Fisher Contrôleur numérique de vanne DVC6200 FIELDVUE (DVC6200 HW2 Digital Valve Controller) Manuel utilisateur
PDF
Télécharger
Document
Manuel d’instructions Contrôleur numérique de vanne DVC6200 D103605X0FR avril 2021 Contrôleur numérique de vanne DVC6200 FIELDVUE™ Fisher™ Ce manuel couvre les modèles et points suivants : Niveau d’instrument Type d’appareil Révision du matériel Révision du micrologiciel Révision de l’appareil Révision DD HC, AD, PD, ODV 1309 2 7 1 3 7 1 Table des matières Section 1 Introduction . . . . . . . . . . . . . . . . . . . . . 3 Installation, connexions pneumatiques et électriques et configuration initiale . . . . . . . . . . . . . . . . . . . . . . . . . . . Objet du manuel . . . . . . . . . . . . . . . . . . . . . . . . . . . . . . . . . . . Conventions utilisées dans ce manuel . . . . . . . . . . . . . . . . . Description . . . . . . . . . . . . . . . . . . . . . . . . . . . . . . . . . . . . . . . Spécifications . . . . . . . . . . . . . . . . . . . . . . . . . . . . . . . . . . . . . Documents connexes . . . . . . . . . . . . . . . . . . . . . . . . . . . . . . . Services de formation . . . . . . . . . . . . . . . . . . . . . . . . . . . . . . . 3 3 3 3 5 5 8 W9713 Section 2 Pratiques de câblage . . . . . . . . . . . . . . 9 Exigences du système de commande . . . . . . . . . . . . . . . . . . 9 Filtre HART . . . . . . . . . . . . . . . . . . . . . . . . . . . . . . . . . . . . . . 9 Tension disponible . . . . . . . . . . . . . . . . . . . . . . . . . . . . . . . . 9 Tension de conformité . . . . . . . . . . . . . . . . . . . . . . . . . . . 11 Recommandations pour la longueur du câblage des bornes auxiliaires . . . . . . . . . . . . . . . . . . . . . . . . . . . . . 12 Capacité (électrique) maximale du câble . . . . . . . . . . . . . 12 Installation avec un Rosemountt 333 HART Tri‐Loopt HART‐vers‐convertisseur de signal analogiques . . . . . . . . . . . . . . . . . . . . . . . . . 13 Section 3 Configuration . . . . . . . . . . . . . . . . . . . 15 Configuration assistée . . . . . . . . . . . . . . . . . . . . . . . . . . . . . Configuration manuelle . . . . . . . . . . . . . . . . . . . . . . . . . . . . Mode et protection . . . . . . . . . . . . . . . . . . . . . . . . . . . . . . Mode de l’instrument . . . . . . . . . . . . . . . . . . . . . . . . Verrouillage en écriture . . . . . . . . . . . . . . . . . . . . . . . Instrument . . . . . . . . . . . . . . . . . . . . . . . . . . . . . . . . . . . . . Identification . . . . . . . . . . . . . . . . . . . . . . . . . . . . . . . Numéros de série . . . . . . . . . . . . . . . . . . . . . . . . . . . . Unités . . . . . . . . . . . . . . . . . . . . . . . . . . . . . . . . . . . . . Boîtier à bornes . . . . . . . . . . . . . . . . . . . . . . . . . . . . . Plage d’entrée . . . . . . . . . . . . . . . . . . . . . . . . . . . . . . Fiche technique . . . . . . . . . . . . . . . . . . . . . . . . . . . . . Paramétrer l’heure de l’instrument . . . . . . . . . . . . . www.Fisher.com 15 15 16 16 16 16 16 17 17 17 17 18 18 Régulation de la course/pression . . . . . . . . . . . . . . . . . . . Sélection pression/course . . . . . . . . . . . . . . . . . . . . . Coupures et limites . . . . . . . . . . . . . . . . . . . . . . . . . . Régulation de la pression . . . . . . . . . . . . . . . . . . . . . Pression de secours . . . . . . . . . . . . . . . . . . . . . . . . . . Mode contrôle . . . . . . . . . . . . . . . . . . . . . . . . . . . . . . Caractérisation . . . . . . . . . . . . . . . . . . . . . . . . . . . . . . Réponse dynamique . . . . . . . . . . . . . . . . . . . . . . . . . Réglage . . . . . . . . . . . . . . . . . . . . . . . . . . . . . . . . . . . . . . . . Réglage de course . . . . . . . . . . . . . . . . . . . . . . . . . . . Réglage de la pression . . . . . . . . . . . . . . . . . . . . . . . . Réglages intégrés de course/pression . . . . . . . . . . . Vanne et actionneur . . . . . . . . . . . . . . . . . . . . . . . . . . . . . Test de course partielle . . . . . . . . . . . . . . . . . . . . . . . . . . . Sorties . . . . . . . . . . . . . . . . . . . . . . . . . . . . . . . . . . . . . . . . . Configuration de la borne de sortie . . . . . . . . . . . . . Configuration des commutateurs . . . . . . . . . . . . . . Affectations de variable HART . . . . . . . . . . . . . . . . . Sortie du transmetteur . . . . . . . . . . . . . . . . . . . . . . . Configuration des alertes . . . . . . . . . . . . . . . . . . . . . . . . . . . Passer à HART 5 / Passer à HART 7 . . . . . . . . . . . . . . . . . . . . 18 18 19 19 20 20 21 23 24 24 27 27 28 30 36 36 36 37 37 38 38 Manuel d’instructions Contrôleur numérique de vanne DVC6200 avril 2021 D103605X0FR Sommaire (suite) Section 4 Étalonnage . . . . . . . . . . . . . . . . . . . . . 39 Présentation de l’étalonnage . . . . . . . . . . . . . . . . . . . . . . . . Étalonnage de la course . . . . . . . . . . . . . . . . . . . . . . . . . . . Étalonnage automatique . . . . . . . . . . . . . . . . . . . . . . Étalonnage manuel . . . . . . . . . . . . . . . . . . . . . . . . . . Étalonnage du bouton-poussoir . . . . . . . . . . . . . . . . Étalonnage du capteur . . . . . . . . . . . . . . . . . . . . . . . . . . . Capteurs de pression . . . . . . . . . . . . . . . . . . . . . . . . . Étalonnage de l’entrée analogique . . . . . . . . . . . . . . Réglage du relais . . . . . . . . . . . . . . . . . . . . . . . . . . . . . . . . Relais à double action . . . . . . . . . . . . . . . . . . . . . . . . Relais à simple action . . . . . . . . . . . . . . . . . . . . . . . . . Étalonnage PST . . . . . . . . . . . . . . . . . . . . . . . . . . . . . . . . . . Section 5 Informations de l’appareil, alertes, 39 40 40 41 42 43 43 44 45 45 46 47 et diagnostics . . . . . . . . . . . . . . . . . . . . . . . . . . . 48 Aperçu . . . . . . . . . . . . . . . . . . . . . . . . . . . . . . . . . . . . . . . . . . Variables à fonction principale et variables d’état . . . . . Informations de l’appareil . . . . . . . . . . . . . . . . . . . . . . . . . Outils de maintenance . . . . . . . . . . . . . . . . . . . . . . . . . . . . . État de l’appareil . . . . . . . . . . . . . . . . . . . . . . . . . . . . . . . . Registre des alertes . . . . . . . . . . . . . . . . . . . . . . . . . . . . . . Rapport d’alertes . . . . . . . . . . . . . . . . . . . . . . . . . . . . . . . . Principe de fonctionnement de la bande morte . . . . . . . Diagnostics . . . . . . . . . . . . . . . . . . . . . . . . . . . . . . . . . . . . . Vanne de course . . . . . . . . . . . . . . . . . . . . . . . . . . . . . Test de course partielle (niveau ODV seulement) . . Variables . . . . . . . . . . . . . . . . . . . . . . . . . . . . . . . . . . . . . . . . 48 48 48 49 49 49 49 52 54 54 54 56 Section 6 Maintenance et dépannage . . . . . . . 57 Remplacement du système de contre-réaction magnétique . . . . . . . . . . . . . . . . . . . . . . . . . . . . . . . . . . . . Maintenance de la base du module . . . . . . . . . . . . . . . . . . . Outils requis . . . . . . . . . . . . . . . . . . . . . . . . . . . . . . . . . . . . Remplacement de composant . . . . . . . . . . . . . . . . . . . . . Retrait de la base du module . . . . . . . . . . . . . . . . . . . . . . . Remplacement de la base du module . . . . . . . . . . . . . . . 2 58 58 58 59 59 60 Maintenance du sous-module . . . . . . . . . . . . . . . . . . . . . . . Convertisseur I/P . . . . . . . . . . . . . . . . . . . . . . . . . . . . . . . . Circuit imprimé . . . . . . . . . . . . . . . . . . . . . . . . . . . . . . . . . Relais pneumatique . . . . . . . . . . . . . . . . . . . . . . . . . . . . . . Jauges, bouchons de tuyauterie ou valves pneumatiques . . . . . . . . . . . . . . . . . . . . . . . . . . . . . . . . Boîtier à bornes . . . . . . . . . . . . . . . . . . . . . . . . . . . . . . . . . . . Retrait du boîtier à bornes . . . . . . . . . . . . . . . . . . . . . . . . . Remplacement du boîtier à bornes . . . . . . . . . . . . . . . . . Dépannage . . . . . . . . . . . . . . . . . . . . . . . . . . . . . . . . . . . . . . Vérification de la tension disponible . . . . . . . . . . . . . . . . . . Redémarrer du processeur . . . . . . . . . . . . . . . . . . . . . . . . . Liste de vérification du support technique DVC6200 . . . . 61 61 63 65 65 66 66 67 67 67 68 70 Section 7 Pièces . . . . . . . . . . . . . . . . . . . . . . . . . 71 Commande de pièces de rechange . . . . . . . . . . . . . . . . . . . Kits de pièces de rechange . . . . . . . . . . . . . . . . . . . . . . . . . . Circuit imprimé . . . . . . . . . . . . . . . . . . . . . . . . . . . . . . . . . Liste des pièces détachées . . . . . . . . . . . . . . . . . . . . . . . . . . Boîtier . . . . . . . . . . . . . . . . . . . . . . . . . . . . . . . . . . . . . . . . . Pièces communes . . . . . . . . . . . . . . . . . . . . . . . . . . . . . . . Base du module . . . . . . . . . . . . . . . . . . . . . . . . . . . . . . . . . Convertisseur I/P . . . . . . . . . . . . . . . . . . . . . . . . . . . . . . . . Relais . . . . . . . . . . . . . . . . . . . . . . . . . . . . . . . . . . . . . . . . . . Boîtier à bornes . . . . . . . . . . . . . . . . . . . . . . . . . . . . . . . . . Boîtier à bornes de raccordement de contre-réaction . . Manomètres, bouchons de tuyauterie ou assemblages de valves pneumatiques . . . . . . . . . . . . . . . . . . . . . . . . Unité de contre-réaction DVC6215 . . . . . . . . . . . . . . . . . Filtres HART . . . . . . . . . . . . . . . . . . . . . . . . . . . . . . . . . . . . 71 71 71 73 73 73 73 73 73 74 74 74 74 74 Annexe A Principe de fonctionnement . . . . . . . 81 Communication HART . . . . . . . . . . . . . . . . . . . . . . . . . . . . . 81 Contrôleur numérique de vanne DVC6200 . . . . . . . . . . . . 81 Annexe B Arborescences du menu de l’interface de communication . . . . . . . . . . . . 85 Glossaire . . . . . . . . . . . . . . . . . . . . . . . . . . . . . . . 95 Index . . . . . . . . . . . . . . . . . . . . . . . . . . . . . . . . . 101 Manuel d’instructions Présentation D103605X0FR avril 2021 Section 1 Introduction Installation, Raccordements pneumatiques et électriques Raccordements, configuration initiale Voir le Guide de démarrage rapide de la série DVC6200 (D103556X012) pour les informations relatives à l’installation, au raccordement et à la configuration initiale des produits DVC6200. Pour obtenir un exemplaire de ces documents, cliquer sur le code approprié ci-dessous ou le numériser, ou contacter un bureau commercial Emerson, ou consulter notre site Web à l'adresse suivante : Fisher.com. Cliquer sur le code ou le numériser pour accéder à l'assistance sur site Objet du manuel Ce manuel d’instructions est un supplément au Guide de démarrage rapide de la série DVC6200 (D103556X012) livré avec chaque instrument. Ce manuel d’instructions contient des caractéristiques produits, des matériaux de référence, des informations de configuration personnalisées et des informations détaillées concernant les pièces de rechange. Ce manuel d’instructions décrit l’utilisation d’un appareil Emerson L’interface de communication pour installer et étalonner l’instrument. On peut également utiliser le logiciel Fisher ValveLink™ ou l’application mobile ValveLink pour la configuration, l’étalonnage et le diagnostic de la vanne et de l’instrument. Pour plus d’informations sur l’utilisation du logiciel ValveLink avec l’instrument, se reporter à l’aide ou à la documentation du logiciel ValveLink. Les personnes effectuant les procédures d'installation, d'exploitation ou de maintenance du contrôleur numérique de vanne DVC6200 doivent être parfaitement formées et qualifiées aux procédures d'installation, d'exploitation et de maintenance de vannes, d'actionneurs et d'accessoires. Pour éviter des blessures ou des dommages matériels, il est important de lire attentivement, d'assimiler et d'observer l'intégralité de ce manuel, y compris les avertissements et les précautions. Pour toute question au sujet de ces instructions, contacter votre bureau commercial Emerson avant toute intervention. Conventions utilisées dans ce manuel Les chemins de navigation et les séquences d’accès rapide-sont inclus dans les procédures et les paramètres accessibles à l’aide de l’interface de communication. Par exemple, pour accéder à « Configuration de l’appareil » : Interface de communication Configurer > Configuration assistée > Configuration de l’appareil (2‐1‐1) Voir l’annexe B pour en savoir plus sur les arborescences du menu de l'interface de communication. Remarque Les séquences d’accès rapide ne s’appliquent qu’à l’interface de communication 475. Elles ne s’appliquent pas à l’interface de communication Trex™. Description Les contrôleurs numériques de vanne DVC6200 (figures 1‐1 et 1‐2) sont des instruments de communication intensité/air pilotés par microprocesseur. Outre la fonction traditionnelle consistant à convertir un courant d’entrée en une pression de sortie pneumatique, le contrôleur numérique de vanne de la série DVC6200, au moyen du protocole de communication HARTr, offre un accès commode aux informations essentielles relatives aux opérations. On peut obtenir des informations du composant principal du procédé, de la vanne de régulation, de l’interface de communication de l’appareil au niveau de la vanne ou de la boîte de jonction d’un site, ou en utilisant un ordinateur personnel ou console de l’opérateur au sein de la salle de commande. De plus, une 3 Manuel d’instructions Présentation avril 2021 D103605X0FR Figure 1‐1. Contrôleur numérique de vanne DVC6200 FILEDVUE monté sur un actionneur de vanne droite Fisher Figure 1‐2. Contrôleur numérique de vanne DCV6200 FIELDVIEW à montage intégré sur une vanne de régulation Fisher GX X1182-1 W9616 option qui prévoit un circuit isolé pour un transmetteur de position de vanne est disponible (pour une indication distincte sur la position de chaque valve) ou un commutateur intégré qui peut être réglé en tant que contacteur de fin de course ou en tant que commutateur d’alerte. À l’aide d’un ordinateur personnel et le logiciel ValveLink ou d’AMS Suite : Intelligent Device Manager, ou d’une interface de communication, on peut effectuer plusieurs opérations avec le contrôleur numérique de vanne DVC6200. On peut obtenir des informations générales sur le niveau de révision du logiciel, les messages, le repère, le descripteur et la date. Des informations de diagnostic sont disponibles pour vous aider lors du dépannage. Les paramètres de configuration de l’entrée et de la sortie peuvent être réglés et le contrôleur numérique de vanne peut être étalonné. Voir le Tableau 1‐1 pour des informations détaillées sur les fonctions de chaque niveau de diagnostic. Grâce au protocole HART, les informations provenant du site peuvent être intégrées dans les systèmes de régulation ou être reçues sur une seule boucle. Le contrôleur numérique de vanne DVC6200 est conçu pour remplacer directement des positionneurs pneumatiques et électropneumatiques montés sur des vannes. Tableau 1‐1. Capacités par niveau d'instrumentation CAPACITÉ NIVEAU DE DIAGNOSTIC(2) HC AD PD ODV Étalonnage automatique X X X X Personnaliser la caractérisation X X X X Communication en mode Rafale X X X X Alertes X X X X Réponse à un changement par palier, test de signal d’entraînement et intervalle d’erreur dynamique X X X Diagnostics avancés (signature de vanne) X X X Optimiseur de performances(3) X X X Contrôle de course - pression de secours X X X X X X Diagnostic de performances X X Test d’électrovanne X X Capteur de pression d’alimentation Filtre du point d’entrée du fil/délai(1) X(4) X 1. Voir la brochure n° D351146X012 pour plus d’informations sur les vannes numériques optimisées Fisher pour des applications d’anti-saturation des compresseurs. 2. HC = communication HART ; AD = diagnostics avancés ; PD = diagnostics de performance ; ODV = vanne numérique optimisée. 3. L’optimiseur de performances n’est disponible qu’avec le logiciel ValveLink. 4. Capteur de pression d’alimentation disponible à partir du micrologiciel 7. 4 Manuel d’instructions Présentation D103605X0FR avril 2021 Spécifications AVERTISSEMENT Voir le tableau 1‐2 pour les spécifications. Toute configuration incorrecte d'un instrument de positionnement peut entraîner un dysfonctionnement du produit, des dommages matériels ou des blessures. Les caractéristiques des contrôleurs numériques de vanne DVC6200 sont indiquées dans le tableau 1‐2. Les caractéristiques de l’interface de communication se trouvent dans le Guide de démarrage rapide de l’interface de communication. Documents connexes Cette section dresse la liste d'autres documents contenant des informations relatives au contrôleur numérique de vanne DVC6200. Ces documents sont les suivants : D Bulletin 62.1 : DVC6200 – contrôleur numérique de vanne FIELDVUE DVC6200 Fisher (D103415X012) D Bulletin 62.1 : DVC6200(S1) – dimensions du contrôleur numérique de vanne FIELDVUE DVC6200 Fisher (D103543X012) D Bulletin 62.1 : contrôleur numérique de vanne – sélection du contrôleur numérique de vanne FIELDVUE Fisher (D104363X012) D Guide de démarrage rapide du contrôleur numérique de vanne de la série DVC6200 FIELDVUE Fisher (D103556X012) D Le contrôleur numérique de vanne FIELDVUE pour fractionnement (D103262X012) D Utilisation d’instruments FIELDVUE avec le Smart HART Loop Interface and Monitor (HIM) (D103263X012) D Utilisation des instruments FIELDVUE avec l’adaptateur adaptateur THUM Smart Wireless et un module d’interface HART (HIM) (D103469X012) D Moniteur audio pour les communications HART (D103265X012) D Caractéristiques du dispositif de terrain HART - En supplément du contrôleur numérique de vanne FIELDVUE DVC6200 Fisher (D103639X012) D Utilisation du HART Tri‐Loop convertisseur de HART en signal analogique avec le contrôleur numérique de vanne FIELDVUE (D103267X012) D Mise en œuvre du verrou-dans la-dernière stratégie (D103261X012) D Manuel d’instructions du filtre HF340 de Fisher (D102796X012) D Interface de communication de l’appareil AMS Trex Guide d’utilisation D Assistance ou documentation pour le logiciel ValveLink Tous ces documents sont disponibles dans un bureau commercial Emerson ou sur Fisher.com. 5 Manuel d’instructions Présentation avril 2021 D103605X0FR Tableau 1‐2. Spécifications Selon la norme ISO 8573-1 Masse volumique maximale des particules : Classe 7 Teneur en lubrifiant : Classe 3 Point de rosée sous pression : Classe 3 ou au moins 10 _C en dessous de la température ambiante la plus basse attendue Montage disponible Contrôleur numérique de vanne DVC6200 ou unité de contre-réaction DVC6215 : J Support intégré aux actionneurs GX ou 657/667 Fisher J Montage intégré aux actionneurs rotatifs Fisher J Applications linéaires à tige coulissante J Applications rotatives quart-de-tour Signal de sortie Unité de base DVC6205 pour montage sur paroi ou tube de 2 pouces (pour montage déporté) Signal pneumatique, jusqu’à la pression d’alimentation totale Étendue d’échelle minimale : 0,4 bar (6 psig) Étendue d’échelle maximale : 9,5 bar (140 psig) direct àà J à double action, J à simple action ou J à action inverse Le contrôleur numérique de vanne DVC6200 ou l’unité de contre-réaction DVC6215 peuvent aussi être montés sur d'autres actionneurs conformes aux normes de montage IEC 60534‐6-1, IEC 60534-6-2, VDI/VDE 3845 et NAMUR. Consommation d’air à régime stable(2)(3) Protocole de communication J HART 5 ou J HART 7 Signal d’entrée Point-àà-Point Signal d’entrée analogique : CC 4-20 mA, nominal ; séparation du parcours de course disponible Tension minimale disponible aux bornes de l’instrument doivent être de 9,5 V c.c. pour le contrôle analogique, 10 V c.c. pour la communication HART Courant de contrôle minimum : 4,0 mA Courant minimum w/o redémarrage du microprocesseur : 3,5mA Tension maximale : 30 V c.c. Protégé contre la surintensitéé Protégé contre la polarité inverse Alimentation multi-point De l’instrument : 11 à 30 V c.c. à 10 mA Protégé contre la polarité inverse Relais standard À une pression d’alimentation de 1,4 bar (20 psig) : Valeur inférieure à la normale 0,38 m3/h (14 scfh) À une pression d’alimentation de 5,5 bar (80 psig) : Valeur inférieure à la normale 1,3 m3/h (49 scfh) Relais à purge faible À une pression d’alimentation de 1,4 bar (20 psig) : Valeur moyenne normale de 0,056 m3/h (2,1 scfh) À une pression d’alimentation de 5,5 bar (80 psig) : Valeur moyenne normaler de 0,184 m3/h (6,9 scfh) Capacité de sortie maximale(2)(3) À une pression d’alimentation de 1,4 bar (20 psig) : Valeur inférieure à la normale 10,0 m3/h (375 scfh) À une pression d’alimentation de 5,5 bar (80 psig) : Valeur inférieure à la normale 29,5 m3/h (1100 scfh) Limites de température ambiante de fonctionnement(1)(4) Pression d’alimentation(1) -40 à 85 _C (-40 à 185 _F) -52 à 85 _C (-62 à 185 _F) pour les instruments utilisant l'option « Température extrême » (pour les élastomères de fluorosilicone) -52 à 125 _C (-62 à 257 _F) pour l’unité de contre-réaction à montage déporté Minimum recommandé : 0,3 bar (5 psig) au-delà des recommandations maximales des actionneurs Maximum : 10,0 bar (145 psig) ou selon la classe de pression maximale de l’actionneur, choisir la pression la plus basse des deux Produit : air ou gaz naturel Linéarité indépendante(5) Le produit d'alimentation doit être propre, sec et non corrosif Valeur standard : ±0,50 % de l’étendue d’échelle de sortie Selon la norme ISA 7.0.01 des particules de 40 micromètres au maximum dans le circuit pneumatique sont acceptables. Il est recommandé de procéder à une filtration supplémentaire pour réduire la taille des particules à 5 micromètres. La teneur en lubrifiant ne doit pas dépasser 1 ppm en poids (p/p) ou en volume (vol/vol). La condensation dans l'alimentation d'air doit être minimale. Compatibilité électromagnétique Conforme à la norme EN 61326-1:2013 Immunité – Installations industrielles selon le tableau 2 de la norme EN 61326‐1. Les performances sont indiquées dans le tableau 1‐3 ci-dessous. Émissions – Classe A Classe d'équipement ISM : Groupe 1, Classe A -suite- 6 Manuel d’instructions Présentation D103605X0FR avril 2021 Tableau 1‐2. Spécifications (suite) Protection contre la foudre et les surtensions – Le degré d'immunité contre la foudre est spécifié comme immunité contre les surtensions dans le tableau 1‐3. Pour une protection supplémentaire contre les surtensions, il est possible d'utiliser des dispositifs de protection contre les transitoires disponibles dans le commerce. ESMA— Autorités de normalisation et de métrologie des Émirats arabes unis – ECAS-Ex (EAU) INMETRO— National Institute of Metrology, Quality, and Technology (Institut national de la métrologie, de la qualité et de la technologie) (Brésil) KOSHA— Agence coréenne pour la sécurité et la santé au travail (Corée du Sud) KTL— Korea Testing Laboratory (Laboratoire d’essai en Corée) (Corée du Sud) NEPSI : Centre national de contrôle et d'inspection pour la protection contre les explosions et la sécurité de l'emploi des instruments (Chine) PESO CCOE— Petroleum and Explosives Safety Organisation - Chief Controller of Explosives (Inde) (Organismation pour la sécurité en matière d'hydrocarbures et d'explosifs Contrôleur en chef des explosifs) (Inde) SANS— Normes nationales de l’Afrique du Sud Contacter un bureau commercial Emerson pour obtenir des informations spécifiques sur les classifications/certifications Méthode de test de la résistance aux vibrations Testé conformément à la norme ANSI/ISA-S75.13.01, Section 5.3.5. Une recherche de fréquence de résonance est effectuée sur les trois axes. L'instrument est soumis au test d'endurance d'une demi-heure spécifié par ISA pour chaque résonance majeure. Impédance d'entrée Une impédance équivalente de 500 ohm peut être utilisée. Cette valeur correspond à 10 V et 20 mA. Méthode de test de la résistance à l’humidité Raccordements Testé conformément à la norme IEC 61514‐2 Pression d’alimentation : 1/4 NPT en interne avec pad intégré pour le montage du détendeur 67CFR Pression de sortie : 1/4 NPT en interne Tuyauterie recommandée : 3/8 pouces Évent : 3/8 NPT en interne Électricité : 1/2 NPT en interne ou M20 Classification électrique Certificats de zone dangereuse CSA— Sécurité intrinsèque, antidéflagrant, division 2, protection contre les coups de poussière FM— Sécurité intrinsèque, antidéflagrant, protection contre les coups de poussière, non incendiaire ATEX— Sécurité intrinsèque, antidéflagrant, type « n », poussières par sécurité intrinsèque IECEx— Sécurité intrinsèque, antidéflagrant, type « n », poussière par sécurité intrinsèque et boîtier Compatibilité de l’actionneur Tige glissante linéaire Actionneurs linéaires avec course nominale comprise entre 6,35 mm (0,25 po) et 606 mm (23,375 po) Rotation d’un quart de tour Actionneurs rotatifs avec course nominale comprise entre 45 et 180°(6) Boîtier électrique : CSA— Type 4X, IP66 FM— Type 4X, IP66 ATEX— IP66 IECEx— IP66 Poids DVC6200 Aluminium : 3,5 kg (7,7 lb) Acier inoxydable : 8,6 kg (19 lb) DVC6205 : 4,1 kg (9 lb) DVC6215 : 1,4 kg (3,1 lb) Autres homologations/certifications Appareil à joint simple certifié gaz naturel— CSA, FM, ATEX et IECEx Matériaux de construction Lloyds Register— Homologation type marin Boîtier, base du module et boîtier à bornes : Alliage d’aluminium à faible teneur en cuivre A03600 (standard) Acier inoxydable (en option) Couvercle : Polyester thermoplastique Élastomère : Nitrile (standard) Fluorosilicone (très haute température) CCC— Certification de produit obligatoireen Chine CML— Certification Management Limited (Japon) CUTR— Customs Union Technical Regulations (Réglementation technique de l'Union douanière) (Russie, Kazakhstan, Bélarus) -suite- 7 Manuel d’instructions Présentation avril 2021 D103605X0FR Tableau 1‐2. Spécifications (suite) Options J Manomètres de sortie et d’alimentation ou J Valves pneumatiques J Filtre détendeur à montage intégré J Relais de purge faible débit(7) J Température extrême J Montage déporté(8) J Acier inoxydable J Position 4‐20 mA intégrée Transmetteur(9) : sortie 4‐20 mA, isolée Tension d’alimentation : 8‐30 V c.c. Précision de référence : 1 % d’étendue de course Le transmetteur de position est conforme aux exigences NAMUR NE43 ; sélectionnable pour montrer les défaillances élevées ( > 22,5 mA) ou les défaillances faibles (< 3,6 mA). Défaillance élevée lorsque le contrôleur est mis en marche. J Essentielle Changement(9): Un contacteur isolé, configurable tout au long de la plage de course étalonnée ou actionné à partir d’une alerte d’appareil État OFF : 0 mA (nominal) État activé : jusqu’à 1 A Tension d’alimentation : 30 Vcc maximum Incertitude nominale : 2 % de l’étendue de course Contacter votre bureau de vente Fisher ou se rendre sur Fisher.com pour plus d’informations Déclaration de SEP Fisher Controls International LLC déclare que ce produit est conforme à l’article 4, paragraphe 3, de la Directive équipement sous pression (DESP) 2014/68/UE. Il a été conçu et fabriqué conformément aux Règles de l’Art en Usage (RAU) et ne peut pas porter le marquage CE relatif à la DESP. Cependant, le produit peut porter la marque CE indiquant la conformité à d'autres directives européennes applicables. REMARQUE : la terminologie des instruments spécialisés est définie par la norme ANSI/ISA 51.1 - terminologie des instruments de procédé. 1. Les limites de pression et de température contenues dans ce document et celles de toute norme ou de tout code applicable ne doivent pas être dépassées. 2. m3/h normaux – mètres cubes normaux par heure à 0 _C et 1,01325 bar, valeur absolue. Scfh : pieds cubes standard par heure à 60 _F et 14,7 psia. 3. Valeurs de 1,4 bar (20 psig) basées sur un relais direct à -action simple ; valeurs de 5,5 bar (80 psig) basées sur un relais àà-double action. 4. Les limites de température varient selon l’homologation pour utilisation en zone dangereuse. Limite inférieure de température pour l’approbation CUTR Ex avec les elastomères au fluorosilicone est de -53 _C (-63,4 _F). 5. Ne s’aplique pas aux courses de moins de 19 mm (0,75 pouce) sans objet ou aux rotations d'arbre inférieures à 60 degrés. Ne s’applique pas aux contrôleurs numériques de vanne pour les longues courses. 6. Les actionneurs rotatifs avec une course nominale de 180° nécessitent un kit de montage spécial ; contacter un bureau commercial Emerson pour connaître la disponibilité des kits 7. L'exigence de consommation en régime stable du Quad O de 6 scfh peut être satisfaite par un DVC6200 avec l'option de relai A à faible purge, lorsqu'il est utilisé avec une alimentation en gaz naturel jusqu'à 4,8 bars (70 psi) à 16 _C (60 _F). L’exigence de 6 scfh peut être satisfaite par les relais de purge basse B et C lorsqu'ils sont utilisés avec une alimentation en gaz naturel allant jusqu'à 5,2 bars (75 psi) à 16 _C (60 _F). 8. Un câble gainé à 4 conducteurs, de calibre 18 à 22 AWG minimum, dans un conduit métallique rigide ou flexible, est nécessaire pour le raccordement entre l'unité de base et l'unité de contre-réaction. Un tubage pneumatique entre le raccordement de sortie de l'unité de base et l'actionneur a été testé jusqu'à 91 mètres (300 pieds). Aucune dégradation des performances n’a eu lieu jusqu’à 15 mètres (50 pieds). À 91 mètres, il y avait un léger décalage pneumatique. 9. La sortie électronique est disponible avec le transmetteur de position ou le commutateur intégré. Tableau 1‐3. Synthèse des résultats CEM – Immunité Port Boîtier Phénomène Décharge électrostatique (DES) IEC 61000‐4‐2 Champ électromagnétique rayonné IEC 61000‐4‐3 Champ magnétique de fréquence industrielle nominale Rafale Signal/contrôle E/S Norme de base Niveau de test Critères de performance(1) Contact 4 kV Air 8 kV De 80 à 1000 MHz à 10 V/m avec 1 kHz AM à 80 % 1400 à 2000 MHz à 3 V/m avec 1 kHz AM à 80 % 2000 à 2700 MHz à 1 V/m avec 1 kHz AM à 80 % A IEC 61000‐4‐8 30 A/m à 50/60 Hz A IEC 61000‐4‐4 1 kV A Surtension IEC 61000‐4‐5 1 kV B Radio-fréquences transmises par conduction IEC 61000‐4‐6 150 kHz à 80 MHz à 3 Vrms A Critère de performance : effet de +/- 1 %. 1. A = Aucune dégradation pendant les essais. B = Dégradation temporaire durant les essais, mais rétablissement automatique. Services de formation Pour obtenir des informations sur les cours de formation disponibles au sujet du contrôleur numérique de vanne DVC6200, et également d'une grande variété d'autres produits, contacter : Emerson Automation Solutions Educational Services - Registration Téléphone : +1 641/754/3771 ou +1 800/338/8158 Adresse e‐mail : education@emerson.com emerson.com/fishervalvetraining 8 A Manuel d’instructions Pratiques de câblage D103605X0FR avril 2021 Section 2 pratiques de câblage22 Exigences du système de régulation Plusieurs paramètres doivent être vérifiés pour s’assurer que le système de contrôle-commande est compatible avec le contrôleur numérique de vanne DVC6200. Filtre HART Selon le système de commande utilisé, un filtre HART peut être nécessaire pour permettre une communication HART. Le filtre HART est un dispositif passif inséré dans le câblage in situ en provenance de la boucle HART. Le filtre est normalement installé à proximité des bornes de câblage in situ d’E/S du système de commande (se reporter à la figure 2‐1). Il vise à isoler efficacement la sortie du système de commande des signaux de communication HART modulés et à augmenter l’impédance du système de commande afin de permettre une communication HART. Pour plus d’informations sur la description et l’utilisation du filtre HART, se référer au manuel d’instructions adéquat concernant les filtres HART. Pour déterminer si un système a besoin d’un filtre, contacter un bureau commercial d’Emerson. Remarque Un filtre HART n’est en général PAS requis pour les systèmes de régulation Emerson, y compris PROVOXt, RS3t et les systèmes DeltaVt. Figure 2‐1. Application des filtres HART DCS NON BASÉS SUR LE PROTOCOLE HART E/S E/S FILTRE HART 4‐20 mA + HART CONTRÔLEUR NUMÉRIQUE DE VANNE Émetteur Émetteur VANNE A6188‐1 Tension disponible La tension disponible au niveau du contrôleur numérique de vanne DVC6200 doit être d’au moins 10 V c.c.. La tension disponible au niveau de l’instrument n’est pas la tension réelle mesurée au niveau de l’instrument lorsque l’instrument est connecté. La tension mesurée au niveau de l’instrument est limitée par l’instrument et est généralement inférieure à la tension disponible. 9 Manuel d’instructions Pratiques de câblage avril 2021 D103605X012 Comme illustré dans la figure 2‐2, la tension disponible sur l’instrument dépend des éléments suivants : D la tension de conformité du système de contrôle-commande D en cas d’utilisation d’un filtre, d’un adaptateur sans fil THUM ou d’une barrière de sécurité intrinsèque, et D le type et la longueur du câble. La tension de conformité du système de contrôle-commande est la tension maximale au niveau des bornes de sortie du système de contrôle-commande, à partir de laquelle le système de contrôle-commande peut produire un courant de boucle maximum. La tension disponible au niveau de l’instrument peut être calculée à partir de l’équation suivante : Tension disponible = [tension de conformité du système de contrôle-commande (au courant maximum)] - [chute de tension du filtre (si un filtre HART est utilisé)] - [résistance totale du câble courant maximum] - [résistance de barrière x courant maximum]. La tension calculée disponible doit être supérieure ou égale à 10 V c.c.. Le tableau 2‐1 indique la résistance de certains câbles typiques. L’exemple suivant montre comment calculer la tension disponible pour un système de contrôle-commande TDC2000 Honeywellt avec filtre HART HF340 et 1000 pieds de câble Beldent 9501 : Tension disponible = [18,5 volts (à 21,05 mA)] - [2,3 volts] - [48 ohm 0,02105 A] Tension disponible = [18,5] - [2,3] - [1,01] Tension disponible = 15,19 volts Figure 2‐2. Détermination de la tension disponible au niveau de l’instrument RÉSISTANCE TOTALE DU CÂBLE DE BOUCLE TENSION DE CONFORMITÉ SYSTÈME DE CONTRÔLECOMMANDE + - BARRIÈRE DE SÉCURITÉ INTRINSÈQUE (le cas échéant) FILTRE HART (le cas échéant) ADAPTATEUR THUM (LE CAS ÉCHÉANT) R Calculer la tension disponible au niveau de l’instrument comme suit : Exemple de calcul La tension de conformité du système de contrôle-commande 18,5 volts (à 21,05 mA) – Chute de tension du filtre (le cas échéant) 1 TENSION DISPONIBLE + AU NIVEAU DE - L’INSTRUMENT – 2,3 volts (pour filtre HF300) – Résistance de barrière de sécurité intrinsèque (si utilisée) x courant de boucle maximum – 2,55 volts (121 ohm x 0,02105 A) – Chute de tension de l’adaptateur Smart Wireless THUM (le cas échéant) 2 – Résistance totale du câble de boucle x courant de boucle maximum = tension disponible au niveau de l’instrument 3 – 1,01 volts (48 ohm x 0,02105 A pour 1000 pieds de câble Belden 9501) = 15,19 volts, disponible : si la barrière de sécurité (2,55 volts) n’est pas utilisée REMARQUES : 1 10 Récupérer la chute de tension du filtre. Le chute mesurée sera différente de cette valeur. La chute de tension du filtre mesurée dépend de la tension de sortie du système de contrôle-commande, de la barrière de sécurité intrinsèque (le cas échéant) et de l’instrument. Voir la remarque 3. 2 La chute de tension de l’adaptateur THUM est linéaire de 2,25 volts à 3,5 mA jusqu’à 1,2 volts à 25 mA. 3 La tension disponible au niveau de l’instrument n’est pas la tension mesurée aux bornes de l’instrument. Une fois l’instrument connecté, l’instrument limite la tension mesurée à environ 8,0 à 9,5 volts. Manuel d’instructions Pratiques de câblage D103605X0FR avril 2021 Tableau 2‐1. Caractéristique d’entrée Capacitéé(1) pF/pi Capacitéé(1) pF/m Résistance(2) Ohm/pi Résistance(2) Ohm/m BS5308/1, 0,5 mm² 61,0 200 0,022 0,074 BS5308/1, 1,0 mm² 61,0 200 0,012 0,037 BS5308/1, 1,5 mm² 61,0 200 0,008 0,025 BS5308/2, 0,5 mm² 121,9 400 0,022 0,074 BS5308/2, 0,75 mm² 121,9 400 0,016 0,053 BS5308/2, 1,5 mm² 121,9 400 0,008 0,025 BELDEN 8303, 22 AWG 63,0 206,7 0,030 0,098 BELDEN 8441, 22 AWG 83,2 273 0,030 0,098 BELDEN 8767, 22 AWG 76,8 252 0,030 0,098 BELDEN 8777, 22 AWG 54,9 180 0,030 0,098 BELDEN 9501, 24 AWG 50,0 164 0,048 0,157 BELDEN 9680, 24 AWG 27,5 90,2 0,048 0,157 BELDEN 9729, 24 AWG 22,1 72,5 0,048 0,157 BELDEN 9773, 18 AWG 54,9 180 0,012 0,042 BELDEN 9829, 24 AWG 27,1 88,9 0,048 0,157 BELDEN 9873, 20 AWG 54,9 180 0,020 0,069 Type de câble 1. Les valeurs de capacité représentent la capacité d’un conducteur à tous les autres conducteurs et le blindage. Il s’agit de la valeur appropriée à utiliser dans les calculs de longueur de câble. 2. Les valeurs de résistance comprennent les deux fils de la paire torsadée. Tension de conformité Si la tension de conformité du système de contrôle-commande n’est pas connue, effectuer le test de tension de conformité suivant. 1. Débrancher le câblage sur site du système de contrôle-commande et raccorder l’équipement comme illustré dans la figure 2‐3 aux bornes du système de contrôle-commande. Figure 2‐3. Schéma du test de tension POTENTIOMÈTRE 1 kW MILLIAMPEREMÈTRE TENSIOMÈTRE CIRCUIT TESTÉ A6192‐1 2. Configurer le système de contrôle-commande pour fournir un courant de sortie maximum. 3. Augmenter la résistance du potentiomètre 1 kW, illustré à la figure 2‐3, jusqu’à ce que l’intensité observée sur le milliampermètre commence à décroître rapidement. 4. Noter la tension indiquée sur le voltmètre. Il s’agit de la tension de conformité du système de contrôle-commande. Pour des informations sur les paramètres spécifiques à votre système de contrôle-commande, contacter votre Bureau commercial Emerson. 11 Manuel d’instructions Pratiques de câblage avril 2021 D103605X012 Recommandations pour la longueur du câblage des bornes auxiliaires Les bornes d’entrée auxiliaires du contrôleur DVC6200 SIS peuvent être utilisées avec un contacteur monté localement et permettant de lancer le test de course partielle. Dans certaines cas, le commutateur doit être installé à distance à partir du DVC6200. La longueur du câblage relié aux bornes d’entrée auxiliaires est limitée par la capacité. Pour un fonctionnement correct des bornes d’entrée auxiliaires, la capacité électrique ne doit pas excéder 100 000 pF. Comme pour tous les câblages de signaux de commande, les bonnes pratiques de câblage doivent être observées afin de minimiser les effets néfastes du bruit électrique sur la fonction de commutation auxiliaire. Exemple de calcul : la capacité par pied ou par mètre est requise pour calculer la longueur de câble qui peut être connectée à l’entrée de commutateur auxiliaire. Le câble ne doit pas dépasser la limite de capacité de 100 000 pF. En général, le fabricant fournit une fiche de données qui fournit toutes les propriétés électriques du câble. Le paramètre pertinent correspond à la capacité la plus élevée possible. Pour les câbles blindés, le chiffre correspondant est la valeur « Conducteur / autre conducteur et Blindage ». Exemple : câble de contrôle, d’instrumentation non blindé et audio 18 AWG Les caractéristiques du fabricant sont les suivantes : Capacité Capacité nominale (électrique) conducteur/conducteur à 1 KHz : 26 pF/pi Nom. Résistance c.c. du conducteur à 20 °C : 5,96 ohm/1 000 pi Maximum. Tension de fonctionnement-UL 200 V RMS (PLTC, CMG), 150 V RMS (ITC) Longueur autorisée avec ce câble = 100 000 pF/(26 pF/pi) = 3 846 pi Exemple : Câble de contrôle et d’instrumentation blindé et audio 18 AWG Les caractéristiques du fabricant sont les suivantes : Nom. Impédance caractéristique nominale : 29 ohm Inductance nominale : 0,15 μH/pi Capacité nominale (électrique) conducteur/conducteur à 1 KHz : 51 pF/pi Capitale. Condition à condition et blindage à 1 KHz : 97 pF/pi longueur autorisée avec ce câble = 100 000 pF/(97 pF/pi) = 1 030 pi L’entrée du contacteur auxiliaire envoie un courant inférieur à 1 mA aux contacts du commutateur et utilise une tension inférieure à 5 V de sorte que les limites de résistance et de tension du câble ne sont pas critiques. S’assurer que la corrosion du commutateur est évitée. Il est en général conseillé d’utiliser des contacts scellés ou plaqués or pour le commutateur. Capacité (électrique) maximale du câble La longueur de câble maximale pour la communication HART est limitée par la capacité (électrique) caractéristique du câble. La longueur maximale déduite de la capacité peut être calculée à l’aide des formules suivantes : Longueur (pi) = [160 000 - Cbus(pF)] [Ccâble(pF/pi)] Longueur (m) = [160.000 - Cbus(pF)] [Ccâble(pF/m)] quand : 160 000 = constante dérivée des instruments FIELDVUE pour s’assurer que la constante de temps HART Network RC ne soit pas supérieure à 65 μs (selon la spécification HART). Cbus = capacité du système de contrôle-commande ou du filtre HART Ccâble = la capacité du câble utilisé (voir le tableau 2‐1) 12 Manuel d’instructions Pratiques de câblage D103605X0FR avril 2021 L’exemple suivant montre comment calculer la longueur du câble d’un Foxborot Système de commande I/A (1988) avec un Cbus de 50 000 pF et un câble Belden 9501 avec une capacité caractéristique de 50 pF/pi. Longueur (pi) = [160 000 - 50 000 pF] [50 pF/pi] Longueur = 2 200 pi La longueur de câble maximale pour la communication HART est limitée par la capacité (électrique) caractéristique du câble. Pour augmenter la longueur du câble, sélectionner un câble avec une capacité (électrique) inférieure par pied. Pour des informations sur les paramètres spécifiques à votre système de contrôle-commande, contacter votre Bureau commercial Emerson. Installation en association avec un convertisseur Rosemount 333 de signal Tri-Loop HART en signal analogique. Utiliser le contrôleur numérique de vanne DVC6200 en fonctionnement avec un convertisseur de signal Rosemount 333 Tri-Loop HART en un signal de sortie analogique indépendant de 4-20 mA pour l’entrée analogique, la cible de course, la pression ou la course. La Tri-Loop HART accepte trois de ces signaux numériques et les convertit en trois canaux analogiques 4-20 mA distincts. Voir la figure 2‐4 pour des informations de base sur l’installation. Voir le manuel du convertisseur de signal Rosemount 333 Tri-Loop HART en un signal de sortie analogique (00809-0100-4754) pour des informations complètes sur l’installation. Figure 2‐4. Organigramme d’installation du module Tri-Loop HART DÉMARRER ICI Déballage du Tri-Loop HART Installer le Tri-Loop HART ; voir le manuel du produit Tri-Loop HART Consulter le manuel du produit Tri-Loop HART Contrôleur numérique de vanne installés ? Oui Montage du Tri-Loop HART sur le rail DIN Non Installer le contrôleur numérique de vanne Raccordement du contrôleur numérique au Tri-Loop HART Réglage de l’option rafale du contrôleur numérique de vanne Installer les fils du canal 1 du Tri-Loop HART dans la salle de commande Réglage du mode rafale du contrôleur numérique de vanne Installer les fils des canaux 2 et 3 du Tri-Loop HART dans la salle de commande (facultatif) Configurer le Tri-Loop HART pour recevoir des commandes en mode rafale du contrôleur numérique Test système OK ? Non Vérifier les procédures de dépannage dans le manuel du produit Tri-Loop HART Oui ACCOMPLIS E0365 13 Manuel d’instructions Pratiques de câblage avril 2021 D103605X012 Mise en service du contrôleur numérique de vanne à utiliser avec le convertisseur de signal Tri-Loop HART Pour préparer le couplage du contrôleur numérique de vanne avec un Tri-Loop HART 333, il est nécessaire de configurer le contrôleur numérique de vanne en mode rafale et de sélectionner la commande rafale n° 3. En mode Rafale, le contrôleur numérique de vanne fournit des informations numériques au Tri-Loop HART vers le convertisseur en signal analogique. Le Tri-Loop HART convertit les informations numériques en un signal analogique de 4 à 20 mA. Chaque message en mode rafale contient la valeur la plus récente des variables primaires (entrée analogique), secondaire (cible de course), tertiaire (pression de sortie configurée) et quaternaire (course). Pour mettre en service un DVC6200 à utiliser avec un Tri-Loop HART, effectuer les procédures suivantes. Remarque Les séquences d’accès rapide ne s’appliquent qu’à l’interface de communication 475. Elles ne s’appliquent pas à l’interface de communication Trex. Activer le fonctionnement en mode rafale Interface de communication Avec emballage E/Se Configurer > Configuration manuelle > Sorties > Mode Rafale HC (2‐2‐6‐6), AD, PD ou ODV (2-2-7-6) Sans emballage E/S Configurer > Configuration manuelle > Sorties > Mode Rafale HC (2‐2‐6‐2), AD, PD ou ODV (2-2-7-2) Choisir « Activer le mode Rafale » et suivre les intructions pour activer le mode Rafale. Puis sélectionner « Commande mode Rafale » et suivre les instructions pour configurer le courant de boucle/PV/SV/TV/QV. Sélectionner les affectations de variable HART Interface de communication Avec emballage E/Se Configurer > Configuration manuelle > Sorties > Affectations de variable HART, HC (2-2-6-4), AD, PD ou ODV (2-2-7-4) Sans emballage E/S Configurer > Configuration manuelle > Sorties > Affectations de variable HART, HC (2-2-6-1), AD, PD ou ODV (2-2-7-1) Configurer les affectations de variable HART La variable primaire (PV) est toujours une entrée analogique. La variable secondaire (SV), la variable tertiaire (TV) et la variable quaternaire (QV) peuvent être configurées sur l’une des variables suivantes. Les affectations de variable du DVC6200 doivent correspondre aux affectations des variables dans le Tri-Loop. D Point de consigne D Course (voir la remarque ci-dessous) D Pression A D Pression B D Pression A­B D Pression d’alimentation D Signal d’entraînement D Entrée analogique Remarque Si l’appareil est configuré pour fonctionner en mode contrôle régulation de la pression ou détecte une lecture incorrecte du capteur de course, la variable de course indiquera la pression en pourcentage de la plage de tarage à sec. 14 Manuel d’instructions Configuration D103605X0FR avril 2021 Section 3 Configuration Remarque Les séquences d’accès rapide ne s’appliquent qu’à l’interface de communication 475. Elles ne s’appliquent pas à l’interface de communication Trex. Configuration assistée Interface de communication Configurer > Configuration assistée (2‐1) Pour configurer rapidement l’instrument, les procédures suivantes vous expliquent le processus. Configuration de l’appareil sert à configurer les paramètres uniques pour la construction de la vanne, de l’actionneur de vanne, de l’instrument et de l’accessoire. Une fois la configuration de l’appareil terminée, procéder à l’étalonnage automatique. L’étalonnage automatique sert à établir les limites de course physique. Au cours de cette procédure, la vanne passe complètement d’une course à l’autre. Trois options d’étalonnage sont possibles : d L’étalonnage automatique – standard exécute le processus d’étalonnage complet (recommandé). d L’étalonnage automatique – sans biais établit les points de fin de course, mais ne règle pas le décalage de contre-réaction de boucle mineure. Cette option est destinée à une utilisation avancée lors du réglage manuel des biais pour les grands actionneurs. d Les paramètres avancés permettent la configuration personnalisée supplémentaire des paramètres d’étalonnage. Cette option est destinée à une utilisation avancée lors du réglage pour les grands actionneurs. Configuration manuelle33 La configuration manuelle permet de configurer le contrôleur numérique de vanne pour l’application. Les listes de tableaux 3‐1 indiquent les paramètres par défaut de la configuration d’usine standard. Il est possible de régler la réponse de l’actionneur, de définir les différents modes, alertes, plages, coupures de course et limites. Il est également possible de redémarrer l’instrument et de régler la protection. Tableau 3‐1. Paramètres de configuration détaillés par défaut Paramètre de configuration Mode contrôle Analogique Mode contrôle au redémarrage Configuration de l’instrument Reprendre au dernier utilisé Plage basse entrée analogique 4 mA Plage basse entrée analogique 20 mA Unités d’entrée analogique Etat dernier étal. auto Adresse d’interrogation Activation du mode rafale Commande rafale mA Désactivé 0 Non 3 Tendance de pression cmd 3 Caractéristique d’entrée Limite de course haute Limite de course basse Réponse et réglage dynamiques Paramétrage par défaut(1) A-B Linéaire 125 % -25 % Coupure de course/pression haute 99,46 % Coupure de course/pression basse 0,50 % Débit ouvert au point de consigne 0 %/s Débit fermé au point de consigne 0%/s Délai du filtre au point de consigne (temps de retard) Activation de l’intégrateur Gain intégral 0s Oui 9,4 répétitions/minute Bande morte intégrale 0,26 % (suite à la page suivante) 15 Manuel d’instructions Configuration avril 2021 D103605X0FR Tableau 3‐1. Paramètres de configuration détaillés par défaut (suite) Paramètre de configuration Paramétrage par défaut(1) Activation de l’alerte de déviation de course Point d’alerte de déviation de course Durée de déviation de course Déviation et autres alertes Activation de l’alerte d’écart de pression Oui 5% 9,99/s Oui Point d’alerte d’écart de pression 5 psi(2) Durée de l’alerte d’écart de pression 5,0 sec Activation de l’alerte du signal d’entraînement Oui Activation de l’alerte de pression d’alimentation Oui 1. Les paramètres listés sont destinés à une configuration d’usine standard. Les instruments DVC6200 peuvent également être commandés avec des paramètres de configuration personnalisés. Voir la demande de commande pour les paramètres personnalisés. 2. Régler en bar, kPa ou kg/cm2 si nécessaire. Mode et protection Interface de communication Configurer > Configuration manuelle > Mode et protection (2‐2‐1) Mode de l’instrument Il existe deux modes d’instrument pour la DVC6200, en service ou hors service. En service est le mode de fonctionnement normal afin que l’instrument suive le signal de commande de 4­20 mA. Dans certains cas, la modification des paramètres de configuration ou l’exécution des diagnostics nécessite l’utilisation d’une sortie hors service. Remarque Certaines modifications nécessitant la mise hors service de l’instrument ne prendront pas effet tant que l’instrument ne sera pas remis en service ou que l’instrument n’aura pas été redémarré. Verrouillage en écriture Il existe deux modes de verrouillage en écriture pour le DVC6200 : Non protégé (« Not Protected ») ou Protégé (« Protected »). Le mode Protégé empêche les modifications de configuration et d’étalonnage de l’instrument. Le réglage par défaut est en mode Non protégé. Le verrouillage en écriture peut passer en mode Protégé à distance. Le verrouillage en écriture peut être modifié en mode Protégé à distance. Cependant, pour changer le verrouillage en écriture en mode Non protégé, il faut disposer d’un accès physique à l’instrument. Pour ce faire, la procédure requiert d’appuyer sur un bouton ( ) du boîtier à bornes par mesure de sécurité. Instrument Interface de communication Configurer > Configuration manuelle > Instrument (2‐2‐2) Suivre les instructions qui s’affichent sur l’indicateur de l’interface de communication pour configurer les paramètres d’instrumentation suivants : Identification D Repère HART : Un nom de repère jusqu’à 8 caractères est disponible pour l’instrument. Le repère HART constitue le moyen le plus simple de distinguer les différents instruments dans un environnement à instruments multiples. Ce repère HART permet d’étiqueter électroniquement des instruments en fonction des exigences de l’application considérée. Le repère affecté est automatiquement affiché lorsque l’interface de communication établit le contact avec le contrôleur numérique de vanne lors de la mise en marche. D Repère long HART (HART Universal Revision 7 seulement) : un nom de repère jusqu’à 32 caractères est disponible pour l’instrument. 16 Manuel d’instructions D103605X0FR Configuration avril 2021 D Description : saisir une description pour l’application jusqu’à 16 caractères. La description fournit une étiquette électronique définie par l’utilisateur, plus longue qu’un repère HART, permettant de spécifier des données nécessaires à une identification précise de l’instrument. D Message : Saisir n’importe quel message jusqu’à 32 caractères. Le message constitue le moyen le plus spécifique dont dispose l’utilisateur pour identifier des appareils particuliers au sein d’un environnement à instruments multiples. D Adresse d’interrogation : si le contrôleur numérique de vanne est utilisé en mode de fonctionnement point-à-point, l’adresse d’interrogation est 0. Lorsque plusieurs appareils sont connectés dans la même boucle, par exemple pour un fractionnement, une adresse d’interrogation unique doit être affectée à chaque appareil. L’adresse d’interrogation est réglée sur une valeur comprise entre 0 et 63 pour les HART 7 et 0 et 15 pour les HART 5. Pour modifier l’adresse d’interrogation, l’appareil doit être hors service. Pour que l’interface de communication puisse communiquer avec un dispositif dont l’adresse d’interrogation n’est pas 0, elle doit être configurée pour rechercher automatiquement tous les appareils connectés ou spécifiques. Numéros de série D Numéro de série de l’instrument : saisir le numéro de série sur la zone d’immatriculation de l’instrument jusqu’à 12 caractères. D Numéro de série de la vanne : saisir le numéro de série de la vanne dans l’application, jusqu’à 12 caractères. Unités D Unités de pression : définit les unités des pressions d’alimentation et de sortie en psi, bar, kPa, ou kg/cm2. D Unités de température : degrés Fahrenheit ou Celsius. La température mesurée provient d’un capteur monté sur le circuit imprimé du contrôleur numérique de vanne. D Unités d’entrée analogique : permettent de définir les unités d’entrée analogiques en mA ou en pourcentage de la plage de 4-20mA. Boîtier à bornes D Bouton d’étalonnage (CAL) : ce bouton est situé à proximité des bornes de câblage du boîtier à bornes et fournit un moyen rapide d’étalonner l’instrument. Le bouton doit être enfoncé pendant 3 à 10 secondes. L’étalonnage automatique déplace la vanne sur toute la plage de course, que le mode de l’instrument soit en service ou hors service. Cependant, si le verrouillage en écriture est en mode Protégé, ce bouton ne sera pas actif. Pour abandonner, appuyer à nouveau sur le bouton pendant 1seconde. Le bouton d’étalonnage est désactivé par défaut. D Action de borne auxiliaire : ces bornes peuvent être configurées pour initier un test de course partielle lors de la détection d’un court-circuit entre les bornes (+) et (-). Les bornes doivent être court-circuitées pendant 3 à 10 secondes. Remarque La fonction de borne auxiliaire n’est disponible que pour les instruments de niveau ODV. Plage d’entrée analogique D Plage d’entrée haute : permet de définir la valeur haute de la plage d’entrée. La plage d’entrée haute doit correspondre à la plage de course haute, si la condition d’alimentation nulle est configurée comme fermée. Si la condition d’alimentation nulle est configurée comme ouverte, la plage d’entrée haute correspond à une plage d’entrée basse. Voir la figure 3‐1. 17 Manuel d’instructions Configuration avril 2021 D103605X0FR D Plage d’entrée basse : permet de définir la valeur basse de la plage d’entrée. La plage d’entrée basse doit correspondre à la plage de course basse, si la condition d’alimentation nulle est configurée comme fermée. Si la condition d’alimentation nulle est configurée comme ouverte, la plage d’entrée haute correspond à une plage d’entrée haute. Voir la figure 3‐1. Figure 3‐1. Course étalonnée vers la relation d’entrée analogique Plage de course haute ZPC = OUVERT COURSE ÉTALONNÉE EN % ZPC = FERMÉ LA FORME DE CES LIGNES DÉPEND DE LA CARACTÉRISTIQUE LINÉAIRE DES CARACTÉRISTIQUES D’ENTRÉE ILLUSTRÉE Portée de course basse PLAGE D'ENTRÉE BASSE ENTRÉE ANALOGIQUE mA OU % de 4-20 mA PLAGE D'ENTRÉE HAUTE REMARQUE : ZPC = Condition d'alimentation nulle A6531‐1 Fiche technique La fiche technique fournit un moyen de stocker les caractéristiques complètes de la vanne de régulation sur le DVC6200. Régler l’heure de l’instrument Permet de régler l’horloge de l’instrument. Lorsque les alertes sont stockées dans l’enregistrement de l’alerte, l’enregistrement inclut l’heure et la date. L’horloge de l’instrument utilise un format de 24 heures. Régulation de la course/pression Interface de communication Configurer > Configuration manuelle > Régulation de la pression/course (2‐2-3) Sélection pression/course Cela définit le mode de fonctionnement de l’instrument ainsi que le comportement de l’instrument en cas de défaillance du capteur de course. Il existe quatre choix. D Régulation de la course : l’instrument contrôle la course vers une cible. L’option de secours n’est pas activée. D Régulation de la pression : l’instrument contrôle la course vers une cible. L’option de secours n’est pas activée. D Défaillance du capteur de secours : l’instrument revient à la régulation de la pression en cas de détection d’une défaillance du capteur de course. 18 Manuel d’instructions D103605X0FR Configuration avril 2021 D Déviation de course/capteur de secours : l’instrument revient à la régulation de la pression en cas de détection d’une défaillance du capteur de course, ou si la pression de secours de déviation de course dépasse la durée de la pression de secours de déviation de course. Remarque La sélection pression/course doit être réglée sur Course pour les actionneurs à double effet. Coupures et limites D Sélection de la limite/coupure supérieure : lorsque la sélection de la limite/coupure haute est configurée pour la coupure, la cible de course est réglée sur 123 % lorsque la course dépasse le seuil de coupure haut. Lorsque la sélection de la limite/coupure supérieure est configurée pour la limite, la cible de course ne dépasse pas le seuil de limite haut. D Seuil de limite/coupure haut : il s’agit du seuil de la plage de course étalonnée au-dessus duquel la limite ou la coupure est en vigueur. Lors de l’utilisation de seuils de coupure, il est recommandé d’utiliser un seuil de coupure de 99,5 % pour s’assurer que la vanne est complètement ouverte. La coupure/limite supérieure est désactivée en la réglant sur 125 %. D Taux de coupure haut souple : ce paramètre permet à la vanne de se ramper jusqu’à l’extrême de la course supérieure lorsque le seuil de coupure est atteint à la vitesse configurée. Cela permet d’obtenir une rampe contrôlée dans le siège afin de minimiser les dommages au siège. S’il est réglé sur 0 %/s, le taux de coupure souple est désactivé. D Sélection de la limite/coupure basse : quand l’option Limite/Coupure est configurée sur Coupure, la cible de course est configurée sur ­23 % quand la course est en-dessous du seuil de coupure bas. Quand la sélection de la limite/coupure supérieure est configurée sur Limite, la cible de course ne tombera pas sous le seuil de coupure bas. D Seuil de limite/coupure bas : il s’agit du point du parcours de course étalonnée en-dessous duquel la limite ou la coupure est active. En cas d’utilisation de seuils de coupure, il est recommandé d’utiliser un seuil de coupure de 0,5 % pour assurer une charge maximale du siège de fermeture. La limite/coupure basse est désactivée lorsqu’elle est réglée sur ­25 %. D Taux de coupure bas souple : ce réglage permet à la vanne de passer à l’extrémité de la course basse lorsque le seuil de coupure est atteint à la vitesse configurée. Cela permet d’obtenir une rampe contrôlée dans le siège afin de minimiser les dommages au siège. S’il est réglé sur 0 %/seconde, le taux de coupure souple est désactivé. Régulation de la pression D Valeur haute de la plage de pression : l’extrémité supérieure de la gamme de pression de sortie. Saisir la pression correspondant à 100 % de la course de la vanne lorsque la condition d’alimentation nulle est fermée, ou à 0 % de la course de la vanne lorsque la condition d’alimentation nulle est ouverte. Cette pression doit être supérieure à la valeur basse de la plage de pression. D Valeur basse de la plage de pression : l’extrémité inférieure de la plage de pression de sortie. Saisir la pression correspondant à 0% de la course de la vanne lorsque la condition d’alimentation nulle est fermée, ou à 100 % de la course de la vanne lorsque la condition d’alimentation nulle est ouverte. Cette pression doit être inférieure à la valeur haute de la plage de pression. 19 Configuration Manuel d’instructions avril 2021 D103605X0FR Pression de secours Remarque La pression de secours est disponible pour les instruments de niveau AD, PD, ODV. D Pression de secours de déviation de course : lorsque la différence entre la cible de la course et la course réelle dépasse cette valeur pendant une durée supérieure à celle de la pression de secours de déviation de course, l’instrument ne tiendra plus compte de la contre-réaction de la course ni de la régulation basée sur la pression de sortie. D Durée de la pression de secours de déviation de course : il s’agit du temps, en secondes, pendant lequel la cible de course et la course réelle doivent être dépassées avant que l’instrument ne se remette à réguler la pression. D Récupération de secours : si l’instrument est tombé en régulation de la pression et que le problème de rétroaction est résolu, la récupération de la régulation de la course peut se produire automatiquement ou à l’aide d’une intervention manuelle. Pour revenir au contrôle de course lorsque la fonction de récupération manuelle est sélectionnée, changer la récupération de secours en récupération automatique, puis revenir en mode de récupération manuelle (si nécessaire). Mode contrôle D Mode contrôle : affiche le mode contrôle actuel de l’instrument. « Analogique » s’affiche si l’instrument est en mode point­àà­point et utilise un signal 4­20 mA pour l’alimentation et le point de consigne. « Numérique » s’affiche si l’instrument est en mode multipoint et utilise une tension de 24 V c.c. pour l’alimentation ainsi qu’un point de consigne numérique pour la régulation. Remarque Un autre mode, le mode Test, peut s’afficher. Normalement, l’instrument ne doit pas être en mode Test. Le contrôleur numérique de vanne bascule automatiquement sur ce mode à chaque fois qu’il doit faire une course de la vanne pendant l’étalonnage par exemple. Cependant, en cas d’abandon d’une procédure où l’instrument est en mode de test, il peut demeurer dans ce mode. Pour sortir l’instrument du mode Test, sélectionner « Changer le mode contrôle » et saisir « Analogique » ou « Numérique ». D Changer le mode contrôle : cela permet à l’utilisateur de configurer le mode contrôle sur « Analogique » ou « Numérique ». D Redémarrer le mode contrôle :cela définit le mode contrôle de l’instrument après un redémarrage (p. ex., un cycle d’alimentation). Les choix disponibles sont « Restaurer le dernier mode », « Analogique » et « Numérique ». 20 Manuel d’instructions D103605X0FR Configuration avril 2021 Caractérisation D Caractérisation d'entrée La caractérisation d’entrée définit la relation entre la cible de course et le point de consigne parcouru. La valeur du point de consigne correspond à l’entrée de la fonction de caractérisation. Si le signal de contrôle nul est fermé, alors une valeur de consigne de 0 % correspond à une entrée de 0 %. Si le signal de contrôle nul est ouvert, alors une valeur de consigne de 0 % correspond à une entrée de 100 %. La course souhaitée correspond à la valeur de sortie de la fonction de caractérisation. Pour sélectionner une caractérisation d’entrée, sélectionner « Caractérisation d’entrée » à partir du menu « Caractérisation ». Il est possible de choisir parmi les trois caractéristiques d’entrée fixes illustrées dans la figure 3‐2 ou de sélectionner une caractéristique personnalisée. La figure 3‐2 illustre la relation entre la cible de course et le point de consigne pour les caractéristiques d’entrée fixe, en supposant que la condition d’alimentation nulle est configurée comme fermée. Il est possible de spécifier 21 points sur une courbe caractéristique personnalisée. Chaque point définit une cible de course, en % de la course étendue, pour un point de consigne correspondant, en % du point de consigne de l’échelle. La plage de valeurs de point de consigne est comprise entre -6,25 % et 106,25 %. Avant toute modification, la caractéristique personnalisée est linéaire. D Personnaliser la caractérisation Pour définir une caractéristique d’entrée personnalisée, sélectionner « Personnaliser » depuis le menu « Caractérisation ». Sélectionner le point à définir (1 à 21), puis saisir la valeur de point de consigne souhaitée. Appuyer sur « Entrer », puis saisir la cible de course souhaitée pour le point de consigne correspondant. Lorsque cela est terminé, sélectionner le point 0 pour revenir au menu «Caractérisation ». Grâce à la caractérisation des entrées, il est possible de modifier la caractéristique globale de la vanne et de la combinaison de l’instrument. La sélection d’un pourcentage égal, d’une ouverture rapide ou personnalisée (autre que la caractéristique d’entrée linéaire par défaut) modifie la caractéristique globale de la vanne et de l’instrument. Cependant, si on sélectionne la caractéristique d’entrée linéaire, la caractéristique globale de la vanne et de l’instrument sont la caractéristique de la vanne, qui est déterminée par les éléments internes de la vanne (c.-à-d. le bouchon ou la cage). 21 Manuel d’instructions Configuration avril 2021 D103605X0FR Figure 3‐2. Cible de course par rapport au point de consigne de plage, pour diverses caractéristiques d’entrée (condition d’alimentation nulle = fermée) 125 100 100 Cible de course, % Cible de course en, % 125 0 0 -25 -25 0 Point de consigne parcouru en, % -25 100 125 Caractéristique d’entrée = linéaire -25 0 125 Cible de course en, % 100 0 -25 -25 0 Point de consigne parcouru en, % 100 125 Caractéristique d’entrée = ouverture rapide A6535‐1 22 Point de consigne parcouru, % 100 125 Caractéristique d’entrée = pourcentage égal Manuel d’instructions Configuration D103605X0FR avril 2021 Réponse dynamique D Débit SP ouvert : débit maximal (% de la course de la vanne par seconde) auquel le contrôleur numérique de vanne se déplace vers la position ouverte, quelle que soit la vitesse de modification du courant d’entrée. Une valeur de 0 désactive cette fonction et permet à la vanne de s’ouvrir aussi rapidement que possible. D Débit SP ferméé : débit maximal (% de la course de la vanne par seconde) auquel le contrôleur numérique de vanne se déplace vers la position fermée, quelle que soit la vitesse de modification du courant d’entrée. Une valeur de 0 désactive cette fonction et permet à la vanne de s’ouvrir aussi rapidement que possible. D Durée du filtre de point de consigne (Temps de retard) : la durée du filtre du point de consigne (temps de retard) ralentit la réponse du contrôleur numérique de vanne de vanne. Une valeur comprise entre 0,2 et 10,0 peut être utilisée pour les procédés bruyants ou rapides afin d’améliorer le contrôle du procédé en boucle de régulation. La saisie d’une valeur de 0,0 va désactiver le filtre de retard. Remarque La durée du filtre du point de consigne (temps de retard) est disponible pour les niveaux d’instrumentation HC, AD et PD. D Filtre avance/retard du point de consigne : les appareils ODV ont accès à un filtre avance/retard du point de consigne qui peut être utilisé pour améliorer la réponse dynamique d’une vanne. Le filtre avance/retard fait partie de la routine de traitement des points de consigne qui reforme le signal d’entrée avant qu’il ne devienne un point de consigne de course. Les filtres avance/ retard sont caractérisés par des constantes de temps de retard et d’avance. Remarque L’option avance/retard n’est disponible que pour le niveau d’instrument ODV. Lorsque la vanne est dans sa zone de régulation active (hors du siège), le filtre avance/retard améliore la réponse d’amplitude réduite en surchargeant momentanément le point de consigne de course. Cette fonctionnalité est utile lorsque l’actionneur est grand et qu’il est équipé d’accessoires. En conséquence de cela, tous les boosters de volume présents seront activés. Plus le retard est long, plus le surentraînement est prononcé. Dans la mesure où le filtre d’entrée avance/retard est utilisé pour améliorer la réponse dynamique d’une vanne de régulation, les paramètres de filtre doivent être définis après l’établissement des paramètres de réglage. Lorsque la vanne est à son siège, le filtre avance/retard est également doté d’une fonction de boost qui définit les conditions d’origine du filtre de façon artificiellement basse de sorte que les changements de signal de petite amplitude semblent être des changements de signal importants au niveau du filtre. La fonction Boost présente un pic important qui surcharge momentanément l’instrument et active tous les boosters de volume externes qui peuvent être présents. La fonction Boost avance/retard est normalement désactivée, sauf dans les cas où la vanne doit répondre aux petits signaux de commande du siège. En réglant le ratio avance/retard dans les directions d’ouverture et de fermeture sur 1,0, la fonction boost peut être activée sans mettre en place de dynamiques avance/retard dans la zone de régulation active. Voir le tableau 3‐2 pour connaître les paramètres standard du filtre avance/retard. Tableau 3‐2. Avance/retard standard Paramètres du filtre pour le niveau d’instrument ODV Paramètre Description Valeur standard Retard Constante de temps de premier ordre. Une valeur de 0,0 désactive le filtre avance/retard. Rapport avance/retard d’ouverture Réponse initiale au filtre dans le sens d’ouverture. 2,0 Rapport avance/retard de fermeture Réponse initiale au filtre dans le sens de fermeture. 2,0 Mode Boost avance/ retard Conditions d’origine du filtre avance/retard lorsque la coupure de course inférieure est active. 0,2/s Déconnecté 23 Manuel d’instructions Configuration avril 2021 D103605X0FR Réglage Interface de communication Configuration > Configuration manuelle > Réglage (2‐2-4) Réglage de course AVERTISSEMENT Toute modification du réglage configuré peut entraîner l'actionnement de l'ensemble vanne/actionneur. Pour éviter les blessures ou dommages matériels causés par des pièces en mouvement, garder les mains, les outils et tout autre objet éloignés de l’ensemble vanne/actionneur. D Ensemble de réglage de course Il y a onze ensembles de réglage à choisir. Chaque ensemble de réglage fournit des valeurs présélectionnées pour les paramètres de gain du contrôleur numérique de vanne. L’ensemble de réglage C offre la réponse la plus lente et l’ensemble de réglage M offre la réponse la plus rapide. Le tableau 3‐3dresse la liste des valeurs de gain proportionnel, de gain de vitesse et de gain de contre-réaction de la boucle mineure pour les jeux de réglage. Tableau 3‐3. Valeurs de gain pour les ensembles de réglage de course préselectionnés Ensemble de réglage Gain proportionnel Gain de vitesse Gain de contre-réaction de la boucle mineure C D E F G 4,4 4,8 5,5 6,2 7,2 3,0 3,0 3,0 3,1 3,6 35 35 35 35 34 H I J K L M X (Expert) 8,4 9,7 11,3 13,1 15,5 18,0 Ajusté par l’utilisateur 4,2 4,85 5,65 6,0 6,0 6,0 Ajusté par l’utilisateur 31 27 23 18 12 12 Ajusté par l’utilisateur En outre, il est possible de spécifier le mode de réglage « Expert » et de paramétrer individuellement le gain proportionnel, le gain de vitesse, et les gains mineurs de la boucle de contre-réaction. La définition ou la modification individuelle d’un paramètre de réglage ou l’exécution de « Stabilisation/Optimisation » modifie automatiquement le réglage placé sur X (Expert). Remarque Utiliser le réglage Expert seulement si le réglage standard n’a pas permis d’obtenir les résultats escomptés. Les fonctions « Stabilisation/Optimisation » ou « Optimiseur de performances » permettent d’obtenir les résultats escomptés plus rapidement qu’avec le mode de réglage manuel « Expert ». Le tableau 3‐4 fournit les recommandations de sélection des ensembles de réglage pour les actionneurs Fisher et Baumann. Ces ensembles de réglage sont seulement recommandés en tant que points de départ. Une fois la configuration et l’étalonnage de l’instrument terminés, il se peut qu’il faille sélectionner un réglage supérieur ou inférieur pour obtenir la réponse souhaitée. 24 Manuel d’instructions Configuration D103605X0FR avril 2021 Tableau 3‐4. Informations sur l’actionneur pour la configuration initiale Fabricant de l’actionneur Modèle de l’actionneur 585C et 585CR 657 667 1051 et 1052 1061 Ressort et membrane Ensemble de réglage pour le démarrage E I J L M H K L À l’écart de la partie supérieure de l’instrument Ressort et membrane M H K L Vers la partie supérieure de l’instrument Taille de l’actionneur Type d’actionneur 25 50 60 68, 80 100 et 130 30, 30i 34, 34I, 40, 40I 45, 45i, 50, 50i 46, 46I, 60, 60i, 70, 70I et 80‐100 30, 30i 34, 34i, 40, 40i 45, 45i, 50, 50i 46, 46i, 60, 60i, 70, 70i, 76, 76i et 80‐100 Piston Dbl avec ou sans ressort. Voir le manuel d’instructions et la plaque signalétique de l’actionneur. 20, 30 33 40 60, 70 30 40 60 68, 80, 100 et 130 Mouvement du capteur de course(2) Relais A ou C(3) Spécifié par l’utilisateur M H I K M J K L M Ressort et membrane (montage sur fenêtre) Piston Dbl avec ou sans ressort. Fisher À l’écart de la partie supérieure de l’instrument Dépend des raccordements pneumatiques. Voir la description du mouvement du capteur de course Type de montage A 1066SR 20 27 et 75 2052 1 2 3 3024C 30, 30E 34, 34E, 40, 40E 45 et 45E Baumann 750 B À l’écart de la partie supérieure de l’instrument Vers la partie supérieure de l’instrument C Vers la partie supérieure de l’instrument D À l’ de la partie supérieure de l’instrument Ressort et membrane (montage sur fenêtre) H J M À l’écart de la partie supérieure de l’instrument Ressort et membrane E H K Pour Po mode de fonctionnement (air ouvert) : vers le haut de l’instrument Pour Ps mode de fonctionnement (fermeture de l’air) : à l’écart de la partie supérieure de l’instrument X(1) 225 GX G L Piston Sgl avec ressort Mouvement du capteur de course Ressort et membrane K 1 200 M Extraction de la tige (vers le bas) par augmentation de la pression d’air Rétraction de la tige (vers le haut) par augmentation de la pression d’air 16 32 54 C E H Rotatif 10 25 54 L’entrée d’air s’ouvre vers le haut de l’instrument L’entrée d’air se ferme à l’écart de la partie supérieure de l’instrument À l’écart de la partie supérieure de l’instrument Ressort et membrane Vers la partie supérieure de l’instrument E H J Spécifier REMARQUE : voir le tableau de la figure 3‐6 pour les informations relatives au raccordement de contre-réaction (aimant). 1. X = réglage Expert. Gain proportionnel = 4,2 ; gain de vitesse = 3,0 ; gain de contre-réaction de boucle mineure = 18,0 2. Dans cet exemple, le mouvement du capteur de course fait référence au mouvement de l’aimant. 3. Les valeurs indiquées sont pour les relaiss A et C. L’inverse pour le relais B. 25 Configuration avril 2021 Manuel d’instructions D103605X0FR D Gain proportionnel : le gain proportionnel pour l’ensemble de réglage de la régulation de la course. La modification de ce paramètre fait également passer l’ensemble de réglage sur « Expert ». D Gain de vitesse : le gain de vitesse pour le réglage de la régulation de la course. La modification de ce paramètre fait également passer l’ensemble de réglage sur « Expert ». D Gain MLFB : le gain de contre-réaction de la boucle mineure pour l’ensemble de réglage de régulation de la course. La modification de ce paramètre fait également passer l’ensemble de réglage sur « Expert ». D Activation intégrale : « Oui » ou « Non ». Activer le réglage intégré pour améliorer les performances statiques en corrigeant l’erreur qui existe entre la cible de course et la course réelle. La régulation intégrale de course est activé par défaut. D Gain intégral : le gain intégral de course correspond au rapport entre la modification de la sortie et la modification de l’entrée, basé sur l’action de régulation dans laquelle la sortie est proportionnelle à l’intégrale de temps de l’entrée. D Stabilisation/Optimisation AVERTISSEMENT Lors de la stabilisation/optimisation, la vanne peut bouger, causant la libération d’un fluide mesuré ou une dissipation de la pression. Pour éviter les blessures et les dommages matériels causés par le relâchement de pression ou de fluide mesuré, isoler la vanne du procédé et équilibrer la pression des deux côtés de la vanne ou purger le fluide mesuré. La fonction de stabilisation/optimisation permet d’ajuster la réponse de vanne en changeant le réglage du contrôleur numérique de vanne. Lors de cette procédure, l’instrument doit être hors service, même si cela n’empêche pas l’instrument de répondre aux changements de point de consigne. Si la vanne est instable, sélectionner « Diminuer la réponse » afin d’en stabiliser le fonctionnement. Cela a pour effet de sélectionner l’ensemble de réglage inférieur suivant (en passant par exemple de F à E). Si la réponse de vanne est lente, sélectionner « Augmenter la réponse » pour rendre la vanne plus réactive. Cela a pour effet de sélectionner le réglage supérieur suivant (en passant par exemple de F à G). Si, après avoir sélectionné « Diminuer la réponse » ou « Augmenter la réponse », le dépassement du point de consigne de la course de la vanne est excessif, sélectionner « Diminuer l’amortissement » pour sélectionner une valeur d’amortissement qui permet plus de dépassement. Sélectionner « Augmenter l’amortissement » pour choisir une valeur d’amortissement qui réduit le dépassement du point de consigne. Une fois l’opération terminée, sélectionner « terminé ». 26 Manuel d’instructions Configuration D103605X0FR avril 2021 Réglage de la pression D Ensemble de réglage de la pression Il y a douze ensembles de réglage de la pression à choisir Chaque ensemble de réglage fournit une valeur présélectionnée pour les paramètres de gain du contrôleur numérique de vanne. L’ensemble de réglage C offre la réponse la plus lente et le réglage M offre la réponse la plus rapide. L’ensemble de réglage B est approprié pour le contrôle d’un positionneur pneumatique. Le tableau 3‐5 dresse la liste des valeurs de gain proportionnel, de gain de vitesse et de gain de contre-réaction de boucle mineure pour les ensembles de réglage. Tableau 3‐5. Valeurs de gain pour les ensembles de réglage de la pression présélectionnés Ensemble de réglage B C D E F G H I J K L M X (expert) Gain proportionnel Gain de l’intégrateur Gain de contre-réaction de la boucle mineure 0,5 2,2 2,4 2,8 3,1 3,6 4,2 4,8 5,6 6,6 7,8 9,0 Ajusté par l’utilisateur 0,3 0,1 0,1 0,1 0,1 0,1 0,1 0,1 0,1 0,1 0,1 0,1 Ajusté par l’utilisateur 35 35 35 35 35 34 31 27 23 18 12 12 Ajusté par l’utilisateur En outre, il est possible de spécifier le mode de réglage Expert et de paramétrer individuellement le gain proportionnel, l’intégrateur de pression, et le gain de contre-réaction de la boucle mineure. La définition ou la modification individuelle d’un paramètre de réglage modifie automatiquement le réglage placé sur X (Expert). Remarque Utiliser le réglage Expert seulement si le réglage standard n’a pas permis d’obtenir les résultats escomptés. Les fonctions « Stabilisation/Optimisation », ou « Optimiseur de performances » dans le logiciel ValveLink peuvent être utilisées pour parvenir aux résultats escomptés plus rapidement qu’avec le mode de réglage Expert. D Gain proportionnel : le gain proportionnel pour le réglage de régulation de la pression. La modification de ce paramètre fait également passer l’ensemble de réglage sur « Expert ». D Gain MLFB : gain de contre-réaction de la boucle mineure des ensembles de réglage pour la régulation de la pression. La modification de ce paramètre fait également passer l’ensemble de réglage sur « Expert ». D Activation intégrale : « Oui » ou « Non ». Activer le réglage intégré de la pression pour améliorer les performances statiques en corrigeant l’erreur qui existe entre la pression cible et la pression réelle. La régulation intégrale de la pression est activée par défaut. D Gain intégral : le gain intégral de pression (également appelé « Reset ») est le facteur de gain appliqué à l’intégrale de temps du signal d’erreur entre la pression souhaitée et la pression réelle. Cette fonction est utilisée pendant le régulation de la pression pour une plus grande précision de la régulation de la pression ou de la pression de secours. La modification de ce paramètre fait également passer l’ensemble de réglage sur « Expert ». Réglages intégrés de course/pression D Bande morte intégrée : une fenêtre entourant le point de consigne principal dans lequel l’action intégrale est désactivée. La bande morte peut être configurée entre 0 % et 2 %, ce qui correspond à une fenêtre symétrique, de 0 % à +/-2 % du point de 27 Manuel d’instructions Configuration avril 2021 D103605X0FR consigne principal. La bande morte intégrée est utilisée pour éliminer les cycles de seuil induits par friction sur le point de consigne principal lorsque l’intégrateur est actif. Cette valeur de bande morte est utilisée lors de l’étalonnage automatique de la procédure de course, même si l’intégrale de course est désactivée ; dans le cas de défaillances de la course d’étalonnage automatique avec des actionneurs à piston, cette valeur doit être réglée sur 1 %. La valeur par défaut est de 0,26 %. D Limite de l’intégrateur : la limite de l’intégrateur fournit une limite supérieure à la sortie de l’intégrateur. La limite haute peut être configurée entre 0 et 100 % du signal d’entraînement I/P. Vanne et actionneur Interface de communication Configuration > Configuration manuelle > Vanne et actionneur (2-2-5) Type de vanne : renseigner le type de vanne, rotative ou à tige coulissante. Type d’actionneur : renseigner le type d’actionneur, ressort et membrane, piston à double action sans ressort, piston à simple action sans ressort, ou piston à double action sans ressort. Raccordement de contre-réaction : voir le tableau 3‐6 pour les options de raccordement de contre-réaction. Choisir l’assemblage correspondant à la plage de course de l’actionneur. Remarque En règle générale, ne pas utiliser moins de 60 % du parcours de course de l’aimant pour mesurer la course totale. L’utilisation de l’ensemble sur une gamme réduite affecte les performances. La course utile des aimants linéaires est indiquée par des flèches moulées sur la pièce. Ceci implique que le capteur hall (situé au dos du boîtier du DVC6200) doit rester dans ces limites sur la totalité de la course de la vanne. Les montages des aimants linéaires sont symétriques. N’importe quelle extrémité peut pointer vers le haut. Tableau 3‐6. Options de raccordement de contre-réaction Aimant. Course mm in. Degrés Tige coulissante n° 7 4,2-7 0,17-0,28 - Tige coulissante n° 19 8-19 0,32-0,75 - Tige coulissante n° 25 20-25 0,76-1,00 - Tige coulissante n° 38 26-38 1,01-1,50 - Tige coulissante n° 50 39-50 1,51-2,00 - Tige coulissante n° 110 51-110 2,01-4,125 - Tige coulissante n° 210 110-210 4,125-8,25 Galet n° 1 pour tige coulissante > 210 > 8,25 60-90_ Fenêtre Rshaft n° 1 - - 60-90_ Fenêtre Rshaft n° 2 - - 60-90_ Montage d’extrémité Rshaft - - 60-90_ Type de relais : il existe trois catégories de relais qui donnent les combinaisons à sélectionner. Type de relais : le type de relais est imprimé sur l’étiquette apposée sur le corps du relais. A = à double action ou simple action B = inverse à simple action C = direct à simple action Application spéciale : ce mode est utilisé dans les applications à action unique où l’orifice de sortie « inutilisé » est configuré pour lire la pression en aval d’une vanne électromagnétique. Faible purge : l’étiquette apposée sur le corps du relais indique s’il s’agit d’une version à faible purge. 28 Manuel d’instructions Configuration D103605X0FR avril 2021 Condition d’alimentation nulle : la position de la vanne (ouverte ou fermée) quand l’alimentation électrique est retirée de l’instrument. La condition d’alimentation nulle (ZPC) est déterminée par l’action du relais et de l’actionneur comme illustré à la Figure 3‐3. Figure 3‐3. Condition d’alimentation nulle A B Type de relai Perte d’énergie électrique Direct à simple action (relais A ou C) Orifice A pression jusqu’à zéro. À double action (relais A) Orifice A pression jusqu’à zéro. Orifice B pression pour une alimentation complète. Inverse à simple action (relais B) Orifice B pression pour une alimentation complète. Mouvement du capteur de course AVERTISSEMENT Si la réponse est « OUI » à la demande de permission de déplacer la vanne lors de la détermination du mouvement du capteur de course, l’instrument déplace la vanne sur une partie significative de sa plage de course. Pour éviter les blessures et les dommages matériels causés par le relâchement de pression ou de fluide mesuré, isoler la vanne du procédé et équilibrer la pression des deux côtés de la vanne ou purger le fluide mesuré. Sélectionner « Sens horaire / vers le bas » ou « Sens antihoraire / vers le haut ». Le déplacement du capteur de course permet d’établir le sens de rotation correct du capteur de course. Pour les actionneurs quart-de-tour, déterminer la direction de rotation en observant la rotation de l’aimant depuis l’arrière de l’instrument. Remarque Dans cet exemple, le mouvement du capteur de course fait référence au mouvement de l’aimant. L’aimant peut être désigné par l’expression « réseau magnétique » dans les outils d’interface de l’utilisateur. D Pour les instruments avec relaiss A et C : si l’augmentation de la pression d’air au niveau de la sortie A provoque le déplacement de l’aimant vers le bas ou de l’axe rotatif dans le sens horaire, saisir le code « Sens horaire / vers les bas ». Si l’aimant se déplace vers le haut ou si l’axe rotatif tourne dans le sens antihoraire, saisir le code « Sens antihoraire / vers le haut ». D Pour les instruments avec relais B : si une diminution de la pression d’air au niveau de la sortie B provoque le déplacement de l’aimant vers le bas ou la rotation de l’axe dans le sens horaire, saisir le code « Sens horaire / vers le bas ». Si l’aimant se déplace vers le haut, ou si l’axe rotatif tourne dans le sens anti-horaire, saisir le code « CCW/to Top inst. ». Pression d’alimentation maximale Saisir la pression d’alimentation maximale requise pour lancer la course complète de la vanne. 29 Manuel d’instructions Configuration avril 2021 D103605X0FR Limite de pression de l’orifice A Dans les applications à simple effet direct uniquement, l’instrument limitera la pression de sortie à l’actionneur de l’orifice A. Lorsque cette limite de pression est dépassée, l’appareil passe en état d’absence d’air. ATTENTION Il s’agit d’une fonction de commande du microprogramme qui nécessite l’alimentation de l’instrument en boucle. En cas de perte de l’alimentation de la boucle, ou si une défaillance électronique ou du micrologiciel se produit, la fonction de protection restera en vigueur. Activation de la limite de pression de sortie : active/désactive la fonction de limite de la pression à l’orifice A. Remarque Une alerte associée est disponible avec cette fonction. Voir l’alerte de surpression au niveau de l’orifice A dans la section «Configuration de l’alerte ». Test de course partielle (PST) Interface de communication Configuration > Configuration manuelle > Course partielle (2-2-7) Remarque La course partielle n’est disponible que pour le niveau d’instrument ODV. Paramètres de test de course partielle Le point de départ du test définit le côté normal (sans déclenchement) de la course de la vanne. La vanne doit se trouver à cette extrémité pour qu’un PST soit initié. Si cette valeur n’est pas configurée, les tests de course partielle sont désactivés. La course HI HI définit, en pourcentage (%) de la course étalonnée, le point au-dessus duquel la vanne est considérée comme ayant atteint l’extrémité supérieure. La course Lo Lo définit, en pourcentage (%) de la course étalonnée, le point en-dessous duquel la vanne est considérée comme ayant atteint l’extrémité inférieure. Le temps de pause représente le temps entre les courses sortantes et entrantes du test. La valeur par défaut est de 5 secondes. Le temps de pause n’est pas utilisé si la courte durée PST est activée. La course sortante va du côté normal à la cible PST et la course entrante est la course de retour à la normale. Voir la figure 3‐4. 30 Manuel d’instructions Configuration D103605X0FR avril 2021 Figure 3‐4. Représentation de la signature de vanne Point de départ PST j k l m n COURSE ENTRANTE COURSE SORTANTE PRESSION o DÉCLENCHÉ p NORMAL COURSE j PRESSION D’ALIMENTATION k RÉGULATION DE LA PRESSION D’UNE EXTRÉMITÉ l SEUIL DE PRESSION ENTRANTE m SEUIL DE PRESSION DE RUPTURE À FAIBLE FROTTEMENT n SEUIL DE PRESSION DE RUPTURE À FROTTEMENT ÉLEVÉ o SEUIL DE PRESSION DE SORTIE p DÉPLACEMENT DE LA COURSE CIBLE 30 % La pression de rupture à frottement élevéé indique que la rupture nécessitait une force plus élevée que celle configurée par l’utilisateur. Voir la figure 3‐4. La pression de rupture à faible frottement indique que la rupture nécessitait une force plus élevée que celle configurée par l’utilisateur. Voir la figure 3‐4. L’action sur un test ratéé définit si la vanne doit être replacée à l’étape ou à la rampe lors d’un test de course défectueux. L’intervalle de test automatique représente l’intervalle de temps en jours entre les tests de course de vanne qui sont automatiquement exécutés par le contrôleur numérique de vanne, sous réserve que l’appareil soit sous tension. La valeur 0 désactive cette fonction. Paramètres de course partielle Le mouvement de course minimum représente le pourcentage de l’étendue totale que la vanne éloigne de son extrémité de course normale vers son extrémité de course déplacée pendant le test. La valeur par défaut est 10 %. PST de courte durée : lorsque cette option est activée, la course d’entrée est initiée dès que la course atteint le mouvement de course minimum. Voir la figure 3‐5 pour une représentation de ce paramètre dans une série de temps. 31 Manuel d’instructions Configuration avril 2021 D103605X0FR COURSE COURSE Figure 3‐5. Représentation de la série chronologique du PST de courte durée RYTHME D’ENTRÉE DE LA RAMPE NORMAL RYTHME DE SORTIE DE LA RAMPE NORMAL DURÉE DU PST RÉDUITE PAS DE RETOUR j k j k PAS DE RETOUR l DURÉE TEMPS DE PAUSE PST DE COURTE DURÉE DÉSACTIVÉ TEMPORISATION DE RUPTURE ARRÊTS PRÉCOCES DURÉE PST DE COURTE DURÉE ACTIVÉ j MOUVEMENT DE COURSE MINIMUM k DÉPLACEMENT DE LA CIBLE DE COURSE l MAX. COURSE ADMISSIBLE Le rythme de sortie de la rampe représente la fréquence à laquelle la vanne se déplace pendant la course sortante du test de course partielle. La valeur par défaut est de 0,25 %/seconde. Le rythme d’entrée de la rampe est la vitesse à laquelle la vanne bougera durant la course entrante durant le test de course partielle. La valeur par défaut est de 0,25 %/seconde. Pas de retour définit le pourcentage (%) du changement de point de consigne pour surmonter l’hystérésis de la vanne. L’erreur entre le point de consigne et l’erreur réelle est ajoutée à ce pourcentage de variation. Par exemple, si le pas de retour est réglé à 0,5% et qu’il y a une erreur de 1 %, cette valeur sera réglée à 1,5% La temporisation de rupture correspond à la durée configurée par l’utilisateur avant laquelle la vanne doit quitter le côté normal au cours d’un PST. Seuil de pression de sortie définit la pression de l’actionneur à laquelle un test de course partielle est abandonné pendant la course sortante (voir la figure 3‐4). Cela empêche le DVC6200 d’épuiser (ou de construire) une pression excessive de/vers l’actionneur lors d’une tentative de déplacement d’une vanne bloquée. Lors de l’étalonnage PST, le seuil de pression de sortie de course partielle est automatiquement défini comme suit : d Actionneurs à simple action : pour les actionneurs qui dépassent la pression du point de départ du test partiel, le seuil de la pression de sortie est une valeur minimale. Pour les actionneurs qui engendrent de la pression à partir du point de départ du test partiel, le seuil de la pression de sortie est une valeur maximale. d Actionneurs à double action : le seuil de pression de sortie est défini sur une valeur négative pour les actionneurs où le point de départ de la course partielle est opposé à la condition d’alimentation nulle (p. ex., point de départ du test de course partielle = ouvert et la condition d’alimentation nulle = fermée) et sur une valeur positive pour les actionneurs où le point de départ du test de course partielle est le même que la condition d’alimentation nulle. 32 Manuel d’instructions Configuration D103605X0FR avril 2021 Le signal de pression utilisé pour déterminer ce paramètre dépend du type de relais et est résumé ci-dessous. Type de relai A ou C B B pour applications spéciales C pour applications spéciales Signal de pression Orifice A - orifice B Orifice B - Orifice A Orifice B Orifice A Pour régler manuellement le seuil de pression de course partielle, il faut examiner les résultats du test de course partielle en utilisant le logiciel ValveLink. Les étapes suivantes guident tout le processus : 1. Connecter le DVC6200 à un système exécutant le logiciel ValveLink. 2. Désactiver la limite de pression sortante de course partielle en veillant à ce qu’elle ne soit pas sélectionnée en tant que critère d’évaluation pour le PST anormal. 3. Lancer un test de course partielle 4. Sélectionner le bouton radio « Press/Time » sur le graphique de course partielle (voir l’exemple de la figure 3‐6). Si la pression de l’actionneur démarre à un niveau élevé et diminue, trouver la pression minimale de l’actionneur (Pmin). Si la pression de l’actionneur démarre à un niveau bas et augmente, trouver la pression maximale de l’actionneur (Pmax). ­Les actionneurs à double action affichent une pression différentielle. Utiliser le tableau 3‐7 pour estimer le seuil de pression de sortie. 5. Activer la limite de pression de sortie précédemment désactivée - calculer la valeur à l’aide du tableau 3‐7. Tableau 3‐7. Estimations pour les limites de pression de course partielle sortante Type d’actionneur Type de relai Condition d’alimentation nulle Fermé A ou C Ouvert Ressort et membrane Fermé B Ouvert Fermé A ou C Ouvert Piston à simple action Fermé B Ouvert Fermé Piston à double action A Ouvert Point de départ PST Limites de pression du test de course partielle Ouvert Pmin - 0,25 * (tarage à sec élevé - tarage à sec bas) Fermé Pmin + 0,25 * (tarage à sec élevé - tarage à sec bas) Ouvert Pmax + 0,25 * (tarage à sec élevé - tarage à sec bas) Fermé Pmin - 0,25 * (tarage à sec élevé - tarage à sec bas) Ouvert Pmax + 0,25 * (tarage à sec élevé - tarage à sec bas) Fermé Pmin - 0,25 * (tarage à sec élevé - tarage à sec bas) Ouvert Pmin - 0,25 * (tarage à sec élevé - tarage à sec bas) Fermé Pmax + 0,25 * (tarage à sec élevé - tarage à sec bas) Ouvert 0,5 * Pmin Ouvert Pmax + 0,5 * (Psupply - Pmax) où Psupply = Pression d’alimentation Pmax + 0,5 * (Psupply - Pmax) Fermé Fermé 0,5 * Pmin Ouvert Pmax + 0,5 * (Psupply - Pmax) Fermé 0,5 * Pmin Ouvert 0,5 * Pmin Fermé Pmax + 0,5 * (Psupply - Pmax) Ouvert Pmin - 0,5 * (Psupply + Pmin) Ouvert Pmax + 0,5 * (Psupply - Pmax) où Psupply = Pression d’alimentation Pmax + 0,5 * (Psupply - Pmax) Fermé Pmin - 0,5 * (Psupply + Pmin) Fermé 33 Manuel d’instructions Configuration avril 2021 D103605X0FR PRESSION (%) Figure 3‐6. Exemple de tracé série temps ; Pression de l’actionneur PRESSION MINIMALE Pmin TRACE RÉELLE À PARTIR DU TEST (STANDARD) LIMITE DE PRESSION DE SORTIE Temps (s) Le seuil de pression d’entrée définit la pression de l’actionneur à laquelle un test de course partielle est abandonné pendant la course de sortie (voir la figure 3‐4). Cela empêche le DVC6200 d’évacuer (ou d’accumuler) une pression excessive depuis/vers l’actionneur lors d’une tentative de déplacement d’une vanne bloquée. Critères anormaux PST Un test de course partielle est signalé comme étant anormal s’il échoue à l’un des critères sélectionnés par l’utilisateur. 1. Pression de course (y compris sortante et entrante) 2. Pression de rupture à frottement élevé 3. Pression de rupture à faible frottement 4. Course maximale 5. Course insuffisante 6. Non assis (au début ou à la fin du test) 7. Test SOV précédé du PST et échoué 8. Déviation de course Critères d’annulation PST Le PST est interrompu et la vanne retourne à du côté normal. Le retour au côté normal se fait conformément à la configuration utilisateur pour un test interrompu. Les critères d’annulation ne sont actifs que s’ils sont ajoutés en tant que critères à évaluer au cours du PST en les ajoutant au critère anormal du PST. L’utilisateur peut sélectionner l’une des options suivantes pour interrompre un test de course partielle : 1. Pression de course (y compris sortante et entrante) 2. Pression de rupture à frottement élevé 3. Pression de rupture à faible frottement 4. Course maximale 5. Course insuffisante 6. Non assis (au début ou à la fin du test) 7. Test SOV précédé du PST et échoué 8. Déviation de course 34 Manuel d’instructions Configuration D103605X0FR avril 2021 PST non autorisé Un test de course partielle n’est pas déclenché si l’une des conditions suivantes configurables par l’utilisateur est activée : 1. Défaillance de l’intégrité de la mémoire flash 2. Défaillance de la boucle d’induction électromagnétique 3. Défaillance de la tension de référence 4. Défaillance du courant d’entraînement 5. Défaillance NVM critique 6. Panne du capteur de température 7. Défaillance du capteur de pression 8. Défaillance du capteur de course 9. Pression d’alimentation basse 10. Déviation de course 11. Pression de secours activée 35 Manuel d’instructions Configuration avril 2021 D103605X0FR Sorties Interface de communication Configuration > Configuration manuelle) > Sorties HC, AD, PD (2-2-6) ou ODV (2-2-7) Configuration de la borne de sortie Remarque Ces options de menu sont seulement disponibles pour les modèles dotés d’un transmetteur de position 4­20 mA ou disposent d’un commutateur. Pour plus d’informations sur le câblage et la configuration du transmetteur de position/commutateur tout-ou-rien, se reporter au Guide de démarrage rapide de la série DVC6200, D103556X012. D Activation des bornes de sortie : si la borne de sortie optionnelle est utilisée pour un transmetteur de position ou une sortie du commutateur, ce paramètre doit être activé avec un outil d’interface utilisateur tel que le logiciel ValveLink. D Fonction : les bornes de sortie peuvent être configurées comme suit : Transmetteur : sortie de 4­20 mA représentant 0­100 % de la course étalonnée de la vanne. Contacteur de fin de course : commutateur à entrées TOR (1 A max) qui se déclenche à un point configurable entre 0­100 % de la course étalonnée de la vanne. Commutateur d’alerte : commutateur à entrées TOR (1 A max) qui se met en sécurité en fonction d’une alerte de dispositif configurable. D Signal d’échec : si le circuit de sortie ne fonctionne pas correctement, la sortie essaiera d’atteindre un état connu. En fonction de la nature de la panne, le circuit peut ou non être capable d’atteindre cet état d’échec. Lorsqu’il est configuré en tant que transmetteur de position, la sortie peut être configurée de façon à être défectueuse (< 3,6 mA). La sortie peut être configurée pour une défaillance élevée (> 22,5 mA) lorsque le contrôleur numérique de vanne est alimenté. Lorsqu’il est configuré en tant que commutateur, la sortie peut être configurée pour être fermée ou ouverte. Remarque En cas de perte de puissance du contrôleur numérique de vanne, le circuit du commutateur passera toujours à l’état ouvert. Configuration des commutateurs Remarque La configuration du commutateur est seulement disponibles pour les modèles dotés d’un transmetteur de position 4­20 mA ou disposent d’un commutateur. D Point de déclenchement du contacteur de seuil :lorsque la fonction est configurée en tant que contacteur de fin de course, cette option définit le seuil pour le contacteur de fin de course en pourcentage de l’étalonnage. D Source du commutateur d’alerte :lorsque la fonction est configurée en tant que commutateur d’alerte, cette option détermine l’alerte qui va activer le commutateur. Les options d’alerte sont les suivantes : déviation de course ou pression de secours. 36 Manuel d’instructions Configuration D103605X0FR avril 2021 D Commutateur ferméé : ceci configure l’action du commutateur. Les choix possibles sont : au-dessous du point de déclenchement / alerte inactive ou au-dessus du point de déclenchement / alerte active. Affectations de variable HART Les variables de l’instrument peuvent être transmises à l’aide de quatre affectations de variables HART différentes. La variable primaire (PV) est toujours configurée en tant qu’entrée analogique. Cependant, les trois variables restantes sont dotées d’options supplémentaires, comme indiqué ci-dessous. Variable principale (PV) entrée analogique Variable secondaire (SV) course, point de consigne de course, pression A, pression B, pression A­B, pression d’alimentation, signal d’entraînement ou entrée analogique Variable tertiaire (TV) course, point de consigne de course, pression A, pression B, pression A­B, pression d’alimentation, signal d’entraînement ou entrée analogique Variable quaternaire (QV) course, point de consigne de course, pression A, pression B, pression A­B, pression d’alimentation, signal d’entraînement ou entrée analogique Sortie du transmetteur Remarque La sortie du transmetteur est seulement disponible pour les modèles qui disposent de transmetteur de position 4­20 mA ou disposent d’un commutateur. Ceci permet de configurer la relation entre la course de la vanne et le signal de sortie du transmetteur de position. Il existe deux choix ; 4 mA = vanne fermée ou 4 mA = vanne ouverte. Mode Rafale Le mode Rafale fournit une communication continue par contrôleur numérique de vanne. Le mode Rafale s’applique uniquement à la transmission de données en mode Rafale (affectation des variables HART), il n’affecte en rien la façon dont les autres données sont accessibles. D Activation du mode Rafale : cette fonction active ou désactive le mode Rafale. D Commande en rafale : cette option définit la commande HART configurée pour le signalement de rafale. Lors de l’utilisation d’un Tri­Loop, sélectionner la commande 3. HART 5 - Entrée analogique (commande 1) - Courant de boucle/course (commande 2) - Courant de boucle/PV/SV/TV/QV (commande 3) HART 7- Entrée analogique (commande 1) - Courant de boucle/course (commande 2) - Courant de boucle/PV/SV/TV/QV (commande 3) - Lire la variable de l’appareil et son état (commande 9) - Lire la variable de l’appareil (commande 33) - Lire l’état additionnel (commande 48) 37 Manuel d’instructions Configuration avril 2021 D103605X0FR Remarque L’accès aux informations de l’instrument est normalement obtenu par l’interrogation/réponse dans la communication HART. L’interface de communication ou le système de contrôle-commande peuvent demander toutes les informations normalement disponibles, même lorsque l’instrument est en mode Rafale. Une courte pause entre chaque transmission en mode rafale émise par l’instrument permet à l’interface de communication ou au système de contrôle-commande de lancer une requête. L’instrument reçoit la requête, traite le message de réponse, puis continue d’envoyer des données en mode Rafale. Le mode rafale est automatiquement désactivé lors des tests de diagnostic tels que la signature de la vanne. Le HART 7 dispose de trois commandes de mode Rafale. Lors de l’utilisation d’un Tri-Loop, ne pas activer les 2e ou 3e commandes de rafale. Ces commandes supplémentaires provoquent des messages manqués, ce qui permet de faire en sorte que la sortie de la Tri-Loop soit en état d’erreur. Remarque Si l’appareil est configuré pour fonctionner en mode régulation de la pression ou détecte une lecture incorrecte du capteur de course, la variable de course indiquera la pression en pourcentage de la plage de tarage à sec. Configuration des alertes Interface de communication Configuration > Configuration des alertes (2‐3) Une alerte est une notification indiquant que l’instrument a détecté un problème. Les alertes activées et actives seront enregistrées dans la mémoire de l’instrument au sein du registre de l’alerte (voir la section 5). Certaines alertes sont également définies dans la structure de réponse de la commande HART 48, qui peut être lue par n’importe quel système hôte de communication HART (voir la spécification de l’appareil de terrain HART, D103639X012). Certaines alertes critiques peuvent être configurées pour arrêter l’appareil lorsqu’il est actif (c.-à-d. le loquet en condition d’alimentation nulle). Cette option peut être activée ou désactivée pour chaque alerte. Le paramètre d’arrêt par défaut est désactivé. Mettre fin à l’arrêt, corriger le problème, puis mettre l’appareil hors tension (ou désactiver l’alerte). Les alertes peuvent être activées ou désactivées avec l’instrument en mode « En service », « Hors service », « Protégé » ou « Non protégé ». Cependant, les alertes d’arrêt ne peuvent être activées ou désactivées que lorsque le mode Protégé est désactivée. Pour plus d’informations détaillées sur les alertes et les mesures recommandées, voir la section 5. Passer au HART 5 / Passer au HART 7 Interface de communication Ooutil d’entretien > Maintenance > Passer au HART 5 / Passer au HART 7 HC (3-5-3) ou AD (3-5-4), PD ou ODV (3-5-5). Remarque Cette procédure ne doit jamais être effectuée tant que la vanne est en service et en train de contrôler le procédé. Selon le système de contrôle-commande ou le système de gestion des équipements raccordé, une réinitialisation complète du système peut être nécessaire pour rétablir la communication HART. Consulter la documentation du système pour plus d’informations. Cette procédure permet de faire passer l’instrument de la version HART Universal Revision 5 à la version HART Universal Revision 7 (ou vice-versa). Avant de continuer, vérifier que les systèmes sont prêts à prendre en charge les appareils HART Universal Revision7. Suivre les instructions qui apparaissent sur l’indicateur de l’interface de communication. 38 Manuel d’instructions D103605X0FR Étalonnage avril 2021 Section 4 Étalonnage44 Remarque Les séquences d’accès rapide ne s’appliquent qu’à l’interface de communication 475. Elles ne s’appliquent pas à l’interface de communication Trex. Présentation de l’étalonnage Lorsqu’un contrôleur numérique de vanne DVC6200 est commandé dans le cadre d’une commande d’un ensemble de régulation de vanne, l’usine monte le contrôleur numérique de vanne sur l’actionneur et s’occupe de faire les raccordements de tuyauterie nécessaires, puis procède à l’étalonnage du contrôleur. Pour les contrôleurs numériques de vanne commandés séparément, il n’est généralement pas nécessaire de réétalonner l’entrée analogique ou les capteurs de pression. Cependant, après le montage sur un actionneur, il faut effectuer la configuration initiale, puis étalonner la course en sélectionnant Configurer > Étalonnage > Étalonnage de la course > Étalonnage automatique. Pour des informations d’étalonnage plus détaillées, se reporter aux procédures d’étalonnage suivantes. Interface de communication Configurer > Étalonnage (2-4) Étalonnage de course automatique - voir la page 40 Étalonnage de course manuel - voir la page 41 Étalonnage du bouton-poussoir - voir la page 42 Étalonnage du capteur de pression - voir la page 43 Étalonnage de l’entrée analogique 44 Réglage du relais : voir page 45 Étalonnage PST (niveau d’instrumentation ODV uniquement) - voir la page 47 Remarque L’instrument doit être en mode « Hors service » et la protection sur « Aucune » avant que l’instrument ne puisse être étalonné. Si le mode Rafale est activé, nous vous recommandons de désactiver la fonction Rafale avant de continuer l’étalonnage. Une fois l’étalonnage terminé, le mode Rafale peut alors être réactivé. AVERTISSEMENT Pendant l’étalonnage, la vanne se déplace sur l’ensemble de sa course. Pour éviter les blessures et les dommages matériels causés par le relâchement de pression ou de fluide procédé, isoler la vanne du procédé et équilibrer la pression des deux côtés de la vanne ou purger le fluide procédé. 39 Manuel d’instructions Étalonnage avril 2021 D103605X0FR Étalonnage de la course Si un relais à double action est utilisé, une invite pour exécuter le réglage du relais lorsque l’étalonnage automatique ou manuel est sélectionné apparaît. Sélectionner « Oui » pour régler le relais, sélectionner « Non » pour procéder à l’étalonnage. Pour plus d'informations, se reporter au réglage des relais à la page 45. Étalonnage automatique 1. La procédure d’étalonnage automatique est automatique. Elle est terminée lorsque le menu « Étalonnage »» apparaît. Lors de l’étalonnage, l’instrument cherche les extrémités high et low et la boucle mineure de contre-réaction (MLFB) ainsi que le biais de sortie. En recherchant les extrémités, l’instrument établit les limites de course physique, c.-à-d. les positions réelles de course entre 0 et 100 %. Cela détermine également la distance de mise en marche du faisceau de relais pour étalonner la sensibilité du capteur MLFB. 2. Mettre l’instrument en service et vérifier que la course suit correctement la source de courant. Si l'unité ne s'étalonne pas, se reporter au tableau 4‐1 indiquant les messages d'erreur et les solutions possibles. Tableau 4‐1. Messages d'erreur d’étalonnage automatique de la course Message d’erreur Problème et solution possible Panne d'alimentation lors de l'étalonnage automatique Le signal d'entrée analogique de l'instrument doit être supérieur à 3,8 mA. Régler la sortie actuelle du système de contrôle-commande ou de la source de courant pour fournir au moins 4,0 mA. Le calibrage automatique ne s'est pas achevé dans la limite de temps Le problème peut être : 1. L'ensemble de réglage choisi est trop bas et la vanne n'atteint pas l'extrémité dans le temps imparti. Sélectionner Configuration manuelle, > Réglage, > Réglage de la course, > Stabilisation/Optimisation puis « Augmenter la réponse » (ce qui sélectionne l'ensemble de réglage supérieur suivant). 2. L'ensemble de réglage sélectionné est trop haut, le fonctionnement de la vanne est instable et ne demeure pas à une seule extrémité durant le temps défini. Sélectionner Configuration manuelle, > Réglage, > Réglage de course, > Stabilisation/optimisation puis Diminuer la réponse (ce qui sélectionne le préréglage immédiatement inférieur). Course insuffisante Avant que ce message s'affiche, la sortie de l'instrument est-elle passée de zéro à une alimentation totale ? Si la réponse est non, vérifier la pression d'alimentation de l'instrument en se référant aux caractéristiques données dans le manuel d'instructions de l'actionneur utilisé. Si la pression d'alimentation est correcte, vérifier les composants pneumatiques de l'instrument (convertisseur I/P et relais). Si la sortie de l'instrument n'est pas passée de zéro à l'alimentation totale avant la réception de ce message, vérifier le montage correct en consultant la procédure de montage appropriée dans la section Installation et en vérifiant l'alignement correct du faisceau de l'aimant. Le signal d'entraînement est supérieur à la limite basse ; vérifier la pression d'alimentation 1. Vérifier la pression d'alimentation (relais à action inversée) 2. Le frottement est trop élevé. Le signal d'entraînement est supérieur à la limite haute ; vérifier la pression d'alimentation 1. Vérifier la pression d'alimentation (relais à action directe) 2. Le frottement est trop élevé 40 Manuel d’instructions D103605X0FR Étalonnage avril 2021 Étalonnage manuel Deux procédures sont disponibles pour étalonner manuellement les courses : D Réglage analogique : cette procédure est utilisée lorsqu’il est possible de modifier manuellement la source de courant 4-20 mA pour déplacer la vanne. D Réglage analogique : cette procédure est utilisée lorsqu’il est possible modifier manuellement la source de courant 4-20 mA pour déplacer la vanne. Réglage de l’étalonnage analogique Connecter une source de courant variable aux bornes LOOP + et LOOP - de l’instrument. La source de courant doit être capable de générer 4 à 20 mA. Suivre les instructions apparaissant sur l’écran de l'interface de communication pour étalonner la course de l’instrument en pourcents. Remarque 0 % de course = vanne fermée 100 % de course = vanne ouverte 1. Régler le courant d'entrée de telle sorte que la vanne soit presque à mi-course. Appuyer sur OK. Remarque Les étapes 2 de 7 la précision du réglage de la source actuelle affecte la précision de la position. 2. 3. 4. 5. 6. 7. 8. Régler la source de courant jusqu’à ce que la vanne soit à 0 % de la course, puis appuyer sur OK. Régler la source de courant jusqu’à ce que la vanne soit à 100 % de la course, puis appuyer sur OK. Régler la source de courant jusqu’à ce que la vanne soit à 0 % de la course, puis appuyer sur OK. Régler la source de courant jusqu’à ce que la vanne soit à 100 % de la course, puis appuyer sur OK. Ajuster la source de courant jusqu’à ce que la vanne soit à 5 % de la course, puis appuyer sur OK. Ajuster la source de courant jusqu’à ce que la vanne soit à 95 % de la course, puis appuyer sur OK. Mettre l’instrument en service et vérifier que la course suit correctement la source de courant. Étalonnage numérique Connecter une source de courant variable aux bornes LOOP+ et LOOP- de l’instrument. La source de courant doit être configurée entre 4 et 20 mA. Suivre les invites apparaissant sur l’écran de l'interface de communication pour étalonner la course de l’instrument en pourcents. 1. Régler le courant d'entrée de telle sorte que la vanne soit presque à mi-course. Appuyer sur OK. Remarque Course à 0 % = vanne fermée course à 100 % = vanne ouverte 41 Étalonnage Manuel d’instructions avril 2021 D103605X0FR 2. Dans le menu de réglage, sélectionner le sens et la taille du changement requis pour régler la course à 0 %. La sélection des réglages grand, moyen et faible entraîne des variations d’environ 10,0 %, 1,0 %, et 0,1 %, respectivement. Si un autre réglage est nécessaire, répéter l’étape 2. Sinon, sélectionner « Terminé » et passer à l’étape 3. 3. Dans le menu de réglage, sélectionner le sens et la taille du changement requis pour régler la course à 100 %. Si un autre réglage est nécessaire, répéter l’étape 3. Sinon, sélectionner « Terminé » et passer à l’étape 4. 4. Dans le menu de réglage, sélectionner le sens et la taille du changement requis pour régler la course à 0 %. Si un autre réglage est nécessaire, répéter l’étape 4 Sinon, sélectionner « Terminé » et passer à l’étape 5. 5. Dans le menu de réglage, sélectionner le sens et la taille du changement requis pour régler la course à 100 %. Si un autre réglage est requis ; répéter l’étape 5 Sinon, sélectionner « Terminé » et passer à l’étape 6. 6. Dans le menu de réglage, sélectionner le sens et la taille du changement requis pour régler la course à 5 %. Si un autre réglage est requis ; répéter l’étape 6 Sinon, sélectionner « Terminé » et passer à l’étape 7. 7. Dans le menu de réglage, sélectionner le sens et la taille du changement requis pour régler la course à 95 %. Si un autre réglage est requis ; répéter l’étape 7 Sinon, sélectionner « Terminé » et passer à l’étape 8. 8. Mettre l’instrument en service et vérifier que la course suit correctement la source de courant. Étalonnage du bouton-poussoir Un bouton-poussoir est situé à proximité des bornes de câblage du boîtier à bornes et fournit un moyen rapide d’étalonner automatiquement l’instrument. Le bouton doit être enfoncé pendant 3 à 10 secondes. L’étalonnage automatique déplace la vanne sur toute la plage de course, que le mode de l’instrument soit en service ou hors service. Cependant, si le verrouillage en écriture est en mode Protégé, ce bouton ne sera pas actif. Pour abandonner, appuyer à nouveau sur le bouton pendant 1 seconde. Le bouton d’étalonnage est désactivé par défaut. Pour l’activer, se rendre dans Configuration manuelle > puis Instrument, > Bouton d’étalonnage. Remarque La plage de pression (utilisée pour la pression de secours) n’est pas réétalonnée au cours de cette procédure. Cette procédure d’étalonnage est recommandée à chaque fois que le convertisseur I/P ou le relais pneumatique est remplacé. Ne pas utiliser l’étalonnage du bouton-poussoir pour l’étalonnage initial lors du montage de l’instrument sur un actionneur ou si le circuit imprimé a été remplacé. Si il semble que l’étalonnage a changé en raison d’une dérive, effectuer d’abord un test de diagnostic de signature de vanne à l’aide du logiciel ValveLink pour enregistrer les­données trouvées pour l’analyse future de la cause profonde. 42 Manuel d’instructions Étalonnage D103605X0FR avril 2021 Étalonnage du capteur Capteurs de pression Remarque Le capteur de pression est étalonné en usine et ne nécessite pas d’étalonnage. Capteur de pression Pour étalonner le capteur de pression de sortie, raccorder un manomètre de référence externe à la sortie à étalonner. La jauge doitêtre capable de mesurer la pression d’alimentation maximale de l’instrument. En fonction selon le capteur à étalonner, sélectionner le capteur de sortie A ou le capteur de sortie B. Suivre les instructions apparaissant sur l’écran de l'interface de communication pour étalonner la course du capteur de pression de sortie de l’instrument. 1. Ajuster le régulateur de la pression d'alimentation sur la pression d'alimentation maximale de l'instrument. Appuyer sur OK. 2. L’instrument réduit la pression de sortie à 0. Le message suivant s’affiche. Sélectionner « Augmenter » et «Diminuer » jusqu'à ce que la pression affichée corresponde à la pression de sortie x. Appuyer sur OK après avoir lu le message. 3. La valeur de la pression de sortie apparaît à l’écran. Appuyer sur OK pour afficher le menu de réglage. 4. Dans le menu réglage, sélectionner la direction et l’ampleur du réglage à la valeur affichée. La sélection de grands, moyens et petits réglages provoque des variations d’environ 3,0 psi/0,207 bar/20,7 kPa, 0,30 PSI/ 0,0207 bar/2,07 kPa, et 0,03 PSI/0,00207 bar/0,207 kPa, respectivement. Si la valeur affichée ne correspond pas à la pression de sortie, appuyer sur OK, puis répéter cette étape (étape 4) pour ajuster la valeur affichée. Lorsque la valeur affichée correspond à la pression de sortie, sélectionner « Terminé » et passer à l’étape 5. 5. L’instrument règle la pression de sortie au niveau d’alimentation maximal. Le message suivant s’affiche. Sélectionner « Increase » et «Decrease » jusqu'à ce que la pression affichée corresponde à la pression de sortie x. Appuyer sur OK après avoir lu le message. 6. La valeur de la pression de sortie apparaît à l’écran. Appuyer sur OK pour afficher le menu de réglage. 7. Dans le menu réglage, sélectionner la direction et l’ampleur du réglage à la valeur affichée. Si la valeur affichée ne correspond pas à la pression de sortie, appuyer sur OK, puis répéter cette étape (étape 7) pour mieux ajuster la valeur affichée. Lorsque la valeur affichée correspond à la pression de sortie, sélectionner « Terminé » et passer à l’étape 8. 8. Mettre l’instrument en service et vérifier que la pression affichée correspond à la pression de sortie mesurée. 43 Manuel d’instructions Étalonnage avril 2021 D103605X0FR Capteur de pression d'alimentation Pour étalonner le capteur de pression d'alimentation, connecter une jauge de référence externe au côté sortie du régulateur d'alimentation. La jauge doit être capable de mesurer la pression d’alimentation maximale de l’instrument. Suivre les instructions sur l’interface de communication pour étalonner la pression d’alimentation de l’instrument. 1. Sélectionner a) Zéro uniquement ; ou b) Étendue de l'échelle et zéro (manomètre requis). a. Si le réglage « Zéro uniquement » est sélectionné, régler le régulateur de pression d’alimentation pour retirer la pression d’alimentation de l’instrument. Appuyer sur OK. Une fois l’étalonnage terminé, passer à l’étape 5. b. Si le réglage « Zéro uniquement » est sélectionné, régler le régulateur de pression d’alimentation pour retirer la pression d’alimentation de l’instrument. Appuyer sur OK. Ajuster le régulateur d’alimentation au maximum de la pression d’alimentation de l’instrument. Appuyer sur OK. Passer à l’étape 2. 2. Le message suivant s’affiche : Utiliser « Augmenter » et «Diminuer » jusqu'à ce que la pression affichée corresponde à la pression d'alimentation. Appuyer sur OK après avoir lu le message. 3. La valeur de la pression de sortie apparaît sur l’indicateur. 4. Dans le menu réglage, sélectionner la direction et l’ampleur du réglage à la valeur affichée. La sélection de grands, moyens et petits réglages provoque des variations d’environ 3,0 psi/0,207 bar/20,7 kPa, 0,30 PSI/0,0207 bar/2,07 kPa, et 0,03 PSI/0,00207 bar/0,207 kPa, respectivement. Ajuster les valeurs affichées jusqu’à ce qu’elles concordent avec la pression d’alimentation, sélectionner « Terminé » et passer à l’étape 5. 5. Mettre l’instrument en service et vérifier que la pression affichée correspond à la pression d’alimentation mesurée. Étalonnage de l’entrée analogique Pour calibrer le capteur d’entrée analogique, connecter une source de courant variable aux borne LOOP+ et LOOP- de l’instrument. La source de courant doit être capable de générer 4 à 20 mA. Suivre les instructions sur l’interface de communication pour étalonner l’entrée analogique de l’instrument. 1. Régler la source de courant sur la valeur cible affichée sur l’indicateur. La valeur cible correspond à la valeur basse de la plage d’entrée. Appuyer sur OK. 2. Le message suivant s’affiche : Utiliser « Augmenter » et «Diminuer » jusqu'à ce que le courant affiché corresponde au courant souhaité. 44 Manuel d’instructions Étalonnage D103605X0FR avril 2021 Appuyer sur OK après avoir lu le message. 3. La valeur de l’entrée analogique apparaît sur l’indicateur. Appuyer sur OK pour afficher le menu de réglage. 4. Dans le menu réglage, sélectionner la direction et l’ampleur du réglage à la valeur affichée. La sélection des réglages grand, moyen et faible entraîne des variations d’environ 0,4 mA, 0,04 mA, et 0,004 mA, respectivement. Si la valeur affichée ne correspond pas au courant source, appuyer sur OK, puis répéter cette étape (étape 4) pour mieux ajuster la valeur affichée. Lorsque la valeur affichée correspond au courant source, sélectionner « Terminé » et passer à l’étape 5. 5. Régler la source de courant sur la valeur cible affichée sur l’indicateur. La valeur cible correspond à la valeur haute de la plage d’entrée. Appuyer sur OK. 6. Le message suivant s’affiche : Utiliser « Augmenter » et « Diminuer » jusqu'à ce que le courant affiché corresponde au courant souhaité. Appuyer sur OK après avoir lu le message. 7. La valeur de l’entrée analogique apparaît sur l’indicateur. Appuyer sur OK pour afficher le menu de réglage. 8. Dans le menu réglage, sélectionner la direction et l’ampleur du réglage à la valeur affichée. Si la valeur affichée ne correspond pas au courant source, appuyer sur OK, puis répéter cette étape (étape 8) pour mieux ajuster la valeur affichée. Lorsque la valeur affichée correspond au courant source, sélectionner « Terminé » et passer à l’étape 9. 9. Mettre l’instrument en marche et vérifier que l’entrée analogique affichée correspond au courant source. Réglage du relais Avant de commencer l’étalonnage de la course, vérifier le réglage du relais. Remettre en place le couvercle du contrôleur numérique de vanne une fois l'opération terminée. Remarque Les relais B et C ne peuvent pas être réglés par l'utilisateur. Relais à double action Le relais à double action est nommé « relais A » sur une étiquette apposée sur le relais lui-même. Pour les actionneurs à double action, le réglage du relais ne peut s'effectuer correctement que si la vanne est proche de la mi-course. L'interface de communication positionne automatiquement la vanne lorsque « Régalge du relais » est sélectionné. Faire tourner le disque de réglage, illustré à la figure 4‐1, jusqu'à ce que la pression de sortie affichée sur l'interface de communication se trouve entre 50 et 70 % de la pression d'alimentation. Ce réglage est très sensible. Veiller à laisser les relevés de pression se stabiliser avant d'effectuer un autre réglage (la stabilisation peut prendre 30 secondes ou plus pour les grands actionneurs). Si l’option de relais à faible purge a été commandée, la stabilisation peut prendre environ deux minutes de plus que le relais standard. 45 Manuel d’instructions Étalonnage avril 2021 D103605X0FR Figure 4‐1. Réglage du relais A (protection retirée pour plus de clarté) POUR LES RELAIS DIRECTS À SIMPLE ACTION : TOURNER LE DISQUE DE RÉGLAGE DANS CE SENS JUSQU'A CE QU'IL ENTRE EN CONTACT AVEC LE FAISCEAU POUR LES RELAIS DIRECTS À DOUBLE ACTION TOURNER LE DISQUE DE RÉGLAGE DANS CE SENS POUR DIMINUER LA PRESSION DE SORTIE. DISQUE DE REGLAGE POUR LES RELAIS À DOUBLE ACTION : TOURNER LE DISQUE DE RÉGLAGE DANS CE SENS POUR AUGMENTER LA PRESSION DE SORTIE. W9034 Il est également possible de régler le relais A pour une utilisation dans des applications à mode d'action directe à simple action. Faire tourner le disque de réglage comme illustré à la figure 4‐1 pour obtenir un mode d’action directe à simple action. ATTENTION Faire preuve de précaution lors du réglage du relais car le disque de réglage peut se désengager s’il est trop tourné. Relais à simple action AVERTISSEMENT Pour les instruments de niveau ODV seulement : Si le port inutilisé est en train de surveiller la pression, s’assurer que la source de pression est conforme à la norme ISA7.0.01 et qu’elle ne dépasse pas la pression fournie à l’instrument. Le non-respect de cette consigne peut entraîner des blessures ou des dégâts matériels, dus à une perte de contrôle du procédé. Relais direct à simple action Le relais direct à double action est nommé « relais A » sur une étiquette apposée sur le relais lui-même. Le relais C ne requiert pas de réglage. Relais inverse à simple action Le relais inverse à double action est nommé « relais A » sur une étiquette apposée sur le relais lui-même. Le relais B est étalonné en usine et ne requiert pas de réglage supplémentaire. 46 Manuel d’instructions D103605X0FR Étalonnage avril 2021 Étalonnage PST (niveau d’instrumentation ODV uniquement) Cette procédure vous permet d’exécuter l’étalonnage de course partielle, ce qui permet de procéder au test de course partielle. Elle définit les valeurs pour la limite de pression de course partielle, le point de consigne de pression et la durée de saturation pour la régulation de la pression d’une extrémité, le point d’alerte de déviation de course et la durée de l’écart de course L’étalonnage de la course partielle définit également les valeurs par défaut pour les mouvements de course maximums, la vitesse du test et le temps de pause du test. Remarque Arrêter l’instrument avant de lancer l’étalonnage de course partielle. S’assurer que l’instrument est remis en marche après la procédure d’étalonnage. 47 Manuel d’instructions Informations sur l’appareil, alertes et diagnostics avril 2021 D103605X0FR Section 5 Informations de l’appareil, alertes, et diagnostics55 Remarque Les séquences d’accès rapide ne s’appliquent qu’à l’interface de communication 475. Elles ne s’appliquent pas à l’interface de communication Trex. Aperçu Interface de communication Aperçu (1) Variables à fonction principale et variables d’état La section vue d’ensemble fournit des informations de base sur l’état actuel de l’instrument et vous donne accès aux valeurs actuelles de : D D D D D D D D D l’état d’alerte, l’état de la communication, le mode de l’instrument (en/hors service), l’entrée analogique, le point de consigne, la course, la pression d’alimentation, les pressions de l’actionneur, la configuration de la régulation de la course/pression. Informations de l’appareil Les informations de l’appareil fournissent des détails sur la construction de l’instrument, notamment : D D D D D D D D le nom de repère, le numéro de série de l’instrument, le niveau de l’instrument (voir tableau 5‐1), le numéro d’immatriculation de l’appareil (numéro unique utilisé pour empêcher l’instrument d’accepter des commandes destinées à d’autres instruments), les numéros de série, les révisions du microprogramme, du DD et du matériel, la révision universelle HART, le verrouillage en écriture (fournit une procédure pour activer/désactiver l’instrumen). Tableau 5‐1. Fonctions disponibles selon le niveau de l’instrument Niveau de l instrument HC AD Inclut toutes les fonctions listées plus haut (avec le logiciel ValveLink), tous les tests de diagnostic hors ligne (bande d’ dynamique, signal du variateur, réponse d’étape et signature de vanne) ainsi que les tendances en ligne PD Inclut toutes les fonctions indiquées ci-dessus ainsi que tous les diagnostics de performances en ligne / dans les tests de vanne de service (frottement de la vanne, éléments électroniques et condition mécanique) ODV 48 Fonctions disponibles Communique avec l’interface de communication et le logiciel ValveLink. De plus, HC dispose de : coupures et limites de course, durées d’ouverture et de fermeture minimales, caractérisation d’entrée (linéaire, pourcentage égal, ouverture rapide et personnaliser), tendances avec ValveLink Solo, et les alertes suivantes : déviation de course ; alerte de course haute, basse, haute haute et basse basse ; signal d’excitation ; compteur de cycles ; et l’accumulation de courses. Inclut toutes les fonctions indiquées ci-dessus, le test de course partielle ainsi que le filtre avance/retard du point de consigne Manuel d’instructions Informations sur l’appareil, alertes et diagnostics D103605X012 avril 2021 Outils de maintenance Interface de communication Outils d’application (3) État de l'appareil Lorsqu'elles sont activées, les alertes de l’instrument permettent de détecter une grande variété de problèmes de fonctionnement et de performances susceptibles de présenter un intérêt. Si aucune alerte n’est actuellement enclenchée, rien ne sera affiché. Registre des alertes Le DVC6200 peut enregistrer 20 alertes. Lorsque le registre des alertes est plein, aucune alerte supplémentaire n’est stockée tant que l’enregistrement n’est pas supprimé. Rapport d’alertes Outre les alertes de stockage embarquées, le DVC6200 peut signaler des alertes actives via la « Commande HART n° 48 - Lire l’état additionnel ». Voir le tableau 5‐2 pour un résumé des paramètres d’alerte d’usine. Ci-après une description détaillée de la signification de chaque alerte. Tableau 5‐2. Paramètres d’alerte par défaut Nom Alerte Arrêt Catégorie NE107 Défaillance de l’intégrité de la mémoire flash Activé(1) Désactivé Défaillance Défaillance de la boucle d’induction électromagnétique Activé(1) Désactivé Défaillance Défaillance de la tension de référence Activé(1) Désactivé Défaillance Défaillance du courant d’entraînement Activé(1) Désactivé Défaillance Défaillance critique NVM (mémoire non volatile) Activé(1) Désactivé Défaillance Panne du capteur de température Activé(1) Désactivé Défaillance Défaillance du capteur de pressions Activé(1) Désactivé Défaillance Défaillance du capteur de course Activé(1) Désactivé Défaillance Registre des alertes non vide Désactivé Non disponible Maintenance Étalonnage en cours Désactivé Non disponible Contrôle des fonctions Diagnostics en cours Désactivé Non disponible Contrôle des fonctions Pression de secours activée Activé Non disponible Hors caractéristiques Étalonnage automatique en cours Désactivé Non disponible Contrôle des fonctions NVM non critique Activé(1) Désactivé Défaillance Compteur de cycles élevés Désactivé Non disponible Maintenance Accumulateur de course haut Désactivé Non disponible Maintenance L’heure de l’instrument est approximative Désactivé Non disponible Non disponible Registre des alertes plein Désactivé Non disponible Maintenance Hors ligne / échec Activé Non disponible Défaillance Données de diagnostic accessibles Désactivé Non disponible Non disponible Pression d’alimentation basse Activé Non disponible Hors caractéristiques Déviation de la pression d’une extrémité Activé Non disponible Hors caractéristiques Pression d’alimentation haute Activé Non disponible Maintenance 1. Ces configurations d’alertes par défaut ne peuvent pas être modifiées. -suite- 49 Manuel d’instructions Informations sur l’appareil, alertes et diagnostics avril 2021 D103605X0FR Tableau 5‐2. Paramètres d’alerte par défaut (suite) Nom Alerte Arrêt Catégorie NE107 Intégrateur à saturation élevée Désactivé Non disponible Hors caractéristiques Intégrateur à faible saturation Désactivé Non disponible Hors caractéristiques Alerte de course Low Désactivé Non disponible Non disponible Alerte de course basse basse Désactivé Non disponible Non disponible Alerte de course haute Désactivé Non disponible Non disponible Alerte de course haute haute Désactivé Non disponible Non disponible Déviation de course Activé Non disponible Hors caractéristiques Limite/coupure de course haute Désactivé Non disponible Non disponible Limite/coupure de course basse Désactivé Non disponible Non disponible Alerte du signal d'entraînement Activé Non disponible Hors caractéristiques Erreur du circuit de sortie Activé Non disponible Défaillance Orifice A surpressurisé Activé Désactivé Défaillance « Registre des alertes plein » apparaît lorsque le registre d’alerte est plein. Les alertes supplémentaires détectées ne seront pas enregistrées dans le registre d’alertes tant que le registre des alertes n’aura pas été supprimé. « Registre des alertes non vide » apparaît lorsqu’une ou plusieurs alertes sont enregistrées dans le registre des alertes. « Étalonnage automatique en cours » apparaît lorsque l’étalonnage automatique est en cours. « Étalonnage en cours » apparaît lorsque l’étalonnage est en cours. « Défaillance de la NVM » apparaît en cas de panne liée à la NVM qui est essentielle au fonctionnement de l’instrument. Pour effacer l'alerte, redémarrer l'instrument. Si l'alerte ne s'efface pas après le redémarrage, remplacer le circuit imprimé. « Compteur de cycles élevé » apparaît si le compteur de cycles excède le point d’alerte du compteur de cycles. Le compteur de cycles enregistre le nombre de changements de course lorsqu’elle est en dehors de la bande morte. Pour effacer l’alerte, régler le compteur de cycles sur une valeur inférieure au point d’alerte. Voir la figure 5‐2. « Données de diagnostic disponibles » apparaît lorsque les données de diagnostic ont été recueillies et sont stockées dans l’instrument. « Diagnostics en cours » apparaît lorsqu’un test de diagnostic est en cours. « Défaillance du courant d’entraînement » apparaît lorsque le courant le courant d’entraînement du convertisseur I/P ne s’écoule pas comme prévu. Si cette alerte se déclenche, vérifier le raccordement entre le convertisseur I/P et le circuit imprimé. Essayer de retirer le convertisseur I/P et de le réinstaller. Si l'alerte ne s'efface pas, remplacer le convertisseur I/P ou la plaquette de circuit imprimé équipée. « Alerte du signal d’entraînement » surveille le signal d’entraînement et la course étalonnée. Si l’une des conditions suivantes est présente pendant plus de 20 secondes, l’alerte est activée. Dans le cas où la condition d’alimentation nulle est définie comme « fermée » : Signal d’entraînement < 10 % et course calibrée > 3 % Signal d’entraînement > 90 % et course calibrée < 97 % Dans le cas où la condition d’alimentation nulle est définie comme « ouverte » : Signal d’entraînement < 10 % et course calibrée < 97 % Signal d’entraînement > 90 % et course calibrée > 3 % 50 Manuel d’instructions Informations sur l’appareil, alertes et diagnostics D103605X012 avril 2021 « Déviation de pression d’une extrémité » apparaît si l’instrument est en mode régulation de la pression et que la pression ne suit pas le point de consigne compris dans l’allocation de déviation configurée. « Dysfonctionnement de l’appareil de terrain » apparaît si les capteurs de pression, de position et les capteurs de température fournissent des valeurs non valides. « Défaillance de l’intégrité de la mémoire flash » apparaît en cas de panne associée à la mémoire flash (lecture seule). Pour effacer l'alerte, redémarrer l'instrument. Si l'alerte ne s'efface pas après le redémarrage, remplacer le circuit imprimé. « Heure de l’instrument approximative » apparaît si l'instrument a été mis hors tension depuis la dernière fois que l'horloge de l'instrument a été réglée. Pour effacer l'alerte, essayer de redémarrer l'instrument. « Intégrateur à saturation élevée » apparaît si l’intégrateur de l’instrument est saturé à extrémité supérieure. « Intégrateur à faible saturation » apparaît si l’intégrateur de l’instrument est saturé à l’extrémité inférieure. « Capteur interne hors limites » apparaît en cas de problème avec le capteur de pression ou le circuit imprimé. « Alerte de validation du courant de boucle » apparaît si le courant de boucle est largement hors limites ou en cas de problème avec l’électronique du circuit analogique. Pour effacer l’alerte, redémarrer l’instrument avec le courant de boucle vérifié pour être dans la plage de 4-20 mA. Si l'alerte ne s'efface pas après le redémarrage, remplacer le circuit imprimé. Remarque Si le système de contrôle-commande est connu pour un courant de sortie de 24 mA ou plus, l’arrêt sur la validation de courant de boucle ne doit pas être activé. « Défaillance du capteur de boucle mineure » apparaît si la mesure de la position du relai pneumatique est en dehors de la plage valide. Si l'alerte ne s'efface pas après le redémarrage, remplacer le circuit imprimé. « NVM non critique » apparaît s’il y a une défaillance associée à la NVM (mémoire non volatile) qui n’est pas critique pour le fonctionnement de l’instrument. Pour effacer l'alerte, redémarrer l'instrument. Si l'alerte ne s'efface pas après le redémarrage, remplacer le circuit imprimé. « Hors ligne/défaillant » apparaît si une alerte d’arrêt met l’appareil en état d’échec et qu’il ne contrôle plus de ce fait l’entrée. Examiner les alertes à l’origine de l’arrêt. « Erreur du circuit de sortie » apparaît si le circuit de sortie ne répond pas. Vérifier que le commutateur DIP sur les composants électroniques principaux correspond à la configuration des bornes de sortie. Si le réglage de l’interrupteur DIP est correct et que l’alerte est toujours enclenchée, remplacer les composants électroniques principaux. « Orifice A surpressurisé » implique à la fois que « Alerte de surpression de l’orifice A » et que « Limite de pression de sortie de l’orifice A » apparaîssent et cela ne concerne que les applications directes à simple action. L’alerte est enclenchée si la pression de sortie de l’orifice A du DVC6200 dépasse le réglage de la limite de pression configurée. Vérifier que le régulateur de pression d’alimentation n’est pas endommagé et vérifier son point de consigne de pression. « Pression de secours activée » apparaît lorsque l’instrument a détecté un problème avec le retour de course et se met à réguler la sortie comme un transducteur I/P. « Défaillance du capteur de pression » apparaît si l’une des 3 mesures du capteur de pression (sortie A, sortie B, alimentation) est en dehors de la plage de 24,0 à 125,0 % de la pression étalonnée pendant plus de 60 secondes. Si cette alerte est enclenchée, vérifier la pression d’alimentation de l’instrument, s’assurer que le circuit imprimé est correctement monté sur la base du module s’assurer que le joint torique du capteur de pression est correctement installé. Si l'alerte ne s'efface pas après le redémarrage, remplacer le circuit imprimé. 51 Informations sur l’appareil, alertes et diagnostics Manuel d’instructions avril 2021 D103605X0FR « Défaillance de la tension de référence » apparaît en cas de défaillance associée à la tension interne de référence. Si l'alerte persiste après le redémarrage, remplacer le circuit imprimé. « Pression d’alimentation élevée » apparaît si la pression d’alimentation passe au-dessus du point d’alerte haut de la pression d’alimentation. « Pression d’alimentation faible » apparaît si la pression d’alimentation passe en dessous du point d’alerte bas de la pression d’alimentation. « Défaillance du capteur de température » lorsque le capteur de température de l’instrument dysfonctionne, ou si la valeur lue par le capteur est en-dehors de l’intervalle borné par les valeurs -60 et 100 °C (-76 to 212 °F). La valeur de température lue est utilisée en interne pour la compensation de température des entrées. Si cette alerte est enclenchée, redémarrer l’instrument. Si l'alerte ne s'efface pas après le redémarrage, remplacer le circuit imprimé. « Accumulateur de course haut » apparaît si l’accumulateur de course excède le point d’alerte de l’accumulateur de course. L’accumulateur de course comptabilise la course de la vanne lorsque la bande morte est dépassée. Pour effacer l’alerte, régler le compteur de cycles sur une valeur inférieure au point d’alerte. Voir la figure 5‐2. « Alerte de course haute » apparaît lorsque la course dépasse le point haut de l’alerte de course. Une fois l’alerte activée, l’alerte s’efface lorsque la course passe en dessous du point haut de l’alerte de course, moins la bande morte de l’alerte de course. Voir la figure 5‐1. Remarque Les points d’alerte de course haute haute et d’alerte de course basse basse servent à calculer la durée de la course dans le cas d’une demande. Les valeurs sont généralement réglées sur 99 % et 1 % respectivement, cependant, il n’est pas nécessaire d’activer l’alerte. La durée de course peut être lue à partir de l’appareil à l’aide du logiciel ValveLink. « Alerte de course haute haute » apparaît lorsque la course dépasse le point haut haut de l’alerte de course. Une fois l’alerte activée, l’alerte s’efface lorsque la course passe en dessous du point haut haut de l’alerte de course, moins la bande morte de l’alerte de course. Voir la figure 5‐1. « Alerte de course basse » apparaît lorsque la course est en dessous du point bas de l’alerte de course. Une fois l’alerte activée, l’alerte s’efface lorsque la course passe au-dessus du point Lo de l’alerte de course, plus la bande morte de l’alerte de course. Voir la figure 5‐1. « Alerte de course basse basse » apparaît lorsque la course est en dessous du point bas de l’alerte de course. Une fois l’alerte activée, l’alerte s’efface lorsque la course passe au-dessus du point bas de l’alerte de course, plus la bande morte de l’alerte de course. Voir la figure 5‐1. « Limite/Coupure de course haute » apparaît lorsque la course dépasse le seuil de coupure/limite haut. « Limite/Coupure de course basse » apparaît lorsque la course passe en-dessous du seuil de coupure/limite bas. « Déviation de la course » : si la différence entre la cible de course et la course réelle excède le point d’alerte de déviation de course pendant une durée supérieure à celle de la déviation de course, l’alerte de déviation de course est activée. Elle reste enclenchée jusqu’à ce que la différence entre la cible de la course et la course soit inférieure au point d’alerte de déviation de course moins la bande morte de l’alerte de course. Voir la figure 5‐1. « Défaillance du capteur de course » apparaît si la course détectée est en dehors de la plage de 25,0 à 125,0 % de la course étalonnée. Si cette alerte est enclenchée, vérifier le montage de l’instrument. Par ailleurs, vérifier aussi que la connexion électrique du capteur de course est correctement branchée sur le circuit imprimé. Si l'alerte ne s'efface pas après le redémarrage, remplacer le circuit imprimé ou le capteur de course. « Variable hors limites » apparaît si une ou plusieurs des mesures du capteur analogique mesurées (courant de boucle, pression, température ou course) sont saturées ou relevées de la plage configurée. Cela est peut-être dû à une configuration incorrecte ou à la configuration physique, et non à un dysfonctionnement du capteur. Principe de fonctionnement de la bande morte Le bande morte est le pourcentage (%) de déplacement par rapport à un point de référence de course où aucune modification de l’état d’alerte ne se produira. Ceci empêche l’alerte d’activer ou de désactiver le fonctionnement à proximité du point d’alerte. 52 Manuel d’instructions Informations sur l’appareil, alertes et diagnostics D103605X012 avril 2021 Le bande morte d’alerte de course s’applique à l’alerte déviation de course, ainsi qu’aux alertes de course haute, basse, haute haute et basse basse. La figure 5‐1 illustre le principe de la configuration et de l’effacement d’une alerte de course haute. L’alerte est activée lorsque la course dépasse le point d’alerte et est effacée lorsqu’elle passe en dessous de la bande morte. Figure 5‐1. Bande morte d’alerte de course POSITION DE VANNE L’ALERTE EST ACTIVÉE POINT ÉLEVÉ D’ALERTE DE COURSE BANDE MORTE D’ALERTE DE COURSE ALERTE DÉSACTIVÉE DURÉE A6532 Le compteur de cycles et la bande morte de l’accumulateur de course s’appliquent à la fois à l’alerte élevée du compteur de cycle et à l’alerte élevée de l’accumulateur de course. Le bande morte établit une zone à travers un point de référence de course. Le point de référence de la course est rétabli au point d'inversion de la course qui se produit en dehors de la bande morte. La bande morte doit être dépassée avant qu’un changement du sens de la course ne soit compté comme un cycle et que la course accumulée (jusqu’au point de contrepassation de la course) soit ajoutée à l’accumulation totale. Voir la figure 5‐2. Figure 5‐2. Exemple de compteur de cycles et de bande morte de l’accumulateur de course (réglé à 10 %) POINT DE RÉFÉRENCE EN BANDE MORTE POSITION DE LA VANNE BANDE MORTE DÉPASSÉE, NOUVEAU POINT DE RÉFÉRENCE ÉTABLI BANDE MORTE (+/- 5 %) DURÉE BANDE MORTE LES SEGMENTS FONCÉS REPRÉSENTENT LA QUANTITÉ DE COURSE QUI SERA AJOUTÉE À L’ACCUMULATEUR DE COURSE E1473 INCRÉMENTS DU COMPTEUR DE CYCLES 53 Informations sur l’appareil, alertes et diagnostics Manuel d’instructions avril 2021 D103605X0FR Diagnostics Vanne de course Suivre les instructions qui apparaissent sur l'indicateur de l'interface de communication : D « Terminé » : sélectionner cette option à la fin. Toute accélération est arrêtée lorsque « Terminé » est sélectionné. D « Accélération vers l’ouverture » : accélère la course vers l’ouverture à une vitesse de 1,0 % par seconde de la course parcourue. D « Accélération vers la fermeture » : accélère la course vers la fermeture à une vitesse de 1,0 % par seconde de la course parcourue. D « Accélération vers la cible » : accélère la course vers la cible spécifiée à une vitesse de 1,0 % par seconde de la course parcourue. D « Étape jusqu’à la cible » : fait passer la course à la cible spécifiée. Test de course partielle Remarque Test de course partielle est seulement disponible pour les instruments de niveau ODV. Le test de course partielle permet au contrôleur numérique de vanne DVC6200 d’effectuer un test de type « signature de vanne » alors même que l’instrument est en service et en fonctionnement. Dans certaines applications, il est important de pouvoir tester la vanne pour vérifier qu’elle fonctionne correctement lorsqu’elle est sollicitée. Cette fonction permet à l’utilisateur de déplacer partiellement la vanne tout en continuant à surveiller le signal d’entrée. Si une demande se produit, le test est interrompu et la vanne se déplace sur sa position commandée. La course de la vanne de course partielle peut être configurée entre 1 et 30 % de la course maximale, par incréments de 0,1 %. Les données recueillies lors du précédent test de course partielle sont enregistrées dans la mémoire de l’instrument pour pouvoir être récupérées par le logiciel AMS ValveLink. Le test de course partielle permet d’effectuer un test de course partielle, de 10 %, d’inversion (standard) ou d’un test de course personnalisé. Dans le cadre du test de course personnalisé, la course peut atteindre jusqu’à 30 %. Vérifier les mesures de vérification spécifiques au site avant d’effectuer un test de course personnalisé. Ce test a pour objectif de s’assurer que la vanne se déplace à la demande. Le test de course partielle peut être effectué lorsque la vanne fonctionne à 4 ou 20 mA (mode point-à-point). Lorsqu’il est activé, le test de course partielle peut être lancé par le dispositif lui-même (test de course partielle automatique planifié), à l’aide d’un bouton-poussoir distant situé sur le site ou au niveau de la vanne, par le biais de l’interface de communication ou du logiciel ValveLink. Pour plus d’informations sur la configuration du test de course partielle se reporter à la section « Partial Stroke Variables » (variables partielles de course) dans la section « Detailed Setup » (configuration avancée). D Automatique (planifié) Le test de course partielle automatique permet au test de course partielle d’être programmé par le DVC6200. La programmation consiste à prévoir le nombre d’heures entre chaque test. Chaque redémarrage réinitialise la minuterie de l'horloge de test. D Bouton-poussoir local Une commande de test de course partielle peut être envoyée au contrôleur numérique de vanne à l’aide de contacts raccordées aux bornes auxiliaires +/-. Pour effectuer un test, les contacts doivent être fermés 3 à 5 secondes puis ouverts. Pour interrompre le 54 Manuel d’instructions Informations sur l’appareil, alertes et diagnostics D103605X012 avril 2021 test, fermer les contacts pendant 1 seconde. Les dernières données de diagnostic sont enregistrées dans la mémoire de l’instrument pour pouvoir être récupérées plus tard à l’aide du logiciel ValveLink. D Interface de communication 1. Raccorder l’interface de communication aux bornes LOOP sur le contrôleur numérique de vanne. 2. Mettre l’interface de communication en marche. 3. Dans le menu « En ligne », sélectionner Outils de maintenance > Diagnostics > Test de course partielle. 4. Sélectionner « Standard (10 %) » ou « Personnaliser ». En cas de test de course personnalisé, la course peut atteindre jusqu’à 30 % et sa vitesse et le temps d’arrêt peuvent être réglés. 5. La course, la vitesse de course et le temps d’arrêt tel que définis actuellement s’affichent. Sélectionner « Oui » pour effectuer le test avec ces valeurs. Sélectionner « Non » pour modifier ces valeurs. La valeur par défaut pour la vitesse de course est de 0,25%/seconde. 6. La vanne commence à se déplacer et la course réelle détectée par le contrôleur numérique de vanne s’affiche sur l’interface de communication. 7. Une fois que la vanne a atteint l’extrémité, vérifier que la vanne a atteint le point de consigne souhaité. La vanne doit revenir à sa position d’origine. D Logiciel ValveLink Exécuter le diagnostic de course partielle. Surveillance de l’état de l’électrovanne La surveillance de l’état des électrovannes nécessite la configuration suivante : D Actionneur à simple action D L’électrovanne installée entre la sortie de pression DVC6200 et l’actionneur D Orifice de pression de sortie non utilisé du DVC6200 connecté entre le solénoïde et l’actionneur, à proximité de l’actionneur D Relais configuré en tant qu’« application spéciale » D Le profil déclenché a été activé et l’événement de déclenchement « Différentiel de pression » est sélectionné. Si l’électrovanne est directement raccordée au solveur logique, il est possible d’utiliser les étapes suivantes pour tester le robinet électromagnétique. 1. Interrompre momentanément l’alimentation de l’électrovanne à l’aide du solveur logique (généralement de 100 à 200millisecondes). La durée de l’interruption doit être suffisamment courte pour que la course de la vanne de sécurité ne bouge pas, mais suffisamment longue pour qu’une chute de pression au niveau de l’électrovanne soit détectée. 2. Correctement configurée, la collecte de données se déclenche automatiquement et celles-ci seront stockées dans le DVC6200. 3. Avec le logiciel ValveLink, télécharger les données de diagnostic à partir du menu de profil déclenché. 4. Examiner le graphique et observer qu’il y a eu un changement dans la mesure de la pression en aval du solénoïde. 55 Informations sur l’appareil, alertes et diagnostics avril 2021 Manuel d’instructions D103605X0FR Variables Interface de communication Outils de maintenance > Variables (3-4) La section Variables fournit les valeurs du moment présent des variables de l’instrument. La liste des variables visualisables est la suivante : D le verrouillage en écriture (fournit une procédure pour activer/désactiver), D le mode de l’instrument (fournit également une procédure de mise en service), D l’entrée analogique, D le point de consigne, D la course, D le signal d’entraînement, D la caractérisation des entrées (fournit également une procédure de modification), D le compteur de cycles, D l’accumulateur de course, D la pression d’alimentation, D les pressions de l’actionneur, D la configuration de la commande de course/contrôle de pression (fournit également une procédure de modification), D le mode contrôle (fournit également une procédure de modification), D la température de l’instrument, D les décomptes de déplacements (il s’agit de la lecture du capteur de course brute utilisée pour les réglages avancés), D la température maximale enregistrée, D la température minimale enregistrée, D le nombre de mises sous tension, D les jours de mise sous tension. 56 Manuel d’instructions Maintenance et dépannage D103605X0FR avril 2021 Section 6 Maintenance et dépannage66 Le boîtier du contrôleur numérique de vanne DVC6200 est de type 4X et IP66, il n’est donc pas nécessaire de nettoyer régulièrement les composants internes. Si le DVC6200 est installé dans une zone où les surfaces extérieures ont tendance à être fortement recouvertes ou saliess à cause des contaminants industriels ou atmosphériques, il est recommandé que l’évent (item52) soit régulièrement retiré et inspecté pour s’assurer qu’il n’y a pas d’obstruction partielle ou totale. Si l’évent semble partiellement ou complètement obstrué, il doit être nettoyé ou remplacé. Polir légèrement l’extérieur de l’évent pour éliminer les contaminants et faire couler une solution eau/détergent peu concentrée dans l’évent pour s’assurer qu’il n’y a pas d’obstruction. Laisser sécher l’évent avant de le réinstaller. AVERTISSEMENT La défaillance par surpression du couvercle peut entraîner des blessures ou des dommages matériels. Vérifier que l’ouverture d’évent du boîtier est ouverte et exempte de débris afin d’éviter une montée en pression sous le couvercle. AVERTISSEMENT Pour éviter une décharge statique provenant du couvercle en plastique en présence de gaz ou de poussières inflammables, ne pas frotter ou nettoyer le couvercle avec des solvants. Ceci pourrait provoquer une explosion et entraîner des blessures et des dommages matériels. Nettoyer uniquement avec un détergent doux et de l'eau. AVERTISSEMENT Éviter toute blessure ou tout dommage matériel résultant d’une fuite soudaine de fluide sous pression ou de l’éclatement de pièces. Avant d’effectuer toute procédure de maintenance sur le contrôleur numérique de vanne DVC6200 : D Toujours porter des gants, des vêtements et des lunettes de protection pour éviter de se blesser. D Ne pas retirer l’actionneur de la vanne tant que celle-ci est sous pression. D Débrancher toutes les conduites alimentant l’actionneur en pression d’air, en électricité ou en signal de commande. S’assurer que l’actionneur ne peut ni ouvrir ni fermer soudainement la vanne. D Utiliser des vannes de dérivation ou fermer complètement le procédé pour isoler la vanne de la pression du procédé. Dissiper la pression du procédé des deux côtés de la vanne. D Utiliser des méthodes de verrouillage pour être certain que les mesures précédentes restent effectives lors du travail sur l’équipement. D Consulter votre ingénieur des procédés de fabrication ou votre ingénieur en sécurité pour connaître les éventuelles mesures supplémentaires à prendre afin de se protéger contre les fluides du procédé. D Purger la pression de charge de l'actionneur pneumatique et dissiper toute pré-compression du ressort de l'actionneur de sorte que ce dernier n'applique aucune force sur la tige de vanne et ce, pour permettre le retrait en toute sécurité du connecteur de tige. AVERTISSEMENT Lors de l’utilisation de gaz naturel comme gaz d’alimentation, ou pour des applications antidéflagrantes, les avertissements suivants s’appliquent également : D Couper l’alimentation électrique avant de retirer le couvercle du boîtier. Un incendie ou une explosion pouvant entraîner des blessures et des dommages matériels peuvent survenir si l’alimentation électrique n’est pas coupée avant le retrait du couvercle. D Couper l’alimentation électrique avant de débrancher tout raccord pneumatique. 57 Manuel d’instructions Maintenance et dépannage avril 2021 D103605X0FR D Lors du débranchement d’un raccord pneumatique ou d’une pièce sous pression, du gaz naturel se dégage de l’unité et de tout équipement connecté dans l’atmosphère environnante. Des blessures et des dommages matériels peuvent résulter d’un incendie ou d’une explosion si du gaz naturel est utilisé comme produit d’alimentation et si les mesures de prévention appropriées ne sont pas prises. Les mesures préventives nécessaires peuvent comprendre, notamment, l’un des éléments suivants : assurance d’une ventilation adéquate et élimination de toute source d’inflammation D S’assurer que le couvercle est installé correctement avant de remettre l’appareil en service. Le non-respect de cette consigne risque d’entraîner des blessures et des dommages matériels par incendie ou explosion. ATTENTION Lors du remplacement de composants, n’utiliser que des composants spécifiés par le fabricant. Toujours employer les techniques adéquates de remplacement des composants, comme indiqué dans ce manuel. Le choix de techniques ou de composants incorrects peut invalider les certifications et les caractéristiques du produit, comme indiqué dans le tableau 1‐2 et peut aussi altérer le fonctionnement et les fonctions prévues de l’appareil. Grâce à la capacité de diagnostic de l’DVC6200, la maintenance prédictive est disponible grâce à l’utilisation du logiciel ValveLink. En utilisant le contrôleur numérique de vanne, la maintenance de la vanne et de l’instrument peut être améliorée, évitant ainsi une maintenance inutile. Pour plus d’informations sur l’utilisation du logiciel ValveLink, se rendre sur l’assistance en ligne du logiciel ValveLink. Démontage de l’aimant de contre-réaction Pour démonter l’aimant de la tige de l’actionneur, procéder comme suit : 1. S’assurer que la vanne est isolée du procédé. 2. Retirer le couvercle du boîtier à bornes de l’instrument. 3. Déconnecter les câbles du tableau de bornes sur le site. 4. Couper l’alimentation d’air de l’instrument. 5. Déconnecter les lignes d’impulsion pneumatiques et retirer le DVC6200 ou le DVC6215 de l’actionneur. 6. Retirer les vis maintenant l’aimant au bras de connexion. Lors du remplacement de l’instrument, veiller à suivre les instructions de montage dans le Guide de démarrage rapide (D103556X012) livré avec le contrôleur numérique de vanne. Configurer et étalonner l’instrument avant de le remettre en marche. Maintenance de la base du module La base du module contient les sous-modules suivants : convertisseur I/P, un circuit imprimé et un relai pneumatique. La base du module peut être facilement remplacée sur le terrain sans déconnecter le câblage ou les lignes d’impulsion de terrain. Outils requis Le tableau 6‐1 indique les outils nécessaires à la maintenance du contrôleur numérique de vanne DVC6200. Tableau 6‐1. Outils requis Outil Tournevis Phillips Clé hexagonale Clé hexagonale Clé hexagonale Clé hexagonale 58 Dimension 5 mm 1,5 mm 2,5 mm 6 mm Composant Relais, circuit imprimé et vis de couvercle Vis de la boîte à bornes Vis du couvercle du boîtier à bornes Vis du convertisseur I/P Vis de la base du module Manuel d’instructions Maintenance et dépannage D103605X0FR avril 2021 Remplacement de composant Lors du remplacement d’un des composants du DVC6200, la maintenance doit, si possible, être effectuée dans un atelier spécialisé. Veiller à ce que le câblage électrique et lignes d’impulsion pneumatiques soient débranchés avant de démonter l’instrument. Démontage de la base du module Voir la figure 7‐2 ou 7‐4 pour l’emplacement des items numérotés. AVERTISSEMENT Pour éviter des blessures ou des dégâts matériels dus à l’éclatement de pièces, couper la pression d’alimentation vers le contrôleur numérique de vanne et purger toute pression d’alimentation excédentaire avant de tenter de retirer la base du module du boîtier. 1. Dévisser les quatre vis imperdables du couvercle (item 43) et retirer le couvercle de la base du module (item 2). 2. À l’aide d’une clé à douille hexagonale de 6 mm, desserrer les trois vis à tête de douille (item 38). Ces vis sont maintenues dans la base du module par des anneaux de retenue (item 154). Remarque La base du module est reliée au boîtier par deux ensembles de câbles. Déconnecter ces ensembles de câbles après avoir tiré la base du module du boîtier. 3. Tirer la base du module directement hors du boîtier (item 1). Une fois le boîtier dégagé, basculer la base du module sur le côté du boîtier pour accéder aux assemblages de câbles. 4. Le contrôleur numérique de vanne / l’unité de base est doté de deux câbles, illustrés dans la figure 6‐1 qui connectent la base du module au capteur de course et au boîtier à bornes par le circuit imprimé. Déconnecter ces ensembles de câbles du circuit imprimé situé à l’arrière de la base du module. Figure 6‐1. Raccordements de câbles sur le circuit imprimé BASE DU MODULE CIRCUIT IMPRIMÉ BOÎTIER À BORNES W9924-1_n° étiquette BOÎTIER CÂBLE VERS LE BOÎTIER À BORNES CÂBLE VERS LE CAPTEUR DE COURSE 59 Maintenance et dépannage Manuel d’instructions avril 2021 D103605X0FR Remplacement de la base du module Voir la figure 7‐2 ou 7‐4 pour l’emplacement des items numérotés. ATTENTION Pour éviter d’affecter les performances de l’instrument, veiller à ne pas endommager le joint d’étanchéité du module ou la surface de guidage. Ne pas heurter ou endommager les broches des connecteurs nues situées sur le circuit imprimé. L’endommagement de la base du module ou de la surface de guidage peut entraîner des dommages matériels, ce qui peut affecter l’étanchéité de l’instrument. Remarque Pour éviter d’affecter les performances de l’instrument, inspecter la surface du guide sur le module et la zone d’appui correspondante dans le boîtier avant d’installer la base du module. Ces surfaces doivent être exemptes de poussières, de saletés, de rayures et de contamination. S’assurer que le joint de la base du module est en bon état. Ne pas réutiliser un joint endommagé ou usé. 1. S’assurer que le joint de la base du module (item 237) est correctement installé dans le boîtier (item 1). S’assurer que le joint torique (item 12) est en place sur la base du module. 2. Raccorder le capteur de course et les câbles du boîtier à bornes au circuit imprimé (item 50). L’orientation du connecteur est requise. 3. Insérer la base du module (item 2) dans le boîtier (item 1). Remarque Pour les contrôleurs numériques de vanne en acier inoxydable, la pose d’un produit d’étanchéité est recommandé sur le filetage de la tuyauterie (item 64) sous la tête des trois vis à tête creuse (item 38) avant de fixer la base du module au boîtier lors de l’étape suivante. 4. Placer les trois vis à tête creuse (item 38) dans la base du module du boîtier. Si ce n’est pas déjà fait, enfoncer trois anneaux de retenue (item 154) dans la base du module. Serrer uniformément les vis en croisant le serrage avec un couple final de 16 NSm (138 lbfSin). AVERTISSEMENT Des blessures, des dommages matériels ou une perturbation du contrôle du procédé peuvent se produire si les assemblages de câbles/câblage sont endommagés lors de la fixation du couvercle sur l’ensemble du module S’assurer que les assemblages de câbles/câblage sont positionnés dans la cavité de la base du module de sorte qu’ils ne soient pas compressés ou endommagés lors de la fixation du couvercle à la base du module à l’étape 5. 5. Fixer le couvercle (item 43) sur la base du module. 60 Manuel d’instructions Maintenance et dépannage D103605X0FR avril 2021 Maintenance du sous-module La base du module du DVC6200 contient les sous-modules suivants : un convertisseur I/P, un circuit imprimé et un relai pneumatique. Si des problèmes surviennent, ces sous-modules peuvent être retirés de la base du module et remplacés par de nouveaux sous-modules. Après avoir remplacé un sous-module, la base du module peut être remise en service. ATTENTION Faites preuve de prudence lors de la maintenance de la base du module. Réinstaller le couvercle pour protéger le convertisseur I/P et les jauges lors de l’entretien d’autres sous-modules. Pour conserver les caractéristiques d’incertitude, ne pas frapper ou déposer le convertisseur I/P lors de la maintenance du sous-module. Convertisseur I/P Voir la figure 7‐2 ou 7‐4 pour l’emplacement des items numérotés. Le convertisseur I/P (item 41) se trouve à l’avant de la base du module. Remarque Après le remplacement du sous-module que constitue le convertisseur I/P, étalonner le contrôleur numérique de vanne pour maintenir les caractéristiques de précision. Remplacement du filtre I/P Un écran du port d’alimentation situé sous le convertisseur I/P sert de filtre secondaire pour le produit d’alimentation. Pour remplacer ce filtre, effectuer la procédure suivante : 1. Retirer le convertisseur I/P (item 41) et la monture (item 169) comme décrit dans la procédure de retrait du convertisseur I/P. 2. Retirer l’écran (item 231) de l’orifice d’alimentation. 3. Installer un nouvel écran dans le l’orifice d’alimentation comme illustré dans la figure 6‐2. Figure 6‐2. Emplacement du filtre I/P JOINT TORIQUE SITUÉ DANS L’ORIFICE DE SORTIE DU CONVERTISSEUR I/P ÉCRAN (FILTRE) SITUÉ DANS L’ORIFICE D’ALIMENTATION DU CONVERTISSEUR I/P W8072 61 Manuel d’instructions Maintenance et dépannage avril 2021 D103605X0FR 4. Inspecter le joint torique (item 39) dans l’orifice de sortie I/P. Si nécessaire, le remplacer. 5. Réinstaller le convertisseur I/P (item 41) et la monture (item 169) comme décrit dans la procédure de retrait du convertisseur I/P. Démontage du convertisseur I/P 1. Retirer le capot avant (item 43), s’il n’est pas encore retiré. 2. Voir la figure 6‐3. À l’aide d’une clé à douille hexagonale de 2,5 mm, retirer les quatre vis à tête creuse (item 23) qui fixent la monture (item 169) et le convertisseur I/P (item 41) à la base du module (item 2). 3. Retirer la monture (item 169) ; extraire ensuite le convertisseur I/P (item 41) de la base du module (item 2). Veiller à ne pas endommager les deux fils électriques qui sortent de la base du convertisseur I/P. 4. S’assurer que le joint torique (item 39) et l’écran (item 231) restent dans la base du module et ne sortent pas avec le convertisseur I/P (item 41). Remplacement du convertisseur I/P 1. Voir la figure 6‐2. Inspecter l’état du joint torique (item 39) et de l’écran (item 231) dans la base du module (item 2). Les remplacer, si nécessaire. Appliquer du lubrifiant au silicone sur les joints toriques. 2. S’assurer que les deux embouts (item 210) illustrées dans la figure 6‐3 sont correctement installés sur les fils électriques. Figure 6‐3. Convertisseur I/P Convertisseur I/P (item 41) W9328 MONTURE (item 169) VIS À TÊTE CREUSE (4) (item 23) EMBOUTS (item 210) 3. Installer le convertisseur I/P (item 41) directement dans la base du module (item 2), en veillant à ce que les deux fils électriques soient alimentés par les guides de la base du module. Ces guides acheminent les fils vers le sous-module du circuit imprimé. 4. Installer la monture (item 169) sur le convertisseur I/P (item 41). 5. Installer les quatre vis à tête creuse (item 23) et les serrer uniformément en croisant le serrage jusqu’à obtenir un couple final de 16 NSm (14 lbfSin). 6. Après avoir remplacé le convertisseur I/P, étalonner la course ou effectuer un étalonnage tactile-pour maintenir les caractéristiques de précision. 62 Manuel d’instructions Maintenance et dépannage D103605X0FR avril 2021 Circuit impriméé (PWB) Voir la figure 7‐2 ou 7‐4 pour l’emplacement des items numérotés. Le circuit imprimé (item 50) se trouve à l’arrière de l’ensemble de la base du module (item 2). Remarque Si le circuit imprimé est remplacé, calibrer et configurer le contrôleur numérique de vanne pour maintenir les caractéristiques de précision. Démontage du circuit imprimé 1. Séparer la base du module du boîtier en procédant au retrait de la base du module. 2. Retirer les trois vis (item 33). 3. Soulever le circuit imprimé (item 50) hors de la base du module (item 2). 4. S’assurer que les joints toriques (item 40) restent dans le bossage du capteur de pression de l’ensemble de la base du module (item 2) une fois que le circuit imprimé (item 50) a été retiré. Remplacement du circuit imprimé et réglage du commutateur DIP 1. Appliquer du lubrifiant au silicone sur les joints toriques du capteur de pression (item 40) et les installer sur le bossage du capteur de pression dans la base du module. 2. Orienter correctement le circuit imprimé comme (item 50) lors de son installation dans la base du module. Les deux fils électriques du convertisseur I/P (item 41) doivent être insérés dans leurs prises sur le circuit imprimé et le bossage capteur de pression de la base du module doit s’intégrer dans les prises du circuit imprimé. 3. Pousser le circuit imprimé (item 50) dans la cavité au sein de la base du module. 4. Placer et serrer les trois vis (item 33) avec un couple de 1 NSm (10,1 lbfSin). 5. Régler le commutateur DIP sur le circuit imprimé conformément au tableau 6‐2. Tableau 6‐2. Configuration du commutateur DIP(1) Étiquette de commutateur Mode de fonctionnement Position du commutateur DIP POINT-À-POINT Multi Boucle point­àà­point de 4­20 mA Boucle multi­point 24 V c.c. GAUCHE DROIT 1. Pour connaître l’emplacement du commutateur, voir la figure 6‐4. 63 Manuel d’instructions Maintenance et dépannage avril 2021 D103605X0FR Figure 6‐4. Raccordements et réglages du circuit imprimé CONNECTEUR DU CAPTEUR DE COURSE Capteur de course CONNECTEUR POUR BOÎTIER À BORNES SÉLECTION DU MODE DE FONCTIONNEMENT X0463 CONNECTEUR DU CAPTEUR DE COURSE SÉLECTION DU TRANSMETTEUR/COMMUTATEUR Capteur de course CONNECTEUR POUR BOÎTIER À BORNES Sortie Transmetteur Commutateur SÉLECTION DU MODE DE FONCTIONNEMENT X0432 Remarque Pour que le contrôleur numérique de vanne fonctionne avec un signal de commande de 4 à 20 mA s’assurer que le commutateur DIP est dans la position point à point de la boucle. 6. Assembler la base du module avec le boîtier en suivant la procédure concernant le remplacement de la base du module. 7. Configurer et étalonner le contrôleur numérique de vanne. 64 Manuel d’instructions Maintenance et dépannage D103605X0FR avril 2021 Relais pneumatique Voir la figure 7‐2 ou 7‐4 pour l’emplacement des items numérotés. Le relais pneumatique (item 24) se trouve à l’avant de la base du module. Remarque Après le remplacement du relais, calibrer le contrôleur numérique de vanne pour maintenir la précision. Démontage du relais pneumatique 1. Desserrer les quatre vis qui fixent le relais (item 24) sur la base du module. Ces vis sont imperdables dans le relais. 2. Retirer le relais. Remplacement du relais pneumatique 1. Inspecter visuellement les trous de la base du module pour s’assurer qu’ils sont propres et exempts d’obstructions. Si un nettoyage est nécessaire, ne pas agrandir les trous. 2. Appliquer du lubrifiant au silicone sur le joint du relai et le positionner dans les rainures sur le fond du relais, comme illustré dans la figure 6‐5. Appuyer sur les pattes de retenue du petit joint de maintien dans les fentes de fixation pour maintenir le joint du relais en place. Figure 6‐5. Relais pneumatique W8074 SÉPARATEUR DE RELAIS 3. Positionner le relais (avec la monture) sur la base du module. Serrer uniformément les vis en croisant le serrage avec un couple final de 2 NSm (20,7 lbfSin). 4. À l’aide de l’interface de communication, vérifier que la valeur du paramètre type pour les relais correspond au type de relais installé. 5. Après avoir remplacé le convertisseur I/P, étalonner la course ou effectuer un étalonnage tactile pour maintenir les caractéristiques de précision. Jauges, bouchons de tuyauterie ou vannes pneumatiques En fonction des options commandées, le DVC6200 ou le DVC6205 est équipé de deux jauges (item 47), de bouchons de tuyauterie (item 66) ou de vannes pneumatiques (item 67). Les instruments à action unique auront également un écran (item 236, figure7‐3). Ces derniers sont situés en haut de la base du module, à côté du relai. 65 Manuel d’instructions Maintenance et dépannage avril 2021 D103605X0FR Effectuer la procédure suivante pour remplacer les jauges, les vannes pneumatiques ou les bouchons de tuyauterie. Voir la figure et 7‐2 pour l’emplacement des items numérotés 7‐3. 1. Retirer le capot avant (item 43). 2. Retirer la jauge, le bouchon de tuyau ou la vanne pneumatique comme suit : Pour les jauges (item 47), les plats sont sur le boîtier du manomètre. Utiliser une clé sur les aplats de la jauge pour retirer la jauge de la base du module. Pour les instruments à double action, retirer une des jauges de sortie pour retirer la jauge d’alimentation. Pour les bouchons de tuyauterie (item 66) et les vannes pneumatiques (item 67), utiliser une clé pour les retirer de la base du module. 3. Appliquer le produit d’étanchéité du filetage (item 64) sur le filetage des jauges de remplacement, des bouchons de tuyauterie ou des vannes pneumatiques. 4. À l’aide d’une clé, desserrer les jauges, les bouchons de conduite ou les vannes de pneu dans la base du module. Boîtier à bornes Voir la figure 7‐2 ou 7‐4 pour l’emplacement des items numérotés. Le boîtier à bornes est situé sur le boîtier et contient le bornier de raccordement pour les raccordements sur site. Remarque Le boîtier à bornes des raccordements de contre-réaction DVC6205 (illustré dans la figure 6‐6) n’est pas une pièce remplaçable. Ne pas retirer la peinture anti-falsifications sur la vis. Figure 6‐6. Boîtier à bornes X0338 BOÎTIER À BORNES PRINCIPAL BOÎTIER A BORNES DE CONNEXIONS DE CONTRE-REACTION, NON REMPLAÇABLE BOÎTIER À BORNES PRINCIPAL DVC6200 X0379 DVC6205 Démontage du boîtier à bornes AVERTISSEMENT Afin d’éviter des blessures ou dommages matériels suite à un incendie ou à une explosion, couper l’alimentation de l’instrument avant de retirer le couvercle du boîtier à bornes dans une atmosphère potentiellement explosive ou dans une zone classée dangereuse. 1. Desserrer la vis de fixation (item 58) dans le capuchon (item 4) de sorte que le capuchon puisse être dévissé du boîtier à bornes. 2. Après avoir retiré le capuchon (item 4), noter les emplacements du câblage de terrain et déconnecter le câblage de terrain du boîtier à bornes. 66 Manuel d’instructions Maintenance et dépannage D103605X0FR avril 2021 3. Séparer la base du module du boîtier en procédant au retrait de la base du module. 4. Déconnecter le connecteur de raccordement du boîtier à bornes du circuit imprimé (item 50). 5. Retirer la vis (item 72). Tirer le boîtier à bornes hors du boîtier. Remplacement du boîtier à bornes Remarque Inspecter les joints toriques pour vérifier qu’ils ne sont pas usés et les remplacer si nécessaire. 1. Appliquer du lubrifiant, de l’enduit de silicone sur le joint torique (item 34) et installer le joint torique sur la tige du boîtier à bornes. 2. Insérer la tige du boîtier à bornes dans le boîtier jusqu’à ce qu’elle touche le fond. Positionner le boîtier à bornes de façon à ce que le trou de la vis (item 72) du boîtier à bornes soit aligné avec le trou fileté dans l’enceinte. Placer la vis (item 72). 3. Brancher le connecteur de raccordement du boîtier à bornes au circuit imprimé (item 50). L’orientation du connecteur est requise. 4. Assembler la base du module avec le boîtier en suivant la procédure concernant le remplacement de la base du module. 5. Reconnecter le câblage sur site comme indiqué à l’étape 2 dans la procédure concernant le retrait de la boîte à bornes. 6. Appliquer du lubrifiant, de l’enduit de silicone sur le joint torique (item 36) et installer le joint torique sur le filetage d’un diamètre de 2‐5/8 pouces du boîtier à bornes. L’utilisation d’un outil est recommandée pour éviter de couper le joint torique lors de son installation sur les filetages. 7. Appliquer de la graisse au lithium (item 63) sur les filetages de 2-5/8 pouces du boîtier à bornes pour éviter l’enrayement ou le grippage lorsque le capuchon est installé. 8. Visser le couvercle (item 4) sur le boîtier à bornes jusqu’à ce qu’il n’y ait plus de jeu. 9. Installer la vis de pression (item 58) dans le couvercle (item 4). Fixer le couvercle en serrant la vis. Dépannage En cas de difficultés de communication ou de sortie avec l’instrument, se reporter au tableau de dépannage 6‐3. Voir aussi la liste de vérification du support technique du DVC6200 à la page 70. Vérification de la tension disponible AVERTISSEMENT Des blessures ou dégâts matériels dus à un incendie ou une explosion peuvent survenir si ce test de connexion est tenté dans une atmosphère potentiellement explosive ou qui a été caractérisée comme dangereuse. Pour vérifier la tension disponible au niveau de l’instrument, procéder comme suit : 1. Brancher l’équipement de la figure 2‐3 au câblage de terrain à la place de l’instrument FIELDVUE. 2. Configurer le système de contrôle-commande pour fournir un courant de sortie maximum. 3. Régler la résistance du potentiomètre 1 kilohm comme illustré à la figure 2‐3 sur zéro. 4. Noter le courant indiqué sur la milliampèremètre. 67 Manuel d’instructions Maintenance et dépannage avril 2021 D103605X0FR 5. Régler la résistance du potentiomètre 1 kilohm jusqu’à ce que la tension sur le tensiomètre soit de 10,0 volts. 6. Noter le courant indiqué sur la milliampèremètre. 7. Si le courant est enregistré à l’étape 6 est identique à celui enregistré à l’étape 4 (± 0,08 mA), la tension disponible est adéquate. 8. Si la tension disponible est insuffisante, se reporter aux consignes de câblage de la section installation. Redémarrer le processeur Interface de communication Outils > Maintenance > Redémarrer le processeur (3-5-2) Il s’agit d’une remise à zéro « en douceur » de l’appareil. Cette procédure ne peut être effectuée que lorsque l’instrument est hors service. Une réinitialisation logicielle mettra immédiatement en application les modifications qui ont été envoyées à l’instrument. De même, si l’appareil est configuré pour s’arrêter sur une alerte, la réinitialisation logicielle annule cette configuration. Tableau 6‐3. Dépannage de l’instrument Symptôme 1. La lecture de l’entrée analogique au niveau de l’instrument ne correspond pas au courant réel fourni. Cause possible 1a. Mode contrôle non analogique. 1b. Tension de conformité du système de contrôle-commande Low. Action 1a. Vérifier le mode contrôle à l’aide de l’interface de communication. En mode numérique ou de test, l’instrument reçoit son point de consigne sous la forme d’un signal numérique. Le contrôle n’est pas basé sur le courant d’entrée. Changer le mode contrôle sur « Analog » (analogique). 1b. Vérifier la tension de conformité du système (voir les pratiques de câblage dans la section « Installation »). 1c. Arrêt de l’instrument en raison d’une défaillance du test 1c. Vérifier l’état de l’instrument à l’aide de l’interface de automatique. communication (se reporter à la section « Affichage des informations sur l’appareil »). 2. L’instrument ne transmet pas d’informations. 68 1d. Capteur d’entrée analogique non étalonné. 1d. Étalonner le capteur d’entrée analogique (voir le paragraphe « Étalonnage de l’entrée analogique » dans la section «Étalonnage »). 1e. Fuite de courant. 1e. Une humidité excessive dans le boîtier à bornes peut entraîner des fuites de courant. En général, le courant varie de façon aléatoire s’il y a une fuite. Laisser l’intérieur du boîtier à bornes sécher, puis recommencer le test. 2a. Tension disponible insuffisante. 2a. Calculer la tension disponible (voir les pratiques de câblage dans la section « Installation »). La tension disponible doit être plus importante ou égale à 10 V c.c. 2b. Impédance de sortie du contrôleur trop faible. 2b. Installer un filtre HART après examen des exigences de tension de conformité du système de contrôle-commande (voir les pratiques de câblage dans la section « Installation »). 2c. Capacité (électrique) du câble trop élevée. 2c. Vérifier les limites de capacité maximale du câble (voir les pratiques de câblage dans la section « Installation »). 2d. Filtre HART mal ajusté. 2d. Vérifier le réglage du filtre (voir le manuel d’instructions du filtre HART approprié). 2e. Câblage de terrain incorrect. 2e. Vérifier la polarité du câblage et l’intégrité des connexions. S’assurer que le blindage de câble est mis à la terre uniquement au niveau du système de contrôle-commande. 2f. Sortie du contrôleur fournissant une boucle inférieure à 4 mA. 2f. Vérifier le paramètre de sortie minimum du système de contrôle-commande, qui ne doit pas être inférieur à 3,8 mA. 2g. Câble de boucle déconnecté du circuit imprimé. 2g. Vérifier que les connecteurs sont correctement branchés. 2h. Le commutateur DIP du circuit imprimé n’est pas réglé correctement. 2h. Vérifier que le réglage n’est pas incorrect et que le commutateur DIP n’est pas cassé à l’arrière circuit imprimé. Réinitialiser le commutateur ou remplacer le circuit imprimé si le commutateur est cassé. Voir le tableau 6‐2 pour les informations de configuration du commutateur Manuel d’instructions Maintenance et dépannage D103605X0FR avril 2021 Tableau 6‐3. Dépannage de l’instrument Symptôme 2. L’instrument ne transmet pas d’informations. Cause possible 2j. Défaillance du circuit imprimé. 2k. Adresse d’interrogation incorrecte. 2l. Boîtier à bornes défectueux. 2m. Interface de communication ou logiciel ValveLink défectueux câble du modem. 2n. Modem ValveLink défectueux ou non compatible avec le PC. 2p. Protection du logicial ValveLink défectueuse ou non programmée. 3. L’instrument ne s’étalonne 3a. Erreurs de configuration pas et fonctionne au ralenti ou par oscillations. 3b. Passages pneumatiques restreints dans le convertisseurI/P. Action 2j. Utiliser une source de courant 4-20 mA pour mettre l’appareil sous tension. La tension des bornes entre les bornes LOOP+ et LOOP- doit être comprise entre 8,0 et 9,5 V c.c.. Si la tension du terminal n’est pas comprise entre 8,0 et 9,5 V c.c., remplacer le circuit imprimé. 2k. Configurer l’adresse d’interrogation à l’aide de l’interface de communication (voir la section « Configuration détaillée »). À partir du menu « Utilitaires » sélectionner Configuration de l’interface de communication > Interrogation > Toujours interroger. Régler l’adresse d’interrogation de l’instrument sur0. 2l. Vérifier la continuité du raccordement entre chaque borne à vis et la broche correspondante du circuit imprimé. Si nécessaire, remettre en place le boîtier à bornes. 2m. Si nécessaire, réparer ou remplacer le câble. 2n. Remplacer le modem ValveLink. 2p. La remplacer en cas de défaut de fonctionnement ou la renvoyer à l’usine pour une programmation. 3a. Vérification de la configuration : si nécessaire, régler la protection sur « Aucune ». S’il n’est pas en marche, le mettre en marche. Vérifier : le mouvement du capteur de course ; le réglage ; la condition d’alimentation nulle ; le raccordement de contre-réaction ; le mode contrôle (qui doit être analogique) ; le mode contrôle de redémarrage (qui doit être analogique). 3b. Vérifier l’écran du port d’alimentation du convertisseur I/P de la base du module. Le remplacer, si nécessaire. Si les passages du convertisseur I/P sont restreints, remplacer le convertisseur I/P. 3c. Joints toriques du convertisseur I/P manquant ou dur et 3c. Remplacer le ou les joints toriques. aplati, en perte d’étanchéité. 3d. Convertisseur I/P endommagé/corrodé/obstrué. 3d. Vérifier que la palette n’est pas tordue, que la bobine est ouverte (continuité), qu’il n’y a pas de contamination ni de coloration ou d’alimentation en air sale. La résistance de la bobine doit être comprise entre 1680-1860 ohm. Remplacer l’ensemble I/P s’il est endommagé, corrodé, obstrué ou ouvert. 3e. Convertisseur I/P non conforme aux caractéristiques. 3e. La buse du convertisseur I/P a peut-être été ajustée. Vérifier le signal d’entraînement (55 à 80 % pour celui à double action ; 60 à 85 % pour celui à simple action) pendant que la vanne est hors des butées. Remplacer le convertisseur I/P si le signal d’entraînement est continuellement haut ou bas. 3f. Joint de la base du module défectueux. 3f. Vérifier l’état et la position du joint de la base du module. Si nécessaire, remplacer le joint d’étanchéité. 3g. Relais défectueux. 3g. Enfoncer le faisceau de relai à l’emplacement de réglage dans la monture, chercher une éventuelle augmentation de la pression de sortie. Retirer le relais, inspecter le joint du relais. Remplacer le joint d’étanchéité du relais ou le relais si le convertisseur I/P est opérationnel et que les passages d’air ne sont pas bloqués. Vérifier le réglage du relais 4. Les tests de diagnostic ValveLink fournissent des résultats erronés. 5. L’interface de communication ne s’allume pas. 3h. Détendeur 67CFR défectueux, la jauge de pression d’alimentation est déplacée. 4a. Capteur de pression défectueux. 3h. Remplacer le détendeur 67CFR. 4b. Joint torique du capteur de pression manquant. 4b. Remplacer le joint torique. 5a. Bloc batterie non chargé. 5a. Charger le bloc-batterie. Remarque : le bloc batterie peut être chargé lorsqu’il est raccordé à l’interface de communication ou séparément. L’interface de communication est complètement opérationnelle et le bloc-batterie est en cours de chargement. Ne pas tenter de charger le bloc batterie dans une zone dangereuse. 4a. Remplacer le circuit imprimé. 69 Manuel d’instructions Maintenance et dépannage avril 2021 D103605X0FR Liste de vérification du support technique DVC6200 Les informations suivantes doivent être disponibles avant de contacter le Bureau commercial Emerson pour obtenir de l’aide. 1. Numéro de série de l’instrument inscrit sur la plaque signalétique _______________________________________________ 2. Le contrôleur numérique de vanne répond-il au signal de contrôle ? Oui _________ Non _________ Si ce n’est pas le cas, donner des détails __________________________________________________________________ 3. Mesurer la tension à travers les bornes Loop - et Loop + lorsque le courant est de 4,0 mA et 20,0 mA : __________V à 4,0 mA __________V à 20,0 mA. (Ces valeurs doivent être comprises entre 8,6 V à 4,0 mA et 8,8 V à 20 mA). 4. Est-il possible de communiquer via HART au contrôleur numérique de vanne ? Oui _________ Non _________ 5. Quel est le niveau de diagnostic du contrôleur numérique de vanne ? AC ____ HC ____ AD ____ PD ____ ODV____ 6. Quelle est la version du microprogramme du contrôleur numérique de vanne ? ______________ 7. Quelle est la version du contrôleur numérique de vanne ? ______________ 8. Le mode du contrôleur numérique de vanne est-il « En service » ? Oui _________ Non _________ 9. Le mode contrôle du contrôleur numérique de vanne est-il réglé sur « Analogique » ? Oui _________ Non _________ 10. Est-il réglé sur « Course » ou « Régulation de la pression » ? 11. Quelles sont les valeurs des paramètres suivants ? Signal d’entrée _________ Signal d’entraînement _________ % Pression d’alimentation _________ Cible de course _________ % Pression A_________ Pression B _________ Course _________ % 12. Qu’affichent les alertes suivantes ? « Alertes de défaillance » ____________________________________________________________________________ « Alertes de vanne » ________________________________________________________________________________ « État de fonctionnement » __________________________________________________________________________ « Entrées des registres d’alerte » ______________________________________________________________________ 13. Exporter les données ValveLink (le cas échéant) de l’appareil (« Surveillance de l’état », « Configuration détaillée », etc.). Montage 1. Quel contrôleur numérique de vanne avez-vous ? DVC6200 ____________ DVC6205/DVC6215 ______________________ 2. Sur quel modèle, marque, taille, etc. d’actionneur le DVC6200 est-il monté ? ______________________________________ 3. Quelle est la course totale de la vanne ? ____________________________________________________________________ 4. Quel est le numéro de référence du kit de montage ? _________________________________________________________ 5. Si des kits de montage sont fabriqués par LBP/Customer, fournir des photos de l’installation. 6. Le kit de montage est-il installé conformément aux instructions ? Oui _________ Non _________ 7. Quelle est la position de sécurité de la vanne ? Échec de fermeture _________ Échec d’ouverture _________ 70 Manuel d’instructions Pièces D103605X0FR avril 2021 Section 7 Pièces77 Commande de pièces de rechange Lors de toute correspondance avec un bureau commercial Emerson à propos du présent équipement, toujours préciser le numéro de série du contrôleur. AVERTISSEMENT Utiliser uniquement des pièces de rechange d’origine Fisher. Des composants non fournis par Emerson ne doivent, en aucune circonstance, être utilisés dans un instrument Fisher. L’utilisation de composants non fournis par Emerson peut annuler la garantie, affecter les performances de l’instrument et provoquer des blessures et des dommages matériels. Kits de pièces de rechange Kit Description 5* Aluminum, with I/O Package Standard Standard, M20 Extreme Temperature Extreme Temperature, M20 Remarque Tous les kits standard à élastomères comprennent des élastomères au nitrile. Les kits pour les température extrêmes comprennent des élastomères au fluorosilicone. Kit 1* Description Elastomer Spare Parts Kit (kit contains parts to service one digital valve controller) Standard Extreme Temperature Stainless Steel, with I/O Package Extreme Temperature Extreme Temperature, M20 19B5402X012 19B5402X022 Small Hardware Spare Parts Kit (kit contains parts to service one digital valve controller) 19B5403X012 3* Seal Screen Kit [kit contains 25 seal screens (key 231) and 25 O‐rings (key 39)] 14B5072X182 4* Integral Mount Seal Kit (for 667 size 30i - 76i and GX actuators) [kit contains 5 seals (key 288)] PWB Assembly (HW2) (see figure 7‐2 and 7‐4) for DVC6200 and DVC6205 19B5402X032 Terminal Box Kit (see figure 7‐1) Remarque A utiliser uniquement en cas de remplacement en nature. Les boîtiers à bornes suivants sont compatibles uniquement avec la révision 2 des composants du circuit imprimé (HW2). Aluminum, without I/O Package Standard 19B5401X142 Standard, M20 19B5401X342 Standard, Natural Gas Certified 19B5401X162 Standard, Natural Gas Certified, M20 19B5401X362 Extreme Temperature 19B5401X152 Extreme Temperature, M20 19B5401X352 Extreme Temperature, Natural Gas Certified 19B5401X172 Extreme Temperature, Natural Gas Certified, M20 19B5401X372 *Pièces de rechange recommandées 19B5401X202 19B5401X412 Item 50 5* 19B5401X182 19B5401X392 19B5401X192 19B5401X402 Stainless Steel, without I/O Package Extreme Temperature, Natural Gas Certified 19B5401X312 Extreme Temperature, Natural Gas Certified, M20 19B5401X382 Numéro de pièce 2* Numéro de pièce Remarque Les circuits imprimés suivant sont compatibles uniquement avec les boîtiers à bornes illustrés dans la figure 7‐1. Contacter un bureau de vente Emerson pour remplacer un circuit imprimé. Hardware Revision 2 (HW2), without I/O Package For instrument level HC For instrument level AD For instrument level PD For instrument level ODV Hardware Revision 2 (HW2), with I/O Package For instrument level HC For instrument level AD For instrument level PD For instrument level ODV 71 Manuel d’instructions Sections avril 2021 D103605X0FR Kit Figure 7‐1. Boîtier à bornes SANS MODULE D'E/S Kit 6* 7* 8* I/P Converter Kit Standard Extreme Temperature 11 Feedback Array Kit Sliding Stem (Linear) [kit contains feedback array and hex socket cap screws, qty. 2, washer, plain, qty. 2, external tooth lock washer, qty. 2 (only with aluminum feedback array kit) and alignment template. 210 mm (8-1/4 inch) kit contains feedback array and hex socket cap screws, qty. 4, washer, plain, qty. 4, external tooth lock washer, qty. 4 (only with aluminum feedback array kit), alignment template and insert]. Stainless steel kits only for use with stainless steel mounting kits. Numéro de pièce 7 mm (1/4-inch) Aluminum 19 mm (3/4-inch) Aluminum Stainless steel 25 mm (1-inch) Aluminum Stainless steel 38 mm (1-1/2 inch) Aluminum Stainless steel 50 mm (2-inch) Aluminum Stainless steel 110 mm (4-1/8 inch) Aluminum Stainless steel 210 mm (8-1/4 inch) Aluminum Stainless steel 38B6041X152 38B6041X132 Spare Housing Assembly Kit [kit contains housing (key 1); vent assembly (key 52); seal (only included in Housing A kits) (key 288); seal (key 237); O‐ring (key 34); O‐ring (only used with integrally mounted regulator) (key 5)] Stainless Steel Housing B (used for all actuators except GX) Extreme Temperature 9* Remote Mount Feedback Unit Kit (see figure 7‐5) [remote housing assembly (key25); hex socket set screw (key 58); 1/2 NPT pipe plug (key 62); wire retainer, qty 2 (key 131); terminal cover (key 255); o-ring (key 256); gasket (Housing A only, used for GX actuator) (key 287); seal (Housing A only, used for GX actuator) (key 288) Spare Module Base Assembly Kit, [kit contains module base (key 2); drive screws, qty. 2, (key 11); shield/label (key 19); hex socket cap screw, qty. 3, (key 38); self tapping screw, qty. 2 (key 49); pipe plug, qty. 3 (key 61); retaining ring, qty. 3 (key 154); screen (key 236); and flame arrestors, qty. 3 (key 243)] Aluminum GE18654X012 Stainless Steel GE18654X022 Aluminum Housing A (used for GX actuator) Standard Extreme Temperature Housing B (used for all actuators except GX) Standard Extreme Temperature Spare I/P Shroud Kit [kit contains shroud (key 169) and hex socket cap screw, qty. 4 (key 23)] Numéro de pièce 10 AVEC MODULE D'E/S Description Description GG20240X012 GG20240X022 GE65853X012 GG20240X032 GE65853X022 GG20240X042 GE65853X032 GG20240X052 GE65853X042 GG20240X082 GE65853X062 GG20243X012 GE65853X072 Rotary [Kit contains feedback assembly, pointer assembly, travel indicator scale and M3 machine pan head screws qty. 2]. Stainless steel kits only for use with stainless steel mounting kits. Aluminum GG10562X012 Stainless steel GG10562X022 GE48798X032 GE48798X042 GE48798X072 GE48798X082 Rotary array kit with coupler [Kit contains feedback assembly and NAMUR coupler] Aluminum Stainless steel GE48798X102 12 GE29183X012 GE71982X012 GE71982X022 Mounting Shield Kit [kit contains shield, qty. 3 and machine screws, qty. 6] GG05242X022 Gasket/Seal Kit, for use with GX actuator [kit contains insulating gasket (key 287) and seal (key 288)] GE45468X012 Remarque Le kit de rétroaction à distance (kit 10) ne peut pas être commandé parle biais d’un numéro de pièce en raison des exigences concernantlesplaques signalétique/certification. Contacter un bureaucommercialEmerson pour des informations sur la commande dece kit. 13* 72 *Pièces de rechange recommandées Manuel d’instructions Pièces D103605X0FR avril 2021 Liste des pièces détachées Item 63 64 Remarque Les pièces dont les numéros de note de bas de page sont indiqués sont disponibles en kits de pièces. Voir les informations de la note de bas de page dans la partie inférieure. 65 154 236 237 Description Numéro de pièce Lithium grease (not furnished with the instrument) Pipe thread sealant, anaerobic (not furnished with the instrument) Lubricant, silicone sealant (not furnished with the instrument) Retaining Ring(2) (3 req'd) Screen (required for relay B and C only)(8) Module Base Seal(1) Pour obtenir des informations sur les commandes de pièces détachées, contacter un bureau commercial Emerson. Toutes les pièces contenant des élastomères comprennent des élastomères au nitrile. Les pièces destinées aux température extrêmes comprennent des élastomères au fluorosilicone. Base de module (voir la figure 7‐2 et 7‐4) DVC6200 et DVC6205 Item Description Numéro de pièce Boîtier (voir la figure 7‐2 et 7‐4) 2 11 12 19 61 243 Module Base(7) Drive Screw(7) (2 req'd) O‐ring(1) Shield(7) Pipe Plug, hex socket(7) (3 req'd) Slotted Pin (flame arrestor)(7) (3 req'd) DVC6200 et DVC6205 1 11 20 52 74 248 249 250 267 271 287 288 Housing(8) Drive Screw (2 req'd) (DVC6205 only) Shield (DVC6205 only) Vent(2) Mounting Bracket (DVC6205 only) Screw, hex head (4 req’d) (DVC6205 only) Screw, hex head (4 req’d) (DVC6205 only) Spacer (4 req’d) (DVC6205 only) Standoff (2 req’d) (DVC6205 only) Screen(8) Gasket, Housing A only (used for GX actuator) (DVC6200 only) Seal (used for 667 size 30i - 76i and GX actuators) (DVC6200 only) Ensemble convertisseur I/P (voir la figure 7‐2 et 7‐4) DVC6200 et DVC6205 23 39* 41 169 210* 231* Cap Screw, hex socket(2)(9) (4 req'd) O‐ring(1)(3)(6) I/P Converter(6) Shroud(6)(9) (see figure 6‐3) Boot(1)(6) (2 req'd) (see figure 6‐3) Seal Screen(1)(3)(6) Pièces communes (voir la figure 7‐2, 7‐3, et 7‐4 ) Relai (voir la figure 7‐2 et 7‐4) DVC6200 et DVC6205 24* Relay Assembly, (includes shroud, relay seal, mounting screws) 16* 29 33 38 43* 48 49 61 O‐ring(1) (3 req'd) Warning label, for use only with LCIE hazardous area classifications Mach Screw, pan head(2) (3 req'd) Cap Screw, hex socket(2)(7) (3 req'd) Cover Assembly (includes cover screws) Standard GG53748X012 Extreme temperature GG53748X022 Nameplate Screw, self tapping (2 req'd)(7) Pipe Plug, hex socket(7) Housing A with relay C (2 req'd ) (used for GX actuator) Housing A with relay B (1 req'd) (used for GX actuator) Housing B with relay B and C (1 req'd) (used for all actuators except GX) Not required for relay A *Pièces de rechange recommandées 1. Disponible dans le kit de pièces de rechange en élastomère 2. Disponible dans le kit de petites pièces de rechange en élastomère 3. Disponible dans le kit d’étanchéité de l’écran 6. Disponible dans le kit du convertisseur I/P 7. Disponible dans le kit de montage de base du module de rechange 8. Disponible dans le kit de montage du boîtier de rechange 9. Disponible dans le kit de gaine de rechange DVC6200 et DVC6205 Standard Standard Bleed Housing A (used for GX actuator) Single‐acting direct (relay C) Single‐acting reverse (relay B) Housing B (used for all actuators except GX) Single‐acting direct (relay C) Double‐acting (relay A) Single‐acting reverse (relay B) Low Bleed Housing A (used for GX actuator) Single‐acting direct (relay C) Single‐acting reverse (relay B) Housing B (used for all actuators except G) Single‐acting direct (relay C) Double‐acting (relay A) Single‐acting reverse (relay B) 38B5786X182 38B5786X172 38B5786X132 38B5786X052 38B5786X092 38B5786X202 38B5786X192 38B5786X152 38B5786X072 38B5786X112 73 Manuel d’instructions Sections avril 2021 Item Description D103605X0FR Numéro de pièce 24* Relay Assembly, (includes shroud, relay seal, mounting screws) (continued) Extreme Temperature Standard Bleed Single‐acting direct (relay C) Double‐acting (relay A) Single‐acting reverse (relay B) 38B5786X142 38B5786X032 38B5786X102 Low Bleed Single‐acting direct (relay C) Double‐acting (relay A) Single‐acting reverse (relay B) 38B5786X162 38B5786X082 38B5786X122 Item Manomètres, bouchons de tuyauterie ou assemblages de valves pneumatiques (voir la figure 7‐3) DVC6200 et DVC6205 47* Pressure Gauge Double‐acting (3 req'd); Single‐acting (2 req'd) PSI/MPA Gauge Scale To 60 PSI, 0.4 MPa To 160 PSI, 1.1 MPa PSI/bar Gauge Scale To 60 PSI, 4 bar To 160 PSI, 11 bar PSI/KG/CM2 Gauge Scale To 60 PSI, 4 KG/CM2 To 160 PSI, 11 KG/CM2 66 Pipe Plug, hex head For units w/o gauges 67 Tire Valve, used with Tire Valve Option only Double‐acting (3 req'd); Single‐acting (2 req'd) Connexions à boucle Boîtier à bornes (voir la figure 7‐2 et 7‐4) DVC6200 et DVC6205 4 34* 36* 58 72 164 Terminal Box Cap O‐ring(1)(5) O‐ring(1)(5) Set Screw, hex socket(2) Cap Screw, hex socket(2) Terminal Box Assembly Raccordements de contre-réaction du boîtier à bornes (voir la figure 7‐4) DVC6205 4 34* 36* 58 62 262 263* Terminal Box Cap O‐ring(1)(5) O‐ring(1)(5) Set Screw, hex socket(2) Pipe Plug, hex hd Adapter O-ring Description Unité de contre-réaction DVC6215 (voir la figure 7‐5) 65 Lubricant, silicone sealant (not furnished with the instrument) 256* O-Ring Filtres HART HF340, DIN rail mount HF341, DIN rail Mount, pass through (no filter) *Pièces de rechange recommandées 74 1. Disponible dans le kit de pièces de rechange en élastomère 2. Disponible dans le kit de petites pièces de rechange en élastomère 5. Disponible dans le kit de boîtier à bornes Manuel d’instructions Pièces D103605X0FR avril 2021 Figure 7‐2. Contrôleur numérique de vanne FIELDVUE DVC6200 BOÎTIER A : VUE ARRIÈRE (UTILISÉ POUR LES ACTIONNEURS GX)) DOUBLE ACTION ACTION DIRECTE BOÎTIER B : VUE ARRIÈRE (UTILISÉ POUR TOUS LES ACTIONNEURS SAUF GX) ACTION INVERSÉE APPLIQUER UN LUBRIFIANT, UN PRODUIT D'ÉTANCHÉITÉ OU UN VERROU FILETÉ APPLIQUER DU LUBRIFIANT SUR TOUS LES JOINTS TORIQUES, SAUF INDICATION CONTRAIRE GE40185 feuille 1 sur 3 75 Manuel d’instructions Sections avril 2021 D103605X0FR Figure 7‐2. Boîtier du contrôleur numérique de vanne FIELDVUE DVC6200 (suite) SECTION C-C ÉCHELLE 2 : 1 SECTION A-A SECTION C-C ÉCHELLE 2 : 1 ACIER INOXYDABLE UNIQUEMENT APPLIQUER UN LUBRIFIANT, UN PRODUIT D’ÉTANCHÉITÉ OU UN VERROU FILETÉ SECTION C-C ÉCHELLE 2 : 1 APPLIQUER DU LUBRIFIANT SUR TOUS LES JOINTS TORIQUES, SAUF INDICATION CONTRAIRE GE40185 feuille 2 sur 3 Figure 7‐3. Configuration de la jauge DOUBLE ACTION ACTION DIRECTE POUR L'OPTION DU BOUCHON DE TUYAU, REMPLACER LE 47 PAR LE 66 POUR L'OPTION DE LA VANNE DE PNEU, REMPLACER LE 47 PAR LE 67 APPLIQUER UN LUBRIFIANT, UN PRODUIT D'ÉTANCHÉITÉ OU UN VERROU FILETÉ APPLIQUER DU LUBRIFIANT SUR TOUS LES JOINTS TORIQUES, SAUF INDICATION CONTRAIRE GE40185 feuille 3 sur 3 76 ACTION INVERSÉE Manuel d’instructions Pièces D103605X0FR avril 2021 Figure 7‐4. Boîtier de l’unité de base FIELDVUE DVC6205 SECTION B‐B SECTION A-A APPLIQUER UN LUBRIFIANT, UN PRODUIT D'ÉTANCHÉITÉ OU UN VERROU FILETÉ SECTION H-H APPLIQUER DU LUBRIFIANT SUR TOUS LES JOINTS TORIQUES, SAUF INDICATION CONTRAIRE GE40181 77 Manuel d’instructions Sections avril 2021 D103605X0FR Figure 7‐4. Boîtier de l’unité de base FIELDVUE DVC6205 (suite) SECTION C-C ÉCHELLE 2 : 1 ACIER INOXYDABLE UNIQUEMENT SECTION C-C ÉCHELLE 2 : 1 DOUBLE ACTION MONTRÉE : DOUBLE ACTION ACTION DIRECTE APPLIQUER UN LUBRIFIANT, UN PRODUIT D'ÉTANCHÉITÉ OU UN VERROU FILETÉ APPLIQUER DU LUBRIFIANT SUR TOUS LES JOINTS TORIQUES, SAUF INDICATION CONTRAIRE GE40181 78 ACTION INVERSÉE Manuel d’instructions Pièces D103605X0FR avril 2021 Figure 7‐4. Boîtier de l’unité de base FIELDVUE DVC6205 (suite) MONTAGE SUR PAROI MONTAGE SUR TUBE APPLIQUER UN LUBRIFIANT, UN PRODUIT D'ÉTANCHÉITÉ OU UN VERROU FILETÉ APPLIQUER DU LUBRIFIANT SUR TOUS LES JOINTS TORIQUES, SAUF INDICATION CONTRAIRE GE40181 79 Manuel d’instructions Sections avril 2021 D103605X0FR Figure 7‐5. Ensemble de contre-réacion à distance FIELDVUE DVC6215 SECTION A-A PARTIES NON MONTRÉES : 158 APPLIQUER UN LUBRIFIANT/PRODUIT D'ÉTANCHÉITÉ GE46670-B BOÎTIER A (UTILISÉ POUR LES ACTIONNEURS GX)) SECTION A-A PARTIES NON MONTRÉES : 158 APPLIQUER UN LUBRIFIANT/PRODUIT D'ÉTANCHÉITÉ GE40178-B BOÎTIER B (UTILISÉ POUR TOUS LES ACTIONNEURS SAUF GX) 80 Manuel d’instructions Principe de fonctionnement D103605X0FR avril 2021 Annexe A Principe de fonctionnementAA−A Communication HART Le protocole HART (« Highway Addressable Remote Transducer », transducteur à distance adressable par bus) offre aux appareils deterrain la possibilité de communiquer numériquement les données de l’instrument et les données de procédé. Cette communication numérique se produit sur la même boucle à deux fils qui fournit le signal de contrôle du procédé de 4-20 mA, sans perturber le signal de procédé. De cette manière, le signal analogique de procédé, peut être utilisé pour le contrôle avec sa fréquence d’actualisation la plus rapide. En même temps, le protocole HART permet d’accéder aux diagnostics numériques, à la maintenance et aux données de procédé supplémentaires. Le protocole fournit une intégration totale du système via un appareil faisant office de système hôte. Le protocole HART utilise la modulation par déplacement de fréquence (FSK). Deux fréquences individuelles de 1 200 et 2 200 Hz sont superposées sur le signal de courant de 4-20 mA. Ces fréquences représentent les chiffres 1 et 0 (voir la figure A‐1). En superposant un signal de fréquence sur le courant 4-20 mA, la communication numérique est obtenue. La valeur moyenne du signal HART est égale à zéro, aucune valeur CC n’est donc ajoutée au signal de 4-20 mA. Par conséquent, une communication simultanée est réalisée sans interrompre le signal de procédé. Figure A‐1. Technique de modulation par déplacement de fréquence HART +0,5 V 0 SIGNAL ANALOGIQUE -0,5 V 1 200 Hz “1” 2 200 Hz “0” CHANGEMENT DE COURANT MOYEN PENDANT LA COMMUNICATION = 0 A6174 Le protocole HART permet de disposer d’une seule ligne de communication, donc de mettre en réseau plusieurs appareils. Ce procédé est bien adapté au contrôle des applications distantes telles que les canalisations, les sites de comptage transactionnel et les parcs à réservoirs. Voir le tableau 6‐2 pour savoir comment passer le commutateur à double rangée de connexions (DIP) du circuit imprimé en configuration multipoint. Contrôleur numérique de vanne DVC6200 Le boîtier du contrôleur numérique de vanne DVC6200 contient le capteur de course, la boîte à bornes, les connexions d’entrée et de sortie pneumatiques et une base pour le module qui peut facilement être remplacé sur le terrain sans déconnecter le câblage ou la tuyauterie du site. La base du module contient les sous-modules suivants : convertisseur I/P, un circuit imprimé et un relai pneumatique. La position du relai est détectée par l’intermédiaire d’un détecteur situé sur le circuit imprimé lorsque l’aimant passe devant le faisceau du relai. Ce capteur est utilisé pour la lecture de la contre-réaction de boucle mineure (MLFB). La base du module peut être reconstruite en remplaçant les sous-modules. Voir les figures A‐3, A‐4, A‐5 et A‐6. 81 Principe de fonctionnement avril 2021 Manuel d’instructions D103605X0FR Figure A‐2. Instrument FIELDVUE courant pour les connexions à un ordinateur personnel avec le logiciel ValveLink SYSTÈME DE CONTRÔLE−COMMANDE MODEM HART BORNES DE L’APPAREIL E1362 Les contrôleurs numériques de vanne DVC6200 sont des instruments alimentés par boucle qui fournissent une position de vanne de régulation proportionnelle à un signal d’entrée de la salle de commande. Les éléments suivants décrivent un contrôleur numérique de vanne à action double monté sur un actionneur à piston. Le signal d’entrée est acheminé vers le boîtier à bornes par l’intermédiaire d’une seule paire de fils torsadés, puis vers le sous-module du circuit imprimé, à l’endroit où il est lu par le microprocesseur, traité par un algorithme numérique, et converti en un signal d’entraînement I/P analogique. Au fur et à mesure que le signal d’entrée augmente, le signal d’entraînement vers le convertisseur I/P augmente, augmentant ainsi la pression de sortie I/P. La pression de sortie I/P est acheminée vers le sous-module de relai pneumatique. Le relai est également raccordé à la pression d’alimentation et amplifie le petit signal pneumatique du convertisseur I/P. Le relai accepte le signal pneumatique amplifié et fournit deux pressions de sortie. Avec une entrée croissante (signal de 4 à 20 mA), la sortie A est toujours augmentée et la pression de sortie B diminue. La pression de sortie A est utilisée pour les applications à double action et à action simple directe. La pression de sortie B est utilisée pour les applications à double action et à action simple inverse. Comme cela est montré dans la figure A‐3, A‐4, et A‐5 la pression augmentée de la sortie A provoque le déplacement vers le bas de la tige de l’actionneur. La position de la tige est détectée par le capteur de contre-réaction sans contact. La tige continue à se déplacer vers le bas jusqu’à ce qu’elle atteigne la position correcte. À ce stade, le circuit imprimé stabilise le signal d’entraînement I/P. Cela positionne le clapet de manière à éviter toute augmentation supplémentaire de la pression de piquage. Au fur et à mesure que le signal d’entrée diminue, le signal d’entraînement à destination du convertisseur I/P augmente, augmentant ainsi la pression de sortie I/P. Le relais pneumatique diminue la pression de sortie A et augmente la pression de sortie B. La tige continue à se déplacer vers le haut jusqu’à ce qu’elle atteigne la position correcte. À ce stade, le circuit imprimé stabilise le signal d’entraînement I/P. Cela positionne le clapet de manière à éviter toute autre diminution de la pression de piquage. 82 Manuel d’instructions Principe de fonctionnement D103605X0FR avril 2021 Figure A‐3. Schéma fonctionnel du contrôleur numérique de vanne FIELDVUE DVC6200 SIGNAL D'ENTRÉE 4-20 mA + HART VANNE DE CONTRE-RÉACTION CIRCUIT IMPRIMÉ BOÎTIER À BORNES SIGNAL D’ENTRAÎNEMENT SORTIE A BORNES AUXILIAIRES CONVERTISSEUR I/P RELAIS PNEUMATIQUE PRESSION D’ALIMENTATION SORTIE B ÉVENT VANNE ET ACTIONNEUR E1361 Figure A‐4. Schéma fonctionnel du contrôleur numérique de vanne FIELDVUE DVC6200 BOÎTIER À BORNES AO 4-20 mA BORNES DE BOUCLE CIRCUIT IMPRIMÉ + BORNES AUXILIAIRES VANNE DE CONTRE-RÉACTION SIGNAL D’ENTRAÎNEMENT -+-+ SORTIE A BORNES DE SORTIE AI ALIMENTATIO N 8-30 V c.c. CONVERTISSEUR I/P + - PRESSION D’ALIMENTATION SORTIE B ÉVENT VANNE ET ACTIONNEUR 83 Manuel d’instructions Principe de fonctionnement avril 2021 D103605X0FR Figure A‐5. Schéma fonctionnel du contrôleur numérique de vanne FIELDVUE DVC6200 à entrées TOR BORNES DE BOUCLE BOÎTIER À BORNES AO 4-20 mA CIRCUIT IMPRIMÉ + BORNES AUXILIAIRES VANNE DE CONTRE-RÉACTION SIGNAL D’ENTRAÎNEMENT -+-+ SORTIE A BORNES DE SORTIE DI (entrée directe) CONVERTISSEUR I/P PRESSION D’ALIMENTATION + - SORTIE B 30 V MAX. ÉVENT VANNE ET ACTIONNEUR Figure A‐6. Assemblage du contrôleur numérique de vanne FIELDVUE DVC6200 BOÎTIER RELAIS PNEUMATIQUE JAUGES COUVERCLE BOÎTIER À BORNES AVEC COUVERCLE CIRCUIT IMPRIMÉ BASE DU MODULE W9925-2 84 CONVERTISSEUR I/P Manuel d’instructions Arborescences du menu de l’interface de communication D103605X0FR avril 2021 Annexe B Arborescences du menu de l’interface de communication Cette section contient les arborescences de menu de l’interface de communication pour les niveaux d’instrumentation HC, AD, PD et ODV. Elle contient également une liste de fonctions/variables classées par ordre alphabétique pour aider à localiser la fonction/variable dans l’arborescence de menu appropriée. Toutes les séquences d’accès rapide référencées dans les arborescences de menu sont basées sur le menu en ligne (voir la figureB-2) pour commencer. Remarque Les séquences d’accès rapide ne s’appliquent qu’à l’interface de communication 475. Elles ne s’appliquent pas à l’interface de communication Trex. Niveaux d’instrumentation HC, AD et PD et ODV Function/Variable Actual Travel Actuator Manufacturer Actuator Model Actuator Selection Actuator Size Actuator Style Air Alert Record Full (Alert Record/Status Alerts Enable) Alert Record Full (Alert Record/Status Alerts NE107) Alert Record Not Empty (Alert Record/Status Alerts Enable) Alert Record Not Empty (Alert Record/Status Alerts NE107) Alert Switch Source Analog Input Analog Input (Calibration) Analog Input Units Area Units Auto Calibration Autocal in Progress (Alert Record/Status Alerts Enable) Autocal in Progress (Alert Record/Status Alerts NE107) Auxiliary Terminal Action Auxiliary Terminal Action, Edit Breakout Timeout Breakout Torque Burst Command Burst Enable Calibration Button Calibration in Progress (Alert Record/Status Alerts Enable) Calibration in Progress (Alert Record/Status Alerts NE107) Calibration Record Calibration Time Calibration Type Calibrator See Figure B-5 B-5 B-5 B-5 B-5 B-7 B-5 B-9 B-9 B-9 B-9 B-7 B-3, B-11 B-10 B-5 B-5 B-4, B-10 B-9 B-9 B-5 B-5 B-7 B-5 B-7 B-7 B-5 B-9 B-9 B-10 B-10 B-10 B-10 Function/Variable Change Control Mode Change Instrument Mode Change to HART 5 / Change to HART 7 Change Travel/Pressure Select Change Write Protection Clear Records Control Mode Critical NVM Failure (PST Prohibited Electronics Alerts) Critical NVM Failure (Electronics Alerts NE107) Critical NVM Failure Shutdown Custom Characterization Cycle Count Cycle Count Hi (Travel History Alerts Enable) Cycle Count High (Travel History Alerts NE107) Cycle Count High Alert Point Cycle Count/Travel Accum Deadband Days Powered Up DD Information Description Device ID Device Revision Device Setup Device Status Diagnostic Data Available (Alert Record/Status Alerts Enable) Diagnostic Data Available (Alert Record/Status Alerts NE107) Diagnostic in Progress (Alert Record/Status Alerts Enable) Diagnostic in Progress (Alert Record/Status Alerts NE107) Drive Current Failure (Electronics Alerts NE107) Drive Current Failure (PST Prohibited Electronics Alerts) Drive Current Failure Shutdown Drive Signal Drive Signal (Electronics Alerts Enable) Drive Signal (Electronics Alerts NE107) Dynamic Torque See Figure B-6, B-11 B-1, B-5 B-11 B-6, B-11 B-1, B-3, B-5 B-9, B-11 B-6, B-11 B-9 B-8 B-8 B-6, B-11 B-8, B-11 B-8 B-8 B-8 B-8 B-11 B-3 B-3, B-5 B-3 B-3 B-4 B-3, B-11 B-9 B-9 B-9 B-9 B-8 B-9 B-8 B-3, B-11 B-8 B-8 B-5 85 Arborescences du menu de l’interface de communication Manuel d’instructions avril 2021 Function/Variable Edit Cycle Counts Edit Instrument Time Edit Travel Accumulator Effective Area Fail Signal Fallback Recovery Fallback-Sensor Failure Fallback-Sensor/Travel Deviation Feedback Connection Firmware Revision Flash Integrity Failure (Electronics Alerts NE107) Flash Integrity Failure (PST Prohibited Electronics Alerts) Flash Integrity Failure Shutdown Flow Direction Flow Tends to Function Hardware Revision (Device) HART Long Tag HART Tag HART Universal Revision HART Variable Assignments High Friction Breakout Pressure Hi Limit/Cutoff Point Hi Limit/Cutoff Select Hi Soft Cutoff Rate Incoming Pressure Threshold Inlet Pressure Input Characterization Input Range Hi Input Range Lo Instrument Alert Record Instrument Level Instrument Mode Instrument Serial Number Instrument Time is Approximate (Alert Record/Status Alerts Enable) Instrument Time is Approximate (Alert Record/Status Alerts NE107) Integral Enable (Travel & Pressure Tuning) Integral Gain (Travel & Pressure Tuning) Integrator Limit Integrator Saturated Hi (Alert Record/Status Alerts Enable) Integrator Saturated Hi (Alert Record/Status Alerts NE107) Integrator Saturated Lo (Alert Record/Status Alerts Enable) Integrator Saturated Lo (Alert Record/Status Alerts NE107) Integral Dead Zone Last AutoCal Status Last PST Results Leak Class Length Units Lever Arm Length Lever Style Limit Switch Trip Point 86 D103605X0FR See Figure B-8 B-5, B-9 B-8 B-5 B-7 B-6, B-9, B-11 B-9 B-9 B-5, B-7 B-3 B-8 B-9 B-8 B-5 B-5 B-7 B-3 B-3, B-5 B-3, B-5 B-3 B-7 B-7 B-6, B-8 B-6 B-6 B-7 B-5 B-6, B-11 B-5 B-5 B-9 B-3 B-1, B-5 B-3, B-5 B-9 B-9 B-7 B-7 B-7 B-9 B-9 B-9 B-9 B-7 B-10 B-7 B-5 B-5 B-5 B-5 B-7 Function/Variable Limit Switch Valve Close Limit Switch Valve Open Lo Limit/Cutoff Point Lo Limit/Cutoff Select Lo Soft Cutoff Range Low Friction Breakout Pressure Lower Bench Set Manual Calibration Manufacturer (Device) Maximum Allowable Travel Movement Maximum Recorded Temperature Maximum Supply Pressure Message Minimum Recorded Temperature Minimum Required Travel Movement Minor Loop Sensor Failure (PST Prohibited Electronics Alerts) Minor Loop Sensor Failure (PST Prohibited Electronic Alerts) Minor Loop Sensor Failure (Sensor Alert NE107) Minor Loop Sensor Failure Shutdown MLFB Gain (Travel & Pressure Tuning) Model (Device) Nominal Supply Non-Critical NVM Failure (Electronics Alerts NE107) Non-Critical NVM Failure Shutdown Number of Power Ups Outgoing Pressure Threshold Output Circuit Error (Electronics Alerts Enable) Output Circuit Error (Electronics Alerts NE107) Outlet Pressure Output Pressure Limit Enable Output Terminal Enable Packing Type Partial Stroke Test Polling Address Port A Overpressurized (Pressure Alerts Enable) Port A Overpressurized (Pressure Alerts NE107) Port A Pressure Limit Port Diameter Port Type Position Transmitter Pressure A Pressure A-B Pressure B Pressure Control Pressure Deviation Alert Point Pressure Deviation (Pressure Alerts Enable) Pressure Deviation (Pressure Alerts NE107) Pressure Deviation Time Pressure Fallback Active (PST Prohibited Alerts Enable) Pressure Fallback Active (Sensor Alerts Enable) Pressure Fallback Active (Sensor Alerts NE107) Pressure Range High Pressure Range Low See Figure B-5 B-5 B-6, B-8 B-6 B-6 B-7 B-5 B-10 B-3 B-7 B-11 B-7 B-3, B-5 B-11 B-7 B-9 B-9 B-9 B-9 B-7 B-3 B-5 B-8 B-8 B-11 B-7 B-8 B-8 B-5 B-8 B-7 B-5 B-11 B-5 B-8 B-8 B-8 B-5 B-5 B-5 B-3, B-11 B-3, B-11 B-3, B-11 B-9 B-8 B-8 B-8 B-8 B-9 B-9 B-9 B-6 B-6 Manuel d’instructions Arborescences du menu de l’interface de communication D103605X0FR Function/Variable Pressure Sensor Failure (PST Prohibited Alerts Enable) Pressure Sensor Failure (Sensor Alerts NE107) Pressure Sensor Failure Shutdown Pressure Sensors (Calibration) Pressure Tuning Set Pressure Units Program Flow Failure (Partial Stroke Alerts NE107) Program Flow Failure Shutdown Proportional Gain (Travel & Pressure Tuning) PST Abnormal (Partial Stroke Alerts Enable) PST Abnormal (Partial Stroke Alerts NE107) PST Abnormal Criteria PST Abort Criteria PST Enable PST Calibration PST Deferral Reason PST Pass (Partial Stroke Alerts Enable) PST Pass (Partial Stroke Alerts NE107) PST Prohibited (Partial Stroke Alerts Enable) PST Prohibited (Partial Stroke Alerts NE107) PST Result Criticality PST Start Point PST Variables Push Down To PWB Serial Number Quick Release Rated Travel Relay Adjust Relay Type Reference Voltage Failure (Electronics Alerts NE107) Reference Voltage Failure (PST Prohibited Electronics Alerts) Reference Voltage Failure Shutdown Reset PST Abnormal Alert Restart Control Mode Restart Processor Return Lead Seat Type (Trim) Setpoint Short Duration PST Shutdown Activated (Electronics Alerts Enable) Shutdown Activated (Electronics Alerts NE107) Simulate Solenoid Valve SP Rate Close SP Rate Open Spring Rate Spring Rate Units Stabilize/Optimize Stem Diameter Stroke Valve Supply Pressure Supply Pressure Hi (Pressure Alerts Enable) Supply Pressure Hi (Pressure Alerts NE107) Supply Pressure Hi Alert Point avril 2021 See Figure B-9 B-9 B-9 B-10 B-7 B-5 B-9 B-9 B-7 B-9 B-9 B-7 B-7 B-7 B-10 B-7 B-9 B-9 B-9 B-9 B-7 B-7 B-7 B-5 B-3 B-5 B-5 B-10 B-7 B-8 B-9 B-8 B-11 B-6, B-11 B-11 B-7 B-5 B-3, B-8, B-11 B-7 B-8 B-8 B-11 B-5 B-6 B-6 B-5 B-5 B-7, B-11 B-5 B-11 B-3, B-8, B-11 B-8 B-8 B-8 Function/Variable Supply Pressure Lo (PST Prohibited Alerts Enable) Supply Pressure Lo (Pressure Alerts Enable) Supply Pressure Lo Alert Point Switch Closed Temperature Temperature Units Temp Sensor Failure (PST Prohibited Alerts Enable) Temp Sensor Failure (Sensor Alerts NE107) Temp Sensor Failure Shutdown Torque Units Transmitter Output Travel Travel Accumulator (Alert Setup) Travel Accumulator (Travel History) Travel Accumulator Alert Point Travel Accumulator High (Travel History Alerts Enable) Travel Accumulator High (Travel History Alerts NE107) Travel Alert Deadband Travel Control Travel Counts Travel Deviation Travel Deviation (PST Prohibited Alerts Enable) Travel Deviation (Travel Alerts Enable) Travel Deviation (Travel Alerts NE107) Travel Deviation Alert Point Travel Deviation Time Travel Deviation Pressure Fallback Travel Deviation Pressure Fallback Time Travel Hi (Travel Alerts Enable) Travel Hi (Travel Alerts NE107) Travel Hi Hi (Travel Alerts Enable) Travel Hi Hi (Travel Alerts NE107) Travel Hi Alert Point Travel Hi Hi Alert Point Travel Lo (Travel Alerts Enable) Travel Lo (Travel Alerts NE107) Travel Lo Lo (Travel Alerts Enable) Travel Lo Lo (Travel Alerts NE107) Travel Lo Alert Point Travel Lo Lo Alert Point Travel Limit/Cutoff Hi (Travel Alerts Enable) Travel Limit/Cutoff Hi (Travel Alerts NE107) Travel Limit/Cutoff Lo (Travel Alerts Enable) Travel Limit/Cutoff Lo (Travel Alerts NE107) Travel/Pressure Select Travel Sensor Failure (Sensor Alerts NE107) Travel Sensor Failure (PST Prohibited Alerts Enable) Travel Sensor Failure Shutdown Travel Sensor Motion Travel Tuning Set Travel Units Unbalanced Area Upper Bench Set Valve Class See Figure B-8 B-8 B-6, B-8 B-7 B-11 B-5 B-9 B-9 B-9 B-5 B-7 B-3, B-8, B-11 B-8 B-11 B-8 B-8 B-8 B-8 B-9 B-11 B-8 B-9 B-8 B-8 B-8 B-8 B-6 B-6 B-8 B-8 B-8 B-8 B-8 B-8 B-8 B-8 B-8 B-8 B-8 B-8 B-8 B-8 B-8 B-8 B-6, B-9, B-11 B-9 B-9 B-9 B-5, B-7 B-7 B-5 B-5 B-5 B-5 87 Manuel d’instructions Arborescences du menu de l’interface de communication avril 2021 D103605X0FR Function/Variable Valve Manufacturer Valve Model Valve Serial Number Valve Size Valve Style Velocity Gain See Figure B-5 B-5 B-3, B-5 B-5 B-5, B-7 B-7 Function/Variable View Alert Records View/Edit Burst Messages View/Edit Lag Time Volume Booster Write Protection Zero Power Condition Figure B-2. En ligne Figure B-1. Raccourci HART Application Favorites Hot Key 1 2 3 4 See Figure B-9, B-11 B-7 B-6 B-5 B-1, B-3, B-5 B-7 1 2 3 4 Instrument Mode Change Instrument Mode Write Protection Change Write Protection Offline Online Utility HART Diagnostics Online 1 Overview 2 Configure 3 Service Tools Figure B-3. Aperçu 1-7-1 1-6 Identification Pressure Variables 1 2 3 4 Supply Pressure Pressure A Pressure B Pressure A-B 1 1 Overview 1-7 1 2 3 4 5 6 7 Device Information Device Status Analog Input Setpoint Travel Drive Signal Pressure Variables Device Information 1 Identification 2 Revisions 3 Security 1-7-3 Security 1 Write Protection 2 Change Write Protection 1 2 3 4 5 6 7 8 HART Tag HART Long Tag 2 Manufacturer Model Instrument Level Device ID and Serial Numbers Message Description 1-7-2 Revisions 1 2 3 4 5 REMARQUES : 1 LA PRESSION D'ALIMENTATION EST DISPONIBLE POUR LES NIVEAUX D'INSTRUMENTS AD, PD, ODV. 2 LE REPÈRE LONG HART EST DISPONIBLE AVEC HART 7 SEULEMENT. Figure B-4. Configuration assistée 2 Configure 1 2 3 4 88 Guided Setup Manual Setup Alert Setup Calibration 2-1 Guided Setup 1 Device Setup 2 Auto Calibration HART Universal Revision Device Revision Hardware Revision Firmware Revision DD Information 1-7-1-6 Device ID and Serial Numbers 1 2 3 4 Device ID Valve Serial Number Instrument Serial Number PWB Serial Number Manuel d’instructions Arborescences du menu de l’interface de communication D103605X0FR avril 2021 Figure B-5. Configuration manuelle > Mode, protection et configuration manuelle > Instrument 2 2-2-1 Configure Mode and Protection 1 2 3 4 1 2 3 4 Guided Setup Manual Setup Alert Setup Calibration 2-2-2-1 Instrument Mode Change Instrument Mode Write Protection Change Write Protection 2-2 2-2-2 Manual Setup Instrument 1 2 3 4 5 6 7 1 2 3 4 5 6 7 Mode and Protection Instrument Travel/Pressure Control Tuning Valve and Actuator Partial Stroke Test (PST) Outputs 1 2 3 4 5 Accessories 1 2 3 4 5 6 Units Valve Trim Actuator Accessories 3 3 Lever Style 1 Lever Style 2 Lever Arm Length HART Tag HART Long Tag Description Message Polling Address 1 2-2-2-2 Identification Serial Numbers Units Terminal Box Analog Input Range Spec Sheet Edit Instrument Time Serial Numbers 1 Instrument Serial Number 2 Valve Serial Number 2-2-2-3 Units 1 Pressure Units 2 Temperature Units 3 Analog Input Units 2-2-2-4 Terminal Box 2-2-2-6-3 1 Calibration Button 2 Auxiliary Terminal Action 2 3 Edit Auxiliary Terminal Action Trim 1 2 3 4 5 6 7 8 2-2-2-6-5 Volume Booster Quick Release Solenoid Valve Position Transmitter Limit Switch Valve Open Limit Switch Valve Close 2-2-2-6-4-6 1 2 3 4 5 2-2-2-6 Spec Sheet Identification Seat Type Leak Class Port Diameter Port Type Flow Direction Push Down To Flow Tends To Unbalanced Area 2-2-2-6-4 2-2-2-6-2 Actuator Valve 1 2 3 4 5 6 7 8 9 1 2 3 4 5 6 7 8 9 Actuator Manufacturer Actuator Model Actuator Size Actuator Selection Travel Lever Style Effective Area Spring Rate Air 2-2-2-5 2 Analog Input Range 1 Input Range Hi 2 Input Range Lo 2-2-2-6-1 Valve Manufacturer Valve Model Valve Serial Number Valve Style Stem Diameter Packing Type Valve Travel Inlet/Outlet Pressures Torque 3 Units 1 2 3 4 5 Travel Units Length Units Area Units Spring Rate Units Torque Units 2-2-2-6-2-4 Valve Style 1 Valve Style 2 Valve Size 3 Valve Class 2-2-2-6-2-7 2-2-2-6-4-9 Air 1 2 3 4 Air Upper Bench Set Lower Bench Set Nominal Supply Valve Travel 2-2-2-6-4-5 1 Rated Travel 2 Actual Travel Travel 1 Feedback Connection 2 Travel Sensor Motion 2-2-2-6-2-8 Inlet/Outlet Pressures 2-2-2-6-2-9 Torque 1 Inlet Pressure 2 Outlet Pressure 3 1 Dynamic Torque 2 Breakout Torque REMARQUES : 1 LE REPÈRE LONG HART EST DISPONIBLE AVEC HART 7. 2 L'ACTION DE LA BORNE ET LE PARAMÉTRAGE DE L'ACTION DE LA BORNE AUXILIAIRE SONT DISPONIBLES AVEC L'INSTRUMENT DE NIVEAU ODV. 3 DISPONIBLE POUR UNE VALVE ROTATIVE. 89 Manuel d’instructions Arborescences du menu de l’interface de communication avril 2021 D103605X0FR Figure B-6. Configuration manuelle > Régulation de la course/pression 2-2-3 Travel/Pressure Control 2-2 Manual Setup 1 2 3 4 5 6 7 Mode and Protection Instrument Travel/Pressure Control Tuning Valve and Actuator Partial Stroke Test (PST) Outputs 1 2 3 4 5 6 7 8 Travel/Pressure Select Change Travel/Pressure Select Cutoffs/Limits Pressure Control Pressure Fallback 1 Control Mode Characterization Dynamic Response 2-2-3-7 (HC) 2-2-3-8 (AD, PD, ODV) Dynamic Response 1 SP Rate Open 2 SP Rate Close 3 View/Edit Lag Time 2-2-3-3 Cutoffs and Limits 1 2 3 4 5 6 Hi Limit/Cutoff Select Hi Limit/Cutoff Point Hi Soft Cutoff Rate Lo Limit/Cutoff Select Lo Limit/Cutoff Point Lo Soft Cutoff Rate 2-2-3-4 Pressure Control 1 Pressure Range High 2 Pressure Range Low 2-2-3-5 (AD, PD, ODV) Pressure Fallback 2-2-3-6 (HC) 2-2-3-7 (AD, PD, ODV) Characterization 1 Input Characterization 2 Custom Characterization 1 2 3 4 1 Tvl Dev Press Fallback Tvl Dev Press Fallback Time Fallback Recovery Supply Pressure Lo Alert Point 2-2-3-5 (HC) 2-2-3-6 (AD, PD, ODV) Control Mode REMARQUE : 1 LA PRESSION DE SECOURS EST DISPONIBLE POUR LES INSTRUMENTS DE NIVEAU AD, PD, ET ODV. 90 1 Control Mode 2 Change Control Mode 3 Restart Control Mode Manuel d’instructions Arborescences du menu de l’interface de communication D103605X0FR avril 2021 Figure B-7. Configuration manuelle > Paramétrage par configuration manuelle > Sorties 2-2-4-1 Travel Tuning 2-2-4 1 Travel Tuning 2 Pressure Tuning 3 Travel/Pressure Integral Settings 2-2 Manual Setup Travel/Pressure Integral Settings Mode and Protection Instrument Travel/Pressure Control Tuning Valve and Actuator Partial Stroke 1 Outputs WITHOUT I/O PACKAGE 1 2 3 4 5 6 7 2-2-6 Partial Stroke 1 2 3 4 5 Output Terminal Config Limit Switch Configuration Alert Switch Configuration HART Var Assignments Transmitter Output Burst Mode 1 Output Terminal Enable 2 Function 3 Fail Signal Burst Mode 1 2 3 4 5 6 7 1 PST Enable PST Start Point PST Variables Return Lead Short Duration PST Max Allowable Travel Movement Min Required Travel Movement 2-2-6-2 Test Acceptance Criteria PST Alert Behavior 1 PST Abnormal Criteria 2 PST Abort Criteria 3 PST Result Criticality 1 2 3 4 5 Outgoing Pressure Threshold Incoming Pressure Threshold High Friction Breakout Press Low Friction Breakout Press Breakout Timeout 2 2-2-6-2 (HC, AD, PD) 2-2-7-2 (ODV) HART Var Assignments Limit Switch Configuration 1 2 3 4 1 Limit Switch Trip Point 2 Switch Closed Primary Variable (PV) Secondary Variable (SV) Tertiary Variable (TV) Quaternary Variable (QV) Test Configuration 2-2-6-3 Output Terminal Config Pressure Tuning Set Proportional Gain MLFB Gain Integral Enable Integral Gain 2-2-6-1 Test Configuration Test Acceptance Criteria PST Alert Behavior PST Deferral Reason Last PST results 2-2-6-1 (HC, AD, PD) 2-2-7-1 (ODV) 2-2-6-6 (HC, AD, PD) 2-2-7-6 (ODV) 2-2-6-4 (HC, AD, PD) 2-2-7-4 (ODV) 1 2 3 4 5 Valve Style Actuator Style Feedback Connection Relay Type Zero Power Condition Travel Sensor Motion Max Supply Pressure Travel Tuning Set Proportional Gain Velocity Gain MLFB Gain Integral Enable Integral Gain Stabilize/Optimize Pressure Tuning Valve and Actuator Outputs 1 Burst Enable 2 View/Edit Burst Messages 2-2-4-2 2-2-5 WITH I/O PACKAGE 2-2-6 (HC, AD, PD) 2-2-7 (ODV) 1 2 3 4 5 6 2-2-4-3 1 Integral Dead Zone 2 Integrator Limit WITH I/O PACKAGE 1 2 3 4 5 6 7 1 2 3 4 5 6 7 Tuning 2-2-6-3 (HC, AD, PD) 2-2-7-3 (ODV) Alert Switch Configuration 1 Alert Switch Source WITHOUT I/O PACKAGE 2-2-6 (HC, AD, PD) 2-2-7 (ODV) 2-2-6-1 (HC, AD, PD) 2-2-7-1 (ODV) Outputs HART Var Assignments 1 HART Var Assignments 2 Burst Mode 1 2 3 4 Primary Variable (PV) Secondary Variable (SV) Tertiary Variable (TV) Quaternary Variable (QV) 2-2-6-2 (HC, AD, PD) 2-2-7-2 (ODV) Burst Mode 1 Burst Enable 2 View/Edit Burst Messages 2 REMARQUES : 1 LA COURSE PARTIELLE EST DISPONIBLE POUR L'INSTRUMENT DE NIVEAU ODV. 2 L'ÉTIQUETTE INDIQUE « MODE RAFALE » POUR HART 5. 91 Manuel d’instructions Arborescences du menu de l’interface de communication avril 2021 D103605X0FR Figure B-8. Configuration de l’alerte > Éléments électroniques dans l’historique de course 2-3-1-1 2-3-1 2 Configure 1 2 3 4 1 Drive Signal 2 Shutdown Activated 3 Output Circuit Error 1 Electronic Alerts Enable 2 Electronic Alerts NE107 4 3 Electronic Alerts Shutdown Guided Setup Manual Setup Alert Setup Calibration Alert Setup Electronics Pressure Travel Travel History Partial Stroke 1 Sensors Alert Record/Status Electronic Alerts Shutdown Electronic Alerts NE107 1 2 3 4 5 1 2 3 4 5 6 7 8 Drive Current Failure Shutdown Critical NVM Failure Shutdown Non-Critical NVM Failure Shutdown Flash Integrity Failure Shutdown Reference Voltage Failure Shutdown 2-3-2 Pressure 1 2 2 3 4 5 6 7 8 2-3-4-1 Pressure Alerts Enable 1 2 3 4 Pressure Alerts NE107 1 2 3 4 2-3-3 Supply Pressure Hi Supply Pressure Lo 2 Pressure Deviation Port A Overpressurized Travel Travel History 1 2 3 4 5 Supply Pressure Hi Supply Pressure Lo 2 Pressure Deviation Port A Overpressurized 2-3-2-2 Travel History Alerts Enable 2-3-4 1 2 3 4 5 6 7 8 Travel History Alerts Enable Travel History Alerts NE107 4 Cycle Count/Travel Accum Deadband Cycle Counter Travel Accumulator 2-3-4-5 Travel Accumulator 2-3-3-1 Travel Alerts Enable Travel Alerts NE107 Travel Setpoint Travel Alert DB Travel Deviation Travel Limit Travel Limit/Cutoff 2-3-4-2 1 Travel Accumulator 2 Edit Travel Accumulator 3 Travel Accumulator Alert Point Drive Current Failure Drive Signal Critical NVM Failure Non-Critical NVM Failure Flash Integrity Failure Reference Voltage Failure Shutdown Activated Output Circuit Error 3 2-3-2-1 Pressure Alerts Enable Pressure Alert NE107 4 Supply Pressure Supply Pressure Hi Alert Point Supply Pressure Lo Alert Point Pressure Deviation Alert Point Pressure Deviation Time Port A Pressure Limit Output Pressure Limit Enable 1 Cycle Count Hi 2 Tvl Accum Hi 3 2-3-1-2 2-3-1-3 2-3 1 2 3 4 5 6 7 Electronic Alerts Enable Electronics Travel Alerts Enable 4 1 2 3 4 5 6 7 2-3-3-8 Travel History Alerts NE107 1 Cycle Count High 2 Travel Accumulator High 2-3-4-4 Tvl Deviation Tvl Hi Hi Tvl Lo Lo Tvl Hi Tvl Lo Tvl Limit/Cutoff Hi Tvl Limit/Cutoff Lo 2-3-3-2 Travel Limit/Cutoff Travel Alerts NE107 1 Hi Limit/Cutoff Point 2 Lo Limit/Cutoff Point 1 2 3 4 5 6 7 2-3-3-7 Cycle Counter Travel Limit 1 Cycle Count 2 Edit Cycle Counts 3 Cycle Count High Alert Point 1 2 3 4 Travel Hi Hi Alert Point Travel Lo Lo Alert Point Travel Hi Alert Point Travel Lo Alert Point REMARQUES : 1 LA COURSE PARTIELLE EST DISPONIBLE POUR L'INSTRUMENT DE NIVEAU ODV. Travel Deviation Travel Hi Hi Travel Lo Lo Travel Hi Travel Lo Travel Limit/Cutoff Hi Travel Limit/Cutoff Lo 2-3-3-6 Travel Deviation 1 Travel Deviation 2 Travel Deviation Alert Point 3 Travel Deviation Time 2 LA PRESSION D'ALIMENTATION EST DISPONIBLE POUR LES NIVEAUX D'INSTRUMENTS AD, PD, ODV. 3 L'ERREUR DU CIRCUIT DE SORTIE EST DISPONIBLE QUAND LA FONCTION DU TRANSMETTEUR EST CONFIGURÉE. 4 LES ALERTES NE107 SONT DISPONIBLES POUR HART 7. TOUTES LES SÉQUENCES DE TOUCHES D'ACCÈS RAPIDE HART 5 DIMINUENT D'UN NOMBRE APRÈS L'ENTRÉE DE CONFIGURATION DE L'ALERTE NE107. 92 Manuel d’instructions Arborescences du menu de l’interface de communication D103605X0FR avril 2021 Figure B-9. Configuration de l’alerte > Course partielle dans Enregistrement/état de l’alerte 2-3-5-1 (ODV) Partial Stroke Alerts Enable 1 PST Abnormal 2 PST Pass 3 PST Prohibited 2-3-5 (ODV) Partial Stroke 2-3 1 2 3 4 Alert Setup 1 2 3 4 5 6 7 Electronics Pressure Travel Travel History Partial Stroke 1 Sensors Alert Record/Status Partial Stroke Alerts NE107 1 2 3 4 2-3-5-4 (ODV) 1 2 3 4 5 6 7 Alert Record/Status Alert Record/Status Alerts Enable Alert Record/Status Alerts NE107 View Alert Records Clear Records Instrument Alert Record Edit Instrument Time 2-3-5-2 (ODV) PST Abnormal PST Pass PST Prohibited Program Flow Failure PST Prohibited Alerts Enable 2-3-6 (HC, AD, PD) 2-3-7 (ODV) 1 2 3 4 5 6 Partial Stroke Alerts Enable Partial Stroke Alerts NE107 3 Partial Stroke Alerts Shutdown PST Prohibited Alerts Enable 3 PST Prohibited Electronic Alerts Travel Sensor Failure Pressure Sensor Failure Temp Sensor Failure Pressure Fallback Active Supply Pressure Lo Travel Deviation 2-3-5-3 (ODV) Partial Stroke Alerts Shutdown 1 Program Flow Failure Shutdown 2-3-5-4-1 (ODV) PST Prohibited Electronic Alerts 1 2 3 4 5 Critical NVM Failure Drive Current Failure Reference Voltage Failure Minor Loop Sensor Failure Flash Integrity Failure 2-3-6-2 (HC, AD, PD) 2-3-7-2 (ODV) 2-3-5 (HC, AD, PD) 2-3-6 (ODV) Alert Record/Status Alerts NE107 1 2 3 4 5 6 7 8 9 Alert Record Not Empty Alert Record Full Instrument Time is Approximate Calibration in Progress Autocal in Progress Diagnostic in Progress Diagnostic Data Avail Integrator Sat Hi Integrator Sat Lo 2-3-6 -1 (HC, AD, PD) 2-3-7-1 (ODV) Alert Record/Status Alerts Enable 1 2 3 4 5 6 7 8 9 Alert Record Not Empty Alert Record Full Instrument Time is Approximate Calibration in Progress Autocal in Progress Diagnostic in Progress Diagnostic Data Avail Integrator Sat Hi Integrator Sat Lo 2-3-5-1 (HC, AD, PD) 2-3-6-1 (ODV) Sensors 1 2 3 4 5 6 2 Sensor Alerts Enable Sensor Alerts NE107 3 Sensor Alerts Shutdown Change Travel/Pressure Select Travel/Pressure Select 2 Fallback Recovery 2 Sensor Alerts Enable 1 Pressure Fallback Active 2 2-3-5-2 (HC, AD, PD) 2-3-6-2 (ODV) Sensor Alerts NE107 2-3-5-4 (HC, AD, PD) 2-3-6-4 (ODV) 1 2 3 4 5 Change Travel/Pressure Select 1 2 3 4 Travel Control Pressure Control Fallback-Sensor Failure Fallback-Sensor/Tvl Deviation 2 Travel Sensor Failure Pressure Sensor Failure Temp Sensor Failure Minor Loop Sensor Failure Pressure Fallback Active 2 2-3-5-3 (HC, AD, PD) 2-3-6-3 (ODV) Sensor Alerts Shutdown 1 2 3 4 Travel Sensor Failure Shutdown Pressure Sensor Failure Shutdown Temp Sensor Failure Shutdown Minor Loop Sensor Failure Shutdown REMARQUES : 1 LA COURSE PARTIELLE EST DISPONIBLE POUR L'INSTRUMENT DE NIVEAU ODV. 2 LES SECTIONS DU MENU DE LA PRESSION DE SECOURS SONT DISPONIBLES POUR LES INSTRUMENTS DE NIVEAU AD, PD, ET ODV. 3 LES ALERTES NE107 SONT DISPONIBLES POUR HART 7. LES SÉQUENCES D'ACCÈS RAPIDE HART 5 SE RÉDUISENT D'UN CHIFFRE APRÈS LA SAISIE DE LA CONFIGURATION D'ALERTE NE107. 93 Manuel d’instructions Arborescences du menu de l’interface de communication avril 2021 D103605X0FR Figure B-10. Étalonnage 2 Configure HART 5 2-4-1 Guided Setup Manual Setup Alert Setup Calibration Travel Calibration HART 5 1 2 3 4 2-4 Calibration 1 2 3 4 Travel Calibration Relay Adjust Sensor Calibration PST Calibration 1 1 2 3 4 HART 7 Auto Calibration Last AutoCal Status Manual Calibration Calibration Record HART 7 2-4-1 Travel Calibration 1 2 3 4 5 6 2-4-3 Sensor Calibration 1 Pressures Sensors 2 Analog Input 2 Auto Calibration Last AutoCal Status Manual Calibration Calibration Type Calibration Time Calibrator REMARQUES : 1 L'ÉTALONNAGE PST EST DISPONIBLE POUR LE NIVEAU D'INSTRUMENT ODV. 2 L'ENTRÉE ANALOGIQUE IS NON DISPONIBLE WHEN THE COMMUTATEUR DIP IS SET TO MULTI-DROP. Figure B-11. Outils de maintenance 3-4-1-4 Pressure Variables 3-2 Alert Record 3 Service Tools 1 2 3 4 5 6 Device Status Alert Record Diagnostics Variables Maintenance Simulate 5 Maintenance 1 2 3 4 1 2 3 4 1 View Alert Records 2 Clear Records 3-4-1 3-3 Diagnostics 1 Stroke Valve 2 Partial Stroke Test 1 3-4 3-5 Variables Stabilize/Optimize Restart Processor Reset PST Abnormal Alert Change to HART 5 4 1 2 3 4 5 6 7 8 3 Travel/Pressure Control Mode Analog Input Temperature Travel Counts Characterization Travel History Run Time Extremes Supply Pressure Pressure A Pressure B Pressure A-B 2 Travel/Pressure 1 2 3 4 5 6 7 Setpoint Travel Drive Signal Pressure Variables Change Travel/Pressure Select Travel/Pressure Select Fallback Recovery 2 3-4-2 Control Mode 1 Control Mode 2 Change Control Mode 3 Restart Control Mode 3-4-8 Run Time Extremes 1 2 3 4 Maximum Recorded Temperature Minimum Recorded Temperature Days Powered Up Number of Power Ups 3-4-6 3-4-7 Travel History 1 Cycle Count 2 Travel Accumulator REMARQUES : 1 2 3 4 5 94 LE TEST DE COURSE PARTIELLE EST DISPONIBLE POUR LE NIVEAU D'INSTRUMENT ODV. LA PRESSION D'ALIMENTATION ET LA RÉCUPÉRATION DE SECOURS SONT DISPONIBLES POUR LES NIVEAUX AD, PD, ODV. L'ALERTE ANORMALE DE RESET PST EST DISPONIBLE POUR L'INSTRUMENT DE NIVEAU ODV. L'ÉTIQUETTE EST « PASSER À HART 7 » POUR HART 5. HART 7 UNIQUEMENT. Characterization 1 Input Characterization 2 Custom Characterization Manuel d’instructions Glossaire D103605X0FR 2021 avril Glossaire Accumulateur de course Capacité d’un instrument FIELDVUE à enregistrer un changement total de course. La valeur de l’accumulateur augmente lorsque l’ampleur du changement dépasse la bande morte de l’accumulateur de course. Pour réinitialiser l’accumulateur de course, il suffit de le définir sur zéro. Alerte du compteur de cycles Vérifie la différence entre le compteur de cycles et le point d’alerte du compteur de cycles. L’alerte de compteur de cycles est active lorsque la valeur du compteur de cycles dépasse le point d’alerte du compteur de cycles. Elle s’efface une fois que le compteur de cycles a été redéfini à une valeur inférieure au point d’alerte. Alerte du signal d’entraînement Adresse d’interrogation Adresse de l’instrument. Si le contrôleur numérique de vanne est utilisé dans une configuration point-à-point, régler l’adresse d’interrogation sur 0. S’il est utilisé dans une configuration multipoint ou dans une application de plage fractionnée, régler l’adresse d’interrogation à une valeur comprise entre 0 et 15 pour HART 5 et 0 à 63 pour HART 7. Vérifie le signal d’entraînement et la course étalonnée. Si l’une des conditions suivantes est présente pendant plus de 20 secondes, l’alerte du signal d’entraînement est activée. Si aucune de ces conditions ne se réalise, l’alerte est annulée. Si la condition d’alimentation nulle = fermée L’alerte est activée lorsque : signal d’entraînement <10 % et course étalonnée >3 % signal d’entraînement >90 % et course étalonnée <97 % Alerte de course Vérifie la course parcourue par rapport aux points d’alerte haut et bas des points d’alerte. L’alerte de course est activée si le point haut ou bas est dépassé. Une fois qu’un point haut ou bas est dépassé, la course parcourue doit effacer ce point en passant par la bande morte d’alerte de course avant que l’alerte ne s’efface. Quatre alertes de course sont disponibles : alerte de course haute, alerte de course basse, alerte de course haute haute et alerte de course basse basse. Alerte de déviation de course Vérifie la différence entre la course cible et la course parcourue. Si la différence dépasse le point d’alerte de déviation de course pendant une durée supérieure à celle de la déviation de course, l’alerte de déviation de course est activée. Elle reste activée jusqu’à ce que la différence soit inférieure à la valeur du point d’alerte de déviation de course. Alerte de l’accumulateur de course Vérifie la différence entre la valeur de l’accumulateur de course et le point d’alerte de l’accumulateur de course. L’alerte de l’accumulateur de course est activée lorsque la valeur de l’accumulateur de course dépasse le point d’alerte de l’accumulateur de course. Elle s’efface une fois que l’on a redéfini l’accumulateur de course à une valeur inférieure au point d’alerte. Si la condition d’alimentation nulle = ouverte L’alerte est activée lorsque : signal d’entraînement <10 % et course étalonnée <97 % signal d’entraînement >90 % et course étalonnée >3 % Algorithme Ensemble d’étapes logiques permettant de résoudre un problème ou d’accomplir une tâche. Un programme informatique contient un ou plusieurs algorithmes. Alphanumérique Composé de lettres et de chiffres. ANSI (acronyme) L’acronyme ANSI signifie American National Standards Institute (Institut des normes nationales américaines) Bande morte d’alerte de course Course, en pourcentage de la course parcourue, nécessaire pour effacer une alerte de course, une fois qu’elle est active. Les valeurs valides sont comprises entre -25 % et 125 %. Bande morte de l’accumulateur de course Zone située autour du point de référence de la course définie par la dernière augmentation de l’accumulateur. Cette zone doit être dépassée avant de pouvoir compter un changement de course. Les valeurs valides sont comprises entre 0 % et 100 %. 95 Manuel d’instructions Glossaire avril 2021 Boucle de régulation Agencement des composants physiques et électroniques pour le contrôle du procédé. Les composants électroniques de la boucle permettent de mesurer en continu un ou plusieurs aspects du procédé, puis d’altérer les aspects nécessaires pour obtenir une condition de procédé souhaitée. Une boucle de régulation simple ne mesure qu’une seule variable. Les boucles de régulation plus sophistiquées mesurent de nombreuses variables et maintiennent des relations spécifiques entre ces variables. Capteur de course Dispositif au sein de l’instrument FIELDVUE qui détecte le mouvement de la tige ou de l’axe de la vanne. Le capteur de course du DVC6200 est le capteur à effet Hall qui mesure la position de l’assemblage magnétique. Capteur de pression Appareil interne de l’instrument FIELDVUE qui détecte la pression pneumatique. Le DVC6200 est doté de trois capteurs de pression : un pour la mesure de la pression d’alimentation et deux autres pour détecter les pressions de sortie. Capteur de température Dispositif au sein de l’instrument FIELDVUE qui mesure la température interne de l’instrument. Caractéristique d’entrée La relation entre la course parcourue et l’entrée en plage. Les valeurs possibles sont les suivantes : linéaire, pourcentage égal et ouverture rapide. D103605X0FR Compteur de cycles en bande morte Zone située autour du point de référence de la course (défini par le dernier incrément du compteur de cycles), en pourcentage de la distance parcourue. La bande morte doit être dépassée avant qu’un changement de course ne puisse être comptabilisé comme un cycle. Les entrées valides sont comprises entre 0 % et 100 %. La valeur standard est comprise entre 2 % et 5 %. Condition d’alimentation nulle Position de la vanne (ouverte ou fermée) quand la source d’électricité est retirée de l’instrument. La condition d’alimentation nulle (Zero Power Condition ou ZPC) est déterminée par l’action du relais et de l’actionneur comme il suit : Direct à simple action (relais C) En cas de perte d’alimentation électrique l’instrument fait passer son débit d’air de l’orifice A à zéro. À double action (relais A) En cas de perte d’alimentation électrique l’instrument fait passer son débit d’alimentation d’air sortant de l’orifice B à un débit complet. L’orifice A demeure à un débit nul. Inverse à action simple (relais B) En cas de perte d’alimentation électrique l’instrument fait passer son débit d’alimentation d’air sortant de l’orifice B à un débit complet. Configuration Instructions stockées et paramètres de fonctionnement d’un instrument FIELDVUE. Contrôleur Dispositif qui fonctionne automatiquement pour réguler une variable contrôlée. Convertisseur de courant en pression (I/P) Charge du siège Force exercée sur le siège de la vanne, généralement exprimée en livres-force par pouce de la circonférence de l’orifice. La charge du siège est déterminée par les exigences de fermeture. Classe ANSI Pression/température nominale de la vanne. Classe de fuite Définit la fuite admissible par une vanne lorsqu’elle est fermée. Les numéros de classe de fuite sont répertoriés en deux normes : ANSI/FCI 70‐2 et IEC 534-4. Compteur de cycles Capacité d’un instrument FIELDVUE à enregistrer le nombre de fois que la course change de direction. Le changement de direction doit intervenir après le dépassement de la bande morte pour pouvoir être comptabilisé comme un cycle. 96 Composant ou dispositif électronique qui convertit un signal analogique en un signal de sortie de pression pneumatique proportionnel. Coupure de course Définit le point de coupure de la course, en pourcentages de la course parcourue. Il existe deux coupures de course : « élevée » et « faible ». Une fois que la course dépasse le seuil de coupure, le signal du variateur est réglé sur maximum ou minimum, selon le signal de commande Zéro et si la coupure est « élevée » ou « faible ». La durée d’ouverture minimale ou la durée minimale de fermeture ne fonctionnent pas lorsque la course est parvenue au-delà du seuil de coupure. Utiliser la coupure de course pour obtenir la charge du siège souhaitée ou pour s’assurer que la vanne est complètement ouverte. Courant d’entrée Le signal de courant provenant du système de contrôle-commande qui sert d’entrée analogique à l’instrument. Voir aussi signal d’entrée. Manuel d’instructions Glossaire D103605X0FR Course Mouvement de la tige ou de l’axe de la vanne qui modifie la quantité d’ouverture ou de fermeture de la vanne. 2021 avril Ensemble de réglage Valeurs prédéfinies qui identifient les réglages de gain d’un instrument FIELDVUE. Le jeu de réglage et la pression d’alimentation déterminent ensemble la réponse d’un instrument aux changements de signal d’entrée. Course Course, en pourcentage de la course étalonnée, correspondant à la plage d’entrée. Course complète Courant, en mA, qui correspond au point où le parcours de la course est à son maximum, par exemple, lorsqu’elle est limitée par les butées de course mécaniques. Délai du filtre au point de consigne (temps de retard) La constante de temps, en secondes, pour le premier filtre d’entrée. La valeur par défaut de 0 seconde permet de contourner le filtre. Gain Le rapport entre le changement de sortie et le changement d’entrée. Garde numérique Minuteur que le microprocesseur doit réactiver périodiquement. Si le microprocesseur n’est pas en mesure de réactiver le minuteur, l’instrument passe à zéro. HART (acronyme) L’acronyme HART signifie Highway Addressable Remote Transducer (Transducteur à distance adressable par bus). Limite de course Déviation de course La différence entre le signal d’entrée analogique (pourcentage de l’entrée étendue), la course « cible » et la course réelle « parcourue ». Un paramètre de configuration qui définit la course maximale admissible (en pourcentage de la course parcourue) de la vanne. Pendant le fonctionnement, la cible de la course ne dépasse pas cette limite. Il existe deux limites de course : « haute » et « basse ». Généralement, la limite inférieure de course est utilisée pour éviter que la vanne ne se ferme complètement. Durée de déviation de course Durée, en secondes, que la déviation de course doit dépasser avant que l’alerte ne soit activée. Les entrées valides sont comprises entre 1 et 60 secondes. Durée de la course La durée, en secondes, requise pour déplacer la vanne de sa position complètement ouverte vers complètement fermée, ou vice versa. Écart Généralement, il s’agit de la différence entre le point de consigne et la variable procédé. Plus généralement, il s’agit de tout écart par rapport à une valeur ou à un motif attendu. Égal pourcentage Caractéristique de débit de vanne pour laquelle des incréments égaux de la course de la tige de vanne produisent des variations de pourcentage égales dans le débit existant. Une des caractéristiques d’entrée disponibles pour un instrument FIELDVUE. Voir aussi : ouverture linéaire et rapide. Linéaire Caractéristique d’un débit de vanne où les variations du débit sont directement proportionnelles aux variations de course de la tige de vanne. Une des caractéristiques d’entrée disponibles pour un instrument FIELDVUE. Voir aussi, pourcentage égal et ouverture rapide. Linéarité, dynamique La linéarité (indépendante) correspond à l’écart maximum entre une ligne droite convenant le mieux aux courbes d’ouverture et de fermeture et une ligne représentant la valeur moyenne de ces courbes. Logiciels Microprocesseur ou programmes informatiques et routines qui résident dans une mémoire modifiable (généralement de la RAM), contrairement au micrologiciel, qui comprend des programmes et des routines qui sont programmés en mémoire (généralement la ROM) lors de la fabrication de l’instrument. Les logiciels peuvent être manipulés pendant le fonctionnement normal, le micrologiciel ne peut pas. 97 Manuel d’instructions Glossaire avril 2021 Maître principal Les maîtres sont des appareils de communication. Un maître principal est un appareil de communication qui est relié de façon permanente à un instrument de terrain. En général, le maître principal est un système de contrôle-commande compatible avec HART ou un ordinateur exécutant le logiciel ValveLink. En revanche, il est rare qu’un maître secondaire soit branché en permanence à un instrument de terrain. L’interface de communication ou un ordinateur exécutant le logiciel ValveLink communiquant par le biais d’un modem HART pourrait être considéré comme un maître secondaire. Remarque : Si un type de maître prend un instrument hors service, le même type de maître doit le remettre en service. Par exemple, si un appareil configuré en tant que maître principal prend un instrument hors service, un dispositif configuré en tant que maître principal doit être utilisé pour mettre l’instrument en service. D103605X0FR Menu Une liste de programmes, commandes ou autres activités que l’on peut sélectionner à l’aide des touches fléchées pour mettre en surbrillance l’élément, puis en appuyant sur ENTER (entrée) ou en saisissant la valeur numérique de la section du menu. Mode contrôle Définit l’endroit où l’instrument atteint son point de consigne. Les modes contrôle suivants sont disponibles sur tous les instruments FIELDVUE : Analogique L’instrument accède au point de consigne sur la boucle de 4‐20 mA. Numérique L’instrument accède au point de consigne numériquement, par le lien de communication HART. Test Ce n’est pas un mode sélectionnable par un utilisateur. L’interface de communication ou le logiciel ValveLink place l’instrument dans ce mode à chaque fois qu’il doit déplacer la vanne, comme pour les tests d’étalonnage ou de diagnostic. Mode contrôle, redémarrage Mémoire Type de semi-conducteur utilisé pour le stockage de programmes ou de données. Les instruments FIELDVUE utilisent trois types de mémoire : mémoire vive (RAM), mémoire morte (ROM) et mémoire non volatile (NVM). Voir également ces listes dans ce glossaire. Mémoire morte (ROM) Mémoire dans laquelle les informations sont stockées au moment de la fabrication de l’instrument. On peut examiner le contenu de la ROM, mais pas le changer. Mémoire non volatile (NVM) Type de mémoire d’un semi-conducteur qui conserve son contenu même si l’alimentation est déconnectée. Le contenu de la NVM peut être modifié pendant la configuration, contrairement à la ROM, qui ne peut être modifiée qu’au moment de la fabrication de l’instrument. La mémoire non volatile stocke les données de redémarrage de la configuration. Mémoire vive (RAM) Type de mémoire d’un semi-conducteur normalement utilisée par le microprocesseur lors d’un fonctionnement normal, ce qui permet une récupération et un stockage rapides des programmes et des données. Voir aussi mémoire morte (ROM) et mémoire non volatile (NVM). 98 Détermine le mode de commande de l’instrument après un redémarrage. Voir la section « Mode contrôle» pour les modes de commande de redémarrage disponibles. Mode de l’instrument Détermine si l’instrument répond à son signal d’entrée analogique. Il existe deux modes d’instrument : « En service » : pour un instrument entièrement fonctionnel, la sortie de l’instrument est modifiée en réponse à une modification de l’entrée analogique. Engénéral, il n’est pas possible de modifier la configuration ou l’étalonnage lorsque le mode de l’instrument est « En service ». « Hors service » : la sortie de l’instrument ne change pas en fonction des changements de l’entrée analogique lorsque le mode de l’instrument est « Hors service ». Certains paramètres de configuration ne peuvent être modifiés que lorsque le mode de l’instrument est « Hors service ». Mouvement du capteur de course En augmentant ou en diminuant la pression de l’air, l’aimant se déplace vers le haut ou vers le bas, ou l’axe rotatif tourne dans le sens horaire ou dans le sens anti-horaire. L’assistant de configuration demande s’il peut déplacer la vanne pour déterminer la course. N° d’identification de l’appareil Identifiant unique intégré dans l’instrument à l’usine. Niveau de l’instrument Détermine les fonctions disponibles pour l’instrument. Voir le tableau 5‐1. Manuel d’instructions Glossaire D103605X0FR Numéro de série de l’instrument Le numéro de série assigné au circuit imprimé par l’usine, mais peut être modifié lors de la configuration. Le numéro de série de l’instrument doit correspondre au numéro de série sur la plaque signalétique de l’instrument. Octet Unité de chiffres binaires (bits). Un octet se compose de huit bits. Ouverture rapide Caractéristique du débit de vanne où la majeure partie du changement de débit a lieu pour les petites portions de course de la tige à partir de la position fermée. La courbe de caractéristique de débit est linéaire pendant les premiers 40 % de la course de la tige. Une des caractéristiques d’entrée disponibles pour un instrument FIELDVUE. Voir aussi, pourcentage égal et linéaire. Parallèle En simultané : dit d’une transmission de données sur deux canaux ou plus en même temps. Plage d’entrée La plage du signal d’entrée analogique correspondant au parcours de la course. Point bas bas d’alerte de course Valeur de la course, en pourcentage de la course étendue, qui, lorsqu’elle est dépassée, déclenche l’alerte basse basse des alertes de course. Les valeurs valides sont comprises entre -25 % et 125 %. Point bas d’alerte de course Valeur de la course, en pourcentage de la course étendue, qui, lorsqu’elle est dépassée, déclenche l’alerte basse des alertes de course. Les valeurs valides sont comprises entre -25 % et 125 %. Point d’alerte Valeur réglable qui, lorsqu’elle est dépassée, active une alerte. Point d’alerte de déviation de course Une valeur réglable pour la course cible et la course parcourue, exprimée en pourcentage, lorsque cette valeur est dépassée par la déviation de course pendant une période supérieure à la durée de la déviation de course, l’alerte de déviation de course est activée. Les valeurs valides sont comprises entre 0 % et 100 %. Généralement, cette valeur est définie sur 5%. 2021 avril Point d’alerte de l’accumulateur de course Valeur réglable qui, lorsqu’elle est dépassée, active l’alerte de l’accumulateur de course. Les valeurs valides sont comprises entre 0 % et 4 %. Point d’alerte du compteur de cycles Valeur réglable qui, lorsqu’elle est dépassée, active une alerte. Les entrées valides sont comprises entre 0 et 4milliards de cycles. Point haut d’alerte de course Valeur de la course, en pourcentage de la course étendue, qui, lorsqu’elle est dépassée, déclenche l’alerte haute des alertes de course. Les valeurs valides sont comprises entre -25 % et 125 %. Point haut haut d’alerte de course Valeur de la course, en pourcentage de la course parcourue, qui, lorsqu’elle est dépassée, déclenche l’alerte haute haute des alertes de course. Les valeurs valides sont comprises entre -25 % et 125 %. Protection de l’instrument Détermine si les commandes d’un dispositif HART peuvent étalonner ou configurer certains paramètres de l’instrument. Il existe deux types de protection d’instrument : « Configuration et étalonnage » : interdit la modification des paramètres de configuration protégés ; interdit l’étalonnage. « Aucun » : permet à la fois la configuration et l’étalonnage. L’instrument est « non protégé ». Réglage Ajustement des conditions de régulation ou des valeurs de paramétrage pour produire l’effet de régulation souhaité. Révision de l’appareil Numéro de révision de l’interface du logiciel qui permet de communiquer entre l’interface de communication et l’instrument. Révision du matériel Numéro de révision du matériel de l’instrument Fisher. Les composants physiques de l’instrument sont définis comme le matériel. Révision du micrologiciel Numéro de version du micrologiciel de l’instrument. Le micrologiciel est un programme qui est saisi dans l’instrument au moment de la fabrication et ne peut pas être modifié par l’utilisateur. Révision universelle HART Numéro de révision des commandes universelles HART, faisant partie du protocole de communications de l’instrument. 99 Manuel d’instructions Glossaire avril 2021 Signal d’entraînement Le signal envoyé au convertisseur I/P depuis le circuit imprimé. Il s’agit du pourcentage de l’effort total du microprocesseur nécessaire pour ouvrir la vanne complètement. Signal d’entrée Le signal de courant en provenance du système de contrôle-commande. Le signal d’entrée peut être affiché en milliampères ou en pourcentage du signal d’entrée. Signal de contre-réaction Indique à l’instrument la position réelle de la vanne. Le capteur de course fournit le signal contre-réaction au circuit imprimé. Tarage à sec La pression fournie à un actionneur et nécessaire pour diriger l’actionneur à travers la course nominale de la vanne. Exprimée en livres par pouce carré. Taux Quantité de variation de la sortie proportionnellement au taux de variation de l’entrée. 100 D103605X0FR Temps de fermeture minimum Durée minimale, en secondes, pour que la course diminue à travers l’ensemble de la course parcourue. Ce taux est appliqué à toute baisse de course. Lesentrées valides sont comprises entre 0 et 400secondes. La désactiver en entrant une valeur de0seconde. Temps de fermeture minimum Durée minimale, en secondes, pour que la course augmente à travers l’ensemble de la course parcourue. Ce taux est appliqué à toute augmentation de course. En raison de la friction, la course réelle de la vanne peut ne pas répondre exactement au même moment. Lesentrées valides sont comprises entre 0 et 400secondes. La désactiver en entrant une valeur de0seconde. Temps libre Pourcentage de temps pendant lequel le microprocesseur est inactif. La valeur standard est de 25 %. La valeur réelle dépend du nombre de fonctions de l’instrument activées et de la quantité de communications en ce même moment. Unités d’entrée analogique Unités dans lesquelles l’entrée analogique est affichée et enregistrée dans l’instrument. Zone d’étalonnage Là où l’instrument a été étalonné pour la dernière fois ; soit en usine, soit sur site. Manuel d’instructions Index D103605X0FR Index A Accumulateur de course haut, 52 Action de borne auxiliaire, 17 Activation de la borne de sortie, 36 Activation de la limite de pression de sortie, 30 Activation intégrale Réglage de course, 26 Réglage de la pression, 27 Adresse d'interrogation, 17 Affectations de variable HART, 37 Agence coréenne pour la sécurité et la santé au travail (KOSHA), Corée du Sud, Certifications, 7 Aimant de contre-réaction, démontage, 58 Aimant., 28 Alerte de course basse, 52 avril 2021 Action de borne auxiliaire, 17 Bouton d’étalonnage (CAL), 17 démontage, 66 Maintenance, 66 remplacement, 67 Borne auxiliaire, Consignes de longueur de câblage, 12 Bouchons de tuyauterie, Maintenance, 65 Bouton d’étalonnage (CAL), 17 C Capacité (électrique) maximale du câble, 12 Capacité de sortie maximale, 6 Capteur de pression, Étalonnage, 43 Capteur de pression d'alimentation, Étalonnage, 44 Capteur de secours/déviation de course, Sélection pression/course, 19 Capteur interne hors limites, 51 Capteurs de pression, Étalonnage, 43 Alerte de course haute, 52 Caractérisation, 21 Caractéristique d'entrée, 21 Personnaliser la caractérisation, 21 Alerte de course haute haute, 52 Caractérisation d’entrée, 21 Alerte du signal d'entraînement, 50 Catégorie NE107, Paramètres d’alerte, 49 Alerte validation du courant de boucle, 51 Centre national de contrôle et d'inspection pour la protection contre les explosions et la sécurité del'emploi des instruments (NEPSI), Chine, Certifications, 7 Alerte de course basse basse, 52 AMS Suite : Intelligent Device Manager, 4 Aperçu, 48 Appareil, 56 Variables à fonction principale et variables d’état, 48 Appareil à fermeture étanche, certifié gaz naturel, Certifications, 7 Application spéciale, Relais, 28 Arborescences du menu de l’interface de communication,85 Autorités de normalisation et de métrologie des Émiratsarabes unis (ESMA), Émirats arabes unis, Certifications, 7 Avance/retard, 23 avance/retard, 23 B Certification Management Limited (CML), Japon, Certifications :, 7 Certifications : Afrique du Sud, SANS, 7 Appareil à fermeture étanche, certifié gaz naturel, 7 Brésil, INMETRO, 7 Chine CCC, 7 NEPSI, 7 Corée du Sud KOSHA, 7 KTL, 7 Émirats arabes unis, ESMA, 7 Inde, PESO CCOE, 7 Japon, CML, 7 Registre Lloyds, 7 Russie, Kazakhstan, Bélarus, CUTR, 7 Bande morte, Principe de fonctionnement, 52 Certificats de zone dangereuse , 7 Bande morte intégrale, Réglages intégrés de course/pression, 27 Changer la révision universelle HART, 38 Base du module, remplacement, 59, 60 Boîtier à bornes, 17 Changer le mode contrôle, 20 China Compulsory Certification (CCC) (Certification de produit obligatoire en Chine), Chine, Certifications, 7 101 Manuel d’instructions Index avril 2021 D103605X0FR Circuit imprimé démontage, 63 Maintenance, 63 remplacement, 63 Débit ouvert au point de consigne, 23 Classification électrique, 7 Défaillance de l’intégrité de la mémoire flash, 51 Commande HART n° 48, 49 Défaillance de la boucle d’induction électromagnétique, 51 Communication HART, principe de fonctionnement, 81 Défaillance de la tension de référence, 52 Commutateur, 36 Spécifications, 8 Défaillance du capteur de course, 52 Commutateur d’alerte, Fonction, Configuration de la borne de sortie, 36 Défaillance du capteur de secours, Sélection pression/course, 18 Commutateur de limite intégré, spécifications, 8 Défaillance du courant d’entraînement, 50 Commutateur DIP, réglage, 63 Commutateur intégré, 8 Dépannage Communications ou sorties, 67 instrument, 68 Vérification de la tension disponible, 67 Compatibilité de l’actionneur, 7 Descripteur, 17 Compatibilité électromagnétique, 6 Déviation de course, 52 Compteur de cycles élevés, 50 Déviation de la pression d’une extrémité, 51 Condition d’alimentation nulle, 29 Configuration de la borne de sortie, 36 Diagnostics, 54 Test de course partielle, 54 Vanne de course, 54 Configuration des alertes, 38 Diagnostics de l'appareil, 49 Configuration des commutateurs, 36 Commutateur fermé, 37 Point de déclenchement du contacteur de fin de course,36 Source du commutateur d’alerte, 36 Diagnostics en cours, 50 Configuration guidée, 15 Durée du filtre au point de consigne, 23 Configuration manuelle, 15 Durée du filtre avance/retard au point de consigne, 23 Configuration, initiale, 3 Dysfonctionnement de l’appareil de terrain, 51 Commutateur fermé, 37 Déclaration de SEP, 8 Défaillance critique NVM (mémoire non volatile), 50 Défaillance du capteur de pressions , 51 Documents connexes, 5 Données de diagnostic accessibles, 50 Durée de la pression de secours de déviation de course, 20 Consommation d’air à régime stable, 6 Contacteur de fin de course, Fonction, Configuration de la borne de sortie, 36 Convertisseur I/P Maintenance, 61 remplacement, 62 Coupure de course haute, 52 Coupure de course Lo, 52 Coupures et limites, 19 Sélection de la limite/coupure basse, 19 Sélection de la limite/coupure haute, 19 Seuil de limite/coupure bas, 19 Seuil de limite/coupure haut, 19 D Débit fermé au point de consigne, 23 102 E Électrovanne, Surveillance de l’état de fonctionnement, 55 Ensemble de réglage Course, 24 Pression, 27 Ensemble de réglage de course, 24 Ensemble de réglage de la pression, 27 Ensembles de réglage de course, Valeurs de gain, 24 Ensembles de réglage de la pression, Valeurs de gain, 27 Erreur du circuit de sortie , 51 Étalonnage, 39 Bouton-poussoir, 42 Capteur, 43 Capteurs de pression, 43 Course, 40 Manuel d’instructions Index D103605X0FR Auto, 40 Manuel, 41 Entrée analogique, 44 PST, 47 Réglage du relai, 45 Étalonnage automatique, 15, 40 Messages d'erreur, 40 Paramètres avancés, 15 Sans biais, 15 Standard, 15 Étalonnage automatique en cours, 50 Étalonnage de la course, 40 avril 2021 H Heure de l’instrument, Régler, 18 Hors ligne / échec , 51 I Impédance d'entrée, 7 Informations de l’appareil, 48 Installation, 3 Étalonnage du bouton-poussoir, 42 Institut national de la métrologie, de la qualité et de la technologie (INMETRO), Brésil, Certifications, 7 Étalonnage du capteur, 43 Intégrateur à faible saturation, 51 Étalonnage en cours, 50 Intégrateur à saturation élevée, 51 Étalonnage manuel, 41 Interface de communication, Test de course partielle, 55 Étalonnage numérique, 41 Étalonnage PST, 47 État de l'appareil, 49 F J Jauges, Maintenance, 65 L Fenêtre Rshaft n° 1, Aimant., 28 L’heure de l’instrument est approximative, 51 Fenêtre Rshaft n° 2, Aimant., 28 Laboratoire d’essai en Corée (KTL), Corée du Sud, Certifications :, 7 Fiche technique, 18 Filtre HART, 9 Filtre I/P, remplacement, 61 Fonction, Configuration de la borne de sortie Commutateur d’alerte, 36 Contacteur de fin de course, 36 Transmetteur, 36 Fonctionnement en mode rafale, réglage du Tri-Loop, 14 Limite de l’intégrateur, Réglages intégrés de course/pression, 28 Limite Hi/seuil de coupure, 19 Limite Lo/seuil de coupure, 19 Limites de température, Température ambiante de fonctionnement, 6 Linéarité indépendante, 6 Liste de vérification du support, 70 G Gain de vitesse, Réglage de course, 26 Gain intégral Réglage de course, 26 Réglage de la pression, 27 Logiciel ValveLink, 4 M Gain proportionnel Réglage de course, 26 Réglage de la pression, 27 Maintenance base du module, 58 Boîtier à bornes, 66 Circuit imprimé, 63 Convertisseur I/P, 61 Jauges, bouchons de tuyauterie ou vannes pneumatiques,65 outils requis, 58 Relai pneumatique, 65 Galet n° 1 pour tige coulissante, Aimant., 28 Maintenance de la base du module, 58 Gaz naturel, en tant que produit d’alimentation, 57 Maintenance et dépannage, 57 Gain MLFB Réglage de course, 26 Réglage de la pression, 27 103 Manuel d’instructions Index avril 2021 D103605X0FR Matériaux de construction, 7 Paramètres d’alerte, Par défaut, 49 Message, 17 Paramètres de course partielle, 31 Mouvement de course minimum, 31 Pas de retour, 32 PST de courte durée, 31 Rythme d’entrée de la rampe, 32 Rythme de sortie de la rampe, 32 Seuil de pression entrante, 34 Seuil de pression sortante, 32 Temporisation de rupture, 32 Méthode de test de la résistance à l’humidité, 7 Méthode de test de la résistance aux vibrations, 7 Mode, Rafale, 37 Mode contrôle, 20 Changer le mode contrôle, 20 Mode contrôle, 20 Mode contrôle au redémarrage, 20 Paramètres du filtre, Avance/retard standard, 23 Mode contrôle au redémarrage, 20 Pas de retour, 32 Mode de l’instrument, 16 Personnaliser la caractérisation, Définition, 21 Mode Rafale, 37 Pièces commande, 71 Kits, 71 Liste, 73 modulation par déplacement de fréquence (FSK), 81 Montage d’extrémité Rshaft, Aimant., 28 Mouvement de course minimum, 31 Plage d'entrée analogique, 17 Plage d’entrée Hi, 17 Plage d’entrée Lo, 18 Mouvement du capteur de course, 29 Plage d’entrée, 17 Montages, 6 Plage d’entrée basse, 18 N NAMUR NE43, 8 Niveau de l'instrument, Capacités, 4 Normes nationales de l’Afrique du Sud (SANS), Certifications, 7 Numéro de série Instrument, 17 Vanne, 17 Numéro de série de l’instrument, 17 Numéro de série de la vanne, 17 NVM non critique, 51 O Options, 8 Organisme de protection contre les explosifs et les hydrocarbures - Contrôleur en chef des explosifs (PESOCCOE), Inde, Certifications, 7 Orifice A surpressurisé, 51 Outils de maintenance, 49 État de l'appareil, 49 P Panne du capteur de température, 52 Paramètres par défaut, Configuration détaillée, 15 104 Plage d’entrée haute, 17 Poids DVC6200, 7 DVC6205, 7 DVC6215, 7 Point de déclenchement du contacteur de fin de course, 36 Pratiques de câblage, 9 Capacité (électrique) maximale du câble, 12 Exigences du système de commande, 9 Filtre HART, 9 Tension de conformité, 11 Tension disponible, 9 Pression d'alimentation, 6 Pression d’alimentation basse, 52 Pression d’alimentation haute, 52 pression d’alimentation maximale, 29 Pression de secours activée, 51 Pression de secours de déviation de course, 20 Principe de fonctionnement Communication HART, 81 DVC6200, 81 Protection contre la foudre et les surtensions, 7 Protocole de communication, HART 7 ou HART 5, 6 Protocole de communication HART, 3 PST de courte durée, 31 R Raccordement de contre-réaction, 28 Manuel d’instructions Index D103605X0FR Raccordements, 7 Électriques, 3 Pneumatiques, 3 Raccordements électriques, 3 Raccordements pneumatiques, 3 Rapport d’alertes, 49 avril 2021 Retard, 23 Rythme d’entrée de la rampe, 32 Rythme de sortie de la rampe, 32 S Récupération de secours, 20 Sélection de la limite/coupure basse, 19 Redémarrer le processeur, 68 Sélection de la limite/coupure haute, 19 Registre des alertes, 49 Sélection pression/course, 18 Capteur de secours/déviation de course, 18 Pression-capteur de secours, 18 Régulation de la course, 18 Régulation de la pression, 18 Registre des alertes non vide, 50 Registre des alertes plein, 50 Registre Lloyds, Homologation de type marin, 7 Réglage, 24 Course, 24 Pression, 27 Réglages intégrés, 27 Réglage de course, 24 Stabilisation/Optimisation, 26 Séquences d’accès rapide, Interface de communication, 85 Services de formation, 8 Seuil de pression d’entrée, 34 Seuil de pression de sortie, 32 Signal d’échec, Configuration de la borne de sortie, 36 Réglage de l’étalonnage analogique, 41 Signal d’entrée, 6 Réglage de la pression, 27 Signal de sortie, 6 Réglage du relai, 45 Sortie du transmetteur, 37 Réglage Expert, réglage de course, 24, 27 Sorties, 36 Affectations de variable HART, 37 Configuration de la borne de sortie, 36 Configuration des commutateurs, 36 Mode rafale, 37 Sortie du transmetteur, 37 Réglages intégrés, 27 Réglementations techniques de l’Union douanière (CUTR), Russie, Kazakhstan, Bélarus, Certifications, 7 Régler l’heure de l’instrument, 18 Régulation de la course, Sélection pression/course, 18 Régulation de la course/pression, 18 Durée de la pression de secours de déviation de course, 20 Mode contrôle, 20 Pression de secours, 20 Pression de secours de déviation de course, 20 Récupération de secours, 20 Régulation de la pression, 19 Sélection pression/course, 18 Source du commutateur d’alerte, 36 Spécifications, 5 Stabilisation/Optimisation, 26 Synthèse des résultats CEM, Immunité, 8 T Taux de coupure bas souple, 19 Régulation de la pression, 19 Lim. basse plage de pression, 19 Plage de pression élevée, 19 Sélection pression/course, 18 Taux de coupure haut souple, 19 Régulation de la pression/course, Coupures et limites, 19 Temps de retard, 23 Relai pneumatique démontage, 65 Maintenance, 65 remplacement, 65 Tension de conformité, 11 Repère HART, 16 Repère long HART, 16 Réponse dynamique, 23 Temporisation de rupture, 32 Temps d’avance/retard, 23 Tension disponible, 9 vérification, 67 Test de course partielle, Automatique (planifié), 54 Test de course partielle (niveau ODV seulement), 54 Borne auxiliaire, Bouton-poussoir local, 54 Interface de communication, 55 105 Manuel d’instructions Index avril 2021 Test de course partielle (PST), 30 Test de course partielle (PST) Critère anormal, 34 Critères d’annulation, 34 Non autorisé, 35 D103605X0FR U Test de course partielle automatique, 54 Unités Entrée analogique, 17 Pression, 17 Température, 17 Tige coulissante n° 110, Aimant., 28 Unités d'entrée analogique, 17 Tige coulissante n° 19, Aimant., 28 Unités de pression, 17 Tige coulissante n° 210, Aimant., 28 Unités de température, 17 Tige coulissante n° 25, Aimant., 28 Tige coulissante n° 38, Aimant., 28 Tige coulissante n° 50, Aimant., 28 Tige coulissante n° 7, Aimant., 28 Transmetteur, 8, 36 Fonction, Configuration de la borne de sortie, 36 Spécifications, 8 Transmetteur de position, 36 Transmetteur de position 4‐20 mA intégré, 8 Spécifications, 8 Tri-Loop Hart, 13 Organigramme d’installation, 13 Type d’actionneur, 28 V Valeur basse de la plage de pression, 19 Valeur haute de la plage de pression, 19 Valeurs de gain Ensembles de réglage de course, 24 Ensembles de réglage de la pression, 27 Vanne de course, 54 Vannes pneumatiques, Maintenance, 65 Variable hors limites, 52 Variables, État et fonction principale, 48 Type de relais, 28 Variables à fonction principale et variables d’état, Informations de l’appareil, 48 Type de vanne, 28 Verrouillage en écriture, 16 106 Manuel d’instructions D103605X0FR Contrôleur numérique de vanne DVC6200 avril 2021 107 Contrôleur numérique de vanne DVC6200 avril 2021 Manuel d’instructions D103605X0FR Ni Emerson, ni Emerson Automation Solutions, ni aucune de leurs entités affiliées n’assument quelconque responsabilité que ce soit quant au choix, à l’utilisation ou à la maintenance d’un quelconque produit. La responsabilité du choix, de l’utilisation et de la maintenance de tout produit incombe uniquement à l’acquéreur et à l’utilisateur final. Fisher, FIELDVUE, ValveLink, PROVOX, Rosemount, Tri-Loop, DeltaV, RS3, et THUM sont des marques qui appartiennent à une des sociétés de l’unité commerciale Emerson Automation Solutions d’Emerson Electric Co. Emerson Automation Solutions, Emerson et le logo Emerson sont des marques de commerce et de service d’Emerson Electric Co. HART est une marque déposée de FieldComm Group. Toutes les autres marques sont la propriété de leurs détenteurs respectifs. Le contenu de cette publication est présenté à titre d’information uniquement et, bien que tous les efforts aient été mis en œuvre pour en assurer l’exactitude, il ne doit pas être interprété comme une garantie, expresse ou tacite, concernant les produits et services décrits, leur utilisation ou leur applicabilité. Toutes les ventes sont régies par nos conditions générales, disponibles sur demande. La société se réserve le droit de modifier ou d’améliorer les conceptions ou les spécifications de tels produits à tout moment et sans préavis. Emerson Automation Solutions Marshalltown, Iowa 50158 USA Sorocaba, 18087 Brazil Cernay, 68700 France Dubai, United Arab Emirates Singapore 128461 Singapore www.Fisher.com 108 E 2012, 2021 Fisher Controls International LLC. Tous droits réservés. ">
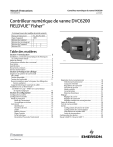
Lien public mis à jour
Le lien public vers votre chat a été mis à jour.