ESAB iSeries 100i, 200i, 300i, and 400i Plasma Systems Manuel utilisateur
Ajouter à Mes manuels100 Des pages
▼
Scroll to page 2
of
100
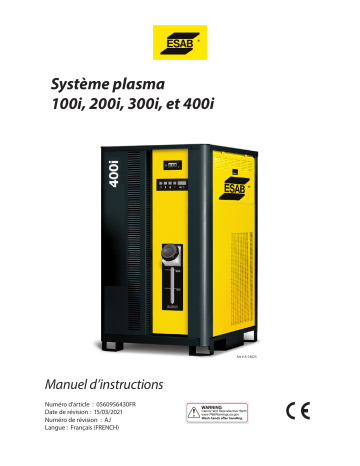
Système plasma 100i, 200i, 300i, et 400i Art # A-14025 Manuel d’instructions Numéro d'article : 0560956430FR Date de révision : 15/03/2021 Numéro de révision : AJ Langue : Français (FRENCH) A-08004FR NOUS APPRÉCIONS VOTRE FIDÉLITÉ ! Félicitations pour l'achat de votre produit ESAB. Nous sommes fiers de vous compter parmi notre clientèle et ferons tout en notre pouvoir pour vous fournir le service le plus fiable et de meilleure qualité dans le domaine. Ce produit est protégé par notre large garantie et notre réseau mondial de service. Pour trouver le distributeur le plus près de chez vous ou un centre de réparation, visiter le site web www.ESAB.com. Ce mode d'emploi a été conçu pour vous indiquer la bonne façon d'utiliser votre produit ESAB. Notre préoccupation principale est votre satisfaction et l'utilisation appropriée du produit. Il est donc important de prendre le temps de lire ce guide en entier, en particulier les Consignes de sécurité. Ceci permet d'éviter les risques possibles liés à l'utilisation du produit. VOUS ÊTES EN BONNE COMPAGNIE ! La marque de choix des entrepreneurs et des fabricants dans le monde entier. ESAB est une marque Internationale de produits de coupage manuel et mécanisés. Nous nous démarquons de nos concurrents grâce à nos produits fiables et d'avant-garde qui ont fait leurs preuves au fil des ans. Nous sommes fiers de nos innovations techniques, nos prix compétitifs, nos délais de livraison hors pair, notre service à la clientèle et notre soutien technique de qualité supérieure, en plus de l'excellence de notre savoir dans le domaine de la vente. Avant tout, nous sommes engagés dans la conception de produits aux technologies innovatrices pour obtenir un environnement de travail plus sûr dans le domaine de la soudure. ! AVERTISSEMENT Lire et comprendre ce Guide au complet et les consignes de sécurité de votre employeur avant l’installation, l’utilisation ou l’entretien de l’équipement. L’information contenue dans ce Guide représente le bon jugement du fabricant, mais celui-ci n’assume aucune responsabilité lors de l’utilisation. Système plasma 100i, 200i, 300i, et 400i Publié par : ESAB Welding and Cutting Products. 2800 Airport Rd. Denton, Texas 76207 www.esab.com © Copyright 2015, 2018, 2021 par ESAB Welding and Cutting Products. MD Tous droits réservés. Il est interdit de reproduire ce document en tout ou en partie sans la permission de l’éditeur. L’éditeur décline toute responsabilité envers les parties en cas de pertes ou de dommages provoqués par une erreur ou une omission figurant dans ce manuel, qu’elle soit le résultat d’une négligence, d’un accident ou d’une autre cause. Date de la publication : 26 février, 2016 Date de révision : 15/03/2021 Conserver les renseignements suivant pour la garantie : Endroit de l’achat : ___________________________________ Date de l’achat :______________________________________ No de série de l’appareil :_______________________________ Numéro de série de la torche :_______________________________________ ASSUREZ-VOUS QUE CETTE INFORMATION EST DISTRIBUÉE À L’OPÉRATEUR. VOUS POUVEZ OBTENIR DES COPIES SUPPLÉMENTAIRES CHEZ VOTRE FOURNISSEUR. MISE EN GARDE Les INSTRUCTIONS suivantes sont destinées aux opérateurs qualifiés seulement. Si vous n’avez pas une connaissance approfondie des principes de fonctionnement et des règles de sécurité pour le soudage à l’arc et l’équipement de coupage, nous vous suggérons de lire notre brochure « Precautions and Safe Practices for Arc Welding, Cutting and Gouging, » Brochure F52-529. Ne permettez PAS aux personnes non qualifiées d’installer, d’opérer ou de faire l’entretien de cet équipement. Ne tentez PAS d’installer ou d’opérer cet équipement avant de lire et de bien comprendre ces instructions. Si vous ne comprenez pas bien les instructions, communiquez avec votre fournisseur pour plus de renseignements. Assurez-vous de lire les Règles de Sécurité avant d’installer ou d’opérer cet équipement. RESPONSABILITÉS DE L’UTILISATEUR Cet équipement opérera conformément à la description contenue dans ce manuel, les étiquettes d’accompagnement et/ou les feuillets d’information si l’équipement est installé, opéré, entretenu et réparé selon les instructions fournies. Vous devez faire une vérification périodique de l’équipement. Ne jamais utiliser un équipement qui ne fonctionne pas bien ou n’est pas bien entretenu. Les pièces qui sont brisées, usées, déformées ou contaminées doivent être remplacées immédiatement. Dans le cas où une réparation ou un remplacement est nécessaire, il est recommandé par le fabricant de faire une demande de conseil de service écrite ou par téléphone chez le Distributeur Autorisé de votre équipement. Cet équipement ou ses pièces ne doivent pas être modifiés sans permission préalable écrite par le fabricant. L’utilisateur de l’équipement sera le seul responsable de toute défaillance résultant d’une utilisation incorrecte, un entretien fautif, des dommages, une réparation incorrecte ou une modification par une personne autre que le fabricant ou un centre de service désigné par le fabricant. ! ASSUREZ-VOUS DE LIRE ET DE COMPRENDRE LE MANUEL D’UTILISATION AVANT D’INSTALLER OU D’OPÉRER L’UNITÉ. PROTÉGEZ-VOUS ET LES AUTRES! DÉCLARATION DE CONFORMITÉ Selon La Directive 2014/35/EU sur la basse tension, entrée en vigueur le 20 avril 2016 La Directive EMC 2014/30/UE, entrée en vigueur le 20 avril 2016 La Directive RoHS 2011/65/UE, entrée en vigueur le 2 janvier 2013 Type d'équipement ALIMENTATION ÉLECTRIQUE SYSTÈME PLASMA Saisissez la désignation etc. Système plasma 100i, 200i, 300i, et 400i, du numéro de série ???? HE800 Radiateurs, À partir du numéro de série MX2113xxxxxx HE400 Radiateurs, À partir du numéro de série MX2113xxxxxx Nom de pain ou marque commerciale ESAB Fabricant ou son mandataire autorisé Nom, adresse, numéro de téléphone : ESAB Group Inc. 2800 Airport Rd Denton TX 76207 Téléphone : +01 800 426 1888, télécopieur +01 603 298 7402 Les normes harmonisées ci-dessous, qui sont en vigueur dans l'EEE, ont été utilisées pour la conception du produit : EN IEC 60974-1:2017 / AMD1:2019 Matériel de soudage à l'arc - Partie 1: Sources de courant de soudage. EN IEC 60974-10:2014 +A1:2015 - Matériel de soudage à l'arc – Partie 10: Exigences de compatibilité électromagnétique (EMC) EN IEC 60974-2:2019 Matériel de soudage à l'arc-Partie 2: Systèmes de refroidissement par liquide Autres informations : Usage restreint, équipement de classe A, conçu pour être utilisé dans des endroits non résidentiels. En signant ce document, le soussigné déclare en tant que fabricant, ou représentant autorisé du fabricant, que l'équipement en question satisfait aux exigences de sécurité énoncées ci-dessus. Date Signature 1 Mars, 2021 John Boisvert 2021 Position Vice-président Coupure Globale Coupure Mécanisée Cette page est intentionnellement laissée vierge. TABLE DES MATIÈRES SECTION 1 : SÉCURITÉ.............................................................................................................. 9 1.01 Précautions de sécurité.......................................................................................................9 SECTION 2 : SPÉCIFICATIONS................................................................................................15 2.01 Description générale du système................................................................................. 15 2.02 Bloc d’alimentation en plasma....................................................................................... 15 2.03 Démarreur à distance de l’arc......................................................................................... 15 2.04 Module de commande de gaz....................................................................................... 15 2.05 Précision Plasma Découpe Torche................................................................................ 15 2.06 Caractéristiques et exigences électriques................................................................. 16 2.07 Dimensions du bloc d’alimentation............................................................................. 18 2.08 Caractéristiques du panneau arrière du bloc d’alimentation............................. 20 2.09 Exigences en matière de gaz.......................................................................................... 21 2.10 Applications de Gaz........................................................................................................... 23 2.11 Spécifications de la torche............................................................................................... 24 SECTION 3: INSTALLATION....................................................................................................27 3.01 Conditions d’installation.................................................................................................. 27 3.02 Disposition du système 100 - 300 Amp ..................................................................... 29 3.03 Disposition du système 400 Amp................................................................................. 30 3.04 Tuyau recommandé pour l’alimentation en gaz..................................................... 30 3.05 Fils et câbles toutes intensités........................................................................................ 31 3.06 Soulevez le bloc d’alimentation.................................................................................... 32 3.07 Installer des pièces consommables de la torche..................................................... 33 SECTION 4 : FONCTIONNEMENT...........................................................................................37 4.01 Détail du panneau alimentation électrique.............................................................. 37 4.02 Système Fonctionnement................................................................................................ 37 4.03 Code d’état CCMs................................................................................................................ 39 4.04 Code d’état de la console de sélection de gaz......................................................... 49 4.05 Codes de l’unité de commande de gaz...................................................................... 51 4.06 Résolution des problèmes du démarreur d’arc à distance.................................. 54 4.06 Résolution des problèmes du démarreur d’arc à distance.................................. 55 SECTION 5 : ENTRETIEN.........................................................................................................57 5.01 Entretien général................................................................................................................ 57 5.02 Procédure de nettoyage du filtre externe du liquide de refroidissement...... 57 5.03 Procédures de remplacement des refroidissement............................................... 58 TABLE DES MATIÈRES SECTION 6 : ASSEMBLAGES ET PIÈCES DE RECHANGE.....................................................59 6.01 Rechange du bloc d’alimentation................................................................................. 59 6.02 Disposition du système 100 - 200 Amp...................................................................... 60 6.03 Disposition du système 300 Amp................................................................................. 60 6.04 Disposition du système 400 Amp................................................................................. 61 6.05 Tuyau recommandé pour l’alimentation en gaz..................................................... 61 6.06 Fils et câbles toutes intensités........................................................................................ 62 6.07 Pièces de rechange externes du bloc d’alimentation............................................ 64 6.08 Pièces de rechange du bloc d’alimentation - Côté supérieur droit.................. 65 6.09 Pièces de rechange du bloc d’alimentation - Côté inférieur droit ................... 66 6.10 Pièces de rechange du bloc d’alimentation - Panneau arrière........................... 67 6.11 Pièces de rechange du bloc d’alimentation - Côté gauche................................. 68 6.12 Système de contrôle automatisé des pièces de remde l’endroit....................... 70 6.13 Pièces de rechange du console de sélection de gaz.............................................. 71 6.14 Pièces de rechange du unité de commande de gaz.............................................. 72 6.15 Pièces de rechange de démarreur d’arc à distance (RAS).................................... 73 SECTION 7 : ENTRETIEN DE LA TORCHE...............................................................................75 7.01 Enlèvement Consommable............................................................................................. 75 7.02 Lubrification du joint torique......................................................................................... 76 7.03 Vêtements de Parties......................................................................................................... 77 7.04 Installation des consommables de la torche............................................................ 78 7.05 Fuite de liquide de refroidissement dépannage .................................................... 80 ANNEXE 1: SCHÉMA DE REFROIDISSEMENT.......................................................................83 ANNEXE 2: SCHÉMA DE PRINCIPE 100 A, 380-415 V PG 1..................................................84 ANNEXE 3: SCHÉMA DE PRINCIPE 100 A, 380-415 V PG 2..................................................86 ANNEXE 4: SCHÉMA DE PRINCIPE 200A, 380-415 V PG 1...................................................88 ANNEXE 5: SCHÉMA DE PRINCIPE 200A, 380-415 V PG 2...................................................90 ANNEXE 6: SCHÉMA DE PRINCIPE 300A, 380-415 V PG 1...................................................92 ANNEXE 7: SCHÉMA DE PRINCIPE 300A, 380-415 V PG 2...................................................94 ANNEXE 8: SCHÉMA DE PRINCIPE 400A, 380-415 V PG 1...................................................96 ANNEXE 9: SCHÉMA DE PRINCIPE 400A, 380-415 V PG 2...................................................98 ANNEXE 10: INTERFACE SCU POUR ISERIES......................................................................100 100i / 200i / 300i / 400i SECTION 1 : SÉCURITÉ AVERTISSEMENT : Ces règles de sécurité ont pour but d’assurer votre protection. Ils récapitulent les informations de précaution provenant des références dans la section des Informations de sécurité supplémentaires. Avant de procéder à l’installation ou d’utiliser l’unité, assurez-vous de lire et de suivre les précautions de sécurité ci-dessous, dans les manuels, les fiches d’information sur la sécurité du matériel et sur les étiquettes, etc. Tout défaut d’observer ces précautions de sécurité peut entraîner des blessures graves ou mortelles. ! PROTÉGEZ-VOUS -- Les processus de soudage, de coupage et de gougeage produisent un niveau de bruit élevé et exige l’emploi d’une protection auditive. L’arc, tout comme le soleil, émet des rayons ultraviolets en plus d’autre rayons qui peuvent causer des blessures à la peau et les yeux. Le métal incandescent peut causer des brûlures. Une formation reliée à l’usage des processus et de l’équipement est essentielle pour prévenir les accidents. Par conséquent : 1. Portez des lunettes protectrices munies d’écrans latéraux lorsque vous êtes dans l’aire de travail, même si vous devez porter un casque de soudeur, un écran facial ou des lunettes étanches. 2. Portez un écran facial muni de verres filtrants et de plaques protectrices appropriées afin de protéger vos yeux, votre visage, votre cou et vos oreilles des étincelles et des rayons de l’arc lors d’une opération ou lorsque vous observez une opération. Avertissez les personnes se trouvant à proximité de ne pas regarder l’arc et de ne pas s’exposer aux rayons de l’arc électrique ou le métal incandescent. 3. Portez des gants ignifugiés à crispin, une chemise épaisse à manches longues, des pantalons sans rebord et des chaussures montantes afin de vous protéger des rayons de l’arc, des étincelles et du métal incandescent, en plus d’un casque de soudeur ou casquette pour protéger vos cheveux. Il est également recommandé de porter un tablier ininflammable afin de vous protéger des étincelles et de la chaleur par rayonnement. 4. Les étincelles et les projections de métal incandescent risquent de se loger dans les manches retroussées, les rebords de pantalons ou les poches. Il est recommandé de garder boutonnés le col et les manches et de porter des vêtements sans poches en avant. 5. Protégez toute personne se trouvant à proximité des étincelles et des rayons de l’arc à l’aide d’un rideau ou d’une cloison ininflammable. 6. Portez des lunettes étanches par dessus vos lunettes de sécurité lors des opérations d’écaillage ou de meulage du laitier. Les écailles de laitier incandescent peuvent être projetées à des distances considérables. Les personnes se trouvant à proximité doivent également porter des lunettes étanches par dessus leur lunettes de sécurité. INCENDIES ET EXPLOSIONS -- La chaleur provenant des flammes ou de l’arc peut provoquer un incendie. Le laitier incandescent ou les étincelles peuvent également provoquer un incendie ou une explosion. Par conséquent : 1. Éloignez suffisamment tous les matériaux combustibles de l’aire de travail et recouvrez les matériaux avec un revêtement protecteur ininflammable. Les matériaux combustibles incluent le bois, les vêtements, la sciure, le gaz et les liquides combustibles, les solvants, les peintures et les revêtements, le papier, etc. 2. Les étincelles et les projections de métal incandescent peuvent tomber dans les fissures dans les planchers ou dans les ouvertures des murs et déclencher un incendie couvant à l’étage inférieur Assurez-vous que ces ouvertures sont bien protégées des étincelles et du métal incandescent. 3. N’exécutez pas de soudure, de coupe ou autre travail à chaud avant d’avoir complètement nettoyé la surface de la pièce à traiter de façon à ce qu’il n’ait aucune substance présente qui pourrait produire des vapeurs inflammables ou toxiques. N’exécutez pas de travail à chaud sur des contenants fermés car ces derniers pourraient exploser. 0560956430FR INSTRUCTIONS DE SÉCURITÉ 9 SÉCURITÉ 1.01 Précautions de sécurité 100i / 200i / 300i / 400i SÉCURITÉ 4. Assurez-vous qu’un équipement d’extinction d’incendie est disponible et prêt à servir, tel qu’un tuyau d’arrosage, un seau d’eau, un seau de sable ou un extincteur portatif. Assurez-vous d’être bien instruit par rapport à l’usage de cet équipement. 5. Assurez-vous de ne pas excéder la capacité de l’équipement. Par exemple, un câble de soudage surchargé peut surchauffer et provoquer un incendie. 6. Une fois les opérations terminées, inspectez l’aire de travail pour assurer qu’aucune étincelle ou projection de métal incandescent ne risque de provoquer un incendie ultérieurement. Employez des guetteurs d’incendie au besoin. 7. Pour obtenir des informations supplémentaires, consultez le NFPA Standard 51B, « Prévention des incendies dans l’utilisation des processus de coupe et de soudage » disponible au National Fire Protection Association, Batterymarch Park, Quincy, MA 02269. CHOC ÉLECTRIQUE -- Le contact avec des pièces électriques ou les pièces de mise à la terre sous tension peut causer des blessures graves ou mortelles. NE PAS utiliser un courant de soudage c.a. dans un endroit humide, en espace restreint ou si un danger de chute se pose. 1. Assurez-vous que le châssis de la source d’alimentation est branché au système de mise à la terre de l’alimentation d’entrée. 2. Branchez la pièce à traiter à une bonne mise de terre électrique. 3. Branchez le câble de masse à la pièce à traiter et assurez une bonne connexion afin d’éviter le risque de choc électrique mortel. 4. Utilisez toujours un équipement correctement entretenu. Remplacez les câbles usés ou endommagés. 5. Veillez à garder votre environnement sec, incluant les vêtements, l’aire de travail, les câbles, le porteélectrode/torche et la source d’alimentation. 6. Assurez-vous que tout votre corps est bien isolé de la pièce à traiter et des pièces de la mise à la terre. 7. Si vous devez effectuer votre travail dans un espace restreint ou humide, ne tenez vous pas directement sur le métal ou sur la terre; tenez-vous sur des planches sèches ou une plate-forme isolée et portez des chaussures à semelles de caoutchouc. 8. Avant de mettre l’équipement sous tension, isolez vos mains avec des gants secs et sans trous. 9. Mettez l’équipement hors tension avant d’enlever vos gants. 10. Consultez ANSI/ASC Standard Z49.1 (listé à la page suivante) pour des recommandations spécifiques concernant les procédures de mise à la terre. Ne pas confondre le câble de masse avec le câble de mise à la terre. CHAMPS ÉLECTRIQUES ET MAGNÉTIQUES — comportent un risque de danger. Le courant électrique qui passe dans n’importe quel conducteur produit des champs électriques et magnétiques localisés. Le soudage et le courant de coupage créent des champs électriques et magnétiques autour des câbles de soudage et l’équipement. Par conséquent : 1. Un soudeur ayant un stimulateur cardiaque doit consulter son médecin avant d’entreprendre une opération de soudage. Les champs électriques et magnétiques peuvent causer des ennuis pour certains stimulateurs cardiaques. 2. L’exposition à des champs électriques et magnétiques peut avoir des effets néfastes inconnus pour la santé. 3. Les soudeurs doivent suivre les procédures suivantes pour minimiser l’exposition aux champs électriques et magnétiques : A. Acheminez l’électrode et les câbles de masse ensemble. Fixez-les à l’aide d’une bande adhésive lorsque possible. B. Ne jamais enrouler la torche ou le câble de masse autour de votre corps. 10 INSTRUCTIONS DE SÉCURITÉ 0560956430FR 100i / 200i / 300i / 400i D. Branchez le câble de masse à la pièce à traiter le plus près possible de la section à souder. E. Veillez à garder la source d’alimentation pour le soudage et les câbles à une distance appropriée de votre corps. LES VAPEURS ET LES GAZ -- peuvent causer un malaise ou des dommages corporels, plus particulièrement dans les espaces restreints. Ne respirez pas les vapeurs et les gaz. Le gaz de protection risque de causer l’asphyxie. Par conséquent : 1. Assurez en permanence une ventilation adéquate dans l’aire de travail en maintenant une ventilation naturelle ou à l’aide de moyens mécanique. N’effectuez jamais de travaux de soudage, de coupage ou de gougeage sur des matériaux tels que l’acier galvanisé, l’acier inoxydable, le cuivre, le zinc, le plomb, le berylliym ou le cadmium en l’absence de moyens mécaniques de ventilation efficaces. Ne respirez pas les vapeurs de ces matériaux. 2. N’effectuez jamais de travaux à proximité d’une opération de dégraissage ou de pulvérisation. Lorsque la chaleur ou le rayonnement de l’arc entre en contact avec les vapeurs d’hydrocarbure chloré, ceci peut déclencher la formation de phosgène ou d’autres gaz irritants, tous extrêmement toxiques. 3. Une irritation momentanée des yeux, du nez ou de la gorge au cours d’une opération indique que la ventilation n’est pas adéquate. Cessez votre travail afin de prendre les mesures nécessaires pour améliorer la ventilation dans l’aire de travail. Ne poursuivez pas l’opération si le malaise persiste. 4. Consultez ANSI/ASC Standard Z49.1 (à la page suivante) pour des recommandations spécifiques concernant la ventilation. 5. AVERTISSEMENT: Ce produitcontient des produits chimiques, notamment du plomb, reconnu par l’Étatde la Californie pour causerdes malformations congénitaleset d’autresdommages touchant le système reproductif. Se laver les mainsaprès manipulation. ! MANIPULATION DES CYLINDRES -- La manipulation d’un cylindre, sans observer les précautions nécessaires, peut produire des fissures et un échappement dangereux des gaz. Une brisure soudaine du cylindre, de la soupape ou du dispositif de surpression peut causer des blessures graves ou mortelles. Par conséquent : 1. Utilisez toujours le gaz prévu pour une opération et le détendeur approprié conçu pour utilisation sur les cylindres de gaz comprimé. N’utilisez jamais d’adaptateur. Maintenez en bon état les tuyaux et les raccords. Observez les instructions d’opération du fabricant pour assembler le détendeur sur un cylindre de gaz comprimé. 2. Fixez les cylindres dans une position verticale, à l’aide d’une chaîne ou une sangle, sur un chariot manuel, un châssis de roulement, un banc, un mur, une colonne ou un support convenable. Ne fixez jamais un cylindre à un poste de travail ou toute autre dispositif faisant partie d’un circuit électrique. 3. Lorsque les cylindres ne servent pas, gardez les soupapes fermées. Si le détendeur n’est pas branché, assurez-vous que le bouchon de protection de la soupape est bien en place. Fixez et déplacez les cylindres à l’aide d’un chariot manuel approprié. Toujours manipuler les cylindres avec soin. 4. Placez les cylindres à une distance appropriée de toute source de chaleur, des étincelles et des flammes. Ne jamais amorcer l’arc sur un cylindre. 5. Pour de l’information supplémentaire, consultez CGA Standard P-1, “Precautions for Safe Handling of Compressed Gases in Cylinders”, mis à votre disposition par le Compressed Gas Association, 1235 Jefferson Davis Highway, Arlington, VA 22202. 0560956430FR INSTRUCTIONS DE SÉCURITÉ 11 SÉCURITÉ C. Ne jamais vous placer entre la torche et les câbles de masse. Acheminez tous les câbles sur le même côté de votre corps. 100i / 200i / 300i / 400i ENTRETIEN DE L’ÉQUIPEMENT -- Un équipement entretenu de façon défectueuse ou inadéquate peut causer des blessures graves ou mortelles. Par conséquent : SÉCURITÉ ! 1. Efforcez-vous de toujours confier les tâches d’installation, de dépannage et d’entretien à un personnel qualifié. N’effectuez aucune réparation électrique à moins d’être qualifié à cet effet. 2. Avant de procéder à une tâche d’entretien à l’intérieur de la source d’alimentation, débranchez l’alimentation électrique. 3. Maintenez les câbles, les fils de mise à la terre, les branchements, le cordon d’alimentation et la source d’alimentation en bon état. N’utilisez jamais un équipement s’il présente une défectuosité quelconque. 4. N’utilisez pas l’équipement de façon abusive. Gardez l’équipement à l’écart de toute source de chaleur, notamment des fours, de l’humidité, des flaques d’eau, de l’huile ou de la graisse, des atmosphères corrosives et des intempéries. 5. Laissez en place tous les dispositifs de sécurité et tous les panneaux de la console et maintenez-les en bon état. 6. Utilisez l’équipement conformément à son usage prévu et n’effectuez aucune modification. INFORMATIONS SUPPLÉMENTAIRES RELATI VES À LA SÉCURITÉ -- Pour obtenir de l’information supplémentaire sur les règles de sécurité à observer pour l’équipement de soudage à l’arc électrique et le coupage, demandez un exemplaire du livret “Precautions and Safe Practices for Arc Welding, Cutting and Gouging”, Form 52-529. ! Les publications suivantes sont également recommandées et mises à votre disposition par l’American Welding Society, 550 N.W. LeJuene Road, Miami, FL 33126 : 1. 2. 3. 4. 5. 6. 7. 8. ANSI/ASC Z49.1 - “Sécurité dans le soudage et la coupure”. AWS C5.1 - “Pratiques recommandées pour le coupage à l’arc au plasma”. AWS C5.2 - “Pratiques recommandées pour le coupage à l’arc au plasma”. AWS C5.3 - “Pratiques recommandées pour le gougeage et le coupage à l’arc au carbone”. AWS C5.5 - « Pratiques recommandées en cas de soudage à l’arc avec électrode en tungstène » AWS C5.6 - « Pratiques recommandées en cas de soudage à l’arc sous gaz avec fil plein » AWS SP - « Pratiques sécurisées » - Réédition, Manuel de soudage ANSI/AWS F4.1 - « Pratiques de sécurité recommandées pour le soudage et la coupure des conteneurs ayant contenu des substances dangereuses » 9. Norme CSA - W117.2 = Règles de sécurité en soudage, coupage et procédés connexes ! SIGNIFICATION DES SYMBOLES - Ce symbole, utilisé partout dans ce manuel, signifie “Attention” ! Soyez vigilant ! Votre sécurité est en jeu. DANGER Signifie un danger immédiat. La situation peut entraîner des blessures graves ou mortelles. MISE EN GARDE Signifie un danger potentiel qui peut entraîner des blessures graves ou mortelles. AVERTISSEMENT Signifie un danger qui peut entraîner des blessures corporelles mineures. 12 INSTRUCTIONS DE SÉCURITÉ 0560956430FR 100i / 200i / 300i / 400i Classe de protection de l’enveloppe MISE EN GARDE Ce produit a été conçu pour la découpe au plasma seulement. Toute autre utilisation pourrait causer des blessures et/ou endommager l’appareil. MISE EN GARDE L’équipement pourrait basculer s’il est placé sur une surface dont la pente dépasse 15°. Vous pourriez vous blesser ou endommager l’équipement de façon importante. 15° Art# A-12726 MISE EN GARDE Soulevez à l’aide de la méthode et des points d’attache illustrés afin d’éviter de vous blesser ou d’endommager l’équipement. Art# A-12736 0560956430FR INSTRUCTIONS DE SÉCURITÉ 13 SÉCURITÉ L’indice de protection (codification IP) indique la classe de protection de l’enveloppe, c’est-à-dire, le degré de protection contre les corps solides étrangers ou l’eau. L’enveloppe protège contre le toucher, la pénétration d’objets solides dont le diamètre dépasse 12 mm et contre l’eau pulvérisée à un angle de jusqu’à 60 degrés de la verticale. Les équipements portant la marque IP21S peuvent être entreposés à l’extérieur, mais ne sont pas conçus pour être utilisés à l’extérieur pendant une précipitation à moins d’être à l’abri. SÉCURITÉ 100i / 200i / 300i / 400i Cette page est intentionnellement laissée vierge. 14 INSTRUCTIONS DE SÉCURITÉ 0560956430FR 100i / 200i / 300i / 400i SECTION 2 : SPÉCIFICATIONS 2.01 Description générale du système La Configuration typique d’un système plasma comprend : • Un bloc d’alimentation • Module de commande de gaz • Assemblage de la soupape de la torche • Précision Plasma Découpe Torche • Ensemble de fils de connexion • Un jeu de pièces de rechange pour la torche Les composants sont reliés entre eux lors de l’installation. 2.02 Bloc d’alimentation en plasma Le bloc d’alimentation fournit le courant d’alimentation requis pour les opérations de coupe. Le bloc d’alimentation contrôle également la performance du système et refroidit/fait circuler le liquide de refroidissement pour la torche et les fils. 2.03 Démarreur à distance de l’arc Cette unité produit une pulsation HF temporaire pour démarrer l’arc pilote. L’arc pilote en question crée un sillon de façon à ce que l’arc principal puisse être transféré sur la pièce. Lorsque l’arc principal est établi, l’arc pilote s’arrête. 2.04 Module de commande de gaz Ce module permet le réglage à distance de la sélection des gaz, des pressions et des débits associés au réglage de l’intensité de découpe. 2.05 Précision Plasma Découpe Torche La torche fournit le courant contrôlé sur la pièce à souder par l’arc principal, coupant ainsi le métal. 0560956430FR CARACTÉRISTIQUES DU MODÈLE 15 CARACTÉRISTIQUES DU MODÈLE • Démarreur à distance de l’arc 100i / 200i / 300i / 400i 2.06 Caractéristiques et exigences électriques Spécifications et fonctionnalités du 100iTM Max OCV (U0) 425 vdc (400 vdc CE / CCC) Courant de sortie minimum 5 Amps Courant de sortie max. 100 Amps Tension de sortie 60 - 180 vdc CARACTÉRISTIQUES DU MODÈLE Système 100 A Valeur nominale du facteur de marche 100 % @ 100 A, 200 V, (20 kW), Température ambiante pour la valeur nominale du facteur de marche 104F° (40°C) Plage de fonctionnement 14°F à 122°F (-10°C à +50°C) Facteur de puissance 0,94 @ 100 A Sortie c.c. Refroidissement Liquide de refroidissement et air forcé (classe F) Spécifications et fonctionnalités du 200iTM Système 200 A Max OCV (U0) 425 vdc Courant de sortie minimum 5 Amps Courant de sortie max. 200 Amps Tension de sortie 60 - 180 vdc Valeur nominale du facteur de marche 100% @ 200A, 200V, (40kW), Température ambiante pour la valeur nominale du facteur de marche 104F° (40°C) Plage de fonctionnement 14°F à 122°F (-10°C à +50°C) Facteur de puissance 0,94 @ 200 A Sortie c.c. Refroidissement Liquide de refroidissement et air forcé (classe F) Spécifications et fonctionnalités du 300iTM Max OCV (U0) 425 vdc Courant de sortie minimum 5 Amps Courant de sortie max. 300 Amps Tension de sortie / IEC 60 - 180 vdc / 60 - 200 v c.c. Système 300 A Valeur nominale du facteur de marche 100% @ 300A, 200V, (60kW), Température ambiante pour la valeur nominale du facteur de marche 104F° (40°C) Plage de fonctionnement 14°F à 122°F (-10°C à +50°C) Facteur de puissance 0,94 @ 300 A Sortie c.c. Refroidissement Liquide de refroidissement et air forcé (classe F) Spécifications et fonctionnalités du 400iTM Système 400 A 16 Max OCV (U0) 425 vdc Courant de sortie minimum 5 Amps Courant de sortie max. 400 Amps Tension de sortie 60 - 200 v c.c. Valeur nominale du facteur de marche 100 % @ 400 Amps, 200V, (80kW), Température ambiante pour la valeur nominale du facteur de marche 104F° (40°C) Plage de fonctionnement 14°F à 122°F (-10°C à +50°C) Facteur de puissance 0,94 @ 400 A Sortie c.c. Refroidissement Liquide de refroidissement et air forcé (classe F) CARACTÉRISTIQUES DU MODÈLE 0560956430FR 100i / 200i / 300i / 400i Alimentation électrique 100iTM Entrée Puissance d’entrée Tension (Volts) Fréq. (Hz) 3-Ph (kVA) Courant Tailles recommandées (Voir la remarque) 3-Ph (Amps) Fusible (A) 3-Ph 80 Fil (AWG) 3-Ph Fil (mm2) 3-Ph #4 25 50/60 28 78 230 50/60 27 70 70 #6 16 380 50/60 21 33 40-45 #12 4 400 50/60 21 31 40-45 #12 4 480 50/60 21 26 35-40 #12 4 600 50/60 25 25 30 #12 4 CARACTÉRISTIQUES DU MODÈLE 208 Alimentation électrique 200iTM Entrée Puissance d’entrée Tension (Volts) Fréq. (Hz) 3-Ph (kVA) Courant Tailles recommandées (Voir la remarque) 3-Ph (Amps) Fusible (A) 3-Ph Fil (AWG) 3-Ph Fil (mm2) 3-Ph 208 50/60 47 133 175 #2 35 230 50/60 47 121 150 #2 35 380 50/60 42 65 100 #6 16 400 50/60 42 62 100 #6 16 480 50/60 42 52 100 #8 10 600 50/60 45 45 60 #8 10 Alimentation électrique 300iTM Entrée Puissance d’entrée Tension (Volts) Fréq. (Hz) 3-Ph (kVA) IEC IEC Courant Tailles recommandées (Voir la remarque) 3-Ph (Amps) Fusible (A) 3-Ph Fil (AWG) 3-Ph Fil (mm2) 3-Ph 208 50/60 76 215 3/0 3/0 95 230 50/60 76 194 2/0 2/0 70 400 50/60 63 93 #4 #4 25 400 480 480 600 50/60 50/60 50/60 50/60 72 63 72 75 106 77 88 73 #4 #4 25 #4 #4 25 #4 #6 #4 #6 25 16 Alimentation électrique 400iTM Entrée Puissance d’entrée Tension (Volts) Fréq. (Hz) 3-Ph (kVA) Courant Tailles recommandées (Voir la remarque) 3-Ph (Amps) Fusible (A) 3-Ph Fil (AWG) 3-Ph Fil (mm2) 3-Ph 380 50/60 93 144 200 #1 50 400 50/60 93 137 200 #1 50 480 50/60 93 114 175 #3 35 600 50/60 93 96 125 #4 25 REMARQUE ! * La taille de câble suggérée est basée sur le code national d’électricité américain NFPA 70 publié en 2011 par la National LA PRÉVENTION DES INCENDIES Association. Les listes sont contenues dans le tableau 400.5(A)(2) pour le cordon flexible de certains types prévus pour 75 °C à des températures ambiantes atteignant jusqu’à 30 °C. L’utilisation des câbles à faible cote de température ou d’un type d’isolation différent peut exiger une taille de câble plus grande. Réduire la valeur nominale pour des températures ambiantes plus élevées. Il s’agit uniquement de suggestions. L’installation doit en tout temps être conforme à la réglementation locale et nationale en vigueur dans votre région en ce qui concerne le choix du type et la taille de câble appropriés. 0560956430FR CARACTÉRISTIQUES DU MODÈLE 17 100i / 200i / 300i / 400i CARACTÉRISTIQUES DU MODÈLE 2.07 Dimensions du bloc d’alimentation 1213 mm 47,77 Pouce 914 mm 35,97 Pouce 701 mm 27,6 Pouce 100A 420 lb / 190 kg 200A 465 lb / 211 kg 300A 560 lb / 254 kg 400A 580 lb / 263 kg Art # A-11487FR_AB 18 CARACTÉRISTIQUES DU MODÈLE 0560956430FR 100i / 200i / 300i / 400i 208-230V / 600V Tension d'entrée CARACTÉRISTIQUES DU MODÈLE 230V 100A_740 lb / 336 kg 200A_1001 lb / 455 kg 300A_1220 lb / 555 kg 65.27 pouces (1658 mm) 600V 100A_652 lb / 296 kg 200A_718 lb / 326 kg 300A_783 lb / 356 kg 400A_849 lb / 386 kg 35.97 pouces (914 mm) 27.6 pouces (701 mm) Art # A-14628FR 0560956430FR CARACTÉRISTIQUES DU MODÈLE 19 100i / 200i / 300i / 400i 2.08 Caractéristiques du panneau arrière du bloc d’alimentation TSC/Comm Disjoncteurs Clients ports en option Connecteur GCM CARACTÉRISTIQUES DU MODÈLE Connecteur CNC C.C.M. CAN IN CAN OUT ESTOP VDR J55 - GCM USER INPUT Retour du liquide de refroidissement J15 - CNC HEIGHT CONTROL Alimentation du liquide de refroidissement J54 - TSC /COMM J59 - RAS Connecteur de l’amorce d’arc CB2 - 5A 120 VAC CB3 - 5A 24 VAC J70 - HE Connecteur à 7 broches CB4 - 5A 120 VAC F1 - 8A SB 230 VAC F2 - 8A SB 230 VAC Voyant alimentation CA Fusible Câble de l’arc pilote Ports d'entrée d'alimentation Câble de mise à la terre Rendement négatif Filtre du liquide de refroidissement Art # A-13975FR 20 CARACTÉRISTIQUES DU MODÈLE 0560956430FR 100i / 200i / 300i / 400i 2.09 Exigences en matière de gaz Le client doit fournir tous les gaz et les régulateurs de pression. Les gaz doivent être de qualité supérieure. Les régulateurs de pression doivent être à deux étages et installés à un rayon de 3 mètres de la Console de gaz. Bloc d’alimentation 100i : Conditions de pression du gaz, de débit et de qualité Qualité Pression minimale Débit O2 (Oxygène) Pureté de 99,5% (Liquide recommandé) 120 psi 8,3 bar / 827 kPa 70 scfh (33 lpm) N2 (Azote) Pureté de 99,5% (Liquide recommandé) <1000 ppm O2, <32 ppm H2O) 120 psi 8,3 bar / 827 kPa 200 scfh (95 lpm) Air comprimé ou embouteillé Propre, sec, exempt d’huile (voir Remarque 1) 120 psi 8,3 bar / 827 kPa 250 scfh (118 lpm) H35 (Argon-Hydrogène) H35 = 35% Hydrogène, 65% Argon Pureté de 99,995% (Recommandé de gaz) 120 psi 8,3 bar / 827 kPa 90 scfh (42.5 lpm) H2O (Eau) Voir Remarque 2 55 psi (3,8 bar) 10 gph (0.6 lpm) Remarque 1 : La source d’aération doit être correctement filtrée pour retirer toute trace d’huile ou de graisse. La contamination de l’huile ou de la graisse par de l’air comprimé ou embouteillé peut provoquer un incendie en conjonction avec de l’oxygène. Pour le filtrage, un filtre coalescent permettant de filtrer jusqu’à 0,01 micron doit être placé aussi près que possible des entrées de gaz du Module de commande de gaz. Remarque 2 : L’arrivée d’eau du robinet n’a pas besoin d’être déionisée, mais pour les systèmes présentant un fort taux de minéraux, un adoucisseur d’eau est recommandé. L’eau du robinet présentant un niveau de particules élevé doit être filtrée. Remarque 3 : Un régulateur de pression de l’eau N°8-6118 est recommandé pour garantir une pression de l’eau adéquate. Alimentation électrique 200i : Conditions de pression du gaz, de débit et de qualité Gaz Qualité Pression minimale Débit O2 (Oxygène) Pureté de 99,5% (Liquide recommandé) 120 psi 8,3 bar / 827 kPa 200 scfh (95 lpm) N2 (Azote) Pureté de 99,5% (Liquide recommandé) <1000 ppm O2, <32 ppm H2O) 120 psi 8,3 bar / 827 kPa 200 scfh (95 lpm) Air comprimé ou embouteillé Propre, sec, exempt d’huile (voir Remarque 1) 120 psi 8,3 bar / 827 kPa 450 scfh (212,4 lpm) H35 (Argon-Hydrogène) H35 = 35% Hydrogène, 65% Argon Pureté de 99,995% (Recommandé de gaz) 120 psi 8,3 bar / 827 kPa 200 scfh (95 lpm) H2O (Eau) Voir Remarque 2 55 psi (3,8 bar) 10 gph (0.6 lpm) Remarque 1 : La source d’aération doit être correctement filtrée pour retirer toute trace d’huile ou de graisse. La contamination de l’huile ou de la graisse par de l’air comprimé ou embouteillé peut provoquer un incendie en conjonction avec de l’oxygène. Pour le filtrage, un filtre coalescent permettant de filtrer jusqu’à 0,01 micron doit être placé aussi près que possible des entrées de gaz du Module de commande de gaz. Remarque 2 : L’arrivée d’eau du robinet n’a pas besoin d’être déionisée, mais pour les systèmes présentant un fort taux de minéraux, un adoucisseur d’eau est recommandé. L’eau du robinet présentant un niveau de particules élevé doit être filtrée. Remarque 3 : Un régulateur de pression de l’eau N°8-6118 est recommandé pour garantir une pression de l’eau adéquate. 0560956430FR CARACTÉRISTIQUES DU MODÈLE 21 CARACTÉRISTIQUES DU MODÈLE Gaz 100i / 200i / 300i / 400i CARACTÉRISTIQUES DU MODÈLE Alimentation électrique 300i : Conditions de pression du gaz, de débit et de qualité Gaz Qualité Pression minimale Débit O2 (Oxygène) Pureté de 99,5% (Liquide recommandé) 120 psi 8,3 bar / 827 kPa 200 scfh (95 lpm) N2 (Azote) Pureté de 99,5% (Liquide recommandé) <1000 ppm O2, <32 ppm H2O) 120 psi 8,3 bar / 827 kPa 300 scfh (141,6 lpm) Air comprimé ou embouteillé Propre, sec, exempt d’huile (voir Remarque 1) 120 psi 8,3 bar / 827 kPa 450 scfh (212,4 lpm) H35 (Argon-Hydrogène) H35 = 35% Hydrogène, 65% Argon Pureté de 99,995% (Recommandé de gaz) 120 psi 8,3 bar / 827 kPa 200 scfh (94,4 lpm) H2O (Eau) Voir Remarque 2 55 psi (3,8 bar) 10 gph (0.6 lpm) Remarque 1 : La source d’aération doit être correctement filtrée pour retirer toute trace d’huile ou de graisse. La contamination de l’huile ou de la graisse par de l’air comprimé ou embouteillé peut provoquer un incendie en conjonction avec de l’oxygène. Pour le filtrage, un filtre coalescent permettant de filtrer jusqu’à 0,01 micron doit être placé aussi près que possible des entrées de gaz du Module de commande de gaz. Remarque 2 : L’arrivée d’eau du robinet n’a pas besoin d’être déionisée, mais pour les systèmes présentant un fort taux de minéraux, un adoucisseur d’eau est recommandé. L’eau du robinet présentant un niveau de particules élevé doit être filtrée. Remarque 3 : Un régulateur de pression de l’eau N°8-6118 est recommandé pour garantir une pression de l’eau adéquate. Alimentation électrique 400i : Conditions de pression du gaz, de débit et de qualité Gaz Qualité Pression minimale Débit O2 (Oxygène) Pureté de 99,5% (Liquide recommandé) 120 psi 8,3 bar / 827 kPa 200 scfh (95 lpm) N2 (Azote) Pureté de 99,5% (Liquide recommandé) <1000 ppm O2, <32 ppm H2O) 120 psi 8,3 bar / 827 kPa 300 scfh (141,6 lpm) Air comprimé ou embouteillé Propre, sec, exempt d’huile (voir Remarque 1) 120 psi 8,3 bar / 827 kPa 500 scfh (236 lpm) H35 (Argon-Hydrogène) H35 = 35% Hydrogène, 65% Argon Pureté de 99,995% (Recommandé de gaz) 120 psi 8,3 bar / 827 kPa 200 scfh (95 lpm) H17 17,5% Hydrogène 32,5 % Argon 50 % Azote Pureté de 99,995% (Recommandé de gaz) 120 psi 8,3 bar / 827 kPa 200 scfh (95 lpm) Ar (Argon) Pureté de 99,995% (Recommandé de gaz) 120 psi 8,3 bar / 827 kPa 150 scfh (70,8 lpm) H2O (Eau) Voir Remarque 2 55 psi (3,8 bar) 10 gph (0,6 lpm) Remarque 1 : La source d’aération doit être correctement filtrée pour retirer toute trace d’huile ou de graisse. La contamination de l’huile ou de la graisse par de l’air comprimé ou embouteillé peut provoquer un incendie en conjonction avec de l’oxygène. Pour le filtrage, un filtre coalescent permettant de filtrer jusqu’à 0,01 micron doit être placé aussi près que possible des entrées de gaz du Module de commande de gaz. Remarque 2 : L’arrivée d’eau du robinet n’a pas besoin d’être déionisée, mais pour les systèmes présentant un fort taux de minéraux, un adoucisseur d’eau est recommandé. L’eau du robinet présentant un niveau de particules élevé doit être filtrée. Remarque 3 : Un régulateur de pression de l’eau N°8-6118 est recommandé pour garantir une pression de l’eau adéquate. 22 CARACTÉRISTIQUES DU MODÈLE 0560956430FR 100i / 200i / 300i / 400i 2.10 Applications de Gaz MATÉRIAUX FONCTIONNEMENT Découpe à 50 A Air Découpe à 70 A Air Découpe à 100 A Air Découpe à 150 A Air Découpe à 200 A Air Découpe à 400 A 0560956430FR ALUMINIUM TYPE DE GAZ TYPE DE GAZ TYPE DE GAZ O2 O2 O2 O2 O2 O2 O2 Air Air Air Air Air Air Air N2 Air N2 Air H20 Air N2 Air N2 Air H20 Air Air N2 Air N2 Air H20 Air N2 Air N2 Air H20 Air Air N2 N2 N2 H35 H20 N2 N2 N2 N2 H35 H20 N2 Air N2 N2 N2 H35 H20 N2 N2 N2 N2 H35 H20 N2 Air N2 N2 N2 H35 H20 N2 N2 N2 N2 H35 H20 N2 N2 N2 H20 N2 N2 H20 N2 N2 H35 N2 H20 N2 N2 H35 N2 H20 N2 H20 N2 N2 N2 N2 Air O2 Air Air O2 Air Air O2 Air N2 N2 N2 N2 H35 N2 H17 CARACTÉRISTIQUES DU MODÈLE N2 H35 N2 H17 CARACTÉRISTIQUES DU MODÈLE Air Découpe à 300 A ACIER INOXYDABLE PRÉ-DÉBIT PLASMA BOUCLIER PRÉ-DÉBIT PLASMA BOUCLIER PRÉ-DÉBIT PLASMA BOUCLIER Découpe à 30 A Découpe à 250 A ACIER DOUX N2 H20 N2 23 24 CARACTÉRISTIQUES DU MODÈLE 3.98" 101.1 mm 2.7" 69.6 mm 1.6" 40. mm Tube plongeur 1.49" 37.8 mm 2.4" 61 mm 2.0" 50.8 mm 2.25" 57.15 mm 6.6” 4.3” 109.1 mm 168.5 mm Base 100 A dimensions de la torche 6.3" 160.1 mm 15.5" 393.8 mm 19" 482.7 mm Capuchon Art # A-09534FR 1.4” 34.5 mm 70° .5” 2.4” 61 mm 2” 50.8 mm 12.7 mm CARACTÉRISTIQUES DU MODÈLE 100i / 200i / 300i / 400i 2.11 Spécifications de la torche A. Dimensions de la torche Base 400 A dimensions de la torche 0560956430FR 100i / 200i / 300i / 400i B. Longueur de fils de la torche Montage du fil de la torche Longueurs Mètres 10 3,05 15 4,6 25 7,6 50 15,2 75 22,9 100 30,4 CARACTÉRISTIQUES DU MODÈLE Pieds C. Pièces de la torche (Pièces génériques illustrées) Distributeur du gaz plasmagène Distributeur du gaz de protection Art # A-04741 Jupe Coiffe de protection Tuyère Electrode Cartouche D. Pièces en place (PIP) La torche est conçue pour être utilisée avec un bloc d’alimentation qui détecte le débit de retour du liquide de refroidissement qui confirme que les pièces de la torche sont en place. Si le débit de retour du liquide de refroidissement vers le bloc d’alimentation est absent ou insuffisant, le bloc d’alimentation n’alimentera pas la torche. Une fuite de liquide de refroidissement sur la torche indique également que des pièces de la torche sont manquantes ou mal installées. E. Type de refroidissement La combinaison des flux gazeux par la torche et le liquide de refroidissement. F. Données de la torche Caractéristiques nominales de la torche pour une utilisation avec un Bloc d’alimentation 100i-400i Température ambiante 104° F 40° C Facteur de marche 100 % @ 400 Amps Courant maximum 400 Amps Tension (Vcrête) 500V Tension d’amorçage d’arc 10kV Courant Jusqu’à 400 Amps, C.C., polarité normale Spécifications du gaz de la torche 0560956430FR Gaz plasma : Air comprimé, Oxygène, Azote, H35, H17, Ar Gaz de protection : Air comprimé, Oxygène, Azote, Eau, H35 Pression de fonctionnement 125 psi ± 10 psi 8,6 bar ± 0,7 bar Pression d’entrée maximale 135 psi/9,3 bar Flux de gaz 10 - 500 scfh CARACTÉRISTIQUES DU MODÈLE 25 CARACTÉRISTIQUES DU MODÈLE 100i / 200i / 300i / 400i Cette page est intentionnellement laissée vierge. 26 CARACTÉRISTIQUES DU MODÈLE 0560956430FR 100i / 200i / 300i / 400i SECTION 3: INSTALLATION 3.01 Conditions d’installation Alimentation électrique Le réseau d’alimentation électrique, le gaz et le système d’alimentation en eau doivent tous se conformer aux normes locales en vigueur. Cette conformité doit être vérifiée par un personnel qualifié. iSeries 100i™ Bloc d’alimentation Entrée Puissance d’entrée Tension (Volts) Freq. (Hz) Courant Tailles recommandées (voir la remarque) 3-Ph (kVA) 3-Ph (Amps) Fuse (Amps) 3-Ph Fil (AWG) 3-Ph Fil (mm2) 3-Ph 100 #4 25 50/60 35,9 101,4 230 50/60 35,6 91 90 #4 25 380 50/60 21 33 40-45 #12 4 400 50/60 21 31 40-45 #12 4 480 50/60 21 26 35-40 #12 4 600 50/60 33,2 32,5 40 #10 6 INSTALLATION 208 iSeries 200i™ Alimentation électrique Entrée Puissance d’entrée Tension (Volts) Freq. (Hz) Courant Tailles recommandées (voir la remarque) 3-Ph (kVA) 3-Ph (Amps) Fuse (Amps) 3-Ph Fil (AWG) 3-Ph Fil (mm2) 3-Ph 208 50/60 47 133 175 #2 35 230 50/60 47 121 150 #2 35 380 50/60 42 65 100 #6 16 400 50/60 42 62 100 #6 16 480 50/60 42 52 100 #8 10 45 45 60 #8 10 600 50/60 iSeries 300i™ Alimentation électrique Entrée Puissance d’entrée Courant Tailles recommandées (voir la remarque) Tension (Volts) Freq. (Hz) 3-Ph (kVA) 3-Ph (Amps) Fuse (Amps) 3-Ph Fil (AWG) 3-Ph Fil (mm2) 3-Ph 208 50/60 76 213 250 3/0 95 230 50/60 76 194 225 2/0 70 400 50/60 63 93 150 #4 25 400 50/60 72 106 150 #4 25 480 50/60 63 77 150 #4 25 480 50/60 72 88 150 #4 25 600 50/60 75 73 90 #6 16 IEC IEC iSeries 400i™ Alimentation électrique Entrée Puissance d’entrée Courant Tailles recommandées (voir la remarque) 3-Ph (kVA) 3-Ph (Amps) Fuse (Amps) 3-Ph Fil (AWG) 3-Ph Fil (mm2) 3-Ph 50/60 93 144 200 #1 50 400 50/60 93 137 200 #1 50 480 50/60 93 114 175 #3 35 600 50/60 98 96 125 #4 25 Tension (Volts) Freq. (Hz) 380 0560956430FR INSTALLATION 27 100i / 200i / 300i / 400i REMARQUE ! * La taille de câble suggérée est basée sur le code national d’électricité américain NFPA 70 publié en 2011 par la National LA PRÉVENTION DES INCENDIES Association. Les listes sont contenues dans le tableau 400.5(A)(2) pour le cordon flexible de certains types prévus pour 75 °C à des températures ambiantes atteignant jusqu’à 30 °C. L’utilisation des câbles à faible cote de température ou d’un type d’isolation différent peut exiger une taille de câble plus grande. Réduire la valeur nominale pour des températures ambiantes plus élevées. Il s’agit uniquement de suggestions. L’Installation doit en tout temps être conforme à la réglementation locale et nationale en vigueur dans votre région en ce qui concerne le choix du type et la taille de câble appropriés. Gaz Le client doit fournir tous les gaz et les régulateurs de pression. Les gaz doivent être de qualité supérieure. Les régulateurs de pression doivent être à deux étages et installés aussi près que possible de la console de gaz. Un gaz contaminé peut provoquer un ou plusieurs des problèmes suivants : INSTALLATION • Vitesse de coupe réduite • Mauvaise qualité de coupe • Faible précision de coupe • Durée de vie des consommables réduite. • La contamination de l’huile ou de la graisse par de l’air comprimé ou embouteillé peut provoquer un incendie en conjonction avec de l’oxygène. Conditions du système de refroidissement Le liquide de refroidissement doit être ajouté au système au moment de l’Installation. La quantité requise varie en fonction de la longueur des fils de la torche. ESAB recommande l’utilisation de ses liquides de refroidissement 7-3580 et 7-3581 (pour de faibles températures). Capacités de refroidissement Chat. Nombre et Mixture Mélange 7-3580 ‘Extra-Cool™’ 25 / 75 7-3581 ‘Ultra-Cool™’ 50 / 50 7-3582 ‘Extreme Cool™’ Concentré* * Pour mélanger avec du D-I Cool™ 7-3583 28 INSTALLATION Protège contre 10° F / -12° C -27° F / -33° C -76° F / -60° C 0560956430FR 100i / 200i / 300i / 400i 3.02 Disposition du système 100 - 300 Amp Se reporter aux sections 3.08 et 3.10 pour les connexions et les câbles de mise à la terre. 175’ / 53.3 m Longueur maximale 100’ / 30.5 m Longueur maximale 125’ / 38.1 m Longueur maximale F1 A Retour de l’arc pilote Négatif Puissance principale Alimentation du liquide C Retour du liquide D Câble de commande E P Art # A-11995FEU 0560956430FR Alimentation du liquide Retour du liquide Coiffe Rez-de câble Seulement pour PS quand DMC monté sur Haut de PS -Si ce n'est pas Terre- L Gaz plasmagène I L Gaz de protection J Gaz de protection Q Gaz plasmagène K F H Fibre optique Console de gaz DMC-3000 Flux préliminaire R Câble de commande S Rideau d’eau T Marquage U Commande du gaz DPC-3000 G INSTALLATION F Contrôleur tactile Câble de commande V Amorce de l’arc à distance F1 Fibre optique W Coiffe B Générateur Ultra-Cut CNC Retour de l’arc pilote Tube plongeur F Torche Pièce Câble de mise à la terre INSTALLATION O 29 100i / 200i / 300i / 400i 3.03 Disposition du système 400 Amp Se reporter aux sections 3.08 et 3.10 pour les connexions et les câbles de mise à la terre. 175’ / 53.3 m Longueur maximale 125’ / 38.1 m Longueur maximale F1 50’ / 15.25 m Longueur maximale A Retour de l’arc pilote #8 Négatif 2/0 Alimentation du liquide 10’ C Retour du liquide 10’ D Câble de commande Y Générateur Ultra-Cut CNC INSTALLATION P F Fibre optique W C C M Contrôleur tactile V Câble de commande Rez-de câble Seulement pour PS quand DMC monté sur Haut de PS -Si ce n'est pas Terre- E chaleur échangeur HE 400 L K F Coiffe B Câble de commande Puissance principale Retour de l’arc pilote Console de gaz DMC-3000 Démarreur à distance Arc Alimentation du liquide Retour du liquide Alimentation du liquide C Retour du liquide D Coiffe Gaz plasmagène H Gaz plasmagène I Fibre optique L Gaz de protection J Gaz de protection Q Flux préliminaire R F1 Câble de commande S Rideau d’eau T Marquage U Commande du gaz DPC-3000 G Tube plongeur F Torche Pièce Câble de mise à la terre O Art # A-11996FEU 3.04 Tuyau recommandé pour l’alimentation en gaz Article # Qté 1 30 Description catalogue # 3/8”Tuyau Synflex Gris. Aucun raccord inclus. Numéro de catalogue par pied. INSTALLATION 9-3616 0560956430FR 100i / 200i / 300i / 400i 3.05 Fils et câbles toutes intensités Art # A-11997FR Câble AWG n° 8 Retour de l’arc pilote, du générateur à l’amorce de l’arc A Câble 3/0 AWG (95 mm2 ) Câble négatif, du générateur à l’amorce de l’arc B C Vert Vert Câble d’alimentation du liquide de refroidissement, du générateur à l’amorce de l’arc D Rouge Rouge Câble de retour du liquide de refroidissement, du générateur à l’amorce de l’arc E - Câble de commande, du générateur à l’amorce de l’arc E,Y 14/7 Y - Câble de commande de l’échangeur de chaleur Câble de masse, de l’amorce de l’arc à distance à la mise à la terre 1/0 vert / jaune (50 mm2) F1 G Câble de la torche blindé, de l’amorce de l’arc à distance à la torche I Câble du gaz plasmagène, de la valve de la torche à la torche J Câble du gaz de protection, de la valve de la torche à la torche K INSTALLATION Câble de masse AWG n° 4 vert / jaune F Câble de commande, du générateur au module de commande du gaz 37 Câble à fibre optique, du générateur au module de commande du gaz L Pour une utilisation avec le DFC-3000 H, Q, R,T, U S - Câble de commande, du DMC-3000 au DPC-3000 S,V 16 pin V - TSC-3000 au PS Câble 3/0 (95 mm )2 O P Câble de mise à la terre 37 0560956430FR Câble CNC (fil 37) INSTALLATION 31 100i / 200i / 300i / 400i 3.06 Soulevez le bloc d’alimentation AVERTISSEMENT Ne pas toucher les pièces électriques sous tension. Déconnecter les conducteurs d’alimentation de la source électrique mise hors tension avant de déplacer la unité. TOUTE CHUTE D’ÉQUIPEMENT peut entraîner des blessures graves voire endommager l’équipement. INSTALLATION Utiliser un chariot élévateur à fourches, une grue ou un palan pour soulever l’unité de la palette d’expédition comme illustré. Le bloc d’alimentation doit être stable et en position verticale. Ne pas soulever une charge plus élevée que nécessaire pour retirer la palette d’expédition. S’assurer que tous les panneaux et vis sont fermement attachés avant d’effectuer le levage. Art # A-11531_AC Régler le bloc d’alimentation sur une surface dure et plane. L’installateur peut fixer le bloc d’alimentation au sol ou sur une structure de support, les pièces passant à travers les pièces horizontales des pieds du bloc d’alimentation. 32 INSTALLATION 0560956430FR 100i / 200i / 300i / 400i 3.07 Installer des pièces consommables de la torche Installer les consommables comme suit pour assurer un bon fonctionnement. Ces étapes vous aideront à vous assurer que les pièces sont bien emboîtées. MISES EN GARDE Ne pas placer de consommables dans la cartouche quand celle-ci est fixée au corps de la torche. Faire en sorte qu’aucun matériau étranger ne pénètre dans les consommables et la cartouche. Manipuler soigneusement toutes les pièces afin d’éviter de les endommager car cela pourrait affecter les performances de la torche. Art # A-03887FR 1. Vérifier le diagramme de coupage pour trouver la combinaison de pièces correspondantes pour l’Application de découpage. INSTALLATION 2. Pour les pièces de 200 Amp uniquement, visser sur le Dispositif de retenue sur le blindage. 3. Empiler les pièces consommables. A B he uc rto Ca de tro ec El D ga istri z p bu las teu m rd ag u èn e Jupe uy èr e Dispositif de retenue D ga istri z d bu e p teu ro r d te u ct io n T Art # A-12789FR C 1 - Assembler « A » 200 A uniquement. 2 - Assembler « B ». 3 - Assembler « B .sur « C ». 4 - Assembler « A » sur le bloc « B-C ». 4. Insérer la pile des consommables dans la cartouche. S’assurer que l’embout du grand joint torique de la torche entre complètement dans la cartouche. Si l’une des pièces du joint torique dépasse de la cartouche, cela signifie qu’elle n’est pas bien fixée. 5. Utiliser l’outil de la cartouche pour tenir l’ensemble de la cartouche, tout en tournant le godet de protection (et le dispositif de retenue de la protection pour les pièces de 200 Amp) sur l’assemblage de la cartouche. Pour les pièces de 300 Amp, tourner le dispositif de retenue sur le blindage. Lorsque ce groupe est entièrement assemblé, l’écran doit jaillir de l’avant de du dispositif de retenue. Si cette saillie n’apparaît pas, c’est que le bouclier n’est pas bien serré sur l’ensemble de cartouche. 6. Retirer l’outil de la cartouche. Ajuster l’ensemble de cartouche sur la tête de la torche. L’anneau Speed Lok doit s’enclencher en position et le montage de la cartouche doit toucher le grand joint torique sur le corps de la torche. 0560956430FR INSTALLATION 33 100i / 200i / 300i / 400i Tête de la torche Joint torique de la tête de la torche 0.063 - 0.083 po (1.6 - 2.1 mm) Saillie Art # A-08300FR INSTALLATION Installation de la cartouche assemblée sur la tête de la torche 7. Faites glisser le clip ohmique au-dessus du bouclier si vous utilisez la détection du contrôle de la hauteur de la torche ohmique. 8. Connecter le faisceau de fils de l’altimètre à la borne du capteur ohmique si la détection ohmique de hauteur de torche est utilisée. Clip ohmique Art # A-03393FR REMARQUE! La détection de la hauteur ohmique est déconseillée avec un brouillard d’eau. L’eau sur la plaque interfère électriquement avec le circuit de détection ohmique. 34 INSTALLATION 0560956430FR 100i / 200i / 300i / 400i 30 - 100 Amp Assemblage des pièces 2: Appuyer la cartouche contre les pièces empilées 1: Empiler les pièces Electrode Distributeur du gaz plasmagène Joint torique supérieur sur la tuyère Aucun vide entre les pièces Tuyère Distributeur du gaz de protection INSTALLATION La cartouche couvre le joint torique supérieur sur la tuyère de la torche Coiffe de protection 3: Enfiler la jupe sur la cartouche 4: Contrôler que la jupe dépasse Jupe Bouclier cap La coiffe de protection dépasse de 0.063-0.083" (1.6 - 2.1 mm) Art # A-04873FR Installation de la cartouche assemblée sur la tête de la torche 0560956430FR INSTALLATION 35 INSTALLATION 100i / 200i / 300i / 400i Cette page est intentionnellement laissée vierge. 36 INSTALLATION 0560956430FR 100i / 200i / 300i / 400i SECTION 4 : FONCTIONNEMENT 4.01 Détail du panneau alimentation électrique Indicateur de gaz Indicateur C.A. Indicateur de température A/ Indicateur d'état Indicateur c. c. A/ Art # A-11541FR Indicateur d’alimentation AC A-08038FR A-08015FR Voyant TEMP : Normalement sur OFF. L’indicateur est ALLUMÉ lorsque les capteurs de température interne détectent une température supérieure aux limites normales. Laisser refroidir l’unité avant de poursuivre les opérations. Voyant GAS : Clignotement durant le début de purge du gaz/l’amorçage de la pompe, puis devient stable une fois que le gaz circule. Indique que la appuyer surion de gaz et le débit de liquide de refroidissement sont à un niveau suffisant pour faire fonctionner la torche. A-08006FR Voyant CC : Indique que le bloc d’alimentation génère une tension de sortie en CC. A/ Indicateur d’état : Affiche la version du code CCM au démarrage suivie par le paramètre de contrôle actuel et l’état du système. Se reporter aux sections 4.05 et du Code de statut pour plus de détails. Voyant d’alimentation c.a. du panneau arrière Indique que l’appareil est traversé par l’alimentation en c.a. 4.02 Système Fonctionnement Cette section contient des informations sur le fonctionnement spécifiques du bloc d’alimentation. AVERTISSEMENT Passer en revue les précautions de sécurité de la CHAPITRE 1. Si le cordon d’alimentation est doté d’une prise ou n’est pas connecté en permanence à l’alimentation, s’assurer que l’alimentation à la prise est débranchée lors de l’insertion de la fiche dans la prise. Déconnecter l’alimentation principale à la source avant de monter ou de démonter le bloc d’alimentation, les pièces de la torche, la torche et les assemblages de câbles ou avant d’ajouter le liquide de refroidissement. Il ne suffit pas simplement de régler l’interrupteur MARCHE / ARRÊT sur l’appareil sur la position ARRÊT lorsque les opérations de coupe ont été effectuées. Toujours actifr l’interrupteur de déconnexion de l’alimentation cinq minutes après la dernière coupe. 0560956430FR FONCTIONNEMENT 37 FONCTIONNEMENT Indique que l’unité a passé les tests d’alimentation d’entrée et que la tension AC alimente les modules de l’onduler par le contacteur d’entrée lorsque l’interrupteur ON/OFF est en position ON. 100i / 200i / 300i / 400i REMARQUE! Avant de démarrer le système, déterminer le processus à suivre. Le processus est déterminé par le type et l’épaisseur du métal à couper. Sélectionner et installer les consommables nécessaires, connecter les gaz nécessaires au système. 1. Connecterer le système à l’alimentation d’entrée principale. Un voyant s’allume sur le panneau arrière lorsque l’alimentation C.A est branchée à l’appareil. Placer l’interrupteur d’activation du plasma (Vision T5 : le commutateur d’activation/d’arrêt d’urgence du plasma) en position « Activé » 2. Mettre l’interrupteur ON/OFF sur la position MARCHE (haut). Le système passe par la « séquence de démarrage ». • Les points décimaux de l’affichage à 4 chiffres clignotent pendant environ 10 secondes de droite à gauche. • Ensuite, les 4 indicateurs DEL rectangulaires et les 4 chiffres d’affichage d’état s’allument entièrement à titre d’essai. • Puis, pendant environ 6 secondes, l’écran affiche la lettre « C » (code), suivie de la version du code CCM. Exemple « C1.2.0 ». Pendant ce temps, différents essais de tension d’entrée sont effectués. Si une erreur est détectée, son code s’affiche et le démarrage s’arrête. En cas d’erreur, l’écran affiche « E » ou « L ». Si le plasma n’a pas encore été activé à ce moment, E101 s’affiche et la séquence de démarrage ne débute pas. FONCTIONNEMENT • La pompe de liquide de refroidissement se met en marche, l’indicateur de gaz clignote et l’affichage indique « 0 » pour signaler qu’aucun processus de découpe n’a été chargé. Si l’unité est désactivée, l’activation du plasma s’éteint, la pompe ne démarre pas et l’affichage alterne entre le code de statut E101 et « 0 ». • En supposant que l’unité n’est pas désactivée, dès qu’un écoulement adéquat de liquide de refroidissement est détecté, généralement après 5 secondes environ, la DEL de gaz arrête de clignoter, les contacteurs se ferment et l’indicateur de DEL CA s’allume. Si le liquide de refroidissement contient des bulles, il est possible que le code E406 s’affiche en alternance avec le code « 0 » jusqu’à ce que ces bulles soient éliminées. Il s’agit là d’un avertissement qui ne vous empêche pas de continuer. Si aucun débit n’est détecté, la pompe continuera de fonctionner et le voyant DEL de gaz de clignoter jusqu’à ce qu’un débit soit détecté ou pendant quatre minutes, au bout desquelles la pompe s’arrêtera et l’affichage indiquera E404 pour signaler que la circulation de liquide de refroidissement ne s’est pas établie avec un débit suffisant. • Utiliser maintenant le programme compris dans la commande CNC du Vision T5™. PUISSANCE I ON OFF O OFF O O OFF O OFF Art # A-11542FR 38 FONCTIONNEMENT 0560956430FR 100i / 200i / 300i / 400i B. Gaz de protection Suggestions de fonctionnement 1. Écran d’air comprimé • L’écran d’air est utilisé en général avec le plasma à air ou à oxygène. • Améliore la qualité de coupe sur certains matériaux ferreux. 1. Après l’opération, patienter quatre minutes avant de régler l’interrupteur de MARCHE/ARRÊT sur ARRÊT. Cela permet aux ventilateurs de refroidissement de fonctionner pour dissiper la chaleur de fonctionnement provenant du bloc d’alimentation. 2. Pour ne pas affecter la durée de vie maximale des pièces, ne pas utiliser l’arc pilote plus longtemps que nécessaire. • L’écran d’azote est utilisé avec du plasma à l’azote (N2) ou Ar/H2 (H35). 3. Faire attention lors de la manipulation des fils de la torche et les protéger contre tous dommages. • Offre des finitions lisses sur des matériaux non ferreux. 4. Lors de l’utilisation de l’eau comme bouclier, il est important de noter que : • Peut réduire la fumée lorsqu’il est utilisé avec du plasma Ar/H2. 3. Écran d’eau • Il est impératif d’utiliser de l’eau du robinet de qualité potable afin de prévenir une accumulation de particules dans le système de plomberie du bouclier d’eau. • La contamination particulaire et l’accumulation peuvent réduire la durée de vie des pièces consommables et causer une défaillance prématurée de la torche. • Un filtre de particules d’eau de type cartouche peut contribuer à atteindre des performances de coupe optimales. • Normalement utilisé avec de l’azote. • Offre une surface de coupe très lisse. • Réduit la fumée et la chaleur sur la pièce à souder. • Efficace en cas d’utilisation avec N2 jusqu’à 2 po (50 mm) maximum d’épaisseur de matériau. • L’eau du robinet représente un faible coût opérationnel. 4.03 Code d’état CCMs REMARQUE! Voir l’annexe pour un dépannage avancé Lors du démarrage et de l’utilisation, les circuits de commande du bloc d’alimentation effectue différents tests. Si le circuit détecte une condition nécessitant l’attention de l’opérateur, l’écran d’état sur le panneau avant affiche un code à 3 chiffres précédé soit par la lettre « E » (défaillance actif actuellement) ou la lettre « L » (dernière défaillance ou défaillance verrouillée) indiquant qu’une défaillance s’est produite lors de la procédure mais n’est pas actif actuellement. Certaines conditions peuvent être actifs indéfiniment, tandis que d’autres sont temporaires Le bloc d’alimentation enclenche des conditions momentanées ; certaines conditions momentanées peuvent arrêter le système. L’indicateur peut afficher de multiples conditions séquentiellement ; it is important to recognize all possible conditions that may be displayed. REMARQUE! Ces tableaux couvrent les appareils jusqu’à 400 A ; les appareils à plus basse intensité n’ont pas tous les hacheurs auxquels il est fait référence dans le groupe 2. Les codes pour ces sections ne doivent pas apparaître. 0560956430FR FONCTIONNEMENT 39 FONCTIONNEMENT • Peu coûteux - réduit les coûts de fonctionnement. 2. Écran d’azote (N2) 100i / 200i / 300i / 400i Code d’état CCM Groupe 1 -- Processus plasma Code Solution / Remarques Plasma désactivé Activation plasma - Arrêt ; Désactivation actionnée ou SW externe désactivé (CNC) (CNC); Cavalier CCM TB1-1&2 manquant ; Câble-ruban du circuit 40 au relais PCB et CCM déconnecté ou défectueux ; 102 Échec de l’amorçage du pilote Le pilote n’a pas démarré dans les 15 secondes. Les consommables de torche sontils usés ? Vérifier que le bon procédé a été sélectionné ou que le réglage manuel, y compris le réglage de contrôle d’intensité électrique, correspond aux consommables ; appuyer surion du plasma trop élevée ; Démarreur de l’arc défectueux ; Circuit imprimé pilote défectueux ; Onduleur défectueux CHAPITRE 1A. Câbles-rubans inversés sur les sections INV1 1A et 1B. 103 Pilotee perdu Le pilote est sorti lors du processus de démarrage. Les consommables de torche sont-ils usés ? Vérifier que le procédé de découpe ou que le réglage du contrôle d’intensité électrique correspond aux consommables ; Pression de plasma trop élevée ; 104 Transfertt annulé L’arc a été transféré sur la pièce d’usinage puis s’est éteint lors du démarrage. L’arc a perdu contact avec la pièce d’usinage (a dépassé la bordure, est passé sur un orifice, etc.) ; Distance de sécurité trop élevée ; Vérifier que le procédé de découpe ou les réglages manuels (contrôle d’intensité électrique, appuyer surions des gaz) correspond aux consommables ; 105 Non utilisé Réservé pour l’ancien produit 106 Le transfert doit se faire du pilote vers l’arc de coupe en 0,085 seconde (ARRÊT de SW8-1) ou 3 sec. (SW8-1 EN MARCHE). Distance de sécurité trop élevée ou nulle Délai de pilote, pas de pendant le travail sous la torche ; sélection d’un mauvais procédé de découpe ou transfert mauvais réglages manuels (contrôle d’intensité électrique réglé trop bas ou mauvaise appuyer surion des gaz). 107 Défaillance de la proLa pointe est restée en contact avec la pièce pendant plus de 15 secondes. tection de la pointe 108 Tension de pointe trop proche de la tension d’électrode ; Consommables de torche usées ; Consommables erronés installés provoquant un court-circuit de la pointe Pointe pour défaut de sur l’électrode ; Sélection d’un mauvais procédé ou mauvais réglage manuel du tension d’électrode. gaz de plasma ou de l’intensité de découpe; Fuite dans le tuyau de plasma vers la torche ; Circuit imprimé pilote défectueux ; Corps de torche court-circuité. 109 Procédé de pièce non S’applique uniquement à la Commande automatique de gaz. Sélectionner et charconfiguré. ger un procédé de découpe. 110 Appareil verrouillé 101 FONCTIONNEMENT Message Commande automatique de gaz: Chargement du procédé ; attendre qu’il soit terminé Code d’état CCM Groupe 2 -- Bloc d’alimentation en plasma Code 40 Message Solution / Remarques 201 Phase c.a. Absente Fusible mural disjoncté ; fusible de l’appareil F1 ou F2 ou du panneau arrière disjoncté ; mauvaise connexion du câble d’alimentation ; circuit de polarisation du système défectueux. 202 Non utilisé Réservé pour l’ancien produit 203 Non utilisé Réservé pour l’ancien produit 204 Non utilisé Réservé pour l’ancien produit 205 Sortie c.c. Faible Inférieure à 60 V c.c ; Câble négatif en court-circuit à la pièce ou à la terre ; Hâcheur défectueux (sortie court-circuitée) ; Capteur (J24) tension CCM déconnecté ou fil cassé ; CCM défectueux. FONCTIONNEMENT 0560956430FR 100i / 200i / 300i / 400i Code d’état CCM Groupe 2 -- Bloc d’alimentation en plasma Code Message Solution / Remarques Non utilisé Réservé pour l’ancien produit 207 Courant inattendu dans le fil de masse Courant dépassant 8 A dans le câble de masse avant l’amorçage ou le transfert. Court-circuit du fil négatif à la terre ou au châssis du démarreur d’arc ; Capteur de courant du câble de masse HCT1 défectueux ; Circuit imprimé de relais défectueux. 208 Courant inattendu dans le circuit de pilotage Courant dépassant 6 A dans le circuit de pilote avant l’amorçage. Consommables erronés ou inappropriés, causant un court-circuit entre la pointe et l’électrode ; court-circuit entre le fil du pilote au pôle négatif du tube de la torche ; circuit du relais défectueux ; court-circuit possible au niveau de la torche. 209 Non utilisé Réservé pour l’ancien produit 210 Courant de service trop élevé Courant du fil de masse détecté supérieur à 16 % du réglage de procédé. Possibilité de défaut du capteur de courant de masse HCT1 ou du circuit du relais ; CCM défectueux. 211 Courant de service trop bas Courant de service détecté inférieur à 16 % du réglage de procédé. Possibilité de défaut du capteur de courant de masse HCT1 ou du circuit du relais ; Possible défectuosité du circuit de pilote (court-circuit IGBT) ; 212 Faible courant de fonctionnement du plasma lors de la coupe et attribué à un Faible courant de courant faible en sortie de la section A du module hâcheur 1 ; sortie du hâcheur sortie du hâcheur 1A déconnectée ; possibilité de câble-ruban défectueux ; si le problème persiste, remplacer le module hâcheur 1 213 Faible courant de fonctionnement du plasma lors de la coupe et attribué à un Faible courant de courant faible en sortie de la section B du module hâcheur 1 ; sortie du hâcheur sortie du hâcheur 1B déconnectée ; Possible défectuosité du câble-ruban ; Si le problème persiste, remplacer le module 1 du hâcheur 214 Faible courant de fonctionnement du plasma lors de la coupe et attribué à un Faible courant de courant faible en sortie de la section A du module hâcheur 2 ; sortie du hâcheur sortie du hâcheur 2A déconnectée ; possibilité de câble-ruban défectueux ; si le problème persiste, remplacer le module hâcheur 2 215 Faible courant de fonctionnement du plasma lors de la coupe et attribué à un Faible courant de courant faible en sortie de la section B du module hâcheur 1 ; sortie du hâcheur sortie du hâcheur 2B déconnectée ; Possible défectuosité du câble-ruban ; Si le problème persiste, remplacer le module 2 du hâcheur 216 Faible courant de fonctionnement du plasma lors de la coupe et attribué à un Faible courant de courant faible en sortie de la section A du module hâcheur 1 ; sortie du hâcheur sortie du hâcheur 3A déconnectée ; Possible défectuosité du câble-ruban ; Si le problème persiste, remplacer le module 3 du hâcheur 217 Faible courant de fonctionnement du plasma lors de la coupe et attribué à un Faible courant de courant faible en sortie de la section B du module hâcheur 1 ; sortie du hâcheur sortie du hâcheur 3B déconnectée ; Possible défectuosité du câble-ruban ; Si le problème persiste, remplacer le module 2 du hâcheur 218 Courant de fonctionnement du plasma élevé pendant la découpe et attribué à Courant de sortie un courant élevé en sortie de la section A du module hâcheur 1 ; Si le problème élevé du hâcheur 1A persiste, remplacer le module 1 du hâcheur 219 Courant de fonctionnement du plasma élevé lors de la coupe et attribué à un couCourant de sortie rant élevé en sortie de la section B du module hâcheur 1 ; Si le problème persiste, élevé du hâcheur 1B remplacer le module 1 du hâcheur 220 Courant de fonctionnement du plasma élevé pendant la découpe et attribué à Courant de sortie un courant élevé en sortie de la section A du module hâcheur 2 ; Si le problème élevé du hâcheur 2A persiste, remplacer le module 2 du hâcheur 0560956430FR FONCTIONNEMENT 41 FONCTIONNEMENT 206 100i / 200i / 300i / 400i Code d’état CCM Groupe 2 -- Bloc d’alimentation en plasma FONCTIONNEMENT Code 42 Message Solution / Remarques 221 Courant de fonctionnement du plasma élevé lors de la coupe et attribué à un couCourant de sortie rant élevé en sortie de la section B du module hâcheur 1 ; Si le problème persiste, élevé du hâcheur 2B remplacer le module 2 du hâcheur 222 Courant de fonctionnement du plasma élevé pendant la découpe et attribué à Courant de sortie un courant élevé en sortie de la section A du module hâcheur 3 ; Si le problème élevé du hâcheur 3A persiste, remplacer le module 3 du hâcheur 223 Courant de fonctionnement du plasma élevé lors de la coupe et attribué à un couCourant de sortie rant élevé en sortie de la section B du module hâcheur 1 ; Si le problème persiste, élevé du hâcheur 3B remplacer le module 3 du hâcheur 224 Hâcheur 1 introuvable Module hâcheur 1 section A nécessaire au pilotage ; mauvaise connexion du câble-ruban CCM J31 au module hâcheur 1 section A. 225 Révision incompatible hâcheur 1A Version du hâcheur non supportée ; câble-ruban CCM J31 au module hâcheur 1 section A endommagé ; version du code CCM incompatible avec la version ou le modèle du hâcheur 226 Révision incompatible hâcheur 1B Révision du hâcheur non supportée ; Le câble-ruban CCM J32 au module 1 du hâcheur section B est endommagé; La version du code CCM est incompatible avec le modèle ou la révision du hâcheur 227 Révision incompatible hâcheur 2A Version du hâcheur non supportée ; câble-ruban CCM J33 au module hâcheur 2 section A endommagé ; version du code CCM incompatible avec la version ou le modèle du hâcheur 228 Révision incompatible hâcheur 2B Version du hâcheur non supportée ; câble-ruban CCM J34 au module hâcheur 2 section B endommagé ; version du code CCM incompatible avec la version ou le modèle du hâcheur 229 Révision incompatible hâcheur 3A Version du hâcheur non supportée ; câble-ruban CCM J35 au module hâcheur 3 section A endommagé ; version du code CCM incompatible avec la version ou le modèle du hâcheur 230 Révision incompatible hâcheur 3B Version du hâcheur non supportée ; câble-ruban CCM J36 au module hâcheur 3 section B endommagé ; version du code CCM incompatible avec la version ou le modèle du hâcheur 231 Décalage V c.a. Du hâcheur 1A Étalonnage de tension du hâcheur c.a incompatible avec l’étalonnage de la tension d’alimentation ; mauvaise connexion du câble-ruban CCM J31 au module hâcheur 1 section A ; mauvaise tension installée sur le module hâcheur 1 ; module hâcheur défectueux 232 Décalage V c.a. Du hâcheur 1B Étalonnage de tension du hâcheur c.a. Incompatible avec l’étalonnage de la tension d’alimentation ; Mauvaise connexion du câble ruban CCM J32 au module onduleur 1 section B ; Mauvaise tension installée sur le module hâcheur 1 ; Module du hâcheur défectueux 233 Décalage V c.a. Du hâcheur 2A Étalonnage de tension du hâcheur c.a. Incompatible avec l’étalonnage de la tension d’alimentation ; Mauvaise connexion du câble ruban CCM J33 au module onduleur 2 section A ; Mauvaise tension installée sur le module hâcheur 2 ; Module du hâcheur défectueux 234 Décalage V c.a. Du hâcheur 2B Étalonnage de tension du hâcheur c.a. Incompatible avec l’étalonnage de la tension d’alimentation ; Bad ribbon cable connection CCM J34 to Module d’onduleur 2 Section B; Mauvaise tension installée sur le module hâcheur 2 ; Module du hâcheur défectueux 235 Décalage V c.a. Du hâcheur 3A Étalonnage de tension du hâcheur c.a. Incompatible avec l’étalonnage de la tension d’alimentation ; Mauvaise connexion du câble ruban CCM J35 au module onduleur 3 section A ; Mauvaise tension installée sur le module hâcheur 3 ; Module du hâcheur défectueux FONCTIONNEMENT 0560956430FR 100i / 200i / 300i / 400i Code d’état CCM Groupe 2 -- Bloc d’alimentation en plasma Code Message Solution / Remarques Étalonnage de tension du hâcheur c.a. Incompatible avec l’étalonnage de la tension d’alimentation ; Connexion par câble Bad Ribbon entre CCM 3B (J36) et Inverter Module 3 Section B Mauvaise tension installée sur le module hâcheur 3 ; Module du hâcheur défectueux 237 Pas assez de hâcheurs trouvés Il faut au moins deux sections de hâcheur pour fonctionner ; câble-ruban CCM à la section de hâcheur endommagé ou déconnecté ; 238 BIAS VAC Invalide Sélection de tension c.a. Invalide ; connexion endommagée ou détachée de J61 de l’alimentation du système de Bias ; circuit imprimé du système de Bias défectueux Tension c.a. Élevée La tension du circuit de polarisation du système détectée dépasse la tension de la valeur nominale du bloc d’alimentation ; La connexion de sélection de la tension d’alimentation de polarisation du système est défectueuse ou endommagée ; système Bias PCB défectueux, CCM défectueux 240 Tension c.a. Basse La tension détectée sur le circuit de polarisation du système est inférieure à la tension d’étalonnage de l’alimentation électrique ; La connexion de sélection de la tension d’alimentation de polarisation du système est défectueuse ou endommagée ; système Bias PCB défectueux, CCM défectueux 241 Défaut de tension d’entrée du hâcheur ; tension hors limites ou phase manquante Erreur de tension à l’entrée c.a. Du module hâcheur 1 section A ; Mauvaise qualité de l’alimentation d’entrée du hâcheur c.a ; Contacteur W1 défectueux ; Connexion ouverte ou desserrée entre les bornes 1A d’entrée et le contacteur W1 ou entre le contacteur et l’entrée de la section de l’onduleur ; Module du hâcheur défectueux 242 Défaut de tension d’entrée du hâcheur ; tension hors limites ou phase manquante Erreur de tension à l’entrée c.a. Du module hâcheur 1 section B ; Mauvaise qualité de l’alimentation d’entrée du hâcheur c.a ; Contacteur W1 défectueux ; Connexion ouverte ou desserrée entre les bornes 1B d’entrée et le contacteur W1 ou entre le contacteur et l’entrée de la section de l’onduleur ; Module du hâcheur défectueux 243 Défaut de tension d’entrée du hâcheur ; tension hors limites ou phase manquante Erreur de tension à l’entrée c.a. du module hâcheur 2 section A ; Mauvaise qualité de l’alimentation d’entrée du hâcheur c.a ; Contacteur W1 défectueux ; Connexion ouverte ou desserrée entre les bornes 2A d’entrée et le contacteur W1 ou entre le contacteur et l’entrée de la section de l’onduleur ; Module du hâcheur défectueux 244 Défaut de tension d’entrée du hâcheur ; tension hors limites ou phase manquante Erreur de tension à l’entrée c.a. Du module hâcheur 2 section B ; Mauvaise qualité de l’alimentation d’entrée du hâcheur c.a ; Contacteur W2 défectueux ; Connexion ouverte ou desserrée entre les bornes 2B d’entrée et le contacteur W2 ou entre le contacteur et l’entrée de la section du hâcheur ; Module du hâcheur défectueux 245 Défaut de tension d’entrée du hâcheur ; tension hors limites ou phase manquante Erreur de tension à l’entrée c.a. Du module hâcheur 3 section A ; Mauvaise qualité de l’alimentation d’entrée du hâcheur c.a ; Contacteur W2 défectueux ; Connexion ouverte ou desserrée entre les bornes 3A d’entrée et le contacteur W2 ou entre le contacteur et l’entrée de la section du hâcheur ; Module du hâcheur défectueux 246 Défaut de tension d’entrée du hâcheur ; tension hors limites ou phase manquante Erreur de tension à l’entrée c.a. Du module hâcheur 3 section B ; Mauvaise qualité de l’alimentation d’entrée du hâcheur c.a ; Contacteur W2 défectueux ; Connexion ouverte ou desserrée entre les bornes 3B d’entrée et le contacteur W2 ou entre le contacteur et l’entrée de la section du hâcheur ; Module du hâcheur défectueux 247 Défaut de circuit du Le module 1 du hâcheur section A a détecté un défaut dans le circuit, module 1 du hâcheur 1A hâcheur défectueux 239 0560956430FR FONCTIONNEMENT 43 FONCTIONNEMENT 236 Décalage V c.a. Du hâcheur 3B 100i / 200i / 300i / 400i Code d’état CCM Groupe 2 -- Bloc d’alimentation en plasma FONCTIONNEMENT Code 44 Message Solution / Remarques 248 Défaut de circuit du Le module 1 du hâcheur section B a détecté un défaut dans le circuit, module 1 du hâcheur 1B hâcheur défectueux 249 Défaut de circuit du Le module 2 du hâcheur section A a détecté un défaut dans le circuit, module 2 du hâcheur 2A hâcheur défectueux 250 Défaut de circuit du Le module 2 du hâcheur section B a détecté un défaut dans le circuit, module 2 du hâcheur 2B hâcheur défectueux 251 Défaut de circuit du Le module 3 du hâcheur section A a détecté un défaut dans le circuit, module 3 du hâcheur 3A hâcheur défectueux 252 Défaut de circuit du Le module 3 du hâcheur section B a détecté un défaut dans le circuit, module 3 du hâcheur 3B hâcheur défectueux 253 Température excessive du hâcheur 1A La température du module hâcheur 1 section A est excessive ; enlever les panneaux latéraux pour travailler, vérifier que rien n’entrave l’écoulement d’air ni ne bouche le radiateur ; ventilateur défectueux ; si le problème persiste, remplacer le module hâcheur. 254 Température excessive du hâcheur 1B La température du module hâcheur 1 section B est excessive ; enlever les panneaux latéraux pour travailler, vérifier que rien n’entrave l’écoulement d’air ni ne bouche le radiateur ; ventilateur défectueux ; si le problème persiste, remplacer le module hâcheur. 255 Température excessive du hâcheur 2A La température du module hâcheur 2 section A est excessive ; enlever les panneaux latéraux pour travailler, vérifier que rien n’entrave l’écoulement d’air ni ne bouche le radiateur ; ventilateur défectueux ; si le problème persiste, remplacer le module hâcheur. 256 Température excessive du hâcheur 2B La température du module hâcheur 2 section B est excessive ; enlever les panneaux latéraux pour travailler, vérifier que rien n’entrave l’écoulement d’air ni ne bouche le radiateur ; ventilateur défectueux ; si le problème persiste, remplacer le module hâcheur. 257 Température excessive du hâcheur 3A La température du module hâcheur 3 section A est excessive ; enlever les panneaux latéraux pour travailler, vérifier que rien n’entrave l’écoulement d’air ni ne bouche le radiateur ; ventilateur défectueux ; si le problème persiste, remplacer le module hâcheur. 258 Température excessive du hâcheur 3B La température du module hâcheur 3 section B est excessive ; enlever les panneaux latéraux pour travailler, vérifier que rien n’entrave l’écoulement d’air ni ne bouche le radiateur ; ventilateur défectueux ; si le problème persiste, remplacer le module hâcheur. 259 Température ambiante excessive du hâcheur 1A La température excessive du circuit du hâcheur pourrait se devoir à une température ambiante de plus de 40 ºC ; réduire l’alimentation en coupant le facteur de marche ; réduire la température de l’air ambiant ; ajouter un radiateur supplémentaire. 260 Température ambiante excessive du hâcheur 1B La température excessive du circuit du hâcheur pourrait se devoir à une température ambiante de plus de 40 ºC ; réduire l’alimentation en coupant le facteur de marche ; réduire la température de l’air ambiant ; ajouter un radiateur supplémentaire. 261 Température ambiante excessive du hâcheur 2A La température excessive du circuit du hâcheur pourrait se devoir à une température ambiante de plus de 40 ºC ; réduire l’alimentation en coupant le facteur de marche ; réduire la température de l’air ambiant ; ajouter un radiateur supplémentaire. FONCTIONNEMENT 0560956430FR 100i / 200i / 300i / 400i Code d’état CCM Groupe 2 -- Bloc d’alimentation en plasma Code Message Solution / Remarques La température excessive du circuit du hâcheur pourrait se devoir à une température ambiante de plus de 40 ºC ; réduire l’alimentation en coupant le facteur de marche ; réduire la température de l’air ambiant ; ajouter un radiateur supplémentaire. 263 Température ambiante excessive du hâcheur 3A La température excessive du circuit du hâcheur pourrait se devoir à une température ambiante de plus de 40 ºC ; réduire l’alimentation en coupant le facteur de marche ; réduire la température de l’air ambiant ; ajouter un radiateur supplémentaire. 264 Température ambiante excessive du hâcheur 3B La température excessive du circuit du hâcheur pourrait se devoir à une température ambiante de plus de 40 ºC ; réduire l’alimentation en coupant le facteur de marche ; réduire la température de l’air ambiant ; ajouter un radiateur supplémentaire. 265 N° de puissance absorbée du hâcheur 1A La section du hâcheur pourrait ne pas avoir une puissance absorbée. Contacteur W1 non fermé ; contacteur défectueux ou CB4 déclenché ; section de hâcheur non connectée en entrée ; hâcheur défectueux. 266 N° de puissance absorbée du hâcheur 1B La section du hâcheur pourrait ne pas avoir une puissance absorbée. Contacteur W1 non fermé ; contacteur défectueux ou CB4 déclenché ; section de hâcheur non connectée en entrée ; hâcheur défectueux. 267 N° de puissance absorbée du hâcheur 2A La section du hâcheur pourrait ne pas avoir une puissance absorbée. Contacteur W1 non fermé ; contacteur défectueux ou CB4 déclenché ; section de hâcheur non connectée en entrée ; hâcheur défectueux. 268 N° de puissance absorbée du hâcheur 2B La section du hâcheur pourrait ne pas avoir une puissance absorbée. Contacteur W2 non fermé ; Contacteur défectueux ou CB4 activé ; Entrée de la section du hâcheur non connectée ; Hâcheur défectueux. 269 N° de puissance absorbée du hâcheur 3A La section du hâcheur pourrait ne pas avoir une puissance absorbée. Contacteur W2 non fermé ; Contacteur défectueux ou CB4 activé ; Entrée de la section du hâcheur non connectée ; Hâcheur défectueux. 270 N° de puissance absorbée du hâcheur 3B La section du hâcheur pourrait ne pas avoir une puissance absorbée. Contacteur W2 non fermé ; Contacteur défectueux ou CB4 activé ; Entrée de la section du hâcheur non connectée ; Hâcheur défectueux. 271 Défaut de lecture de l’identifiant du hâcheur Valeurs d’identifiant CCM trouvées inconsistantes lors de la lecture. CCM à une section de hâcheur, câble-ruban défectueux ou déconnecté, chemin du câble-ruban inapproprié Code d’état CCM Groupe 3 -- État et protocole du contrôleur de gaz & Code 301/302 303 0560956430FR Message Solution / Remarques Anomalie de réponse des communications avec le système de commande des gaz Problème avec le câble en fibre optique de la Console de sélection des gaz ou l’Unité de contrôle des gaz ; Saleté aux extrémités de la fibre ou dans les connecteurs ; souffler avec de l’air propre et sec. Fibre non verrouillée dans le connecteur; Fortes courbures dans leu câble de la fibre ; Fibre défectueuse; Bloc d’alimentation de la Console de sélection de gaz ou de l’Unité de commande de gaz défectueux ; Circuit imprimé de la Console de sélection de gaz ou de l’Unité de commande de gaz défectueux Pression de l’entrée de plasma ou de l’écran faible ou capteurs de appuyer Pression d’alimentation en surion PS3 et PS4 défectueux ; Pour la Commande automatique de gaz, esgaz hors limite. sayer l’Unité de commande de gaz pour détecter les défaillances de appuyer surion. FONCTIONNEMENT 45 FONCTIONNEMENT 262 Température ambiante excessive du hâcheur 2B FONCTIONNEMENT 100i / 200i / 300i / 400i 304 Purge de commande du gaz Suivi normal de la puissance ou du retour à partir de la désactivation du plasma. Attendre que la purge se termine. 305 Erreur de protocole de commande du gaz Vérifier que la version du firmware est compatible avec la Console de sélection de gaz et l’Unité de commande de gaz. 306 Non utilisé Réservé à une utilisation ultérieure 307 Erreur de séquence de commande du gaz Vérifier que la version du firmware est compatible avec la Console de sélection de gaz et l’Unité de commande de gaz 308 Incompatibilité de type de CCM incorrect pour le bloc d’alimentation ; installer un bon CMM commande du gaz 309 Erreur de commande du contrôle de gaz Vérifier que la version du firmware est compatible avec la Console de sélection de gaz et l’Unité de commande de gaz; interférences électromagnétiques avec le démarreur d’arc ; inspecter la mise à la terre, la métallisation et l’isolation. 310 * Défaillance de l’unité de commande de gaz Vérifier l’indicateur d’état de l’Unité de commande de gaz pour détecter un problème spécifique 311 * Défaillance du contrôle de Vérifier l’indicateur d’état de l’Unité de commande de gaz pour détecter un la soupape de l’Unité de problème spécifique commande de gaz 312 * Défaillance de la Console de sélection de gaz Vérifier l’indicateur d’état de la Console de sélection des gaz pour un problème spécifique 313 * Contrôleur de gaz non configuré. Console de sélection de gaz ou Unité de commande de gaz non configurées ou verrouillées ; Voir l’état de la Console de sélection de gaz et de l’Unité de commande de gaz * S’applique au commande automatique de gaz 3000 (gaz automatique) uniquemen Code d’état CCM Groupe 4 -- Système de refroidissement de la torche 46 Code Message Solution / Remarques 401 Niveau de liquide de refroidissement faible Vérifier le niveau du liquide de refroidissement, ajouter au besoin. Capteur de niveau défectueux ou déconnecté. 402 Faible débit du liquide de refroidissement Le débit de liquide de refroidissement tel que mesuré par le débitmètre FS1 est inférieur à 0,7 gpm (2,65 l/min) ; Filtre bouché ; Restriction au niveau du fil ou de la tête de la torche ; Mauvais styles de consommables ; Joint torique défectueux sur la soupape de contrôle de la torche ; tube de refroidissement ou clapet anti-retour de la torche rompu ou défectueux ; Pompe ou soupape de dérivation défectueux (se). Un code 402 accompagné d’un code 2104 indique vraisemblablement un problème de faible débit. 403 La température d’alimentation du liquide de refroidissement dépasse 75 degrés Celsius (167 F). Fonctionnement avec le panneau latéral lâche ou retiré ; CircuLiquidee de refroidisselation d’air bouchée à l’entrée d’air ou à la sortie de l’alimentation électrique ; ment surchauffé Défaillance du ventilateur du liquide de refroidissement ; ailettes du radiateur obstruées par de la saleté. 404 Le flux du liquide de refroidissement approprié de 0,07 gpm tel que mesuré par le débitmètre FS1 n’a pas été obtenu au bout de 4 minutes d’amorçage. Une nouvelle installation peut nécessiter de(s) cycle(s) d’amorçage(s) supplémentaire(s) pour remplir les tuyaux avec le liquide de refroidissement ; éteindre et Système de refroidisse- rallumer pour redémarrer l’amorçage ; Tuyaux du liquide de refroidissement et ment pas prêt. ceux de la torche inversés : Filtre du liquide de refroidissement bouché ; Restriction au niveau du fil ou de la tête de la torche ; Mauvais styles de consommables ; tube de refroidissement ou clapet anti-retour de la torche rompu ou défectueux ; Capteur de débit FS1 défectueux ou déconnecté. Pompe ou soupape de dérivation défectueux (se). FONCTIONNEMENT 0560956430FR 100i / 200i / 300i / 400i 405 Alarme de bas niveau Faible niveau du liquide de refroidissement lors de la coupe, mais n’arrête pas la du liquide de refroidiscoupe. Ajouter du liquide de refroidissement au besoin. sement 406 Ceci est un avertissement, qui n’interrompt pas le fonctionnement du système. Le débit du liquide de refroidissement est inférieur aux prévisions. Cela peut résulAlarme de bas débit de ter de bulles introduites dans le liquide de refroidissement ou de consommables liquide de refroidisse- erronés, mal assortis ou usés, de joints défectueux de la cartouche ou du corps ment de la torche, d’un filtre à liquide de refroidissement bouché, d’une restriction de la conduite ou de la tête de la torche, ou d’un débitmètre FL1 défectueux ou déconnecté. 407 Liquidee de refroidissement surchauffé, température ambiante élevée. La température du circuit de refroidissement dépasse 75 °C (167 °F), probablement parce que la température ambiante est supérieure à 40 °C (104 °F) ; réduire le facteur de marche de découpe ; réduire la température ambiante ; ajouter un système séparé de refroidissement du liquide. Code d’état CCM CCM-Groupe-5 Port de communication du contrôleur de gaz Message Solution / Remarques 501 Défaut de Câble de contrôle en fibre optique de la Console de sélection de gaz au CCM reconnaissance CANBUS non connecté, mal connecté ou défectueux. Bloc d’alimentation ou circuit de contrôle de la console de sélection de gaz défectueux. CCM défectueux, remplacer. 502 CANBUS arrêté Saleté aux extrémités de la fibre ou dans les connecteurs ; souffler avec de l’air propre et sec; Fibre non verrouillée dans le connecteur; Fortes courbures de la fibre optique ; Fibre defective 503 Avertissement d’erreurs CANBUS Saleté aux extrémités de la fibre ou dans les connecteurs ; souffler avec de l’air propre et sec; Fibre non verrouillée dans le connecteur; Fortes courbures de la fibre optique ; Fibre défectueuse; 504 Réservé Pas d’informations disponibles ; Contacter le service à la clientèle. Code d’état CCM Groupe 6 -- CCM Code Message Solution / Remarques 601 Erreur de tension analogique CCM défectueux, remplacer. 602 Erreur CAN ou CNA CCM défectueux, remplacer. 603 Réservé Pas d’informations disponibles ; Contacter le service à la clientèle. 604 Erreur de mémoire de données CCM défectueux, remplacer. 605 Défaillance mémoire du programme CCM défectueux, remplacer. 606 Bas niveau +5 V Logic CCM défectueux, remplacer. 607 Excès de température du processeur Réduire la température ambiante ; CCM défectueux; replace 608 Alimentation 5 V faible pour communication RS 485/422. CCM défectueux, remplacer. 609 Erreur du dispositif de mise à jour du micrologiciel CCM défectueux; replace 610 Erreur de protocole de mise à jour du micrologiciel CCM défectueux; replace 611 Défaillance contrôleur USB CCM défectueux; replace 0560956430FR FONCTIONNEMENT 47 FONCTIONNEMENT Code 100i / 200i / 300i / 400i 612 613 614 615 616 FONCTIONNEMENT 617 618 619 620 621 622 Défaillance alimentation USB Appareil USB défectueux branché sur le port USB ; l’enlever ; CCM défectueux Création de protocole USB défectueux Incapable de créer fichier journal sur lecteur Flash USB lors de la dernière tentative de mise à jour du micro-logiciel Utiliser un autre lecteur USB Flash ou reformater No USF File Fichier VTCCMFW. USF absent de Flash Entraînement; Ajouter des fichiers appropriés au lecteur Flash pour la mise à jour du firmware ; Utiliser un autre lecteur USB Flash ou reformater No CCM Mettre à jour File Logiciel CCM spécifié dans VTCCMFW.USF introuvable ; Ajouter des fichiers adéquats au lecteur Flash pour mettre à jour le micrologiciel Une panne est survenue lors de l’actualisation du firmware de l’Unité Erreur de mise à jour de l’unité de commande de gaz Ajouter des fichiers appropriés au lecteur Flash de commande de gaz USB pour la mise à jour du firmware; Se reporter à CCM_LOG.TXT sur le lecteur Flash pour plus de détails Erreur de mise à jour de la console de sélection de gaz Une panne est survenue lors de l’actualisation du firmware de la Console de sélection de gaz ; Ajouter des fichiers appropriés au lecteur Flash USB pour la mise à jour du firmware; Se reporter à CCM_LOG.TXT sur le lecteur Flash pour plus de détails Défaut étalonnage CAN Erreur d’étalonnage ADC trop grand, si la panne persiste, le CCM est défectueux ; Défaillance de l’interrupteur de Commutateur d’écoulement signalant le flux de liquide de refroidissedébit ment lors de la pompe; Erreur de mémoire ROM Le stockage de mémoire ROM a été corrompu et écrasé ; si la panne persiste, le CCM est défectueux. Erreur de formatage USB Une clé USB a été détectée mais ne peut pas être lue par le CCM. Faire une copie de sauvegarde de tous les fichiers se trouvant sur la mémoire flash, reformater la mémoire flash USB sous système de fichiers FAT ou FAT32, ne placer que les fichiers de mise à jour du CCM et essayer à nouveau. Utiliser différentes clés USB formatées sous système de fichiers FAT ou FAT32. Anomalie de l’exécution du code CCM Possible problème de bruit EMI ou de code de défaillance. Vérifier la bonne mise à la terre et métallisation de l’équipement et le routage des fils et des câbles de la torche afin de réduire l’interférence des émissions électromagnétiques sur le module CCM. Si le problème persiste, vérifier que la version du code CCM correspond à la dernière version compatible. Remplacer le module CCM. Code d’état CCM Groupe 7 -- Option Code 48 Message Solution / Remarques 701 Défaillance du contacteur d’isolation Le contacteur d’isolation W5 du 1Torch s’avère fermé alors qu’il devrait être ouvert. Les contacts peuvent être amorcés, ou le W5 pourrait être sous tension avec 24 V c.a. Sur la bobine, alors qu’il ne le devrait pas à cause d’un circuit de relais défectueux. 702 Défaillance du consommable du démarreur de contact Avant le pré-débit 1Torch, il doit y avoir continuité entre l’électrode, la cartouche de démarrage et la pointe. Cette défaillance peut être causée par des consommables usés ou manquants ou par la Cartouche de démarrage. Inspecter, nettoyer ou remplacer. 703 Dans le 1Torch, le module K201 doit se mettre sous tension lorsque le W5 Défaillance du circuit de détecle devient. Il n’a pas réussi à se mettre sous tension, ou le manostat PS2 tion du démarreur de contact est fermé en état d’échec. FONCTIONNEMENT 0560956430FR 100i / 200i / 300i / 400i Interrupteur de appuyer surion PS2 détecte moins que 35 PSI. La appuyer surion normale est de 75-85 PSI. Pas d’air connecté à l’entrée du module 1Torch ou pression trop faible ; si vous utilisez un filtre à étage unique, l’élément peut devoir être nettoyé ou remplacé, voir le chapitre sur l’entretien;Régulateur de pression 1Torch réglé trop bas; Le solénoïde SOL4 du module 1Torch a échoué ; Le circuit de relais ne transmet pas de tension 24 V c.a. Sur le SOL4. 704 Défaillance de appuyer surion du démarreur de contact 705 La appuyer surion de l’air doit séparer la Cartouche d’amorçage de la pointe pour démarrer le pilote. Cette défaillance peut être causée par Défaillance de la cartouche du une cartouche ou des consommables coincés ou endommagés. Nettoyer démarreur de contact ou remplacer. Ou pas de sortie CC des onduleurs, la LED CC du panneau avant ne s’allume pas. 4.04 Code d’état de la console de sélection de gaz Indicateurs de code d’état : 2. Indicateur vert •Voyant allumé en continu = OK, communication établie •Clignotement = pas de communication avec le CCM 3. Indicateur rouge •Off = État OK •Clignotement rapide = téléchargement d’un nouveau programme •Code à 2 chiffres clignotant = État (tableau ci-dessous) Les Indicateurs d’état sur les modules Console de sélection de gaz et l’Unité de commande de gaz indiquent en clignotant un code en 2 parties. Le voyant vert et le voyant rouge indiquent la version du firmware en clignotant au démarrage. Seul le voyant rouge clignote lors d’une défaillance. La première partie du code indique un groupe de codes, et la deuxième partie une condition particulière dans ce groupe. La Console de sélection de gaz et l’Unité de commande de gaz peuvent indiquer simultanément des codes clignotants et ces codes peuvent être différents. Par exemple, une défaillance du bloc d’alimentation, comme 1-3, sur la Console de sélection de gaz peut empêcher la communication avec l’Unité de commande de gaz afin que l’Unité de commande de gaz indique un des codes du groupe 2 en clignotant. Il faut prendre en considération les codes dans tous les modules, la CCM, la Console de sélection de gaz et l’Unité de commande de gaz avant de pouvoir déterminer quelle pièce présente une défaillance. Le code a 2 chiffres est séparé par un délai de 1,2 secondes entre les chiffres et un délai de 4 secondes avant que la séquence se répète ou qu’un autre groupe code clignote. Les codes affichés peuvent être actifs actuellement ou peuvent représenter une défaillance qui arrête le processus mais qui n’est plus actif actuellement. Si la défaillance qui a interrompu le processus n’est plus actif, le premier clignotement du premier chiffre est particulièrement long. Exemple : L’indicateur clignote 1 long suivi par 3 clignotements plus courte l’état est dans le groupe 4. Après un délai de 1,2 secondes, l’indicateur clignote 3 fois ; le code de condition est 4-3 (le premier clignotement long compte dans le premier chiffre), indiquant que la Console de sélection de gaz a détecté une erreur d’expiration de l’Unité de commande de gaz et qu’elle n’est pas actif actuellement. Après un délai de 4 secondes, l’indicateur répète la séquence jusqu’à ce que la condition soit corrigée. 0560956430FR FONCTIONNEMENT 49 FONCTIONNEMENT 1. Au démarrage, les indicateurs ROUGE et VERT clignotent indiquant le numéro de révision du firmware du programme en un code à 2 chiffres comme détaillé plus bas. Suivant le code de révision 100i / 200i / 300i / 400i Clé code d’état de la console de sélection de gaz Groupe 1 - Console de sélection de gaz Code Message Cause/Solution 1-1 Plasma désactivé Activation du plasma ; Bloc d’alimentation de la console de sélection de gaz défectueux (relais E-Stop) 1-2 Défaut 24 V c.c. Vérifier/remplacer le fusible du bloc d’alimentation de Console de sélection des gaz (F2) ; Remplacer le bloc d’alimentation de la console de sélection de gaz ; Remplacer le circuit de commande de la console de sélection de gaz 1-3 Défaut 5 V c.c. Vérifier/remplacer le bloc d’alimentation de la Console de sélection des gaz ; Remplacer le circuit de commande de la console de sélection de gaz 1-4 Aucun procédé choisi pour Sélectionner et envoyer un procédé depuis ou CNC ; les gaz 1-5 La console de sélection de gaz est verrouillée Chargement du procédé, attendre qu’il soit terminé 1-6 Gaz non purgé Une défaillance de l’unité de commande de gaz a empêché la purge de s’effectuer, voir l’état de la défaillance de l’unité de commande de gaz FONCTIONNEMENT Groupe 2 - Port de communication de l’unité de commande de gaz * 2-1 Erreur de reconnaissance de l’unité de commande de gaz Vérifier le câble en fibre optique et les connexions reliant la Console de sélection des gaz à l’Unité de commande de gaz ; Fibre optique sale ou défectueuse ;Bloc d’alimentation, fusible ou circuit de contrôle de l’unité de commande de gaz. Circuit de commande de la Console de sélection de gaz 2-2 Unité de commande de gaz Bus OFF error Vérifier le câble en fibre optique et les connexions reliant la Console de sélection des gaz à l’Unité de commande de gaz ; Fibre optique sale ou défectueuse ;Bloc d’alimentation, fusible ou circuit de contrôle de l’unité de commande de gaz. Circuit de commande de la Console de sélection de gaz. 2-3 Réservé Pas d’informations disponibles ; Contacter le service à la clientèle. 3-1 Erreur de reconnaissance CCM Vérifier le câble en fibre optique et les connexions reliant la Console de sélection des gaz au CCM ; Fibre optique sale ou défectueuse ; Remplacer Circuit de commande de la Console de sélection de gaz; Remplacer le CCM. 3-2 CCM Bus OFF error Vérifier le câble en fibre optique et les connexions reliant la Console de sélection des gaz au CCM ; Fibre optique sale ou défectueuse ; Remplacer Circuit de commande de la Console de sélection de gaz; Remplacer le CCM. 3-3 Réservé Pas d’informations disponibles ; Contacter le service à la clientèle. Groupe 3 - Port de communication CCM * Groupe 4 - Erreurs d’état et de protocole du contrôleur de gaz 4-1 Perte de la connexion CCM Perte de communication avec l’Unité de commande de gaz ou avec la Console de sélection de gaz, vérifier si la fibre optique de l’Unité de commande de gaz ou du CCM est sale ou défectueuse.; Voir les codes d’état de l’Unité de commande de gaz et du CCM 4-2 Temps expiré au CCM Perte de communication avec l’Unité de commande de gaz ou avec la Console de sélection de gaz, vérifier si la fibre optique de l’Unité de commande de gaz ou du CCM est sale ou défectueuse.. Voir les codes d’état de l’Unité de commande de gaz et du CCM. Groupe 5 - Court-circuit sur les solénoïdes 50 5-1 Sol 1 – Plasma au H35 Remplacer le solénoïde ; Faisceau de câbles court-circuité ; Circuit de commande de la Console de sélection de gaz défectueux 5-2 Sol 2 – Plasma à l’oxygène Remplacer le solénoïde ; Faisceau de câbles court-circuité ; Circuit de commande de la Console de sélection de gaz défectueux 5-3 Sol 3 – Plasma à l’air Remplacer le solénoïde ; Faisceau de câbles court-circuité ; Circuit de commande de la Console de sélection de gaz défectueux 5-4 Sol 4 – Plasma à l’azote Remplacer le solénoïde ; Faisceau de câbles court-circuité ; Circuit de commande de la Console de sélection de gaz défectueux 5-5 Sol 5 – Plasma auxiliaire Remplacer le solénoïde ; Faisceau de câbles court-circuité ; Circuit de commande de la Console de sélection de gaz défectueux FONCTIONNEMENT 0560956430FR 100i / 200i / 300i / 400i Sol 6 – Écran d’oxygène Remplacer le solénoïde ; Faisceau de câbles court-circuité ; Circuit de commande de la Console de sélection de gaz défectueux 5-7 Sol 7 – Écran d’air Remplacer le solénoïde ; Faisceau de câbles court-circuité ; Circuit de commande de la Console de sélection de gaz défectueux 5-8 Sol 8 – Écran d’azote Remplacer le solénoïde ; Faisceau de câbles court-circuité ; Circuit de commande de la Console de sélection de gaz défectueux 5-9 Sol 9 – Écran H2O Remplacer le solénoïde ; Faisceau de câbles court-circuité ; Circuit de commande de la Console de sélection de gaz défectueux 5-10 Sol 10 – Pré-débit d’oxygène Remplacer le solénoïde ; Faisceau de câbles court-circuité ; Circuit de commande de la Console de sélection de gaz défectueux 5-11 Sol 11 – Pré-débit à l’air Remplacer le solénoïde ; Faisceau de câbles court-circuité ; Circuit de commande de la Console de sélection de gaz défectueux 5-12 Sol 12 – Pré-débit à l’azote Remplacer le solénoïde ; Faisceau de câbles court-circuité ; Circuit de commande de la Console de sélection de gaz défectueux 5-13 Sol 13 – Marquage à l’argon Remplacer le solénoïde ; Faisceau de câbles court-circuité ; Circuit de commande de la Console de sélection de gaz défectueux 5-14 Sol 14 – Marquage à l’air Remplacer le solénoïde ; Faisceau de câbles court-circuité ; Circuit de commande de la Console de sélection de gaz défectueux 5-15 Sol 15 – Marquage à l’azote Remplacer le solénoïde ; Faisceau de câbles court-circuité ; Circuit de commande de la Console de sélection de gaz défectueux FONCTIONNEMENT 5-6 * Les pannes de communication illustrées sur la Console de sélection des gaz peuvent provenir de l’appareil à l’autre extrémité de la ligne de communication. Avant de présumer que la Console de sélection du gaz est à l’origine de la panne, vérifier si le CCM ou l’Unité de commande de gaz présente un code de nature à indiquer que la panne vient d’eux. 4.05 Codes de l’unité de commande de gaz Clé de code d’état de l’unité de commande de gaz Groupe 1 - Unité de commande de gaz Code Message Cause/Solution 1-1 Plasma désactivé Activation du plasma ; Fusible F1 du bloc d’alimentation de la Console de sélection de gaz grillé (voyant éteint sur la Console de sélection de gaz) ; Bloc d’alimentation de la console de sélection de gaz défectueux (relais E-Stop). Bloc d’alimentation de l’unité de commande de gaz défectueux (relais E-Stop). Circuit de contrôle de l’unité de commande de gaz défectueux 1-2 Défaut 24 V c.c. Vérifier/remplacer le fusible de sortie du bloc d’alimentation de l’Unité de commande de gaz (F2) ; Bloc d’alimentation de l’unité de commande de gaz défectueux; Remplacer le circuit de commande de l’unité de commande des gaz 1-3 Défaut +12 V c.c. Vérifier/remplacer le bloc d’alimentation de l’Unité de commande de gaz ; Remplacer le circuit de commande de l’unité de commande des gaz 1-4 Défaut -12 V c.c. Vérifier/remplacer le bloc d’alimentation de l’Unité de commande de gaz ; Remplacer le circuit de commande de l’unité de commande des gaz 1-5 Défaut 5 V c.c. Vérifier/remplacer le bloc d’alimentation de l’Unité de commande de gaz ; Remplacer le circuit de commande de l’unité de commande des gaz 1-6 Défaut de référence analogique Remplacer Circuit de contrôle de l’unité de commande de gaz 1-7 Défaut de tension CAN Remplacer Circuit de contrôle de l’unité de commande de gaz 1-8 Réservé 1-9 Soupape non configurée Renvoyer le processus depuis ou CNC 1-10 L’unité de commande de gaz est verrouillée Chargement du procédé, attendre qu’il soit terminé 0560956430FR FONCTIONNEMENT 51 100i / 200i / 300i / 400i Groupe 2 - Communication de contrôle 2-1 Erreur de reconnaissance Câble en fibre optique ; Circuit de contrôle de l’unité de commande de gaz 2-2 Temps expiré Perte de communication : Vérifier les codes de la Console de sélection des gaz ; Si la Console de sélection de gaz affiche 2-1 vérifier le câble en fibre optique reliant l’Unité de commande de gaz à la Console de sélection des gaz, si la Console de sélection des gaz affiche 4-2 vérifier le câble en fibre optique reliant la Console de sélection des gaz au CCM.; Circuit de contrôle de l’unité de commande de gaz; Circuit de commande de la Console de sélection de gaz; CCM. 2-3 Protocole Défaillance du firmware, contacter le fabricant 2-4 Bus OFF Câble en fibre optique ; Circuit de contrôle de l’unité de commande de gaz 2-5 Problème physique Câble en fibre optique ; Circuit de contrôle de l’unité de commande de gaz FONCTIONNEMENT Groupe 3 - Défaut de appuyer surion d’entrée 3-1 Haute appuyer surion de gaz du plasma (> 145 psi) Réduire la appuyer surion de l’alimentation en gaz ; capteur de appuyer surion défectueux (PS4). 3-2 Haute appuyer surion de gaz du pilote (> 145 psi) Réduire la appuyer surion de l’alimentation en gaz ; capteur de appuyer surion défectueux (PS3). 3-3 Haute appuyer surion de gaz de protection (> 145 psi) Réduire la appuyer surion de l’alimentation en gaz ; capteur de appuyer surion défectueux (PS1). 3-4 Haute appuyer surion de H2O de l’écran (> 145 psi) Réduire la appuyer surion de l’alimentation en gaz ; capteur de appuyer surion défectueux (PS2). Groupe 4 - Défauts des vannes proportionnelles et des solénoïdes électriques 4-1 Court-circuit aux hautes valeurs de plasma (V5) Vérifier le faisceau de câble pour y détecter tout court-circuit ; Remplacer la soupape 4-2 Vanne proportionnelle de basse appuyer surion de plasma (V4) Vérifier le faisceau de câble pour y détecter tout court-circuit ; Remplacer la soupape 4-3 Court-circuit au niveau du pilote (V3) Vérifier le faisceau de câble pour y détecter tout court-circuit ; Remplacer la soupape 4-4 Court-circuit au niveau du gaz de protection (V1) Vérifier le faisceau de câble pour y détecter tout court-circuit ; Remplacer la soupape 4-5 Court-circuit au niveau H2O d’écran (V2) Vérifier le faisceau de câble pour y détecter tout court-circuit ; Remplacer la soupape 4-6 Court-circuit à la soupape (SOL2) Vérifier le faisceau de câble pour y détecter tout court-circuit ; Remplacer la soupape 4-7 Court-circuit à la découpe (SOL3) Vérifier le faisceau de câble pour y détecter tout court-circuit ; Remplacer la soupape 4-8 Court-circuit au marquage (SOL1) Vérifier le faisceau de câble pour y détecter tout court-circuit ; Remplacer la soupape 4-9 Soupape (SOL2) ouverte Vérifier la présence de connexions ouvertes ; Remplacer la soupape. 4-10 Découpe (SOL3) ouverte Vérifier la présence de connexions ouvertes ; Remplacer la soupape. 4-11 Marquage (SOL1) ouvert Vérifier la présence de connexions ouvertes ; Remplacer la soupape. Groupe 5 - Vanne proportionnelle de haute appuyer surion de plasma (V5) 5-1 Soupape ouverte 5-2 Pression d’alimentation Augmenter la appuyer surion d’entrée de plasma ; vérifier que la soupape de la Console de d’entrée faible dans l’unité de sélection du gaz n’est pas ouverte; restrictions dans l’alimentation et les tuyaux à gaz. commande de gaz 5-3 La appuyer surion en sortie est trop basse Soupape ouverte à fond Leak in plasma hose to torch; robinet de régulation (V5) défectueux ; capteur de appuyer surion défectueux (PS6); Circuit de contrôle de l’unité de commande de gaz 5-4 Pression en sortie basse Erreur de surveillance Fuite du tuyau plasma de la torche ; robinet de régulation (V5) défectueux ; capteur de appuyer surion défectueux (PS6); Circuit de contrôle de l’unité de commande de gaz 52 Vérifier la présence de connexions ouvertes ; Remplacer la soupape. FONCTIONNEMENT 0560956430FR 100i / 200i / 300i / 400i Soupape réglée au minimum. Restrictions dans le tuyau à plasma, la torche, le collecteur de l’unité de commande des gaz ; robinet de régulation (V5) défectueux ; capteur de appuyer surion défectueux (PS6); Circuit de contrôle de l’unité de commande de gaz 5-5 Pression en sortie trop haute 6-1 Soupape ouverte 6-2 Pression d’alimentation Augmenter la appuyer surion d’entrée de plasma ; vérifier que la soupape de la Console de d’entrée faible dans l’unité sélection du gaz n’est pas ouverte; restrictions dans l’alimentation et les tuyaux à gaz. de commande de gaz 6-3 Pression en sortie trop basse La soupape est ouverte à fond mais la appuyer surion reste trop basse. Fuite dans le tuyau de plasma à la torche; Robinet de régulation défectueux (V4) ; capteur de pression défectueux(PS6); Circuit de contrôle de l’unité de commande de gaz 6-4 Pression en sortie basse Erreur de surveillance. Fuite dans le tuyau de plasma à la torche; Robinet de régulation défectueux (V4) ; capteur de pression défectueux (PS6); Circuit de contrôle de l’unité de commande de gaz 6-5 Pression de sortie trop élevée La soupape est réglée au minimum, mais la appuyer surion reste trop élevée. Restriction dans le tuyau à plasma vers la torche ; ou Unité de commande de gaz manifold; Robinet de régulation défectueux (V4) ; capteur de pression défectueux (PS6); Circuit de contrôle de l’unité de commande de gaz 6-6 Pression en sortie haute Erreur de surveillance. Restriction dans le tuyau à plasma ; torche or Unité de commande de gaz manifold; Robinet de régulation défectueux (V4) ; capteur de pression défectueux (PS6); Circuit de contrôle de l’unité de commande de gaz Groupe 6 - Vanne proportionnelle de basse appuyer surion de plasma (V4) Vérifier la présence de connexions ouvertes ; Remplacer la soupape. FONCTIONNEMENT Groupe 7 - Vanne proportionnelle du pilote (V3) 7-1 Soupape ouverte Vérifier la présence de connexions ouvertes ; Remplacer la soupape. 7-2 Pression d’alimentation Augmenter la appuyer surion d’entrée de plasma ; vérifier que la soupape de la Console de d’entrée faible dans l’unité sélection du gaz n’est pas ouverte; restrictions dans l’alimentation et les tuyaux à gaz. de commande de gaz 7-3 Pression en sortie trop basse La soupape est ouverte à fond mais la appuyer surion reste trop basse. Fuite dans le tuyau de plasma à la torche; robinet de régulation défectueux ; capteur de appuyer surion défectueux (PS6); Circuit de contrôle de l’unité de commande de gaz 7-4 Pression en sortie basse Erreur de surveillance. Fuite dans le tuyau de plasma à la torche; robinet de régulation défectueux ; capteur de appuyer surion défectueux (PS6); Circuit de contrôle de l’unité de commande de gaz 8-1 Soupape ouverte 8-2 Pression d’alimentation Augmenter la appuyer surion d’entrée de plasma ; vérifier que la soupape de la Console de d’entrée faible dans l’unité sélection du gaz n’est pas ouverte; restrictions dans l’alimentation et les tuyaux à gaz. de commande de gaz 8-3 Pression en sortie trop basse La soupape est ouverte à fond mais la appuyer surion reste trop basse. Fuite dans le tuyau de plasma à la torche; robinet de régulation défectueux ; capteur de appuyer surion défectueux (PS5). Circuit de contrôle de l’unité de commande de gaz 8-4 Pression en sortie basse Erreur de surveillance. Fuite dans le tuyau de plasma à la torche; robinet de régulation défectueux ; capteur de appuyer surion défectueux (PS5). Circuit de contrôle de l’unité de commande de gaz 8-5 Sortie appuyer surure Too high La soupape est réglée au minimum, mais la appuyer surion reste trop élevée. Restrictions dans le tuyau à plasma, la torche, le collecteur de l’unité de commande des gaz ; robinet de régulation défectueux ; capteur de appuyer surion défectueux (PS5). Circuit de contrôle de l’unité de commande de gaz 8-6 Pression en sortie haute Erreur de surveillance. Restrictions dans le tuyau à plasma, la torche, le collecteur de l’unité de commande des gaz ; robinet de régulation défectueux ; capteur de appuyer surion défectueux (PS5). Circuit de contrôle de l’unité de commande de gaz Groupe 8 - Vanne proportionnelle du gaz de protection (V1) 0560956430FR Vérifier la présence de connexions ouvertes ; Remplacer la soupape. FONCTIONNEMENT 53 100i / 200i / 300i / 400i FONCTIONNEMENT Groupe 9 - Vanne proportionnelle H2O d’écran (V2) 9-1 Soupape ouverte Vérifier la présence de connexions ouvertes ; Remplacer la soupape. 9-2 Pression d’alimentation Augmenter la appuyer surion d’entrée de plasma ; check for Console de sélection de gaz valve d’entrée faible dans l’unité not open; restrictions dans l’alimentation et les tuyaux à gaz. de commande de gaz 9-3 Débit en sortie trop bas La soupape est ouverte à fond mais la pression reste trop basse. Fuite dans le tuyau de gaz de protection vers la torche ; Robinet de régulation défectueux (V2) ; Capteur de appuyer surion (PS5) ou capteur de débit (FS-1) défectueux, s’il y a lieu ; Circuit de contrôle de l’unité de commande de gaz 9-4 Débit en sortie bas Erreur de surveillance, Pression en sortie trop faible. Fuite dans le tuyau de gaz de protection vers la torche ; Robinet de régulation défectueux (V2). Capteur de appuyer surion (PS5) ou capteur de débit (FS-1) défectueux, s’il y a lieu ; Circuit de contrôle de l’unité de commande de gaz 9-5 Débit en sortie trop élevé La soupape est ouverte au minimum mais la appuyer surion reste trop élevée. Accumulation de minéraux ou autres restrictions dans la soupape de contrôle (V2), le collecteur de l’Unité de commande de gaz, le tuyau d’écran ou la torche ; Robinet de régulation défectueux (V2). Capteur de appuyer surion (PS5) ou capteur de débit (FS-1) défectueux, s’il y a lieu ; Circuit de contrôle de l’unité de commande de gaz 9-6 Débit en sortie élevé Erreur de surveillance, appuyer surion en sortie trop haute. Accumulation de minéraux ou autres restrictions dans la soupape de contrôle (V2), le collecteur de l’Unité de commande de gaz, le tuyau d’écran ou la torche ; Robinet de régulation défectueux (V2) ; Capteur de appuyer surion (PS5) ou capteur de débit (FS-1) défectueux, s’il y a lieu ; Circuit de contrôle de l’unité de commande de gaz 4.06 Résolution des problèmes du démarreur d’arc à distance Résolution des problèmes de l’allumage de l’arc Symptôme Pas d’amorçage du pilote : l’indicateur au néon sur le panneau du couvercle s’allume, mais il n’y a pas d’amorçage. 54 Cause Vérification Solution Le fil de retour du pilote n’est pas connecté à la tête de la torche ou est rompu dans le fil de la torche Contrôle visuelle, contrôle de continuité Connecterer le câblage ou remplacer les fils. Le liquide de refroidissement devient un conducteur Utiliser un conductivimètre Purger le système, remplacer le liquide de refroidissement. Le condensateur à haute fréquence (C4 sur le circuit de Cond.) a peut-être ouvert des câbles déconnectés. Utiliser un capacimètre Reconnecterer ou remplacer. Le câble d’alimentation négatif Contrôle visuelle n’est pas bien connecté Reconnecter Le fil de retour du pilote n’est pas ou mal connecté dans le démarreur d’arc. Connecterer le câblage. Contrôle visuelle FONCTIONNEMENT 0560956430FR 100i / 200i / 300i / 400i 4.06 Résolution des problèmes du démarreur d’arc à distance Résolution des problèmes de l’allumage de l’arc Symptôme Cause Vérifier si un câble est en court-circuit, si le disjoncteur est défectueux, si l’entrée du module d’amorçage est court-circuité. (voir prochain symptôme) Pas d’alimentation 120 V, CB4 du plasma déclenché sur le panneau arrière Module d’allumage électronique court-circuité en entrée Mesure de résistance, les bonnes Remplacer un module défecmesures de résistance sont aux tueux alentours de 45 Ω 120 V présent - câble de contrôle ouvert ; 120 V absent - défaut d’alimentation électrique du plasma Module d’allumage électronique défectueux Raccord(s) desserré(s) Contrôle visuelle Resserrer les raccords. Conduite(s) du liquide de refroidissement endommagée(s) ou percée(s). Contrôle visuelle Remplacer les conduits de refroidissement FONCTIONNEMENT Vérifier l’alimentation électrique 120 V c.a. sur les connecteurs J59-7 et 9 du panneau arrière d’alimentation en plasma pendant la période d’amorçage. En cas de présence de la tenVérifier la tension 120 V c.a. Au sion 120 V c.a. mais si le néon niveau des bornes 115 V des mon’est pas allumé, le module dules pendant la phase d’amorest défectueux ; remplacer le çage du pilote module Fuites de liquide de refroidissement Inversion du tuyau d’arrivée et de retour Assortir les couleurs des connexions du liquide de Contrôle visuelle des connexions refroidissement à celles des à codes couleur raccords du démarreur de l’arc. Colmatage dans les tuyaux d’alimentation/retour Desserrer légèrement les raccords et vérifier le débit du liquide de refroidissement Purger le système ou remplacer le tuyau bouché. Mise à la terre inexistante ou desserrée Contrôle visuelle du fil de mise à la terre au démarreur de l’arc Faire ou resserrer les connexions pour une meilleure mise à la terre. Le bouclier du fil de la torche n’est pas relié ou lâche. Câble de mise à la terre F1 non connecté. Contrôle visuelle de la fixation de protection du fil au démarreur de l’arc Reconnecterer / serrer les connecteurs de fil. Comportement La vis de mise à la terre du panerratique du neau des condensateurs est Contrôle visuelle système (interfémanquante ou mal serrée. rence EMI) Condensateur C5 ou C7 (sur le circuit condensateur) ouvert Contrôle visuelle / mesure du ou fils déconnectés vers le condensateur panneau. 0560956430FR Solution Réinitialiser le coupe-circuit ; vérifier l’alimentation 120 V c.a. Sur les bornes 115 V du module pendant la durée d’amorçage. Aucun amorçage pilote : Indicateur au néon non Pas d’alimentation 120 V, CB4 allumé. non-déclenché Refroidissement inexistant ou insuffisant : Aucun débit du liquide de refroidissement Vérification FONCTIONNEMENT Serrer ou remplacer. Remplacer le circuit. 55 FONCTIONNEMENT 100i / 200i / 300i / 400i Cette page est intentionnellement laissée vierge. 56 FONCTIONNEMENT 0560956430FR 100i / 200i / 300i / 400i SECTION 5 : ENTRETIEN 5.01 Entretien général Effectuer régulièrement les vérifications suivantes pour garantir une performance optimale du système : Calendrier d’entretien du bloc d’alimentation Quotidien Vérifier le niveau du liquide de refroidissement ; Ajouter du liquide de refroidissement au besoin. Vérifier les branchements et la pression du tuyau de gaz. Vérifier le ventilateur de refroidissement, le nettoyer si besoin est. Hebdomadaire Vérifier les joints toriques de la torche et de la cartouche Mensuellement Vérifier le ventilateur de refroidissement et le radiateur ; le nettoyer si besoin est. S’assurer que les tuyaux de gaz ne présentent pas de craquelures, de fuites ou de marques d’abrasion. Les remplacer si nécessaire. Vérifier toutes les connexions électriques pour y repérer fissures et abrasions. Les remplacer si nécessaire. Nettoyer le filtre à eau (en cas de pulvérisation H2O) Tous les six mois Nettoyer ou remplacer le filtre du liquide de refroidissement. Nettoyer le réservoir du liquide de refroidissement. ENTRETIEN Éliminer à l’aide d’un aspirateur toute poussière accumulée dans le bloc d’alimentation. 5.02 Procédure de nettoyage du filtre externe du liquide de refroidissement Le nettoyage régulier du filtre du liquide de refroidissement permet de garantir une efficacité maximale du débit de liquide de refroidissement. Un faible débit du liquide de refroidissement entraîne un refroidissement insuffisant des pièces de la torche, entraînant une usure plus rapide des consommables. Vérifier le filtre du liquide de refroidissement de la façon suivante : 1. Déconnecter le système de l’alimentation d’entrée principale. 2. Dévisser et retirer la cartouche filtrante à la main. Grande cartouche filtrante située à l’arrière du bloc d’alimentation. S’assurer de conserver le joint torique. 3. Vérifier et remplacer le filtre si besoin est. Réinstaller la cartouche en la serrant manuellement. S’assurer que le joint torique est bien en place. 4. Allumer le système et vérifier la présence de fuites. 0560956430FR ENTRETIEN 57 100i / 200i / 300i / 400i 5.03 Procédures de remplacement des refroidissement Remplacer le liquide de refroidissement comme indiqué ci-dessous ; 1. Déconnecter le système de l’alimentation d’entrée principale. 2. Enlever les deux panneaux du côté droit. 3. Localiser le raccord du conduit du liquide de refroidissement provenant du fond du récipient du liquide de refroidissement, élément N°1 de l’illustration suivante. Déconnecter le conduit du liquide de refroidissement de ce raccord et évacuer le liquide dans un récipient jetable ‘une taille appropriée. Garder à l’esprit que vous viderez plus que les contenus du réservoir à liquide de refroidissement. 4. À la fin de l’évacuation du liquide de refroidissement, déconnecter le raccord du tuyau gris, élément N° 2 de l’illustration ci-dessous. Permettre l’évacuation du liquide de refroidissement excédentaire et appliquer ensuite une pression de 5 psi maximum pour dégager les conduites. ! MISE EN GARDE L’Application d’une pression d’air supérieure à 5 psi au système de refroidissement peut entraîner des dégâts. Il convient de prendre des précautions supplémentaires durant cette tâche. 2 ENTRETIEN 1 L'agent de refroidissement déborde égouttera par le port dans le fond d'unité via ce tuyau. Art # A11689FR 5. Reconnecter ces deux raccords et enlever ensuite la cuve du filtre de la cartouche filtrante à l’arrière du bloc d’alimentation. Verser le liquide de refroidissement restant dans le récipient et remplacer la cuve du filtre. REMARQUE! De même pour remplacer le liquide de refroidissement restant dans les fils, les déconnecter de l’alimentation et procéder à une évacuation manuelle. 6. Remplir le réservoir de liquide de refroidissement jusqu’au niveau indiqué ; vérifier qu’il n’y a pas de fuites. 7. Mettre le système en marche, le laisser fonctionner pendant quelques minutes et vérifier le niveau du liquide de refroidissement, remplir si besoin est. 8. Installer les panneaux latéraux. 58 ENTRETIEN 0560956430FR 100i / 200i / 300i / 400i SECTION 6 : ASSEMBLAGES ET PIÈCES DE RECHANGE 6.01 Rechange du bloc d’alimentation Unité complète / Composant Catalogue de numéro Alimentation électrique 100i, 480V 0559381162 Alimentation électrique 100i, 400V 0559381163 Alimentation électrique 100i, 400V CE 0559381164 Alimentation électrique 200i, 480V 0559381192 Alimentation électrique 200i, 400V 0559381193 Alimentation électrique 200i, 400V CE 0559381194 Alimentation électrique 300i, 480V 0559381182 Alimentation électrique 300i, 400V 0559381183 Alimentation électrique 300i, 400V CE 055938118 Alimentation électrique 400i, 480V 0559381202 Alimentation électrique 400i, 400V 0559381203 Alimentation électrique 400i, 400V CE 0559381204 Console de sélection de gaz 0559099491 Unité de commande de gaz 0559099493 Démarreur à distance de l’arc 0559039130 Bloc du Filtre du Liquidee de refroidissement 0559390155 Kit de roue 9-7378 PIÈCES DE RECHANGE 0560956430FR NOMENCLATURE DES PIÈCES 59 100i / 200i / 300i / 400i 6.02 Disposition du système 100 - 200 Amp 175’ / 53.3 m Longueur maximale 100’ / 30.5 m Longueur maximale 125’ / 38.1 m Longueur maximale F1 Alim. Primaire Retour du pilote A Négative B Alimentation de refroidisseur C Retour de refroidisseur D Câble de contrôle E Fibre optique W P F Contrôleur d'Écran de Contact L Câble de contrôle V Blindage Démar reur à distance de l'arc Alimentation de refroidisseur Retour de refroidisseur Blindage F1 Alime ntation CNC Retour du pilote Câble au sol à PS seulement lorsque DMC monté sur le dessus de PS si ce n’est pas - Terre- K Console du Gaz F Gaz plasmagène H Gaz plasmagène I Fibre optique L Gaz de protection J G Q Gaz de protection R Pré-débit Câble de contrôle S Écran d'eau T Marquage U Contrôle de gaz Tubes de positionnement F Torche Travail O Câble de masse Art # A-14027FR 175’ / 53.3 m Longueur maximale 6.03 Disposition du système 300 Amp 175’ / 53.3 m Longueur maximale 125’ / 38.1 m Longueur maximale F1 Alim. Primaire Retour du pilote A Négative B Alimentation de refroidisseur C Retour de refroidisseur D Câble de contrôle E PIÈCES DE RECHANGE Fibre optique W P F Contrôleur d'Écran de Contact Câble de contrôle V 60 Blindage Démar reur à distance de l'arc Alimentation de refroidisseur Retour de refroidisseur Blindage Câble au sol à PS seulement lorsque DMC monté sur le dessus de PS si ce n’est pas - Terre- K F H Gaz plasmagène I Fibre optique L Gaz de protection J Gaz de protection Q Pré-débit R Gaz plasmagène L Console du Gaz Câble de contrôle S Écran d'eau T Marquage U Contrôle de gaz G Tubes de positionnement F Torche Travail Câble de masse Art # A-14026FR Retour du pilote F1 Alime ntation CNC 50’ / 15.25 m Longueur maximale O 175’ / 53.3 m Longueur maximale NOMENCLATURE DES PIÈCES 0560956430FR 100i / 200i / 300i / 400i 6.04 Disposition du système 400 Amp 175’ / 53.3 m Longueur maximale 125’ / 38.1 m Longueur maximale F1 50’ / 15.25 m Longueur maximale Retour du pilote #8 A Négative 2/0 B Câble de contrôle Alim. Primaire Alime ntation CNC C Retour de refroidisseur 10’ D Câble de contrôle Y Fibre optique W P F Alimentation de refroidisseur 10’ C C M Contrôleur d'Écran de Contact V Câble de contrôle Câble au sol à PS seulement lorsque DMC monté sur le dessus de PS si ce n’est pas - Terre- Blindage E Chaleur Échangeur Alimentation de refroidisseur C Retour de refroidisseur D Démar reur à distance de l'arc Alimentation de refroidisseur Retour de refroidisseur Blindage F1 Gaz plasmagène L K F Retour du pilote Console du Gaz H Gaz plasmagène I Fibre optique L Gaz de protection J Gaz de protection Q Pré-débit R Câble de contrôle S Écran d'eau T Marquage U Contrôle de gaz G Tubes de positionnement F Torche Travail Câble de masse Art # A-14028FR O 175’ / 53.3 m Longueur maximale 6.05 Tuyau recommandé pour l’alimentation en gaz Article n° Qté 1 Description Catalogue n° 3/8”Tuyau Gray Synflex. Aucun raccord inclus. Numéro de catalogueue par pied 9-3616 PIÈCES DE RECHANGE 0560956430FR NOMENCLATURE DES PIÈCES 61 100i / 200i / 300i / 400i 6.06 Fils et câbles toutes intensités Retour de l’arc pilote, du générateur à l’amorce de l’arc A Câble 3/0 AWG (95 mm2 ) Câble négatif, du générateur à l’amorce de l’arc B C Vert Vert Câble d’alimentation du liquide de refroidissement, du générateur à l’amorce de l’arc D Rouge Rouge Câble de retour du liquide de refroidissement, du générateur à l’amorce de l’arc E - Câble de commande, du générateur à l’amorce de l’arc E,Y 14/7 Y - Câble de commande de l’échangeur de chaleur AWG n° 4 vert / jaune F 1/0 vert / jaune (50 mm2) F1 Câble de masse Câble de masse, de l’amorce de l’arc à distance à la mise à la terre G Câble de la torche blindé, de l’amorce de l’arc à distance à la torche I Câble du gaz plasmagène, de la valve de la torche à la torche J Câble du gaz de protection, de la valve de la torche à la torche K Câble de commande, du générateur au module de commande du gaz 37 Câble à fibre optique, du générateur au module de commande du gaz L PIÈCES DE RECHANGE Art # A-11997FR Câble AWG n° 8 Pour une utilisation avec le DFC-3000 H, Q, R,T, U S - Câble de commande, du DMC-3000 au DPC-3000 S,V 16 pin V - TSC-3000 au PS Câble 3/0 (95 mm )2 O P 62 37 Câble de mise à la terre Câble CNC (fil 37) NOMENCLATURE DES PIÈCES 0560956430FR 0560956430FR NOMENCLATURE DES PIÈCES 63 4 ft 1,2 m 10 ft 15 ft 3,05 m 4,5 m 20 ft 6m 25 ft 7,6 m 30 ft 9,1 m 35 ft 40 ft 10,6 m 12 m 50 ft 60 ft 75 ft 100 ft 125 ft 150 ft 175 ft 200 ft 15,2 m 18,3 m 22,8 m 30,5 m 38,1 m 45,7 m 53,3 m 61 m 225 ft 68,6 m Réglage du fil d’alimentation 4-3096 4-3097 4-3098 4-3099 4-3100 4-3101 4-3105 4-3102 4-3103 4-3104 4-3109 4-3110 (Remarque 1) Câble de retour du pilote 9-4890 9-4891 9-4790 9-4791 9-9426 9-4792 4-3200 9-4793 9-4794 9-4796 9-7454 9-7455 Câble négatif 9-7356 9-7357 9-7358 9-7359 9-7360 9-7361 4-3201 9-7362 9-7363 9-7364 9-7456 9-7457 Tuyau, alimentation du C 9-4805 9-4887 9-4806 9-4807 9-9424 9-4808 4-3202 9-4809 9-4810 9-4812 9-7458 9-7465 liquide de refroidissement Tuyau, retour du liquide de D 9-4813 9-4889 9-4814 9-4815 9-9425 9-4816 4-3203 9-4817 9-4818 9-4820 9-7466 9-7467 refroidissement Câble de contrôle au déE 9-4941 9-4916 9-4917 9-4918 9-9428 9-4942 4-3205 9-4943 9-4944 9-4922 9-7468 9-7469 marreur d’arc Fil de mise à la terre, PS F 9-4923 9-4924 9-4925 9-4926 9-4927 9-4928 9-4929 9-4930 vers GCM Fil de mise à la terre, AS à F1 9-4931 9-4932 9-4933 9-4934 9-4935 9-4936 9-4937 9-4938 distance vers terre G Assemblage, fil de la torche 4-5200 4-5201 4-5202 4-5203 4-5204 4-5205 4-5206 4-5207 4-3016 I Fil plasma 9-3333 J Câble blindé 9-3334 Câble de contrôle, PS vers K 9-4907 9-4908 9-4909 9-9332 9-4910 9-4911 9-4912 9-4913 9-4914 9-4967 9-4968 DMC 3000 O Câble de masse 9-7350 9-7351 9-7352 9-7353 Câble de contrôle, CNC P 9-7368 9-7369 9-7370 9-7371 9-7372 vers PS H,L,Q,R, Auto Gas Lead Set (Note 4-3086 4-3087 4-3088 4-3089 4-3090 4-3091 4-3092 4-3093 4-3094 4-3095 S,T, U 2) H Tuyau à gaz plasmagène 9-7103 9-7104 8-0149 9-7270 9-7271 9-7272 9-7273 9-7274 9-7275 9-7276 Fibre optique du câble de L 9-4898 9-4899 9-4900 9-9335 9-4901 9-4902 9-4903 9-4904 9-4905 9-4906 9-4967 9-4968 contrôle Q Tuyau du gaz de protection 9-7277 9-7278 9-7279 9-7280 9-7281 9-7282 9-7283 9-7284 9-7285 9-7286 Tuyau de gaz/pré-débit R 9-6956 9-6957 9-6959 9-6961 9-6963 9-6964 9-7080 9-7081 9-4876 9-4877 pilote S Câble de contrôle 9-7093 9-7094 9-7095 9-7096 9-7097 9-7098 9-7099 9-7100 9-7101 9-7102 T Écran d’eau 9-6985 9-6986 9-6987 9-6988 9-6989 9-6996 9-6991 9-6992 9-6993 9-7073 9-7074 9-7075 9-7076 U Câble de marquage 9-4725 9-4726 9-4727 9-4728 9-4729 9-4730 9-4731 9-4732 9-4733 9-4734 9-7077 9-7078 9-7079 Câble de commande à V 9-9230 9-9231 9-9232 9-9233 9-9234 9-9235 9-9236 9-9237 9-9238 9-9239 distance Câble de commande de W 9-8674 9-8675 9-8676 9-8677 9-8678 9-8679 9-8680 communication, CNC REMARQUE 1: Alimentation lead sets inslude Câble de retour du pilote, Câble négatif, Approvisionnement en liquide de refroidissement & Retourner Hoses and Câble de contrôle. NOTE 2: Auto Gas lead sets include Tuyau à gaz plasmagène, Tuyau du gaz de protection,Fibre optic cable, Preflow Gas Hose, Écran d’eau and Câble de contrôles individually, not combined. Description PIÈCES DE RECHANGE A,B,C, D,E A B Clé Fils de la torche 100i, 200i, 300i, 400i 100i / 200i / 300i / 400i 100i / 200i / 300i / 400i 6.07 Pièces de rechange externes du bloc d’alimentation Article n° Qté Description Catalogue n° 0559235533 1 1 Couvercle des câbles d’alimentation et des fils 2 1 Panneau supérieur,0559097300 3 1 Couvercles supérieurs0559097301 4 1 Panneau inférieur gauche 0559097304 5 1 Panneau inférieur droit 0559097344 7 1 Œillet de levage 9-9373 J55 - GCM USER INPUT J15 - CNC HEIGHT CONTROL J54 - TSC /COMM J59 - RAS Art # A-13976 CB2 - 5A 120 VAC CB3 - 5A 24 VAC J70 - HE CB4 - 5A 120 VAC F1 - 8A SB 230 VAC 1 F2 - 8A SB 230 VAC 1 7 2 3 3 5 PIÈCES DE RECHANGE 4 64 NOMENCLATURE DES PIÈCES 0560956430FR 100i / 200i / 300i / 400i 6.08 Pièces de rechange du bloc d’alimentation - Côté supérieur droit Article n° Qté Description Réf. des. Catalogue n° 1 1 Circuit imprimé de polarisation du système 9-9253 2 1 Circuit imprimé du pilote 3 1 Montage CCM 0559097335 4 1 Relais, Pompe / ventilateur MC3 / MC2 9-7314 5 1 Relais, Commande d’appel K1 9-7336 6 1 Relais, appel de courant MC1 9-7337 7 1 Résistance, appel de courant R2 9-7376 8 1 Afficher le circuit imprimé 9-9252 9 1 Auxilliar Transformer T1 9-7315 10 1 Interrupteur Marche/Arrêt du disjoncteur CB1 9-7316 11 1 Circuit imprimé de relais et d’interface 9-9250 9-9251 1 2 11 10 9 8 3 7 6 5 PIÈCES DE RECHANGE 4 Art # A-11546_AB 0560956430FR NOMENCLATURE DES PIÈCES 65 100i / 200i / 300i / 400i 6.09 Pièces de rechange du bloc d’alimentation - Côté inférieur droit Article n° Qté Description Réf. des. Catalogue n° 1 1 Couvercle du réservoir de refroidissement 8-5142 2 1 Réservoir du liquide de refroidissement 9-7306 3 1 Capteur de niveau de liquide de refroidissement 9-7307 4 1 Pompe, liquide de refroidissement, montage (avec moteur) 9-7309 1 Pompe, liquide de refroidissement, montage (pas de moteur) 9-7422 5 1 Moteur, pompe (moteur uniquement) 9-7424 6 1 Ventilateur(s) de refroidissement Unique et grand pour les systèmes 300 A / 400 A 9-7348 Deux plus petits pour les systèmes 100 A/200 A 7 1 Radiateur 9-7312 9-7349 9-7311 Systèmes 300 A/400 A Systèmes 100 A/200 A 8 1 Flow, Switch (Not shown) FS1 9-7310 9 1 Détecteur de bulles (débit) (non illustré) FL1 9-9359 10 1 Transducteur de courant, 300 A (non illustré) HCT1 W7005324 Art # A-11984_AC 1 2 PIÈCES DE RECHANGE 3 9 4 7 8 5 6 66 NOMENCLATURE DES PIÈCES 0560956430FR 100i / 200i / 300i / 400i 6.10 Pièces de rechange du bloc d’alimentation - Panneau arrière Article n° Qté Description Calibre du disjoncteur Calibre du circuit Réf. des. Catalogue n° 1 1 Bloc du Filtre du Liquide de refroidissement 0559390155 2 1 Liquidee de refroidissement Filter 3 1 Fusible, 8 A 500 V - Délai (2 total) 9-7377 9-7321 1 J55 - GCM USER INPUT J15 - CNC HEIGHT CONTROL 2 J54 - TSC /COMM J59 - RAS CB2 - 5A 120 VAC CB3 - 5A 24 VAC 4 J70 - HE 6 7 CB4 - 5A 120 VAC 5 F1 - 8A SB 500 VAC F2 - 8A SB 500 VAC 3 Art # A-11549_AD PIÈCES DE RECHANGE 0560956430FR NOMENCLATURE DES PIÈCES 67 100i / 200i / 300i / 400i 6.11 Pièces de rechange du bloc d’alimentation - Côté gauche Article n° Qté 1 2 3 1 1 1 Description Réf. des Catalogue n° Circuit de supappuyer surion c.a. Contacteur principal (2 total) W1, W2 Module d’onduleur, Full, 480 VAC 9-9254 9-7318 9-7330 3 1 Module de l’onduleur, complet, 400 VAC (100 and Système 200 As use 1) 9-7317 (Le système 300 A en utilise 2) (Le système 400 A en utilise 3) 4 1 Module de l’onduleur, 480 VAC partiel (pour 200 A et 300 A UNIQUEMENT) 9-7331 4 1 Module de l’onduleur, 400 VAC partiel (pour 200 A et 300 A UNIQUEMENT) 9-7319 5 1 EMI Filtre PCB 9-9264 (Les systèmes 100 A en utilisent 1) (Les systèmes 200 A en utilisent 2) (Les systèmes 300 A en utilisent 3) (Les systèmes 400 A en utilisent 4) Le cordon câble du module onduleur à CCM, NON montré Le Câble de Cordon, 30Ckt, l’onduleur 1A à CCM 9-7431 1 Le Câble de Cordon, 30Ckt, l’onduleur 1B à CCM 9-7432 1 Le Câble de Cordon, 30Ckt, l’onduleur 2A à CCM 9-7433 1 Le Câble de Cordon, 30Ckt, l’onduleur 2B à CCM 9-7434 1 Le Câble de Cordon, 30Ckt, l’onduleur 3A à CCM 9-7435 1 Le Câble de Cordon, 30Ckt, l’onduleur 3B à CCM 9-7436 PIÈCES DE RECHANGE 1 68 NOMENCLATURE DES PIÈCES 0560956430FR 100i / 200i / 300i / 400i Bloc d'alimentation 400 A Bloc d'alimentation 200 A 1 2 4 3 Art # A-12185FR Non CE 400 A d'alimentation 200 A d'alimentation 1 2 4 5 5 PIÈCES DE RECHANGE 3 Art # A-11943FR CE ONLY 0560956430FR NOMENCLATURE DES PIÈCES 69 100i / 200i / 300i / 400i 6.12 Système de contrôle automatisé des pièces de remde l’endroit Article n° Qté Description Catalogue n° 1 1 Assemblage de la console de sélection du gaz 0559099491 2 1 Assemblage unité de commande de gaz 0559099443 PIÈCES DE RECHANGE Art # A-13242 Art # A-13243 70 NOMENCLATURE DES PIÈCES 0560956430FR 100i / 200i / 300i / 400i 6.13 Pièces de rechange du console de sélection de gaz Article n° Qté Description Catalogue n° 0559099491 1 1 Montage de contrôle de sélection de gaz 2 1 Solénoïde 9-8264 3 1 Montage de distribution (inclut 15 de l’article 2) 9-7546 4 1 Circuit SMPS 9-8263 5 1 Circuit imprimé de contrôle 9-7291 6 1 Kit adoucisseur d’eau WMS (inclut les éléments suivants) 9-1068 7 1 WMS Remplacement Filter Cartouche 9-1069 8 1 WMS Filter Boîtier 9-1070 9 1 Support de montage de filtre WMS 9-4523 10 1 Raccord et tuyau du filtre WMS 9-4524 Non illustré : 5 4 2 15 au total PIÈCES DE RECHANGE Art # A-09163FR_AC 1 3 0560956430FR NOMENCLATURE DES PIÈCES 71 100i / 200i / 300i / 400i 6.14 Pièces de rechange du unité de commande de gaz Article n° Qté Description Catalogue n° 1 1 Ensemble de l’unité de commande de gaz 0559099443 2 1 Unité de commande de gaz - PCB 9-8262 3 1 Circuit SMPS 9-8263 4 1 Soupape P du gaz de protection 9-8267 5 1 Capteur, Pression, 1/8 mnpt (6 au total) 9-8269 6 1 Solénoïde 9-8264 7 1 Soupape plasma faible et de pré-débit 9-8268 8 1 Collecteur de l’unité de commande de gaz entièrement assemblé 9-7658 1 2 3 6 PIÈCES DE RECHANGE Art # A-09164_AC 4 7 7 8 5 72 NOMENCLATURE DES PIÈCES 0560956430FR 100i / 200i / 300i / 400i 6.15 Pièces de rechange de démarreur d’arc à distance (RAS) Article n° Qté Description Catalogue n° 1 1 Montage RAS complet 0559039130 2 1 Montage du condensateur pilote 9-9423 3 1 Module d’allumage électronique 9-7342 4 1 Bobine toroïdale 9-7343 1 2 3 4 Art # A-12066 PIÈCES DE RECHANGE 0560956430FR NOMENCLATURE DES PIÈCES 73 100i / 200i / 300i / 400i PIÈCES DE RECHANGE Cette page est intentionnellement laissée vierge. 74 NOMENCLATURE DES PIÈCES 0560956430FR 100i / 200i / 300i / 400i SECTION 7 : ENTRETIEN DE LA TORCHE 7.01 Enlèvement Consommable 1. Utiliser l'outil d'extraction pour bloquer le Godet de protection et l'Ensemble de la cartouche. Tourner le Godet de protection pour l'extraire de l'Ensemble de la cartouche. Outil pour la cartouche Cartouche montée Art # A-04344 Jupe 2. Retirer l'outil d'extraction de l'arrière du montage de la cartouche. Utiliser l'outil d'extraction pour extraire les pièces consommables hors de la Cartouche. Outil pour la cartouche Cartouche Art # A-04345 ENTRETIEN DE LA TORCHE 0560956430FR INFORMATIONS RELATIVES À LA TORCHE 75 100i / 200i / 300i / 400i 7.02 Lubrification du joint torique Lubrifier régulièrement les trois joints toriques sur l'assemblage de la cartouche et les trois joints toriques sur la tête de la torche à l'aide du lubrifiant spécifique fourni. Retirer la bague élastique sur l'ensemble de la cartouche et faire glisser l'anneau de blocage vers le bas pour accéder au joint torique sous l'anneau de blocage. Joint torique interne (n° cat. 8-0545) Emplacement (sous la bague de serrage) Joints toriques Joint torique, n° cat. 8-0544 Joint torique, n° cat. 8-0540 Corps de torche N° cat. 9-9041 N° cat. 8-0524 Cartouche N° cat. 9-3026 Circlip N° cat. 9-3025 Art # A-04071 N° cat. 9-9429 Art # A-04066FR_AE Joint torique du connecteur intérieur (Nº cat. 9-3030) Emplacement (Sous vitesse joint torique du connecteur de blocage) Joint torique, Cat. nº 9-3029 Joint torique, Cat. nº 9-3028 Joint torique, Cat. nº 8-0547 Assemblage de cartouche Speed-Lock Bague et bague filetée pour plus de clarté Art # A-09684FR_AD ENTRETIEN DE LA TORCHE ! 76 Joint torique, Cat. nº 8-0561 Joint torique, Cat. nº 9-3029 Cartouche externe MISE EN GARDE Utilisez la ESAB No. 9-4893 du Lubrifiant d'O- anneau (l'Huile de graissage de Christo MCG129) avec cette partie de torche. L'utilisation d'autres lubrifiants peut provoquer le dommage irréparable à la torche. INFORMATIONS RELATIVES À LA TORCHE 0560956430FR 100i / 200i / 300i / 400i 7.03 Vêtements de Parties Remplacer le distributeur de gaz s'il est brûlé ou craquelé. Remplacer le distributeur de gaz si la bride est endommagée de quelque façon que ce soit. Remplacer la pointe et/ou l'électrode si elles sont abîmées. Tuyère usagée Tuyère en bon état Electrode en bon état Electrode usagée Art # A-04745 ENTRETIEN DE LA TORCHE 0560956430FR INFORMATIONS RELATIVES À LA TORCHE 77 100i / 200i / 300i / 400i 7.04 Installation des consommables de la torche MISES EN GARDE Ne pas placer de consommables dans la cartouche quand celle-ci est fixée au corps de la torche. Faire en sorte qu’aucun matériau étranger ne pénètre dans les consommables et la cartouche. Manipuler soigneusement toutes les pièces afin d’éviter de les endommager car cela pourrait affecter les performances de la torche. Art # A-03887FR 1. Installez les consommables comme suit : 1: Empiler les pièces 2: Appuyer la cartouche contre les pièces empilées Electrode Distributeur du gaz plasmagène Joint torique supérieur sur la tuyère Aucun vide entre les pièces Tuyère Distributeur du gaz de protection La cartouche couvre le joint torique supérieur sur la tuyère de la torche Coiffe de protection 3: Enfiler la jupe sur la cartouche 4: Contrôler que la jupe dépasse ENTRETIEN DE LA TORCHE Jupe Bouclier cap La coiffe de protection dépasse de 0.063-0.083" (1,6 – 2,1 mm) Art # A-04716FR 2, Retirez l'Outil de démontage de cartouche et installez la Cartouche assemblée sur la Tête de la torche. 78 INFORMATIONS RELATIVES À LA TORCHE 0560956430FR 100i / 200i / 300i / 400i ! MISE EN GARDE L'ensemble de la cartouche doit couvrir le joint torique sur la tête de la torche. Éviter de forcer la cartouche si elle n'est pas entièrement serrée. Enlever la cartouche et nettoyer délicatement les fils du corps de la tête de la torche à l'aide d'une brosse métallique. Appliquer le lubrifiant compatible à l'oxygène (fourni avec la torche) sur les fils. Corps de torche Joint torique du corps de torche Saillie de 0.063 - 0.083" (1,6 – 2,1 mm) Art # A-07202FR Installation de la cartouche sur le corps de torche 3. Faites glisser le clip ohmique au-dessus du bouclier si vous utilisez la détection du contrôle de la hauteur de la torche ohmique. REMARQUE ! La détection de la hauteur ohmique est déconseillée avec un brouillard d'eau. L'eau sur la plaque interfère électriquement avec le circuit de détection ohmique. Borne du capteur ohmique A-03393 4. Connectez le câble de sortie du détecteur de hauteur au clip ohmique. ENTRETIEN DE LA TORCHE 0560956430FR INFORMATIONS RELATIVES À LA TORCHE 79 100i / 200i / 300i / 400i 7.05 Fuite de liquide de refroidissement dépannage Ne jamais utiliser le système si du liquide de refroidissement fuit de la torche. Un égouttement régulier indique que des parties de la torche sont endommagées ou mal installées. Utiliser le système dans ces conditions peut endommager la tête de la torche. Consulter le diagramme suivant pour plus d'informations à propos des fuites de liquide de refroidissement au niveau de la tête de la torche. La torche fuit Les consommables de la torche sont-ils montés ? Non Fuite provenant de l’alimentation ou du retour du liquide de refroidissement ? Oui Les pièces sontelles neuves ou utilisées ? Retour Commander le kit du clapet de non-retour du liquide de refroidissement 9-4846 Alimentation Commander le kit de rechange du tube du liquide de refroidissement Les pièces sont probablement usagées. Consulter le tableau pour connaître la durée de vie moyenne. Usagé Il se peut que la torche soit endommagée. Voir la page pour déterminer si le corps a été endommagé. Neuf Les pièces sontelles entièrement montées dans la torche ? Oui La torche est-elle endommagée ? Non Vous n’êtes pas sûr ? Enlever et lubrifier tous les joints toriques sur le corps de torche, la cartouche de consommables et les consommables. Remonter la torche. Fuit-elle encore ? Oui Oui Démonter entièrement et remonter la torche correctement. Consulter le manuel d’installation. Remplacer le corps de torche Oui Remplacer la cartouche des consomambles et la jupe. La torche fuit-elle encore ? ENTRETIEN DE LA TORCHE Art # A-09638FR Torch Electrodes Art # A-09653FR 80 INFORMATIONS RELATIVES À LA TORCHE 0560956430FR 100i / 200i / 300i / 400i Ampérage 30 50 70 100 150 200 250 300 400 Recommandé pour la profondeur d'usure de remplacement de l'électrode Gaz plasmagène Pouce mm O2 0,04 1 Air 0,04 1 N2 0,04 1 O2 0,04 1 Air 0,08 2 N2 0,04 1 O2 0,04 1 Air 0,08 2 N2 0,04 1 O2 0,04 1 H35 0,08 2 N2 0,08 2 O2 0,06 1,5 H35 0,08 2 N2 0,08 2 O2 0,06 1,5 H35 0,08 2 N2 0,08 2 O2 0,06 1,5 O2 0,06 1,5 H35 0,08 2 N2 0,08 2 O2 0,08 2 H17 0,08 2 H35 0,08 2 N2 0,08 2 ENTRETIEN DE LA TORCHE 0560956430FR INFORMATIONS RELATIVES À LA TORCHE 81 100i / 200i / 300i / 400i ENTRETIEN DE LA TORCHE Cette page est intentionnellement laissée vierge. 82 INFORMATIONS RELATIVES À LA TORCHE 0560956430FR 0560956430FR ANNEXE Art # A-14024FR_AB Trop-plein Alimentation Réservoir du liquide de refroidissement 1 Plaque de refroidissement 2 Plaque de refroidissement 3 Pompe Capteur de température HS1 Interrupteur de niveau Retour de refroidisseur Radiateur Clapet Débit Débit Interrupteur de débit Alimentation en liquide de refroidissement de la torche Filtre1 Retour de liquide de refroidissement de la torche ANNEXE Plaque de refroidissement POUR SYSTÈMES 400 A 100i / 200i / 300i / 400i ANNEXE 1: SCHÉMA DE REFROIDISSEMENT 83 100i / 200i / 300i / 400i ANNEXE 2: SCHÉMA DE PRINCIPE 100 A, 380-415 V PG 1 1 2 3 4 5 ANNEXE A W1A B L1 L2 J105B (1) 1 (23) INVERTER MODULE (IM) #1 (24) J100 -- 30 C K T R IB B ON MA IN PCB L EDS D3, RED, CAP IMB AL ANCE D4, GREEN, READY 1 2 (24) J103B L3 E arth (3) 1 (25) 1 2 (25) J105A CAP BIAS PCB L EDS D6, GREEN, -12V D11, GREEN, +12V P D13, GREEN, +12V 019X502700 W1C 1 IM #1 Section B (upper) A C IN PU T J104B W1B (2) 1 1 2 (23) IM #1 Section A (lower) A C IN PU T 1 2 (23) CONTROL PCB L EDS D1, RED, INV FLT D14, RED, OV ER TEMP D24, GREEN, PWM ON D32, RED, PRI OC J100 -- 30 C K T R IB B ON J104A CHASSIS GND 1 2 (24) J103A 1 2 (25) 019X502000 C J50 1 2 3 4 5 6 7 8 9 10 11 12 13 14 (1) (2) 019X504000 (10) LT 1 Component Locations (not including PCB components) (11) C4 CB1 (12) J52 LT 2 1 2 3 4 GND (13) IN TER N A L A C IN D IC ATO R A C LI N E LT1 & LT2 INPUT POWE R NEON INDICATORS Rear Panel & Internal CHASSIS GND (3-22) To J27 on CCM I/O PCB (28) SYSTEM BIAS SUPPLY PCB F2 019X501900 (86A) (27A) E (85A) (86B ) (27B) (85B) A C IN PU T 1 2 3 4 5 6 7 8 9 10 11 12 13 14 15 16 17 18 2 3 4 5 6 7 8 9 10 GND 11 12 13 K 1A K 1B 1 2 3 4 5 6 7 8 9 10 11 12 J63 TO A U X TR A N SFOR M ER System Bias Test Points SECONDARY GND 24VDC DC INPUT POSITIVE VCC1 VCC2 GATE PRIMARY GND +12V PRIMARY P ISOL GND 24 V DC 24 V DC MI SSING PHASE a MI SSING PHASE b AC V HIGH a AC V HIGH b AC V L OW a 24 V DC_RET 24 V DC_RET AC V L OW b VAC_IDA a / VAC_IDA b VAC_IDB a / VAC_IDB b 1 LEDS D3, RED, MISSING PHASE +V D4, RED, AC V HIGH D14, RED, AC V LOW D15, GREEN, VAC_IDA D26, GREEN, +12V PRI D27, GREEN, VAC_IDB D30, GREEN, 24VDC D44, GREEN, T1 ON J60 TP1 TP2 TP3 TP4 TP5 TP6 TP7 TP8 TP9 (Sht 2, E3) J62 +24VDC 8A , 500V, SB 8A , 500V, SB 480V-ID 400V-ID 208-230V-ID COM (26) F1 (27A& B) ON / OF F 16 A F 1 2 3 4 PA N EL A C IN D IC ATO R (2-21) CB1 J51 (43A) (44A) TO J12 T1 PRIMA RY (Sht 2, A1) 4 3 2 1 D (3) 18 AWG wire both in and out of CB1 (1-20) AC SUP PRES SION PCB 14 (29) (30) (31) (32) (33) (34) (35) (36) (37) (38) (39) (40) (41) (42) For SY S BIAS PCB VAC_ID L EDs, corresponds to 0 in the table. 230V 400V 1 J62-14 (/VAC_IDBb) 0 0 J61 J62-12 (/VAC_IDAb) 0 Capacitor, fan starting, 8uf 440VAC (Sht 2, E1) Circuit Breaker /ON/OFF SW, 15A 480V (Sht 1, E1) CB2-4 Circuit Breaker, 5A, 250V (Sht 2, B3) F1, 2 Fuse, 8A, 500V, S.B. (Sht 1,E1) FAN1,2 Fan, Heat Exchanger , 230 VAC (Sht 2, D2) FL1 Flow meter, pulse output (Sht 2, B2) FS1 Flow SW, 0.5 GPM (3.8 lpm), N.O. (Sht 2, A2) HCT1 Current Sensor, Hall Effect 200A, Work Lead (Sht 1, C8) K1 Relay, 24VAC, Inrush Control, (Sht2, B9) L1 Inductor, (Sht 1, B7) L3-5 Toriod Core Common Mode Ind (Sht1 B8, B&C3) LS1 Level Switch, Coolant Tank (Sht 2, A3) LT1, LT2 Indicator, Neon, 250V, AC Volts Present (Sht 1, B2 & C2) M1 Motor, Pump, ½ hp 230VAC, 50/60 Hz, 1Ph (Sht 2, C2) MC1 Relay, 120VAC, Inrush, coil (Sht2, B8, B9) contact (Sht2, A1) MC2 Relay, 120 VAC, Fan Control, coil (Coil at Sht 2, A7)(Contacts at Sht 2, D1) MC3 Relay, 120 VAC, Pump Motor Control, coil (Coil at Sht 2, A7)(Contacts at Sht 2, C1) R2 Inrush, 4.7 Ohm, 30W (Sht2, A1) R3,4 Ext RC, 100 ohm 55W (Sht1, A7) SA1-3 Snubber, Contactor & Relay coils (Sht 2, A8 & A9) T1 Aux Transformer (Sht 2, B2) TB4 Terminal Block (Sht 1, C9) TS1 Temperature Sensor, NTC, Coolant Return (Sht 2, A5) TS2 Temperature Sensor, NTC, Ambient (Sht 2, A5) W1 Contactor , Input (Coil Sht 2, A8), (Contacts C2) ON 480V ERR 0 1 1 1 "0" = 10-12V "1" = 24V Measured relative to TP1 (24V DC_RET) (48) V OLTA G E SELEC TI ON Wire #48 from J61-1 to: J61-2 for 208-230 VAC J61-3 for 400 VAC J61-4 for 480 VAC Art # A-11972_AE 1 84 2 3 ANNEXE 4 5 0560956430FR 100i / 200i / 300i / 400i 7 8 9 10 TORCH (49) (49) TES T POIN TS TP 1 G N D TP 2 PILO T G ATE TP 3 +5V 1 J43 ELEC TR OD E J44 J41 1 2 J40 019X501600 ELECTRODE (-) WORK (+) TO R ELA Y B OA R D L1 (51B) TO I/O B OA R D B Tip (+) Work TIP V OLTS To J24 on I-O PCB (Sht 2, C3) (+) (53) (Sht 2, A5) TO C C M C PU PC B J31 To / From Optional 1 Torch Module (Refer to 1 Torch section for details.) J45 10 ckt R ibbon TO J3 on RELAY PCB J102B OU TP U T J42 1 2 3 4 5 6 7 8 2 1 (49B) J46-F IN V ER TER 5 4 3 2 1 (-) CHASSIS GND TI P 1 2 3 4 5 6 7 8 9 10 J46-M 5 4 3 2 1 ANNEXE 2 1 CHASSIS GND J58C (50) 2 1 1 J41 (J87) (Sht 2, C3) 1 (52) EA RTH G R OU N D R3 & R4 RAS PILOT TIP To TB 4-6 PILOT PCB J58A TO C C M C PU PC B J32 A TORCH To TB 4-7 (49) 1 PILOT BOARD LED'S D2 PILOT ENABLE D11 +5V E lectrode 6 WO RK (Sht 2, D3) ARC V OLTS (55) (51) (49A) Hall E ffect Sensor (51) 4 1 OU TP U T WORK 1 J102A 3 WORK (+) HCT 1 (50) 2 5 4 3 2 1 ELECTRODE (-) TORCH TO J1 on REL AY PCB (Sht 2, A5) 4 3 C OMMON 2 SIG (+) -15 V DC +15 V DC J16 1 (Sht 1, A 9) C FER R ITE C OR E 3 TU R N S TB4 (49) TIP (Sht 1, A 9) (56) o AC 120V- TB4-4 (57) b AC 120V- Ret- TB4-3 (58) g AC 24V-TB4-2 (59) w AC 24V- Ret -TB4-1 (52) (51) (60) (61) (62) (63) 7 ARC VOLTS (TORCH) 6 TIP VOLTS (PILOT) 5 WORK 4 3 2 1 120 VAC @ 100 ma. 24 VAC @ 1A (J10 Sht 2, B8) RIBBON CABLE 30 ckt. CCM (J31& 32) - INVER TER (J100) 1 2 3 4 5 6 7 8 9 10 11 12 13 14 15 16 17 18 19 20 21 22 23 24 25 26 27 28 29 30 READY + READY INVER TER_ FLT + INVER TER_ FLT OVER TEM P_FLT + OVER TEM P_FLT PWR_ PRES ENT + PWR_ PRES ENT OUT_ COM (+3 to 5VDC) VAC_ SELA VAC_ SELB IS _IDA IS _IDB IS _IDC ENABLE + ENABLE STAR T2 + STAR T2 SPARE SYNC_ IN + SYNC_ IN NC NC 47 OHM to COM M DEM AND + DEM AND 47 OHM to COM M CURRENT + CURRENT 47 OHM to COM M RIBBON CABLE 40 ckt CCM (J23) - RELA Y PCB (J4) 32 COM M ON 1 COM M ON 33 -15 VDC 2 /1TORCH STAR T * 34 COM M ON 3 NA 35 24 VDC 4 /1TORCH GAS SOL ON * 36 COM M ON 5 /MAIN TORCH IDLE * 37 24 VDC 6 /1TORCH PRES S OK * 38 COM M ON 7 FLOW SENS OR (pulses) 39 24 VDC 8 LOW COOLANT FLOW 40 COM M ON 9 COOLANT LEVEL OK 10 COM M ON RIBBON CABLE 16 ckt 11 NA CCM ( J37) - DIS PLA Y 12 /PLAS M A ENABLE-HM I PCB (J17) 13 /COOLANT PUM P ON 14 COM M ON 1,3,5,7 24 VDC 15 /PILOT ENABLE 2,4,6,8 COM M ON 16 /RAS ON 9,10 NC 17 /CONT ACTORS ON 11-16 SERIAL DA TA 18 COM M ON 19 /COOLANT FANS ON 20 /1TORCH CONT ACTOR ON * RIBBON CABLE 10 ckt 21 /PLAS M A ENABLE RELA Y RELA Y PCB (J3) – PILOT PCB (J42) 22 COM M ON 23 PILOT CURRENT SIG24 NC 1,2 24 VDC 25 PILOT CURRENT SIG+ 3,4,7,10 COM M ON 26 COM M ON 5 PILOT ENABLE + 27 WORK CURRENT SIG6 PILOT ENABLE – 28 WORK CURRENT SIG+ 8 PILOT CURRENT SIG – 29 NC 9 PILOT CURRENT SIG + 30 AM BIENT TEM P 31 COOLANT TEM P * Used with 1 Torch Option D E Art # A-11972_AE Revision Rev 00 Initial Design AA By Date DAT 10/03/2012 DAT 9/16/2014 DAT 10/17/2014 AB ECO 1 Torch Option AC V C R -02672 M C 1, K 1 change DAT Revision Rev By Date Victor Technologies Headquarters 16052 Swingley Ridge Road, Suite 300 St Louis, Missouri 63017 USA Date Printed 8/28/2018 8/6/2018 Date The information contained herein is proprietary to Victor Technologies. Not for release, reproduction or distribution without written consent. DAT Size C Sheet Title Drawing Number SCHEMATIC Ultra-Cut XT 100A 480V 6 0560956430FR 7 8 ANNEXE 9 F Date Revised 8/6/2018 Drawn 10/05/2012 1 of 2 042X1349 10 85 100i / 200i / 300i / 400i ANNEXE 3: SCHÉMA DE PRINCIPE 100 A, 380-415 V PG 2 (89) 3 T1 1 2 3 4 (81) (82) J49 460V 24V RET 6 RED 24V B 400V RED 2 YELLOW 1 120V_2 220V 5 YELLOW 4 BLUE 3 120V_2 RET J6 (79) BLUE 12 11 10 9 8 7 6 5 4 3 2 1 (77) (78) CB2 5 A (76) (74) (75) CB3 5 A (73) (71) (72) CB4 5 A J9 J14 120V-1 RET SIGNAL (pulse) TORCH FLOW SENSOR 0V 120VAC_2 24VAC BIAS TRANSFORMER 1 1 2 3 (65A) MC2B (64A) D (69) 1 2 3 (70) BK C? FAN1 BN BL R (55) 1 2 3 (70) 1 2 3 4 5 6 7 8 J24 (70) 230 VAC _ SW (A9) 230 VAC_SW goes to J70 for HE 400 1 2 3 FAN1 J72 1 2 3 E Harness from System Bias PCB J62 (Sht 1, E3) 24 VDC 24 VDC MISSING PHASE a MISSING PHASE b AC V HIGH a AC V HIGH b AC V LOW a 24 VDC_RET 24 VDC_RET AC V LOW b VAC_IDA a / VAC_IDA b VAC_IDB a / VAC_IDB b FAN2 J73 (29) (30) (31) (32) (33) (34) (35) (36) (37) (38) (39) (40) (41) (42) For SYS BIAS PCB VAC_ID LEDs, ON corresponds to 0 in the table. 230V 400V 480V ERR J62-12 (/VAC_IDAb) 0 1 0 1 J62-14 (/VAC_IDBb) 0 0 1 1 J28 30 CKT PIN HEADER I / O PCB TEST POINTS ------------------------------------TP1 PCB COMMON TP2 COOLANT FANS ON TP3 PUMP ON TP4 LOW FLOW (SW) TP5 FLOW SIGNAL (pulse, Ultracut only) TP6 +15VDC_ISO (ref to TP10) TP7 -15VDC_ISO (ref to TP10) TP8 +16-18 VDC_ISO (ref to TP10) TP9 ANALOG CURRENT SIGNAL (remote & Autocut only) TP10 ISOLATED VOLTAGE COMMON TP11 1 TORCH CONTACTOR ON TP12 +5 VDC TP13 -15 VDC TP14 +15 VDC TP15 +24 VDC TP18 +5 VDC_ISO (ref to TP10) CHASSIS GND Alternate fans. Earlier 100 & 200A units may have 2 smaller fans. J36 - 30 CKT RIBBON I / O PCB LEDS ---------------------------------------------D2 CNC PLASMA ENABLE D3 E-STOP_PS D4 GAS ON (Auto-cut, PAK) D6 CNC START D8 HOLD START D12 PREFLOW ON D13 CSD (corner current reduction) D18 MARK D20 SPARE D25 EXP METAL D33 OK_CNC D37 PSR D41 SPARE OUT 2 D43 SPARE OUT 1 (53) (51) J73 (69) I-O PCB (CCM) 230 VAC _ SW _ RET R J72 (Sht 1, B8) TIP VOLTS 230 VAC (69) MC2A J34 - 30 CKT RIBBON J28 30 CKT RECEPTACLE - BOTTOM ENTRY 19X501100 Harness from Pilot PCB J45 Torch Coolant Pump (67) CPU PCB (CCM) M1 J16 WORK (64B) J85 N/C J35 - 30 CKT RIBBON ARC VOLTS 2 3 (65B) 4 (64A) (64B) (65A) J13 to CB5 and to MC2 & MC3, also J14, J16 all 18 AWG J32 - 30 CKT RIBBON J84 N/C N/C MC3BCHASSIS GND 019X501700 J11 J33 - 30 CKT RIBBON (66) Test Points TP1, GND TP2, -15V TP3, +5VDC TP4, +12V TP5, +24V TP6, +15V TP7, +5VDC 1 TORCH INTERFACE J31 - 30 CKT RIBBON Mini-Fit Jr MC3A TEMP SENSOR Refer to 1 Torch Module Schematic for Details 120VAC_1 N/C J13 J2 D2, GREEN, 1TORCH GAS ON D7, GREEN, PILOT ENABLED D11, GREEN, PILOT CURRENT D12, GREEN, WORK CURRENT D22, GREEN, CONTACTORS ON D23, GREEN, RF ON D24, GREEN, FANS ON D25, GREEN, PLASMA ENABLED D26, GREEN, 1TORCH ON D27, GREEN, COOLANT ON To J100 of IM #1B To J100 of IM #1A (Sht 1, B&C- 5&6) 120V_1 C J1 RELAY & INTERFACE PCB +5VDC 14 13 12 11 10 9 8 7 6 5 4 3 2 1 1 2 3 4 5 6 7 8 J7 (95) 3 2 1 1 5 2 6 3 7 4 8 J12 (93) (94) COOLANT FLOW SW LEVEL SENSORS WORK CURRENT SENSOR (80) 1 2 3 4 TS1 5 4 3 2 1 r b g 1 2 Mini-Fit Jr ANNEXE J5 FL1 (87) 8 7 6 5 4 3 2 1 R2 2 1 0.7 GPM 4.7 30W (92) COOLANT 6 5 4 3 2 1 (83) 1 (84) 1 2 (59) (58) (57) (56) J74 TS2 COMMON SIG (+) -15 VDC +15 VDC FS1 COOLANT MC1A 4 J71 AMBIENT (Sht 1, C8) COOLANT LEVEL (44A) (43A) (90) 2 3 From Sys Bias J63 (Sht 1, F2) A 1 LS1 5 2 J12 = Mini-Fit Jr 400 VAC -- Single 18 AWG in pins 1 & 4 480 VAC -- Single 18 AWG in pins 1 & 8 230 VAC -- 18 AWG wires in pins 1,5,2,6 4 TO HCT1 (Work) 3 3 2 4 1 1 2 3 4 5 6 7 8 9 10 11 12 13 14 J27 19X501200 I / O PCB DIP SW --------------------------------------------SW6 OK TO MOVE (CONTACTS, VOLTS) SW11 ANALOG CC SOURCE SW12 DIVIDED ARC VOLTAGE (50:1, 16.7:1, 30:1, 40:1, 25:1) "0" = 10-12V "1" = 24V Measured relative to TP1 (24VDC_RET) F Art # A-11973_AE 1 86 2 3 ANNEXE 4 5 0560956430FR 100i / 200i / 300i / 400i 6 7 (70) (161) 10 CKT RIBBON (160) (163) (162) / PILOT ENABLE / PILOT ENABLE RET MC3 (D2) (96) SA1 (96) SA4 (97) (D2) ARC_SUPPRESSOR CHASSIS GND 16 15 14 13 12 11 10 9 8 7 6 5 4 3 2 1 2 1 4 3 120VAC * INRUSH CONTROL 120 VAC_2 J4 -- 40 CKT RIBBON CABLE HMI/GCM (104) (62) (106) AC 120V - GCM (111) (63) (113) (61) J18 J54 - Remote HMI & CNC COMM (100) 1 (60) (101) (102) AC 24V-TB4-2 (109) AC 120V- TB4-4 (108) (115) AC 24V Ret- GCM1 (63) AC 120V- Ret- GCM Harness AC 24V- Ret -TB4-1 (62) 1 AC 120V- Ret- TB4-3 (116) (117) (118) K1 (OLD) (119) (120) 2 1 2 3 4 J47 4 WIRE RxTx+ Rx+ Tx- (116) (117) (120) (115) (119) (118) 1 2 3 4 5 6 J30 2 WIRE ENABLE CPU PCB TEST POINTS -------------------------------------------TP1 GND (PCB common) TP2 +5V_ISO (REF TP5) TP3 +24 VDC TP4 +3.3V TP5 GND_ISO TP6 +5.0 V TP7 TOTAL DEMAND (3.3V = 400A) TP9 /WR TP10 /RD TP11 CPU TEMP SENSE TP12 +3.3VA TP13 -15VDAC TP14 PC2 TP15 +15VDAC TP16 CLKO TP18 OSC_CLOCK PLAS_ENABLE SW PLAS_ EN_SW_RET / GAS PRESS OK / BASIC ID CPU PCB DIP SW --------------------------------------------SW1 AUTO PILOT RESTART SW3 PREFLOW TIME SW4 POSTFLOW TIME SW5 FUNCTION SW8 SYSTEM CONTROL (pilot time, etc.) SW9 RESERVED (future) SW10 ADDRESS (default = 0) SW13 UNIT TYPE (AC / UC) SW14 LINE TERMINATION (serial comm.) 12 11 10 9 8 7 6 5 4 3 2 1 Harness FERRITE CORE 3 TURNS 16 CKT RIBBON (121) (122) (123) (124) (125) (126) (127) (128) (129) (130) (131) GND 1 2 3 4 5 6 7 8 9 10 11 12 13 14 15 16 17 18 TB2 OK to MOVE (+) 12 11 OK to MOVE (-) 10 9 8 7 6 5 4 3 2 1 PILOT is ON Preflow ON (+) Preflow ON (-) Hold Start (+) Hold Start (-) 1 2 3 4 5 6 7 8 9 10 11 12 13 14 15 16 (130) (131) (112) (114) (121) (122) (124) (129) (128) (123) 00 Revision +10V GND GND TB3 12 11 10 9 * Plasma Ready (b) 87 6 Spare 5 Digital 4 Inputs 3 / Plasma Marking (-) 2 / Plasma Marking (+) 1 PSR (133) (134) (137) (139) (138) (143) Initial Design AA DAT 10/03/2012 DAT 9/16/2014 AB ECO 1 Torch Option DAT 10/17/2014 AC VCR-02672 MC1, K1 change DAT 8/6/2018 Revision Rev (111) (166) J69 (167) AC 120V - GCM AC 120V- Ret- GCM FERRITE CORE 3 TURNS (106) (113) FERRITE CORE 3 TURNS 0560956430FR (143) (144) (145) (146) (147) (148) (149) (150) (151) (152) (154) (155) (132) (152) (153) (154) (155) (156) (157) (158) (159) (156) (157) (158) (159) Art # A-11973_AE By J55 - GCM 1 2 3 4 5 6 7 8 9 10 11 12 13 14 15 16 17 18 19 20 21 22 23 24 25 26 27 28 29 30 31 32 33 34 35 36 37 1- PLAS_ENABLE SW * 2- PLAS_ EN_SW_RET 3- GAS PRESS OK RET 4- / GAS PRESS OK 5- POT HIGH (GCM 1000) 6- POT WIPER (GCM 1000) 7- POT LOW (GCM 1000) 8- BASIC ID RET 9- / BASIC ID ** 1011- 1 2 3 4 5 6 7 8 9 10 11 12 13 14 15 16 17 18 19 20 21 22 23 24 25 26 27 28 29 30 31 32 33 34 35 36 37 C GCM 1000 XT Jumper 1415- 24 VAC - RET * Plasma Enable SW in GCM 2010. Jumpered in GCM 1000 XT and DMC 3000. ** Jumper in GCM 1000 XT 27- GAS SEL SW RET 28- GAS SEL SW D J15-1 to chassis used for SC-11 cable shield J15-13 connects SC-11 chassis to PS chassis. The COMM Ref at pin 8 is also for the SC-11 3- / CNC Start (+) 4- / CNC Start (-) 5- Divided Arc V (-) 6- Divided Arc V (+) 7- / Preflow ON (+) 8- COMM Ref (1K Ohm) 9- / Preflow ON (-) 10- / Spare Digital Input (+) 11- / Spare Digital Input (-) 12- OK to Move (-) 14- OK to Move (+) 15 - Key Plug 16- / Hold Start (+) 17- / Hold Start (-) E 21- / Plasma Mark (+) 22- / Plasma Mark (-) 23- / Spare Digital Input(+) 24- / Spare Digital Input (-) 25- / CNC Plasma Enable (+) 26- / CNC Plasma Enable (-) 29- Remote CC Pot High 30- Remote CC (analog) 31- Remote CC Pot Low 32- Stop SW (momentary) * 33- Stop SW Ret 34- Pilot is ON (a) 35- Pilot is ON (b) 36 - 37 Plasma Ready (a) Normally Open Contact * Used with Momentary CNC Start SW Date Victor Technologies Headquarters 16052 Swingley Ridge Road, Suite 300 St Louis, Missouri 63017 USA Date Printed 8/28/2018 Date The information contained herein is proprietary to Victor Technologies. Not for release, reproduction or distribution without written consent. DAT Size C Sheet Title Drawing Number SCHEMATIC 7 8 ANNEXE 9 F Date Revised 8/24/2018 Drawn Ultra-Cut XT 100A 480V 6 12 - Tx13 - Rx+ 14 - Rx- J15-CNC CHASSIS GND (133) (134) (135) (136) (137) (138) (139) (140) (141) (142) (153) (144) (145) (146) (147) (148) (149) (150) (151) (104) J22 * Plasma Ready (a) Date AC 24V Ret-GCM2 (140) (141) (136) (135) (132) J21 1 2 3 4 5 6 7 8 9 10 11 12 13 14 15 16 17 18 19 20 Spare Digital Inputs By AC 24V-GCM2 2 1 * CCM code 2.5 or later Rev AC 24V Ret - GCM1 (125) (126) (127) (142) (112) (114) (103) (110) AC 24V-GCM1 J26 OK PILOT is ON B Comm J17 GAS ON TB1 5-HMI Plasma Enable SW 6-HMI Plasma Enable SW 7 - Key Plug 8 - Tx+ 9 - GND RS 485 10 - GND / 422 019X501800 J37 J23- 40 ckt ribbon cable OK2 (contact) +10V (CC Pot Hi) CC Pot Wiper CC Pot Low Div Arc V (+) Div Arc V (-) /Start - Stop (+) /Start - Stop (-) Stop Mom NC OK2 (contact) / CNC Enable (+) / CNC Enable (-) 1 - 24 VAC 2 - 24 VAC Ret 3- Jumper to 24 VAC Display PCB INRUSH CONTROL J20 J29 30 CKT PIN HEADER 2 3 4 5 6 7 8 9 10 11 12 13 14 (61) 3 (63) 5 J29 30 CKT RECEPTACLE - BOTTOM ENTRY CPU PCB LEDs ---------------------------D2 RXD (red) D3 TXD (red) D4 CAN BUS (slave) D7 CAN BUS (MAIN) D11 5 VDC POWER D17 STATUS CODE D18 INITIALIZING / PROGRAMMING (red) 3 - Key Plug 4 (107) GND GND J19 (98) (107) J10 1 2 3 4 5 6 7 8 9 10 11 12 NORMAL PROGRAM PROG USB IC (62) AC 24V - RET - GCM2 1 2 3 4 1 2 3 4 5 6 7 8 9 1 2 3 4 5 6 120 VAC Ret MC1 (OLD) AC 24V GCM1 AC 24V GCM2 (108) (109) (110) J39 USB PORT 1 2 3 4 5 6 7 8 9 10 11 12 (99) A 120VAC (101) (102) (103) USB Cable to Front Panel RS 232 D-SUB SERIAL PROG PORT 120 VAC to RAS 1 2 3 4 5 6 7 8 9 10 11 12 13 14 ANNEXE 120 VAC_1 * New MC1 location requires Relay & Interface PCB revision AB or later. (60) (100) 18 17 16 15 14 13 12 11 10 9 8 7 6 5 4 3 2 1 * 24 VAC (107) * INRUSH CONTROL (K1) MOVED TO RELAY PCB CONTROL OUTPUTS GND 1 2 3 4 5 6 7 J59 - RAS (97) MC1 (NEW) (91) J8 (70) (69) 230 VAC Ret (99) 24 VDC J70 - HE (98) ARC_SUPPRESSOR PILOT PCB 10 230 VAC to HE 400 (69) 230 VAC _ SW _ RET W1 ARC_SUPPRESSOR J38 9 230 VAC _ SW SA3 Pump Motor Control 5 6 PILOT A SIG Vin+ PILOT A SIG Vin8 7 9 10 J3 8 Fan Control MC2 TO PILOT PCB (Sht 1, B8) 10/5/2012 2 of 2 042X1349 10 87 100i / 200i / 300i / 400i ANNEXE 4: SCHÉMA DE PRINCIPE 200A, 380-415 V PG 1 1 2 3 4 5 A INVER T ER MO DULE (IM) #2 half module (middle position) ANNEXE J105A 1 2 (23) A C IN PU T IM # 2 Se ction A (l ower) J104A B J100 -- 30 C K T R IB B ON 1 2 (24) J103A 1 2 (25) 019X502000 W1A 1 (1) L2 1 (2) L3 1 E arth 1 L1 J105B (23) (23) (24) (24) 1 2 J104B W1B 1 2 J103B C (25) (3) 1 2 (25) INVER T ER MO DULE (IM) #1 (bottom) A C IN PU T IM # 1 Se ction B (u pper) J100 -- 30 C K T R IB B ON MA IN PCB L EDS D3, RED, CAP IMB AL ANCE D4, GREEN, READY CAP BIAS PCB L EDS D6, GREEN, -12V D11, GREEN, +12V P D13, GREEN, +12V 019X502700 W1C J105A IM # 1 Se ction A (l ower) A C IN PU T 1 2 (23) CONTROL PCB L EDS D1, RED, INV FLT D14, RED, OV ER TEMP D24, GREEN, PWM ON D32, RED, PRI OC J100 -- 30 C K T R IB B ON J104A C H AS S IS GN D 1 2 (24) J103A 1 2 (25) 18 AWG wire both in and out of CB1 AC SUP PRES SION J50 PCB J51 019X504000 (26) (27A& B) F R ONT PANE L F1 8A , 500V, SB 1 2 3 4 LT 1 4 3 2 1 1 2 3 4 5 6 7 8 9 10 11 12 480 V-ID 400 V-ID 208 -23 0V-ID CO M E (1) 1 2 3 4 5 6 7 8 9 10 11 12 13 14 (28) CB 1 ON / OF F 16 A (10) Component Locations (not including PCB components) C4 Ca pacitor, fa n s tarting, 8 uf 4 40VAC (Sh t 2, E1 ) CB1 Ci rcuit Bre aker /ON/OFF SW , 1 5A 4 80V (11) (Sh t 1, E1 ) LT1 & LT2 PA N EL A C IN D IC ATO R INPUT POWE R CB2 -4 Ci rcuit Bre aker, 5 A, 2 50V (Sh t 2, B3 ) (12) (2-21) (2) J52 F1 , 2 Fu s e, 8 A, 5 00V, S.B. (Sh t 1,E1 ) LT 2 NEON INDICATORS 1 Rear Panel & Internal FAN1 ,2 Fa n, He at Ex changer , 2 30 V AC (Sh t 2, D2 ) 2 3 FL 1 Fl ow meter, p uls e output (Sh t 2, B2 ) 4 GND FS1 Fl ow SW , 0 .5 G PM (3 .8 lpm), N.O . (Sh t 2, A2 ) (3-22) (3) (13) HCT1 Cu rrent Se ns or, Ha ll Ef fect 200A, Wo rk L ead IN TER N A L A C IN D IC ATO R A C LI N E (Sh t 1, C8 ) K1 Re lay, 2 4VAC, In rus h Co ntrol, (Sh t2, B9 ) C H AS S IS GN D L1 Inductor, (Sh t 1, B7 ) To J27 on CCM I/O PCB L3-5 Toriod Co re Co mmon M ode In d (Sh t1 B8 , B&C3 ) LS1 Level Swi tch, Co olant Tank (Sh t 2, A3 ) (Sht 2, E3) SYSTEM BIAS SUPPL Y PCB LT1 , L T2 In dicator, Ne on, 2 50V, AC V olts Pre s ent J62 019X501900 F2 (Sh t 1, B2 & C2 ) 24 V DC (29) 8A , 500V, SB +24V D C 1 M1 Motor, Pu mp, ½ hp 2 30VAC, 5 0/60 Hz , 1 Ph LEDS 24 V DC (30) 2 D3, RED, MISSING PHASE (Sh t 2, C2 ) MI SSING PHASE a (31) +V 3 D4, RED, AC V HIGH MC1 Re lay, 1 20VAC, In rus h, c oil (Sh t2, B8 , B9 ) MI SSING PHASE b (32) D14, RED, AC V LOW A C IN PU T 4 c ontact (Sh t2, A1 ) AC V HIGH a (33) D15, GREEN, VAC_IDA (86A) 1 5 D26, GREEN, +12V PRI AC V HIGH b (34) MC2 Re lay, 1 20 V AC, Fa n Co ntrol, c oil 2 6 D27, GREEN, VAC_IDB 3 AC V L OW a (35) (Co il a t Sh t 2, A7 )(Co ntacts a t Sh t 2, D1 ) 4 7 D30, GREEN, 24VDC (27A) 24 V DC_RET (36) 5 MC3 Re lay, 1 20 V AC, Pu mp M otor Co ntrol, c oil D44, GREEN, T1 ON 8 6 24 V DC_RET (37) (Co il a t Sh t 2, A7 )(Co ntacts a t Sh t 2, C1 ) 7 9 AC V L OW b (38) 8 (85A) R2 In rus h, 4 .7 O hm, 3 0W (Sh t2, A1 ) 10 9 GN D VAC_IDA a (39) (86B ) 10 11 R3 ,4 Ex t RC, 1 00 ohm 5 5W (Sh t1, A7 ) / VAC_IDA b (40) 11 12 SA1 -3 Sn ubber, Co ntactor & Re lay c oils 12 VAC_IDB a (41) 13 13 (Sh t 2, A8 & A9 ) (27B) / VAC_IDB b (42) 14 14 K 1A T1 Aux Trans former (Sh t 2, B2 ) K 1B 15 16 TB4 Terminal Bl ock (Sh t 1, C9 ) 17 (85B) For SY S B IA S PC B V A C _ID L E Ds, O N 18 TS1 Temperature Se ns or, NTC, Co olant Re turn correspondsto 0 in the table. (Sh t 2, A5 ) J60 230V 400V 480V E R R TS2 Temperature Se ns or, NTC, Ambient (Sh t 2, A5 ) J62-12 ( /VA C _IDA b) 0 1 0 1 J63 J61 J62-14 ( /VA C _IDB b) 0 0 1 1 W1 Co ntactor , In put (Co il Sh t 2, A8 ), (Co ntacts C2 ) (1-20) D 019X502000 " 0" = 10-12V " 1" = 24V Measured relative to T P1 ( 24V DC _R E T ) System Bias Test Points F TP1 TP2 TP3 TP4 TP5 TP6 TP7 TP8 TP9 SECONDARY GND 24VDC DC INPUT POSITIVE VCC1 VCC2 GATE PRIMARY GND +12V PRIMARY P ISOL GND TO A U X TR A N SFOR M ER (43A) (44A) TO J12 T1 PRIMA RY (Sht 2, A1) (48) V OLTA G E SELEC TI ON Wire #48 from J61-1 to: J61-2 for 208-230 VAC J61-3 for 400 VAC J61-4 for 480 VAC Art # A-11974_AE 1 88 2 3 ANNEXE 4 5 0560956430FR 100i / 200i / 300i / 400i 7 8 9 10 TORCH (49) (49) J43 ELEC TR OD E PIL OT PCB J58A R3 & R4 (51C) 2 1 1 2 3 4 5 6 7 8 10 ckt R ibbon TO J 3 on R E LAY PC B (Sht 2, A5) To J 24 on I-O PC B (Sht 2, D3) L1 WO R K (+) B Work (53) (+) WO RK ARC V OLTS (49B) (55) HCT 1 (51B) (51) Hall E ffect Sensor (51) WORK 1 4 1 TOR C H TO J1 on REL AY PCB (Sht 2, A5) o (57) b (58) g (59) w 4 3 2 SIG (+) 1 (56) C 3 TU R N S TB4 C OMMON (50) -15 V DC +15 V DC (49A) (A 9) FER R ITE C OR E J16 J102A OU TP U T Tip (51) (Sht 2, C3) 5 4 3 2 1 (+) TIP V OLTS TO C C M C PU PC B J31 E LE C T R ODE (-) To / From Optional 1 Torch Module (Refer to 1 Torch section for details.) J45 TO R ELA Y B OA R D J102B OU TP U T (-) C H AS S IS GN D 019X501600 2 WO R K (+) J40 IN V ER TER J42 (Sht 2, C3) 5 4 3 2 1 1 2 TI P 1 2 3 4 5 6 7 8 9 10 2 1 (51F) TO C C M C PU PC B J32 E LE C T R ODE (-) J41 5 4 3 2 1 J102A OU TP U T C H AS S IS GN D 3 WO R K (+) J46-F J46-M 5 4 3 2 1 E LE C T R ODE (-) (49C) 1 ANNEXE (Sht 2, C3) J44 J41 (J87) RAS PILOT (52) 1 J58C (50) TO C C M C PU PC B J33 A TI P To TB 4-6 1 D2 PI LOT EN ABL E D11 +5V 1 TOR C H To TB 4-7 2 1 TES T POIN TS TP 1 G N D TP 2 PILO T G ATE TP 3 +5V PI LOT BO AR D LED 'S E lectrode 6 (49) (Sht 1, A 9) TI P (Sht 1, A 9) AC 120V- TB 4-4 AC 120V- R et- TB 4-3 AC 24V-TB 4-2 AC 24V- R et -TB 4-1 (52) (51) (60) (61) (62) (63) 7 AR C VOLTS (TOR C H) 6 TIP VOLTS (PILOT) 5 WOR K 4 3 2 1 120 VAC @ 100 ma. 24 VAC @ 1A (J10 Sht 2, B8) RIBBON CABLE 30 ckt. CCM (J31-36) - INVER TER (J100) 1 2 3 4 5 6 7 8 9 10 11 12 13 14 15 16 17 18 19 20 21 22 23 24 25 26 27 28 29 30 RIBBON CABLE 40 ckt CCM (J23) - RELA Y PCB 1 COM MON 32 COM MON 2 /1TORCH STAR T * 33 -15 VDC 3 NA 34 COM MON 4 /1TORCH GAS SOL ON * 35 24 VDC 5 /MAIN TORCH IDLE * 36 COM MON 6 /1TORCH PRES S OK * 37 24 VDC 7 FLOW SENS OR (pulses) 38 COM MON 8 LOW COOLANT FLOW 39 24 VDC 9 COOLANT LEVEL OK 40 COM MON 10 COM MON 11 NA 12 /PLAS MA ENABLE-HM I 13 /COOLANT PUM P ON 14 COM MON 15 /PILOT ENABLE 16 /RAS ON 17 /CONT ACTORS ON 18 COM MON 19 /COOLANT FANS ON 20 /1TORCH CONT ACTOR ON * 21 /PLAS MA ENABLE RELA Y 22 COM MON 23 PILOT CURRENT SIG24 NC 25 PILOT CURRENT SIG+ 26 COM MON 27 WORK CURRENT SIG28 WORK CURRENT SIG+ 29 NC 30 AM BIENT TEM P 31 COOLANT TEM P * Used with 1 Torch Option READY + READY INVER TER_ FLT + INVER TER_ FLT OVER TEM P_FLT + OVER TEM P_FLT PWR_ PRES ENT + PWR_ PRES ENT OUT_ COM (+3 to 5VDC) VAC_ SELA VAC_ SELB IS _IDA IS _IDB IS _IDC ENABLE + ENABLE STAR T2 + STAR T2 SPARE SYNC_ IN + SYNC_ IN NC NC 47 OHM to COM M DEM AND + DEM AND 47 OHM to COM M CURRENT + CURRENT 47 OHM to COM M (J4) D RIBBON CABLE 16 ckt CCM ( J37) - DIS PLA Y PCB (J17) 1,3,5,7 2,4,6,8 9,10 11-16 24 VDC COM MON NC SERIAL DA TA RIBBON CABLE 10 ckt RELA Y PCB (J3) – PILOT PCB (J42) 1,2 3,4,7,10 5 6 8 9 E 24 VDC COM MON PILOT ENABLE + PILOT ENABLE – PILOT CURRENT SIG – PILOT CURRENT SIG + Art # A-11974_AE R ev 00 R evisi on Initial Desi gn AA By Date DAT 10/03/2012 DAT 9/16/2014 DAT 10/17/2014 AB E C O 1 Torch Option AC V C R -02672 M C 1, K 1 change DAT R evisi on R ev By Date Victor Technol ogies Headquar ters 16052 Sw ingley R idge R oad, Su ite 300 St Louis, Missouri 63017 USA D ate P rinted 8/28/2018 8/3/2018 T he information contained herein is proprietary to Victor Technologies. Not for release, reproduction or distribution without written consent. DAT D ate S ize C S heet Title D rawing N umber SCHEMATIC Ultra-Cu t X T 2 00A 4 80V 6 0560956430FR 7 8 ANNEXE 9 F D ate R evis ed 8/3/2018 D rawn 10/05/2012 1 of 2 042X1348 10 89 100i / 200i / 300i / 400i ANNEXE 5: SCHÉMA DE PRINCIPE 200A, 380-415 V PG 2 3 J12 = Mini-Fit Jr 400 VAC -- Single 18 AWG in pins 1 & 4 480 VAC -- Single 18 AWG in pins 1 & 8 230 VAC -- 18 AWG wires in pins 1,5,2,6 1 LS1 COOLANT LEVEL (89) FS1 COOLANT MC1A 4 J71 J74 (84) 1 2 (83) AMBIENT TS2 (59) (58) (57) (56) (43A) (90) 2 3 (44A) 5 (92) 0.7 GPM COOLANT TS1 (93) COMMON SIG (+) -15 VDC +15 VDC From Sys Bias J63 (Sht 1, F2) A 4 Sht 1, C8) 2 TO HCT1 (Work) 1 (94) (95) 1 2 3 4 (81) (82) J49 24V RET 6 RED 24V B 400V YELLOW 4 BLUE 120V_2 RET (74) (75) CB3 5 A (73) 3 RED 2 (71) (72) CB4 5 A YELLOW 1 120V_2 220V 5 120V-1 RET SIGNAL (pulse) TORCH FLOW SENSOR 12 11 10 9 8 7 6 5 4 3 2 1 (77) (78) CB2 5 A (76) 120VAC_2 24VAC BIAS TRANSFORMER 1 1 2 3 (67) (69) (65A) MC2B (64A) D J72 (69) 1 2 3 (70) (A9) BK C4 BL (55) 1 2 3 (A9) CHASSIS GND Alternate fans. Earlier 100 & 200A units may have 2 smaller fans. E 230 VAC_SW goes to J70 for HE 400 (Sht 1 F2) 24 VDC 24 VDC MISSING PHASE a MISSING PHASE b AC V HIGH a AC V HIGH b AC V LOW a 24 VDC_RET 24 VDC_RET AC V LOW b VAC_IDA a / VAC_IDA b VAC_IDB a / VAC_IDB b FAN2 J73 For SYS BIAS PCB VAC_ID LEDs, ON corresponds to 0 in the table. 230V 400V 480V ERR J62-12 (/VAC_IDAb) 0 1 0 1 J62-14 (/VAC_IDBb) 0 0 1 1 (29) (30) (31) (32) (33) (34) (35) (36) (37) (38) (39) (40) (41) (42) 6 5 4 3 2 1 1 3 4 J36 - 30 CKT RIBBON J28 30 CKT PIN HEADER I / O PCB TEST POINTS ------------------------------------TP1 PCB COMMON TP2 COOLANT FANS ON TP3 PUMP ON TP4 LOW FLOW (SW) TP5 FLOW SIGNAL (pulse, Ultracut only) TP6 +15VDC_ISO (ref to TP10) TP7 -15VDC_ISO (ref to TP10) TP8 +16-18 VDC_ISO (ref to TP10) TP9 ANALOG CURRENT SIGNAL (remote & Autocut only) TP10 ISOLATED VOLTAGE COMMON TP11 1 TORCH CONTACTOR ON TP12 +5 VDC TP13 -15 VDC TP14 +15 VDC TP15 +24 VDC TP18 +5 VDC_ISO (ref to TP10) Harness from System Bias PCB FAN1 J72 1 2 3 1 2 3 4 5 6 7 8 J24 230 VAC _ SW J34 - 30 CKT RIBBON I / O PCB LEDS ---------------------------------------------D2 CNC PLASMA ENABLE D3 E-STOP_PS D4 GAS ON (Auto-cut, PAK) D6 CNC START D8 HOLD START D12 PREFLOW ON D13 CSD (corner current reduction) D18 MARK D20 SPARE D25 EXP METAL D33 OK_CNC D37 PSR D41 SPARE OUT 2 D43 SPARE OUT 1 (53) (51) J73 (69) (70) 1 2 3 FAN1 BN R (70) I-O PCB (CCM) (Sht 1, B8) 230 VAC _ SW _ RET R MC2A Harness from Pilot PCB J45 WORK (64B) J85 J28 30 CKT RECEPTACLE - BOTTOM ENTRY 19X501100 Torch Coolant Pump TIP VOLTS MC3BCHASSIS GND ARC VOLTS 2 3 4 (64A) (64B) (65A) (65B) (66) J84 CPU PCB (CCM ) N/C J35 - 30 CKT RIBBON M1 J16 J32 - 30 CKT RIBBON N/C J33 - 30 CKT RIBBON N/C MC3A 019X501700 J11 J31 - 30 CKT RIBBON To J100 of IM #2A (Sht 1, B,C6) J13 to CB5 and to MC2 & MC3, also J14, J16 all 18 AWG Refer to 1 Torch Module Schematic for Details To J100 of IM #1B To J100 of IM #1A (Sht 1, C,D6) 120V_1 J13 Test Points TP1, GND TP2, -15V TP3, +5VDC TP4, +12V TP5, +24V TP6, +15V TP7, +5VDC 1 TORCH INTERFACE 0V C D2, GREEN, 1TORCH GAS ON D7, GREEN, PILOT ENABLED D11, GREEN, PILOT CURRENT D12, GREEN, WORK CURRENT D22, GREEN, CONTACTORS ON D23, GREEN, RF ON D24, GREEN, FANS ON D25, GREEN, PLASMA ENABLED D26, GREEN, 1TORCH ON D27, GREEN, COOLANT ON 120VAC_1 J9 J14 TEMP SENSORS RELAY & INTERFACE PCB +5VDC J6 (79) BLUE J2 14 13 12 11 10 9 8 7 6 5 4 3 2 1 460V 1 2 3 4 5 6 7 8 J1 3 2 1 1 5 2 6 3 7 4 8 3 1 2 3 4 T1 230 VAC ANNEXE J12 2 J7 COOLANT FLOW SW LEVEL SENSORS WORK CURRENT SENSOR (80) 5 4 3 2 1 r b g 1 2 J5 FL1 (87) 8 7 6 5 4 3 2 1 4.7 30W 2 1 R2 1 2 3 4 5 6 7 8 9 10 11 12 13 14 J27 19X501200 I / O PCB DIP SW --------------------------------------------SW6 OK TO MOVE (CONTACTS, VOLTS) SW11 ANALOG CC SOURCE SW12 DIVIDED ARC VOLTAGE (50:1, 16.7:1, 30:1, 40:1, 25:1) "0" = 10-12V "1" = 24V Measured relative to TP1 (24VDC_RET) F Art # A-11975_AE 1 90 2 3 4 ANNEXE 5 0560956430FR 100i / 200i / 300i / 400i 6 7 MC2 TO PILOT PCB Sht 1, B8) 9 (70) (161) (160) 10 CKT RIBBON 230 VAC _ SW SA3 (D2) SA1 (69) (163) J59 - RAS (97) (96) (162) / PILOT ENABLE / PILOT ENABLE RET SA4 16 15 14 13 12 11 10 9 8 7 6 5 4 3 2 1 2 1 4 3 120VAC 120 VAC_RET 120 VAC_1 * INRUSH CONTROL 120 VAC_2 HMI/GCM J4 -- 40 CKT RIBBON CABLE 120VAC (101) (102) (103) (104) (62) (106) (62) (60) AC 120V - GCM (63) (113) (61) AC 24V - RET - GCM2 AC 120V- Ret- GCM AC 120V- Ret- TB4-3 1 2 3 4 (62) 1 PROG USB IC J18 GND GND J19 RxTx+ Rx+ Tx- 4 WIRE 1 2 3 4 5 6 7 8 9 10 11 12 1 2 3 4 5 6 J37 (115) (116) (117) Harness AC 24V- Ret -TB4-1 (118) (119) (120) 2 4 (107) 3 (61) Harness ENABLE PLAS_ENABLE SW PLAS_ EN_SW_RET / GAS PRESS OK / BASIC ID TB1 CPU PCB TEST POINTS -------------------------------------------TP1 GND (PCB common) TP2 +5V_ISO (REF TP5) TP3 +24 VDC TP4 +3.3V TP5 GND_ISO TP6 +5.0 V TP7 TOTAL DEMAND (3.3V = 400A) TP9 /WR TP10 /RD TP11 CPU TEMP SENSE TP12 +3.3VA TP13 -15VDAC TP14 PC2 TP15 +15VDAC TP16 CLKO TP18 OSC_CLOCK CPU PCB DIP SW --------------------------------------------SW1 AUTO PILOT RESTART SW3 PREFLOW TIME SW4 POSTFLOW TIME SW5 FUNCTION SW8 SYSTEM CONTROL (pilot time, etc.) SW9 RESERVED (future) SW10 ADDRESS (default = 0) SW13 UNIT TYPE (AC / UC) SW14 LINE TERMINATION (serial comm.) 12 OK2 (contact) +10V (CC Pot Hi) 11 CC Pot Wiper 10 CC Pot Low 9 Div Arc V (+) 8 7 Div Arc V (-) /Start - Stop (+) 6 /Start - Stop (-) 5 4 Stop Mom NC 3 OK2 (contact) / CNC Enable (+) 2 / CNC Enable (-) 1 1 2 3 4 5 6 7 8 9 10 11 12 13 14 15 16 17 18 TB2 OK to MOVE (+) 12 +10V GND GND (121) (122) (123) (124) (125) (126) (127) (128) (129) (130) (131) (130) (131) (112) (114) TB3 Spare Digital Inputs 12 11 10 9 8 * Plasma Ready (b) 7 6 Spare 5 Digital 4 Inputs 3 / Plasma Marking (-) 2 / Plasma Marking (+) 1 PSR AC 24V Ret - GCM1 (121) (122) (124) (129) (128) AC 24V-GCM2 AC 24V Ret-GCM2 (123) 00 Revision Initial Design AA By Date DAT 10/03/2012 DAT 9/16/2014 AB ECO 1 Torch Option DAT 10/17/2014 AC VCR-02672 MC1, K1 change DAT 8/3/2018 Revision Rev (111) (166) (125) (126) (127) J69 (167) 2 1 (142) AC 120V - GCM AC 120V- Ret- GCM FERRITE CORE 3 TURNS (133) (134) (137) (139) (138) (143) (106) (113) (140) (141) (136) (135) (132) (153) FERRITE CORE 3 TURNS 0560956430FR (143) (146) (147) (148) (149) (150) (151) (152) (154) (155) (132) (152) (153) (154) (155) (156) (157) (158) (159) (156) (157) (158) (159) J55 - GCM 1 2 3 4 5 6 7 8 9 10 11 12 13 14 15 16 17 18 19 20 21 22 23 24 25 26 27 28 29 30 31 32 33 34 35 36 37 1- PLAS_ENABLE SW * 2- PLAS_ EN_SW_RET 3- GAS PRESS OK RET 4- / GAS PRESS OK 5- POT HIGH (GCM 1000) 6- POT WIPER (GCM 1000) 7- POT LOW (GCM 1000) 8- BASIC ID RET 9- / BASIC ID ** 1011- 1 2 3 4 5 6 7 8 9 10 11 12 13 14 15 16 17 18 19 20 21 22 23 24 25 26 27 28 29 30 31 32 33 34 35 36 37 C GCM 1000 XT Jumper 1415- 24 VAC - RET * Plasma Enable SW in GCM 2010. Jumpered in GCM 1000 XT and DMC 3000. ** Jumper in GCM 1000 XT 27- GAS SEL SW RET 28- GAS SEL SW D J15-1 to chassis used for SC-11 cable shield J15-13 connects SC-11 chassis to PS chassis. The COMM Ref at pin 8 is also for the SC-11 3- / CNC Start (+) 4- / CNC Start (-) 5- Divided Arc V (-) 6- Divided Arc V (+) 7- / Preflow ON (+) 8- COMM Ref (1K Ohm) 9- / Preflow ON (-) 10- / Spare Digital Input (+) 11- / Spare Digital Input (-) 12- OK to Move (-) 14- OK to Move (+) 15 - Key Plug 16- / Hold Start (+) 17- / Hold Start (-) E 21- / Plasma Mark (+) 22- / Plasma Mark (-) 23- / Spare Digital Input(+) 24- / Spare Digital Input (-) 25- / CNC Plasma Enable (+) 26- / CNC Plasma Enable (-) 29- Remote CC Pot High 30- Remote CC (analog) 31- Remote CC Pot Low 32- Stop SW (momentary) * 33- Stop SW Ret 34- Pilot is ON (a) 35- Pilot is ON (b) 36 - 37 Plasma Ready (a) Normally Open Contact * Used with Momentary CNC Start SW Date Victor Technologies Headquarters 16052 Swingley Ridge Road, Suite 300 St Louis, Missouri 63017 USA Date Printed 8/28/2018 The information contained herein is proprietary to Victor Technologies. Not for release, reproduction or distribution without written consent. DAT Date Size C Sheet Title Drawing Number SCHEMATIC 7 8 9 ANNEXE F Date Revised 8/24/2018 Drawn Ultra-Cut XT 200A 480V 6 (133) (134) (135) (136) (137) (138) (139) (140) (141) (142) (144) (145) (144) (145) (146) (147) (148) (149) (150) (151) Art # A-11975_AE By 12 - Tx13 - Rx+ 14 - Rx- J15-CNC CHASSIS GND * CCM code 2.5 or later Rev (104) J22 * Plasma Ready (a) (112) (114) (103) (110) AC 24V-GCM1 J21 1 2 3 4 5 6 7 8 9 10 11 12 13 14 15 16 17 18 19 20 B Comm 019X501800 16 CKT RIBBON J26 GND OK 11 OK to MOVE (-) 10 9 PILOT is ON 8 7 PILOT is ON 6 5 Preflow ON (+) 4 Preflow ON (-) 3 Hold Start (+) 2 Hold Start (-) 1 1 2 3 4 5 6 7 8 9 10 11 12 13 14 15 16 5-HMI Plasma Enable SW 6-HMI Plasma Enable SW 7 - Key Plug 8 - Tx+ 9 - GND RS 485 10 - GND / 422 3 TURNS GAS ON J23- 40 ckt ribbon cable 1 - 24 VAC 2 - 24 VAC Ret 3- Jumper to 24 VAC FERRITE CORE J20 30 CKT PIN HEADER 2 3 4 5 6 7 8 9 10 11 12 13 14 J17 J29 30 CKT RECEPTACLE - BOTTOM ENTRY CPU PCB LEDs ---------------------------D2 RXD (red) D3 TXD (red) D4 CAN BUS (slave) D7 CAN BUS (MAIN) D11 5 VDC POWER D17 STATUS CODE D18 INITIALIZING / PROGRAMMING (red) 3 - Key Plug Display PCB INRUSH CONTROL (116) (117) (120) (115) (119) (118) J30 2 WIRE 1 2 3 4 5 6 1 2 3 4 5 6 7 8 9 10 11 12 NORMAL PROGRAM RS 232 D-SUB SERIAL PROG PORT (108) K1 (63) 5 J47 1 2 3 4 1 2 3 4 5 6 7 8 9 J39 USB PORT (109) AC 120V- TB4-4 J10 USB Cable to Front Panel (101) (102) AC 24V-TB4-2 AC 24V Ret- GCM1 (63) A J54 - Remote HMI & CNC COMM (100) 1 AC 24V GCM1 AC 24V GCM2 (108) (109) (110) (111) (107) 1 2 3 4 5 6 7 8 9 10 11 12 13 14 ANNEXE 24 VAC * New MC1 location requires Relay & Interface PCB revision AB or later. (98) MC1 (OLD) (60) (100) 18 17 16 15 14 13 12 11 10 9 8 7 6 5 4 3 2 1 * (99) 120 VAC Ret (107) * INRUSH CONTROL (K1) MOVED TO RELAY PCB CONTROL OUTPUTS 24 VDC 120 VAC to RAS MC1 (NEW*) (91) J8 CHASSIS GND ARC_SUPPRESSOR (98) (99) ARC_SUPPRESSOR GND J29 1 2 3 4 5 6 7 MC3 PILOT PCB J38 (70) 230 VAC Ret J70 - HE (D2) W1 ARC_SUPPRESSOR 10 230 VAC to HE 400 (69) 230 VAC _ SW _ RET Pump Motor Control 5 6 PILOT A SIG Vin+ PILOT A SIG Vin8 9 7 10 J3 8 Fan Control 10/5/2012 2 of 2 042X1348 10 91 100i / 200i / 300i / 400i ANNEXE 6: SCHÉMA DE PRINCIPE 300A, 380-415 V PG 1 1 2 3 4 5 INVERTER MODULE (IM) #3 (top) J105B IM #3 Section B (upper) AC INPUT 1 2 (7) J100 -- 30 CKT RIBBON J104B (8) 1 2 A J103B (9) 1 2 019X502700 W2A (1) AC INPUT IM #3 Section A (lower) 1 2 J100 -- 30 CKT RIBBON J104A (8) (8) (9) (9) 1 2 J103A W2C (3) (7) (7) W2B (2) ANNEXE J105A 1 2 019X502000 INVERTER MODULE (IM) #2 half module (middle position) B AC SUPPRESSION J50 PCB J51 019X504000 1 2 3 4 5 6 7 8 9 10 11 12 13 14 (1) (2) (3) (10) 1 2 3 4 LT1 (11) PANEL AC INDICATOR (12) J52 LT2 1 2 3 4 GND J105A (23) CHASSIS GND IM #2 Section A (lower) J104A (24) INTERNAL AC INDICATOR AC LINE AC INPUT 1 2 (13) LT1 & LT2 INPUT POWER NEON INDICATORS Rear Panel & Internal J100 -- 30 CKT RIBBON 1 2 J103A (25) 1 2 019X502000 C W1A L1 J105B (1) 1 L2 1 (2) L3 1 (3) (23) (23) (24) (24) 1 2 INVERTER MODULE (IM) #1 (bottom) J100 -- 30 CKT RIBBON J104B W1B MAIN PCB LEDS D3, RED, CAP IMBALANCE D4, GREEN, READY 1 2 J103B Earth (25) 1 2 (25) J105A (1-20) D (23) 18 AWG wire both in and out of CB1 CHASSIS GND J100 -- 30 CKT RIBBON J104A 1 2 J103A (25) (3-22) ON / OFF 1 2 019X502000 FRONT PANEL To J27 on CCM I/O PCB (28) (26) (27A&B) 16 A F1 8A, 500V, SB SYSTEM BIAS SUPPLY PCB F2 8A, 500V, SB 019X501900 J62 +24VDC AC INPUT (27A) E (85A) (86B) (27B) (85B) 1 2 3 4 5 6 7 8 9 10 11 12 13 14 15 16 17 18 4 5 6 7 8 10 11 12 13 K1A K1B 1 2 3 4 5 6 7 8 9 10 11 12 4 3 2 1 TO AUX TRANSFORMER (48) System Bias Test Points SECONDARY GND 24VDC DC INPUT POSITIVE VCC1 VCC2 GATE PRIMARY GND +12V PRIMARY P ISOL GND 3 9 J63 TP1 TP2 TP3 TP4 TP5 TP6 TP7 TP8 TP9 2 GND J60 F 1 LEDS D3, RED, MISSING PHASE +V D4, RED, AC V HIGH D14, RED, AC V LOW D15, GREEN, VAC_IDA D26, GREEN, +12V PRI D27, GREEN, VAC_IDB D30, GREEN, 24VDC D44, GREEN, T1 ON 480V-ID 400V-ID 208-230V-ID COM (86A) CONTROL PCB LEDS D1, RED, INV FLT D14, RED, OVER TEMP D24, GREEN, PWM ON D32, RED, PRI OC IM #1 Section A (lower) AC INPUT 1 2 (24) (2-21) CB1 CAP BIAS PCB LEDS D6, GREEN, -12V D11, GREEN, +12VP D13, GREEN, +12V 019X502700 W1C 1 IM #1 Section B (upper) AC INPUT 14 (Sht 2, E3) 24 VDC 24 VDC MISSING PHASE a MISSING PHASE b AC V HIGH a AC V HIGH b AC V LOW a 24 VDC_RET 24 VDC_RET AC V LOW b VAC_IDA a / VAC_IDA b VAC_IDB a / VAC_IDB b For SYS BIAS PCB VAC_ID LEDs, ON corresponds to 0 in the table. 230V 400V 480V ERR J62-12 (/VAC_IDAb) 0 1 0 1 J61J62-14 (/VAC_IDBb) 0 0 1 1 "0" = 10-12V "1" = 24V Measured relative to TP1 (24VDC_RET) VOLTAGE SELECTION (43A) (44A) TO J12 T1 PRIMARY (Sht 2, A1) (29) (30) (31) (32) (33) (34) (35) (36) (37) (38) (39) (40) (41) (42) Wire #48 from J61-1 to: J61-2 for 208-230 VAC J61-3 for 400 VAC J61-4 for 480 VAC Component Locations (not including PCB components) C4 Capacitor, fan starting, 8uf 440VAC (Sht 2, D2) CB1 Circuit Breaker /ON/OFF SW, 15A 480V (Sht 1, E1) CB2-4 Circuit Breaker, 5A, 250V (Sht 2, B3) F1, 2 Fuse, 8A, 500V, S.B. (Sht 1,E1) FAN1 Fan, Heat Exchanger , 230 VAC (Sht 2, D2) FL1 Flow meter, pulse output (Sht 2, B2) FS1 Flow SW, 0.5 GPM (3.8 lpm), N.O. (Sht 2, A2) HCT1 Current Sensor, Hall Effect 200A, Work Lead (Sht 1, C8) K1 Relay, 24VAC, Inrush Control, (Sht2, B9) L1 Inductor, (Sht 1, B7) L3-9 Toriod Core Common Mode Ind (Sht1 B8, A-D3) LS1 Level Switch, Coolant Tank (Sht 2, A3) LT1, LT2 Indicator, Neon, 250V, AC Volts Present (Sht 1, B2 & C2) M1 Motor, Pump, ½ hp 230VAC, 50/60 Hz, 1Ph (Sht 2, C2) MC1 Relay, 120VAC, Inrush, coil (Sht2, B8, B9) contact (Sht2, A1) MC2 Relay, 120 VAC, Fan Control, coil (Coil at Sht 2, A7)(Contacts at Sht 2, D1) MC3 Relay, 120 VAC, Pump Motor Control, coil (Coil at Sht 2, A7)(Contacts at Sht 2, C1) R2 Inrush, 4.7 Ohm, 30W (Sht2, A1) R3,4 Ext RC, 100 ohm 55W (Sht1, A7) SA1-4 Snubber, Contactor & Relay coils (Sht 2, A8 & A9) T1 Aux Transformer (Sht 2, B2) TB4 Terminal Block (Sht 1, C9) TS1 Temperature Sensor, NTC, Coolant Return (Sht 2, A5) TS2 Temperature Sensor, NTC, Ambient (Sht 2, A5 W1 Contactor , Input (Coil Sht 2, A8), (Contacts C2) W2 Contactor , Input (Coil Sht 2, A8), (Contacts A2) Art # A-11976_AE 1 92 2 3 ANNEXE 4 5 0560956430FR 100i / 200i / 300i / 400i 6 7 8 9 10 TO CCM CPU PCB J36 (Sht 2, C3) (49F) PILOT BOARD LED'S TEST POINTS TP1 GND TP2 PILOT GATE TP3 +5V D2 PILOT ENABLE D11 +5V J102B TO CCM CPU PCB J35 (49) J43 ELECTRODE 1 J41 (J87) (49E) CHASSIS GND J58C (50) J41 5 4 3 2 1 1 2 J40 INVERTER 019X501600 J42 TO RELAY BOARD (51F) L1 (55) HCT1 (51C) Hall Effect Sensor (51) WORK 1 TORCH 4 (51) 2 (49C) (A9) J102A 5 4 3 2 1 ELECTRODE (-) WORK (+) (49B) (51B) TO J1 on RELAY PCB (Sht 2, A5) J102B OUTPUT TO CCM CPU PCB J31 3 1 4 (Sht 1, A9) TIP (56) o AC 120V- TB4-4 (57) b AC 120V- Ret- TB4-3 (58) g AC 24V-TB4-2 (59) w AC 24V- Ret -TB4-1 WORK (+) (49A) 1 2 3 4 5 6 7 8 9 10 11 12 13 14 15 16 17 18 19 20 21 22 23 24 25 26 27 28 29 30 (50) J102A OUTPUT (52) (51) (60) (61) (62) (63) 7 ARC VOLTS (TORCH) 6 TIP VOLTS (PILOT) 5 WORK 4 3 2 1 120 VAC @ 100 ma. 24 VAC @ 1A (J10 Sht 2, B8) RIBBON CABLE 30 ckt. CCM (J31-36) - INVERTER (J100) ELECTRODE (-) C TB4 (49) (Sht 2, C3) 5 4 3 2 1 3 TURNS COMMON J46-F SIG (+) +15 VDC 2 1 2 1 (Sht 2, C3) J46-M 2 FERRITE CORE J16 TO CCM CPU PCB J32 -15 VDC OUTPUT (+) Work (51) 1 WORK (+) B WORK ARC VOLTS 3 5 4 3 2 1 Tip (53) (Sht 2, D3) ELECTRODE (-) TO I/O BOARD TIP VOLTS To J24 on I-O PCB (Sht 2, C3) (+) To / From Optional 1 Torch Module (Refer to 1 Torch section for details.) J45 10 ckt Ribbon TO J3 on RELAY PCB (Sht 2, A5) TO CCM CPU PCB J33 (-) CHASSIS GND TIP 1 2 3 4 5 6 7 8 (51E) J102A OUTPUT ANNEXE WORK (+) RAS 1 (52) EARTH GROUND 1 2 3 4 5 6 7 8 9 10 ELECTRODE (-) PILOT TIP To TB4-6 R3 & R4 5 4 3 2 1 A PILOT PCB J44 J58A (Sht 2, C3) 1 TORCH To TB4-7 Electrode OUTPUT TORCH (49) (51F) 2 1 WORK (+) 5 4 3 2 1 1 ELECTRODE (-) RIBBON CABLE 40 ckt CCM (J23) - RELAY PCB (J4) 32 COMMON 1 COMMON 33 -15 VDC 2 /1TORCH START * 34 COMMON 3 NA 35 24 VDC 4 /1TORCH GAS SOL ON * 36 COMMON 5 /MAIN TORCH IDLE * 37 24 VDC 6 /1TORCH PRESS OK * 38 COMMON 7 FLOW SENSOR (pulses) 39 24 VDC 8 LOW COOLANT FLOW 40 COMMON 9 COOLANT LEVEL OK 10 COMMON RIBBON CABLE 16 ckt 11 NA CCM ( J37) - DISPLAY 12 /PLASMA ENABLE-HMI PCB (J17) 13 /COOLANT PUMP ON 14 COMMON 15 /PILOT ENABLE 1,3,5,7 24 VDC 16 /RAS ON 2,4,6,8 COMMON 17 /CONTACTORS ON 9,10 NC 18 COMMON 11-16 SERIAL DATA 19 /COOLANT FANS ON 20 /1TORCH CONTACTOR ON * 21 /PLASMA ENABLE RELAY 22 COMMON RIBBON CABLE 10 ckt 23 PILOT CURRENT SIGRELAY PCB (J3) – PILOT PCB (J42) 24 NC 25 PILOT CURRENT SIG+ 26 COMMON 1,2 24 VDC 27 WORK CURRENT SIG3,4,7,10 COMMON 28 WORK CURRENT SIG+ 5 PILOT ENABLE + 29 NC 6 PILOT ENABLE – 30 AMBIENT TEMP 8 PILOT CURRENT SIG – 31 COOLANT TEMP 9 PILOT CURRENT SIG + * Used with 1 Torch Option READY + READY INVERTER_FLT + INVERTER_FLT OVERTEMP_FLT + OVERTEMP_FLT PWR_PRESENT + PWR_PRESENT OUT_COM (+3 to 5VDC) VAC_SELA VAC_SELB IS_IDA IS_IDB IS_IDC ENABLE + ENABLE START2 + START2 SPARE SYNC_IN + SYNC_IN NC NC 47 OHM to COMM DEMAND + DEMAND 47 OHM to COMM CURRENT + CURRENT 47 OHM to COMM D E Art # A-11976_AE Revision Rev 00 Initial Design AA ) By Date DAT 10/03/2012 DAT 9/16/2014 AB ECO 1 Torch Option DAT 10/17/2014 AC VCR-02672 MC1, K1 change DAT 8/3/2018 Revision Rev By Date Victor Technologies Headquarters 16052 Swingley Ridge Road, Suite 300 St Louis, Missouri 63017 USA Date Printed 8/28/2018 Drawn Date The information contained herein is proprietary to Victor Technologies. Not for release, reproduction or distribution without written consent. DAT Size C Sheet Title Drawing Number SCHEMATIC Ultra-Cut XT 300A 480V 6 0560956430FR 7 8 9 ANNEXE F Date Revised 8/3/2018 10/05/2012 1 of 2 042X1347 10 93 100i / 200i / 300i / 400i ANNEXE 7: SCHÉMA DE PRINCIPE 300A, 380-415 V PG 2 COOLANT LEVEL (89) J5 1 5 2 6 3 7 4 8 T1 J49 460V 1 2 3 4 5 6 7 8 1 2 3 4 (81) (82) 24V RET (79) BLUE 6 RED 24V B 400V (74) (75) CB3 5 A (73) 2 (71) (72) CB4 5 A YELLOW 1 120V_2 220V 5 RED 120V-1 RET 12 11 10 9 8 7 6 5 4 3 2 1 (77) (78) CB2 5 A (76) YELLOW 4 BLUE 3 120V_2 RET J6 J9 J14 120V_1 1 2 3 R MC2A MC2B (64A) 120VAC_2 24VAC D2, GREEN, 1TORCH GAS ON D7, GREEN, PILOT ENABLED D11, GREEN, PILOT CURRENT D12, GREEN, WORK CURRENT D22, GREEN, CONTACTORS ON D23, GREEN, RF ON D24, GREEN, FANS ON D25, GREEN, PLASMA ENABLED D26, GREEN, 1TORCH ON D27, GREEN, COOLANT ON J72 (69) 1 2 3 (70) BK C4 1 TORCH INTERFACE BIAS TRANSFORMER (Sht 1, B8) FAN1 BN BL (55) 1 2 3 230 VAC _ SW (A9) CHASSIS GND J34 - 30 CKT RIBBON J35 - 30 CKT RIBBON J36 - 30 CKT RIBBON 1 2 3 4 5 6 7 8 (Sht 1 F2) E 1 2 3 4 5 6 7 8 9 10 I / O PCB DIP SW --------------------------------------------SW6 OK TO MOVE (CONTACTS, VOLTS) SW11 ANALOG CC SOURCE SW12 DIVIDED ARC VOLTAGE (50:1, 16.7:1, 30:1, 40:1, 25:1) 11 12 13 14 J27 For SYS BIAS PCB VAC_ID LEDs, ON corresponds to 0 in the table. 230V 400V 480V ERR J62-12 (/VAC_IDAb) 0 1 0 1 J62-14 (/VAC_IDBb) 0 0 1 1 J28 30 CKT PIN HEADER I / O PCB TEST POINTS ------------------------------------TP1 PCB COMMON TP2 COOLANT FANS ON TP3 PUMP ON TP4 LOW FLOW (SW) TP5 FLOW SIGNAL (pulse, Ultracut only) TP6 +15VDC_ISO (ref to TP10) TP7 -15VDC_ISO (ref to TP10) TP8 +16-18 VDC_ISO (ref to TP10) TP9 ANALOG CURRENT SIGNAL (remote & Autocut only) TP10 ISOLATED VOLTAGE COMMON TP11 1 TORCH CONTACTOR ON TP12 +5 VDC TP13 -15 VDC TP14 +15 VDC TP15 +24 VDC TP18 +5 VDC_ISO (ref to TP10) Harness from System Bias PCB (29) (30) (31) (32) (33) (34) (35) (36) (37) (38) (39) (40) (41) (42) J85 I / O PCB LEDS ---------------------------------------------D2 CNC PLASMA ENABLE D3 E-STOP_PS D4 GAS ON (Auto-cut, PAK) D6 CNC START D8 HOLD START D12 PREFLOW ON D13 CSD (corner current reduction) D18 MARK D20 SPARE D25 EXP METAL D33 OK_CNC D37 PSR D41 SPARE OUT 2 D43 SPARE OUT 1 230 VAC_SW goes to J70 for HE 400 24 VDC 24 VDC MISSING PHASE a MISSING PHASE b AC V HIGH a AC V HIGH b AC V LOW a 24 VDC_RET 24 VDC_RET AC V LOW b VAC_IDA a / VAC_IDA b VAC_IDB a / VAC_IDB b J84 CPU PCB (CCM) J28 30 CKT RECEPTACLE - BOTTOM ENTRY I-O PCB (CCM) J24 (70) J32 - 30 CKT RIBBON J33 - 30 CKT RIBBON (53) (51) J73 (70) 019X501700 N/C Harness from Pilot PCB J45 R (69) Test Points TP1, GND TP2, -15V TP3, +5VDC TP4, +12V TP5, +24V TP6, +15V TP7, +5VDC Refer to 1 Torch Module Schematic for Details 120VAC_1 230 VAC _ SW _ RET TIP VOLTS 230 VAC (69) (65A) D Torch Coolant Pump (67) WORK (64B) TORCH FLOW SENSOR 19X501100 ARC VOLTS MC3BCHASSIS GND J13 to CB5 and to MC2 & MC3, also J14, J16 all 18 AWG M1 J16 (66) TEMP SENSOR J11 To J100 of IM #3B To J100 of IM #3A (Sht 1, A,B6) 1 2 3 4 (64A) (64B) (65A) (65B) MC3A J2 RELAY & INTERFACE PCB +5VDC SIGNAL (pulse) J31 - 30 CKT RIBBON To J100 of IM #2A (Sht 1, B,C6) J13 (95) WORK CURRENT SENSOR To J100 of IM #1B To J100 of IM #1A (Sht 1, C,D6) 0V C J1 LEVEL SENSORS (94) 14 13 12 11 10 9 8 7 6 5 4 3 2 1 ANNEXE 3 (80) 1 2 3 4 (93) 3 2 1 2 J12 J7 COOLANT FLOW SW r b g 1 TS1 5 4 3 2 1 FL1 (87) 8 7 6 5 4 3 2 1 R2 2 1 0.7 GPM 4.7 30W (92) COOLANT 6 5 4 3 2 1 (83) 1 (84) 1 2 TS2 (59) (58) (57) (56) J74 AMBIENT COMMON SIG (+) -15 VDC +15 VDC COOLANT MC1A 4 J71 FS1 (44A) (43) (90) 2 3 From Sys Bias J63 (Sht 1, F2) A 1 LS1 5 2 J12 = Mini-Fit Jr 400 VAC -- Single 18 AWG in pins 1 & 4 480 VAC -- Single 18 AWG in pins 1 & 8 230 VAC -- 18 AWG wires in pins 1,5,2,6 4 TO HCT1 (Work) 3 3 2 4 1 19X501200 "0" = 10-12V "1" = 24V Measured relative to TP1 (24VDC_RET) F Art # A-11977_AE 1 94 2 3 ANNEXE 4 5 0560956430FR 100i / 200i / 300i / 400i 6 7 MC2 8 9 Fan Control (96) SA1 (161) (160) SA3 230 VAC _ SW SA2 (D2) W2 10 230 VAC to HE 400 (70) 230 VAC Ret (69) (69) 230 VAC _ SW _ RET W1 ARC_SUPPRESSOR (70) SA4 ARC_SUPPRESSOR (D2) 120VAC * New MC1 location requires Relay & Interface PCB revision AB or later. 120 VAC_1 * INRUSH CONTROL 120 VAC_2 J4 -- 40 CKT RIBBON CABLE HMI/GCM (104) (62) (106) AC 24V GCM2 AC 120V - GCM (108) (109) (110) (111) (63) (113) (61) AC 24V - RET - GCM2 AC 120V- Ret- GCM AC 120V- Ret- TB4-3 J18 1 2 3 4 1 2 3 4 J19 (101) (102) AC 24V-TB4-2 AC 120V- TB4-4 (108) (115) AC 24V Ret- GCM1 (63) (62)1 (116) (117) Harness AC 24V- Ret -TB4-1 (118) K1 (OLD) (119) (120) 2 GND GND 4 WIRE RxTx+ Rx+ Tx- 1 2 3 4 5 6 J37 Harness ENABLE PLAS_ENABLE SW PLAS_ EN_SW_RET / GAS PRESS OK / BASIC ID CPU PCB DIP SW --------------------------------------------SW1 AUTO PILOT RESTART SW3 PREFLOW TIME SW4 POSTFLOW TIME SW5 FUNCTION SW8 SYSTEM CONTROL (pilot time, etc.) SW9 RESERVED (future) SW10 ADDRESS (default = 0) SW13 UNIT TYPE (AC / UC) SW14 LINE TERMINATION (serial comm.) 12 OK2 (contact) +10V (CC Pot Hi) 11 CC Pot Wiper 10 CC Pot Low 9 Div Arc V (+) 8 Div Arc V (-) 7 /Start - Stop (+) 6 /Start - Stop (-) 5 4 Stop Mom NC 3 OK2 (contact) / CNC Enable (+) 2 / CNC Enable (-) 1 3 TURNS 019X501800 16 CKT RIBBON (121) (122) (123) (124) (125) (126) (127) (128) (129) (130) (131) GND 1 2 3 4 5 6 7 8 9 10 11 12 13 14 15 16 17 18 TB2 OK to MOVE (+) 12 11 OK to MOVE (-) 10 PILOT is ON PILOT is ON Preflow ON (+) Preflow ON (-) Hold Start (+) Hold Start (-) 1 2 3 4 5 6 7 8 9 10 11 12 13 14 15 16 (130) (131) (112) (114) (121) (122) (124) (129) (128) (123) +10V GND GND TB3 Spare Digital Inputs 12 11 10 9 8 * Plasma Ready (b) 7 6 Spare 5 Digital 4 Inputs 3 / Plasma Marking (-) 2 / Plasma Marking (+) 1 PSR * Plasma Ready (a) 00 Initial Design AA AB AC ECO 1 Torch Option VCR-02672 MC1, K1 change By Date DAT 10/03/2012 DAT 9/16/2014 DAT 10/17/2014 DAT Revision Rev (111) AC 24V Ret-GCM2 (166) J69 (167) (133) (134) (137) (139) (138) (143) AC 120V - GCM AC 120V- Ret- GCM FERRITE CORE 3 TURNS (106) (113) CHASSIS GND (140) (141) (136) (135) (132) (153) FERRITE CORE 3 TURNS J21 1 2 3 4 5 6 7 8 9 10 11 12 13 14 15 16 17 18 19 20 (104) AC 24V-GCM2 2 1 (152) (154) (155) (132) (152) (153) (154) (155) (156) (157) (158) (159) (156) (157) (158) (159) Art # A-11977_AE 0560956430FR J55 - GCM 1 2 3 4 5 6 7 8 9 10 11 12 13 14 15 16 17 18 19 20 21 22 23 24 25 26 27 28 29 30 31 32 33 34 35 36 37 1- PLAS_ENABLE SW * 2- PLAS_ EN_SW_RET 3- GAS PRESS OK RET 4- / GAS PRESS OK 5- POT HIGH (GCM 1000) 6- POT WIPER (GCM 1000) 7- POT LOW (GCM 1000) 8- BASIC ID RET 9- / BASIC ID ** 1011GCM 1000 XT Jumper 1415- 24 VAC - RET * Plasma Enable SW in GCM 2010. Jumpered in GCM 1000 XT and DMC 3000. ** Jumper in GCM 1000 XT 27- GAS SEL SW RET 28- GAS SEL SW D J15-1 to chassis used for SC-11 cable shield J15-13 connects SC-11 chassis to PS chassis. J15-CNC 1 2 3 4 5 6 7 8 9 10 11 12 13 14 15 16 17 18 19 20 21 22 23 24 25 26 27 28 29 30 31 32 33 34 35 36 37 C The COMM Ref at pin 8 is also for the SC-11 3- / CNC Start (+) 4- / CNC Start (-) 5- Divided Arc V (-) 6- Divided Arc V (+) 7- / Preflow ON (+) 8- COMM Ref (1K Ohm) 9- / Preflow ON (-) 10- / Spare Digital Input (+) 11- / Spare Digital Input (-) 12- OK to Move (-) 14- OK to Move (+) 15 - Key Plug 16- / Hold Start (+) 17- / Hold Start (-) E 21- / Plasma Mark (+) 22- / Plasma Mark (-) 23- / Spare Digital Input(+) 24- / Spare Digital Input (-) 25- / CNC Plasma Enable (+) 26- / CNC Plasma Enable (-) 29- Remote CC Pot High 30- Remote CC (analog) 31- Remote CC Pot Low 32- Stop SW (momentary) * 33- Stop SW Ret 34- Pilot is ON (a) 35- Pilot is ON (b) 36 - 37 Plasma Ready (a) Normally Open Contact * Used with Momentary CNC Start SW Date Victor Technologies Headquarters 16052 Swingley Ridge Road, Suite 300 St Louis, Missouri 63017 USA 8/3/2018 Date Printed 8/28/2018 Drawn The information contained herein is proprietary to Victor Technologies. Not for release, reproduction or distribution without written consent. DAT Date Size C Sheet Title Drawing Number SCHEMATIC Ultra-Cut XT 300A 480V 6 (143) (146) (147) (148) (149) (150) (151) J22 By (133) (134) (135) (136) (137) (138) (139) (140) (141) (142) (144) (145) (144) (145) (146) (147) (148) (149) (150) (151) * CCM code 2.5 or later Revision AC 24V Ret - GCM1 (125) (126) (127) (142) (112) (114) (103) (110) AC 24V-GCM1 J26 OK 9 8 7 6 5 4 3 2 1 12 - Tx13 - Rx+ 14 - Rx- FERRITE CORE GAS ON CPU PCB TEST POINTS -------------------------------------------TP1 GND (PCB common) TP2 +5V_ISO (REF TP5) TP3 +24 VDC TP4 +3.3V TP5 GND_ISO TP6 +5.0 V TP7 TOTAL DEMAND (3.3V = 400A) TP9 /WR TP10 /RD TP11 CPU TEMP SENSE TP12 +3.3VA TP13 -15VDAC TP14 PC2 TP15 +15VDAC TP16 CLKO TP18 OSC_CLOCK 7 B Comm J17 (116) (117) (120) (115) (119) (118) J30 J23- 40 ckt ribbon cable TB1 5-HMI Plasma Enable SW 6-HMI Plasma Enable SW 7 - Key Plug 8 - Tx+ 9 - GND RS 485 10 - GND / 422 Display PCB INRUSH CONTROL J20 30 CKT PIN HEADER 1 - 24 VAC 2 - 24 VAC Ret 3- Jumper to 24 VAC 3 (61) (63) 5 J29 30 CKT RECEPTACLE - BOTTOM ENTRY CPU PCB LEDs ---------------------------D2 RXD (red) D3 TXD (red) D4 CAN BUS (slave) D7 CAN BUS (MAIN) D11 5 VDC POWER D17 STATUS CODE D18 INITIALIZING / PROGRAMMING (red) 2 3 4 5 6 7 8 9 10 11 12 13 14 (109) 4 (107) 2 WIRE PROG USB IC (60) J47 1 2 3 4 5 6 7 8 9 10 11 12 NORMAL PROGRAM 1 2 3 4 5 6 1 2 3 4 5 6 7 8 9 10 11 12 J54 - Remote HMI & CNC COMM (100) 1 AC 24V GCM1 (62) J10 J39 USB PORT 1 2 3 4 5 6 7 8 9 RS 232 D-SUB SERIAL PROG PORT (107) 120VAC (101) (102) (103) USB Cable to Front Panel J38 (98) A 3 - Key Plug ANNEXE 24 VAC (99) 120 VAC Ret 1 2 3 4 5 6 7 8 9 10 11 12 13 14 MC1 (OLD) (60) (100) 18 17 16 15 14 13 12 11 10 9 8 7 6 5 4 3 2 1 * 120 VAC_RET (107) * INRUSH CONTROL (K1) MOVED TO RELAY PCB CONTROL OUTPUTS 24 VDC 120 VAC to RAS MC1 (NEW*) 16 15 14 13 12 11 10 9 8 7 6 5 4 3 2 1 2 1 4 3 (97) (98) (99) (91) J8 CHASSIS GND ARC_SUPPRESSOR (97) ARC_SUPPRESSOR GND Rev 1 2 3 4 5 6 7 J59 - RAS (96) (163) (162) / PILOT ENABLE / PILOT ENABLE RET MC3 PILOT PCB J29 J70 - HE Pump Motor Control 5 6 8 9 7 J3 10 PILOT A SIG Vin+ PILOT A SIG Vin- 10 CKT RIBBON TO PILOT PCB 8 ANNEXE 9 F Date Revised 8/24/2018 10/5/2012 2 of 2 042X1347 10 95 100i / 200i / 300i / 400i ANNEXE 8: SCHÉMA DE PRINCIPE 400A, 380-415 V PG 1 1 2 3 4 5 INVERTER MODULE (IM) #3 (top) J105B AC INPUT IM #3 Section B (upper) 1 2 (7) J100 -- 30 CKT RIBBON J104B (8) 1 2 A J103B (9) 1 2 019X502700 W2A (1) AC INPUT IM #3 Section A (lower) 1 2 J100 -- 30 CKT RIBBON J104A (8) (8) (9) (9) 1 2 J103A W2C (3) (7) (7) W2B (2) ANNEXE J105A 1 2 019X502000 B 1 2 3 4 5 6 7 8 9 10 11 12 13 14 (1) (2) (3) (7) (10) 1 2 3 4 J100 -- 30 CKT RIBBON 1 2 (8) J103B (9) 1 2 (12) 019X502700 LT2 1 2 3 4 J105A (23) AC INPUT 1 2 (13) IM #2 Section A (lower) J100 -- 30 CKT RIBBON J104A (24) INTERNAL AC INDICATOR CHASSIS GND IM #2 Section B (upper) J104B LT1 (11) J52 AC LINE AC INPUT 1 2 PANEL AC INDICATOR GND INVERTER MODULE (IM) #2 (middle) J105B AC SUPPRESSION PCB J50 019X504000 J51 LT1 & LT2 INPUT POWER NEON INDICATORS Rear Panel & Internal 1 2 J103A (25) 1 2 019X502000 C W1A L1 J105B (1) 1 L2 1 (2) L3 1 (3) (23) (23) (24) (24) 1 2 INVERTER MODULE (IM) #1 (bottom) AC INPUT J104B W1B MAIN PCB LEDS D3, RED, CAP IMBALANCE D4, GREEN, READY 1 2 J103B Earth (25) 1 2 (25) J105A (1-20) D (23) 18 AWG wire both in and out of CB1 CHASSIS GND CB1 J100 -- 30 CKT RIBBON 1 2 J103A (25) 1 2 019X502000 FRONT PANEL To J27 on CCM I/O PCB (28) (26) (27A&B) 16 A F1 SYSTEM BIAS SUPPLY PCB F2 8A, 500V, SB 019X501900 J62 +24VDC AC INPUT (27A) E (85A) (86B) (27B) (85B) 1 2 3 4 5 6 7 8 9 10 11 12 13 14 15 16 17 18 4 5 6 7 8 10 11 12 13 K1A K1B 1 2 3 4 5 6 7 8 9 10 11 12 4 3 2 1 TO AUX TRANSFORMER (48) System Bias Test Points F 3 9 J63 SECONDARY GND 24VDC DC INPUT POSITIVE VCC1 VCC2 GATE PRIMARY GND +12V PRIMARY P ISOL GND 2 GND J60 TP1 TP2 TP3 TP4 TP5 TP6 TP7 TP8 TP9 1 LEDS D3, RED, MISSING PHASE + V D4, RED, AC V HIGH D14, RED, AC V LOW D15, GREEN, VAC_IDA D26, GREEN, +12V PRI D27, GREEN, VAC_IDB D30, GREEN, 24VDC D44, GREEN, T1 ON (43A) 14 480V-ID 400V-ID 208-230V-ID COM (86A) IM #1 Section A (lower) AC INPUT 1 2 (24) (3-22) 8A, 500V, SB J100 -- 30 CKT RIBBON CONTROL PCB LEDS D1, RED, INV FLT D14, RED, OVER TEMP D24, GREEN, PWM ON D32, RED, PRI OC J104A (2-21) ON / OFF CAP BIAS PCB LEDS D6, GREEN, -12V D11, GREEN, +12VP D13, GREEN, +12V 019X502700 W1C 1 IM #1 Section B (upper) J61 (Sht 2, E3) 24 VDC 24 VDC MISSING PHASE a MISSING PHASE b AC V HIGH a AC V HIGH b AC V LOW a 24 VDC_RET 24 VDC_RET AC V LOW b VAC_IDA a / VAC_IDA b VAC_IDB a / VAC_IDB b (29) (30) (31) (32) (33) (34) (35) (36) (37) (38) (39) (40) (41) (42) For SYS BIAS PCB VAC_ID LEDs, ON corresponds to 0 in the table. 230V 400V 480V ERR J62-12 (/VAC_IDAb) 0 1 0 1 J62-14 (/VAC_IDBb) 0 0 1 1 "0" = 10-12V "1" = 24V Measured relative to TP1 (24VDC_RET) VOLTAGE SELECTION (44A) TO J12 Wire #48 from J61-1 to: T1 PRIMARY J61-2 for 208-230 VAC J61-3 for 400 VAC (Sht 2, A1) J61-4 for 480 VAC Component Locations (not including PCB components) C4 Capacitor, fan starting, 8uf 440VAC (Sht 2, D2) CB1 Circuit Breaker /ON/OFF SW, 15A 480V (Sht 1, E1) CB2-4 Circuit Breaker, 5A, 250V (Sht 2, B3) F1, 2 Fuse, 8A, 500V, S.B. (Sht 1,E1) FAN1 Fan, Heat Exchanger , 230 VAC (Sht 2, D2) FL1 Flow meter, pulse output (Sht 2, B2) FS1 Flow SW, 0.5 GPM (3.8 lpm), N.O. (Sht 2, A2) HCT1 Current Sensor, Hall Effect 200A, Work Lead (Sht 1, C8) K1 Relay, 24VAC, Inrush Control, (Sht2, B9) L1 Inductor, (Sht 1, B7) L3-9 Toriod Core Common Mode Ind (Sht1 B8, A-D3) LS1 Level Switch, Coolant Tank (Sht 2, A3) LT1, LT2 Indicator, Neon, 250V, AC Volts Present (Sht 1, B2 & C2) M1 Motor, Pump, ½ hp 230VAC, 50/60 Hz, 1Ph (Sht 2, C2) MC1 Relay, 120VAC, Inrush, coil (Sht2, B8, B9) contact (Sht2, A1) MC2 Relay, 120 VAC, Fan Control, coil (Coil at Sht 2, A7)(Contacts at Sht 2, D1) MC3 Relay, 120 VAC, Pump Motor Control, coil (Coil at Sht 2, A7)(Contacts at Sht 2, C1) R2 Inrush, 4.7 Ohm, 30W (Sht2, A1) R3,4 Ext RC, 100 ohm 55W (Sht1, A7) SA1-4 Snubber, Contactor & Relay coils (Sht 2, A8 & A9) T1 Aux Transformer (Sht 2, B2) TB4 Terminal Block (Sht 1, C9) TS1 Temperature Sensor, NTC, Coolant Return (Sht 2, A5) TS2 Temperature Sensor, NTC, Ambient (Sht 2, A5) W1 Contactor , Input (Coil Sht 2, A8), (Contacts C2) W2 Contactor , Input (Coil Sht 2, A8), (Contacts A2) Art # A-11978_AE 1 96 2 3 ANNEXE 4 5 0560956430FR 100i / 200i / 300i / 400i 6 7 8 9 10 TO CCM CPU PCB J36 (Sht 2, C3) (49F) D2 PILOT ENABLE D11 +5V TO CCM CPU PCB J35 TEST POINTS TP1 GND TP2 PILOT GATE TP3 +5V J43 ELECTRODE EARTH GROUND 1 (51F) L1 (Sht 2, C3) 1 2 3 4 5 6 7 8 (55) HCT1 (51) (51C) Hall Effect Sensor (51) WORK 1 4 (49C) TORCH (A9) J102A 5 4 3 2 1 ELECTRODE (-) WORK (+) (49B) TO J1 on RELAY PCB (Sht 2, A5) J102B OUTPUT TO CCM CPU PCB J31 3 2 1 4 (49) (Sht 1, A9) TIP (Sht 1, A9) (56) o AC 120V- TB4-4 (57) b AC 120V- Ret- TB4-3 (58) g AC 24V-TB4-2 (59) w AC 24V- Ret -TB4-1 RIBBON CABLE 30 ckt. CCM (J31-36) - INVERTER (J100) WORK (+) 5 4 3 2 1 (51) (60) (61) (62) (63) 7 6 TIP VOLTS (PILOT) 5 WORK 4 3 2 1 120 VAC @ 100 ma. 24 VAC @ 1A RIBBON CABLE 40 ckt CCM (J23) - RELAY PCB (J4) 32 COMMON 1 COMMON 33 -15 VDC 2 /1TORCH START * 34 COMMON 3 NA 35 24 VDC 4 /1TORCH GAS SOL ON * 36 COMMON 5 /MAIN TORCH IDLE * 37 24 VDC 6 /1TORCH PRESS OK * 38 COMMON 7 FLOW SENSOR (pulses) 39 24 VDC 8 LOW COOLANT FLOW 40 COMMON 9 COOLANT LEVEL OK 10 COMMON RIBBON CABLE 16 ckt 11 NA CCM ( J37) - DISPLAY 12 /PLASMA ENABLE-HMI PCB (J17) 13 /COOLANT PUMP ON 14 COMMON 15 /PILOT ENABLE 1,3,5,7 24 VDC 16 /RAS ON 2,4,6,8 COMMON 17 /CONTACTORS ON 9,10 NC 18 COMMON 11-16 SERIAL DATA 19 /COOLANT FANS ON 20 /1TORCH CONTACTOR ON * 21 /PLASMA ENABLE RELAY 22 COMMON RIBBON CABLE 10 ckt 23 PILOT CURRENT SIGRELAY PCB (J3) – PILOT PCB (J42) 24 NC 25 PILOT CURRENT SIG+ 26 COMMON 1,2 24 VDC 27 WORK CURRENT SIG3,4,7,10 COMMON 28 WORK CURRENT SIG+ 5 PILOT ENABLE + 29 NC 6 PILOT ENABLE – 30 AMBIENT TEMP 8 PILOT CURRENT SIG – 31 COOLANT TEMP 9 PILOT CURRENT SIG + * Used with 1 Torch Option (49A) 1 2 3 4 5 6 7 8 9 10 11 12 13 14 15 16 17 18 19 20 21 22 23 24 25 26 27 28 29 30 (50) J102A OUTPUT (52) ARC VOLTS (TORCH) (J10 Sht 2, B8) (Sht 2, C3) ELECTRODE (-) C TB4 3 TURNS COMMON J46-F (51B) FERRITE CORE? SIG (+) 2 1 (Sht 2, C3) J46-M +15 VDC 2 1 J16 TO CCM CPU PCB J32 -15 VDC OUTPUT (+) Work (51) 2 WORK (+) B WORK ARC VOLTS 1 5 4 3 2 1 ELECTRODE (-) Tip (53) (Sht 2, D3) TO CCM CPU PCB J33 TO I/O BOARD TIP VOLTS To J24 on I-O PCB J102B OUTPUT (+) To / From Optional 1 Torch Module (Refer to 1 Torch section for details.) J45 10 ckt Ribbon TO J3 on RELAY PCB (Sht 2, A5) (49D) (51D) (-) CHASSIS GND 019X501600 J42 1 2 3 4 5 6 7 8 9 10 J40 TO RELAY BOARD 3 WORK (+) 1 2 TIP INVERTER (Sht 2, C3) 5 4 3 2 1 J41 5 4 3 2 1 TO CCM CPU PCB J34 ELECTRODE (-) CHASSIS GND J58C (50) J102A OUTPUT J41 (J87) (49E) (51E) RAS 1 ANNEXE WORK (+) 5 4 3 2 1 PILOT (52) J44 R3 & R4 ELECTRODE (-) A TIP To TB4-6 PILOT PCB J58A (Sht 2, C3) 1 TORCH To TB4-7 (49) Electrode (51F) J102B OUTPUT TORCH (49) PILOT BOARD LED'S 2 1 WORK (+) 5 4 3 2 1 1 ELECTRODE (-) READY + READY INVERTER_FLT + INVERTER_FLT OVERTEMP_FLT + OVERTEMP_FLT PWR_PRESENT + PWR_PRESENT OUT_COM (+3 to 5VDC) VAC_SELA VAC_SELB IS_IDA IS_IDB IS_IDC ENABLE + ENABLE START2 + START2 SPARE SYNC_IN + SYNC_IN NC NC 47 OHM to COMM DEMAND + DEMAND 47 OHM to COMM CURRENT + CURRENT 47 OHM to COMM D E Art # A-11978_AE Rev 01 Revision By Date Initial Design DAT 10/5/2012 DAT 9/16/2014 DAT 10/17/2014 AA AB AC ECO 1 Torch Option VCR-02672 MC1, K1 change DAT Revision Rev By Date Victor Technologies Headquarters 16052 Swingley Ridge Road, Suite 300 St Louis, Missouri 63017 USA Date Printed 8/28/2018 8/3/2018 Drawn The information contained herein is proprietary to Victor Technologies. Not for release, reproduction or distribution without written consent. DAT Size C Title Drawing Number SCHEMATIC Ultra-Cut XT 400A 480V 6 0560956430FR 7 8 ANNEXE 9 F Date Revised 8/3/2018 Date 10/05/2012 Sheet 1 of 2 042X1346 10 97 100i / 200i / 300i / 400i ANNEXE 9: SCHÉMA DE PRINCIPE 400A, 380-415 V PG 2 (89) 3 COOLANT LEVEL (83) J5 FL1 2 1 5 2 6 3 7 4 8 3 (80) 1 2 3 4 T1 1 2 3 4 (81) (82) J49 460V 24V RET 1 2 3 4 5 6 7 8 (79) BLUE 6 RED 24V B 400V (74) (75) CB3 5 A (73) 3 RED 2 YELLOW 120V_2 220V 4 BLUE 12 11 10 9 8 7 6 5 4 3 2 1 (77) (78) CB2 5 A (76) 5 YELLOW 120V_2 RET J6 (71) (72) CB4 5 A 1 J9 J14 120V-1 RET 0V (64B) 1 2 3 230 VAC SIGNAL (pulse) TORCH FLOW SENSOR 120VAC_2 24VAC Torch Coolant Pump (67) (64A) Harness from Pilot PCB J45 (Sht 1, B8) BL R (55) 1 2 3 230 VAC _ SW (A9) CHASSIS GND J34 - 30 CKT RIBBON J35 - 30 CKT RIBBON J36 - 30 CKT RIBBON 1 2 3 4 5 6 7 8 1 2 3 4 5 6 7 8 9 10 J28 30 CKT PIN HEADER 11 12 13 14 J27 For SYS BIAS PCB VAC_ID LEDs, ON corresponds to 0 in the table. 230V 400V 480V ERR J62-12 (/VAC_IDAb) 0 1 0 1 J62-14 (/VAC_IDBb) 0 0 1 1 CPU PCB (CCM) I / O PCB TEST POINTS ------------------------------------TP1 PCB COMMON TP2 COOLANT FANS ON TP3 PUMP ON TP4 LOW FLOW (SW) TP5 FLOW SIGNAL (pulse, Ultracut only) TP6 +15VDC_ISO (ref to TP10) TP7 -15VDC_ISO (ref to TP10) TP8 +16-18 VDC_ISO (ref to TP10) TP9 ANALOG CURRENT SIGNAL (remote & Autocut only) TP10 ISOLATED VOLTAGE COMMON TP11 1 TORCH CONTACTOR ON TP12 +5 VDC TP13 -15 VDC TP14 +15 VDC TP15 +24 VDC TP18 +5 VDC_ISO (ref to TP10) (Sht 1 F2) E J85 I / O PCB LEDS ---------------------------------------------D2 CNC PLASMA ENABLE D3 E-STOP_PS D4 GAS ON (Auto-cut, PAK) D6 CNC START D8 HOLD START D12 PREFLOW ON D13 CSD (corner current reduction) D18 MARK D20 SPARE D25 EXP METAL D33 OK_CNC D37 PSR D41 SPARE OUT 2 D43 SPARE OUT 1 Harness from System Bias PCB (29) (30) (31) (32) (33) (34) (35) (36) (37) (38) (39) (40) (41) (42) J84 J28 30 CKT RECEPTACLE - BOTTOM ENTRY I-O PCB (CCM) 230 VAC_SW goes to J70 for HE 400 24 VDC 24 VDC MISSING PHASE a MISSING PHASE b AC V HIGH a AC V HIGH b AC V LOW a 24 VDC_RET 24 VDC_RET AC V LOW b VAC_IDA a / VAC_IDA b VAC_IDB a / VAC_IDB b J32 - 30 CKT RIBBON J33 - 30 CKT RIBBON J24 (70) 019X501700 J11 (53) (51) J73 (69) (70) TIP VOLTS FAN1 BN WORK 1 2 3 (70) BK C4 ARC VOLTS J72 (69) Test Points TP1, GND TP2, -15V TP3, +5VDC TP4, +12V TP5, +24V TP6, +15V TP7, +5VDC 1 TORCH INTERFACE BIAS TRANSFORMER 230 VAC _ SW _ RET R MC2A TEMP SENSOR Refer to 1 Torch Module Schematic for Details 120VAC_1 (A9) MC2B D2, GREEN, 1TORCH GAS ON D7, GREEN, PILOT ENABLED D11, GREEN, PILOT CURRENT D12, GREEN, WORK CURRENT D22, GREEN, CONTACTORS ON D23, GREEN, RF ON D24, GREEN, FANS ON D25, GREEN, PLASMA ENABLED D26, GREEN, 1TORCH ON D27, GREEN, COOLANT ON 19X501100 (69) (65A) D M1 J16 (66) MC3BCHASSIS GND J13 to CB5 and to MC2 & MC3, also J14, J16 all 18 AWG To J100 of IM #3B To J100 of IM #3A (Sht 1, A,B6) 1 2 3 4 (64A) (64B) (65A) (65B) MC3A J2 RELAY & INTERFACE PCB +5VDC J31 - 30 CKT RIBBON To J100 of IM #2B To J100 of IM #2A (Sht 1, B,C6) C (95) WORK CURRENT SENSOR To J100 of IM #1B To J100 of IM #1A (Sht 1, C,D6) 120V_1 J13 J1 LEVEL SENSORS (94) 14 13 12 11 10 9 8 7 6 5 4 3 2 1 ANNEXE J12 J7 COOLANT FLOW SW r b g 1 (93) 5 4 3 2 1 (87) 8 7 6 5 4 3 2 1 R2 2 1 0.7 GPM 4.7 30W (92) TS1 3 2 1 (84) 1 2 COOLANT 6 5 4 3 2 1 J74 TS2 1 FS1 COOLANT MC1A 4 J71 AMBIENT (59) (58) (57) (56) (44A) (43) (90) 2 COMMON SIG (+) -15 VDC +15 VDC A 1 LS1 5 3 J12 = Mini-Fit Jr 400 VAC -- Single 18 AWG in pins 1 & 4 480 VAC -- Single 18 AWG in pins 1 & 8 230 VAC -- 18 AWG wires in pins 1,5,2,6 From Sys Bias J63 (Sht 1, F2) 4 TO HCT1 (Work) 3 4 2 2 1 19X501200 I / O PCB DIP SW --------------------------------------------SW6 OK TO MOVE (CONTACTS, VOLTS) SW11 ANALOG CC SOURCE SW12 DIVIDED ARC VOLTAGE (50:1, 16.7:1, 30:1, 40:1, 25:1) "0" = 10-12V "1" = 24V Measured relative to TP1 (24VDC_RET) F Art # A-11979_AE 1 98 2 3 ANNEXE 4 5 0560956430FR 100i / 200i / 300i / 400i 6 7 MC2 8 Fan Control SA1 SA2 (96) (161) (160) SA3 9 (70) 230 VAC _ SW (D2) (D2) W1 230 VAC to HE 400 (70) 230 VAC Ret (69) (69) W2 230 VAC _ SW _ RET 10 (162) / PILOT ENABLE / PILOT ENABLE RET (163) ARC_SUPPRESSOR ARC_SUPPRESSOR (97) (96) SA4 CHASSIS GND (98) (99) 120VAC 120 VAC_1 * INRUSH CONTROL 120 VAC_2 HMI/GCM J4 -- 40 CKT RIBBON CABLE (101) (102) (103) (104) (62) (106) AC 24V GCM2 AC 120V - GCM (108) (109) (110) (111) (63) (113) (61) AC 24V - RET - GCM2 (60) (63) 1 2 3 4 J18 GND GND J19 4 WIRE RxTx+ Rx+ Tx- (118) (119) (120) 2 1 2 3 4 5 6 Harness FERRITE CORE 3 TURNS 019X501800 J37 16 CKT RIBBON (121) (122) (123) (124) (125) (126) (127) (128) (129) (130) (131) GAS ON J23- 40 ckt ribbon cable ENABLE PLAS_ENABLE SW PLAS_ EN_SW_RET / GAS PRESS OK / BASIC ID TB1 CPU PCB TEST POINTS -------------------------------------------TP1 GND (PCB common) TP2 +5V_ISO (REF TP5) TP3 +24 VDC TP4 +3.3V TP5 GND_ISO TP6 +5.0 V TP7 TOTAL DEMAND (3.3V = 400A) TP9 /WR TP10 /RD TP11 CPU TEMP SENSE TP12 +3.3VA TP13 -15VDAC TP14 PC2 TP15 +15VDAC TP16 CLKO TP18 OSC_CLOCK CPU PCB DIP SW --------------------------------------------SW1 AUTO PILOT RESTART SW3 PREFLOW TIME SW4 POSTFLOW TIME SW5 FUNCTION SW8 SYSTEM CONTROL (pilot time, etc.) SW9 RESERVED (future) SW10 ADDRESS (default = 0) SW13 UNIT TYPE (AC / UC) SW14 LINE TERMINATION (serial comm.) OK2 (contact) 12 +10V (CC Pot Hi) 11 CC Pot Wiper 10 CC Pot Low 9 Div Arc V (+) 8 Div Arc V (-) 7 /Start - Stop (+) 6 /Start - Stop (-) 5 Stop Mom NC 4 OK2 (contact) 3 / CNC Enable (+) 2 / CNC Enable (-) 1 GND 1 2 3 4 5 6 7 8 9 10 11 12 13 14 15 16 17 18 TB2 OK to MOVE (+) 12 11 OK to MOVE (-) 10 PILOT is ON PILOT is ON Preflow ON (+) Preflow ON (-) Hold Start (+) Hold Start (-) 1 2 3 4 5 6 7 8 9 10 11 12 13 14 15 16 (130) (131) (112) (114) (121) (122) (124) (129) (128) (123) +10V GND GND TB3 12 11 10 9 * Plasma Ready (b) 8 7 6 Spare 5 Digital 4 Inputs 3 / Plasma Marking (-) 2 / Plasma Marking (+) 1 PSR * Plasma Ready (a) (133) (134) (137) (139) (138) (143) (140) (141) (136) (135) (132) (153) 01 Date Initial Design DAT 10/5/2012 DAT 9/16/2014 AA AB ECO 1 Torch Option DAT 10/17/2014 AC VCR-02672 MC1, K1 change DAT 8/3/2018 Revision Rev (104) (111) (166) J69 AC 120V - GCM AC 120V- Ret- GCM FERRITE CORE 3 TURNS (167) (106) (113) (144) (145) (146) (147) (148) (149) (150) (151) (152) (154) (155) (132) (152) (153) (154) (155) (156) (157) (158) (159) (156) (157) (158) (159) J22 By Art # A-11979_AE 0560956430FR 1 2 3 4 5 6 7 8 9 10 11 12 13 14 15 16 17 18 19 20 21 22 23 24 25 26 27 28 29 30 31 32 33 34 35 36 37 1- PLAS_ENABLE SW * 2- PLAS_ EN_SW_RET 3- GAS PRESS OK RET 4- / GAS PRESS OK 5- POT HIGH (GCM 1000) 6- POT WIPER (GCM 1000) 7- POT LOW (GCM 1000) 8- BASIC ID RET 9- / BASIC ID ** 1011Jumper & SOL in GCM 1000 XT 1415- 24 VAC - RET 1 2 3 4 5 6 7 8 9 10 11 12 13 14 15 16 17 18 19 20 21 22 23 24 25 26 27 28 29 30 31 32 33 34 35 36 37 C * Plasma Enable SW in GCM 2010. Jumpered in GCM 1000 XT and DMC 3000. ** Jumper in GCM 1000 XT 27- GAS SEL SW RET 28- GAS SEL SW D J15-1 to chassis used for SC-11 cable shield J15-13 connects SC-11 chassis to PS chassis. The COMM Ref at pin 8 is also for the SC-11 3- / CNC Start (+) 4- / CNC Start (-) 5- Divided Arc V (-) 6- Divided Arc V (+) 7- / Preflow ON (+) 8- COMM Ref (1K Ohm) 9- / Preflow ON (-) 10- / Spare Digital Input (+) 11- / Spare Digital Input (-) 12- OK to Move (-) 14- OK to Move (+) 15 - Key Plug 16- / Hold Start (+) 17- / Hold Start (-) E 21- / Plasma Mark (+) 22- / Plasma Mark (-) 23- / Spare Digital Input(+) 24- / Spare Digital Input (-) 25- / CNC Plasma Enable (+) 26- / CNC Plasma Enable (-) 29- Remote CC Pot High 30- Remote CC (analog) 31- Remote CC Pot Low 32- Stop SW (momentary) * 33- Stop SW Ret 34- Pilot is ON (a) 35- Pilot is ON (b) 36 - 37 Plasma Ready (a) Normally Open Contact * Used with Momentary CNC Start SW Date Victor Technologies Headquarters 16052 Swingley Ridge Road, Suite 300 St Louis, Missouri 63017 USA Date Printed 8/28/2018 Drawn Date Revised 8/24/2018 Date The information contained herein is proprietary to Victor Technologies. Not for release, reproduction or distribution without written consent. Size Sheet Title Drawing Number SCHEMATIC Ultra-Cut XT 400A 480V 6 J55 - GCM J15-CNC CHASSIS GND (133) (134) (135) (136) (137) (138) (139) (140) (141) (142) FERRITE CORE 3 TURNS (143) (144) (145) (146) (147) (148) (149) (150) (151) * CCM code 2.5 or later By AC 24V-GCM2 AC 24V Ret-GCM2 2 1 J21 1 2 3 4 5 6 7 8 9 10 11 12 13 14 15 16 17 18 19 20 Spare Digital Inputs Revision AC 24V Ret - GCM1 (125) (126) (127) (142) (112) (114) (103) (110) AC 24V-GCM1 J26 OK 9 8 7 6 5 4 3 2 1 Comm 12 - Tx13 - Rx+ 14 - Rx- Display PCB J20 30 CKT PIN HEADER 7 B J17 J29 30 CKT RECEPTACLE - BOTTOM ENTRY CPU PCB LEDs ---------------------------D2 RXD (red) D3 TXD (red) D4 CAN BUS (slave) D7 CAN BUS (MAIN) D11 5 VDC POWER D17 STATUS CODE D18 INITIALIZING / PROGRAMMING (red) 5-HMI Plasma Enable SW 6-HMI Plasma Enable SW 7 - Key Plug 8 - Tx+ 9 - GND RS 485 10 - GND / 422 3 (61) INRUSH CONTROL (116) (117) (120) (115) (119) (118) J30 2 WIRE NORMAL PROGRAM PROG USB IC 1 2 3 4 1 2 3 4 5 6 7 8 9 1 2 3 4 5 6 (116) (117) Harness K1 (OLD) (63) 5 J47 1 2 3 4 5 6 7 8 9 10 11 12 (115) 1 - 24 VAC 2 - 24 VAC Ret 3- Jumper to 24 VAC 4 J39 USB PORT 1 2 3 4 5 6 7 8 9 10 11 12 (108) AC 24V- Ret -TB4-1 (62) 1 AC 120V- Ret- TB4-3 2 3 4 5 6 7 8 9 10 11 12 13 14 (109) AC 120V- TB4-4 J10 RS 232 D-SUB SERIAL PROG PORT (101) (102) AC 24V-TB4-2 AC 24V Ret- GCM1 AC 120V- Ret- GCM USB Cable to Front Panel J38 J54 - Remote HMI & CNC COMM (100) 1 AC 24V GCM1 (62) A 3 - Key Plug ANNEXE 24 VAC (107) 120VAC (100) 18 17 16 15 14 13 12 11 10 9 8 7 6 5 4 3 2 1 * 120 VAC_RET (98) MC1 (OLD) (60) CONTROL OUTPUTS 24 VDC 1 2 3 4 5 6 7 8 9 10 11 12 13 14 (99) 120 VAC Ret (107) 16 15 14 13 12 11 10 9 8 7 6 5 4 3 2 1 2 1 4 3 120 VAC to RAS MC1 (NEW*) (91) J8 J59 - RAS (97) ARC_SUPPRESSOR GND Rev 1 2 3 4 5 6 7 ARC_SUPPRESSOR MC3 PILOT PCB J29 J70 - HE Pump Motor Control 5 6 8 7 9 J3 10 PILOT A SIG Vin+ PILOT A SIG Vin- 10 CKT RIBBON TO PILOT PCB 8 ANNEXE 9 DAT C F 10/5/2012 2 of 2 042X1346 10 99 D C B A 1 PLASMA READY K8 K5 PILOT IS ON GND CNC PLASMA ENABLE/ PLASMA MARK/ HOLD START/ GND DIVIDED ARC V (+) GND PREFLOW ON/ CNC START/ OK TO MOVE GND K4 GND TX+ TXRX+ RXGND GND J22 1 2 3 4 5 6 7 8 9 10 11 12 13 14 15 16 17 18 19 20 J21 1 2 3 4 5 6 7 8 9 10 11 12 13 14 15 16 17 18 J30 6 5 4 3 2 1 BROWN WHITE BLUE BLUE BLACK BLUE YELLOW BLUE ORANGE GREEN BLUE BROWN GREEN WHITE BROWN BLACK ORANGE RED SHIELD GREEN/YELLOW GND 2 SCU Module Connector Locations SHIELD BLACK WHITE BLACK GREEN BLACK RED X74 RED GREEN X60 1 2 3 4 5 6 BROWN WHITE 2 AA Rev WHITE BROWN X62 1 2 3 4 5 6 Revision 3 X63 By DAT SCU MODULE 3 ECR-03142 ORANGE GREEN CCM I/O PCB X67 X63 X61 X65 X66 X64 X62 X60 BLUE BLUE 1 2 3 4 5 6 BLACK ORANGE 8/28/2018 Date Rev X64 4 4 Revision 1 2 3 4 5 6 YELLOW BLUE X71 1 2 BLUE RED X79 1 2 By BLUE RED 1 1 2 3 4 5 X81 X79 X77 X73 X71 X75 X80 X78 X76 X74 X72 ANNEXE X70 Date BLUE X76 X70 5 1 2 X72 SCHEMATIC BLUE BROWN BLACK BLUE BLUE RED WHITE BROWN GREEN BLUE RED WHITE BROWN GREEN Art # A-13972 5 Internal SCU Interface for iSeries 1 of 6 1 08/16/2018 042X1374 Sheet Date Revised 8/28/2018 Date 5th Floor Annapolis Junction, MD 20701 420 National Buisness Parkway 1 2 3 ARC V 1 2 3 4 E STOP 1 2 3 4 5 6 7 8 CAN OUT 1 2 3 4 5 6 7 8 CAN IN CCM REAR PANEL 6 Date Printed 8/28/2018 Drawn DAT The information contained in this drawing is the sole property of ESAB WELDING CUTTING. Any reproduction in part or as a whole without the written permission Size B of ESAB WELDING & CUTTING is prohibited. Drawing Number Title BLUE RED 1 2 3 WHITE BROWN GREEN 100 1 2 3 4 5 6 7 8 ANNEXE D C B A 100i / 200i / 300i / 400i ANNEXE 10: INTERFACE SCU POUR ISERIES 0560956430FR