set-down B12 KMC2 DIGFRQ_9 X2_2 /2.6 2 Modul I/O Anschl. -A2 Cutterbar up B2 KMC2 DIGFRQ_8 X2_33 +KB_1X2-1X2b 33 +KB_1X2-XB2a 2 +KB_1X2-B2 Cutterbar up 1 +KB_1X2-XB2a 1 7 /2.6 6 Input sensors 7 Big Pack Comfort 890/1270/1290... Modul I/O Anschl. -A2 +KB_1X2-1X2b 2 +KB_1X2-XB12a 2 2 1 +KB_1X2-XB12a 1 +KB_1X2-B12 Bale set-down 150100081 000 05 Doc-No.: D24 Twine monitoring B8 KMC2 DIGFRQ_14 X2_26 +KB_1X2-1X2b 26 +KB_1X2-XB8a 2 2 1 +KB_1X2-XB8a 1 +KB_1X2-B8 Twine monitoring 4 /2.6 DIG_GND_14 (X2_27) /2.6 DIG_GND_9 (X2_3) /2.6 DIG_GND_8 (X2_34) 8 8 /2.6 2 1 Modul I/O Anschl. -A2 Sh. of No. Sheet No. Location Plant Bale ejector B14 KMC2 DIG_19 X2_12 +KB_1X2-1X2b 12 +KB_1X2-XB14a 2 Bale ejector +KB_1X2-B14 +KB_1X2-XB14a 1 DIG_GND_19 (X2_13) 0 9 9 5/10 5 /2.6 Annexe A- 15 Modification 1 Date C X2_8 KMC2 DIG_17 3 /2.6 2 last modification Schrameyer 15.10.2004 created Rickermann 15.08.2003 Push button bale-ejector out S4 Modul revision Push button bale-ejector in S3 KMC2 I/O I/O Modul Anschl. X2_4 DIG_16 Anschl. -A2 +KB_1X2-1X2b 8 +KB_1X2-1X2b 4 -A2 2 +KB_1X2-XS4b 2 2 green green +KB_1X2-XS3b 2 +KB_1X2-S4 Bale ejector out 1 +KB_1X2-S3 Bale ejector in +KB_1X2-XS4b 1 1 /2.6 2 +KB_1X2-XS3b 1 3 1 B 0 /2.6 DIG_GND_16 (X2_7) /2.6 DIG_GND_17 (X2_9) 2 3 Origin X2_19 KMC2 DIGFRQ_12 3 /2.6 4 Repl. for 4 Push button Bale chute up S5 Modul I/O Anschl. -A2 +KB_1X2-1X2b 19 +KB_1X2-XS5b 2 yellow +KB_1X2-S5 Bale chute up 1 +KB_1X2-XS5b 1 3 /2.6 DIG_GND_12 (X2_20) /2.6 2 X2_30 KMC2 DIG_21 5 3 /2.6 2 X3_40 KMC3 DIGFRQ_13 3 2 X3_19 DIG_20 KMC3 3 5 6 7 Input push button Repl. by 8 /3.2 8 Push button cutterbar down S2 Modul I/O Anschl. -A3 +KB_1X3-1X3b 19 +KB_1X3-XS2b 2 yellow +KB_1X3-S2 Cutterbar down 1 +KB_1X3-XS2b 1 150100081 000 05 /3.2 7 Big Pack Comfort 890/1270/1290... Push button cutterbar up S1 Modul I/O Anschl. -A3 +KB_1X3-1X3b 40 +KB_1X3-XS1b 2 yellow +KB_1X3-S1 Cutterbar up 1 +KB_1X3-XS1b 1 6 Doc-No.: D24 Push button Bale chute down S6 Modul I/O Anschl. -A2 +KB_1X2-1X2b 30 +KB_1X2-XS6b 2 yellow +KB_1X2-S6 Bale chute down 1 +KB_1X2-XS6b 1 DIG_GND_21 (X2_31) /3.2 DIG_GND_13 (X3_41) /3.2 DIG_GND_20 (X3_20) A - 16 A 0 Plant Sh. of No. Sheet No. Location 9 9 6/10 6 Annexe KMC1 HBPWMSTR_1 X1_1 Modul I/O 2 X1_41 G_STROM_1 KMC1 0 1 12.11.2007 Modification 15.12.2005 revision Date A /2.2 2 last modification Albers 12.11.2007 <2005 B Zusätzliches Knoterreinigungsventil C 2 1 +KB_1X1-XH1b 2 +KB_1X1-H1 Machine lighting A Machine lighting <2005 GND pressure control valve Y11 Modul I/O Anschl. -A1 +KB_1X1-1X1b 41 0-100% 2 +KB_1X1-XY11b +KB_1X1-Y11 pressure control valve 1 +KB_1X1-XH1b 1 -A1 Anschl. +KB_1X1-XY11b 1 /2.2 /2.2 +KB_1X1-1X1b 1 PWMLA_8 X1_7 KMC1 2 Machine lighting H1 +KB_1X1-1X1b 7 -A1 Anschl. I/O Modul pressure control valve Y11 1 GND_L (X1_26) /2.1 KMC1 HBPWMSTR_2 X1_42 I/O -A1 2 15.08.2003 created Rickermann 3 Origin -XY31a 2 -XY31b 2 +KB_1X1-XY31b 2 2 Repl. for 4 +KB_1X1-XY30.1b 2 +KB_1X1-Y30.1 Knotter cleaning 1 5 LA_1 X1_36 KMC1 Knotter cleaning Y30 /2.2 Repl. by 5 150100081 000 05 Doc-No.: D24 -XY30.2b 2 +KB_1X1-XY30.1b 1 -Y30.2 Knotter cleaning 2 -XY30.2b 1 +KB_1X1-1X1b 36 +KB_1X1-XY30.1b 1 +KB_1X1-Y31 central lubrication I/O Modul Anschl. 1 /2.2 4 +KB_1X1-XY31b 1 -XY31b 1 -XY31a 1 +KB_1X1-1X1b 42 -A1 Anschl. Modul Central lubrication Y31 3 GND_L (X1_27) /2.1 GND_L (X1_37) /2.1 I/O Modul I/O Modul +KB_1X3-XY09b 2 6 7 Big Pack Comfort 890/1270/1290... outputs 8 2 Sh. of No. Sheet No. Location Plant +KB_1X3-XY01b 2 +KB_1X3-Y02 2 master control valve (retract) +KB_1X3-XY01b 2 +KB_1X3-Y01 2 master control valve (extend) 1 +KB_1X3-Y09 Squeeze-flap release +KB_1X3-XY02b 1 9 PWMLA_6 X3_10 KMC3 1 -A3 Anschl. +KB_1X3-XY01b 1 /3.2 1 PWMLA_5 X3_8 KMC3 +KB_1X3-XY09b 1 -A3 Anschl. 9 7/10 7 master control valve Y02 +KB_1X3-1X3b 10 /3.2 master control valve Y01 8 +KB_1X3-1X3b 8 PWMLA_9 X3_12 KMC3 7 +KB_1X3-1X3b 12 -A3 Anschl. I/O Modul Squeeze-flap release valve Y09 6 GND_L (X3_13) /3.1 GND_L (X3_9) /3.1 GND_L (X3_11) /3.1 0 /3.2 Annexe A- 17 /2.5 /2.9 -1X3.1a 6 7 -1X3.1b 6 7 3 I/O 1 10.11.2003 C Stecker für Multibale-Option hinzugefügt Modification 10.11.2003 10.11.2003 Multibale B21 B zus. +12V gesch. für Sternrad 0 C revision Date I/O X3_3 STROM_2 KMC3 /3.2 2 last modification Albers 12.11.2007 created Rickermann 17.09.2003 GND Multibale release 1 Y14 Modul Anschl. /3.2 -1X3.1b 4 -1X3.1b 2 /3.2 /3.2 X3_31 STROM_3 KMC3 3 Origin Repl. for GND Multibale release 2 Y15 Modul I/O Anschl. -A3 +KB_1X3-1X3b 31 -1X3.1a 4 X3_23 KMC3 Multibale (2 twines) 2 +KB_1X3-XY15b 2 1 -1X3.1a 2 +KB_1X3-1X3b 3 -A3 +KB_1X3-XY15b +KB_1X3-Y15 Multibale release 2 Option Multibale Only at Big Pack 1270 A Pin_Belegung MULTI/ANAHFRQ_3 geändert Modul 1 MULTI_2 +KB_1X3-1X3b 23 -1X3.1b 5 -1X3.1a 5 +KB_1X3-XB21b 3 2 2 1 total (6 twines) 2 +KB_1X3-XY14b +KB_1X3-Y14 Multibale release 1 +KB_1X3-XY14b 1 -1X3.1a 3 -1X3.1a 1 1 -1X3.1b 3 -1X3.1b 1 -A3 PWMLA_7 X3_21 KMC3 4 5 2 2 X2_22 Repl. by 5 6 7 86 86 85 85 -XM1b 3 -XM1a 3 30 30 options /2.6 87 87 150100081 000 05 B +KB_1X2-XKM7 -KM7 Relay Knotter release 87a +KB_1X2-XKM7b -XM1a 4 -XM1b 4 8 -S1 12 Sh. of No. Sheet No. Location Plant -XS1 11 -XS1 11 /2.6 limit switch 12 PWMLA_4 X2_18 KMC2 Knotter release M1 8 +KB_1X2-1X2b 18 -A2 Anschl. I/O Modul Big Pack Comfort 890/1270/1290... A -XM1 -XM1a 1 -XM1b 1 7 Option elektr. Knotter release 3 Star wheel B15 KMC2 ANAHFRQ_3 1 -XM1 -XM1a 2 -XM1b 2 -M1 Motor Knotter release M 6 Doc-No.: D24 Modul I/O Anschl. -A2 +KB_1X2-1X2b 22 -1X2.3b 2 -1X2.3a 2 +KB_1X2-XB15b +KB_1X2-B15 Star wheel +KB_1X2-XB15b 1 3 -1X2.3a 1 3 +KB_1X3-XB21b 2 1 Anschl. I/O Anschl. +KB_1X3-1X3b 21 -A3 /3.2 +KB_1X3-1X3b 2 PWMLA_2 X3_2 Multibale release 2 Y15 Modul 4 /2.7 -1X2.3b 1 3 4 +KB_1X3-B21 Multibale -A3 I/O Anschl. KMC3 Multibale release 1 Y14 Modul 3 /2.7 -1X2.2a 1 2 +12V3FU_L (X2_25) Klemme1 GND (X2_32) /2.5 GND (X2_29) /2.4 +12V2FU_L (X2_28) 2 87a /2.9 +8V_ANA (X2_40) GND_ANA (X2_41) +12V3FU_L (X2_25) Klemme4 -1X2.2b 1 2 1 GND (X2_17) A - 18 /2.5 0 9 9 24 8/10 8 23 Annexe I/O Modul I/O Modul 2 +KB_1X3-XY07b 2 Date Modification 2 +KB_1X3-XY08b 2 +KB_1X3-Y08 Cutterbar 15.10.2004 2 last modification Schrameyer created Rickermann Origin 3 2 Repl. for +KB_1X3-XY05b 2 +KB_1X3-Y05 Bale ejector 2 +KB_1X3-XY06b 2 +KB_1X3-Y06 Bale ejector Repl. by 5 150100081 000 05 Doc-No.: D24 2 +KB_1X3-XY03b 2 +KB_1X3-Y03 Bale chute 6 7 Big Pack Comfort 890/1270/1290... outputs 2 +KB_1X3-XY04b 2 +KB_1X3-Y04 Bale chute 1 +KB_1X3-Y07 Cutterbar +KB_1X3-XY04b 1 1 PWMLA_12 X3_32 KMC3 +KB_1X3-XY03b 1 -A3 Anschl. 1 /3.2 +KB_1X3-XY06b 1 PWMLA_11 X3_30 KMC3 1 -A3 Anschl. +KB_1X3-XY05b 1 /3.2 1 -A3 LA_4 X3_36 KMC3 +KB_1X3-XY08b 1 4 I/O Modul Anschl. 1 /3.2 Bale chute Y04 8 +KB_1X3-XY07b 1 -A3 LA_3 X3_34 KMC3 Bale chute Y03 7 +KB_1X3-1X3b 32 1 I/O Modul Anschl. 6 +KB_1X3-1X3b 30 15.08.2003 /3.2 Bale ejector Y06 5 +KB_1X3-1X3b 36 LA_2 X3_6 KMC3 Bale ejector Y05 4 +KB_1X3-1X3 34 -A3 revision C I/O Modul Anschl. 3 +KB_1X3-1X3b 6 -A3 /3.2 Cutterbar Y08 2 +KB_1X3-1X3b 4 PWMLA_3 X3_4 KMC3 B 0 I/O Modul Anschl. Cutterbar Y07 1 GND_L (X3_7) /3.2 GND_L (X3_35) /3.2 GND_L (X3_37) /3.2 GND_L (X3_18) /3.2 8 GND_L (X3_22) /3.2 GND_L (X3_5) /3.1 A 0 Sh. of No. Sheet No. Location Plant /3.2 9 9 9/10 9 Annexe A- 19 /2.5 /2.9 +12V3FU_L (X2_25) Klemme2 GND (X2_15) 3 U 2 B B /2.6 C 0 B Aderfarben ergänzt Modification 1 14.10.2004 A Pin- Belegung MULTI_1/ANAHFRQ_3 geändert. 10.11.2003 A Squeeze-flap pressure B17 KMC2 I/O Modul X2_39 MULTI_1 Anschl. -A2 +KB_1X2-1X2b 39 blue +KB_1X2-XB17b 3 +KB_1X2-B17 Bale channel flap pressure P 1 +KB_1X2-XB17b 1 2 brown white Date revision -1X2.1b 2 -1X2.1a 2 2 2 last modification Albers 12.11.2007 1 1 15.08.2003 created Rickermann 3 Origin X1_33 KMC1 ANAHFRQ_2 4 4 /2.2 Repl. for Plunger force right B19 Modul I/O Anschl. -A1 +KB_1X1-1X1b 33 3 Modul I/O X1_30 KMC1 ANAHFRQ_1 X1_40 PWMLA_1 KMC1 B 3 4 4 3 brown white blue black -B18 Left force sensor R 1 2 F 3 4 1 2 rechts Repl. by 5 6 7 8 Schalter force measurement F brown white blue black grey -B19 Right force sensor /2.2 2 Poti Poti 150100081 000 05 Force sensors simulation Modul I/O Anschl. 1 F T315mA -XN1b 1 2 3 4 5 Amplifier -N1 7 Big Pack Comfort 890/1270/1290... /2.2 -A1 +KB_1X1-1X1b 40 6 0V +12V Sign re Doc-No.: D24 Plunger force left B18 Anschl. -A1 +KB_1X1-1X1b 30 5 Sign li 1 GND (X2_14) +Sign 0V +12V -Sign R 8 DIP /2.5 4 3 2 1 ON +12V3FU_L (X2_25) Klemme3 /2.9 links 2 3 Sh. of No. 4 +Sign Sheet No. Location Plant brown white blue black 1 0V +12V -Sign DIP 1 2 3 4 ON A - 20 1 2 3 4 0 9 9 10/10 10 Annexe Annexe A- 21 . . . konsequent, kompetent Maschinenfabrik Bernard Krone GmbH Phone +49 (0) 59 77/935-0 Fax +49 (0) 59 77/935-339 Internet: http://www.krone.de eMail: info.ldm@krone.de 23-Okt-2008 Heinrich-Krone-Straße 10, D-48480 Spelle Postfach 11 63, D-48478 Spelle ">
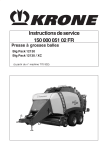
Public link updated
The public link to your chat has been updated.