2. Phénoplastes : Phénol-formaldéhyde. INRS Matières plastiques
Suivant le catalyseur employé et la proportion phénol/formol, la préparation de ces résines conduit à des produits thermoplastiques puis/ou thermodurcissables.
En présence de catalyseurs acides et d’un défaut de formol, on obtient des « novolaques » thermoplastiques. Par addition d’hexaméthylène tétramine, les novolaques deviennent thermodurcissables.
En présence de catalyseurs basiques et d’un excès de formol, on obtient des « résols » puis des « résitols » thermodurcissables.
Les résines formophénoliques sont livrées sous forme de matières à mouler (poudres ou granulés), de sirops, de résines liquides, de résines en solutions, de résines solides ou de composés en poudre.
La formule générale des novolaques, polymères linéaires peut s’écrire :
Les produits thermodurcissables qui en découlent et les résitols sont composés de chaînes ramifi ées formant un réseau tridimensionnel serré de structure pas obligatoirement régulière.
Sous forme liquide ou pâteuse, les produits sont utilisés avec des proportions variables de phénol ou de formol libres (plus de 5% dans les résols).
Différents adjuvants peuvent leur être ajoutés.
1. – Solvants.
Ce sont des alcools et des cétones utilisés pour les mises en solution des résines.
2. – Charges.
Elles sont incorporées dans les matières à mouler à des concentrations diverses (jusqu’à 50 %) et leur confèrent des propriétés particulières. Les phénoplastes chargés ont d’ailleurs une désignation spécifi que constituée de deux chiffres : le premier indique la nature de la charge (1 : minérale ;
2 : bois ; 3 : cellulose ; 4 : textile), le second indique sa forme (1 : poudre ou fl ocons ; 2 : éléments fragmentaires) [2], [20].
Les principales charges sont :
— farine de bois (résines P 21) ;
— charges minérales en poudre : graphite, ardoise, mica… (résine P 11) ;
— charges minérales fi breuses : verre, amiante (résine P 12) ;
— fi bres cellulosiques et synthétiques ;
— charges métalliques.
161
3. – Lubrifi ants.
Ils sont destinés à faciliter la mise en œuvre et le démoulage. Ce sont principalement :
— des dérivés oléiques et stéariques ;
— des cires et des paraffi nes.
4. – Colorants et pigments.
Pour les matières à mouler.
On utilise soit des colorants organiques solubles dans la résine, soit des pigments minéraux : sels de cadmium, de manganèse, de cobalt, oxydes de fer anhydres ou hydratés, oxydes de chrome anhydres…
La forte coloration initiale de la résine rend impossible l’obtention de teintes claires.
Pour les vernis.
On utilise des pigments organiques à raison de 0,5 à 1 % en présence d’une forte proportion d’oxyde de titane.
5. – Durcisseurs.
Dans les composés en poudre, les résines solides et les poudres à mouler, on ajoute de l’hexaméthylène tétramine et éventuellement de la chaux ou de la magnésie.
Dans les résines liquides ou les colles, on ajoute du para-toluène sulfochlorure, de l’acide chlorhydrique, de l’acide para-toluène sulfonique.
Dans les colles à base de résorcine, le durcisseur comporte en général une charge et du paraformaldéhyde.
II. – MISE EN ŒUVRE
1. – Moulage.
La matière sous forme de pastilles, est préchauffée notamment par haute fréquence.
a) Moulage par compression.
C’est le mode de moulage traditionnel des phénoplastes, encore très utilisé avec des presses automatiques à dosage volumétrique. Les températures sont de l’ordre de 155-175 °C.
Les durées de cuisson, c’est-à-dire le temps nécessaire à l’achèvement de la polymérisation jusqu’à l’état thermorigide, sont assez longues, suivant la
162
nature de la matière à mouler, et suivant l’utilisation ou non d’un préchauffage haute fréquence de la matière.
b) Moulage par transfert.
La matière est comprimée dans une chambre, puis, sous l’action d’un piston, fl uidifi ée et transférée dans les empreintes.
Cette technique de moulage permet des temps de cycles plus courts mais provoque une usure plus rapide des moules et une anisotropie des propriétés du produit. Les températures sont de l’ordre de 160-180 °C.
c) Moulage par injection sur presse à vis.
Les températures sont d’environ 160-180 °C.
Cette technique plus récente a encore permis de réduire les temps de cuisson et de réaliser des cycles entièrement automatiques.
2. – Coulée des résines formophénoliques.
Les « résols », résines liquides peu condensées, additionnées de charges et de catalyseurs, peuvent être coulées en moules, à chaud ou à froid.
La cuisson est effectuée sous pression atmosphérique entre 80 et
170 °C.
3. – Stratifi és et agglomérés.
Stratifi és.
Ils sont obtenus à partir de résines condensées avec un excès de formol et des catalyseurs appropriés par imprégnation de strates (feuilles de tissu, papier, bois, carton, etc.) que l’on presse ensuite à chaud à des températures de l’ordre de 100-180 °C.
Agglomérés.
On les fabrique à partir de résidus cellulosiques, de bois, ou de poudres spéciales : le marbre et la silice notamment. Après broyage et malaxage avec une résine en solution, le mélange est pressé à chaud.
4. – Revêtements et imprégnation.
On utilise les mêmes résines que pour la fabrication des stratifi és, mais aussi des résines formophénoliques modifi ées par des huiles, de la colophane, des caoutchoucs, etc., ainsi que des résines en solution aqueuse.
5. – Assemblage.
On emploie des colles à base de résines formol-phénol ou formolrésorcine en solution alcoolique ou aqueuse. À chaud, on peut également réaliser un joint entre deux pièces à partir de résine solide en poudre.
163
6. – Usinage et fi nitions.
On peut effectuer les opérations de découpage, sciage, perçage, poinçonnage, taraudage, tournage, fraisage, polissage sans diffi cultés particulières.
Parmi les nombreuses applications des résines formophénoliques, on peut encore citer leur emploi dans la fabrication de :
— mousses ;
— abrasifs appliqués et meules ;
— moules et noyaux de fonderie (températures atteignant 300 °C) ;
— têtes de lingotières ;
— garnitures de freins et d’embrayage ;
— colles, peintures et vernis ;
— encres d’imprimerie.
III. – RISQUES*
1. – Résines et adjuvants.
Les résines formophénoliques durcies sont diffi cilement infl ammables
[8], [22].
Toutefois, les résines à l’état très divisé et les poudres peuvent exploser ou s’enfl ammer spontanément. Pour éviter ce risque, on opère avec des broyeurs lents en réduisant la teneur en oxygène de l’atmosphère en dessous de la limite explosive, avec un gaz inerte, pendant la préparation des poudres et en opérant les transformations en milieu humide.
a) Les résines formophénoliques utilisées à l’état partiellement condensées ou condensées peuvent entraîner des irritations primaires et des sensibilisations observées notamment lors de leur mise en œuvre ; celles-ci s’expliquent par la nature chimique des matières de départ [3], [35], [130] :
— Formaldéhyde.
C’est un irritant de la peau, des yeux et du système respiratoire. À forte concentration, il peut provoquer des nausées et des vertiges. Il est également responsable d’eczémas allergiques [133].
— Phénols.
Ils sont corrosifs et exercent également sur la peau une action sensibilisante, moins forte cependant que celle produite par le formaldéhyde.
Une certaine quantité de ces composants subsiste à l’état libre dans la résine ; leur action peut se manifester de diverses manières :
également le tableau en fi n de volume.
164
- Exposition aux vapeurs :
En particulier lors du moulage, aux températures mises en œuvre, il y a dégagement de phénol et de formol. Les troubles sont cutanés, digestifs et respiratoires [131].
- Exposition cutanée aux colles, vernis, apprêts :
Toutes ces préparations contiennent en solution des phénoplastes monomères. Leur manipulation peut entraîner l’apparition de dermatoses.
En outre, un risque supplémentaire est dû aux solvants, particulièrement l’alcool méthylique qui est toxique par inhalation.
- Exposition à la poussière de phénoplaste :
Toutes les opérations d’usinage des pièces (fraisage, sciage, taraudage…) dégagent de la poussière dangereuse pour les voies pulmonaires
[132] et risquent de provoquer des éruptions cutanées par un mécanisme d’irritation primaire et de sensibilisation.
Ces opérations comportent aussi un risque de projection dans les yeux lors de l’ébarbage notamment.
b) Les adjuvants ajoutés à divers stades de la préparation présentent des risques au moment de leur incorporation et lors de l’usinage, risques qui s’ajoutent, dans ce cas, à l’action des poussières citées ci-dessus.
— Charges :
Les fi bres d’amiante sont responsables, d’une part, de l’asbestose, d’autre part de cancers bronchiques et de mésothéliomes. Les fi bres de verre sont irritantes pour la peau et les voies respiratoires.
— Durcisseurs :
L’hexaméthylène tétramine peut provoquer des irritations de la peau et des réactions allergiques spécifi ques [3].
L’acide chlorhydrique est corrosif ; ses vapeurs sont très irritantes pour les muqueuses oculaires et respiratoires.
L’acide p-toluène sulfonique est irritant pour la peau et les yeux [27].
— Colorants et pigments :
Les sels de cadmium sont nocifs par inhalation et contact cutané. Ils peuvent provoquer des troubles intestinaux, rénaux et nerveux.
Les sels de cobalt sont sensibilisants [123].
L’anhydride chromique peut provoquer des ulcérations de la peau et des muqueuses.
Les oxydes de fer peuvent entraîner par inhalation une fi brose pulmonaire, la sidérose.
2. – Dégradation thermique. a) Aux températures de mise en œuvre (jusqu’à 300 °C environ).
Au cours de la mise en œuvre, notamment lors du moulage et de la fabrication des noyaux et des moules en fonderie [37], [46], il y a des
165
dégagements importants de vapeurs de phénol et de formol comme il a été dit au paragraphe précédent. D’autre part, l’hexaméthylène tétramine, si elle est présente, se décompose en libérant du formol et de l’ammoniac, toxiques et irritants.
b) Aux températures supérieures à 300 °C , en cas de pyrolyse ou de combustion et en fonderie lors de la coulée notamment [39], [47], les produits de décomposition sont les suivants [6], [30], [33] :
— oxyde de carbone toxique ;
— anhydride carbonique ;
— hydrocarbures aliphatiques (méthane…) ;
— phénol.
Il peut y avoir également formation de produits toxiques :
— ammoniac, acide cyanhydrique, nitriles dans le cas de résines durcies à l’hexaméthylène tétramine ;
— anhydride sulfureux si l’acide p-toluène sulfonique ou des produits soufrés sont utilisés.
166
AMINOPLASTES
URÉE-FORMALDÉHYDE OU URÉE-FORMOL Abréviation normalisée : UF
Noms commerciaux
AMINOCEL KAURIT SCARAB
AMINOLAC UF MÉLOCOL UF SIRIT
BEETLE UF
CASCO-RÉSINE
PLASTOPAL
POLLOPAS S
SKANOPAL
SYNRÉSINE UF
CIBAMINE UF
CIBANOIDE
PRYSTALINE
RÉSICART UF
HYGROMULL RÉSUFIN
URALITE UF
URAMEX UF
UROPLAS
I. – CARACTÉRISTIQUES
Les résines d’urée-formol résultent de la polycondensation de l’urée avec le formaldéhyde. Leur motif de base se développe sur trois dimensions.
Elles peuvent être livrées soit sous forme de sirops peu polycondensés
(milieux aqueux ou solvant) pour le moulage ou le collage, soit sous forme de poudres ou granulés contenant généralement divers adjuvants.
1.
–
Plastifi ants.
On emploie la glycérine et l’eau, à raison de 0,5 à 5 % du poids de la résine.
2. – Charges.
La meilleure est l’alpha cellulose. On emploie également :
— des charges d’origine végétale : farine de bois, pâte de bois ;
167
— des charges synthétiques : fi bres de polyamides ;
— des charges minérales : silice, mica, amiante, graphite, noir de carbone ;
— des charges métalliques : oxydes et poudres de métaux.
3. – Pigments et colorants.
La coloration est obtenue sur de la poudre de résine, ou bien dans l’émulsion aqueuse, par incorporation de :
— pigments minéraux : sels de cadmium, manganèse, cobalt, oxydes de fer hydratés et anhydres, oxydes de chrome anhydres ;
— colorants organiques.
4. – Lubrifi ants.
Les plus employés sont l’eau et les glycols.
5. – Émulsifi ants.
Ils sont à base d’acide phosphorique et de phénol.
6. – Solvants.
Ce sont généralement l’eau ou les alcools.
7. – Durcisseurs et catalyseurs de moulage.
On utilise habituellement des acides (acide phosphorique, acide chlorhydrique à 10 % dans l’alcool éthylique) ou des sels, notamment le chlorure d’ammonium.
Ils permettent l’achèvement de la polycondensation tridimensionnelle au cours du moulage, pour conduire à l’objet fi nal en matière thermodurcie.
II. – MISE EN ŒUVRE
La transformation des résines urée-formol s’effectue soit à partir de poudres ou granulés généralement chargés, plastifi és et colorés, soit à partir de résines en solution.
Les techniques les plus utilisées sont :
1. – Moulage.
— Par compression.
La poudre est la plus souvent pastillée au préalable et préchauffée à
100 °C.
168
On opère à des températures comprises entre 130 et 170°C sous pression.
— Par injection .
De très fortes pressions sont mises en jeu.
— Par extrusion.
Pour la fabrication de joncs, tubes et profi lés.
— Par coulée.
Les résines utilisées sont préparées en sirops avec 10 % d’eau.
Après addition d’un durcisseur (généralement acide), on cuit pour achever la polycondensation.
La coulée peut se faire, soit dans les moules (objets en forme), soit sur un tablier mobile chauffant (obtention de fi lms à partir de la résine plastifi ée).
2. – Fabrication des stratifi és et des agglomérés.
— Stratifi és.
À partir d’une résine peu polycondensée (sirop de résine catalysée au moment de l’emploi par un acide ou un sel, chlorure d’ammonium par exemple) on enduit le support (papier, bois, fi bres de verre, tissus, etc.). On peut également utiliser une dissolution de résine solide dans un solvant.
Après enduction, on presse à température convenable.
— Agglomérés.
Ils sont préparés de façon identique à partir de déchets industriels divers : copeaux de bois, de liège…
3. – Enduction et imprégnation.
Les enduits sont soit des sirops épais, soit des émulsions aqueuses de résine, mélangée à des charges et colorants. En général, ils durcissent à froid.
4. – Vernis.
Pour obtenir des vernis plus souples et plus résistants, on utilise des résines urée-formol modifi ées, solubles dans les solvants habituels des vernis
(alcool, esters, hydrocarbures benzéniques).
Ces vernis peuvent durcir au four vers 120-180 °C ou simplement à l’air en présence d’un catalyseur de durcissement.
169
5. – Colles.
Les colles à base d’urée-formol peuvent être utilisées à chaud et à froid.
Il suffi t d’ajouter le catalyseur acide ou sel d’ammonium juste avant l’emploi.
6. – Usinage.
Découpage, perçage, tournage, etc.
Parmi les nombreuses applications de ces résines, on peut citer leur emploi dans la fabrication de mousses isolantes, de moules et noyaux de fonderie, d’apprêts pour l’industrie textile…
III. – RISQUES
*
1. – Résines et adjuvants.
La résine pure d’urée-formol est ininfl ammable.
Toutefois, l’incorporation de certains adjuvants (charges et solvants) peut favoriser son infl ammation, mais dans ce cas, la combustion est lente et s’arrête d’elle-même [24].
a) Les résines d’urée-formol peuvent entraîner des réactions d’irritation et de sensibilisation [35]. En effet, elles peuvent contenir jusqu’à 10 % de formol et d’urée non condensés.
— L’urée est considérée comme relativement peu nocive. Toutefois, l’urée technique du commerce préparée par synthèse peut provoquer dans certains cas, des irritations dermiques, du fait de la réaction fortement alcaline du produit.
— Le formaldéhyde est un irritant et un sensibilisant [133]. Il est également nocif pour les yeux et le système respiratoire. C’est le grand responsable des dermatoses remarquées chez le personnel manipulant ces résines
[3].
L’action nocive du formaldéhyde peut se manifester, soit par contact cutané, soit par inhalation des vapeurs dégagées.
b) La toxicité éventuelle des adjuvants doit également être prise en considération.
— Durcisseurs.
L’acide phosphorique exerce, sur la peau, une forte action corrosive et il est particulièrement dangereux pour les yeux.
L’acide chlorhydrique est également un produit corrosif.
également le tableau en fi n de volume.
170
— Charges.
Elles peuvent présenter un danger au moment de leur incorporation dans les mélanges ou lors de travaux de fi nition.
La silice, sous sa forme cristallisée, peut provoquer la silicose ; par contre la silice amorphe qui constitue la majeure partie des silices ultrafi nes ne présente pas les mêmes risques.
Les fi bres d’amiante sont responsables, d’une part de l’asbestose, d’autre part de cancers bronchiques et de mésothéliomes.
— Pigments et colorants.
Certains pigments minéraux présentent des risques au moment de leur incorporation :
• les sels de cadmium sont nocifs par inhalation et contact cutané. Ils peuvent provoquer des troubles intestinaux, rénaux et nerveux ;
• les sels de cobalt sont sensibilisants [123] ;
• l’anhydride chromique peut provoquer des ulcérations de la peau et des muqueuses ;
• les oxydes de fer peuvent entraîner par inhalation une fi brose pulmonaire, la sidérose.
— Solvants.
Ce sont surtout des alcools qui interviennent dans la préparation des colles, vernis et enduits.
Parmi eux, l’alcool méthylique, est toxique en particulier par inhalation.
Les hydrocarbures benzéniques (toluène, xylènes) sont nocifs par inhalation (action ébrio-narcotique) et irritants pour la peau et les muqueuses.
2. – Dégradation thermique. a) Aux températures de mise en œuvre (jusqu’à 200 °C environ).
On note essentiellement un dégagement de vapeurs de formol notamment dans les opérations de moulage et en particulier lors du dégazage des moules. Ces vapeurs sont irritantes et sensibilisantes comme il a été dit au paragraphe précédent.
Il peut y avoir également formation d’ammoniac.
b) Lors de la pyrolyse, en fonderie lors des coulées notamment [47] ou en cas
d’incendie, les résines urée-formol se décomposent en libérant les produits suivants :
— oxyde de carbone toxique ;
— anhydride carbonique ;
— ammoniac, gaz toxique et irritant pour les muqueuses oculaires et respiratoires ;
— acide cyanhydrique très toxique par inhalation et nitriles aux vapeurs le plus souvent toxiques ;
— hydrocarbures aliphatiques légers (méthane…).
171
AMINOPLASTES
MÉLANINE-FORMALDÉHYDE ou MÉLANINE-FORMOL
Abréviation normalisée : MF
Noms commerciaux
AMINOLAC MELMEX RÉSART
BEETLE MF MÉLOCHEM RÉSICART MF
CIBAMINE FM MÉLOCOL MF RESMELIN
ERVAMINE MÉLOLAM RUTAFORM
LAMÉLITE MEL-RON SUPRAPLAST
MÉLASESTO
MÉLIT
MELWIT E URALITE MF
I. – CARACTÉRISTIQUES
Les résines de mélamine-formol résultent de la polycondensation incomplète de la mélamine et du formaldéhyde. Leur motif de base : se développe de façon irrégulière et complexe sur trois dimensions. Elles sont livrées sous forme de résines à couler, de poudres ou granulés à mouler, ou de sirops (généralement dans l’eau ou les alcools), en fonction des usages auxquels elles sont destinées.
Leurs principaux adjuvants sont :
1.
–
Plastifi ants.
Phtalates et phosphates, huiles de ricin, glycérine.
172
2. – Charges.
Il est encore plus facile de charger les résines de mélamine-formol que celles d’urée-formol, car elles sont compatibles avec un plus grand nombre de produits cellulosiques et minéraux.
Les principales charges utilisées sont l’alpha-cellulose, la poudre d’amiante fi nement broyée, la farine de bois, les fl ocons de bois et la silice.
3. – Colorants et pigments.
Ce sont les mêmes que pour les résines d’urée-formol, c’est-à-dire :
— des colorants organiques ;
— des pigments minéraux (sels de cadmium, de manganèse, de cobalt, oxydes de fer hydratés ou anhydres, oxydes de chrome anhydres).
4. – Catalyseurs de durcissement.
Les plus utilisés sont des acides (acide chlorhydrique par exemple) ou des sels (chlorure d’ammonium entre autres).
Ils permettent l’achèvement de la polycondensation tridimensionnelle au cours du moulage qui conduit à l’objet fi nal en matière thermodurcie.
Dans le cas particulier des vernis à base de copolymères d’allylemélamine (et en particulier des leurs esters) on emploie des catalyseurs peroxydes avec un accélérateur au cobalt.
5. – Solvants.
Les résines mélanine-formol sont rendues solubles dans les solvants organiques par éthérifi cation avec des alcools.
Les principaux solvants utilisés pour la préparation de colles et vernis sont les alcools, les cétones et les hydrocarbures benzéniques.
II. – MISE EN ŒUVRE
Les différentes techniques de transformation sont les suivantes :
1. – Moulage.
Comme pour les résines urée-formol, il est fortement recommandé de préchauffer les poudres à mouler de mélamine-formol dans une étuve à air chaud 80-100 °C par chauffe infrarouge ou par haute fréquence puis de pastiller ou de préformer.
— Par compression.
Température 145-165 °C.
173
La durée du moulage et les températures dépendent de l’épaisseur de la pièce à mouler. Pour des pièces minces, on moule à des températures
élevées pendant un temps très court, tandis que pour les pièces épaisses, on préfère travailler à température moins élevée, mais plus longtemps.
— Par transfert.
Le moulage par transfert est une opération délicate, qui repose essentiellement sur une bonne conception du moule. Les températures sont de l’ordre de 120-160 °C.
2. – Stratifi és.
Les stratifi és mélamine-formol ont pris une expansion ces dernières années.
Les différents supports (papier, coton, tissu de verre, amiante) sont imprégnés d’une solution ou d’une dispersion de résines en présence d’un catalyseur de durcissement, puis comprimés à chaud dans une presse. Les températures sont de l’ordre de 120-160 °C.
3. – Usinage.
Les pièces moulées sont caractérisées par un bel aspect de surface.
Elles peuvent être usinées par découpage, poinçonnage, sciage, perçage, fraisage, etc.
Le polissage peut se faire par voies mécanique ou chimique, à l’aide de solvants.
4. – Vernis.
On fabrique généralement les vernis à partir de résines mélamine-formol modifi ées, pour en améliorer la qualité. Ces vernis sont fréquemment livrés dans le commerce en solution dans l’alcool butylique. Le séchage peut se faire à l’air en présence d’un catalyseur acide, mais le plus souvent il se fait dans un four.
Des copolymères d’allyle-mélamine ont été récemment mis au point pour la préparation de vernis en particulier des esters d’allyle-mélamine.
Ils durcissent entre 0 et 80 °C, sous l’action d’un catalyseur peroxyde et
éventuellement d’un accélérateur.
III. – RISQUES*
1. – Résines et adjuvants. diffi cilement [24].
également le tableau en fi n de volume.
174
Les résines incomplètement polycondensées contiennent des teneurs importantes de monomères libres qui agissent par contact cutané ou inhalation des vapeurs :
— la mélamine est considérée comme relativement peu nocive [3] ;
— le formol est un irritant et un sensibilisant [133], il agit sur la peau, les yeux et les voies respiratoires. Il est responsable des symptômes observés chez le personnel manipulant les résines, tels que maux de tête, accidents pulmonaires, dermatoses.
b) Les risques dus aux adjuvants qui se manifestent surtout au moment de leur incorporation peuvent aussi intervenir au cours de la transformation ou lors des travaux de fi nition.
— Plastifi ants.
La plupart des phosphates organiques sont des substances nocives et irritantes pour les yeux, la peau et les voies respiratoires. L’orthotricrésylphosphate est toxique et peut être à l’origine de polynévrites. Toutefois, il intervient le plus souvent à une concentration inférieure à 1 % dans le phosphate de tricrésyle industriel.
Les phtalates sont légèrement irritants pour les muqueuses.
— Charges.
La silice, sous sa forme cristallisée, peut provoquer la silicose ; par contre la silice amorphe qui constitue la majeure partie des silices ultrafi nes ne présente pas les mêmes risques.
L’amiante est responsable, d’une part de l’asbestose, d’autre part de cancers bronchiques et de mésothéliomes.
— Catalyseurs.
L’acide chlorhydrique est un produit corrosif.
Les peroxydes utilisés dans les vernis à base d’esters d’allyle-mélamine sont irritants pour la peau et particulièrement dangereux pour les yeux. De plus, ils sont instables et peuvent donner lieu à des décompositions explosives. Il est impératif de respecter certaines règles de sécurité relative à leur stockage et leur manipulation. Se reporter au chapitre III.5. des Généralités.
— Pigments.
Les sels de cadmium sont nocifs par inhalation et contact cutané. Ils peuvent provoquer des troubles intestinaux, rénaux et nerveux.
Les sels de cobalt sont sensibilisants.
L’anhydride chromique peut provoquer des ulcérations de la peau et des muqueuses.
Les oxydes de fer peuvent entraîner par inhalation une fi brose pulmonaire, la sidérose.
175
— Solvants.
Parmi les alcools, l’alcool méthylique est toxique en particulier par inhalation, l’alcool butylique est nocif.
Les hydrocarbures benzéniques sont nocifs par inhalation et irritants pour la peau et les muqueuses.
2. – Dégradation thermique. a) Aux températures de mise en œuvre (jusqu’à 180 °C environ).
Il y a principalement un dégagement de vapeurs de formol, produit irritant et sensibilisant (comme il a été dit au paragraphe précédent).
b) Aux températures supérieures lors de la pyrolyse ou de la combustion les principaux gaz dégagés sont [30], [33] :
— l’oxyde de carbone, toxique ;
— l’anhydride carbonique ;
— l’acide cyanhydrique, très toxique par inhalation ;
— l’ammoniac, toxique et irritant pour les muqueuses oculaires et respiratoires ;
— des hydrocarbures aliphatiques.
176
RÉSINES ALKYDES MODIFIÉES AUX HUILES
OLÉOGLYCÉROPHTALIQUES
Noms commerciaux
ALCREA CARGIL SICALYD
ALKYDAL GLYPTAL SYNRÉSATE
ALKYNOL NAXOL URADIL
BECKACITE RÉSIAL URATHIX
BECKOSOL ROUTALKYD
I. – CARACTÉRISTIQUES polycondensation d’un polyacide ou d’un anhydride d’acide (anhydride phtalique, acides terpéniques, colophane) et d’un polyalcool (glycol, glycérol), en présence d’un agent modifi cateur, généralement un acide gras, ou une huile végétale siccative ou non.
Les glycérophtaliques sont plus précisément les alkydes obtenus à partir d’anhydride phtalique et de glycérol. On peut les représenter par la formule suivante :
L’utilisation principale des résines alkydes concerne les opérations de fi nition des objets manufacturés : traitements de surface par peintures, vernis et émaux au four. Elles sont aussi utilisées dans les encres d’imprimerie.
On classe habituellement les résines alkydes en longueur d’huile [36].
Ce sont :
— les alkydes « longues » séchant à l’air et contenant entre 70 et 80 % d’huile par rapport à la résine. Les solvants habituellement utilisés sont des essences et des hydrocarbures aliphatiques ;
— les alkydes « moyennes » séchant à l’air et au four contenant entre 40 et
60 % d’huile par rapport à la résine. Les solvants les plus employés sont le
177
solvant naphta, le white-spirit, les mélanges d’hydrocarbures benzéniques et alcools ;
— les alkydes « courtes » séchant au four et contenant moins de 40 % d’huile par rapport à la résine. Les solvants spécifi ques sont les hydrocarbures benzéniques et les alcools. On utilise aussi des solvants polaires, en particulier l’acétate d’éthylglycol et l’acétate de l’éther éthylique du diéthylène glycol.
La notation industrielle de ces résines repose sur la juxtaposition de deux nombres dont le premier représente le pourcentage de résine alkyde pure et le second la proportion d’huile. En pratique, on peut mentionner plus simplement la longueur d’huile (ex : alkyde 60/40 ou alkyde à 40 % d’huile).
Les résines glycérophtaliques les plus utilisées en peinture sont celles comprises dans l’intervalle 30/70 et 70/30.
Il existe maintenant des alkydes sans huile, qui sont des polyesters saturés que l’on peut rendre thermodurcissables par combinaison avec des aminoplastes, des polyuréthannes ou des composés époxydes. Dans cette classe, on trouve des produits pour peintures en poudre à appliquer au pistolet électrostatique et des agglomérants pour sables de fonderie (résine alkyde durcie notamment à l’aide de diisocyanate de diphénylméthane). Les résines alkydes se présentent le plus souvent en solution dans les solvants cités plus haut. Elles ne contiennent pas de plastifi ants. On leur ajoute des pigments et des charges dans le cas des peintures satinées ou mates.
Les résines pour peintures brillantes ne contiennent évidemment pas de charges.
1. – Les pigments.
Ils sont dispersés dans le liant par exemple par passage sur des broyeurs rapides à billes de verre ou de stéatite. On emploie des pigments organiques ou des pigments minéraux (dioxyde de titane, sels et oxydes de chrome, de cadmium, de cobalt, de fer, de molybdène, de manganèse, etc.).
2.
–
Les charges.
Ce sont des carbonates de calcium (craie, marbre), de la dolomie, du talc, etc.
II. – MISE EN ŒUVRE
Les résines alkydes sont livrées soit en solutions prêtes à l’emploi, soit en émulsions.
L’application des peintures et vernis peut se faire :
— par pulvérisation au pistolet ;
— à la brosse ou au rouleau ;
— au trempé (immersion de l’objet à peindre dans des bacs de peinture) ;
— par électrodéposition : l’objet à peindre, relié à un pôle électrique, est plongé dans une cuve de peinture en solution dans l’eau et qui contient une électrode de polarité inverse.
178
Le séchage s’effectue à température variable, suivant le produit utilisé, à partir de la température ambiante jusqu’à environ 200 °C environ.
III. – RISQUES*
1. – Résines et adjuvants.
Certaines résines alkydes sont légèrement allergisantes, l’anhydride phtalique pouvant être l’agent sensibilisant [35].
Mais les risques, lors de leur emploi, tiennent essentiellement à l’utilisation de solvants [42].
On peut classer ces risques en deux catégories distinctes :
— risques d’intoxication par inhalation des vapeurs et par contact cutané ;
— risques d’incendie et d’explosion.
Ils sont élevés en particulier lorsque l’application des produits s’effectue au pistolet et le séchage à l’air libre.
Les solvants les plus dangereux sont les hydrocarbures benzéniques
(action ébrio-narcotique notamment).
essentiellement à la présence d’hydrocarbures benzéniques et d’hexane, composé à l’origine de polynévrites.
L’acétate d’éthylglycol est nocif par inhalation et contact cutané.
Parmi les pigments, l’anhydride chromique est corrosif, les sels de chrome et de cobalt sont sensibilisants pour la peau, les sels de cadmium peuvent provoquer des troubles intestinaux, rénaux et nerveux.
Pour les mesures de prévention, se reporter notamment à la brochure citée en référence [42].
2. – Dégradation thermique.
Il existe peu d’information à ce sujet. Les seules données actuellement en notre possession portent sur la dégradation à haute température (800-
900 °C) de résines alkydes durcies avec le diisocyanate de diphénylméthane et utilisées en fonderie [37], [39]. Les principaux produits de décomposition sont :
— l’oxyde de carbone toxique ;
— l’anhydride carbonique ;
— des hydrocarbures benzéniques nocifs par inhalation ;
— des aldéhydes (notamment l’acroléine) irritants pour les voies respiratoires.
également le tableau en fi n de volume.
179
POLYÉPOXYDES OU RÉSINES ÉPOXYDIQUES
Abréviation normalisée : EP
Noms commerciaux
ARALDITE EUREPOX
BECKOPOX LEKUTHERM
DOW D.E.H.
DOW D.E.N.
LEVEPOX
LOPOX
DOW D.E.R. POLYDROX
ECCOMOLD RUTAPOX
EPIKOTE (EPON) SCOTCHCAST
ÉPIPHEN SCOTCHKOTE
ÉPOCAST SCOTCHWELD
ÉPONAL SILIROLITE
ÉPONOL (ÉPIKOTE OL) STYCAST
(phénoxydes) URANOX
ÉPOSIR VEREPOX
I. – CARACTÉRISTIQUES
Les résines époxydiques résultent généralement de la polycondensation de l’épichlorhydrine avec un polyalcool ou un phénol. Lorsque ce dernier est le bisphénol A ou diphénylolpropane, leur formule peut s’écrire :
Il existe également des résines époxydiques à base de novolaques et des résines époxydiques aliphatiques ou cycloaliphatiques suivant leur poids moléculaire, ces résines ont l’aspect de liquides épais ou de solides jaunâtres. Celles qui ont un poids moléculaire inférieur à 1 000 sont en général des liquides plus ou moins visqueux, ou des semi solides. Elles sont livrées
180
sous des formes très variées : résines à couler, poudres à mouler, résines d’imprégnation et de revêtement, stratifi és, colles.
Ce sont des résines thermodurcissables de degré de polycondensation peu élevé, qu’il est nécessaire, sauf exception, d’associer à un durcisseur pour atteindre le stade thermorigide fi nal, par formation de ponts entre les chaînes linéaires.
Durcisseurs.
Le choix du durcisseur est fonction de l’application envisagée et des caractéristiques souhaitées pour le produit fi ni. Les durcisseurs peuvent agir entre 15 et 200 °C, suivant leur nature chimique. On les classe habituellement en deux groupes.
— Durcisseurs acides.
À raison de 30 à 150 % du poids de la résine. Ce sont généralement des anhydrides d’acides (anhydrides méthyltétrahydrophtalique, endométhylène tétrahydrophtalique, phtalique, hexahydrophtalique, chlorendique, pyromellitique…).
— Durcisseurs basiques.
À raison de 5 à 100 % du poids de la résine.
Ce sont habituellement :
• des amines aromatiques (agissant généralement à chaud) : diaminodiphénylméthane, phénylène diamine… ;
• des amines aliphatiques ou cycloaliphatiques (agissant généralement
à température ambiante) triéthylène tétramine, éthylène diamine, triéthanolamine, isophorone diamine, méthylène diamine… ;
• des polyaminoamides ;
• des adducts de polyamines aliphatiques (mélanges de résines ayant partiellement réagi et contenant un excès d’amines).
— Le durcissement peut également être obtenu sous l’action de résines synthétiques telles que phénoplastes et aminoplastes. Dans ce cas, il se développe une réaction d’addition conduisant à la résine thermorigide.
— Certaines résines époxydiques modifi ées, en particulier celles utilisées dans les applications électriques, sont des résines durcies sous l’action de polyanhydrides en présence de catalyseurs spéciaux qui sont généralement des amines tertiaires ou des aminophénols.
— Le complexe trifl uorure de bore/monoéthylamine est souvent utilisé comme catalyseur latent, c’est-à-dire stable à froid, associé au durcisseur ainsi que le dicyanodiamide dans les poudres époxydiques pour peintures.
Différents adjuvants peuvent être ajoutés aux résines. Ce sont :
1. – Charges.
On peut ajouter jusqu’à 200 % du poids de la résine. Ce sont surtout des charges minérales (silice, talc, ardoise, mica, kaolin, graphite, amiante, fi bres de verre, charges métalliques, baryte) et dans certains cas de la farine de bois.
181
2. – Solvants.
Les résines époxydiques, peu polycondensées, sont solubles dans les solvants organiques polaires : alcools, cétones, acétates, chloroforme.
On utilise souvent des mélanges de solvants, par exemple :
— acétate de méthyle + acétate d’éthyle + alcool méthylique + toluène ;
— diacétone-alcool + toluène + xylène + acétate d’éthyle ;
— méthylisobutylcétone + méthylisobutylcarbinol + toluène.
Les mises en solution de résines sont effectuées pour fabriquer les revêtements, adhésifs, peintures et vernis à base de polyépoxydes, ainsi que les préimprégnés destinés à la stratifi cation.
3. – Diluants réactifs.
De nombreuses résines polyépoxydes liquides sont additionnées de diluants réactifs le plus souvent monoépoxydés. Ce sont en général, des
éthers ou esters mono ou polyglycidiques à bas poids moléculaires, lors du durcissement, partiellement ou intégralement à la réaction : butylglycidyléther, crésylglycidyléther, phénylglycidyléther…
4. – Pigments et colorants.
Une vaste gamme de substances colorantes peut être utilisée.
5. – Plastifi ants.
Certains phtalates sont quelquefois ajoutés aux résines.
6. – Extendeurs.
Ce sont des liquides non réactifs, ajoutés aux polyépoxydes, pour en abaisser le prix de revient :
— huile de pin pour les résines liquides sans solvant ;
— brais de houille ou de pétrole, goudrons pour les revêtements routiers.
7. – Flexibilisateurs.
Ce sont des liquides réactifs, c’est-à-dire susceptibles de réagir avec les groupes époxy, qui interviennent dans la réaction conférant une certaine fl exibilité et souplesse aux résines. On utilise notamment des élastomères polysulfurés.
II. – MISE EN ŒUVRE
Suivant la nature de la résine époxydique de départ, les méthodes de transformation varient :
182
1. – Moulage.
— Par coulée.
Les résines faiblement polycondensées se présentent sous la forme de liquides visqueux ou de solides. Le durcisseur est ajouté à la résine liquide, ou bien à la résine préalablement fondue vers 130-140 °C. Le durcissement s’effectue ensuite dans un moule, soit à froid, soit à chaud jusqu’à 200 °C.
— À la presse par compression et transfert.
Il est utilisé pour l’obtention de matériaux renforcés à partir de granulés de polyépoxydes modifi és et chargés notamment de fi bres de verre. Le durcissement s’effectue à des températures allant de 140 à 220 °C sous l’action de la pression.
— À la presse par injection.
Cette technique est utilisée pour mouler les pièces en polyépoxydes.
Les températures sont de l’ordre de 150-220 °C.
2. – Revêtements.
Les résines époxydiques trouvent de larges applications dans l’industrie des vernis et peintures et dans les opérations d’imprégnation.
— Peintures et vernis.
Ces produits présentent de bonnes caractéristiques de dureté, souplesse et résistance aux produits chimiques. Leurs qualités d’adhérence permettent l’application sur les métaux.
On distingue :
• des systèmes multicomposants (résine et durcisseur) avec ou sans solvants susceptibles de durcir à froid ou à chaud. Ces systèmes font appel aux réactions du groupe époxy avec des fonctions amines, des résines aminoplastes ou phénoplastes.
• des esters d’acides gras obtenus par réaction des groupes époxy et hydroxyles d’une résine époxydique avec des acides gras. Ces produits en solution associés à des siccatifs ou des résines aminoplastes, permettent d’obtenir des vernis séchant à l’air ou durcissant au four. L’application peut
être réalisée au pistolet, à la brosse. Le séchage peut s’effectuer, selon le cas, à la température ambiante ou par cuisson de 160 à 240 °C.
— Poudres pour revêtements.
Un mélange de résine fi nement broyée, avec les charges et le durcisseur est pulvérisé au pistolet électrostatique ou appliqué par immersion d’une pièce chaude dans un lit fl uidisé. Le durcissement fi nal s’opère par cuisson à l’étuve à 150-180 °C.
— Résines d’imprégnation.
Ce sont, soit des résines polyépoxydes contenant un durcisseur agissant
à chaud, soit des résines contenant un accélérateur, auxquelles on ajoute le durcisseur agissant à froid avant l ‘emploi.
183
Des polyépoxydes modifi és peuvent également être employés.
3. – Colles.
Les colles à base de polyépoxydes ont d’excellentes propriétés d’adhérence. Elles se présentent sous forme de bâtonnets, de liquides, de solutions ou de pâtes. Elles peuvent être mono ou bicomposants (résine et durcisseur).
Selon leur présentation physique et les données de la production, les colles peuvent être appliquées manuellement (brosse, spatule, gant) ou à la machine (pulvérisation, extrusion, encolleuse à rouleau, etc.).
4. – Stratifi és.
Les supports sont à base de fi bres ou tissus de verre, papier, coton, carbone…
Ils sont imprégnés d’une solution de résine et durcisseur.
La cuisson s’effectue aux environs de 100 °C pour les durcisseurs agissant à chaud. D’autres systèmes durcissent à froid.
Les matériaux préimprégnés et prégélifi és peuvent être moulés à la presse.
Il existe d’autres procédés de stratifi cation, dont l’un consiste à effectuer la projection simultanée de résines et de verre.
III. – RISQUES*
1.
–
Résines et adjuvants.
Les polyépoxydes sont des résines diffi cilement infl ammables mais brûlant assez facilement lorsque la combustion est entretenue.
Leur mise en œuvre présente des risques divers. En particulier, elle peut donner lieu à l’apparition de réaction d’irritation et de sensibilisation de la peau relativement fréquentes [134]. Les phénomènes d’irritation sont provoqués par les résines, les durcisseurs et/ou les solvants. Les réactions de sensibilisation se manifestent comme des allergies envers la résine, envers le durcisseur, envers la résine et le durcisseur ou envers d’autres constituants : les diluants réactifs, les résines formophénoliques notamment. Les lésions
également le tableau en fi n de volume.
184
sont localisées le plus souvent au visage, aux mains et aux avant-bras [35],
[135]. Des troubles respiratoires beaucoup plus rares peuvent également être observés [136], [137].
a) Résines.
Les résines époxydiques solides à base de bisphénol A ne sont pas irritantes et pratiquement pas sensibilisantes.
Les résines à base de bisphénol A liquides non modifi ées, semi solides ou solides en solution, les résines à base de novolaques liquides et les résines aliphatiques sont plus ou moins irritantes pour la peau et peuvent être sensibilisantes.
Les résines liquides modifi ées, c’est-à-dire contenant des abaisseurs de viscosité du type éthers glycidiques sont plus irritantes et peuvent être fortement sensibilisantes. Une allergie de groupe a été signalée [30] entre les résines et les éthers glycidiques.
Les résines époxydiques modifi ées et les diluants glycidiques peuvent contenir des traces (quelques p.p.m.) d’épichlorhydrine résiduelle, toxique par inhalation et contact cutané, cancérogène suspecté.
Certaines résines cychloaliphatiques ont été à l’origine de cancers chez l’animal.
b) Durcisseurs :
— amines : ce sont des composés à réaction fortement basique, facilement absorbés par la peau. Elles ont une action irritante et sensibilisante [17].
Parmi les amines aliphatiques, la trièthylènetétramine corrosive et sensibilisante peut avoir une action nocive sur le foie.
Les amines aromatiques peuvent provoquer des irritations, des troubles sanguins et pour certaines, des cancers. Le diamino-4-4’-diphénylméthane est, en particulier, un poison du foie [41] ;
— anhydrides [25] : ce sont également des irritants et des sensibilisants mais leur action est moins marquée que celle des amines ;
— résines synthétiques (phénoplastes et aminoplastes) : ajoutées comme modifi cateur de la résine époxydique, elles peuvent apporter leur pouvoir réactogène propre (allergie au formol notamment) ;
— les aminophénols : ils sont utilisés comme catalyseurs de certaines résines
époxydiques modifi ées ; ils peuvent également être irritants et allergisants
[29].
Les durcisseurs agissent surtout par contact direct au moment de leur incorporation à la résine et lors de la manipulation du mélange « résine + durcisseur ». Sont également à incriminer les souillures des outils, des postes de travail et l’ébavurage des pièces coulées.
c) Diluants réactifs.
Les éthers glycidiques sont à des degrés variables irritants et sensibilisants pour la peau [140] ; leurs vapeurs sont irritantes pour les muqueuses oculaires et respiratoires. De plus, ils peuvent contenir un peu plus d’épichlorhydrine résiduelle que les résines elles-mêmes.
185
d) Solvants.
L’action nocive et irritante des solvants utilisés dans les vernis, colles et adhésifs s’ajoute à celle des durcisseurs. Les hydrocarbures benzéniques, toluène et xylène, sont les plus nocifs.
e) Charges.
La plupart des résines époxydiques sont fortement chargées.
L’action des charges (fi bres de verre, silice, amiante…) peut se manifester au moment de leur incorporation dans le mélange ainsi qu’à l’usinage :
— les fi bres de verre sont irritantes pour la peau et les voies respiratoires ;
— la silice et le talc peuvent contenir des quantités variables de silice libre cristallisée qui peut provoquer la silicose contrairement à la forme amorphe qui ne présente pas les mêmes risques.
f) Extendeurs.
Parmi eux, l’huile de pin peut être allergisante et le brai de houille comporte des risques d’effet cancérogène.
g) Produits pour traitement de surface.
À la mise en œuvre des colles et vernis, les surfaces des objets doivent
être préparées au préalable. Les produits utilisés à cet effet (acide sulfurique, mélange sulfochromique, solvants chlorés, sable) font intervenir un risque supplémentaire. Se reporter au tableau en fi n de volume.
D’une manière générale, lors de l’emploi de résines époxydiques, des
mesures de prévention [134], [138], collective et individuelle, doivent être prises de façon à empêcher tout contact direct de l’épiderme ou des muqueuses avec les résines et leurs durcisseurs. Se reporter notamment aux documents cités en référence [134], [138] et [42] plus spécialement pour l’application par pulvérisation. Par ailleurs, il est nécessaire d’attirer l’attention de l’utilisateur sur la possibilité qu’il a d’effectuer un choix des produits les moins dangereux parmi les durcisseurs notamment.
Enfi n en cas de souillures de la peau, ce qui doit être exceptionnel, il ne faut pas utiliser de solvants mais des crèmes dissolvantes spéciales du commerce.
2. – Dégradation thermique. a) Aux températures de mise en œuvre.
Lors du durcissement à chaud (température pouvant atteindre 240 °C) il peut y avoir des dégagements des constituants volatils des résines notamment. Leurs vapeurs ont irritantes pour les voies respiratoires et parfois sensibilisantes, comme il est dit au paragraphe précédent.
186
Au cours du durcissement à chaud obtenu par le complexe trifl uorure de bore-monoéthylamine des gaz fl uorés toxiques et corrosifs se dégagent malgré le faible pourcentage de fl uorures.
La dégradation thermique des résines ne commence réellement qu’à partir de 250 °C [139] et même vers 350 °C pour certaines résines durcies
[7].
b) En cas de pyrolyse ou de combustion [33], [48].
Les principaux produits de dégradation sont l’oxyde de carbone, toxique, l’anhydride carbonique, des hydrocarbures aliphatiques (méthane,
éthylène…), des hydrocarbures benzéniques légers (toluène…), nocifs et irritants, de petites quantités d’aldéhydes (formol…) irritants des voies respiratoires. Des produits azotés toxiques (ammoniac, acide cyanhydrique) peuvent également se dégager dans le cas de résines durcies avec des amines.
Les résines polyépoxydes, bien que diffi cilement infl ammables, peuvent brûler assez facilement en dégageant en plus des gaz, des fumées noires de carbone [24]. La manipulation des résines en poudre notamment lors de l’application des revêtements comporte des dangers d’explosion, comme pour toutes les poussières organiques combustibles [42], [141].
187
POLYIMIDES
Noms commerciaux
KINEL
I. – CARACTÉRISTIQUES
Les polyimides, derniers-nés des matières plastiques ayant une bonne résistance à la chaleur (thermostables), sont caractérisés par la présence dans la macromolécule d’hétérocycles imides.
Ils peuvent être obtenus par polycondensation d’un dianhydride aromatique avec une diamine aromatique. Lorsque ce sont l’anhydride pyromellitique et le diaminobenzène par exemple, leur formule peut s’écrire :
Ils peuvent être également obtenus par polymérisation d’un composé contenant préalablement l’hétérocycle imide, l’aminobismaléimide notamment [142].
Il existe aussi les polyamides-imides, famille dérivée des polyimides.
Ces polymères sont caractérisés par leurs propriétés de résistance à la chaleur, aux radiations, à certains produits chimiques (huiles, solvants, fl uides frigorigènes).
Des adjuvants peuvent leur être associés.
1. – Charges.
Les poudres à mouler sont habituellement chargées. Les charges sont de nature fi breuses (verre, carbone, amiante…) ou pulvérulentes (graphite, oxydes ou sulfures métalliques, polytétrafl uoréthylène).
188
2. – Solvants.
Les polyimides sont peu solubles dans les solvants. Les prépolymères peuvent être mis en solution dans les solvants polaires.
Les vernis d’émaillage sont généralement utilisés sous forme de solution dans les mélanges de solvant polaire et de diluant benzénique, le mélange Nméthylpyrrodilone-xylène notamment.
II. – MISE EN ŒUVRE
Les polyimides se présentent dans le commerce sous des formes variées pour lesquelles les mises en œuvre sont différentes.
1. – Poudres à mouler.
Ce sont des poudres ou des granulés constitués de résines associées à des charges. Les résines utilisées sont des prépolymères thermodurcissables possédant un point de ramollissement allant généralement de 70 à 200 °C.
La transformation peut être effectuée par compression, par transfert avec préalablement un pastillage à chaud des préformes.
Le moulage par compression s’effectue vers 200-250 °C et est suivi d’un recuit à 250 °C.
Les pièces moulées sont utilisées en tant qu’élément de structure,
élément de friction ou élément autolubrifi ant. L’application de la technique du surmoulage permet l’obtention d’éléments complexes associant plusieurs de ces fonctions.
2. – Vernis d’émaillage.
Ce sont généralement des solutions de polymère à 25 % environ dans des mélanges de solvant (N-méthylpyrrodilone/xylène).
Ils peuvent être utilisés pour l’émaillage direct ou le surcouchage. L’émail obtenu a une bonne résistance à l’abrasion, aux hydrocarbures fl uorés et une bonne tenue aux surcharges thermiques.
3. – Résines d’imprégnation.
Ce sont des prépolymères thermodurcissables en solution dans des solvants polaires qui servent à l’imprégnation de substances fi breuses. On opère en continu par trempé dans la résine fondue ou dans une solution à
50 % de résine.
L’imprégnation de « rovings » est utilisée dans l’enroulement fi lamentaire.
Les préimprégnés à base de tissus de verre permettent la réalisation de stratifi és plans ou tubulaires et l’obtention de circuits imprimés multicouches.
189
Le moulage des stratifi és peut s’effectuer par cuisson sous presse ou moulage à sec. On fait suivre le moulage d’un recuit à 200-250 °C.
4. – Ébauches.
Elles permettent la réalisation de pièces à géométrie complexe.
5. – Adhésifs.
Ce sont des adhésifs haute température destinés à l’assemblage de pièces métalliques (acier, titane) ou composites (structures isolantes) devant conserver une haute résistance en traction-cisaillement après des expositions
à des températures de 200-300 °C. Ils sont utilisés dans l’électrotechnique et l’aéronautique.
6. – Films.
Dotés d’un ensemble inhabituel de propriétés physiques, chimiques et électriques, ils ont ouvert des perspectives nouvelles au niveau des applications pratiques.
Ces applications concernent le guidage des fi ls de bobinage de moteurs et de câbles d’avion, les garnitures d’encoches de moteurs, les circuits imprimés souples, les condensateurs, les transformateurs.
III. – RISQUES*
1. – Résines et adjuvants.
La manipulation et la mise en œuvre des résines et des polymères peut comporter des risques. Il est possible notamment qu’ils contiennent de petites quantités d’amines aromatiques servant à leur préparation.
Certaines de ces amines peuvent, à l’état pur, être responsables d’irritations cutanées, de méthémoglobinémie et de cancers.
D’autre part, les risques attribuables aux charges et aux solvants ne doivent pas être négligés.
— Charges.
Elles interviennent dans les poudres à mouler au moment de leur incorporation et au cours de la transformation.
Les fi bres de verre sont irritantes pour les voies respiratoires et la peau.
Les fi bres d’amiante sont responsables, d’une part, de l’asbestose, d’autre part, de cancers bronchiques et de mésothéliomes.
également le tableau en fi n de volume.
190
— Solvants.
Ils interviennent dans la préparation et la mise en œuvre des résines à imprégnation, des adhésifs et des vernis.
Les diluants benzéniques, les xylènes notamment, sont nocifs par inhalation et irritants pour la peau et les voies respiratoires.
Le N-méthylpyrrolidone est moyennement irritant pour la peau et les muqueuses.
2.
–
Dégradation thermique.
Les polyamides sont thermiquement stables. Ils commencent à se décomposer entre 400 et 500 °C suivant la nature des composés de départ
[7], [32]. Les produits de dégradation sont principalement l’oxyde de carbone, toxique, l’anhydride carbonique, l’acide cyanhydrique, très toxique en particulier par inhalation, et en quantité moins importante, l’hydrogène, l’ammoniac et des hydrocarbures benzéniques [33].
191
POLYURÉTHANNES
Abréviation normalisée : PUR
Noms commerciaux
Polyuréthannes ou composants pour polyuréthannes.
ATPOL (polyols) LUPRANOL (polyols)
BAYFILL LUVIPREN
BAYFIT MARSIPOL
BAYMER MO-DO
BECKADUR NIAX
BERMODOL NOVADUR
CARADATE (isocyanates)
CARADOL (polyols)
NOVATRON
PAPI (isocyanates)
DALTOCAST (polyols)
DALTOCEL (polyols)
PLURACOL (polyols)
POLYFAN
DALTOLAC (polyols) POLYLEN
DALTOROL POLYPHEN
DESMODUR (isocyanates)
DESMOPHEN (polyols)
QUADROL
RIMTHANE
DURÉTHAN U ROUTANATE
EKAMÈRE ROUTANOL
EKANATE (isocyanates) SCOTCHCAST
ESTAL SCURANE
FLEXOROB (polyols)
FLEXOTHANNE (isocyanates)
FORMREZ (polyols)
GLENDION (polyols)
HYLÈNE (isocyanates)
ISONATE (isocyanates)
ISOROB (polyols)
ISOTHANNE (isocyanates)
SCURATAN
SODÉTHANE (polyols)
SORANE
SUPRASEC (isocyanates)
TÉDIMON (isocyanates)
TERCAROL
TOLONATE
UCÉCOAT
IXOL (polyols) UGIPOL (polyols)
LASTANE URADUR
LILÈNE (isocyanates) VORANOL (polyols)
Mousses de polyuréthannes.
ALVÉOFLEX POLINA
BAYDUR POLITAN
DALTOFLEX ROTANE
DUNLOPREN ROTSTYL
KLEMOCELL SCURAFLEX
192
KLETHERCELL TEXAS
MOLTOPREN URAFLEX
NERTRIL URAFOAM
Élastomères polyuréthannes thermoplastiques.
ADIPRÈNE JECTOTHANE
CYANAPRÈNE PELLETHANE
DALTOMOLD ROYLAR
DESMOPAN TEXIN
E 275 VULKOLLAN
ESTANE prépolymères, isocyanurates, adducts polyisocyanates…
La notation « polyols » signifi e polyols, polyétherpolyols, polyesteropolyols, pouvant contenir des additifs, catalyseurs aminés notamment.
I. – CARACTÉRISTIQUES
Les polyuréthannes constituent une famille très vaste de produits : mousses rigides ou souples, thermoplastiques et thermodurcissables durs ou mous, élastomères, peintures, vernis, colles, solutions et dispersions pour enduction.
Ils résultent généralement de la réaction exothermique d’addition de polyisocyanates sur des polyols auxquels on peut ajouter, selon le cas, des catalyseurs, des tensio-actifs, des agents d’expansion, des solvants, des pigments, etc.
Lorsque les matières premières sont des diisocyanates et des diols, leur formule générale peut s’écrire :
R et R’ étant des radicaux organiques variables. Des réticulations interviennent ensuite entre les chaînes conduisant à un réseau tridimensionnel. Des réactifs secondaires aminés ou de l’eau peuvent aussi réagir avec les polyisocyanates.
1. – Matières premières réactives [147]
— Isocyanates :
Diisocyanates de 2,4 et 2,6-totuylène (TDI).
Diisocyanate de diphénylméthane (MDI).
Diisocyanate d’hexaméthylène (HDI).
Diisocyanate d’isophorone (IPDI).
Polyisocyanates de polyarylène, etc.
193
— Composés à terminaison isocyanate.
Ils dérivent des précédents et se comportent comme des isocyanates lourds, présentant une tension de vapeur et une réactivité diminuées. Ils contiennent des quantités variables de l’isocyanate monomère d’origine. Ce sont :
• les adducts polyisocyanates : le plus classique est l’adduct diisocyanate de toluylène-triméthylolpropane ;
• les prépolymères notamment le polyméthylène polyphénylisocyanate (poly
MDI) ;
• les isocyanurates obtenus par polymérisation des diisocyanates.
— Polyols :
Ce sont des produits à chaîne carbonée plus ou moins longue possédant des groupements hydroxylés : polyéthers polyols, polyesters polyols, glycérine butanediol, etc.
Des polyols halogénés et/ou phosphorés sont utilisés pour améliorer le comportement au feu des produits fi nis.
— Amines (réactifs secondaires) :
•
4,4’-méthylène bis (orthochloraniline) (MOCA), méthylènedianiline…
• méthyldiéthanolamine, N,N,N’,N’tétrakis (2-hydroxypropyl) éthylène-diamine…
— Eau (réactif secondaire).
L’eau neutralise les fonctions isocyanates avec dégagement de gaz carbonique qui peut servir à l’expansion des mousses.
2. – Matières non réactives. a) Catalyseurs :
•
Amines secondaires ou tertiaires tétraméthyléthylènediamine, benzyldiméthylamine…
•
Naphténates de plomb et de cobalt.
b) Agents d’expansion pour mousses et matériaux allégés :
•
Composés fl uorocarbonés : trichlorofl uorométhane (F11), dichlorodifl uorométhane (F12).
•
Solvants légers halogénés : dichlorométhane… c) Solvants pour peintures, vernis, colles, enduction et pour le nettoyage des machines :
•
Esters : acétates d’éthyle, de butyle, de méthylglycol.
•
Cétones : acétone, méthyléthylcétone (MEC), cyclohexanone.
•
Solvants chlorés : dichlorométhane, 1,2-dichloréthane.
•
Sulfate de méthyle, tétrahydrofuranne (THF), diméthylformamide.
•
Diluants : alcools, toluène, xylène, solvant naphta.
d) Tensio-actifs pour produits alvéolaires et émulsions :
•
Silicones oxydes d’alkylène.
e) Stabilisants :
•
Sels organiques d’étain, dilaurate de dibutylétain notamment.
194
f) Charges – Pigments :
•
Craie, sulfate de baryum, oxyde de titane, kaolins, oxydes de fer, poudres métalliques, graphite.
•
Charges ignifugeantes : oxyde d’antimoine, alumine hydratée, composés halogénés, phosphorés notamment le phosphate de trischloroéthyle.
II. – MISE EN ŒUVRE
On doit distinguer la fabrication proprement dite des polyuréthannes à partir des matières premières de base réactives et la transformation qui ne fait plus appel à des réactions chimiques.
1. – Prépolymères et adducts.
Ils sont obtenus généralement par réaction à température rigoureusement contrôlée des isocyanates avec tout ou partie des polyols devant entrer dans la composition fi nale. Si nécessaire, on ajoute des solvants pour éviter la prise en masse ou faciliter la mise en œuvre ultérieure.
Les prépolymères à fort excès d’isocyanates (dits semi-prépolymères) sont pour la plupart liquides sans adjonction de solvants. Après achèvement de la réaction, on refroidit et on stocke.
2. – Mousses et élastomères expansés.
Les mousses sont fabriquées directement à partir des matières premières réactives : polyisocyanates (ou prépolymères) et polyols, en présence de catalyseurs, de tensio-actifs et d’agents d’expansion.
Les différents constituants, dosés en quantités bien déterminées, sont mélangés vigoureusement. Le plus souvent l’opération se fait dans une machine à pompe doseuse et tête mélangeuse. Le mélange liquide, dont l’expansion commence très vite, est coulé sur une bande (blocs) ou dans des modules (moulages) ou dans des cavités à remplir (coulée in situ pour isolation thermique par exemple), ou bien il est projeté comme de la peinture
(isolation thermique également).
3.
–
Élastomères et pièces coulées.
Ils se fabriquent comme les mousses mais sans agents d’expansion ; ils peuvent être moulés (pièces fi nies) ou coulées in situ (joints de bâtiment par exemple).
Les élastomères thermoplastiques polyuréthannes, obtenus à partir de diols simples et macromoléculaires et d’isocyanates sont des polymères séquencés comprenant des segments rigides et d’autres fl exibles [45] (voir aussi le chapitre II des généralités).
4. – Peintures, vernis et enductions [148].
Les peintures et vernis peuvent se présenter sous des formes variées.
195
a) Vernis réactifs à un composant.
Il s’agit de prépolymères à terminaisons isocyanates généralement en solution qui réticulent sous l’action de l’humidité atmosphérique ; la réaction, lente, n’entraîne pas la formation de mousses.
b) Peintures, vernis et enductions réactifs à deux composants.
Ils sont constitués d’un prépolymère à terminaison isocyanate et d’un polyol ou d’une diamine plus ou moins complexes ; ces composants sont en solution ; on les mélange en proportions déterminées au moment de l’application.
Les charges et pigments, ainsi que les catalyseurs, le cas échéant, sont incorporés dans le polyol, plus rarement dans l’isocyanate.
c) Peintures et enductions non réactives.
Ce sont des uréthannes fi nis en solution. On peut leur assimiler les
« huiles d’uréthannes » qui sont des peintures usuelles modifi ées par des quantités plus ou moins importantes d’isocyanates (totalement uréthanisés) pour améliorer les propriétés.
d) Vernis aux isocyanates bloqués.
Ce sont des prépolymères dont la fonction isocyanate est bloquée par un phénol. Par chauffage, le phénol est libéré, les fonctions isocyanates sont régénérées et peuvent réagir avec l’agent de réticulation choisi. Ces produits sont employés pour l’émaillage des fi ls électriques.
5.
–
Thermoplastiques.
Ce sont des uréthannes fi nis, obtenus en solution ou émulsion, séchés et granulés ou mis en écailles. Après addition éventuelle de charges et colorants, on les transforme par compression, injection ou extrusion. Selon les cas, ils se comportent comme des thermoplastiques vrais ou comme des caoutchoucs injectables. Certains peuvent être mis en solution pour enduction.
6. – Utilisations diverses.
Les polyuréthannes sont utilisés comme liants dans la fabrication des noyaux de fonderie [37], [46].
III. – RISQUES*
1. – Résines et adjuvants.
Les résines polyuréthannes sont combustibles mais assez diffi cilement infl ammables, exception faite des mousses qui peuvent donner lieu à des infl ammations spontanées.
également le tableau en fi n de volume.
196
Totalement polymérisés, les produits fi nis sont physiologiquement inactifs. Toutefois, ils peuvent renfermer des restes de catalyseurs (voir les risques ci-dessous) et pendant quelques heures après leur fabrication certains peuvent dégager des vapeurs d’isocyanates qui sont progressivement neutralisées par la vapeur d’eau atmosphérique.
Au cours de leur fabrication et de leur mise en œuvre [143], [144],
[147], par contre, les polyuréthannes entraînent des risques, notamment lors du moulage, de la projection par pistolet pour enduction des moules, de la coulée, de l’application des mousses par projections et des peintures par pulvérisation [42], de la préparation des mélanges, etc. Ces risques sont différents suivant les postes de travail et sont liés en particulier à la toxicité des produits de départ et des adjuvants.
a) Isocyanates et prépolymères [145], [146].
Les isocyanates sont particulièrement dangereux. Leurs vapeurs sont irritantes pour les yeux et l’appareil respiratoire, et sensibilisantes. Leur inhalation peut provoquer des accidents pulmonaires aigus graves et des syndromes asthmatiformes.
Les 2,4 et 2,6-diisocyanate de toluylène (TDI) sont toxiques et particulièrement dangereux à cause de leur volatilité. Il en est de même du diisocyanate d’hexaméthylène. Le diisocyanate de diphénylméthane (MDI) est également dangereux malgré sa moins grande volatilité. Il peut pénétrer dans les voies respiratoires sous forme de vapeurs quand il est chauffé ou sous forme de gouttelettes quand il est pulvérisé. C’est aussi souvent le cas des prépolymères qui se comportent comme des isocyanates à poids moléculaire plus ou moins élevé. Leur toxicité dépend également de leur teneur en monomère libre.
L’action de ces composés intervient aussi bien lors de la préparation des mélanges que pendant la mise en œuvre lorsque les produits sont appliqués notamment à la brosse ou au pistolet (peintures, vernis, colles, etc.) [152].
b) Polyols.
Ce sont des produits stables à haut point d’ébullition donc relativement inoffensifs lorsqu’ils sont purs. Mais ils sont souvent livrés en mélange avec les catalyseurs parmi lesquels fi gurent des amines, ou avec d’autres additifs
(agents d’expansion notamment), qui leur apportent leur toxicité propre.
c) Amines.
Les amines sont irritantes et parfois corrosives pour la peau. Certaines peuvent être sensibilisantes (dermites eczématiformes) [145]. Les amines aromatiques sont à l’origine de troubles sanguins et certaines sont responsables de cancers.
La méthylène bis o-chloraniline (MOCA) notamment est un cancérogène puissant chez l’animal [41].
d) Stabilisants.
Parmi les sels organiques d’étain, les dérivés dibutyles, le dilaurate de dibutylétain notamment, sont généralement nocifs, ils peuvent contenir
197
de faibles quantités de dérivés de tributylétain, toxiques du système nerveux.
e) Agents d’expansion.
Les hydrocarbures fl uorés peu nocifs à faible concentration sont narcotiques à concentration élevée. Ils se décomposent en produits toxiques par contact avec une fl amme ou une surface métallique portée au rouge.
Le dichlorométhane est nocif par inhalation.
f) Solvants.
Ils interviennent à des quantités relativement importantes et s’évaporent d’autant plus facilement que beaucoup d’opérations font intervenir l’action de la température.
Les hydrocarbures chlorés, ainsi que le toluène et les xylènes, sont nocifs par inhalation et contact cutané.
Le tétrahydrofuranne est un irritant des voies respiratoires et des muqueuses.
Le sulfate de méthyle est particulièrement toxique par inhalation. Il est soupçonné d’être cancérogène pour l’homme [31], [161].
g) Charges.
Parmi les charges ignifugeantes, l’oxyde d’antimoine est nocif et irritant pour les voies respiratoires.
Parmi les composés halogénés et/ou phosporés, le phosphate de trischloréthyle notamment est nocif.
Des mesures de prévention sont nécessaires lors de la fabrication et de la mise en œuvre des polyuréthanes. Se reporter notamment aux documents cités en référence [144], [145], [166] et [42] pour l’application par pulvérisation.
2. – Dégradation thermique. a) Aux températures de mise en œuvre (jusqu’à 250 °C environ)
L’action de la chaleur augmente les risques de volatisation des produits de départ (isocyanates monomères, prépolymères…) et des autres réactifs utilisés lors de la fabrication ou encore présents au cours de la transformation.
En outre, il a été constaté pour des mousses ne contenant pas de composés de départ résiduels, une possibilité de dépolymérisation, parfois dès 200 °C, avec formation d’isocyanates et libération d’amines et de diols.
La toxicité de ces composés a été précisée au paragraphe précédent.
On peut également observer pour certains polyuréthannes à partir de 180-
200 °C une libération de traces de cétones, d’aldéhydes et d’hydrocarbures légers.
198
Certains modes de transformation, découpe au fi l chaud notamment, peuvent accélérer cette décomposition.
Il y a lieu de remarquer que, dans certains cas (vernis au four livrés prêts
à l’emploi) où les polyisocyanates sont remplacés par des phényluréthannes, l’infl uence de la chaleur peut libérer du phénol, produit corrosif pour la peau et les muqueuses.
b) En cas de pyrolyse ou de combustion [33], [48], [150].
Les principaux produits de décomposition sont l’anhydride carbonique, l’oxyde de carbone, toxique, des nitriles (acétonitrile, benzonitrile, acrylonitrile), tous toxiques par inhalation, de l’acide cyanhydrique, également très toxique, et des hydrocarbures aliphatiques et benzéniques. La dégradation s’accompagne également de la production de fumées composées de diisocyanates, de leurs dimères ou de leurs premiers polymères et de molécules possédant des terminaisons isocyanates [149]. Si la résine contient des retardateurs de combustion ou des polyols halogénés ou phosphorés, des acides corrosifs chlorhydrique ou bromhydrique notamment ou des produits phosphorés toxiques peuvent se dégager lors de la pyrolyse ou de la combustion [153].
Les polyuréthannes compacts sont combustibles mais propagent mal la fl amme. Par contre, les produits alvéolaires (mousses) sont facilement infl ammables [44]. Leur pouvoir calorifi que est élevé (environ 10 000 kcal/ kg) [8]. Leur combustion est assez vive et provoque une forte élévation de température. Certaines qualités ignifugées s’enfl amment moins facilement mais brûlent aussi rapidement que les mousses non traitées [43] ; les mousses
à base d’isocyanurates sont également moins infl ammables [151].
Une attention particulière doit être portée aux blocs de mousse épais qui sont susceptibles de s’enfl ammer spontanément pendant quelques heures après leur fabrication, notamment s’ils sont empilés aussitôt.
199
POLYORANOLSILOXANES
Abréviation normalisée : SI
Noms commerciaux
DOW CORNING FLUIDS SILASTIC
ECCOSIL SILECTO
RHODORSIL SILITRITE
SILASTÈNE
I. – CARACTÉRISTIQUES
Les polyorganosiloxanes ou silicones ont pour formule générale : où R est un groupe alkyle ou aryle.
Les silicones sont obtenus par polycondensation de silanols dérivés eux-mêmes de chlorosilanes par hydrolyse.
Leurs caractéristiques sont leur grande stabilité thermique, leur caractère hydrophobe, leur résistance aux agents chimiques et atmosphériques et leurs propriétés diélectriques en basse comme en haute fréquence.
Ces produits se trouvent dans le commerce sous des formes variées :
— Huiles : ce sont des liquides transparents, inodores, stables au vieillissement. Leur propriété la plus remarquable est certainement la faible variation de leur viscosité en fonction de la température.
— Pâtes et graisses : elles sont constituées par des huiles silicones pour la plupart épaissies par des charges minérales très fi nes. Certaines graisses contiennent en outre des adjuvants de lubrifi cation. Leur consistance varie très peu avec la température et leur stabilité thermique est excellente.
— Résines : généralement livrées en solution, les résines se trouvent dans un
état de polymérisation incomplète. Au moment de l’utilisation par chauffage et sous l’action d’un catalyseur, le solvant est éliminé et la polycondensation est achevée. Le produit obtenu est un solide de rigidité variable.
— Poudres à moules : elles se différencient entre elles par la nature des charges utilisées.
200
— Des élastomères sont également obtenus à partir de silicones.
Différents produits peuvent être ajoutés aux résines brutes de silicones :
1. – Solvants.
Les solvants les plus courants sont le toluène et le méthylcyclohexane, parfois employés conjointement.
D’autres solvant sont parfois utilisés et notamment :
— des hydrocarbures : xylènes, essence ;
— des hydrocarbures chlorés : trichloréthylène, perchloréthylène ;
— des cétones : acétone, etc.
2. – Charges.
On emploie surtout la silice, mais également les fi bres de verre, la terre d’infusoires, le carborundum en poudre, le bronze d’aluminium, l’oxyde de zirconium, etc.
3.
–
Pigments.
Ajoutés à raison de 1 à 3% en poids de la résine, ce sont :
— des oxydes métalliques (titane, chrome, cobalt, fer, zinc) ;
— du sulfure de cadmium ;
— du noir de fumée.
II. – APPLICATIONS – MISE EN ŒUVRE
Elles varient avec la nature des silicones (fl uides, solutions, émulsions, poudres, pâtes, etc.).
1. – Fluides.
Les fl uides peuvent être utilisés chargés ou non, en solution ou en
émulsion.
Ce sont d’excellents liquides thermoplastiques, supportant de grands
écarts de température, particulièrement indiqués pour le refroidissement des moteurs d’avions et des compresseurs.
Ils trouvent encore de nombreuses applications comme agents de démoulage, anti-adhésifs, antimousses, adjuvants pour peintures.
2. – Pâtes et graisses. températures élevées, comme agents d’étanchéité pour les vannes,
201
coussinets, roulements à billes, axes, etc., et comme agents de protection de connections ou des isolateurs élecriques.
3. – Résines et vernis.
Une première gamme de résines appelées « hydrofugeants » sert à l’hydrofugation de matériaux très divers : textiles, cuir, papier, matériaux de construction, produits pulvérulents, etc.
Ces hydrofugeants se présentent sous forme de fl uide par silicone, en solution ou en émulsion dans l’eau.
Une deuxième gamme de produits, qui sont des solutions de résines dans un solvant, trouve des applications, d’une part dans les industries
électriques et électroniques (vernis isolants – confection de stratifi és), d’autre part pour les revêtements protecteurs ou décoratifs (pigments) présentant une bonne stabilité à la chaleur et au vieillissement naturel. Ces produits ajoutés aux résines organiques leur apportent également ces avantages.
Les applications de ces résines sont faites au trempé, à la brosse, au rouleau ou bien au pistolet. Le séchage peut être réalisé à l’air, en étuve ou au four.
Lorsque le dépôt est appliqué sur des surfaces métalliques, celles-ci doivent être préparées à l’avance par trempage dans un mélange d’alcool, d’acide phosphorique et de chromate de zinc.
Dans certains cas, on recouvre ou imprègne à partir d’un chlorosilane utilisé en phase liquide ou en phase vapeur. Par hydrolyse (action de l’eau) on obtient les silicones correspondants avec départ d’acide chlorhydrique. Ce dernier est éliminé par chauffage. On lave et on sèche ensuite.
4. – Poudres à mouler.
Ce sont généralement des granulés formés d’un mélange de résines de silicones et de fi bres textiles, de fi bres de verre ou d’autres matières minérales.
Le moulage peut être réalisé par transfert ou par compression à des températures de l’ordre de 170-190 °C.
5. – Stratifi és.
Ils sont à base de fi bres de verre ou d’amiantes. Les fi bres sont imprégnées d’une résine à 60 % dans le toluène, puis préséchées et pressées
à une température de l’ordre de 175 °C sur presse « basse pression ».
202
III. – RISQUES
*
1. – Résines et adjuvants.
Les silicones brûlent très diffi cilement.
Excepté une légère action irritante pour la conjonctive [49], les résines ne présentent pas de risque toxicologique particulier à température ordinaire
à l’exception du danger habituel dû aux poussières inertes lorsqu’elles sont manipulées sous forme pulvérulente.
Par contre, les chlorosilanes (produits intermédiaires dans la fabrication des silicones) sont des produits corrosifs. Ils dégagent au contact de l’humidité, de l’acide chlorhydrique, particulièrement dangereux pour les yeux et les voies respiratoires.
La préparation des surfaces métalliques, avant l’application d’une enduction de silicones, fait intervenir l’acide phosphorique et le chromate de zinc. Le premier, lorsqu’il vient au contact de la peau, exerce une forte action corrosive et est particulièrement dangereux pour les yeux. Le chromate de zinc peut provoquer des troubles par inhalation.
Les risques dus aux adjuvants qui se manifestent surtout au moment de leur incorporation peuvent aussi intervenir au cours de la transformation.
— Solvants.
Ils interviennent notamment dans la préparation des adhésifs, vernis
« hydrofugeants ».
Les hydrocarbures benzéniques, toluène et xylènes sont infl ammables et nocifs par inhalation (action ébrio-narcotique).
Les hydrocarbures chlorés : trichloréthylène et perchloréthylène sont nocifs par inhalation et contact cutané.
Tous ces solvants ajoutent à leur toxicité une action irritante pour la peau et les muqueuses.
— Charges.
Elles présentent un risque au moment de leur incorporation.
La silice sous sa forme cristallisée peut provoquer la silicose. Par contre, la silice amorphe qui constitue la majeure partie des silices ultrafi nes ne présente pas les mêmes risques.
Les fi bres de verre sont irritantes pour les voies respiratoires et la peau.
— Pigments.
Se reporter au tableau en fi n de volume.
également le tableau en fi n de volume.
203
2. – Dégradation thermique.
Les silicones commencent généralement à se décomposer au-dessus de 350 °C, les polyphénylsiloxanes sont plus résistants à la chaleur que les polyméthylsiloxanes [32]. Lors de l’anhydride carbonique, de l’oxyde de carbone, des hydrocarbures aliphatiques ou benzéniques et des poussières de silice [33].
204
C. TABLEAU
CARACTÉRISTIQUES DE DIVERS PRODUITS ENTRANT DANS LA COMPOSITION DES
MATIÈRES PLASTIQUES OU POUVANT SE DÉGAGER LORS DE LA MISE EN ŒUVRE
OU EN CAS DE DÉGRADATION THERMIQUE
Acétate de n-amyle
Acétate d’éthyle
Acétate d’éthylglycol
Acétate d’isopropyle
Acétate de méthyle
Acétate de méthylglycol
Acétate de n-propyle
Produits
Acétone
Acétonitrile
Acétophénone
Acide acétique
(glacial)
Acide chlorhydrique
Acide cyanhydrique
Acide fl uorhydrique
Acide formique
Acide phosphorique
Acide sulfurique
Acroléine
Acrylate d’éthyle
Acrylate de méthyle
Acrylonitrile
Températures d’ébullition ou de fusion en °C
Eb.
149
Eb.
77
Eb.
82
Eb.
202
Eb.
118
Eb.
-83
Eb.
26
Eb.
156
Eb.
89
Eb.
57
Eb.
144
Eb.
102
Eb.
56
Eb.
19,5
Eb.
101
Eb.
260
Eb.
290
(décomp.)
Eb.
53
Eb.
100
Eb.
80
Eb.
77
Points d’éclair coupelle fermée en °C
25
- 5
52
6
- 13
52
13
- 18
6
(C.O.)
82-105
40
- 18
69
(C.O.)
- 26
17
- 2,8
- 1
Limites d’explosivité en volume % dans l’air inf.
1,1
2,5
1,7
1,8
3,1
1,7
1,9
2,5
5,4
6
2,8
1,8
2,8
3,0 sup.
7,5
9,0
5,8
8,0
16
8,2
6,3
12,8
16 à 100 °C
41
31
25
17
Fiche toxicologique
INRS n°
175
18
71
107
88
131
107
3
104
24
13
4
6
149
37
30
57
185
181
105
206
CARACTÉRISTIQUES DE DIVERS PRODUITS ENTRANT DANS LA COMPOSITION DES
MATIÈRES PLASTIQUES OU POUVANT SE DÉGAGER LORS DE LA MISE EN ŒUVRE
OU EN CAS DE DÉGRADATION THERMIQUE
Produits
Alcool amylique
Alcool n-butylique
Alcool
éthylique
Alcool isopropylique
Alcool méthylique
Aldéhyde acétique
Aldéhyde crotonique
Aldéhyde formique
(formol)
Aldéhyde furfurylique
Amiante
Ammoniac
Anhydride carbonique
Anhydride chlorendique
Anhydride chromique
Anhydride maléique
Anhydride phtalique
Anhydride (di-) pyromellitique
Anhydride sulfureux
Aniline
Antimoine
(trioxyde d’)
Azo-bis (iso- butyronitrile)
AIBN
Températures d’ébullition ou de fusion en °C
Eb.
138
Eb.
118
Eb.
78
Eb.
82
Eb.
65
Eb.
21
Eb.
104
Eb.
- 19
Eb.
162
Eb.
- 33
Sublimation
– 78
Fus.
240
Fus.
196
Fus.
53
Fus.
131
Fus.
285
Eb.
- 10
Eb.
184
Fus.
655
Points d’éclair coupelle fermée en °C
33
29
13
12
12
- 38
13
60
102
151
70 se décompose dès 30 °C solide infl am.
Limites d’explosivité en volume % dans l’air inf.
1,2
1,4
3,3
2,0
6,0
4,0
2,1
7,0
2,1 à 152 °C
16
1,4
1,7
1,3 sup.
10 à 100 °C
11,2
19,0
11,8
36,5
57
15,5
73
25
7,1
10,4
20-25
Benzène
Eb.
80
- 11 1,4 8
Fiche toxicologique
INRS n°
206
80
48
66
5
120
7
40
145
16
1
205
38
41
19
49
207
CARACTÉRISTIQUES DE DIVERS PRODUITS ENTRANT DANS LA COMPOSITION DES
MATIÈRES PLASTIQUES OU POUVANT SE DÉGAGER LORS DE LA MISE EN ŒUVRE
OU EN CAS DE DÉGRADATION THERMIQUE
Chloroforme
Chlorophénols
(o-, m- ou p-)
Chromates et bichromates
(sels de chrome hexavalent)
Cobalt (sels de)
Crésols : o-
mp-
Cumène (iso- propylbenzène)
Cyanurate de triallyle
Cyclohexane
Produits
Benzonitrile
Benzophénone
Biphényles chlorés
Dérivés à 42% de CI
Dérivé à 54% de CI
Bisphénol A
(diphénylol propane)
Brai de houille
Températures d’ébullition ou de fusion en °C
Eb.
191
Fus.
26-49
Points d’éclair coupelle fermée en °C
75
Eb.
340-375
Fus.
153
195
79
Eb.
171
60 Butylglycol
Cadmium
(composés du)
Camphre 66
ε
-Caprolactame
Fus.
180
Fus.
69
Eb.
61 non infl ammable
64-121
Cyclohexanone
Diacétonealcool
Fus. 31
12
35
Eb.
152
Fus.
27
Eb.
81
Eb.
156
Eb.
166-169
81
86
86
44
166-170
- 20
44-164 pur 54 technique
< 21
Limites d’explosivité en volume % dans l’air inf.
sup.
1,1
à 170°C
0,6
1,4
}
1,1
0,9
1,3
1,3
1,8
10,6
3,5
6,5
8,4
9,4
6,9
Fiche toxicologique
INRS n°
194
91
76
60
82
180
128
97
17
39
61
208
CARACTÉRISTIQUES DE DIVERS PRODUITS ENTRANT DANS LA COMPOSITION DES
MATIÈRES PLASTIQUES OU POUVANT SE DÉGAGER LORS DE LA MISE EN ŒUVRE
OU EN CAS DE DÉGRADATION THERMIQUE
Produits
Températures d’ébullition ou de fusion en °C
4,44’-diamino- diphénylméthane
(méthylène dianiline)
1,2- ou o-di chlorobenzène
1,2dichloroéthane
(chlorure d’éthylène)
1,2dichloréthylène
- cis
- trans
2,4-diisocyanate de toluylène (TDI)
Fus.
90
Eb.
180
Eb.
83,5
Eb.
60
48
Dichlorodifl urométhane
(F 12)
Dichlorométhane
(chlorure de méthylène) gaz se liquéfi e à
- 30
Eb.
40
Diéthanolamine
Diéthylaniline
Diéthylènetriamine
Diisocyanate de diphénylméthane
(MDI)
Fus.
28
Eb.
215
Eb.
207
Fus.
37-39
Diisocyanate d’hexaméthylène
(HDI)
Diisocyanate d’isophorone
(IPDI)
Eb.
187
(à 133 mB)
Eb.
310
Fus.
21,8
Eb.
251
Points d’éclair coupelle fermée en °C
226
68-78
(C.O.)
13
4
2 non infl ammable non infl ammable
137-151
(C.O.)
85
102
(C.O.)
196
(C.O.)
135
(C.O.)
155
(C.O.)
132-135
(C.O.)
Diméthylacétamide
77
(C.O.)
Diméthylaniline
Diméthylformamide
(DMF)
Diméthylsulfoxyde
(DMSO)
Eb.
165
Eb.
193
Eb.
153
Eb.
189
63
67
(C.O.)
95
(C.O.)
Limites d’explosivité en volume % dans l’air inf.
2
6,2
9,7
9,7
15,5
9
15,9
12,8
12,8 dans l’oxygène
0,9
2,0
2,2
2,6
(à 160 °C)
à 100 °C sup.
66,4
9,5
11,5
15,2
28,5
135
Fiche toxicologique
INRS n°
218
73
54
79
34
147
143
129
164
166
46
69
137
209
CARACTÉRISTIQUES DE DIVERS PRODUITS ENTRANT DANS LA COMPOSITION DES
MATIÈRES PLASTIQUES OU POUVANT SE DÉGAGER LORS DE LA MISE EN ŒUVRE
OU EN CAS DE DÉGRADATION THERMIQUE
Produits
Dioxanne
Dioxolane
Épichlorydrine
Essences spéciales
A, B, C, E, F, G...
Éthers glycidiques
Températures d’ébullition ou de fusion en °C
Eb.
101
Eb.
75
Eb.
117
Interv. de distillation
30-160
Éthylène
Éthylène diamine (1,2diamino-éthane)
Gaz
Eb.
117
Éthylène-glycol
Eb.
197
Éthylglycol
Huiles de ricin de soja de lin
Eb.
135
Glycérine
Fus.
18
Eb.
290
Hexaméthylène tétramine
Solide
Sublim. vers
260
Eb. 313
Fus. 22
Eb. 343
Jaune de chrome
(chromate de plomb)
Fus.
844
Lactate d’éthyle
Eb.
154
Mélamine
Fus.
250
Méthacrylate de méthyle
Eb.
101
Méthane
Méthylal gaz
Eb.
42
2-méthylcyclohexanone
Eb.
160-170 fermée en °C
40 coupelle
160
250
229
282
206
46
10
48
Points d’éclair
12,2
1,7
(C.O.)
40
(C.O.)
En général
< 0
43,7
- 18
(C.O.)
111
Limites d’explosivité en
2,6
1,5
2,1
5,3
1,6 volume % dans l’air inf.
2,0
1 voir oxydes de glycidyle
2,7
3,2
15,7
11,4
12,5
15
6,1 sup.
22,2
6,5
36 toxicologique
58
177
59
62
139
Fiche
INRS n°
28
187
96
25
210
CARACTÉRISTIQUES DE DIVERS PRODUITS ENTRANT DANS LA COMPOSITION DES
MATIÈRES PLASTIQUES OU POUVANT SE DÉGAGER LORS DE LA MISE EN ŒUVRE
OU EN CAS DE DÉGRADATION THERMIQUE
Méthylisobutyl- cétone (MIBK)
N-méthyl- pyrrolidone
Monochloro- benzène
Monoéthanol- amine
Naphténate de cobalt
Nitrométhane
Oxyde de carbone
Oxyde de glycidyle et de butyle
Oxyde de glycidyle et de crésyle
Oxyde de glycidyle et de phényle n-Pentane
Produits
Méthylène bis
(o-chloraniline)
(MOCA)
Méthyléthylcétone
(MEC)
Méthylglycol
Températures d’ébullition ou de fusion en °C
Points d’éclair coupelle fermée en °C
Fus.
99-107
Eb.
80
Eb.
124
Eb.
116
Eb.
202
Eb.
132
Eb.
170
- 6
41
16
95
24-29
93
(C.O.)
Perchloréthylène
Eb.
101
Gaz
Eb.
164
Eb.
245
Eb.
36
Eb.
121
35
121
< - 40
Non infl am.
Limites d’explosivité en volume % dans l’air inf.
1,8
1,4
1,3 voir cobalt
7,3
12,5
1,5 sup.
11,5
7,5
7,1
74,2
7,8
Peroxydes
Se reporter au chapitre
« Catalyseurs » pour les risques d’explosions
1,5 Phénol p-Phénylène diamine
Phosgène
Phosphate de tributyle
182
267
Gaz
Eb.
293
79
155
146
(C.O.)
Fiche toxicologique
INRS n°
14
103
56
213
23
146
210
47
29
33
50
15
72
211
CARACTÉRISTIQUES DE DIVERS PRODUITS ENTRANT DANS LA COMPOSITION DES
MATIÈRES PLASTIQUES OU POUVANT SE DÉGAGER LORS DE LA MISE EN ŒUVRE
OU EN CAS DE DÉGRADATION THERMIQUE
Produits
Températures d’ébullition ou de fusion en °C
Phosphate de tricrésyle commercial
(TCP) (mélange des 3 isomères o, m, p)
Phosphate de triphényle (TPP)
Phtalate de diallyle
Phtalate de dibutyle (DBP)
Phtalate de diéthyle (DEP)
Phtalate de diméthyle (DMP)
Phtalate de dioctyle (DOP)
Plomb
(composés du) mais non les dérivés alkylés
Eb.
> 400
Solvant naphta
Styrène
Sulfate de diméthyle
Sulfure de carbone
Tétrachlorure de carbone
Tétrahydrofuranne
(THF)
Thiourée
Titane (oxyde de)
Intervalle de distillation
140-210
Eb.
146
Fus.
32
Eb.
189
Eb.
46
Eb.
76
Eb.
64-66
Fus.
177
Fus.
1 860
(décomp.)
111 Toluène
1,1,1-
Trichloréthane
74
Eb.
302
Eb.
282
Eb.
385
Fus.
48
Eb.
157
Eb.
340
Points d’éclair coupelle fermée en °C
230-250
220
165
171
(C.O.)
162
146
218
(C.O.)
30-60
31
83
- 30 non infl am.
- 17
4 non infl am.
212
Limites d’explosivité en volume % dans l’air inf.
sup.
Fiche toxicologique
INRS n°
1
1,1
1,25
2,3
1,3
6
6,1
50
11,8
7
44
98
161
59
106
2
78
12
8
42
74
26
CARACTÉRISTIQUES DE DIVERS PRODUITS ENTRANT DANS LA COMPOSITION DES
MATIÈRES PLASTIQUES OU POUVANT SE DÉGAGER LORS DE LA MISE EN ŒUVRE
OU EN CAS DE DÉGRADATION THERMIQUE
Produits
Trichloréthylène
Trichlorobenzène technique
Températures d’ébullition ou de fusion en °C
Eb.
87
Intervalle de distillation
205-220
Trichlofl uorométhane (F11)
Triéthanolamine
Triéthylamine
Triéthylène tétramine
Eb.
23,8
Eb.
360 (décomp.)
Eb.
89
Eb.
278
Urée
White-spirit
Fus.
132
Intervalle de distillation
135-205 o, m, p-Xylène 138-144
Zinc (composés du)
Points d’éclair coupelle fermée en °C non infl am.
100 non infl am.
180
- 7
(C.O.)
135
30-65
25-30
2,5
1,2
1,1
1
Limites d’explosivité en volume % dans l’air inf.
sup.
6,6
7,9
6,5
6-7
22
151
136
148
115
94
77
75
Fiche toxicologique
INRS n°
213
D. INDEX ALPHABÉTIQUE
DES NOMS COMMERCIAUX
(à titre indicatif)
INDEX ALPHABÉTIQUE DES NOMS COMMERCIAUX
Noms commerciaux Pages Noms commerciaux Pages Noms commerciaux
AETERNAFORM
AETERNALEN PE
AETERNALEN PP
AETERNAMID
AETERNAPHEN
AETERNAPOL
AETERNYROL
AFCOLAC C
AFCOLENE
AFCOLENE E
AFCORYL
AIRFOAM
AKULON
ALATHON
ALATHON EVA
ALBERTOL
ALCALINOX
ALCIVER
ALCOTEX
ALCREA
ABLAPHENE
ABSACON
ABSON
ACELE
ACELOID
ACÉTAT
ACÉTAVER
ACÉTOPHANE
AC PE
ACRILAN
ACRONAL
ACRYBEL
ACRYLITE
ACRYTEX
ADIPRÈNE
AERODUX
AEROPHEN
AETERNABON
AETERNACRYL
ALFTALAT
ALGOFLON
ALKATHENE
ALKYDAL
ALKYNOL
ALNOVOL
ALPOLIT
ALTENAL
ALTUCHOC
ALTUFIX
ALTUGLAS
ALTULEX
ALTULITE
ALVEOFLEX
ALVEOPHEN
ALVYL
AMBROLITHE
AMBYLENE
AMBYRENE
45
160
160
45
84
78
99
45
62
177
138
45
50
99
148
120
78
69
78
78
96
193
160
160
96
90
96
90
107
84
160
84
84
110
110
110
138
110
45
90
107
90
192
160
62
160
45
78
177
124
45
177
177
160
153
153
84
90
AZOLONE
BAKELITE
BALIPOR
BAREX
BAYDUR
BAYFILL
BAYFIT
BAYLON
BAYMER
BAYMID
BAYTEC
BAYTHERM
BECKACITE
BECKADUR
BECKAMINE
BECKOPOX
BECKOSOL
BECKUROL
BEETLE MF
BEETLE UF
A.M.C.
AMINOCEL
AMINOLAC M
AMINOLAC UF
AMPAGLAS
AQUAREX
ARALDITE
ARDYLAN
ARGUTAN
ARNITEL
ARNITE PETP et PBTP
ARTEVYL
ASTREL
ATLAC
ATLAS
ATPOL
AVICAR
AVI-SUN
BENVIC
BERMODOL
BLENDEX
BLENDEX MBS
BRALEN
BRAX
BREON
BREON CS
BULITOL
BUTACITE
BUTAVER
BUTOFAN
BUTVAR
CALEPPIOFILM
CAPRAN
CAPRINYL
CAPROLAN
CARADATE
CARADOL
177
167
172
167
84
90
180
45
192
120
CELLON
CELLONEX
CELLUFILM
CELLULOID
CELMAR
CELON
CELORON
CESTIDUR
CESTILITE
CHEMASBESTO
CHEMPLEX
CIBAMIDE MF
CIBAMINE UF
CIBANOIDE
CIPONYL
CIPOVIOL
CIPSARENE
CIRES
CLARIFOIL
CODIX
CARBAVER
CARBON
CARGIL
CARIFLEX TR
CARINA
CARINEX
CARLONA
CARLONA P
CASCOPHEN
CASCO-RÉSINE
CAURITE
CEGEITE
CÉGEMIX
CELANAR
CELCON
CÉLÈNE
CELLIDOR, A,
S, U
CELLOBOND
COLUMBIAN
CORVIC
COSDEN
COURTELLE
CRASTIN
CRESLAN
CRILAT
CRIOBEX
CRYLOR
CRYSTIC
CYANAPRENE
CYCOLAC
CYOLON
DACRON
DAIFLOIL
DAIFLON
DALTOCAST
DALTOCEL
DALTOFLEX
54
192
84
84
45
62
54
69
160
74
192
192
177
192
167
180
177
167
172
167
84
78
74
110
99
54
99
192
192
160
160
78
96
192
192
192
45
192
188
120
54
142
153
90
192
78
50
Pages
167
167
160
153
120
138
45
107
45
177
84
54
78
45
50
160
110
153, 160
110
110
110
115
50
99
160
45
45
167
45
172
167
167
99
62
45
45
110
50
193
84
84
120
130
130
192
192
192
54
78
96
120
96
90
78
96
153
217
Noms commerciaux
DUNLOPREN
DURACON
DURETHAN B,
A, C
DURETHAN U
DUREZ
DUROPHEN
DURVINYL
DUTRAL TP
DYFLOR 2000
DYLAN
DYLENE
E275
ECCOMOLD
ECCOSIL
EDIMET
EDISTIR
EXAMERE
EKANATE
EKAVYL
EKTAR PCT E
ELAP
ELOTEX PAE
ELTEX
ELTEX P
ELVACITE
ELVANOL
ELVAX
DALTOLAC
DALTOMOLD
DALTOROL
DAPLEN
DAPON
DEGADUR
DEGALAN
DEGLAS
DEHOPLAST
DELRIN
DERAKANE
DEROTON
DESMOCOLL
DESMODUR
DESMOPAN
DESMOPHEN
DEWOGAN
DEXEL
DIAKON
DIKARYL
DIOFAN
DIOLEN
DISTRENE
DORLYL
DOW ABS
DOW CORNING
FLUIDS
DOW DEH.
DOW DEN
DOW DER
DOW-PE
DRALON
218
200
180
180
180
45
96
192
138
78
192
192
54
120
192
62
45
50
90
62
45
99
192
167
167
54
50
134
45
78
193
180
200
90
Pages
45
138
153
120
192
192
193
192
192
193
192
50
153
90
90
90
90
110
90
84
69
120
78
54
84
Noms commerciaux
ESTYPRENE
ESTYPRO
ESTYSAN
ETHYVER
EUREPOX
EUROPHEN
EUROPOL
EUROPRÈNE
SOL. T
EVAFLEX
EVATANE
EVATATE
EXLANSOR
EXTIR
EXTRULAM
FABELNYL
FATURAN
FELOR
FENOCHEM
FENOLIK
FENYL
FERTENE
FIBERITE
FLAMOLIN
FLEXOROB
FLEXOTHANNE
FLUON
FLUOROLUBE
ERTALENE PP
ERTALON
ERTALYTE
ERTAPHENYL
ERVADUR
ERVAMINE
ERVAPHENE
ESCORENE
PE bd
ESCORENE
Ultra
ESSENE
ESTAL
ESTANE
ESTOLABS
ESTYLENE
EMULSITE
ENJAY
ENKALON
EPIKOTE
EPIPHEN
EPOCAST
EPOK
EPOK V
EPON
EPONAL
EPONOL
EPOSIR
ERACLENE
ERTACETAL
ERTAFLUOR
ERTALENE
45
45
192
193
84
45
78
50
84
45
180
160
192
160
99
160
160
160
45
160
45
192
192
124
130
78
78
50
99
84
45
45
45
Pages
180
180
180
180
45
138
124
45
160
45
99
180
180
180
160
65
50
99
120
148
160
172
160
45
Noms commerciaux
HALON
HOSTAFLON
HOSTAFORM
HOSTALEN G, LD
HOSTALEN PP
HOSTALIT
HOSTAPHAN
HOSTAPOR
HOSTYREN
HYDEX
HYGROMULL
HYLÈNE
HYTREL
IMIDAL
IMPOLEX
ISOMIN
ISONATE
ISOROB
ISOTHANNE
IXAN
IXOL
JECTOTHANE
KAPRONET
KAPTON
KAURIT
KELANEX
KEL F
KELTAR TP
GEDEX
GEDEXAL
GELVATOL
GEON
GEON 200
GERGLASS
GERPALON
GLASSESTER
GLENDION
GLYALKYDE
GLYPTAL
GLOHSENOL
GRILAMID
GRILON
HALAR
HALOCARBON
FLUOROTHENE
FLUOSITE
FORAFLON
FORMALDAFIL
FORMREZ
FORMVAR
FORTIFLEX
FREQUENCITE
FTORLON 3
FTORLON 4
GABRASTER
GABRITE
GAFLON
GARBEL
GEDELITE
GEDEVYL
Pages
192
192
192
69
192
193
84
188
167
120
130
50
78
54
167
192
120
188
153
172
124
124
138
45
50
54
120
78
192
177
177
62
99
99
130
130
69
90
107
120
78
78
62
54
130
124
153
167
124
54
160
54
130
160
134
138
192
74
45
160
Noms commerciaux
MERAKLON
MERAKRIN
MERLON
METACRYLENE BS
MINLON
MIRASON
MIRATHEN
MO-DO
MOLDESITE
MOLTOPREN
MONOCAST
MONOCOLLE
MONSANTO PE
MONTOPORE
MOPLEN
MOPLEN RO
MOWILITH
MOWIOL
MOWITAL B
MYLAR
NABUTENE
NACCONATE
NACROLAQUE
NAPIOL
NAPRYL
NATENE
NAXELLOSE
NAXOID
MELALIT
MELAMITE
MELASBESTO
MELBRITE
MELINEX
MELIT
MELMEX
MELOCHEM
MELOCOL MF
MELOCOL UF
MELOLAM
MELOPAS
MEL-RON
MELSIR
MELSPREA
MELWIT E
LURAN
LUREX
LURON
LUSTRAN A
LUSTRAN I
LUSTREX
LUVIPREN
MAERSK
MAKRISOL
MAKROLON
MANOLENE
MARANYL
MARLEX
MARLEX MG 400
MARSIPOL
MAURYLENE
Pages
54
110
90
45
90
54
54
54
45
192
192
90
180
107
192
96
180
78
84
45
138
50
45
107
96
153
180
45
145
192
120
84
84
78
142
99
134
78
45
50
54
172
148
90
120
90
84
84
84
54
96
153
138
188
153
160
188
84
192
193
Noms commerciaux
LATAN
LATENE
LATENE HD
LATILON
LEACRIL
LEGUVAL
LEKUTHERM
LEVAPREN
LEVEPOX
LEXAN
LILENE
LOPAC
LOPOX
LORKALENE
LORKARIL
LOTRENE
LUCITE
LUCOLENE
LUCOMIX
LUCOREX
LUCOVYL
LUMALINE
LUMIPLAN
LUPOLEN
LUPOLEN V
LUPRANAT
LUPRANOL
LUPRENAL
KYNAR
LACQRENE
LACQTENE
LACQTENE P
LACQVYL
LAMELITE
LARIL
LARODUR
LARTON
LASTANE
LASTER
LASTIL
LASTILAC
LASTIROL
LASULF
LATAMID
KEMATAL
KERIMID
KERIPOL
KERIT
KINEL
KLEGISAB
KLEMOCELL
KLETHERCELL
KODAR
KORAD
KOSTIL
KRALASTIC
KRATON
KRENE
KRILIUM
KRYSTON
Noms commerciaux
NYLON
NYLSENE
NYLTEST
OBTEL
OFALENE
OKITEN
OPALON
ORGALAN
ORGAMIDE R
ORGASSAN
ORGATER
ORLON
OROGLAS
PALATAL
PANTILE
PAPELAC
PAPI
PARAGLAS
PARAPLEX
PAS-POLY-
ETHYLENE
PEG
PELASPAN
PELLETHANE
PERLON L
PERLON N
PERSPEX
PES
NORSODYNE
NORSOLYDE
NORSOMIX
NORSOPHEN
NORSOPLAST
NORSORAU
NORYL
NOVADUR
NOVATEC
NOVATRON
NOVODUR
NOVOID
NOVOLEN
NUC-PE
NYLATRON
NYLFRANCE
NAXOL
NAXOLITE
NEOKARIL
NERTRIL
NESTORITE
NIAX
NICABEL
NIPOFLEX
NIPOLON
NOBEPHENE
NOGELITE
NOLIMID
NOMELLE
NOMEX
NORCHEM
NORDEL TP
Pages
65
62
74
120
84
192
110
192
50
45
115
110
160
193
99
167
45
78
50
45
50
50
107
84
99
45
45
192
172
167
172
172
172
172
172
172
172
172
172
172
120
172
172
172
107
107
45
99
45
50
192
50
84
120
99
84
84
78
192
45
Pages
45
192
84
115
50
45
99
99
153
177
153
160
45
84
148
192
45
160
153
188
96
99
45
50
177
110
84
193
160
192
115
45
99
99
120
96
90
153
107
160
45
45
124
107
99
99
99
99
192
90
153
45
45
78
193
99
99
90
142
219
Noms commerciaux
POLNAC
POLYANE
POLYANYL
POLYCARBAFIL
POLYDROX
POLYFAN
POLYFLEX
POLYFLON
POLYLEN
POLYLITE
POLYPENCO PTFE
POLYPHEN
POLYSTYROL
POLYTHENE
POLYVIOL
PRESSAMINE
PRESTER
PRODILAN
PROFAX
PROGILITE
PROPATHENE
PROPYLAN
PROPYLEN
PROPYVER
PROTESINE
PROTESINE-ZOURON
PRYLENE
PRYSTALINE
PLASTOID
PLASTONEIGE
PLASTOPAL
PLASTYRYL
PLEXIDUR
PLEXIGLAS
PLURACOL
PLYOPHEN
POCAN
POKALON
POLIDENE
POLIMUL
POLINA
POLISOL
POLITAN
POLLOPAS S
PETEN
PETERGLAS
PETERLITE
PETILEN
PETROTHENE
PEVALON
PHENARON
PHENEXPAN
PHENOREZ
PHENOSTRAT
PHENYVER
PIBITER
PIOLOFORM B
PIOLOFORM F
PLASKON CTFE
PLASKON FR PP
220
Noms commerciaux
PYRALEN
QUADROL
QUIRVYL
RAVIKRAL
REDUX
RENYL
RESARIT
RESART
RESUFIN
RESURFENE
REVYL B
REVYL F
REVYLOL
REYNOLON
REXENE
REXLON
RHENOSTYROL
RHIAMER PP
RHODANITE
RHODEFTAL
RHODESTER
RHODEX
RHODIALINE
RHODIALITE
RHODIALON
RHODOID
RESARTGLAS
RESART MPV
RESCOVIN
RESIACRIL
RESIAL
RESICART MF
RESICART UF
RESINA UF
RESIN M 33
RESINOL
RESINOPLAST
RESMELIN
RESOCEL
RESOPHENE
RESPOL
RESTICEL
RESTIL
RESTIRAN
RESTIROLO
RHODOPAS
RHODOPHANE
RHODORSIL
RHODOVIOL
RHOPTIX
RHOVINAL B
RHOVINAL F
RIBLENE
RILFORM
RILSAN A
RILSAN B
RIMTHANE
ROBEX
Pages
153
99
50
160
50
192
50
50
172
167
50
167
192
153
124
192
78
45
62
167
153
45
99
107
180
192
78
124
120
107
69
65
192
78
192
167
96
167
167
78
90
90
192
160
160
160
148
120
74
74
130
50
45
62
160
160
45
90
90
45
Pages
188
192
54
84
160
99
90
{
160
172
78
50
110
188
120
110
110
110
99
167
160
74
74
62
62
45
45
188
160
54
172
160
160
153
78
84
84
78
90
153
65
96
177
172
167
167
{
110
54
65
110
200
62
110
74
74
45
99
99
99
192
78
Noms commerciaux
ROCKITE
RONFALIN
ROOFMATE
ROPOL
ROPOTEN
ROSKYDAL
ROTANE
ROTSTYL
ROUTALKYD
ROUTANATE
ROUTANOL
ROYALEX
ROYLAR
RUMITEN
RUTAFORM
RUTAPOX
RYNITE
RYTON PPS
SABEX
SARAN
SARNYLENE
SCARAB
SCLAIR
SCOTCHCAST
SCOTCH KOTE
SCOTCHPAK
SCOTCHWELD
SCURADEZ
SCURAFLEX
SCURANATE
SCURANE
SCURANOL
SCURATAN
SETACEGEITE
SETAROL
SETILITHE
SHINKOLITE A
SHOLEX
SICALIT
SICALYD
SICOFLEX ABS
SICOFLEX MBS
SICOSTIROL
SICRON
SILASTÈNE
SILASTIC
SILECTO
SILIRITE
SILITROLITE
SIMONA PE
SINVET
SIRALKYD
SIRESTER
SIRFEN
SIRIT
SIRITLE
SIRMASSE
SIRMINOL MF
Pages
{
177
192
192
84
193
45
160
172
160
84
78
45
45
153
192
192
180
120
145
84
69
54
167
45
{
180
192
107
177
153
160
167
167
153
172
84
84
78
54
200
200
200
200
180
45
192
160
153
110
90
45
110
177
180
120
180
120
192
192
192
192
Noms commerciaux
STARPHENYL
STARPYLEN
STARSULFIDE
STARSULFONE
STERLAC
STERNITE
STERPON
STERVYL
STRATO
STRATYL
STYCAST
STYLAC
STYPAC (ABS)
STYPAC PS
STYPOL
STYRABIL
STYRACON
STYRAFIL
STYRANEX
STYRANIL
STYRAVER
STYROCELL
STYROFLEX
STYROFOAM
STYROMAT
STYRON
STYROPOR
STYVACRIL
SOLUPHENE
SOLVIC
SORANE
SOREFLON
SPRIGEL
STAFLENE
STAMYLAN
STAMYLAN P
STARABS
STARAMIDE
STARASAN
STARASTYR
STARBONATE
STARESTER
STARETAL
STARETEN
SIRMINOL UF
SIRPOL
SIRTENE
SIRTENE P
SKANOPAL
SKYBOND
SNIAMID
SNIATRON
SNIAVITRID
SOCARYL
SOCARENE
SODETHANE
SOLAPRENE
SOLEF
SOLOMBREX
SOLPRENE
Noms commerciaux
STYVARENE
SULFIVER
SULFOVER
SUMIKATHENE
SUPER BECKACITE
SUPRALEN
SUPRANE
SUPRAPLAST
TENITE PET et PBT
TENITE PP
TERCAROL
TERENAL
TERGAL
TERITAL
TERLURAN
TERPHANE
TETRAFLON
TEXAS
TEXEL
TEXICOTE
TEXICRYL
TEXIN
TOLONATE
SUPRASEC
SUPRONYL
SURFIL
SYNOLITE
SYNRESATE
SYNRESINE MF
SYNRESINE UF
SYNRESITE
SYNRESOL
SYNRESYL
TECHNOPHEN
TECHNYL
TEDIMON
TEFANYL
TEFLON
TEFZEL
TELCAR
TEINTE Acétate
TENITE PE
TORLON
TOROLITHE
TOROMIX
TOTAL VESTOLEN
TPR
TRANSPREX
TRESPAPHAN
TREVIRA
TRIAFOL
TRIALITHE
TROGAMID T
TROLITAN
TROLITUL
TRONAL
TROSIPLAST
TUBICETA
Pages
78
78
78
78
78
78
78
78
78
78
78
84
84
153
180
84
84
78
153
84
148
50
145
142
153
78
153
54
107
120
138
45
84
99
84
78
160
54
192
124
153
45
45
50
99
84
78
192
62
134
110
84
167
65
45
50
167
188
99
153
50
90
50
120
110
110
99
160
78
84
54
110
124
193
110
65
90
193
192
188
153
153
45
120
50
192
188
120
120
84
120
Pages
78
145
142
45
160
45
45
{
160
172
160
65
160
99
192
54
124
124
50
110
45
192
99
142
153
177
172
167
153
Noms commerciaux
URANOX
URATHIX
URAVAR
UROCHEM
UROPLAS
URTAL
VALOX
VARCUM
VARLAN
VEDRIL
VEDRILENE
VELICREN
VENTENE
VERAMIDE
VEREPOX
VERSAMID
VERSAN
VESPEL
VESTAMID
VESTODUR
A ET B
VESTOLEN A
VESTOLEN P
VESTOLIT
VESTOPAL
VESTOPREN TP
VESTORAN
VESTYPOR
TYRIL
UBE
UCECOAT
UDEL
UFORMITE
UGIKADIOL
UGIKAPON
UGIKRAL
UGIPOL
ULSTRON
ULTRADUR
ULTRAFORM
ULTRAMID A
ULTRAMID B
ULTRAMID S
ULTRAPAS MF
ULTRAPAS UF
ULTRAPHAN
ULTRATHENE
ULTRYL
URADIL
URADUR
URAFLEX
URAFLO
URAFOAM
URALAC
URALAM
URALITE MF
URALITE UF
URAMEX MF
URAMEX UF
Pages
153
193
177
153
172
167
172
167
172
167
107
45
54
177
192
193
84
192
50
120
138
99
99
99
84
45
192
142
167
153
153
50
99
180
99
54
90
90
96
180
177
160
167
167
84
120
160
84
188
99
120
45
50
54
153
50
84
78
221
Noms commerciaux
VESTYRON
VIBRIN
VICLAN
VIDÈNE
VINAMULL
VINAROL
VINATEX
VINAVIL
VINAVILOL
VINNAPAS
VINNOL
VINOFLEX
Pages
78
153
69
120
65
62
54
65
62
65
54
54
Noms commerciaux
VINCHLORE
VINYDUR
VINYLITE
VINYLON
VIPLA
VISTAFLEX
VITREDIL
VITROSIL
VIXIR
VOLTALEF
VONDAFOL CA
VORANOL
Pages
54
50
90
54
54
54
62
160
54
130
110
192
Noms commerciaux
VULKOLLAN
VYNCOLITE
WALOMID
WALOTHEN
WEFAPRESS 1 000
X CEL
XYLOK
YUKALON
ZEFRAN
ZOL
ZYTEL
Pages
193
160
99
50
45
110
160
45
96
167
99
222
E. BIBLIOGRAPHIE
[1] Guide des matières plastiques en mécanique, Cetim Batelle, 1976.
[2] REYNE M. – Les plastiques, Guide pratique de l’utilisateur, CFE, France, 1974.
[3] LEFAUX R. – Chimie et toxicologie des matières plastiques, Paris, Compagnie française d’édition, 1964
[4] BEAUDOUIN L. – Les matières plastiques dans l’industrie, document non publié.
1972.
1964.
York, Elsevier scientifi c publishing company, 1975.
[8] Les plastiques et le feu, GPCP, Compagnie française d’éditions, Paris, 1976.
[9] JOUSSET – Matières plastiques, Paris, Dunod, 1968.
[10] DUBOIS P. – Plastiques modernes, Paris, Masson, 1968.
ITI, Tokyo, 1976.
[12] PLASTIQUES A9, Techniques de l’ingénieur, Paris, 1985.
techniques associées, 1972.
[14] Plastiques modernes et élastomères, Mémento, Paris, 1979-1980.
[15] France plastiques, Annuaire offi ciel des plastiques, 1979-1980.
[16] Prévention et protection incendie, tome 4, Paris, Entreprise moderne d’édition, 1972.
[17] Médecine hygiène et sécurité du travail, Genève, BIT, 1973.
1071-88-77.
Company, 1977.
1959.
PLAST – Union Nationale pour la promotion des Produits et Industries Plastiques.
ministère des Armées, juin 1967.
[23] DELORME W.J. – Dictionnaire des matières plastiques, Paris, éd. Emphora.
[24] HILADO C. – Flammability handbook for plastics, Technomic Stamford, 1969.
[25] Les plastiques. Cahiers de médecine interprofessionnelle, 2 e
et 3 e
trimestre 1972, ACMS.
Brandschutz, Allemagne, 1968, vol. 22, n° 3, pp57-64, trad. INRS, n° 121 A-69.
[27] PATTY F.A. – Industrial hygiene and toxicology, New York, Londres, Interscience Publishers,
1982, vol. II.
[28] PATTY F.A. – Industrial hygiene and toxicology, New York, John Wiley, 1980, volume I.
Reinhold Company, 1984.
processing of plastics, New York, Londres, Elsevier Publishing Company, 1964.
[31] Registry of toxic effects of chemical substances NIOSH, 1982.
publishers, 1968.
Cahiers de notes documentaires n° 95, note n° 1181-95-79.
[34] Fiches toxicologiques INRS, édition révisée, 1980.
[35] FOUSSEREAU et BENEZRA CI. – Eczémas allergiques professionnels, Paris, 1970, Masson.
1975.
fonderie – Nuisance d’ordre chimique – Cahiers de notes documentaires n° 96, note n° 1200-
96-79.
norme NF T 50-050, octobre 1974.
Congress, Cincinnati, Ohio, 1977.
225
n° 1159-94-79.
diphénylméthane – Cahiers de notes documentaires n° 72, note n° 853-72-73.
1979.
Cahiers de notes documentaires n° 72, note n° 857-72-73.
[44] Prévention et lutte contre le feu. Édition INRS n° 310, juin 1985.
Plastiques, avril 1976, n° 559, pp. 37-39.
documentaires n° 93, note n° 1141-93-78.
note n° 958-79-75.
l’usage des services de prévention des Caisses régionales d’assurance maladie.
[49] GRANT M.W. – The Toxicology of the eye, C. Thomas, USA, 1974.
plastiques techniques : polyamide, polycarbonate, polyoxyphénylène (280 °C) et polyacétal
(190 °C). compte rendu d’analyse n° 774/CT, juillet 1979. Document INRS non publié à l’usage des services prévention des CRAM.
ABS vers 250°C. Rapport INRS 492/RE, janvier 1980.
poudre ABS. Rapport interne INRS n° 490/RI.
de mise en œuvre. Compte rendu de mesures n° 700/CT, sept. 78. Document INRS, non publié, à l’usage des services prévention des CRAM.
n° 670/CT, mai 1978. Document INRS non publié à l’usage des services prévention des
CRAM.
alimentaire. Compte rendu de mesures n° 669 CT, janvier 1978. Document INRS, non publié,
à l’usage des services prévention des CRAM.
Melt ». Compte rendu de mesures n° 701/CT, septembre 1978. Document INRS non publié, à l’usage des services prévention des CRAM.
Compte rendu de mesures n° 756/CT, mai 1979. Document INRS non publié à l’usage des services prévention des CRAM.
plastiques n° 591, mai 1979, pp. 61-64.
textile. Note scientifi que et technique de l’INRS, n° 11, mars 1977.
[60] RICHARD S. – L’ignifugation dans l’industrie. Rapport interne INRS n° 232/RI, avril 1976.
n° 1218-97-79 et 1227-98-80.
[62] s 449 et 450, juillet
1974 et février 1976.
1962.
[65] L’électricité statique. Édition INRS n° 507, mai 1984.
plastiques. Rapport INRS, n° 339/RE, octobre 1977.
Risque n° 151, mars 1979.
plastiques. Annales pharmaceutiques françaises, 1977, 35, n° 5-6, p. 153-159.
n° 591, mai 1979, p. 96-98.
[70] Les extincteurs mobiles. Édition INRS n° 380, nouvelle édition en préparation.
d’injection et d’extrusion. Plastiques modernes et élastomères, vol. 25, n° 7, sept. 73,
226
pp. 112-126.
by gas chromatography/Mass spectrometry, Z. Anal Chem. 281 (1976), pp. 23-27.
polypropylene, Fire and materials, déc 1976, vol. 1, n° 4, pp. 160-168.
Polyéthylène. Annales pharmaceutiques françaises, vol. 28, n° 6, juin 1970, pp. 417-423 ; V
Polypropylène, vol. 29, n° 4, août 1976, pp. 259-262.
symposium, 1976, n° 57, pp. 65-71.
cobaye par l’inhalation prolongée de poussières de polychlorure de vinyle au poste de travail.
Medicine del lavoro, Italie, vol. 65, n° 9-10, sept-oct. 1974, pp. 321-342 (traduction INRS n° 5
B-76).
l’industrie des matières plastiques, Arch. Mal. Prof., vol. 35, n° 6, juin 1974, p. 685.
la transformation du chlorure de polyvinyle, Pracovni lékarstyl, Prague, août 1965, vol. 17, n°
6, pp. 257-260.
de ses polymères, recommandation n° 133, Cahiers de notes documentaires n° 90, note n°
1109-90-78.
du PVC, Die Berufsgenossenschalt, n° 1, janvier 1977, pp. 7-13 (traduction INRS n° 39 B-
77).
1 – Polychlorure de vinyle (PVC). Caractérisation d’éventuels composés toxiques volatils.
Annales pharmaceutiques françaises, 1969, 27, n° 2, pp. 97-101.
CRAM Rhône-Alpes, juillet 1975, document non publié.
d’hygiène industrielle. Cahiers de notes documentaires n° 80, note n° 973-80-75.
d’incendie. Cahiers de notes documentaires n° 89, note n° 1080-89-77.
bouteilles plastiques en chlorure de polyvinyle, Arch. Mal. Prof., 1975, 36, pp. 225-241, 315-
327.
de vinyle. Medicinal del lavoro, août-septembre 1970, n° 8-9, pp. 433-436.
note n° 1196-96-79.
combustion et de pyrolyse de matériaux utilisés dans le bâtiment, Arch. Mal. Prof., 1978, 39, n° 1-2, pp. 3-24.
documentaires n° 83, note n° 1012-83-76.
Agency Prepared for the Offi ce of Toxic Substances, DC may 5, 1977, pp. 140-142.
58.
III Polystyrène, Annales pharmaceutiques françaises, vol. 28, n° 1, 1970, pp. 41-48.
[93] Fabrication du polystyrène. Face au risque n° 124, juin 1976, pp. 33-36.
[94] NEUFERT – L’architecture et l’isolation, Paris, Dunod, 1971, pp. 101-117.
n° 87, note n° 1060-87-77.
lapin, RFA., Berufsdermatosen, juin 1971, vol. 19, n° 3, pp. 132-144.
autodurcissante servant au montage de pièces métalliques, RFA, Berufsdermatosen, août
1972, vol. 20, n° 4, pp. 198-199.
Cahiers de médecine interprofessionnelle, vol. 17, n° 65, 1977, pp. 39-42.
and industry, n° 5, juin 1976, pp. 470-474.
[100] MARTIN E.P. – L’infl ammabilité des textiles modernes, traduction INRS 198-A-64, Paris,
227
1964.
[101] CHAIGNEAU M., LE MOAN G. – Étude de la pyrolyse des matériaux en matière plastique : VII
Polyamides, Annales pharmaceutiques françaises, vol. 31, n° 7-8, 1973, pp. 495-501.
[102] Polyamides. Fiche synthèse du CNPP. Face au risque n° 90, février 1973, pp. 47-48.
[103] FERGUSON W., WHEELERD – Caprolactam vapor exposures, Amer. Ind. Hyg. Assoc. Journal, septembre 1973, vol. 34, n° 9, pp. 384-389.
[104] RICHARD S. et MULLER J. – Dégradation thermique sous air de polyamide entre 400 °C et
1 000 °C, rapport INRS 462/RE, mai 1979.
[105] RUSSKIH V.A. – Hygiène du travail et maladies professionnelles dans l’industrie des polymères de polycarbonate, Moscou, Gigiena truda I professional, mars 1973, n° 3, pp. 15-18.
[106] Risques d’incendie et d’explosion présentés par la nitrocellulose, Cahiers de notes
documentaires n° 69, note n° 812-69-72.
[107] Nitrocellulose. Fiche synthèse du CNPP. Face au risque n° 137, novembre 1977, pp. 75-76.
[108] Nitrocellulose. Chemical safety data sheet SD-96, Washington, 1970.
[109] FISHER W. et GHERKE H. – Le polytéréphatalate de butylène, Caoutchoucs et plastiques, mai 1979, n° 591, pp. 57-59.
[110] Les risques au cours du travail du polytétrafl uoréthylène, Travail et sécurité, juillet 1967, n° 7, pp. 332-337.
[111] Occaputional exposure to decomposition products of fl uorocarbon polymers, NIOSH, septembre 1977.
[112] COLEMAN W., and coll. – The particles resulting from polytetrafl uorethylene (PTFE). Pyrolis in air, Am. Ind. Hyg. Ass. Journal, 1968, n° 29, pp. 54-60.
[113] ARITO H. et SODA R. – Pyrolysis products of polytetrafl uorethylene and polyfl uoroethylene propylene with reference to inhalation toxicity, Annals of occupation. Hyg., Grande-Bretagne, décembre 1977, vol. 20, n° 3, pp. 247-255.
[114] PAULET G. – Dangers dans l’industrie du polytétrafl uoréthylène, Arch. Mal. Prof., 1964, t. 25, n° 3, pp. 105-114.
[115] CAVAGNA G. et coll. – Étude expérimentale de la pathogenèse de la fi èvre provoquée par les fumées du téfl on, Medicine del lavoro, 1961, vol. 52, n° 4, pp. 251-261, (traduction INRS n°
122-A-63).
[116] EVANS E. – Pulmonary edema after inhalation of fumes from polytetrafl uorethylene (PFTE).
Journal of Occup. Medec., juillet 1973, vol. 15, n° 7, pp. 599-601.
[117] CARTON B., LIMASSET J.-C., MAIRE C. – Le téfl onnage à chaud, Cahiers de notes
documentaires n° 90, note n° 1097-90-78.
[118] CHAIGNEAU M. – Sur la décomposition thermique du polytétrafl uoréthylène sous vide et en présence d’oxygène, C.R. Académie des Sciences, mai 1971, t. 272, pp. 1639-1642.
[119] BEAUDOUIN L. Les polyacétals. Moulage par injection. Risques et prévention. Cahiers de
notes documentaires n° 85, note n° 1034-85-76.
[120] BALL G., WEISS B., BOETTNER E. – Analysis of the volatile combustion products of polyphenylene oxide plastics, Ann. Arbor., 1969 (Sancar 678-742).
[121] BARBIER J. – Hygiène et sécurité dans la transformation des polyesters renforcés aux fi bres de verre, Travail et sécurité, décembre 1969, pp. 644-654.
[122] BOITEAU H.-L. et ROSSEL-RENAC F. – Étude expérimentale de l’évaporation du styrène au cours de la polymérisation de résines polyesters insaturés, Arch. Mal. Prof., t. 39, janvierfévrier 1978, pp. 52-59.
[123] L’eczéma allergique au cobalt, fi che d’allergologie-dermatologie professionnelle, n° 8, INRS, octobre 1978.
[124] LIMASSET J.-C. et LARDEUX P. – Risques liés à l’inhalation de fi bres minérales synthétiques,
Cahiers de notes documentaires n° 86, note n° 1045-86-77.
[125] MAISONNEUVE J. et LARDEUX P. – Ventilation des locaux et postes de travail. Fabrication de bateaux en matières plastiques. Cahiers de notes documentaires n° 65, note n° 763-65-71.
[126] BOURNE L.-B. et MILNER F.J. – Polyester resin, Hasards British Journal Industrial Medecine,
1963, n° 20, pp. 100-109.
[127] ZIELHUIS R.L. – Problèmes d’hygiène liés à la fabrication des plastiques renforcés, trad.
INRS 188 A-64.
[128] Une cabine atelier pour le travail des stratifi és, tissus de verre, polyesters, Travail et sécurité, février 1972, pp. 94-98.
[129] DE DANI A. – Plastiques renforcés aux fi bres de verre. Eyrolles, Paris, 1966.
[130] MALTEN K.E. – Les résines formaldéhyde de paratertiaire butylphénol et le paratertiaire butylphénol en médecine du travail, Arch. Mal. Prof., avril-mai 1977, vol. 38, n° 4-5, pp. 417-
435.
[131] SCHOENBERG J.B., MITCHELL C.A. – Airway disease caused by phenolic resin exposure,
Arch. of Environm. Health, USA, décembre 1975, vol. 30, n° 12, pp. 574-577.
[132] PIMENTAL J.C. – A granulomatons lung disease produced by bakelite, USA, American review
228
of respiratory disease, décembre 1973, vol. 108, n° 6, pp. 1307-1310.
[133] FOUSSEREAU J. – L’eczéma allergique au formaldéhyde, fi che d’allergologie-dermatologie professionnelle, 1978, n° 14.
[134] Résines époxydiques. Fiche d’allergologie-dermatologie professionnelle, INRS, juin 1976, n° 6.
[135] MEHL J., FUCHS E., FOUSSEREAU J. – Pathologie professionnelle des résines d’époxy,
Arch. Mal. Prof., décembre 1971, vol. 32, n° 12, pp. 713-722.
[136] SARGENT E., MITCHELL C.A. – Respiratory effects of occupational exposure to an epoxy resin system, Arch. Of environmental health, octobre 1976, vol. 31, n° 5, pp. 236-240.
[137] MEHL J. – Manifestations respiratoires dues aux résines epoxy, Arch. Mal. Prof., juillet 1967, t. 28, n° 7-8, pp. 595-600.
[138] GERVAIS P. – L’allergie aux résines polyépoxydes, note documentaire n° 437-39-65, INRS.
[139] NEIMAS M.V. et coll. – The thermal degradation of some epoxy resins, Journal of polymer
science, 1962, vol. 56, pp. 383-389.
[140] THORGEIRSSON A., FERGERT S., MAGNUSSON B. – Allergenicity of epoxy-reactive diluant in the guinea pig., Berufdermatosen, octobre 1975, vol. 23, n° 5, pp. 178-183.
[141] KUT S. – Les questions de sécurité dans l’application des revêtements par poudre, Galvano, mars 1973, vol. 42, n° 431, pp. 261-266.
[142] POUZOLS G. – Les polyimides, Caoutchoucs et plastiques, mai 1979, n° 591, pp. 53-56.
[143] FARHI R. – Études des risques d’accidents du travail et de maladies professionnelles dans la fabrication des mousses polyuréthannes, Cahiers de notes documentaires n° 17, note n° 187-17-59.
[144] BARBIER M. – Risques présentés par la mise en œuvre des mousses de polyuréthanne,
Cahiers de notes documentaires n° 71, n° 839-71-73.
[145] Polyuréthannes, fi che d’allergologie-dermatologie professionnelle, n° 31, 1984, INRS.
[146] CAVELIER C. et coll. – Isocyanates et fonction respiratoire, Cahiers de notes documentaires n° 88, note n° 1068-88-77.
[147] GOUTET P. et PROTOIS J.-C. – Les mousses polyuréthannes. Risques liés à la fabrication et
à la mise en œuvre. Cahiers de notes documentaires n° 98, n° 1226-96-80
[148] ORSINI L. – Peintures et vernis polyuréthannes, EREC, Paris, 1975.
[149] SKIDWARE D.W. and SEWELL PR. – The evolution of toxic gases from heated polymers. III
– Isocyanates products, European Polymer Journal, 1975, vol. 11, n° 2, pp. 139-142.
[150] CHAIGNEAU M. et LE MOAN G. – Étude de la pyrolyse des matériaux en matières plastiques.
VI – Polyuréthannes, Annales pharmaceutiques françaises, 1972, vol. 30, n° 6, pp. 409-414.
[151] STEPNICZKA H.E. – Les mousses de polyuréthannes ignifugées, Information-Chimie, n° 132,
1974, pp. 377-385.
[152] Recommandations pour la manipulation des isocyanates organiques, bulletin d’information
technique International Isocyanate Institute, janvier 1976.
[153] BOULT M.A., NAPIER D.H. – Behaviour of polyurethanne foams under controlled heating, Fire
prevention science and technology, novembre 1972, n° 3, pp. 13-18.
[154] WOLLEY W.D. – The production of free toluylene diisocyaanate from the thermal and thermaloxidative decomposition of fl exible polyurethane foam, Journal fi re fl ammability, 1974, n° 1, p. 259.
[155] GRASSIE N., ZULFIQAR M. – Thermal degradation of polyurethanne from 1,4-butanadiol and methylene bis(4-phenylisocyanate), Journal of polymer science, 1978, vol. 16, pp. 1563-
1674.
[156] MORIKAWA T. – Acrolein, formaldehyde and volatil fatty acids from smoldering combustion,
Journal of combustion toxicology, mai 1976, vol. 3, pp. 135-150.
[157] Norme E 63 600 NF. Machines à injecter pour plastiques et caoutchouc. Prescriptions techniques de sécurité pour la construction des machines.
[158] BEAUDOUIN L. – Les caoutchoucs thermoplastiques. Document non publié.
[159] Le mercure. Prévention de l’hydrargyrisme. Édition INRS n° 546, septembre 1982.
[160] Valeurs limites de concentrations des substances dangereuses dans l’air. Cahiers de notes
documentaires n° 121, note 1555-121-85.
[161] IARC monographs on the evaluation of the carcinogenic risk of chemicals to humans, septembre 1979, vol. 1 à 20, supplement 1.
[162] L’offi ciel du caoutchouc et des plastiques, juillet-août 1979.
[163] LAFOREST J.-C. et MAHIEU J.-C. – Mise en œuvre des polyesters stratifi és. Cahiers de notes
documentaires n° 102, note n° 1305-102-81.
[164] Colorants à base de benzidine, d’o-tolidine et d’o-dianisidine. Risque cancérogène. Cahiers
de notes documentaires n° 104, note n° 1334-104-81.
[165] PINEAU J., GILTAIRE M. et DANGREAUX J. – Suppression des explosions par extincteurs déclenchés. Cahiers de notes documentaires n° 100, note n° 1267-100-80.
[166] MAHIEU J.-C. – Mise en œuvre des mousses polyuréthannes. Cahiers de notes documentaires
229
n° 102, note n° 1304-102-81.
POUR COMMANDER LES FILMS (EN PRÊT), LES BROCHURES ET LES AFFICHES DE L’INRS.
ADRESSEZ-VOUS AU SERVICE PRÉVENTION DE VOTRE CRAM OU CGSS.
SERVICE PRÉVENTION DES CRAM
ALSACE-MOSELLE
(67 Bas Rhin)
14 rue Adolphe-Seyboth
BP 10392
67010 Strasbourg cedex tél. 03 88 14 33 00 – fax 03 88 23 54 13
(57 Moselle)
3 place du Roi-George
BP 31062
57036 Metz cedex 1 tél. 03 87 66 86 22 – fax 03 87 55 98 65
(68 Haut Rhin)
11 avenue De-Lattre-de-Tassigny
BP 70488
68018 Colmar cedex tél. 03 89 21 62 20 – fax 03 89 21 62 21
AQUITAINE
(24 Dordogne, 33 Gironde, 40 Landes,
47 Lot-et-Garonne,
64 Pyrénées-Atlantiques)
80 avenue de la Jallère
33053 Bordeaux cedex tél 05 56 11 64 00 – fax 05 56 39 55 93
AUVERGNE
(03 Allier, 15 Cantal, 43 Haute-Loire,
63 Puy-de-Dôme)
48-50 boulevard Lafayette
63000 Clermont-Ferrand tél. 04 73 42 70 22 – fax 04 73 42 70 15
BOURGOGNE - FRANCHE-COMTÉ
(21 Côte-d’Or, 25 Doubs, 39 Jura,
58 Nièvre, 70 Haute-Saône,
71 Saône-et-Loire, 89 Yonne,
90 Territoire de Belfort)
ZAE Cap-Nord
38 rue de la Carcovie
21044 Dijon cedex tél. 03 80 70 51 22 – fax 03 80 70 51 73
BRETAGNE
(22 Côtes d’Armor, 29 Finistère,
35 Ille et Vilaine, 56 Morbihan)
236 rue de Châteaugiron
35030 RENNES cedex tél. 02 99 26 74 63 – fax 02.99 26 70 48
CENTRE
(18 Cher, 28 Eure-et-Loire, 36 Indre,
37 Indre et Loire, 41 Loir-et-Cher,
45 Loiret)
36 rue Xaintrailles
45033 Orléans cedex 1 tél. 02 38 81 50 00 – fax 02 38 79 70 30
CENTRE OUEST
(16 Charente, 17 Charente-Maritime,
19 Corrèze, 23 Creuse, 79 Deux-Sèvres,
86 Vienne, 87 Haute-Vienne)
4 rue de la Reynie
87048 Limoges cedex tél. 05 55 45 39 04 – fax 05 55 79 00 64
ÎLE-DE-FRANCE
(75 Seine, 77 Seine-et-Marne,
78 Yvelines, 91 Essonne,
92 Hauts-de-Seine,
93 Seine-Saint-Denis, 94 Val-de-Marne,
95 Val-d’Oise)
17 – 19 place de l’Argonne
75019 Paris tél. 01 40 05 32 64 – fax 01 40 05 38 84
LANGUEDOC ROUSSILLON
(11 Aude, 30 Gard, 34 Hérault,
48 Lozère, 66 Pyrénées-Orientales)
29 cours Gambetta
34068 Montpellier cedex 2 tél. 04 67 12 95 55 – fax 04 67 12 95 56
MIDI-PYRÉNÉES
(09 Ariège, 12 Aveyron,
31 Haute-Garonne, 32 Gers, 46 Lot,
65 Hautes-Pyrénées, 81 Tarn,
82 Tarn-et-Garonne)
2 rue Georges-Vivent
31065 Toulouse cedex tél. 05 62 14 29 30 - fax 05 62 14 26 92
230
NORD-EST
(08 Ardennes, 10 Aube, 51 Marne,
52 Haute-Marne,
54 Meurthe-et-Moselle, 55 Meuse,
88 Vosges)
81 à 85 rue de Metz
54073 Nancy cedex tél. 03 83 34 49 02 – fax 03 83 34 48 70
NORD - PICARDIE
(02 Aisne, 59 Nord, 60 Oise,
62 Pas-de-Calais, 80 Somme)
11 allée Vauban
59662 Villeneuve-d’Ascq cedex tél. 03 20 05 60 28 – fax 03 20 05 63 40
NORMANDIE
(14 Calvados, 27 Eure, 50 Manche,
61 Orne, 76 Seine-Maritime)
Avenue du Grand-Cours, 2022 X
76028 Rouen cedex tél. 02 35 03 58 21 – fax 02 35 03 58 29
PAYS DE LA LOIRE
(44 Loire-Atlantique,
49 Maine-et-Loire, 53 Mayenne,
72 Sarthe, 85 Vendée)
2 place de Bretagne
BP 93405, 44034 Nantes cedex 01 tél. 02 51 72 84 00 – fax 02 51 82 31 62
RHÔNE-ALPES
(01 Ain, 07 Ardèche, 26 Drôme,
38 Isère, 42 Loire, 69 Rhône, 73 Savoie,
74 Haute-Savoie)
26 rue d’Aubigny
69436 Lyon cedex 3 tél. 04 72 91 96 96 – fax 04 72 91 97 09
SUD-EST
(04 Alpes-de-Haute-Provence,
05 Hautes-Alpes, 06 Alpes-Maritimes,
13 Bouches-du-Rhône, 2A Corse Sud,
2B Haute-Corse, 83 Var, 84 Vaucluse)
35 rue George
13386 Marseille cedex 5 tél. 04 91 85 85 36 – fax 04 91 85 79 01
SERVICES PRÉVENTION DES CGSS
GUADELOUPE
Immeuble CGRR
Rue Paul-Lacavé
97110 Pointe-à-Pitre tél. 05 90 21 46 00 – fax 05 90 21 46 13
GUYANE
Espace Turenne Radamonthe
Route de Raban, BP 7015
97307 Cayenne cedex tél. 05 94 29 83 04 – fax 05 94 29 83 01
LA RÉUNION
4 boulevard Doret
97405 Saint-Denis cedex tél. 02 62 90 47 00 – fax 02 62 90 47 01
MARTINIQUE
Quartier Place-d’Armes
97232 Le Lamentin, BP 576
97207 Fort-de-France cedex tél. 05 96 66 50 79 – fax 05 96 51 54 00
231
g
L’Institut national de recherche et de sécurité (INRS)
Dans le domaine de la prévention des risques professionnels, l’INRS est un organisme scientifique et technique qui travaille, au plan institutionnel, avec la CNAMTS, les CRAM-CGSS et plus ponctuellement pour les services de l’État ainsi que pour tout autre organisme s’occupant de prévention des risques professionnels.
Il développe un ensemble de savoir-faire pluridisciplinaires qu’il met à la disposition de tous ceux qui, en entreprise, sont chargés de la prévention : chef d’entreprise, médecin du travail,
CHSCT, salariés. Face à la complexité des problèmes, l’Institut dispose de compétences scientifiques, techniques et médicales couvrant une très grande variété de disciplines, toutes au service de la maîtrise des risques professionnels.
Ainsi, l’INRS élabore et diffuse des documents intéressant l’hygiène et la sécurité du travail : publications (périodiques ou non), affiches, audiovisuels, site Internet… Les publications de l’INRS sont distribuées par les CRAM.
Pour les obtenir, adressez-vous au service prévention de la Caisse régionale ou de la Caisse générale de votre circonscription, dont l’adresse est mentionnée en fin de brochure.
L’INRS est une association sans but lucratif (loi 1901) constituée sous l’égide de la CNAMTS et soumise au contrôle financier de l’État.
Géré par un conseil d’administration constitué à parité d’un collège représentant les employeurs et d’un collège représentant les salariés, il est présidé alternativement par un représentant de chacun des deux collèges. Son financement est assuré en quasi- totalité par le Fonds national de prévention des accidents du travail et des maladies professionnelles.
Les Caisses régionales d’assurance maladie (CRAM) etCaisses générales de sécurité sociale (CGSS)
Les Caisses régionales d’assurance maladie et les Caisses générales de sécurité sociale disposent, pour participer
à la diminution des risques professionnels dans leur région, d’un service prévention composé d’ingénieurs-conseils et de contrôleurs de sécurité. Spécifiquement formés aux disciplines de la prévention des risques professionnels et s’appuyant sur l’expérience quotidienne de l’entreprise, ils sont en mesure de conseiller et, sous certaines conditions, de soutenir les acteurs de l’entreprise (direction, médecin du travail,
CHSCT, etc.) dans la mise en œuvre des démarches et outils de prévention les mieux adaptés à chaque situation.
Ils assurent la mise à disposition de tous les documents édités par l’INRS.
Toute représentation ou reproduction intégrale ou partielle faite sans le consentement de l’INRS, de l’auteur ou de ses ayants droit ou ayants cause, est illicite.
Il en est de même pour la traduction, l’adaptation ou la transformation, l’arrangement ou la reproduction, par un art ou un procédé quelconque (article L. 122-4 du code de la propriété intellectuelle).
La violation des droits d’auteur constitue une contrefaçon punie d’un emprisonnement de deux ans et d’une amende de 150 000 euros (article L. 335-2 et suivants du code de la propriété intellectuelle).
© INRS, 2006.
NORD-EST
(08 Ardennes, 10 Aube, 51 Marne,
52 Haute-Marne, 54 Meurthe-et-Moselle,
55 Meuse, 88 Vosges)
81 à 85 rue de Metz
54073 Nancy cedex tél. 03 83 34 49 02 fax 03 83 34 48 70 service.prevention@cram-nordest.fr
NORD-PICARDIE
(02 Aisne, 59 Nord, 60 Oise,
62 Pas-de-Calais, 80 Somme)
11 allée Vauban
59662 Villeneuve-d’Ascq cedex tél. 03 20 05 60 28 fax 03 20 05 63 40 www.cram-nordpicardie.fr
NORMANDIE
(14 Calvados, 27 Eure, 50 Manche,
61 Orne, 76 Seine-Maritime)
Avenue du Grand-Cours, 2022 X
76028 Rouen cedex tél. 02 35 03 58 21 fax 02 35 03 58 29 catherine.lefebvre@cram-normandie.fr
dominique.morice@cram-normandie.fr
PAYS DE LA LOIRE
(44 Loire-Atlantique, 49 Maine-et-Loire,
53 Mayenne, 72 Sarthe, 85 Vendée)
2 place de Bretagne
BP 93405, 44034 Nantes cedex 1 tél. 0 821 100 110 fax 02 51 82 31 62 prevention@cram-pl.fr
RHÔNE-ALPES
(01 Ain, 07 Ardèche, 26 Drôme,
38 Isère, 42 Loire, 69 Rhône,
73 Savoie, 74 Haute-Savoie)
26 rue d’Aubigny
69436 Lyon cedex 3 tél. 04 72 91 96 96 fax 04 72 91 97 09 preventionrp@cramra.fr
SUD-EST
(04 Alpes-de-Haute-Provence,
05 Hautes-Alpes, 06 Alpes-Maritimes,
13 Bouches-du-Rhône, 2A Corse Sud,
2B Haute-Corse, 83 Var, 84 Vaucluse)
35 rue George
13386 Marseille cedex 5 tél. 04 91 85 85 36 fax 04 91 85 75 66 documentation.prevention@cram-sudest.fr
Services prévention des CGSS
GUADELOUPE
Immeuble CGRR
Rue Paul-Lacavé
97110 Pointe-à-Pitre tél. 05 90 21 46 00 fax 05 90 21 46 13 lina.palmont@cgss-guadeloupe.fr
GUYANE
Espace Turenne Radamonthe
Route de Raban, BP 7015
97307 Cayenne cedex tél. 05 94 29 83 04 fax 05 94 29 83 01
LA RÉUNION
4 boulevard Doret
97405 Saint-Denis cedex tél. 02 62 90 47 00 fax 02 62 90 47 01 prevention@cgss-reunion.fr
MARTINIQUE
Quartier Place-d’Armes
97210 Le Lamentin cedex 2 tél. 05 96 66 51 31
05 96 66 51 33 fax 05 96 51 81 54 prevention@cgss-martinique.fr
g
Institut national de recherche et de sécurité pour la prévention des accidents du travail et des maladies professionnelles
30, rue Olivier-Noyer 75680 Paris cedex 14
Fax 01 40 44 30 99
•
Internet : www.inrs.fr
•
•
Tél. 01 40 44 30 00 e-mail : info@inrs.fr
Édition INRS ED 638
3 ème édition
• réimpression octobre 2006
•
1000 ex.
•
ISBN 2-85599-442-X
Matières plastiques
& adjuvants hygiène et sécurité
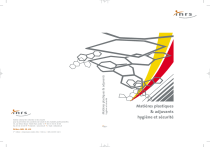
Link público atualizado
O link público para o seu chat foi atualizado.